Sviluppi Storici e Processi Produttivi PDF
Document Details
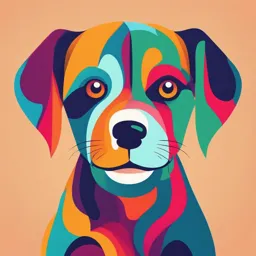
Uploaded by LowCostEclipse2745
University of Ferrara
Tags
Summary
Questo documento fornisce una panoramica dello sviluppo storico dei processi produttivi, evidenziando come l'evoluzione tecnologica, dall'energia muscolare al motore a vapore e all'elettricità, abbia influenzato la produzione industriale. Vengono descritte le fasi di un nuovo prodotto, dalla definizione delle specifiche alla progettazione dettagliata e alle strategie di ottimizzazione dei processi produttivi.
Full Transcript
Sviluppi storici I processi produttivi vengono usati da varie migliaia di anni, inizialmente per realizzare oggetti in pietra, in metallo e ceramici. Nell'antica Roma esistevano fabbriche per la produzione di massa di oggetti in vetro e molte attività, incluse quelle minerarie, metallurgiche, e nel...
Sviluppi storici I processi produttivi vengono usati da varie migliaia di anni, inizialmente per realizzare oggetti in pietra, in metallo e ceramici. Nell'antica Roma esistevano fabbriche per la produzione di massa di oggetti in vetro e molte attività, incluse quelle minerarie, metallurgiche, e nel settore tessile sono state a lungo utilizzate basandosi sul principio della divisione dei compiti. Nonostante questo, la maggior parte delle attività produttive per secoli è rimasta essenzialmente un'attività individuale praticata da artigiani. L'unica forma di energia inizialmente disponibile era quella muscolare umana o animale. L'intuizione di successive generazioni di artigiani ha portato allo sviluppo di molte tecniche ed a una grande varietà di prodotti, ma le quantità prodotte erano necessariamente limitate dalla potenza disponibile. L'acqua ha affiancato la forza muscolare solo nel Medioevo è solo lì dove c'era la disponibilità di acqua corrente; questo ha vincolato il posizionamento delle aziende e la velocità di crescita della produzione industriale. Alla fine del XVIII secolo lo sviluppo del motore a vapore ha reso disponibile grandi quantità di energia dovunque fosse richiesta. Questo ha stimolato progressi nei processi produttivi e ha facilitato l'incremento della produzione fornendo una abbondanza di beni. Di conseguenza anche la società si è trasformata e in seguito questi sviluppi sono stati chiamati rivoluzione industriale. L'energia meccanica ha affiancato l'energia muscolare e quella idraulica. Spesso le macchine erano collegate con cinghie ad un albero che prendeva il moto da un'unica fonte di energia. Verso la metà del XIX secolo alcune funzioni svolte da uomini sono state affidate a macchine nelle quali componenti meccanici come le camme e le leve erano organizzate in modo intelligente per svolgere compiti relativamente semplici e ripetitivi. Questa meccanizzazione ha eliminato alcuni ruoli ma le persone hanno facilmente trovato lavoro nella espansione dei processi produttivi e nel settore terziario. Verso l'inizio del XX secolo ulteriori sviluppi sono stati facilitati dall'introduzione dell'energia elettrica. Adesso le macchine potevano essere messe in movimento individualmente e controlli basati su circuiti elettrici permettevano un ulteriore livello di sofisticazione. Nella seconda metà del XX secolo ulteriori sviluppi sono stati resi possibili dall'avvento del computer che ha reso disponibile potenze di calcolo inimmaginabili fino a quel momento e l'elettronica allo stato solido dei transistor ha permesso la realizzazione di strumenti molto versatili a costi sempre più bassi. All'inizio degli anni 70 la disponibilità di microprocessori con migliaia di componenti elettronici compattati su un piccolo wafer di silicio ha reso possibile lo svolgimento di compiti computazionali, di controllo, di pianificazione e gestione ad alte velocità, spesso in tempo reale, a basso costo. Una caratteristica di questa rivoluzione industriale è che, oltre alla possibilità di sostituire la maggior parte dei lavori faticosi, ha reso fattibile anche migliorare e qualche volta anche sostituire lo sforzo mentale. Alcune conseguenze di questi sviluppi sono evidenti: molti lavori pericolosi, faticosi o noiosi sono svolti da macchine o robot controllati da computer; la varietà dei prodotti aumenta continuamente; la loro qualità migliora; la produttività, espressa come output per operatore cresce continuamente; l'esigenza di risorse naturali diminuisce. Un’ulteriore conseguenza di questa evoluzione è che tendono a sparire i lavori semplici, è richiesta manodopera con competenze di livello sempre maggiore. Un'ulteriore rivoluzione si sta verificando ora con l'avvento dell'intelligenza artificiale, in grado di prendere decisioni (esempio delle ricerche negli studi legali) Azienda manifatturiera Un ente produttivo, che sia azienda o divisione di azienda, di solito si basa sui propri punti di forza per mantenere o aumentare la propria quota di mercato. I punti di forza possono essere una specifica tecnologia che i concorrenti non sono in grado di utilizzare, una competenza specifica (nel settore automobilistico potrebbe essere la capacità di realizzare motori ad alte prestazioni oppure un livello elevato di affidabilità generale), la disponibilità di apparecchiature che i concorrenti non posseggono, oppure la disponibilità di una rete di distribuzione. Quest'ultimo è il motivo per cui i marchi della moda francesi comprano quelli italiani. Ovviamente la valorizzazione dei propri punti di forza è sempre affiancata da indagini di mercato. Una prima fase necessaria di un nuovo prodotto è la definizione delle specifiche. Sotto molti punti di vista questa è la fase più importante. Se le specifiche non sono in correlazione con le esigenze del cliente la conseguenza inevitabile è un fallimento del prodotto. Specifiche inutilmente di alto livello conducono a costi di produzione troppo alti e mancanza di competitività. Le prestazioni devono essere ottimizzate. Per verificare che il prodotto sia in grado di avere successo nel mercato viene confrontato con la concorrenza (benchmarking). In qualche caso un prodotto di cui non siano disponibili disegni e specifiche viene riprodotto mediante il reverse engineering. Qualche volta i prodotti della concorrenza vengono smontati per analizzarne le caratteristiche positive. Progettazione concettuale. Questa è la fase più creativa. Il prodotto viene progettato a grandi linee in modo che possa soddisfare le specifiche, che abbia una durata adeguata e che possa soddisfare le richieste della clientela. Al giorno d'oggi il cliente chiede prodotti personalizzati anche nella produzione di grande serie a prezzi bassi. A questo scopo è necessario che le linee di produzione garantiscano una sufficiente flessibilità. In questa fase non sono necessari disegni dettagliati, sono sufficienti schemi che illustrino i componenti principali. Si effettua una prima selezione dei materiali e, conseguentemente, dei processi produttivi. Progetto dettagliato. Il prodotto viene poi progettato in modo da soddisfare vari criteri. I progettisti si impegnano affinché il prodotto sia bello e che abbia le funzionalità richieste dal cliente. Gli ingegneri meccanici ed elettrici devono fare in modo che il prodotto funzioni regolarmente. Molte fasi della progettazione hanno luogo al computer. Grazie alla modellazione CAD il progettista può rapidamente prendere in considerazione varie alternative ed analizzarle mediante software di simulazione. Alla fine della vita utile bisogna pianificare il riutilizzo, il riciclaggio o, se inevitabile, lo smaltimento del prodotto in modo sicuro e accettabile dal punto di vista ecologico. Spesso il riciclaggio richiede meno energia dell'utilizzo dei materiali a partire dalla materia prima; in questo modo si riduce l'inquinamento in atmosfera oltre all'esigenza di materie prime. Il prodotto deve essere anche facilmente realizzabile. A questo scopo è fondamentale la cooperazione tra ingegneri industriali, meccanici, elettrici ed esperti di produzione. Spesso piccole variazioni progettuali possono comportare o rimuovere enormi problemi produttivi, influenzando in questo modo costo, qualità e affidabilità del prodotto. Nel caso di componenti realizzati internamente si sceglie il processo produttivo e i parametri di processo in modo da ottimizzare la qualità e le proprietà del prodotto finale. Si progettano le attrezzature, si comprano gli utensili, si pianificano i percorsi degli utensili da usare nelle macchine programmabili. Quando la geometria è stata creata col CAD, esiste un database e può essere usato direttamente. I computer sono usati per l'ottimizzazione e il controllo dei processi, la gestione dei materiali, la programmazione e il monitoraggio. Tutte queste attività vengono generalmente chiamate computer aided manufacturing (CAM) e comprende i blocchi compresi fra il 5 e 8. Concurrent engineering Anche la breve e per molti versi incompleta presentazione sul processo manifatturiero vista poco fa indica la complessità del problema. Un'azienda manifatturiera efficiente e competitiva richiede una stretta cooperazione tra le varie attività in modo tale che esse diventino parti di un sistema dinamico interattivo. Sfortunatamente per molti anni questo ideale raramente è stato raggiunto. Il problema è che l'approccio tradizionale valuta l'industrializzazione dei prodotti come un processo sequenziale nel quale un'attività viene avviata solo a conclusione della precedente. Le aziende sono organizzate in reparti con funzioni nettamente separate nei quali persone altamente specializzate prendono decisioni con scarso riguardo sulle conseguenze. In effetti è come se fossero state erette delle pareti tra i reparti. La parete più dannosa è quella interposta fra l'ufficio tecnico e la produzione. Il progettista stabilisce il progetto e implicitamente fissa anche il processo produttivo e di conseguenza il costo di produzione. Malintesi nell'organizzazione sequenziale sono molto frequenti. Questo tipo di problema non si pone se l'organizzazione è di tipo artigianale o nella piccola industria perché il know-how di tutti gli aspetti del prodotto appartiene a una o poche persone. È un problema specifico della grande azienda. Un altro aspetto che è emerso sta nel fatto che i costi di produzione sono decisi quasi completamente in fase di progetto mentre la fase di progettazione in sé costa molto poco. Si può incidere sui costi di produzione anche intervenendo su altri aspetti, materia prima, manodopera, costi generali, ma i risparmi che si possono ottenere sono molto minori. Queste considerazioni hanno portato a modificare la procedura di industrializzazione, dall'industrializzazione sequenziale a quella in parallelo o simultanea (concurrent engineering). Per esempio, in Toyota viene attivato uno staff di progetto costituito da persone provenienti da tutti i reparti; è stato messo a punto nella progettazione della prima Lexus e riutilizzato per la prima versione della Prius, la prima auto ibrida. Come si vede in figura, nell’ingegnerizzazione sequenziale la spesa dedicata al progetto può essere piuttosto piccola ma i costi decisi fino alla produzione sono elevati. Nella progettazione sequenziale le modifiche al progetto sono forzate da problemi che emergono durante la produzione o peggio in servizio. Poiché anche una piccola modifica può influire su molti altri componenti e funzioni, le conseguenze sono costi che aumentano rapidamente e un prolungato ciclo di maturazione del prodotto. Di conseguenza, le aziende che usano l'industrializzazione sequenziale si trovano svantaggiate rispetto ai loro competitori più agili. Il riconoscimento di questi problemi ha condotto all'introduzione, o meglio alla reintroduzione, del concurrent engineering. Come implica il nome, le attività non sono più isolate né si succedono in sequenza; piuttosto esse sono sovrapposte oppure hanno luogo contemporaneamente. Il concetto non è nuovo, l'artigiano praticava il concurrent engineering, così come le piccole aziende. Anche Henry Ford lo usava, la sua squadra era piccola ed ognuno era consapevole delle esigenze del cliente, dei materiali disponibili e delle potenzialità delle tecniche produttive; di conseguenza il progetto era basato sulle tecniche produttive disponibili all'epoca. Il compito è diventato progressivamente più difficile all'aumentare della complessità dei prodotti, della varietà dei materiali e delle tecniche di produzione. Le conoscenze sono aumentate ed ogni individuo è diventato sempre più specializzato. Il concurrent engineering a questo livello richiede una squadra di esperti in continua interazione. La squadra spesso lavora in un ambiente comune sebbene le comunicazioni via computer permettano la cooperazione anche da postazioni diverse. Il concurrent engineering inizia con il riconoscimento che un progetto è sempre un processo iterativo e che la progettazione di un prodotto ha conseguenze sulla produzione. Nelle prime fasi della progettazione le modifiche possono essere apportate facilmente e a basso costo e il prodotto può essere pensato per garantire bassi costi di produzione e qualità al massimo livello. Il costo della fase di progettazione sarà maggiore ma sarà possibile ridurre i costi di produzione e il tempo totale per raggiungere la maturità del prodotto. Se applicato in modo corretto il concurrent engineering può dare risultati formidabili. Per esempio i produttori di automobili statunitensi tradizionalmente avevano bisogno di 6 anni per arrivare sul mercato con un nuovo prodotto, ma il tempo è stato dimezzato e sarà ulteriormente ridotto in seguito. Tempi inferiori di sviluppo del prodotto sono importanti non solo per la riduzione dei costi ma anche perché la vita dei prodotti si sta accorciando; in alcuni settori, in particolare nell’elettronica, il tempo di sviluppo è maggiore della vita del prodotto. L’avvento di potenti modellatori 3D permette la visualizzazione di completi assemblaggi e con le stampanti 3D è possibile realizzare tali modelli rapidamente. Questo permette il confronto tra varie alternative accelerando lo sviluppo del prodotto. Forma e dimensioni Le prime caratteristiche che si osservano di un oggetto sono la forma e le dimensioni. Entrambi gli aspetti hanno connotazioni estetiche ed è compito del designer industriale creare un oggetto piacevole. La forma e le dimensioni sono critici anche dal punto di vista funzionale. In un assemblaggio molti componenti devono essere collegati e questa esigenza richiede che le deviazioni accettabili dalle dimensioni, le cosiddette tolleranze dimensionali, debbano essere specificate e non possano essere superate. Questo porta alla necessità di mettere a punto tecniche e procedure di misura. Le nostre impressioni sono anche molto influenzate dall’aspetto della superficie di un prodotto. Di nuovo il designer industriale dovrà specificare un livello di finitura per le parti in vista ma ci sono anche rigidi requisiti tecnici che devono essere soddisfatti se due componenti devono essere accoppiati per funzionare correttamente. Di conseguenza deve essere adottata una appropriata tecnica di misura e deve essere eseguita la misura della qualità superficiale. La forma di un oggetto è determinata prima di tutto dalla sua funzione. La complessità della forma spesso stabilisce quali processi possano essere presi in considerazione per realizzarla e, in senso generale, al crescere della complessità diminuisce la gamma di processi utilizzabili e aumenta il costo di progetto e di produzione. Una regola base del progetto e perciò quella di mantenere la forma più semplice possibile. Questa regola, tuttavia, non deve essere rispettata se una forma più complessa permette di raggruppare in un unico componente più componenti oppure consente di eliminare una o più fasi produttive. C’è stato un periodo del secolo scorso nel quale sono stati realizzati vari codici di group technology, o tecnologia di gruppo. Spesso questi codici erano finalizzati ad indicare la maggiore o minore facilità di produzione con una determinata tecnica produttiva. A chi serve un codice di questo tipo? Quando in un’azienda A si progetta una componente che si vuole far realizzare in un’azienda B, spesso sono necessarie delle riunioni tra tecnici delle 2 aziende per arrivare a definire la forma definitiva. Questo perché i tecnici dell’azienda A non sono esperti nella tecnica produttiva usata da B. Le informazioni fornite da un piano come quello in figura possono essere utili per ridurre l’esigenza di tali incontri. In seguito sono stati sviluppati programmi che volevano andare oltre gli obiettivi dei piani di classificazione perché cercavano anche di quantificare l’incremento di costo di produzione passando da una forma più semplice a una più complicata. Non hanno avuto molto successo, per vari motivi. Adesso per lo stesso scopo si usa l’intelligenza artificiale. Una caratteristica comune a questi codici è che il codice assegnato a una forma ha un significato ben preciso e sono strutturati in modo che a una forma può essere attribuito solo un codice ben preciso, perciò facendo riferimento alla figura nella slide, ogni forma è posizionabile in una sola casella. Non esiste un sistema di classificazione delle forme universalmente accettato. I raggruppamenti in figura sono stati scelti per identificare le potenzialità dei processi produttivi. I componenti con sezione trasversale uniforme, complessità spaziale = 0, sono bidimensionali, tutti gli altri sono tridimensionali. Al crescere della complessità spaziale, la definizione della forma richiede ulteriori parametri geometrici; si può dire che la forma contiene una maggior quantità di informazioni. Un piccolo incremento di contenuto informativo può, tuttavia avere conseguenze significative dal punto di vista produttivo. Per esempio spostandosi dalla forma piena R1 alla forma cava T1 si aggiunge una sola dimensione, il diametro del foro, questo tuttavia esclude immediatamente alcune tecniche produttive o richiede ulteriori operazioni in altre. In contrapposizione, aggiungere un terzo diametro esterno al componente rotazionale R1 richiede lo stesso incremento informativo senza imporre limitazioni nella scelta del processo produttivo. Vedremo che le limitazioni sulla forma sono rese più stringenti dalle proprietà del materiale e dalle interazioni con l'attrezzatura. Perciò è importante non finalizzare la configurazione del componente troppo presto in fase di progettazione, altrimenti potremmo escludere i processi produttivi più economici. In ogni processo produttivo sarà presentata una tabella che mostra quali forme sono più adatte per essere ottenute con quella tecnica. Lo scopo è, generalmente, quello di produrre un componente net shape, cioè pronto per l'assemblaggio; se questo non fosse possibile, un componente near net shape richiederà solo piccole lavorazioni di finitura, di solito mediante asportazione di truciolo. Le dimensioni dei prodotti dell'industria manifatturiera possono essere estremamente variabili, passando dallo spillo alla superpetroliera. Anche i singoli componenti possono avere dimensioni molto variabili e non tutte le tecniche produttive sono adatte per produrli tutti. Spesso le dimensioni minime sono fissate da leggi naturali, mentre la dimensione massima può essere stabilita anche dalla disponibilità di apparecchiature adatte. Tutti questi vincoli devono essere presi in considerazione durante il progetto. Tolleranze dimensionali L'artigiano realizzava ogni singolo prodotto in modo che ogni componente fosse fatto su misura per adattarsi all'assemblaggio. Quando si rendeva necessario riparare o sostituire un componente, doveva essere fatto su misura ed adattato. La produzione in serie richiede la possibilità di sostituire i componenti e, a causa di questo, le dimensioni devono essere controllate. Dall'inizio del XIX secolo il controllo dimensionale è diventato via via più stringente con l'ausilio di tecniche di misura che si sono evolute rapidamente. Tecniche produttive diverse hanno differenti capacità di realizzare componenti di dimensioni controllate. Anche se le dimensioni devono essere controllate, non è possibile né necessario realizzare componenti aventi dimensioni esatte. Di conseguenza i limiti massimo e minimo delle dimensioni vengono specificati avendo in mente due obiettivi: (1) i limiti devono essere abbastanza stretti per consentire il corretto funzionamento dell'assemblaggio, anche quando vengono utilizzati pezzi di ricambio. (2) I limiti devono essere più ampi possibile, garantendo la funzionalità, perché quando sono troppo stretti richiedono tecniche produttive o sequenze di processo costose. La singola causa più importante di eccessivi costi di produzione è la richiesta di limiti dimensionali inutilmente stretti. Tolleranze strette spesso vengono specificate perfino quando non ci sono esigenze di accoppiamento. Affinché un componente funzioni regolarmente una volta accoppiato ad altri, è spesso necessario fissare ulteriori restrizioni, oltre alle tolleranze dimensionali, sulla posizione delle caratteristiche geometriche e su proprietà geometriche quali la concentricità, la planarità, il parallelismo e la perpendicolarità. Il geometric dimensioning and tolerancing (GD&T) fornisce chiare indicazioni sugli obiettivi del progetto che a loro volta aiutano nella scelta delle tecniche produttive più appropriate. Fornisce anche indicazioni sulla modalità di analisi del componente. Raggiunge questi obiettivi con l'uso di simboli rappresentativi degli attributi geometrici, incorporati nella normativa ISO. Il perno ha un diametro di 15 più o meno 0,05 mm ed è lungo 50 mm. Queste informazioni non ci dicono nulla sulla sua forma, potrebbe essere fortemente curvato. Sappiamo che deve essere accoppiato con un altro componente perciò si specifica che l'errore di linearità non dovrebbe superare 0,2 millimetri su tutta la lunghezza. Sotto le specifiche sul diametro viene indicata una linea diritta, il simbolo della rettilineità, con la lettera greca indicante che l'asse dell'oggetto deve trovarsi all'interno di 0,2 mm. L'albero deve essere posizionato in un contenitore cilindrico avente diametro di 15,05 più 0,20 mm. È evidente che se l'albero si trova nella condizione di minimo materiale, cioè il diametro è di 14,95 mm, sarà accoppiabile anche se la curvatura è di 0,30 mm, perciò abbiamo guadagnato 0,10 millimetri di ulteriore tolleranza. Questo esempio mostra uno dei vantaggi della GD&T: vengono considerati buoni componenti perfettamente funzionali ma che sarebbero stati scartati se fosse stato usato il modo tradizionale di fissare dimensioni e tolleranze. Tolleranze di forma La figura mostra quali tipi di tolleranze di forma sono previste dalla normativa con la relativa simbologia. Esistono tolleranze di forma di tipo individuale e tolleranze che invece necessitano di un riferimento. Col termine “total runout” si intende l'eccentricità valutata su tutta la lunghezza. La figura mostra che la circolarità viene studiata sulla singola sezione trasversale di una superficie di rivoluzione oppure di una sfera. La tolleranza di circolarità viene espressa mediante due cerchi concentrici che individuano l'intervallo di tolleranza ammissibile. La cilindricità, d'altra parte, si applica contemporaneamente a tutte le sezioni trasversali di una superficie cilindrica. La superficie deve giacere tra due superfici cilindriche che individuano l'intervallo di tolleranza. La posizione dell'asse del cilindro di diametro nominale viene stabilita per mezzo di una tecnica di tipo minimi quadrati. Spesso si assume di poter valutare circolarità e cilindricità mediante misure diametrali, per esempio tramite un micrometro. Una misura diametrale è quello che dice il termine, cioè misura il diametro. Non controlla la forma della superficie che invece rappresenta lo scopo delle valutazioni di rotondità e di cilindricità. Poiché le tolleranze di circolarità o di cilindricità sono la distanza radiale tra bordi concentrici, è necessario un metodo radiale per controllare la superficie. Tuttavia, ruotare un componente tra due centri non è un metodo accettabile perché in questo modo si fa riferimento ad un asse e questa tecnicamente è un altro tipo di valutazione, il controllo dell’eccentricità. Il vero controllo di circolarità e cilindricità di una superficie deve essere fatto facendo ruotare il componente mediante un mandrino di altissima precisione su una macchina specifica chiamata rotondimetro. Nelle misure di concentricità una sonda tocca la superficie e ne trascrive il profilo ingrandito su un grafico polare. Il profilo viene poi controllato sovrapponendo cerchi concentrici per verificare se rientra nei limiti di tolleranza previsti. La concentricità è la condizione nella quale gli assi di tutte le sezioni trasversali di una superficie di rivoluzione sono comuni all’asse della figura di riferimento. Poiché la posizione dell'asse di riferimento è difficile da trovare, è più semplice controllare cilindricità o eccentricità. L'eccentricità corrisponde a posizionare un solido di rivoluzione su un mandrino, per esempio quello di un tornio, e ruotare il componente attorno al suo asse centrale mentre si misura con uno strumento analogico la deviazione della sua superficie dalla rotondità perfetta. Nel caso di eccentricità circolare lo strumento analogico non viene mosso lungo l'asse del componente. Di conseguenza l'eccentricità circolare viene misurata indipendentemente in ogni sezione nella lunghezza del componente mentre il componente viene ruotato di 360°. La misura dell'eccentricità totale comporta lo spostamento dello strumento analogico nel senso della lunghezza del componente mentre questo viene ruotato, in modo da controllare le variazioni cumulative di circolarità, cilindricità, rettilineità, coassialità, angolarità, conicità e profilo. In sintesi, quando si devono effettuare misure relative a tolleranze di forma si parte dalla nuvola di punti che sono stati misurati, si individuano due superfici del tipo cercato che li contengono e si verifica che tali superfici si trovino all'interno dell'intervallo di tolleranza. (slide senza commento) Questa slide e la successiva descrivono quali siano i riferimenti e i contributi all’incertezza in alcune misure (slide senza commento) La figura mostra come si presenta la normativa relativa alle misure di circolarità e di cilindricità. A sinistra troviamo la simbologia relativa, andando verso destra vengono definiti gli intervalli di tolleranza, infine verso destra si danno indicazioni ed interpretazioni delle tolleranze stesse. La normativa indica anche la procedura di misura ed eventuali commenti relativi alla procedura stessa indicandone limiti e caratteristiche. (slide senza commento) Principi delle misure Le misure devono essere effettuate con strumenti aventi sufficiente accuratezza e precisione. Spesso, se una dimensione viene misurata più volte si ottengono valori differenti; le letture così come le variabili soggette alla misura, mostreranno sempre una certa dispersione. La dispersione può essere studiata in un grafico in cui in ascissa si mettono intervalli di misura e in ordinata il numero di eventi (grafico superiore). il valore vero, la lunghezza effettiva del tavolo, è un valore convenzionale, tanto più che nessun valore può essere perfettamente noto. Il valore vero, pur essendo convenzionale, è dedotto da misure effettuate con strumenti molto precisi In conclusione si può dire che la misura è l'assegnazione di un intervallo di valori ad una particolare proprietà fisica (chiamata misurando). Lo sviluppo della metrologia ha portato a definire in chiave statistica il valore dei misurandi, e all'introduzione del concetto di incertezza di misura. Quest'ultimo è legato al concetto di intervallo, all'interno del quale, con elevata probabilità, si trova il valore vero di una grandezza Un prerequisito importante per l’uso della distribuzione gaussiana è l’indipendenza tra loro dei dati. Spesso si dimentica questa esigenza. In ambito produttivo la si usa anche se in realtà le dimensioni dei prodotti subiscono una deriva a causa del progressivo deterioramento delle attrezzature, perciò le dimensioni NON si disporranno lungo una gaussiana L'accuratezza di uno strumento di misura esprime quanto i valori misurati con lo strumento si avvicinino al valore vero; poiché il valore vero è sconosciuto, l'errore può essere stabilito usando un riferimento o standard. La precisione è il grado di ripetibilità delle misure, ovvero il loro grado di dispersione. Nel primo caso il lanciatore di freccette è accurato e preciso. I lanci sono vicini tra loro (preciso) e vicini al centro (accurato) (La x indica la posizione media dei lanci. Questa informazione ci consente di dire che il lanciatore in (c) è accurato. Il lanciatore b è preciso perchè la dispersione tra i lanci è piccola, ma non è accurato perchè i lanci sono lontani dal centro. La distribuzione normale, nella teoria della probabilità, è spesso usata come prima approssimazione per descrivere variabili casuali a valori reali che tendono a concentrarsi attorno a un singolo valor medio. Quando dobbiamo giudicare un evento possiamo descriverlo con la distribuzione dei suoi possibili valori.... Se rappresentiamo le misure ottenute su un grafico, se il numero di misurazioni è molto grande, al limite infinito, la curva che otterremo è proprio la curva di Gauss. Questo si verifica solo se gli eventi non si influenzano l’uno con l’altro, sono mutuamente indipendenti. Questa curva ha due importanti caratteristiche: una è la media, l'altra è la dispersione dei dati. Se fosse noto il valore vero della grandezza misurata, l'accuratezza di una serie di misurazioni potrebbe essere valutata dal valore medio x. Questo è la posizione della linea centrale della campana ed è semplicemente la somma di tutti i valori misurati x divisi per il numero delle misure n (per campioni di dimensioni minori si divide per n meno 1). (slide). In figura la gaussiana superiore a destra è rappresentativa di una campagna di misure accurate, mentre la seconda campana rappresenta una campagna di misure precise. State attenti che nelle figure la linea in mezzo non è la media ma il valore vero della dimensione. Se non fosse noto, non siamo in grado di valutare l’accuratezza dello strumento Il valore della deviazione standard è una misura dell’ampiezza della campana. La formula per calcolare la deviazione standard è mostrata nella slide. L'area sotto la curva normale è una misura del numero di valori che rientrano all'interno di limiti specificati. La figura mostra che circa il 68% delle misure rientrano nell'intervallo compreso tra + e meno sigma, il 95% tra i valori più e meno 2 sigma e il 99,73% all'interno dei valori compresi tra più e meno 3 sigma. Nella pratica industriale viene considerato accettabile se l'intervallo all'interno di più e meno 3 sigma coincide con la tolleranza specificata. Questo vuol dire, comunque, che 27 misure su 10000 saranno al di fuori della zona di tolleranza e le tendenze recenti puntano a un controllo più stretto. La sensibilità di uno strumento di misura è il più piccolo intervallo che produce una variazione nell'output, è opportuno che sia elevata nel caso siano richieste misure precise (nel caso di strumenti digitali si parla anche di risoluzione). La linearità influisce sulle letture all'interno di una gamma di valori specificati. Anche se uno strumento è calibrato con uno standard ad un certo punto della gamma, la non linearità influisce sulle letture negli altri punti della gamma di misure. Il grafico di figura fa riferimento a uno strumento per la misura della pressione, ma il concetto è valido per qualsiasi strumento. La relazione vera tra grandezza in input, la pressione, e quella di output, il segnale, è la curva rossa. Quando si misura però ci si riferisce alla linea chiamata “curva caratteristica ideale”. Maggiore è la bombatura della curva rossa, maggiore è l’errore che possiamo commettere quando misuriamo. Questo è il motivo per cui la linearità è importante. Si sceglie di approssimare la curva rossa con la semiretta perchè con una relazione lineare tra input (pressione) e output (segnale) la taratura consiste nel valutare la relazione solo in 2 punti (per 2 punti passa una sola retta). Volendo fare meglio le cose, bisognerebbe approssimare la curva rossa con una spezzata, ma questa scelta implicherebbe una maggiore durata della taratura La ripetibilità determina la più alta precisione raggiungibile sotto condizioni controllate. Lo strumento deve essere in grado di eseguire misure ripetute con la stessa accuratezza con cui può essere letto. La stabilità esprime la resistenza a derive che ridurrebbero sia l’accuratezza che la precisione e che richiederebbero frequenti ricalibrature. La velocità di risposta è critica quando deve essere misurata una variabile in regime transitorio, di solito durante la produzione. La facilità di automazione è importante in molte applicazioni soprattutto adesso che si sta diffondendo l'abitudine di verificare il 100% della produzione. Letture ripetute possono essere affette da errori; gli errori sistematici sono misurabili e spesso controllabili. In aggiunta agli errori insiti nello strumento, le variazioni di temperatura sono la principale fonte di errori sistematici. Se le tolleranze sono strette la temperatura del componente da misurare deve essere uniforme e nota in modo tale da poter compensare le dilatazioni termiche. Nelle misurazioni offline è preferibile effettuare la misura in ambienti a temperatura controllata dopo aver consentito il raggiungimento di una temperatura uniforme nello strumento di misura; questo può richiedere ore o giorni. Gli errori casuali possono derivare da errori umani (letture inaccurate, eccessiva forza applicata su un calibro a contatto, inadeguato allestimento dello strumento, ecc.) e da fonti quali polvere e ruggine. Anche in questo caso un ambiente a temperatura controllata aiuta nel caso ci sia un filtraggio dell'aria e un livello controllato di umidità. Le misure vengono spesso effettuate con riferimento a una superficie che può essere un piano, un foro o un albero. Il riferimento deve essere scelto tenendo presente il metodo di produzione e di controllo. Per avere i migliori risultati, uno strumento di misura dovrebbe rispettare la legge di Abbe: la linea della scala dovrebbe coincidere con la linea di misura. Nel caso di figura, un calibro a corsoio, la distanza tra le 2 linee è pari a R. A causa dei giochi, il becco di destra si inclina dell’angolo theta determinando un errore di misura pari a epsilon, che vale circa R theta. Per ridurre tale errore perciò dobbiamo ridurre i giochi e la distanza R. Portare i giochi a 0 è difficile, possiamo pensare di usare uno strumento diverso, che soddisfi la legge di Abbe, nel quale R sia = 0 Strumenti per verifiche di conformità Questi strumenti sono usati per fare dei confronti; si assume che siano perfetti, cioè perfettamente rettilinei o piani o con angoli esattamente di 90°, ecc. Ci si fa un'idea degli scostamenti. (slide vuota) La rettilineità e la planarità vengono misurate disponendo lo strumento su punti di appoggio tali da realizzare la minima deflessione. Tali punti sono detti punti di Bessel. Qualche volta in alternativa si preferisce fare in modo che le estremità del riferimento siano orizzontali; in questo caso gli appoggi sono in corrispondenza dei punti di Airy. Calibri In questa sede il termine calibro si riferisce prima di tutto ad oggetti in acciaio indurito, carburo di tungsteno, materiale ceramico, che vengono realizzati con tolleranze molto strette. Possono essere fissi o regolabili. Una volta settato, un calibro regolabile può anche essere usato come calibro fisso. Ne esistono di vari tipi. I calibri a tampone, ad anello e a forchetta sono usati per la misura di diametri. Misurano solo lo scostamento da una posizione di riferimento. Sono strumenti manuali impiegati nelle linee di produzione per garantire che la lavorazione sia avvenuta e che sia stata eseguita in modo corretto. Differiscono fra di loro a seconda del tipo di superficie di cui devono controllare la corrispondenza a dimensioni prefissate; a tampone per fori circolari, a forchetta e ad anello per diametri esterni. Questi calibri sono dimensionati in modo che la parte passa si introduca nella zona lavorata ed, al contrario, la parte non passa non si introduca. La parte passa del calibro è il negativo della dimensione nella condizione di massimo materiale, indicando che la parte da accoppiare può essere assemblata. La parte non passa viene realizzata con la dimensione corrispondente alla condizione di minimo materiale e scarta i componenti non in tolleranza. I problemi legati all'uso di questi calibri sono tre: (1) i calibri stessi vengono realizzati con certe tolleranze, perciò provocano lo scarto di componenti buoni e fanno passare componenti che dovrebbero essere scartati. (2) In alcuni casi la decisione potrebbe essere diversa se il confronto viene fatto da differenti operatori. (3) Non forniscono informazioni sulle variazioni dimensionali all'interno dei limiti di tolleranza, perciò sono di scarsa utilità nel caso di controlli statistici della produzione. (slide vuota) Esistono calibri multipli che vengono usati per valutare l'effetto combinato di vari parametri. Esistono calibri per valutare la qualità delle filettature; in questo caso si misura la coppia necessaria per avvitare. Alcuni strumenti comprendono contatti elettrici che attivano segnali luminosi per segnalare la condizione passa e la condizione non passa. Come riferimenti a volte si usano sagome, rettilinee o curve, per verificare lo scostamento di superfici sui componenti prodotti rispetto alle sagome. Il confronto può essere fatto ad occhio nudo o ingrandendo. In un certo senso anche i piani di riscontro rientrano in questa categoria; si usano come riferimenti di altri calibri; per questo motivo i piani di riscontro vengono realizzati con materiali molto stabili, come il granito con un valore ben preciso di planarità. I comparatori misurano solo la deviazione dalla posizione 0; la posizione 0 viene fissata inizialmente come riferimento ed è scelta in modo da avere la dimensione nominale del componente. Rispetto ai calibri fissi, il grande vantaggio è l'avere un'informazione sulla distribuzione delle dimensioni all'interno di un lotto. Se la sensibilità del comparatore è sufficiente e si usa un riferimento adatto, si possono avere molte informazioni non solo sulla lunghezza e le sue variazioni da componente a componente, ma anche sull'eccentricità, sull'allineamento ecc. Il comparatore può essere di vari tipi: I comparatori analogici sono strumenti meccanici che convertono uno spostamento lineare in una rotazione, per esempio con un movimento a cremagliera, e lo amplificano mediante un treno di ingranaggi per aumentare la sensibilità dello strumento a un micron. Alcuni strumenti hanno contatti elettrici all'interno che attivano segnali luminosi rendendoli adatti ad essere usati come calibri passa- non passa. Spesso un comparatore viene fissato a un supporto su base magnetica. Strumenti di misura Passiamo agli strumenti di misura. Sul piano di riscontro possiamo usare un truschino per misurare le quote. Per avere i migliori risultati, uno strumento di misura dovrebbe rispettare la legge di Abbe: la linea della scala dovrebbe coincidere con la linea di misura. Il truschino non soddisfa questa legge. La sensibilità dei righelli graduati e dei metri a nastro è limitata dalle divisioni più piccole. Calibro a corsoio. Grazie al nonio, la sua sensibilità arriva a 0,05 mm. Per effettuare una misura col calibro a corsoio bisogna prima individuare le scale in mm, bisogna poi vedere dove si posiziona lo zero della scala secondaria, cioè del nonio, all'interno della scala principale per determinare i millimetri. Infine bisogna vedere dove una linea del nonio è allineata con una linea della scala principale; se la linea del nonio individuata è la diciassettesima, alla misura in millimetri bisogna aggiungere 17/20 di mm. Esistono calibri a corsoio nei quali il nonio viene sostituito da una sorta di comparatore e calibri a corsoio digitali. Anche il calibro a corsoio non soddisfa la legge di Abbe. Micrometro. In questo strumento lungo l'asse troviamo due scale, una dei mm ed una dei mezzi mm. Nella circonferenza ho un'ulteriore scala, il nonio, che fornisce le frazioni di mezzo millimetro. In questo modo il micrometro arriva ad una sensibilità di un centesimo di millimetro. L'impugnatura del micrometro ha una frizione per applicare sempre la stessa forza di schiacciamento. I due cilindri hanno le estremità indurite superficialmente per evitarne deformazioni. Anche i goniometri di precisione hanno il nonio. Blocchetti Johnson o piano paralleli. Sono usati per realizzare lunghezze. Possono servire per collaudare strumenti di misura o per realizzare calibri fissi ad uso comparatori e distanziatori. Vengono venduti in confezioni che consentono di realizzare impilaggi di qualsiasi dimensione mediante scivolamento e rotazione di blocchetti adiacenti. L'umidità che viene assorbita o film d'olio sulle superfici a contatto dei blocchetti hanno influenza trascurabile sullo spessore ma forniscono una adesione sufficiente da permettere di maneggiare colonne di blocchetti come se fossero un unico oggetto. Anche per separare i blocchetti è necessario uno scorrimento. I blocchetti vengono venduti con vari livelli di incertezza come si può vedere dalla figura. I blocchetti angolari vengono impilati sulla base dello stesso principio dei blocchetti piano paralleli, con la differenza che in questo caso, in funzione dell’orientamento del blocchetto, possiamo aggiungere o sottrarre angoli, come si può vedere dalla figura. Usando una barra di precisione e dei blocchetti piano paralleli, con l'ausilio di un comparatore che rilevi la posizione orizzontale del piano, possiamo effettuare lo stesso tipo di misure che con i blocchetti angolari. In alcune situazioni la luce può produrre su una superficie bande luminose e scure alternate, chiamate frange di interferenza. Una possibilità consiste nel far passare luce monocromatica attraverso fessure, ognuna delle quali diventa una sorgente di luce (figura in alto a destra). La superficie con le fessure viene chiamata reticolo di diffrazione. La sovrapposizione su uno schermo tra i fasci di luce provenienti dalle fessure produce frange di interferenza, la cui distanza dipende dalla lunghezza d’onda della luce e dalla distanza tra il piano su cui si trovano le fessure e lo schermo. Quando 2 reticoli di diffrazione vengono sovrapposti con una piccola inclinazione (figura in alto a sinistra), producono frange di interferenza, la cui posizione dipende dalla posizione relativa dei reticoli. Nella figura in alto CD è circa uguale a DE, perciò contando le frange di interferenza si può calcolare la distanza tra il vetro e la superficie sottostante. L’interferometria può essere usata anche per misurare la planarità. Il numero di frange può essere contato elettronicamente per avere una risoluzione di 5 micron. Strumenti digitali lineari possono essere usati per trasmettere impulsi per via elettronica, fotoelettrica o magnetica fino a una risoluzione di 4 micron. Strumenti digitali lineari possono essere usati x trasmettere impulsi x via elettronica, fotoelettrica o magnetica, fino a una risoluzione di 4 micron. In altre parole, si usa un allineamento di emettitori di segnale. Il segnale può essere di tipo elettronico, fotoelettrico o magnetico. Un sensore del segnale emesso scorre lungo l'allineamento e conta il numero di segnali mentre si muove. Moltiplicando il numero di segnali per la distanza tra emettitori adiacenti si ha la distanza percorsa dal sensore. Un encoder rotante a generazione di impulsi può essere usato per effettuare misure di angoli e, con un movimento a cremagliera e pignone, anche per movimenti lineari. Questi dischi possono fornire, con interfaccia appropriata, una lettura diretta oppure essere l'input per un sistema a controllo numerico. La scala grigia fornisce 2 alla n valori distinti, dove n è il numero di bit per ogni pixel. Dispositivi elettronici allo stato solido che convertono la luce in un segnale elettrico (diodi fotorivelatori e dispositivi ad accoppiamento di carica (CCD)) rilevano la presenza o assenza di luce e, disposti in una schiera lineare, offrono risoluzioni di 3 micron o meglio quando usati da soli o in telecamere. Tutti i misuratori elettronici possono essere utilizzati per misure online. I microscopi da attrezzeria sono microscopi ottici dotati di una slitta trasversale guidata da micrometri, oculare con mirino per la misura della lunghezza e goniometri per la misura di angoli. Possono essere utilizzati anche per controllare e misurare la forma dei componenti. Traduttori elettronici trasformano il movimento meccanico in un segnale elettrico. Si usano spesso i trasformatori differenziali che segnalano 0 quando il cuore mobile è esattamente centrato; l'output è proporzionale allo spostamento nelle altre posizioni. Altri sensori convertono la deflessione di una molla in un segnale elettrico mediante un ponte di Wheatstone. In seguito a deformazione, la resistenza elettrica dei fili cambia e il ponte, sbilanciato, fornisce un segnale proporzionale alla deflessione. Possono anche essere usati online. Gli strumenti pneumatici misurano la contropressione generata quando l'aria esce da un ugello e sbatte su una superficie. Lo strumento è in grado di misurare variazioni molto piccole, perciò è molto sensibile, ma è lineare solo in un ambito limitato. Col proiettore di profili è possibile misurare lunghezze ed angoli. Questa tabella ci dice quale sia la dimensione massima normalmente misurabile con alcuni degli strumenti che abbiamo visto. Più interessante è la colonna di destra che, per gli stessi strumenti, dà l'incertezza di misura. Questa è sempre espressa come somma di una costante, una frazione di micron, e un coefficiente che moltiplica la lunghezza rilevata. Perciò l'incertezza non è mai nulla e cresce con la dimensione del misurando Macchine di misura a coordinate Fino a questo momento abbiamo visto strumenti ognuno dei quali era in grado di misurare un solo o alcuni tipi di dimensioni, lunghezze, profondità, diametri, ecc. Passiamo adesso a vedere apparati capaci di misurare forme, perciò in linea di principio dovrebbero essere in grado di integrare le capacità di tutti gli strumenti visti fino a questo momento. Per questo motivo vengono chiamate "macchine" L'applicazione principale di queste macchine è l'ispezione geometrica, cioè la verifica della forma, ma viene utilizzato anche per ispezioni dimensionali o per identificazioni di geometrie incognite Esistono molti modi di valutare forme. Esistono metodi tattili, che fanno uso di tastatori che sondano la superficie (parte sinistra della figura) e metodi non tattili che possono essere acustici, magnetici ed ottici. (parte destra) Alcune tecniche sono usate normalmente in campo medico, quali la tomografia computerizzata, la risonanza magnetica e l'ecografia. Nella slide sono mostrati 2 esempi di utilizzo di onde sonore. Nel settore civile si usano i laser scanner che, rilevando nuvole di punti, permettono di realizzare rapidamente modelli di grandi superfici, quali edifici, ponti, superficie terrestre, ma hanno una risoluzione troppo bassa per le esigenze del settore metalmeccanico In ambito produttivo, per le misure geometriche si usano metodi tattili e ottici e si parla di conseguenza di macchine di misura meccaniche o ottiche. Seguirò quest'ordine nella presentazione dell'argomento. In realtà esistono anche macchine in grado di usare sia metodi tattili che ottici, come il sistema nella foto L’espressione macchine di misura è usato per indicare strutture realizzate con estrema cura per fornire supporto a trasduttori in grado di rilevare posizioni rispetto a una superficie o ad assi di riferimento Nella maggior parte dei casi le macchine di misura sono realizzate in modo da essere estremamente stabili e sono in grado di effettuare movimenti di alta precisione per misurare lungo 3 assi mutuamente perpendicolari, da qui la denominazione macchine di misura a coordinate Attrezzate con sonde molto sensibili al tocco, mosse a mano o mediante software, le macchine di misura a coordinate sono usate molto spesso per seguire superfici complesse Risoluzioni dell'ordine di 250 nanometri sono possibili sia con sensori meccanici che ottici L’output è di solito fornito in forma digitale in modo che possa essere gestito dal computer Le macchine possono essere collegate a computer per eseguire misure automaticamente Per permettere un'ottimale riuscita dell'operazione di acquisizione della nuvola di punti, la struttura meccanica di una CMM, deve possedere alcune proprietà: Rigidezza statica e dinamica della struttura. Garantire l'accessibilità a tutte le parti del pezzo attraverso sistemi di bloccaggio che permettano di angolare il modello o attraverso l'uso di sonde orientabili, cioè con angolo dello stilo variabile. Facilità di manovra. Le macchine di misura vengono suddivise in: Macchine con assi o testa guidati a mano Macchine con assi motorizzati e guidate a mano con un joystick (come in figura) Macchine con assi motorizzati e comando numerico computerizzato (modalità CNC). Caratteristica comune a tutte le macchine di misura a coordinate è che l’oggetto da misurare viene tastato punto per punto da uno stelo con punta sferica di rubino sintetico o di ceramica Ad ogni contatto di tastatura lo spostamento degli assi X, Y e Z viene rilevato. Le coordinate riferite al punto centrale della sfera del tastatore vengono poi trasmesse al computer connesso per le successive analisi Come si vede dalle figure in basso a destra, si possono montare teste con + tastatori, in funzione delle esigenze I vari costruttori di CMM hanno adottato nel tempo diverse configurazioni di struttura della macchina. struttura a mensola e a tavola fissa, tipo Cantilever; struttura a portale mobile (bridge); struttura a portale fisso e tavola mobile; struttura a braccio orizzontale mobile; struttura a colonna; struttura a braccio orizzontale mobile e tavola mobile; struttura a ponte, tipo Gantry; struttura con portale a L. (nessun commento) Per semplicità, facciamo riferimento a queste 2 configurazioni. In quella di sinistra è mostrata una macchina a sbalzo (o a mensola), nel secondo caso è illustrata una macchina a portale. I vantaggi delle macchine a mensola sono la maggiore economicità e velocità e un più agevole accesso al volume di lavoro che permette un più rapido posizionamento e rimozione del pezzo da misurare. sono macchine di misura a coordinate tipicamente a comando manuale che raccolgono punti del volume di misura attraverso una serie di assi rotanti tipicamente costituiti da tre aste collegate tra loro alle estremità da giunti che consentono movimenti rotatori, che danno origine a cinque, sei o sette gradi libertà vi è una testa di misura con un sensore tattile o ottico, alloggiato sull’estremità libera del braccio la misurazione digitale avviene tramite degli encoder, uno per ogni grado di libertà, che registrano la rotazione degli snodi del braccio e consentono di ricavare la posizione del tastatore La figura mostra i possibili gradi di libertà di un braccio articolato Una caratteristica interessante è la portabilità, cioè possono essere posizionati in vicinanza dell'oggetto da misurare Non necessitando di programmazione, è possibile l'utilizzo in modo rapido anche a personale non altamente qualificato Le accuratezze di misura ottenibili da questi sistemi sono generalmente inferiori a quelle ottenibili con le CMM cartesiane Le Macchine di Misura a scansione utilizzano tastatori analogici per la scansione continua, progettati per trasmettere al computer di sistema un flusso ininterrotto di dati Esse eccellono quindi nell'acquisizione di ingenti volumi di dati dimensionali precisi, con alti livelli di produttività e ripetibilità I tastatori elettronici per la scansione continua sono concepiti per mantenere il contatto con la superficie del pezzo da misurare Le macchine di misura viste fino a questo momento soffrono di alcune limitazioni il volume di misura, che è vincolato alla lunghezza degli assi, per le macchine cartesiane, o dei bracci meccanici, per i bracci articolati, ai quali è collegato il tastatore velocità di misura non supera i 2‐3 punti al secondo, poiché si devono muovere, automaticamente o manualmente, gli organi meccanici costituenti la CMM Limitata accuratezza nella scansione di oggetti facilmente deformabili (imbottiti, pale di ventilatore) accessibilità delle superfici per il sistema tastatore (piccoli fori o piccole cavità e interni ad elevata profondità) Il laser permette la creazione di sistemi di acquisizione tridimensionali attivi, cioè sistemi il cui funzionamento prevede la presenza di una sorgente di luce artificiale ed uno o più sensori atti a rilevare i pattern luminosi riflessi dall’oggetto La sorgente può emettere pattern luminosi di diverso tipo, scelti in funzione dell’accuratezza richiesta nell’acquisizione dei dati ed in base al tipo di analisi che deve essere eseguita sull’oggetto reale la sorgente di luce è integrata nel sensore e l'illuminazione viene opportunamente sincronizzata con la fase di acquisizione Il vantaggio principale prodotto da una sorgente luminosa controllata è la possibilità di automatizzare il processo di misura dei punti è possibile accumulare in pochi secondi migliaia di punti di misura Tali sensori non sono soggetti all'influenza di fattori ambientali come la temperatura e l'umidità La tecnologia corrente nel campo dei sensori ottici per applicazioni di metrologia dimensionale con le Macchine di Misura è del tipo a lama di luce Vengono valutati tutti insieme i punti acquisiti da un sensore bidimensionale come un CCD e per ciascuno di essi si ottengono in soluzione unica le coordinate corrispondenti al segmento illuminato. Ossia si ricavano le coordinate x, y e z di punti 2D Mentre una lampadina emette luce in tutte le direzioni, Il laser ha il vantaggio di rendere quasi nullo l’angolo di divergenza, permettendo di generare lame di spessore limitato e costante su grandi profondità di proiezione Essendo la luce laser monocromatica, è possibile montare davanti al CCD un filtro passa-banda centrato sulla frequenza di emissione del laser rendendo il sensore robusto rispetto a sorgenti di luce parassite, cioè non risente della presenza di altre sorgenti di luce Come avviene per la maggior parte dei sensori a triangolazione, per far sì che il piano individuato dalla lama laser sia perfettamente a fuoco su tutta la profondità di misura è opportuno che l’obiettivo sia angolato rispetto al piano del CCD (come mostrato nello schema di figura 1) Ci sono sensori in grado di acquisire una nube di punti 3D relativa ad una porzione di superficie. Infatti proiettando più strisce di luce contemporaneamente, ovvero un volume di luce, si possono ottenere le posizioni di un numero di punti della superficie sufficienti a descriverla Questi sensori, in virtù della loro elevata produttività metrologica, sono particolarmente adatti alla verifica dimensionale di superfici complesse di grande estensione Un metodo alternativo a quello basato sulla proiezione di lame di luce laser è quello che utilizza sensori a luce strutturata Grazie ad un idoneo proiettore le lame di luce sono prodotte tutte insieme e l'immagine della superficie investita da questo pattern luminoso è acquisita con una telecamera digitale I sistemi di questo tipo proiettano più pattern in sequenza secondo un opportuno codice (Gray code), ossia raddoppiando progressivamente il numero di strisce verticale a partire da una sola transizione bianco/nero, fino ad arrivare alla massima frequenza di alternanza nero/bianco Più transizioni si riescono ad avere nell'immagine e più fine sarà il campionamento spaziale della superficie, con un conseguente aumento della risoluzione Ogni transizione da bianco a nero all'interno del pattern svolge il compito della lama di luce laser visto in precedenza Inoltre l'immagine prodotta dal proiettore (es. una sequenza di strisce verticali alternate bianche e nere) vista dalla telecamera sarà ancora una sequenza di strisce se la proiezione avviene su un piano, mentre queste tenderanno a distorcersi diversamente a seconda della forma della superficie sottostante Le nubi di punti prodotte nel processo di scansione possono essere scaricate su di una stazione CAD/CAM, dove vengono confrontate con le geometrie nominali del pezzo, oppure elaborate direttamente dalla Macchina di Misura usando un software che confronta i dati CAD con i dati del pezzo e genera analisi grafiche tempestive ed esaurienti Esistono software che creano un collegamento bidirezionale tra la Macchina di Misura e il software del CAD e guidano il processo di scansione del pezzo usando il modello CAD stesso Le nubi di punti prodotte nel processo di scansione possono essere scaricate su di una stazione CAD/CAM, dove vengono confrontate con le geometrie nominali del pezzo, oppure elaborate direttamente dalla Macchina di Misura usando un software che confronta i dati CAD con i dati del pezzo e genera analisi grafiche tempestive ed esaurienti La verifica delle prestazioni della macchina viene effettuata mediante la misura di una serie di elementi campione di lunghezza, in pratica sono sostituti del metro campione: 5 elementi misurati 3 volte in 7 posizioni diverse del volume di lavoro della macchina. Si applica a misurazioni di dimensioni Tra i campioni usati per caratterizzare le CMM sono i blocchetti piano paralleli o i calibri a passi Nelle foto, alcuni strumenti usati x calibrare le CMM, alcuni commercializzati, alcuni fatti in casa È prevista anche una prova valutativa delle prestazioni del tastatore su una sfera tarata per errore di forma, in alto a sinistra La norma definisce i test di accettazione e di verifica periodica, utili rispettivamente per accettare un sistema di misura all'acquisto o dopo un intervento manutentivo, verificando le prestazioni in conformità alle dichiarazioni del costruttore e per controllare periodicamente le prestazioni del sistema di misura, anche ai fini dell'assicurazione qualità Taratura: confronto tra le prestazioni della macchina e le dimensioni di un campione che viene spostato nel volume di lavoro Verifica periodica: obbligatoria x i laboratori certificati, controlla l’entità del peggioramento delle prestazioni nel tempo La compatibilità è legata alla possibilità di esprimere le prestazioni usando formule convenzionali, valuta gli errori sistematici, che possono essere compensati via software Introducendo le macchine di misura a coordinate ho detto che la loro applicazione principale è l'ispezione geometrica, cioè la verifica della forma. Questa loro capacità le rende idonee per realizzare il primo passo del reverse engineering (3D scan nella figura) A inizio corso si è parlato di concurrent engineering, in contrapposizione all'industrializzazione sequenziale. L'engineering o industrializzazione è l'insieme di attività comprese tra quando si inizia a pensare al nuovo prodotto e la sua realizzazione Pensate al processo di reverse engineering come la strategia di “iniziare dalla fine”, per scoprire la fonte di un risultato già esistente, o meglio di un oggetto già funzionante Il reverse engineering è, infatti, un processo di analisi fisica dettagliata di un oggetto, in grado di comprenderlo fino al punto di riuscire a modificarlo e addirittura replicarlo, migliorandone alcune funzionalità Topografia superficiale Poche superfici sono lisce e piatte (oppure hanno una forma geometricamente perfetta). Al microscopio le superfici mostrano ondulazione e rugosità. Il profilo della superficie può essere misurato e registrato. Per una più agevole visualizzazione, le registrazioni vengono visualizzate con un'amplificazione maggiore lungo la scala verticale. Questa scelta determina un’immagine distorta del profilo con picchi aguzzi e cavità ripide; in realtà hanno pendenze piccole, tipicamente variabili tra i 5 e i 20° di inclinazione. Il segnale ottenuto dal profilometro può essere trattato elettronicamente oppure, dopo averlo reso digitale in un computer, derivare valori per una caratterizzazione quantitativa del profilo. Tra i parametri per valutare la rugosità quelli usati più spesso sono: (1) Rt è la massima altezza della rugosità (la differenza di quota tra il picco più alto e l’avvallamento più profondo). E’ importante quando la rugosità deve essere rimossa, per esempio tramite lucidatura. Spesso un valore più significativo è ottenuto prendendo in considerazione la differenza di quota tra la media dei 5 picchi più alti e quella dei 5 avvallamenti più profondi all'interno della lunghezza di misura, detta Rz. (2) Si traccia una linea tale per cui l'area compresa tra la linea stessa e la parte del profilo al di sotto di essa è divisa a metà tra pieni e vuoti. La deviazione media del profilo da tale linea è detta Ra. (3) Spesso al posto di Ra si preferisce usare Rq sia nella pratica che nella teoria delle superfici a contatto. Le formule di Ra e Rq sono mostrate nella slide. Rq è in stretta relazione con Ra come si può vedere anche dalla tabella. (4) L’ asimmetria esprime la distribuzione dei picchi della rugosità ed è una misura quantitativa della pienezza della superficie. La curva di Abbott mostra l'area disponibile in grado di sopportare carichi quando vengano eseguiti dei tagli a vari livelli partendo dalla sommità del profilo. Una unità di misura adeguata è il micron. I dettagli della rugosità superficiale sono sovrapposti a un andamento della superficie su scala maggiore che può essere periodico o non periodico, detto ondulazione. Nelle misure di rugosità l'ondulazione è di solito filtrata mediante processamento elettronico del segnale, sebbene l'ondulazione ammissibile talvolta venga specificata e misurata in millimetri quando sia funzionalmente importante. Nei disegni, i limiti di rugosità vengono indicati mediante un simbolo che assomiglia a una radice quadrata sopra la linea alla quale devono essere applicati tali limiti. Un unico numero di rugosità indica un limite superiore, sotto il quale qualsiasi valore di rugosità è accettabile; se è richiesto anche un valore minimo di rugosità vengono indicati due limiti. L'ondulazione massima, quando viene ritenuta importante, viene indicata con un numero sopra la linea orizzontale del simbolo. Le superfici di solito hanno un andamento topografico caratteristico dipendente dalla lavorazione di finitura. La direzionalità caratteristica viene indicata con un simbolo al di sotto del simbolo della rugosità. È opportuno chiarire che gli stessi valori di Ra e Rq possono essere ottenuti da superfici aventi profili molto diversi e che avvallamenti molto localizzati alterano molto poco i valori medi. Di conseguenza, le medie sono inadeguate per descrivere le superfici al fine di specifiche applicazioni. In generale, si può dire che non sia ancora stato identificato un modo soddisfacente per caratterizzare le superfici. Nonostante questo, il processo manifatturiero deve essere in grado di realizzare una superficie adatta per la funzione del componente e vari termini quantitativi o descrittivi possono, e a volte sono usati, per descrivere la finitura richiesta. Lo strumento di misura più usato per valutare la rugosità superficiale è basato sul principio del giradischi. Un braccio con un supporto di riferimento è mosso lungo la superficie, con uno stilo che segue i più minuscoli dettagli della superficie. È possibile registrare il profilo della superficie e calcolare varie caratteristiche di rugosità. Gli strumenti portatili forniscono in output pochi parametri, tipicamente Ra o Rq direttamente. Nel caso di uso in stabilimento spesso sono disponibili raccolte di campioni di superfici standard con indicato i valori di rugosità per ogni campione. Facendo scorrere un'unghia lungo il campione e il componente prodotto, un operatore esperto può derivare stime piuttosto attendibili di Rq. Altri strumenti di analisi della rugosità sono basati sulla misura della capacità elettrica, dell'interferenza ottica, della diffrazione e della caduta di pressione. In alcuni casi gli attributi superficiali sono difficilmente quantificabili. In questo caso si usano campioni di confronto scelti in modo da rappresentare situazioni in cui la superficie sia accettabile o da scartare. Finitura superficiale e tolleranze Poche superfici sono lisce e piatte (oppure hanno una forma geometricamente perfetta). La vera forma della superficie, cioè il suo andamento a livello microscopico, è importante in fase di assemblaggio, verniciature, incollaggi, ecc. Le superfici, più spesso profili estratti dalle superfici, possono essere analizzate a diversi livelli. A scala di indagine macroscopica, quella che si valuta con le macchine di misura a coordinate, abbiamo a che fare con la forma vera e propria. Al microscopio le superfici mostrano ondulazione (2) e rugosità (3) i dettagli della rugosità superficiale sono sovrapposti a un andamento della superficie su scala maggiore che può essere periodico o non periodico, detto ondulazione Vale la pena sottolineare che, anche quando gli andamenti di ondulazione e rugosità non siano periodici, nelle operazioni di filtraggio si assume sempre che rugosità e ondulazione siano date da combinazioni lineari di sinusoidi, perchè il filtraggio di sinusoidi è molto semplice, mediante un operatore chiamato trasformata di Fourier È un’operazione simile a quella che si effettua quando si studi un fenomeno usando la distribuzione gaussiana anche se non ci sarebbero i presupposti. Far finta che un profilo sia esprimibile come sovrapposizione di sinusoidi è utile per poter usare la trasformata di Fourier Il profilo della superficie può essere misurato e registrato. Esistono molte categorie di strumenti usate per analizzare ondulazione e soprattutto rugosità, ma qui parlerò solo del rugosimetro perchè gli altri strumenti sono normalmente usati nei laboratori che fanno ricerca Il rugosimetro è basato sul principio del giradischi. Una punta, detta stilo, percorre un tratto rettilineo della superficie seguendo picchi e avallamenti Per una più agevole visualizzazione, le registrazioni fatte col rugosimetro vengono visualizzate con un'amplificazione maggiore lungo la scala verticale Questa scelta determina un’immagine distorta del profilo con picchi aguzzi e cavità ripide; in realtà hanno pendenze piccole, tipicamente variabili tra i 5 e i 20° di inclinazione Lo stesso strumento spesso può essere usato per misurare rugosità e ondulazione, basta cambiare la scala di indagine. Poiché supponiamo che il profilo tracciato sia dato dalla sovrapposizione di sinusoidi, per la misura di rugosità si prendono in considerazione solo le sinusoidi con lunghezza d’onda molto piccola, mentre per l’ondulazione si usano sinusoidi di lunghezza d’onda intermedia. Questa operazione si chiama filtraggio, è il vantaggio dato dall’usare la trasformata di Fourier Il segnale ottenuto dal rugosimetro può essere usato, dopo averlo reso digitale in un computer, per derivare valori per una caratterizzazione quantitativa del profilo Quando lo strumento è usato per misurare l’ondulazione viene chiamato profilometro Tra i parametri per valutare la rugosità quelli usati più spesso sono: (1) Rt è la massima altezza della rugosità (la differenza di quota tra il picco più alto e l’avvallamento più profondo). In pratica, guardate anche la figura, si deriva l'andamento della curva media del profilo, cioè si deriva l'ondulazione del profilo, e rispetto a questa si valutano il picco e l'avvallamento. Questa operazione di derivazione della curva media e di riferire a questa picchi e avvallamenti viene chiamata filtraggio, nel senso che è come se la curva media fosse stata trasformata in una linea orizzontale Rt è importante quando le asperità devono essere rimosse, per esempio tramite lucidatura Spesso un valore più significativo è ottenuto prendendo in considerazione la differenza di quota tra la media dei 5 picchi più alti e quella dei 5 avvallamenti più profondi all'interno della lunghezza di misura, detta Rz (2) Nel calcolo di Ra si parte ancora dal filtraggio per escludere l'ondulazione, perciò il profilo analizzato si scosta dall’essere una linea orizzontale solo a causa della rugosità, poi si traccia un'altra linea orizzontale che è rappresenta la quota media dei punti del profilo. Attenzione, per il filtraggio ho fatto riferimento alle aree, la posizione di questa seconda linea è determinata dalla quota media dei punti del profilo, perciò sto considerando il "perimetro" del profilo. La distanza tra le 2 linee orizzontali è l'Ra. (3) Spesso al posto di Ra si preferisce usare Rq sia nella pratica che nella teoria delle superfici a contatto Le formule di Ra e Rq sono mostrate nella slide. Rq è in stretta relazione con Ra come si può vedere anche dalla tabella Nell'esempio presentato nella slide si può assumere che Rt sia circa uguale a 10 Ra, perciò circa 32 micron. Per una tolleranza ammessa di 25 micron la rugosità Ra non dovrebbe superare gli 0,8 micron. Rsk è la misura della simmetria del profilo rispetto alla linea media. Questo parametro identifica le differenze di simmetria su profili aventi il medesimo valore di Ra o Rq. (4) Diversamente da Ra ed Rq, l’asimmetria (parte a destra della figura) non prende in considerazione il perimetro ma l'area del profilo ed è una misura quantitativa della pienezza della superficie Se l'asimmetria è < 0 nel profilo prevale la pienezza (figura in alto), cioè al disopra della linea media le aree piene prevalgono su quelle vuote. Se > 0 prevalgono i vuoti (figura in basso). Questa informazione è importante quando la superficie deve sopportare carichi. Collegata all'asimmetria è la curva di Abbott, che mostra l'area disponibile in grado di sopportare carichi quando vengano eseguiti dei tagli a vari livelli partendo dalla sommità del profilo Una unità di misura adeguata per le misure di rugosità è il micron Abbiamo visto che i dettagli della rugosità superficiale sono sovrapposti a un andamento della superficie su scala maggiore che può essere periodico o non periodico, detto ondulazione Vale la pena sottolineare che, anche quando gli andamenti di ondulazione e rugosità non siano periodici, nelle operazioni di filtraggio si assume sempre che rugosità e ondulazione siano date da sovrapposizioni di sinusoidi, perchè il filtraggio di sinusoidi è molto semplice L'ondulazione ammissibile talvolta viene specificata e misurata in millimetri quando sia funzionalmente importante Nei disegni, i limiti di rugosità vengono indicati mediante un simbolo che assomiglia a una radice quadrata sopra la linea alla quale devono essere applicati tali limiti Un unico numero di rugosità indica un limite superiore, sotto il quale qualsiasi valore di rugosità è accettabile; se è richiesto anche un valore minimo di rugosità vengono indicati due limiti L'ondulazione massima, quando viene ritenuta importante, viene indicata con un numero sopra la linea orizzontale del simbolo Le superfici di solito hanno un andamento topografico caratteristico dipendente dalla lavorazione di finitura La direzionalità caratteristica viene indicata con un simbolo al di sotto del simbolo della rugosità È opportuno chiarire che gli stessi valori di Ra e Rq possono essere ottenuti da superfici aventi profili molto diversi e che avvallamenti molto localizzati alterano molto poco i valori medi Spesso è comunque sufficiente valutare una superficie tramite Ra o Rq perchè, se il processo produttivo per ottenere la superficie è sempre lo stesso, l'andamento della superficie rimane sempre simile a se stesso e la valutazione di Ra risulta sufficiente per caratterizzarla. In altre situzioni Ra e Rq sono inadeguate per descrivere le superfici al fine di specifiche applicazioni. In generale, si può dire che non sia ancora stato identificato un modo soddisfacente per caratterizzare le superfici Lo strumento di misura più usato per valutare la rugosità superficiale è basato sul principio del giradischi Un braccio con un supporto di riferimento è mosso lungo la superficie, con uno stilo che segue i più minuscoli dettagli della superficie È possibile registrare il profilo della superficie e calcolare varie caratteristiche di rugosità. Gli strumenti portatili forniscono in output pochi parametri, tipicamente Ra o Rq Nel caso di uso in stabilimento spesso sono disponibili raccolte di campioni di superfici standard con indicato i valori di rugosità per ogni campione Esiste una relazione stretta tra rugosità e tolleranze dimensionali Una buona regola pratica è che Rt, ed eventualmente l'ondulazione, se specificata, dovrebbero essere tra un terzo e metà dell’intervallo di tolleranza, a meno che non sia precisato un montaggio per interferenza e la rugosità superficiale possa essere in parte ridotta nell'operazione di montaggio La relazione tra Rt ed Ra dipende dall'andamento del profilo che, a sua volta, dipende dalla lavorazione che l'ha realizzato Come ho detto, in questo caso bisogna soddisfare una tolleranza molto stretta, perciò abbiamo dovuto usare una operazione di finitura come rettifica (grinding, ground = rettificato) o lappatura (lap, lapped = lappato). Assumiamo che in questo caso sia R t/Ra = 10 Si è appena detto che esiste una relazione stretta tra rugosità e tolleranze dimensionali Tale relazione esiste per ogni processo produttivo La finitura superficiale e le tolleranze normalmente ottenibili da un processo sono indicate nel grafico con linee continue adiacenti al nome del processo stesso Le potenzialità di alcuni processi si sovrappongono; per esempio, la colata in conchiglia (shell) nelle situazioni migliori può competere con la colata in gesso (plaster), ma non può mai raggiungere il livello delle migliori colate in gesso Quando le gamme sono comuni a varie tecniche produttive, il nome di queste tecniche è separato da virgole; per esempio, le stesse tolleranze e finiture superficiali possono essere ottenute nella foratura con trapano (drill) o nella punzonatura di un foro (punch) I componenti in plastica di solito hanno una finitura superficiale che dipende dal livello di finitura delle attrezzature con cui sono stati realizzati, di conseguenza essi possono essere prodotti con qualsiasi livello di finitura (sebbene i componenti rinforzati con fibre possano essere piuttosto ruvidi). Le tolleranze indicate in figura fanno riferimento a una dimensione di 25 mm Per dimensioni maggiori o più piccole i limiti di tolleranza non necessariamente variano in modo proporzionale In ambito produttivo è opportuno sfruttare le raccomandazioni pubblicate da varie associazioni industriali o da singole aziende La rugosità superficiale è indicata in termini di Ra In molte applicazioni anche la giacitura della superficie è importante e per un certo valore di Ra tecniche produttive differenti possono fornire finiture molto diverse Si tende a credere che i costi aumentino esponenzialmente andando verso tolleranze più strette e migliori finiture superficiali. Questo è vero solo se tali tolleranze vengono ottenute mediante sequenze di processi che coinvolgono processi e macchine utensili caratterizzate da capacità limitate. Ci sono, tuttavia, processi e macchine utensili in grado di raggiungere accuratezza e finitura superficiale di livello superiore; di conseguenza prodotti di qualità superiore possono essere ottenuti con incrementi limitati di costo e, se l'utilizzo lo giustifica, certamente con maggiore competitività. Rimane valida la regola fondamentale che un progettista consapevole dei costi di produzione debba specificare le tolleranze più ampie possibili e le peggiori finiture compatibili con la funzione del prodotto da realizzare. Le tolleranze specificate dovrebbero, se possibile, essere interne ai range ottenibile col processo produttivo pensato in modo da evitare operazioni di finitura distinte. Da quanto detto si deduce che i limiti indicati in figura non sono rigidi. Infatti vari settori industriali hanno risposto alla pressione competitiva riducendo gli intervalli di tolleranza, migliorando la qualità superficiale e in generale aumentando la qualità dei prodotti senza necessariamente aumentare il costo dei prodotti stessi. Permanent mold = Stampo permanente Plaster = gesso => colata in stampo in gesso Shell = conchiglia => colata in conchiglia Sand cast = colata in sabbia o terra Al die cast = Pressocolata di alluminio (Cu => pressocolata di leghe di rame, Zn => pressocolata di leghe di zinco) Investment cast = colata a cera persa o microfusione Hot roll, extrude, forge = Laminazione, estrusione, forgiatura a caldo Cold extrude, roll = estrusione, laminazione a freddo Cold draw = trafilatura a freddo Precision blank = Tranciatura di precisione Punch = punzone => punzonatura Drill = Trapano => foratura con trapano Finish mill = fresatura di finitura Rough turn = tornitura di sgrossatura Finish turn, bore = tornitura di finitura Broach, ream = brocciatura, alesatura Prove meccaniche Attributi funzionali dei manufatti Le proprietà che attribuiscono un valore ai manufatti sono chiamate attributi funzionali. Questi sono importanti non solo in ambito progettuale, perché gli attributi funzionali spesso impongono la scelta dei materiali o almeno restringono le possibili alternative che possono essere prese in considerazione. Questo fatto ha immediate ripercussioni sul processo produttivo per varie ragioni: (1) i processi ottimali sono differenti per differenti materiali, (2) i processi possono essere orientati a modificare le proprietà dei materiali, spesso influenzandone la struttura o lo stato tensionale. La sequenza dei processi manifatturieri deve essere scelta per ogni materiale in modo che le proprietà finali vengano ottenute al minimo costo. (3) L'accettabilità del prodotto finale viene valutata sulla base di prove nelle quali si controlla che il materiale soddisfi le specifiche. Le stesse prove possono essere usate durante il processo produttivo per garantire che le proprietà del prodotto finale soddisfino le specifiche. Queste prove sono spesso affiancate da prove tecnologiche, cioè prove che simulano le condizioni imposte sul materiale durante la lavorazione. Le prove tecnologiche saranno descritte quando si parlerà degli specifici processi produttivi. Una proprietà spesso importante nei prodotti è la loro capacità di sopportare i carichi in esercizio. I carichi o forze possono essere di molti tipi; di conseguenza esistono molte tecniche di prova progettate con lo scopo specifico di riprodurre le modalità di carico in servizio. In molti casi il carico è statico, cioè costante e stazionario, e molte prove vengono condotte a velocità così basse che l'applicazione del carico può essere considerata statica. Qualche volta le prove sono finalizzate a valutare il comportamento ad alta temperatura oppure a velocità controllate di applicazione del carico. Le prove possono differire anche in funzione del materiale da verificare. I risultati delle prove sono influenzati dalla modalità di prova stessa; perciò la prova deve essere condotta conformemente a quanto stabilito dalle norme. Nel corso delle prove meccaniche, per deformare il materiale, viene applicata una forza. Il rapporto tra forza e area resistente fornisce la pressione media all'interfaccia. L'integrale del prodotto tra la forza applicata e lo spostamento dell'attrezzatura fornisce il lavoro speso nel corso della prova. Una conseguenza è la variazione di energia nel materiale deformato. E’ sbagliato dire che un corpo contiene una certa quantità di lavoro, il lavoro compiuto determina uno scambio di energia. Possiamo dire che il lavoro è una grandezza di scambio, come il calore. Nella prova di trazione il provino subisce un allungamento. L'unità di misura dell'allungamento è il metro. Il rapporto tra l'allungamento e la lunghezza iniziale del provino fornisce la deformazione che è una grandezza adimensionale. Contrariamente a quello che si potrebbe pensare, il punto di massima resistenza del materiale non si trova nel punto di ordinata massima della curva bensì in corrispondenza della rottura. La prova di trazione permette di stabilire quanto un materiale sia resistente, rigido, duttile e tenace. La resistenza di un materiale è in relazione con la tensione che il materiale è in grado di sopportare. Un materiale è tanto più rigido quanto più alto è il rapporto tensione su deformazione quando il materiale ha comportamento elastico, cioè quanto più è alto il suo modulo elastico. La duttilità deve essere messa in relazione con la deformazione plastica che il materiale accumula prima di rompersi, perciò un materiale è tanto più duttile quanto maggiore è tale deformazione prima della rottura. La tenacità invece è data dal prodotto tensione per deformazione, in pratica è l'area sotto la curva tensione deformazione. Nella pratica la duttilità del materiale viene valutata prendendo in considerazione l'allungamento del provino fino alla rottura oppure mediante la riduzione percentuale dell'area resistente in corrispondenza della strizione. La riduzione d’area e, perciò anche la tenacità, sono molto influenzate dalle condizioni del materiale, perciò raramente vengono fornite tra le caratteristiche specifiche dei materiali. Tuttavia queste grandezze sono molto importanti sia in servizio che durante il processo produttivo; di conseguenza spesso si fanno sforzi notevoli per aumentare la duttilità. 1. Ci si deve aspettare che nel materiale si formino cavità prima se sono presenti punti deboli; di conseguenza uno dei principali obiettivi nel controllo dei processi produttivi è quello di garantire l'assenza di difetti interni. Le inclusioni possono provocare tali difetti, perciò la pulizia è un primo requisito per migliorare la duttilità. La resistenza non è necessariamente influenzata, ma la deformazione dopo strizione (che determina la massima riduzione d’area) aumenta. Materiali molto duttili puliti possono arrivare ad avere una sezione trasversale molto piccola prima di rompersi. 2. Se le tensioni triassiali di trazione sono responsabili della comparsa di vuoti nei punti deboli, la frattura può essere ritardata sovrapponendo tensioni di compressione. Se le tre tensioni sono uguali, si parla di pressione idrostatica. Questo obiettivo può essere raggiunto, per esempio, conducendo la prova in un fluido pressurizzato. La sovrapposizione di pressione idrostatica neutralizza le tensioni di trazione e la deformazione proseguirà fino a valori più alti. Più in generale questa osservazione porta a un principio molto importante, applicabile sia in servizio che durante la produzione: la frattura in un componente può essere ritardata o evitata se prevale uno stato tensionale di compressione sufficientemente alto. È stato appena detto che i difetti interni o inclusioni riducono la duttilità dei metalli. Ancora più dannosi sono i difetti superficiali, in particolare gli intagli. Gli intagli provocano concentrazione della tensione, cioè un aumento locale della tensione stessa. Il fattore di concentrazione della tensione, detto K, è il rapporto tra la tensione massima e la tensione che si avrebbe in un corpo senza intaglio e può raggiungere valori molto alti quando il raggio dell'intaglio è piccolo. È stato detto che la tenacità di un materiale è data dal prodotto tensione per deformazione, cioè è l'energia accumulata nel materiale prima di rompersi. Esistono delle prove, dette di resilienza, che misurano l'energia accumulata in un materiale prima di rompersi a seguito di un urto. La differenza tra tenacità e resilienza sta nel fatto che nella misura di tenacità l'energia viene accumulata lentamente mentre nella misura di resilienza l'energia viene ceduta al materiale a grande velocità. Prova di compressione I materiali fragili, come la ghisa grigia e il calcestruzzo, sono deboli in trazione ma forti in compressione Le lavorazioni per deformazione plastica che vedremo quasi sempre sollecitano il materiale a compressione perchè a compressione i materiali possono subire deformazioni molto maggiori Alcune strutture sono sollecitate solo a compressione In tutti questi casi si preferisce , o si deve, testare il materiale a compressione invece che a trazione L'apparecchio di prova spesso è una pressa o una macchina di prova universale, questa volta allestita in modo che il provino venga schiacciato tra due piatti induriti paralleli e ben lubrificati La forza è maggiore che in trazione perchè la sezione resistente aumenta durante la prova. Gli allungamenti elastici nella pressa e nell'attrezzatura provocherebbero errori significativi, perciò devono essere esclusi misurando la deformazione. La deformazione del campione è misurata tra le due piastre parallele Ovviamente la forza registrata aumenta anche a causa dell’incrudimento, se è presente Come nella prova di trazione, si applica il principio della costanza del volume: l'area della sezione trasversale del provino (perpendicolare al suo asse) deve aumentare per compensare la riduzione di altezza L'area della sezione trasversale istantanea A può essere calcolata a partire dall'altezza istantanea h ottenuta dal trasduttore di spostamento, noto il volume del provino In ogni punto della corsa la pressione sugli stampi p è data da forza diviso per area; se l'effetto dell'attrito è trascurabile lo stato tensionale è di compressione monoassiale e la pressione sugli stampi è uguale alla tensione di compressione e uniforme in tutta la superficie di contatto La deformazione nominale di compressione è data dalla terza formula nella slide Si noti che la deformazione di compressione calcolata in questo modo è diversa dall’equivalente deformazione di trazione. La formula è stata modificata perchè si vuole che la deformazione sia > 0. In futuro ci sarà qualche situazione in cui, anche in compressione, si userà la formula che conoscete Dai valori calcolati di forza e spostamento può essere costruita la curva tensione-deformazione che, per i materiali duttili, è circa sovrapponibile a quella ottenuta da una prova di trazione, ma in compressione la frattura si verifica per valori maggiori di deformazione In genere i componenti meccanici o le strutture subiscono deformazioni abbastanza piccole, perciò la tensione di compressione corrispondente a specifici valori piccoli di deformazione (per esempio 0,2%) vengono presi come riferimento in fase di progetto. In seguito ad ulteriore compressione il provino può acquisire una forma a botte (barreling). Lo stato tensionale cambia e la tensione non è più uguale alla pressione applicata dagli stampi. Poiché le tensioni di compressione impediscono la rottura del materiale si potrebbe pensare che la deformazione possa continuare in modo indefinito. In realtà è ancora possibile il manifestarsi di fratture. 1. Il barreling in presenza di attrito genera tensioni di trazione sulla superficie e si formano fratture se il materiale ha una duttilità limitata. 2. presto o tardi la duttilità di molti materiali si esaurisce e si forma una frattura spesso su una diagonale a 45 gradi. Anche in questo caso la frattura può essere ritardata imponendo una pressione idrostatica. 3. I materiali fragili si rompono all'improvviso al raggiungere di un valore critico di tensione. In conclusione, la prova di compressione al pari di quella di trazione, consente di ottenere la curva tensione deformazione per un materiale Se il materiale si comporta allo stesso modo sottoposto ai 2 tipi di sollecitazione, si ottiene la stessa curva, a parte il fatto che con la prova di compressione la curva è più estesa Anche la prova di torsione, che non vediamo, permette di ottenere la curva tensione deformazione Durezza La resistenza di un materiale alla deformazione può essere valutata mediante una indentazione. Il campione deve essere sufficientemente grande per mantenere la deformazione molto localizzata, in modo che l’indentatore spinga il materiale spostato tutto attorno all'impronta ma non deformi l'intero spessore del campione. Un grande vantaggio di questa prova è che l'indentazione, locale, relativamente piccola, può essere accettata anche su un componente prodotto; in questo modo non si ha l'esigenza di distruggere un componente per eseguire una prova. Le prove di durezza sono standardizzate, sia per quanto riguarda la forma e le dimensioni del penetratore che l'entità della forza applicata e la velocità di applicazione del carico. Nella prova di durezza Brinell l'indentatore è una sfera di acciaio o, per materiali più duri, in carburo di tungsteno. Dopo aver applicato il carico si misura il diametro medio dell'impronta. La forza divisa per l'area della superficie dell'indentazione fornisce il numero di durezza Brinell (HB) che è ancora valutato nella vecchia unità di misura metrica kg/mm2. Poiché l'area della superficie non è una funzione lineare del diametro dell'impronta sono disponibili tabelle per semplificare il calcolo. Impronte molto profonde andrebbero evitate; per questo motivo il carico viene ridotto nel caso di materiali teneri per mantenere il diametro dell'impronta tra 2,5 mm e 4,75 mm. Le impronte prodotte da una piramide rimangono geometricamente simili indipendentemente dal carico, perciò possono essere usate per un'ampia gamma di durezze. Nella prova di durezza Vickers il numero di durezza (HV, kg/mm2) viene anche in questo caso ottenuto dividendo la forza per l'area della superficie, calcolata dalla diagonale dell'impronta. Misure di microdurezza sono usate per valutare variazioni di durezza localizzate all'interno di un corpo e vicino ai bordi. I carichi devono essere molto piccoli, perciò la superficie deve essere preparata con una lucidatura, facendo attenzione a non causare deformazioni locali che aumenterebbero la durezza. Nella prova di durezza Knoop la durezza viene calcolata a partire dalla diagonale lunga dell'impronta. A causa del ritorno elastico dopo l'applicazione di piccoli carichi, la durezza (HK, in kg/mm2) non è una funzione lineare della diagonale. La prova di durezza Rockwell è la più diffusa grazie alla facilità di utilizzo della macchina di prova. Il penetratore è una sfera o un cono in diamante. Dopo aver precaricato per minimizzare gli effetti della rugosità superficiale si applica il carico principale. La macchina misura automaticamente la profondità dell'impronta e fornisce l’output su una scala a scelta tra cui quelle A, B e C sono le più usate (HRA, HRB, HRC). È possibile convertire le misure in una scala di durezza nelle altre, soprattutto nel caso di materiali poco incrudenti come gli acciai trattati termicamente. Tabelle di conversione sono disponibili nei manuali. La durezza di componenti di grandi dimensioni può essere misurata con lo scleroscopio, uno strumento portatile che mette in relazione la durezza con il rimbalzo di un piccolo peso fatto cadere da un’altezza standard; al peso è attaccato un diamante che funge da penetratore. La durezza dei materiali fragili viene misurata in una prova comparativa di scalfittura e viene riportata sulla scala Mohs che è basata sulla resistenza alla scalfittura di minerali selezionati. Poiché gli elastomeri riprendono la forma originaria dopo lo scarico, la loro durezza viene misurata con un durometro mediante indentazione sotto un carico ben preciso. La figura di sinistra mostra come si presentano i bordi di una indentatura nel caso di metalli allo stato ricotto e allo stato incrudito. La figura di destra invece mette in evidenza l'entità della deformazione plastica rispetto alla profondità dell'impronta in una prova di durezza e fa capire perchè l'impronta debba essere ricavata lontano dai bordi del materiale. Il materiale che circonda l'impronta viene sollecitato e deformato plasticamente. Deformandosi contrasta la formazione dell'impronta che perciò risulta di minore grandezza. Se mancasse questo effetto di contenimento, l'impronta sarebbe più grande e la durezza del materiale sembrerebbe minore La durezza dei materiali è circa uguale al triplo della loro tensione massima a rottura, solo se entrambe vengono misurate nella stessa unità. Questa relazione funziona meglio nel caso di materiali poco incrudenti, come gli acciai trattati termicamente, e funziona meglio nel caso di durezza Vickers rispetto alla durezza Brinell. i valori di tensione che si ricavano dalla prova di durezza risultano maggiori rispetto a quelli ottenuti nella prova di trazione o di compressione perchè nella prova di durezza il materiale deve spostare lateralmente il materiale circostante per potersi deformare. Questa esigenza è assente nella prova di compressione, nella quale tutto il materiale è soggetto a compressione monoassiale e viene schiacciato verso il basso Proprietà ad alta temperatura Molti componenti sono destinati a lavorare ad alte temperature. È possibile definire una scala di temperature per ogni materiale che è molto più significativa di ogni altra scala. Questa è chiamata scala delle temperature omologhe, indicando che viene costruita a partire da punti specifici per ogni materiale. Uno dei punti che la determinano e lo zero assoluto, l'altro è la temperatura di fusione Tm espressa in Kelvin. Al di sotto di 0,5 T m la maggior parte dei metalli e molti polimeri termoplastici mostrano un comportamento che possiamo definire a freddo; la resistenza è alta e la duttilità relativamente bassa. Oltre 0.5 Tm i materiali mostrano proprietà tipiche del comportamento a caldo; la resistenza è piuttosto bassa e la duttilità alta. È possibile imporre deformazioni elevate dopo la strizione e la strizione si distribuisce su tutta la lunghezza del provino. Bisogna sottolineare che 0.5 Tm è una linea di confine molto approssimativa; l'aggiunta di elementi in lega nei metalli e variazioni nella struttura dei polimeri possono spostare il manifestarsi del comportamento a caldo verso temperature molto maggiori. In ogni caso, in alcune plastiche la transizione verso il comportamento a caldo può verificarsi al di sotto della temperatura ambiente mentre temperature molto alte sono necessarie per indurre duttilità nei ceramici. È importante osservare che la deformazione nella gamma di temperature a caldo comporta un sostanziale riorganizzazione degli atomi nei metalli o delle molecole nei polimeri. Questi processi richiedono tempo, perciò le proprietà sono anche funzione della velocità di applicazione del carico o, più correttamente, della velocità di deformazione imposta, che nella prova di trazione è data dalla formula nella slide. In questa formula v è la velocità di spostamento della traversa e l è la lunghezza istantanea del materiale che viene deformato, cioè la lunghezza del provino prima della strizione ma la lunghezza della porzione soggetta a strizione dopo la strizione. Basse velocità di deformazione danno più tempo per la riorganizzazione di atomi o molecole, perciò le tensioni sono minori e la duttilità maggiore. Questo vuol dire anche che in un arco di tempo lungo ad elevata temperatura si può verificare deformazione anche se il carico applicato è piuttosto basso. In questo caso diciamo che il materiale è soggetto a creep. Questo aspetto è molto importante se la deformazione è inaccettabile. L'allungamento di una pala di turbina danneggerebbe un motore a reazione e si sono verificate situazioni di prodotti che hanno smesso di funzionare dopo un certo tempo a causa della distorsione di un componente in plastica. Nella tipica prova di creep un provino di trazione viene sottoposto a un carico costante nel tempo a temperatura costante. In una prima fase si verifica un allungamento rapido (creep primario), seguito da una deformazione più lenta a velocità costante (creep secondario) e alla fine quando si verifica un danno strutturale, il creep accelera e il componente si rompe (creep terziario). Quando si desidera che un componente debba durare a lungo, il progetto è basato sul calcolo della tensione che produce una velocità di creep lineare dell’1% per 10.000 ore (per esempio nei componenti dei motori a reazione) o per 100.000 ore (per esempio nei componenti delle turbine a vapore). Per accelerare le prove e ottenere dati di progetto per i componenti che saranno soggetti a creep ma non devono rompersi, le prove vengono condotte con valori di tensione maggiore fino alla rottura. Nelle prove a rottura il tempo necessario per rompere il componente viene determinato a vari livelli di tensione. Il manifestarsi del comportamento a caldo nelle plastiche viene spesso determinato con una prova di flessione. La temperatura alla quale una barra lunga 125 mm si piega di 0,25 millimetri sotto una tensione di 0,44 o 1,82 MPa viene detta temperatura di deflessione a caldo o temperatura di deflessione sotto carico. Tensioni residue Le strutture e i componenti sono progettati per resistere alle tensioni imposte dall'esterno. Queste non sono necessariamente le uniche tensioni agenti. Come conseguenza di operazioni produttive si possono avere anche delle tensioni chiamate tensioni residue all'interno del componente o della struttura. Queste tensioni hanno origine dal fatto che il materiale risulta deformato elasticamente. Un aspetto che deve essere chiaro è che, mancando forze esterne che agiscono sul materiale, l'integrale delle tensioni agenti sul materiale vale 0, cioè le tensioni di trazione e di compressione sono fra loro in equilibrio Per capire come queste tensioni interne possano prodursi, consideriamo un componente cilindrico. Supponiamo che sia stato ottenuto unendo un tubo più corto e un'anima più lunga a contatto con il tubo. Supponiamo anche che durante la giunzione l'anima sia stata compressa alla lunghezza del tubo, assumendo che la deformazione sia solo elastica. Al completamento della giunzione è stata tolta la compressione sull'anima e il cilindro ha assunto una nuova lunghezza. L'anima tenderebbe ad allungarsi per tornare alla lunghezza originaria mentre il tubo tenderebbe ad accorciarsi per tornare alla lunghezza iniziale. Le forze che si scambiano i due elementi devono raggiungere un equilibrio. Poiché anima e tubo sono dello stesso materiale e sono stati scelti per avere la stessa area della sezione trasversale, il cilindro raggiungerà una lunghezza intermedia fra le lunghezze originarie del tubo e dell'anima. Se il comportamento elastico del materiale è esattamente lo stesso in trazione e in compressione, la struttura assume una lunghezza che è la media aritmetica tra le lunghezze di partenza. Il tubo risulterà allungato rispetto alla dimensione originaria e sarà perciò soggetto a tensioni residue o interne di trazione, mentre l'anima risulterà compressa è soggetta a tensioni di compressione. Le distribuzioni di tensioni residue sono sempre equilibrate perché non ci sono carichi esterni agenti Anche se il cilindro risulta esente da difetti, la sua superficie è in trazione. Quando il componente viene sollecitato a trazione, la tensione applicata si somma alla tensione residua superficiale. Questo potrebbe risultare pericoloso per un materiale di duttilità limitata perché ogni difetto superficiale presente potrebbe propagarsi molto più facilmente e il cilindro potrebbe rompersi in trazione o, nel caso di sollecitazione a fatica, per valori inferiori del carico rispetto a un cilindro privo di tensioni intern