Gurus of Total Quality Management PDF
Document Details
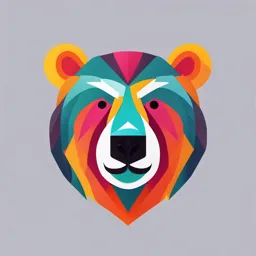
Uploaded by EverlastingLepidolite398
Tags
Related
- Introduction to Operations Management & Total Quality Management PDF
- Introduction to Operations Management and Total Quality Management PDF
- Quality Management System PDF
- Quality Management: An Introduction PDF
- Quality Management Concepts & Techniques PDF
- Total Quality Management (TQM) Presentation PDF
Summary
A summary of the philosophies and contributions of several key figures in the field of Total Quality Management (TQM). It covers the work of individuals like Deming, known for the 14 points, Crosby, Juran, Ishikawa and the seven quality tools, Taguchi, and Shingo, known for continuous quality improvement.
Full Transcript
Gurus of Total Quality Management Dr. WiilIam Edwards Deming (Oct. 14, 1900 - Dec. 20, 1993) He is often referred to as the "Father of Quality Control." Deming is best known for initiating a transformation in the Japanese manufacturing sector in the after effects of World War II. The Deming Prize,...
Gurus of Total Quality Management Dr. WiilIam Edwards Deming (Oct. 14, 1900 - Dec. 20, 1993) He is often referred to as the "Father of Quality Control." Deming is best known for initiating a transformation in the Japanese manufacturing sector in the after effects of World War II. The Deming Prize, the highest award for quality in Japan, is named in his honor. He is also known for his 14 points, for the Deming Chain Reaction and for the Theory of Profound Knowledge. He also modified the Shewhart PDSA cycle to what is now referred to as Deming Cycle. Deming’s 14 Point Methodology Constancy of purpose - create firmness of purpose for continual improvement of products and service and distribute resources to accommodate long term needs rather than short-term profitability with a plan to become competitive, stay in business and provide jobs. The new philosophy - espouse the new philosophy for one can no longer allow delays, mistakes and faulty workmanship. Cease dependence on inspection- remove the need for mass inspection as a technique to attain quality by building quality into the product in the first place. End lowest tender contracts - reduce total cost. Improve every process - Management's job is to constantly make better the system with contribution from workers and management. Institute training on the job - Introduce up to date methods of training on the job, incorporating management to make greatest use of all employees. Institute leadership - Espouse and introduce leadership, aimed at helping people carry out a better job Drive out fear-Build a fear-free environment where everyone can contribute and work effectively. Break down barriers - People should work cooperatively with reciprocal trust respect, and appreciation for the needs of others in their work. Eliminate exhortations - Do away with use of slogans, posters and exhortations demanding zero defects and new level of productivity from the workforce, with no commensurate methods provided. Eliminate arbitrary numerical targets - Remove work standards that stipulate numerical quotas for the workforce and the numerical goals for people in the management. Permit pride of workmanship -eliminate the barriers that steal from hourly workers and people in the management of their rights to pride of workmanship. This implies the eradication of the annual merit rating and management by Encourage education- Deming’s philosophy is founded on long-term, continuous process improvement that cannot be carried out without properly trained and motivated employees a. it leads to better motivated employees; b. it communicates the company goals to the employees; c. it keeps the employees up-to-date on the latest techniques and supports teamwork; d. training and retraining offers a mechanism to ensure enough performance as the job responsibilities change; and e. through increasing job loyalty, it lessens the number of people who "job-hop. Top management's commitment - a clearly defined commitment by the top management to constantly improve quality and productivity and strengthening of obligations to put into practice all these principles is always advantageous to the workforce and the organization. Deming’s 7 Deadly Diseases 1. Lack of constancy of purpose to plan products and services that have a market sufficient to keep the company in business and provide jobs. 2. Stress on short-term profit; short-term thinking that is driven by a fear of unfriendly takeover attempts and pressure from bankers and shareholders to generate dividends. 3. Personal review systems for managers and management by objectives with no methods or resources provided to achieve objectives; includes performance evaluations, merit rating, and annual appraisals. 4. Job-hopping by managers. 5. Using only evident data and information in decision making with little or no consideration given to what is unknown or cannot be known. 6. Extreme medical costs. 7. Too much costs of liability driven up by lawyers who work on contingency fees. Philip Crosby (June 18, 1926-Aug. 18, 2001) He came to national prominence with the publication of his book Quality is Free in 1979. He established the absolutes of quality management, which states that the only performance standard is zero defects and the basic elements of improvement. Four Absolutes of Quality 1. The definition-Quality is conformance to requirements, not goodness. 2. The system-Prevention, not appraisal. 3. The performance standard - Zero defects. 4. The measurement- The price of non-conformance to requirements, not quality circles. Quality Management Maturity Certainty Wisdom Enlightenment Awakening Uncertainty Crosby’s 14 Step Methodology 1. Management commitment - to make clear the management's position on quality. 2. Quality improvement team - to carry out the quality improvement program. 3. Quality measurement - to exhibit existing and possible non-conformance problems in the way that permits objective evaluation and remedial action. 4. Cost of quality -to identify the components of the cost of quality, and give details on its application as a management tool. 5. Quality awareness - to give a method of elevating individual concern among the personnel in the company towards the conformance of the product and service, and the status of the company on the subject of quality. 6. Corrective action -to offer a systematic method of deciding the problems recognized through actions taken in the past. 7. Zero defects planning - to study the different activities that must be performed as groundwork for officially initiating the zero defects program. 8. Supervisor training -to name the type of training that supervisors require to energetically perform their roles with regard to the quality improvement program. 9. Zero defects day - to produce an event that will allow all employee appreciate, through a personal experience, that there has been change. 10. Goal setting -to twist promises and commitments into action by persuading individuals to set up improvement goals for themselves and their groups. 11. Error-cause removal - to offer individual employees a way of communicating to the management, the situations that make it not easy for employees to fulfill the promise to improve. 12. Recognition - to be thankful for those who contribute. 13. Quality councils - to bring collectively professionals in the realm of quality for planned communication on a customary basis with the workforce and management alike. 14. Do it over again - to accentuate that the quality improvement program never ends. Dr. Joseph Moses Juran (24th December, 1904-28th February, 2008) He assisted the Japanese in their reconstruction processes after World War II. Juran first became well-known in the US as the editor of the Quality Control Handbook (1951) and alter for his paper introducing the quality trilogies which are quality planning, quality control and quality improvement. Quality Trilogies by Juran 1. Quality Planning - This involves identifying the customers' needs and expectations, proposing products and services, setting goals, giving training, implementation of projects, reporting, recognizing, and communicating outcome and improvements in systems. 2. Quality control - This concerns creating standards, naming measurements and methods thereof, contrasting results with actual standards and construing the differences and taking action on differences. 3. Quality improvement - This is about the use of structured annual improvements projects and plans, need of improvement, organizing to guide the projects, detecting the causes, giving and verifying remedies and establishing control to keep up gains made. Juran’s Message on Quality 1. Quality control must be essential part of management 2. Quality is no mistake 3. Quality must be planned 4. There are no shortcuts to quality 5. Make use of problems as sources of improvement Juran’s Formula consists of: 1. Create an awareness about the need and propose an opportunity for improvement 2. Set goals for improvements 3. Systematize paths to attain the goals (begin a quality council, identify problems, choose projects, assign teams, delegate facilitators and so on) 4. Give training 5. Do projects to resolve problems 6. Inform progress 7. Provide recognition 8. Communicate outcome 9. Keep score 10. Uphold thrust by making yearly improvements component of the regular systems and processes of the company In his view, the approach to managing for quality consists of: 1. The irregular problem is detected and acted upon by the process of quality control; 2. The constant problem needs a special process, namely, quality improvement; 3. Such constant problems are traceable to a poor-quality planning process. Juran’s Breakthrough Activities or Quality Improvement Include: 1. Breakthrough in attitudes - persuading those responsible that a change in quality level is advantageous and practical; 2. Discovery of the vital few projects - determining which quality problem areas are essential; 3. Organizing for breakthrough in knowledge - defining the organizational system for attaining the knowledge for accomplishing a breakthrough; 4. Formation of a steering arm - defining and staffing a system for directing the study for quality improvement; 5. Formation of an investigative arm - defining and staffing a system for executing the technical inquiry; 6. Diagnosis - collecting and examining the facts necessary and proposing the action desirable; 7. Breakthrough in cultural pattern - determining the effect of a anticipated change on the people involved and looking for ways to rise above opposition to change; 8. Breakthrough in performance - getting agreement to take action; 9. Transition to the new level - implement the change. “Control” Activities Include: 1. Choosing the control subject which is choosing what is intended to regulate; 2. Choosing a unit of measure; 3. Setting a goal for the control subject; 4. Creating a sensor which can measure the control subject in terms of the unit of measure; 5. Measuring real performance; 6. Interpreting the difference between actual performance and the goal; 7. Taking action (if any) on the difference. “Planning” Activities Include: 1. Establish the quality goal 2. Identify customers 3. Discover customer needs 4. Develop product features 5. Develop process features 6. Establish process controls and transfer to operations Dr. Walter Andrew Shewart (March 18, 1891 - March 11, 1967) He is the "Grandfather of Quality Control" was a giant among giants in the quality movement during the first half of the 20th century. His mentoring of other engineers at Western Electric and his groundbreaking work with control charts arguably led a quality revolution and launched the quality profession. By 1924, Shewhart determined the problem of variability in terms of assignable cause and chance cause (Deming named this as common cause). On May 16, 1924, Shewhart prepared a message to his manager, George Edwards about a plain diagram that people would today recognize as a CONTROL CHART. This memorandum set forth the essential principles and considerations that became known as PROCESS QUALITY CONTROL. Shewhart developed what came to be known as the Shewhart cycle: Plan-Do-Study-Act (PDSA) or Plan-Do-Check-Act (PDCA) to manage the effects of variations. He stressed that eliminating variability improved quality. His work created the foundation for statistical process control measures used today. Dr. Armand Feigenbaum (born in 1922) Dr. Feigenbaum is given the credit to the formation of the idea of total quality control in his book Quality Control-Principles, Practice and Administration (1961) and in his article Total Quality Control (1956). The Japanese version of this concept is called Company-wide Quality Control, while it is termed Total Quality Management (TQM) in the United States and elsewhere. He was also the first to classify quality costs as costs of prevention, appraisal and internal and external failures. Feigenbaum philosophy is summed up in his Three Steps to Quality. Armand Feigenbaum is given the credit to the formation of the idea of total quality control in his book Quality Control-Principles, Practice and Administration (1961) and in his article Total Quality Control (1956). He was also the first to classify quality costs as costs of prevention, appraisal and internal and external failures. Feigenbaum’s Three Steps to Quality Quality leadership - This is apparent when the management stresses on sound planning rather than reacting to failures. The management must maintain a constant focus and lead the quality effort. Modern quality technology - The traditional quality development processes cannot resolve 80%-90% of quality problems. This task involves integration of office staff, engineers as well as the shop-floor workers who continually assess and apply latest techniques to satisfy customers in the future. Organizational commitment - Continuous training and motivation of the whole workforce as well as a combination of quality in business planning stage indicates the significance of quality and offers the means for including it in all respects of the organization's activities. Feigenbaum’s 10 Points on TQM: 1. Quality is consciousness programmed not only a technical function. 2. Quality is not what an engineer or marketer says but it is that what the customer speaks of. 3. Quality and cost are a sum, not differences. 4. Quality must be organized to identify everybody's job in the organization 5. Quality is a technique of managing an organization. Good management means continuous stress on the quality. 6. The quality improvement highlighting must take place all through all activities of the organization. 7. Quality is realized through assistance and contribution of each and every person related to the organization. It is also an ethic. 8. Continuous quality improvement needs extensive range of new and existing quality technology of information applications. 9. Total quality program approach leads to productivity and is most effective and less capital intensive. 10. Quality comes, if it is clear, customer oriented, effective and structured. Prof. Kaoru Ishikawa (13th July, 1915-16th April, 1989) He is the "Father of Quality Circles" for his role in launching Japan's quality movement in 1960s. He is recognized with developing the idea of company-wide quality control in Japan. He established the use of quality circles and championed the use of quality tools to know the root causes of problems. He developed one of those tools, the cause-and-effect diagram, which is also known as the Ishikawa diagram or the fishbone diagram. Ishikawa’s Seven Quality Tools: Process flow chart Check sheet Histogram Pareto chart Cause - effect diagram (Ishikawa diagram) Scatter diagram Control chart Ishikawa’s Key Elements of Quality Management: 1. Quality starts with education and culminates with education. 2. The first step in quality is to know the customers' requirements. 3. The perfect state of quality control happens when inspection is no longer compulsory. 4. Take out the root cause, not the symptoms. 5. Quality control is the duty of all workers and all divisions. 6. Do not mistake means with the objectives. 7. Set quality first and set your sights on long-term profits. 8. Market is the entry and way out of quality. 9. Top management must not demonstrate annoyance when facts are presented by subordinates. 10. 99% of problems in a company can be resolved with easy tools for analysis and problem- solving 11. Data without dispersion information (variability) are fake data. Ishikawa’s Six Fundamental Principles: 1. Quality first - not short-term profits first 2. Customer orientation - not producer orientation 3. The next step is your customer - breaking down the fence of sectionalism 4. Using facts and data to make presentations - use of statistical methods 5. Reverence for humanity as a management philosophy, full participatory management 6. Cross-functional management. Dr. Genichi Taguchi (1st January, 1924-2nd June, 2012) Dr. Taguchi was born in Japan and completed his graduation in the subject of Mechanical Engineering and obtained Ph.D. in the year 1962. He estimated that 80% of all defective items are caused by poor product design. Taguchi defines quality as the "loss imparted to the society from the time a product is shipped". Taguchi’s Quality Concept: 1. Quality improvement should focus on reducing the variation of the product's key performance characteristics about their target values. 2. The loss suffered by a customer due to a product's performance variation is often just about proportional to the square of the deviation of the performance characteristics from its target value. 3. The ultimate quality and cost of manufactured products are determined to a great extent by the engineering design of the product and the manufacturing process. 4. A product's or process's performance variation can be lessened by exploiting the non- linear effects of the product or process parameters on the performance characteristics. 5. Statistically planned experiments can be used to name the settings of product/ process parameters that reduce performance variation. Taguchi’s Eight-point Approach: 1. Determine the main functions, side effects and loss modes. 2. Determine the noise factors and the testing conditions for evaluating failure of quality. 3. Determine the quality characteristics to be observed and the objective functions to be optimized. 4. Determine the control factors and their alternate levels. 5. Blueprint the matrix requirements and define the data analysis procedure. 6. Carry out the matrix. 7. Examine the data, identify optimum levels for the control factors and foresee performance under these levels. 8. Perform the confirmation experiment and prepare future actions. Dr. Shingo Shigeo Dr. Shingo Shigeo is the greatest contributor to modern manufacturing practices. While his name has modest recognition in the western hemisphere, his teachings and principles have formed the backbone of efficient engineering practices. Shigeo's Three Concept for Continuous Quality Improvement: 1. Just in Time (JIT) - is about supplying customers with what they want when they want it. The aim of JIT is to diminish inventories by producing only what is necessary when it is necessary. 2. Single Minute Exchange of Dies (SMED) - It is a system for speedy changeovers between products. The target is to make simpler materials, machinery, processes and skills to significantly decrease changeover times from hours to minutes. 3. Zero Quality Control (ZQC) - The ZQC concepts are based on the theoretically ideal scenario. Dr. Shigeo' basic idea was to implement error-proofing devices in the assembly line to abolish the likelihood of flawed operations This technique by Dr. Shigeo makes use of the following engineering principles: a. 100% inspections done at the starting place instead of sampling inspections b. Instant feedback from consecutive quality checks and self-checks c. Poka-yoke designed manufacturing devices-Poka yoke relates to stopping processes as soon as a defect happens, searching the defect source and avoiding it from occurring once more so that there will be reduced reliance on statistical quality inspections and the production process will have zero defects. Masaki Imai Masaki Imai is the Founder and President of Kaizen Institute who threw the word "Kaizen". Kaizen refers to continuous or on-going improvement" in Japanese. Kaizen was originally introduced to the West by Masaaki Imai in his book Kaizen: The Key to Japan's Competitive Success in 1986. Today Kaizen is acknowledged globally as an essential pillar of an organization's long-term competitive strategy. Kaizen Guiding Principles: 1. Good processes carry good results 2. Go see for yourself to grab the present situation 3. Speak with data, direct by facts 4. Take action to contain and remedy root causes of problems 5. Work as a team 6. Kaizen is everyone's business