TQM Lecture 4: Process Focus PDF
Document Details
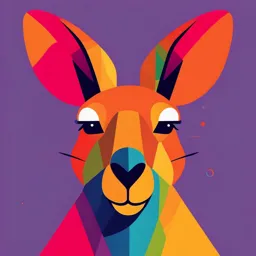
Uploaded by SubsidizedDream
Tags
Summary
This lecture discusses process focus in total quality management (TQM). It covers value-creation and support processes, process requirements, and process design, including factors like safety, cost, and maintainability. The document also touches on mistake-proofing processes.
Full Transcript
TQM LECTURE 4: PROCESS FOCUS These processes typically fall into two categories: Value-creation processes...
TQM LECTURE 4: PROCESS FOCUS These processes typically fall into two categories: Value-creation processes (Sometimes called core processes) are those most important to "running the PROCESS business" and maintaining or achieving a sustainable competitive advantage. Is a sequence of linked activities that is intended to achieve some result, such as producing a good or service for a customer within or outside the organization. Support processes Are those that are most important to an organization's value- creation processes, PROCESS MANAGEMENT employees, and daily operations. Involves planning and administering the activities necessary to achieve a high level of performance in key organizational processes, and identifying opportunities for PROCESS REQUIREMENTS improving quality and operational performance, and ultimately, customer Understanding the requirements that processes should meet is vital to designing satisfaction. them. Given the diverse nature of value-creation processes, the requirements and performance characteristics might vary significantly for different processes. In Three Major Activities of Process Management general, value creation process requirements are driven by consumer or external Design customer feeds. Control Improvement Cycle time-refers to the time it takes to accomplish one cycle of a process (e.g., the time from when a customer orders a product to the time that it is delivered, or the total time needed to introduce a new product). Process Owners- (individual or group) are accountable for process performance and have the authority to control and improve their process. To apply the techniques of process management, processes must be: 1. repeatable 2. measurable AT&T, for example, identified the following principles to guide their process management activities: Process improvement focuses on the end-to-end process. PROCESS DESIGN The mind-set of quality is one of prevention and continuous improvement. The goal of process design is to develop an efficient process that satisfies both internal Everyone manages a process at some level and is simultaneously a customer and external customer requirements and is capable of achieving the requisite level and a supplier. of quality and performance. Customer needs drive process improvement. Corrective action focuses on removing the root cause of the problem rather Factors that might need to be considered in process design includes: than on treating its symptoms. 1. Safety Process simplification reduces opportunities for errors and rework. 2. Cost Process improvement results from a disciplined and structured application of 3. Variability quality management principles. 4. Productivity 5. environmental impact IDENTIFYING PROCESS AND REQUIREMENTS 6. "green" manufacturing Leading organizations identify important processes throughout the value chain that 7. measurement affect their ability to deliver customer value. 8. Capability 9. maintainability of equipment TECHNOLOGY MISTAKE-PROOFING PROCESSES is an integral part of process design that makes today's service and manufacturing Typical mistakes in production are omitted steps in a process, setup errors, missing processes operate productively and meet customer needs better than ever. parts, wrong parts, or incorrect adjustments. Such errors can arise from the following factors: PROCESS MAPPING 1. Forgetfulness due to lack of reinforcement or guidance Designing a process requires a systematic approach. To describe the specific steps in 2. Misunderstanding or incorrect identification because of the lack of familiarity with a process and their sequence, we generally develop a process map or flowchart, a process or procedures. along with standard operating procedures and work instructions. 3. Lack of experience. 4. Absentmindedness and lack of attention, especially when a process is PROCESS DESIGN FOR SERVICES automated Most cross-functional business value-creation processes and all support processes are primarily service- oriented. Thus, it is important to understand the fundamental Preventing mistakes can be done in three ways: differences between manufacturing and service processes. 1. Designing potential defects and errors out of the process. Clearly, this approach is the best because it eliminates any possibility that the error or defect will occur First, the outputs of service processes are not as well defined, as are and will not result in rework, scrap, or wasted time. manufactured products. 2. Identifying potential defects and errors and stopping a process before they Second, most service processes involve a greater interaction with the occur. Although this approach prevents defects and errors, it does result in some customer, often making it easier to identify needs and expectations. nonvalue-added time. “On the other hand, customers often cannot define their needs for service until after 3. Identifying defects and errors soon after they occur and quickly correcting the they have some point of reference or comparison. “ process. This can avoid large amounts of costly defects and errors in the future, but does result in some scrap, rework, and wasted resources. A useful approach to designing services is to recognize that services differ in three dimensions: POKA-YOKE (POH-KAH YOH-KAY) Customer contact and interaction Is an approach for mistake-proofing processes using automatic devices or simple Labor intensity methods to avoid human error. Poka-yoke is focused on two aspects: Customization prediction detection In designing service processes, the following questions should be considered: The poka-yoke concept was developed and refined in the early 1960s by the late What service standards are required to be met? Shigeo. What is the result of the service to be provided? At what point does the service begin, and what signals its completion? The following list summarizes the typical types of service errors and related poka- What is the maximum waiting time that a customer will tolerate? yokes. How long should it take to perform the service? Who must the consumer deal with in completing the service? 1. Task errors What components of the service are essential? Desirable? Superfluous? 2. Treatment Errors Which components can differ from one service encounter to another while still 3. Tangible Errors meeting standard? 4. Customer Errors in preparation 5. Customer Errors during an encounter DESIGN FOR AGILITY 6. Customer Errors at the resolution stage Agility is a term that is commonly used to characterized flexibility and short cycle PROCESS CONTROL times. Control Is the activity of ensuring conformance to the requirements and taking Flexibility refers to ability that to adapt quickly and effectively to changing corrective action when necessary to correct problems and maintain stable requirements. performance. Control should be the foundation for organizational learning. Many companies have adopted an approach that has been used in the U.S. military, company’s targets, strategies, and implementations” or more simply, “ the called after-action review, or debrief. search for industry best practices that lead to superior performance. This review consists of asking four basic questions: The term best practices refers to approaches that produce exceptional What was supposed to happen? results, are usually innovative in terms of the use of technology or human What actually happened? resources and are recognized by customers or industry experts. Why was there a difference? What can we learn? Process Benchmarking – identifies the most effective practices in key work processes in organizations that perform similar functions, no matter in what PROCESS CONTROL IN MANUFACTURING industry. - Manufacturing Control is usually applied to incoming materials, key processes, Reengineering – has been defined as “the fundamental rethinking and radical and final product and services. redesign of business processes to achieve dramatic improvement in critical, - Control in manufacturing starts with purchasing and receiving processes. contemporary measures of performance, such as cost, quality, service, and - Document control procedures are usually written down in a process control plan. speed. PROCESS CONTROL IN SERVICES MANAGING SUPPLY CHAIN PROCESSES For many services, process control follows the same paradigm as in manufacturing: Supply chains are among the most important business processes and can be define a standard or goal, measure accomplishment, compare results with standard, viewed as encompassing may key value creation and support processes such as and make corrections as needed. supplier selection and certification, purchasing, logistics, receiving, and performance measurement. PROCESS IMPROVEMENT 1. Continuous improvement refers to both incremental changes, which are small Supplier include not only companies that provide materials and components, and gradual, and breakthrough improvements, which are large and rapid. but also distributors, transformation companies, and information, health care, and education providers. Learning cycle stages Supplier Certification these processes are designed to rate and certify suppliers Planning who provide quality materials in a cost effective and timely manner. Execution of plans Assessment of progress Certified supplier- defines as one, after extensive investigation, is found to supply Revision of plans based upon assessment findings material of such quality that routine testing on each lot received is necessary. During 1950-1951 Toyota initiated some of the earliest formal continuous improvement programs. Toyota pioneered Just in time (JIT) which showed that companies could make product efficiently with virtual zero defects. Kaizen- is a Japanese word that means gradual and orderly continuous improvement. Kaizen Event- is an intense and rapid improvement process in which a team or a department throws all its resources into an improvement project over a short time period, as opposed to traditional kaizen application, which are performed on a part time basis. 2. Breakthrough Improvement refers to discontinuous change, as opposed to be gradual, continuous improvement philosophy of kaizen. Benchmarking is defined as “measuring your performance against that best- in-class companies, determining how the best in class achieve those performance levels, and using the information as a basis for your own