IMPIANTI MECCANICI PDF - Analisi, Classificazione e Progettazione
Document Details
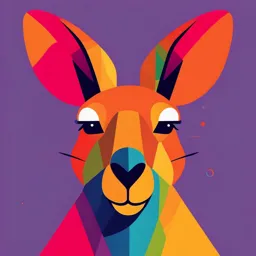
Uploaded by DevoutMookaite6525
Tags
Summary
Il documento tratta i principi dell'ingegneria meccanica come: classificazione degli impianti industriali, i fattori di produzione, le fasi di progettazione, e i criteri per la pianificazione dei layout. Si esamina la produzione su commessa e a magazzino, l'analisi dei costi, e l’importanza di metodi quali di un sistema di produzione.
Full Transcript
IMPIANTI MECCANICI Impianto industriale: un insieme di elementi di qualsiasi specie, integrati ed interagenti, aventi come obiettivo la produzione di beni o servizi. Prodotto finito: Beni e Servizi I Beni sono le cose che soddisfano i bisogni e che hanno un valore economico. Si dividono in Beni St...
IMPIANTI MECCANICI Impianto industriale: un insieme di elementi di qualsiasi specie, integrati ed interagenti, aventi come obiettivo la produzione di beni o servizi. Prodotto finito: Beni e Servizi I Beni sono le cose che soddisfano i bisogni e che hanno un valore economico. Si dividono in Beni Strumentali e Beni di Consumo. I Servizi (beni di servizio) sono le attività che soddisfano i bisogni. 𝐼𝑀𝑃𝐼𝐴𝑁𝑇𝑂 𝐼𝑁𝐷𝑈𝑆𝑇𝑅𝐼𝐴𝐿𝐸= 𝐼𝑀𝑃𝐼𝐴𝑁𝑇𝑂 𝑇𝐸𝐶𝑁𝑂𝐿𝑂𝐺𝐼𝐶𝑂 + 𝑰𝑴𝑷𝑰𝑨𝑵𝑻𝑰 𝑫𝑰 𝑺𝑬𝑹𝑽𝑰𝒁𝑰𝑶 - L’Impianto Tecnologico è l’insieme di macchine che consentono la trasformazione vera e propria delle materie prime in prodotto finito. - Gli Impianti di Servizio supportano l’impianto tecnologico nel suo funzionamento. Sono inseriti negli impianti industriali, ma non partecipano direttamente alla produzione. Possono essere classificati sotto diversi profili di analisi: entità servita, tipo di servizio e funzione svolta. Classificazione degli impianti produttivi: - Dimensione: segue i seguenti parametri: numero di addetti, capitale investito, fatturato annuo, capacità produttiva. - ATECO: è la classificazione delle attività economiche adottata dall’Istat per finalità statistiche cioè per la produzione e la diOusione di dati statistici uOiciali. - Composizione organica del capitale R: rapporto tra capitale fisso determinato dall’insieme dei mezzi di produzione ed il capitale variabile(lavoro). R= capitale fisso/ capitale variabile (capitale fisso/ numero di addetti). - Natura del bene (del prodotto finito). - Modo di rispondere alla domanda (tipologia della domanda): Produzione su commessa e Produzione a magazzino. Produzione su commessa (l’attività produttiva viene intrapresa sulla base degli ordini dei clienti): o Singola: Serie di ordini diversi per singoli prodotti o piccoli lotti estremamente diOerenziati che richiedono: progettazione prodotto e definizione ciclo di produzione. o Ripetitiva: gamma di prodotti di caratteristiche definite e dedicate per clienti stabili o gamma di prodotti a catalogo, su ordine, da parte di una clientela vasta. I progetti e cicli di produzione sono definiti. Produzione a magazzino (l’attività produttiva viene eOettuata prima di avere ricevuto gli ordini dei clienti e quindi sono necessari magazzini per collocare i prodotti finiti) Rischi associati: o Produzione su commessa: rischio di non riuscire a fornire al cliente il prodotto finito nei tempi previsti e ai costi pattuiti. o Produzione a magazzino: rischio di non riuscire a vendere il prodotto finito. - Modo di realizzare il prodotto: Produzioni per parti (manifatturiera): fase di fabbricazione dei componenti e una di montaggio degli stessi per ottenere il prodotto finito. Nel prodotto finito sono identificabili i materiali e i componenti di partenza. Produzione di processo: le materie prime subiscono trasformazioni chimico-fisiche, a causa delle quali il prodotto finale non è più possibile trovare tracce evidenti dei materiali di partenza. - Modalità di realizzazione del volume di produzione (ritmo produttivo): Produzione continua: l’impianto funziona continuamente producendo sempre lo stesso prodotto. Volume di produzione nell’unità di tempo molto elevato, i cicli restano costanti per periodi notevolmente estesi. Produzione intermittente a lotti: l’azienda produce diversi tipi di prodotti e li produce “per lotti”. Volume di produzione più modesto. Produzione unitaria: Volume di produzione basso. - Classificazione a tre assi (Modello di Brandolese): - Classificazione di Wortmann: - Tipologia del ciclo tecnologico: Monolinea Convergenti Divergenti Pianificazione e realizzazione di un sistema di produzione: 1) Studio di fattibilità: è un insieme organico di valutazioni tecniche ed economiche, dirette a verificare la convenienza dell’investimento. o Fase 1: ricerche di mercato e studio del prodotto. o Fase 2: scelta del ciclo produttivo C. o Fase 3: definizione dei servizi S. o Fase 4: scelta della potenzialità produttiva ottimale Q sulla base del confronto costo/prezzi di vendita e valutazione della redditività economica dell’investimento impiantistico. Possibili destinatari dello studio di fattibilità: - Imprenditore - Dirigenti e manager aziendali - Banche/Istituzioni finanziarie - Istituzioni pubbliche - Potenziali clienti e fornitori - Dipendenti Fase 1: Circa il 75% delle idee iniziali viene eliminato quasi subito attraverso una analisi qualitativa, tramiti semplici domande o con il metodo del punteggio. Obiettivi dell’impresa: - Profitti adeguati. - Tasso di espansione adeguato. - Prodotti congruenti con l’immagine della società. Prodotto non accettabile: se si verifica una o più delle seguenti ipotesi: - Non sono prevedibili profitti. - Prodotto incompatibile con altri obiettivi. - Investimenti troppo elevati - Competenze manageriali o tecniche superiori a quelle disponibili in azienda Un’azienda ha costantemente bisogno di immettere sul mercato prodotti nuovi e7o diversificare, rinnovare quelli esistenti. Ciclo di vita: - Introduzione: crescita lenta. - Crescita: aumento veloce delle vendite e del fatturato - Declino: diminuzione vendite e fatturato. Fase 2: Scelta del ciclo produttivo C: - Verifica della esistenza di tecnologie idonee alla fabbricazione del prodotto. - Scelta del ciclo tecnologico più adatto. Grado di flessibilità ed elasticità del processo: misura con la quale si ritiene che il processo produttivo debba rispondere prontamente alle variazioni qualitative e quantitative senza sensibili aumenti del costo di produzione. Fase 3: Principali scelte progettuali in un impianto: - Progettazione ex novo - Ampiamenti o adeguamenti della capacità produttiva - Riconversioni - Modifiche o ristrutturazioni - Manutenzioni e rinnovi 2) Progettazione completa: o Scelta dell’ubicazione. o Studio del lay-out generale. o Progetto del lay-out dettagliato. o Progettazione esecutiva. 3) Realizzazione del progetto: o Determinazione dei tempi e metodi di realizzazione dell’impianto. o Sviluppo e controllo delle varie fasi di realizzazione. Classificazione dei costi di produzione: - In base alla natura di origine - In base alle modalità di attribuzione all’oggetto/obbiettivo di costo: o Costi diretti: di diretta imputazione all’oggetto. o Costi indiretti: comuni alla fabbricazione di più prodotti. Il prodotto o l’attività per la quale un costo è sostenuto è definito obiettivo o destinazione di costo. La definizione di costo diretto o di costo indiretto ha un significato relativo, in quanto dipende dall’oggetto o obiettivo di costo di volta in volta considerato. - In base al volume di produzione dell’impianto: o Costi variabili: variano al variare del volume di produzione. o Costi fissi: sono costi che l’impresa sostiene per il solo fatto di esistere, indipendentemente dal volume di produzione. - In base al periodo di riferimento: o Costi di impianto: costituito dalla somma di tutti i costi e quindi del capitale di cui si deve disporre per dare inizio all’attività. Comprende vari costi tra cui: Costo degli interessi passivi: costi proporzionali al tempo intercorrente tra l’erogazione delle quote di capitale e l’istante in cui l’impianto Costo del capitale circolante: corrisponde al valore monetario delle seguenti voci: materie prime ed accessorie (A) materiali in lavorazione (B) prodotti finiti non ancora venduti (C) crediti dei clienti (D) capitale in cassa per piccole spese (E) Capitale necessario per avviare la produzione e indispensabile per consentire la normale gestione dell’impianto. o Costo di esercizio: somma di tutti i costi da aOrontare in un dato periodo per fare funzionare e gestire l’impianto. Analisi dei costi di produzione: Richiami di matematica finanziaria: Interesse (I): compenso pagato per l’uso di un bene Tasso di interesse (i): rapporto tra la somma pagata per l’uso (I) e la quantità presa in prestito (P), in un certo periodo di tempo, generalmente un anno: i = I / P - Interesse attivo o passivo: a seconda che si tratti di un credito o di un debito monetario. - Interesse semplice o composto. Interesse semplice: Interesse composto: La valutazione degli interessi avviene in base al flusso finanziario che si prevede possa prodursi durante la vita utile dell’investimento. Principali parametri di valutazione degli investimenti industriali: - Flusso di cassa (cash-flow): sta ad indicare le variazioni in positivo o in negativo della liquidità per eOetto della gestione, con riferimento a un determinato periodo di tempo. - Valore attuale netto (VAN): Il VAN rappresenta il valore attualizzato dei flussi di cassa netti nell’intero periodo n di durata dell’investimento. Se all’anno n : VAN = 0, significa che l’operazione servirà a restituire in n anni il capitale investito e gli interessi al tasso i fissato. Se all’anno n : VAN > 0, significa che l’operazione di investimento darà una certa utilità economica. Tra due investimenti A e B risulterà più conveniente l’investimento con VAN maggiore. - Tasso di rendimento interno (TRI o IRR): rappresenta il tasso di interesse (i*) per il quale si annulla il valore del VAN al termine del periodo n di vita dell’investimento. Tanto più il valore di i* è elevato, quanto più l’investimento è positivo. IRR è misura della rischiosità dell’investimento, tanto maggiore è il livello di accettabilità del progetto tanto maggiore è IRR. - Periodo di recupero del capitale (PBP): calcola il tempo necessario a recuperare il capitale investito secondo la relazione: Misura la rapidità di rientro del capitale e quindi privilegia la liquidità ed evidenzia il rischio fra le varie alternative. Scelta dell’ubicazione di un impianto industriale: La scelta relativa all’ubicazione di un impianto industriale è una delle fasi più importanti della pianificazione strategica di un’azienda. Duplice scopo: - Individuare il luogo nel quale collocare un sistema produttivo - Definire le attività industriali più adatte Fattori che possono influenzare la scelta: - Fattori fondamentali: per qualsiasi tipo di sistema produttivo - Fattori secondari o accessori: solo per alcune tipologie di industrie - Fattori speciali: per singoli tipi di aziende Fattori che intervengono nella scelta: - Pianificazione territoriale: definiscono zone di insediamento industriale - Costi delle aree fabbricabili e costi per la realizzazione dei fabbricati - Struttura del mercato: influenza i costi di distribuzione del prodotto - Materie prime: sia per il loro costo sia per la loro reperibilità - Costo dei trasporti - Manodopera - Energia - Impatto ambientale La dislocazione dell’impianto dipende dal tipo di processo produttivo: - Processo con perdita di peso o di volume ridotto: dislocazione indiOerente - Processo con perdita di peso o di volume della materia prima: dislocazione vicino alla fonte Scelta e acquisto del terreno: - Scegliere una superficie maggiore rispetto alla superficie minima richiesta dall’impatto - Forma: lotto terreno rettangolare con rapporto 2:1 - Verificare l’esistenza di servitù e vincoli - Scelta della zona in cui edificare Metodi scelta dell’ubicazione di un impianto industriale: - Metodo del punteggio: o Elencare le ubicazioni prese in considerazione (j=1,2…n) o Elencare i fattori ritenuti importanti (i=1,2…n) o Assegnare un peso pi(%) a ciascuno degli m fattori indicante la sua influenza sulla scelta della località o Assegnare una valutazione numerica Vij alla ubicazione j in relazione al fattore i o Calcolare i punteggi parziali tramite il prodotto (pi Vij) del peso per la valutazione numerica o Determinale il punteggio complessivo per ogni ubicazione: o Scegliere l’ubicazione con il massimo punteggio complessivo. Metodo veloce e di facile applicazione, permette di identificare rapidamente le soluzioni palesemente insuOicienti. - Metodo dei costi: valutazione approssimativa fatta sui costi di investimento e sui costi annui di esercizio. - Metodo in base al criterio di minimizzazione dei costi di trasporto: Approvvigionamento di acqua per uso civile e industriale Fonti di approvvigionamento: - Prelievo diretto da acquedotti pubblici - Derivazione da acque superficiali prelievo da falde sotterrane Derivazione da acquedotto: occorre prevedere un allacciamento del tipo schematizzato. La società provvede ad installare una valvola dentro un pozzetto esterno al recinto dello stabilimento, regolandola e piombandola in relazione alla portata e alla pressione richieste. In un pozzetto interno alla recinzione viene sistemato un contatore del tipo a mulinello o del tipo a turbina (per portate inferiori). Derivazione da acque superficiali: limitata nei casi in cui gli ingenti consumi d’acqua richiesta rendono impraticabile qualsiasi alternativa. - Acque marine: il prelievo avviene tramite condotte di cemento armato ad una distanza opportuna dalla riva. All’arrivo nella stazione di pompaggio l’acqua va filtrata tramite griglie fisse e mobili ed accumulata in vasche di accumulo alimentare tramite un sistema di paratoie. - Acque da lago: le opere di presa vanno poste in profondità per far fronte a variazioni del livello del lago, ma comunque ad una distanza dal fondo tale da evitare: o Richiami di vegetazione e torbidità o Escursioni notevoli di temperatura Acque dolci superficiali (fiumi e canali): la soglia di presa deve risultare più elevata rispetto al letto del fiume per evitare il prelievo di fanghi, sabbie e ghiaie che intaserebbero rapidamente il canale di derivazione. Nel caso in cui il livello subisce variazioni notevoli, oltre al canale ed alla paratoia si realizza anche una diga per assicurare una certa costanza di livello in corrispondenza del punto di presa. Definire le caratteristiche del canale di derivazione: noti la portata Q e la velocità v, si ricava la sezione A = Q / v e si impone che tale sezione oOra la minima resistenza al moto del liquido Estrazioni di acque profonde: - Le falde freatiche sono caratterizzate da acque fluenti a pelo libero attraverso uno strato di materiale poroso su fondo impermeabile. Si trovano solitamente ad una profondità abbastanza ridotta e la captazione delle acque avviene da un pozzo attraverso un sistema di pompaggio. - Le farde artesiane: costituite da acque fluenti in pressione tra due strati impermeabili. La captazione può avvenire senza bisogno di un sistema di pompaggio ma sfruttando il carico della falda stessa. Pozzi freatici: - Livello statico del pozzo H: quota del pelo libero quando il pozzo non viene utilizzato - Livello dinamico del pozzo h(Q): quota del pelo libero dell’acqua quando dal pozzo viene prelevata acqua. - Linea piezometrica: linea che divide la zona prosciugata da quella in cui c’è ancora acqua. Il pozzo crea un campo di moto radiale e una depressione piezometrica che viene chiamata cono di influenza. Il raggio di influenza R di un pozzo può essere definito come la distanza fino alla quale si risente in modo apprezzabile della depressione piezometrica provocata da un pozzo di pompaggio. Pozzi artesiani: La realizzazione di un pozzo: si prevedono indagini preliminari per l’ubicazione e la scelta del tipo di opera, poi si ha la perforazione del pozzo, il completamento del pozzo e il suo utilizzo. È suddivisibile in due fasi: - La frantumazione del terreno tramite utensile - L’asportazione dei detriti prodotti. Può essere fatta in maniera discontinua (perforazione a secco) oppure in maniera continua durante la perforazione (perforazione ad umido). Le perforazioni a secco sono (pozzi a percussione a secco con tubazioni di lavoro, a percussione a secco con infissione a pressione di colonna di rivestimento definitiva, pozzi a raggiera) mentre le perforazioni a umido sono (perforazione a rotazione: circolazione diretta, inversa o inversa con aria) Classificazione in funzione del movimento dell’utensile: - A rotazione: la perforazione viene eseguita per mezzo di un utensile sottoposto ad un peso appropriato che, ruotando sul fondo del foro, frantuma la formazione in detriti. Si può perforare qualsiasi tipo di terreno e la profondità di perforazione ed il diametro dei fori dipendono dalla potenza e dal tipo d’impatto. La perforazione a rotazione, rispetto a come circola il fluido, può essere di due tipi: o Circolazione diretta: fluido è immesso nelle aste di perforazione e ritorna in superficie attraverso lo spazio foro-aste. o Circolazione inversa: l’opposto di sopra. - A percussione: idoneo per formazioni con ghiaia, sabbia, tutti i terreni fino a rocce di media resistenza. L’utensile di perforazione viene spinto nel terreno o per caduta dello stesso strumento o per infissione per mezzo di una mazza battente. Accumula di acqua per uso industriale L’acqua all’interno degli stabilimenti industriali può essere impiegata per uso: - Industriale - Potabile - Antincendio È bene che le reti di distribuzione rimangano distinte perché: - Si possono conseguire dei risparmi di esercizio - La portata dell’acquedotto può essere insuOiciente - Si possono avere problemi di contaminazione L’acqua industriale è destinata ai seguenti impieghi: - Mezzo di raOreddamento nei processi di lavorazione - Materia prima nelle lavorazioni - Mezzo di lavaggio o solvente - Transfer termico e produzione vapore - RaOrescamento aira ambiente In genere si utilizza la soluzione con serbatoio per ragioni di sicurezza (servizi di antincendio) e per la possibilità di sopperire a eventuali picchi di richiesta non previsti. Sistemi di accumulo: la capacità dei serbatoi di accumulo deve essere tale da assicurare l’acqua corrente durante i periodi di punta oppure deve consentire di alimentare le utenze per un periodo di tempo prestabilito, anche in mancanza di alimentazione del serbatoio. Possono essere: - Serbatoi di accumulo o di compenso (aperti a pressione atm): Necessari se i consumi di acqua sono variabili. Per svincolare la portata erogata dalla pompa Qp, dalla richiesta di portata del circuito Qtot, è necessario installare un serbatoio di accumulo. Tramite un serbatoio di accumulo è infatti possibile far funzionare il gruppo di pompaggio in condizioni di portata costante e quindi in condizioni di massimo rendimento, mentre il serbatoio è in grado di fronteggiare i picchi ed i cali di richiesta rispetto a tale portata, svuotandosi e riempendosi. I serbatoi sopraelevati garantiscono il conseguimento dei più alti livelli di aOidabilità nella fornitura del servizio idrico. Costituiscono non solo una riserva di acqua ma anche una riserva di energia potenziale pronta all’uso. I serbatoi di accumulo interrati o seminterrati vengono installati quando l’installazione di serbatoi sopraelevati diventa troppo costosa nel caso in cui la pressione in mandata richiesta diventa troppo elevata. Sono dotati di un apposito sistema di pompaggio per l’alimentazione delle utenze dello stabilimento. I serbatoi di accumulo metallici fuori terra sono la soluzione più economica, lo schema impiantistico è simile a quello dei serbatoi interrati ed è prevista la presenza di un serpentino di riscaldamento per prevenire le gelate. - Sistemi di accumulo pressurizzati (Autoclave): Nei palazzi, anche quelli di altezza minore, gli ultimi piani potrebbero ricevere una pressione insuOiciente per il corretto funzionamento di alcuni apparecchi e un flusso di acqua limitato e instabile. Per ovviare a questi inconvenienti si utilizzano impianti in grado di incrementare la pressione dell’acqua: l’autoclave. È costituito da: o Un serbatoio di accumulo per immagazzinare l’acqua o Una pompa elettrica o Un contenitore a pressione in cui è presente una camera d’aria, chiamato polmone o Un pressostato, un interruttore in grado di accendere la pompa in funzione della pressione dell’acqua L’acqua ricevuto dall’acquedotto viene spinta nel polmone per azione della pompa. In questo contenitore è presente una camera d’aria in modo che allo spegnimento della pompa l’acqua viene mantenuta in pressione. Il pressostato avvia la pompa quando la pressione è inferiore ad un limite minimo e la spegne al raggiungimento del valore massimo prefissato. Il polmone agisce quindi come un accumulatore e consente alla pompa di dilatare il periodo di funzionamento su un periodo di tempo maggiore, evitando un continuo susseguirsi di accensioni e spegnimenti che causano usura. Quindi l’impiego dell’autoclave consente di avere una pressione in rete approssimativamente costante e limita i frequenti interventi della pompa. Il Piping o rete di distribuzione: insieme degli elementi che servono per convogliare e trasferire un fluido, in condizioni di sicurezza, da un punto di prelievo ad uno di utilizzo in un impianto, regolandone e controllandone le condizioni di flusso. La progettazione deve essere improntata a criteri di: economicità, risparmio energetico, sicurezza, espandibilità, manutenibilità e aOidabilità. Gli elementi costituivi di una rete di piping sono: - Tubi - Giunti, raccordi, guarnizioni - Organi di intercettazione e regolazione - Accessori Le reti di distribuzione devono essere visibili, ispezionabili e chiaramente individuabili. Non devono: - Essere di intralcio - Essere danneggiate dal transito dei veicoli - Occupare spazi di lavoro - Costituire barriera alla luce naturale Elementi che contraddistinguono una tubazione: - Diametro nominale - Diametro interno - Spessore - Lunghezza - Tipo di costruzione - Materiale Pressione nominale (PN): pressione convenzionale utilizzata per la scelta della tubazione idonea alle condizioni di esercizio, è legata allo spessore della tubazione. PN con riferimento ai tubi di acciaio definite nella: - Condizione I: fluidi non pericolosi in relazione alle caratteristiche chimiche (T minore/uguale a 120°C) -> Pressione di esercizio pari al 100% PN - Condizione II: fluidi non pericolosi con T = 120÷300 °C o fluidi pericolosi a temperatura non superiore a 120°C -> Pressione di esercizio pari al 80% PN - Condizione III: fluidi non pericolosi con T= 300÷400 °C o fluidi MOLTO pericolosi -> Pressione di esercizio pari al 64% PN Se lo spessore minimo è minore di quello scelto dato dalla diOerenza tra (diametro esterno – diametro interno) abbiamo terminato il dimensionamento, altrimenti si deve prendere un diametro esterno maggiore. I giunti sono elementi per eOettuare il collegamento di testa tra i vari tratti del tubo o tra tubo e altri elementi piping. I raccordi sono elementi filettati o lisci utilizzati per la realizzazione all’interno di una tubazione : - Curve e gomiti - Diramazioni o unioni adi tubi - Variazioni di diametro - Chiusura Le guarnizioni servono per assicurare la tenuta tra due flange. Se p x t< 5000 -> guarnizioni non metalliche Se p x t> 5000 -> guarnizioni metalliche. Le valvole costituiscono gli elementi di intercettazione e di regolazione del flusso dei fluidi all’interno delle reti di trasferimento I filtri hanno lo scopo di rimuovere le impurità ed i detriti all’interno delle tubazioni indirizzando il flusso del fluido verso il cestello filtrante intercambiabile. Introduzione al progetto sistematico del layout Layout : disposizione, tracciato, pianta - Disposizione planimetrica dei reparti produttivi - Disposizione planimetrica delle macchine, apparecchiature , impianti in un reparto - Disposizione planimetrica delle aree di servizio rispetto ad altre aree di servizio e ai reparti produttivi Elementi fondamentali per il progetto di un layout: - Prodotto P: insieme di materiali di partenza, semilavorati e prodotti finiti - Quantità (o volume di produzione): complesso di prodotti fabbricati o impiegati - Ciclo produttivo: insieme delle operazioni (di trasformazione o assemblaggio) che concorrono alla realizzazione del prodotto finito. - Servizi ausiliari: attività e funzioni a sostegno del personale e della produzione - Tempo: variabile indipendente a cui sono legate le funzioni sopra citate - P = f(T) => Evoluzione del prodotto nella forma e dimensioni - Q = f(T) => Evoluzione della domanda - C = f(T) => Evoluzione della tecnologia - S = f(T) => Evoluzione sistemi contabili Fasi del progetto di un layout: - Ubicazione: ricerca di area - Layout generale: disposizione generale dell’area in funzione del flusso dei materiali e delle attività più importanti - Layout dettagliato: collocazione di ogni singola unità del macchinario e delle attrezzature - Installazione: disegni dettagliati dell’installazione Per procedere allo studio del layout generale di impianto è necessario innanzitutto raccogliere informazioni su P e Q utilizzando un modulo normalizzato definito “foglio dei dati sul prodotto e sulle quantità”. Analisi del volume di produzione e delle varietà prodotte/ diagramma P – Q: 1- Suddivisione dei vari prodotti o modelli in esame, sulla base di: processo di lavorazione, dimensione, forma ecc.. 2- Calcolo delle quantità per ciascuna suddivisione e per ciascun prodotto all’interno di ciascun gruppo 3- Stesura diagramma prodotto – quantità Zona I – layout per prodotto (linea): Caratteristiche: - Elevata produzione di poche varietà - Elevato grado di meccanizzazione o automazione - Sistemi di trasporto continui - Investimenti elevati Punti di forza: Punti di debolezza: - Ridotti tempi di ciclo - Notevole rigidità - Possibilità di buon bilanciamento della linea - Elevato tempo di avvio di nuove produzioni - Ridotto WIP (minori aree di stoccaggio) - Rischi di rapida obsolescenza - Ridotto fabbisogno di manodopera - Vulnerabilità ai guasti - Qualità più uniforme - Investimenti elevati Zona II: - Piccole produzioni di molte varietà - Macchine universali - Piccoli investimenti in attrezzature e sistemi di trasporto Si suddivide in: - Layout per processo (reparto): Punti di forza: - Investimento ridotto - Maggior flessibilità di produzione - Controllo e supervisione più specializzati - Scarsa obsolescenza - Più possibilità di applicare metodi incentivanti Punti deboli: - Elevato WIP (maggiori aree di stoccaggio e immobilizzi di scorte) - Scarsa saturazione delle macchine - Maggiori costi di manodopera - Qualità meno omogenea - Scarsa prevedibilità tempi di consegna - Layout a punto fisso: i materiali e il componente principale del prodotto rimangono in una posizione prefissata dello stabilimento e gli attrezzi, il macchinario ed il personale confluiscono verso tale posizione. Zona III: Layout per famiglie (a celle), caso di Group Technology Vengono esaminati tutti i prodotti facenti parte del portafoglio dell'azienda ed essi vengono raggruppati in gruppi aventi ciclo di lavorazione simile ovvero la medesima sequenza di operazioni sulle macchine. Per ogni gruppo ottenuto viene realizzata un'isola, che non è altro che un piccolo layout per prodotto (in linea), cosicché alla fine si hanno tante isole per quanti gruppi sono stati formati. Similarità delle parti: nella fase di raggruppamento si devono ricercare delle similarità considerando varie caratteristiche, tipo: - Attributi di progetto (forma geometrica e dimensioni) - Attributi di fabbricazione (sequenza delle operazioni) Possibili configurazioni di celle: - Layout in linea: macchine disposte in linea retta e servite da un sistema a navetta di tipo rettilineo. Disposizione più semplice ed economica come impianto ma richiede spazio in lunghezza ed un operatore per macchina. - Layout a U: macchine disposte secondo una U e servite da un sistema a navetta curvilineo. Riduzione dello spazio in lunghezza e consente la riduzione di operatori ma meno economica come impianto. STAMPATO FINO QUA - Layout a loop: macchine disposte secondo un loop e sono servite da un sistema a convogliatore. Riduzione dello spazio in lunghezza con riduzione del numero di operatori ma è la soluzione più costosa. Metodo di analisi del flusso dei materiali: A- Per un solo prodotto (max 3-4) => Foglio del processo operativo monoprodotto di montaggio o di lavorazione B- Per pochi prodotti (max5-6) => F.P.O. multiprodotto C- Per molti prodotti => si può applicare il metodo A o B a seconda del numero di gruppi D- Per moltissimi prodotti => foglio origine/destinazione Unità di misura del flusso dei materiali: se non esistono unità di misura di trasporto comuni per materiali diversi, la misura della intensità del flusso risulta molto diOicile. Si passa allora al conteggio del numero di MAG per ogni materiale, il che dà una misura della sua trasportabilità. MAG: un pezzo di materiale che - Può essere tenuto con facilità in una mano - Ragionevolmente solido - Ha una forma compatta e si può accatastare - Poco suscettibile al danneggiamento - Ragionevolmente pulito, saldo e stabile Group Technology: identificare e raggruppare parti simili, di una determinata popolazione di pezzi, da un punto di vista del progetto e/o della fabbricazione. Sistemi di produzione cellulare: basati sul concetto i group technology. Vengono esaminati tutti i prodotti e vengono raggruppati in gruppi aventi ciclo di lavorazione simile ovvero la medesima sequenza di operazioni sulle macchine. Per ogni gruppo ottenuto viene realizzata un’isola. Ciò consente: - Avere flussi unidirezionali all’interno della cella - DiOerenziare la produzione su una maggiore vastità di prodotti attraverso la presenza di più celle specializzate per famiglie - Coniugano eOicienza e flessibilità Metodi di costruzione delle famiglie: 1- Classificazione a vista: basato sulla osservazione delle parti o delle loro fotografie. Metodo economico e di rapida implementazione. Per contro è un metodo che necessita di una grande esperienza, soggettivo, poco ripetibile e fattibile solo se il numero delle parti da classificare è molto limitato. 2- Classificazione e codifica: - Ordinamento delle parti secondo criteri fondati su caratteristiche costruttive e funzionali - Determinazione di una serie di caratteri alfanumerici designati a identificare univocamente le caratteristiche delle parti. Descrizione in maniera compatta delle caratteristiche delle parti che faciliteranno la determinazione e il ritrovamento di parti simili. Non ha senso procedere alla codifica senza aver prima eOettuato un’attenta classificazione delle stesse. Richiede notevole dispendio di tempo e risorse. Un codice si dice parlante o muto a seconda che sia in grado o meno di fornire informazioni particolari sul materiale. Codifica delle parti: - Struttura gerarchica: il significato di una cifra nel codice dipende dal valore delle cifre precedenti - Struttura a catena: il significato di ciascuna cifra dipende soltanto dalla sua posizione all’interno del codice - Struttura mista 3- Analisi dei flussi produttivi – PFA: la creazione delle famiglie avviene analizzando solamente i cicli di lavorazione delle parti e non la loro morfologia. Il metodo si articola nelle seguenti fasi: o Raccolta ed organizzazione dei dati: - Scelta del campo di intervento: scelta della popolazione da analizzare - Scelta del codice e del ciclo di lavorazione: ottenibili dai fogli di lavorazione di ciascuna delle parti considerate - Dati addizionali: dimensione del lotto e tempi standard di lavorazione o Ordinamento dei cicli di lavorazione: combinare ed ordinare le parti in gruppi a seconda delle similitudini dei cicli di lavorazione. Con un notevole numero di parti è consigliabile adottare la tecnica del “raggruppamento in pacchi”. Ogni pacco contiene gruppi di parti caratterizzate da identico ciclo di lavorazione e identificato da una lettera maiuscola e da una serie di codici che identificano il ciclo di lavorazione. 4- Stesura della matrice parte macchina – MCM (carta PFA): costruzione di una matrice nella quale sulle righe sono riportati i processi o le macchine usate e nelle colonne le parti. Ciascun valore può assumere 0 o 1. 0 se la parte non necessita della lavorazione sulla macchina mentre 1 se la necessita. 5- Analisi della carta PFA: utilizzando algoritmi di clustering i gruppi di parti simili sono identificati e raggruppati. Algoritmo rank order clustering: o 0.Costruire la matrice parte – macchina o 1.Associare ad ogni riga un numero binario secondo la formula: o 2.Ordinare le righe dall’alto in baso secondo valori decrescentidel numero binario associato o 3.Associare ad ogni colonna un numero binario o 4.Ordinare le colonne da sinistra a destra secondo valori decrescenti o 5.Se i passi da 2 a 4 non è stato necessario alcuno scambio di righe e/o colonne andare al punto 6, sennò tornare al punto 1 o Stop Studio delle attività di servizio per il progetto del layout generale: Tabella combinata dei rapporti: procedura 1- Identificare tutte le attività di servizio e produzione ed elencare nella medesima tabella: reparti, operazioni, centri di lavoro, fabbricati, fonti di energia, gruppi di macchine 2- Convertire i dati nel codice di giudizio 3- Assegnare un giudizio letterale fra le diOerenti attività di servizio Metodo di calcolo dello spazio richiesto Legislazione => spazi minimi per ogni operatore: 2 m2 Suggerimenti ergonomici: - Semplicità dei movimenti mani e braccia - Minimi spostamenti del corpo - Organi di manovra, utensili e materiali di fronte all’operatore - Evitare lavoro a piedi - Ridurre al minimo gli sforzi necessari Metodo della tendenza ed estrapolazione dei rapporti: metodo meno preciso ma adeguato quando ci sono scarse attrezzature e investimenti fissi. Il metodo stabilisce un rapporto di metri quadrati rispetto a qualche altro fattore della produzione (cifre indice). Si stabiliscono i valori di tali rapporti per ciascun periodo del tempo passato, quindi se ne individua la tendenza, si estrapola per il futuro e si determina il valore più probabile che tali rapporti assumeranno. Metodo del layout schematico: sono necessari la pianta in scala dell’area disponibile e i modelli o sagome delle attrezzature o macchine. Metodo degli spazi standard: si ricorre a spazi standard prestabiliti nella pratica industriale. Le precauzioni da prendere sono quelle di utilizzare spazi standard calcolati nella medesima industria e di utilizzare spazi standard sviluppati da altri solo come guida per sviluppare i propri. Pianificazione automatica dei layout dei sistemi produttivi: I programmi di calcolo sono strumenti per generare diverse configurazioni e selezionare il layout ottimale. Gli algoritmi si distinguono in: - Costruttivi: costruiscono ex-novo una soluzione per layout - Migliorativi: operano cambi di posizionamento dei reparti o attività a partire da una soluzione iniziale fino al miglioramento del layout esistente. Metodo dei calcoli diretti: si tratta di determinare - Numero di macchine e attrezzature necessarie per la produzione - Area occupata fisicamente da ciascuna macchina o attrezzatura - Numero di addetti a ciascuna macchina - Area di lavoro richiesta per ciascun operatore - Area richiesta per interventi di manutenzione - Area richiesta per i magazzini dei materiali in lavorazione Ne deriva un’area totale per macchina o lavorazione: a cui si devono sommare le aree relative all’immagazzinamento e ai servizi Rendimento di produzione di una macchina: => Numero delle macchine nella produzione per reparto: Qij: produzione richiesta del prodotto i sulla macchina j Tij: tempo medio eOettivo di produzione del prodotto i sulla macchina j Nij: numero di ore disponibili per la produzione del prodotto i sulla macchina j nel periodo di produzione considerato 1/Tij: numero eOettivo di pezzi i prodotti con una macchina di tipo j Numero delle macchine necessarie per la produzione in linea: Bilanciamento delle linee di assemblaggio Definizioni e parametri caratteristici del bilanciamento - Linee di assemblaggio: serie di stazioni attraverso le quali le parti componenti di un prodotto devono passare, in prestabilita sequenza, per essere sottoposte ad operazioni di assemblaggio. - Problema: quante e quali operazioni assegnare a ciascuna stazione di lavoro per bilanciare la linea - Obiettivi del bilanciamento: assegnare le singole operazioni da svolgere nelle stazioni, nel rispetto delle relazioni di precedenza, onde garantire la produzione prefissata con i minimi costi - Assemblare: processo di recupero e fissaggio di componenti al fine di ottenere prodotti finiti - Operazione elementare (Task): la più piccola parte di attività in cui tutto il lavoro può essere diviso - Workstation: è un segmento di linea in corrispondenza del quale sono svolti uno o più task. I task sono svolti da un operatore ed il tempo necessario per completarli è detto tempo di lavorazione della workstation. L’insieme di task da eseguire sulla stazione di lavoro è detto carico di lavoro - Tempo elementare (te): tempo necessario per realizzare una operazione elementare - Tempo ciclo: Tc = T/q dove indichiamo con T il tempo disponibile per realizzare un lotto e con q le dimensioni dello stesso. Tempo che intercorre tra l’uscita di un pezzo della linea e l’uscita del pezzo successivo. Metodi euristici per l’assegnamento degli elementi alle stazioni Rispettano le seguenti ipotesi: - Rispetto del tempo ciclo e relazioni di precedenza - I tempi elementari sono ritenuti indipendenti da altre operazioni - I tempi elementari sono sommabili, on si tiene conto di altri fattori Procedura: a) Elencare tutti gli elementi di lavoro presenti nella operazione di assemblaggio b) Non possono essere assegnati alla stazione gli elementi: - Che sono stati già assegnati - Che sono soggetti a vincoli di precedenza - Il cui tempo elementare è maggiore del tempo disponibile c) Usare uno dei seguenti metodi euristici per la scelta dell’elemento da assegnare tra quelli rimasti disponibili Alcuni metodi euristici disponibili: - Largest Candidate: tra gli elementi disponibili si sceglie quello con il più lungo tempo di esecuzione. ð Regole: o Elencare tutti gli elementi di lavoro in ordine decrescente di tempi di esecuzione o Assegnare gli elementi alla prima stazione partendo dalla cima della lista, scegliendo il primo elemento ad essa assegnabile tenendo conto sia dei requisiti di precedenza, che del tempo di ciclo o Continuare il processo di assegnazione degli elementi lavoro con il criterio descritto allo step precedente non considerando più le operazioni già assegnate - Shortest Candidate: tra gli elementi disponibili si sceglie quello con il più breve tempo di esecuzione - Most following tasks: tra gli elementi disponibili si sceglie quello con il più grande numero di elementi da esse dipendenti per vincoli di priorità - Least number of following tasks: tra gli elementi disponibili si sceglie quello con il più piccolo numero di elementi da esso dipendenti per vincoli di priorità - Ranked positional weight: tra gli elementi disponibili si sceglie quello per cui la somma dei tempi di esecuzione dell’elemento stesso e di ciascuno degli elementi seguenti è maggiore. ð Pagina seguente… Determinazione del numero ottimale di macchine automatiche servite da un solo operatore umano Carta uomo-macchina per numero ottimale di macchine automatiche servite da un solo operatore umano: è particolarmente utile quando macchine diverse devono essere supervisionate da un solo operatore. Definizioni: - a: durata di una attività concorrente dell’uomo e della macchina - b: durata di una attività indipendente dell’operatore - t: durata di una attività indipendente della macchina - n’: numero teorico di macchine da assegnare all’operatore - m: numero intero di macchine assegnate all’operatore - Tc: periodo del ciclo ripetitivo - Io: tempo morto per l’operatore durante il ciclo - Im: tempo morto per la macchina durante il ciclo - C(m): costo per unità di prodotto sulla base di m macchine per l’operatore - C1: costo orario per operatore - C2: costo orario per macchina - (a+b): tempo richiesto ad un operatore per compiere il lavoro richiesto su una singola macchina durante un ciclo completo di produzione - (a+t): tempo richiesto alla singola macchina per completare un ciclo di produzione Ciclo ripetitivo di una macchina: