Helwan University Fashion & Textile Printing Terminology PDF
Document Details
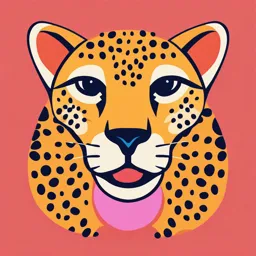
Uploaded by GoodlyPearTree935
Helwan University
Prof. Dalia Maamoun
Tags
Summary
This document is a terminology of specialty field in textile printing prepared by Prof. Dalia Maamoun. It details various aspects of textile and fibers, including natural fibers, synthetic fibers, and different types of yarns. Explains concepts like filament and staple fibers in fabrics, along with other common terms in the textile industry.
Full Transcript
Helwan University Faculty of Applied Arts Fashion and Textile Printing Program Freshmen Year Terminology of Specialty Field Code: HUM003 Prepared by Prof. Dalia Maamoun 1 Both industrialized and developing countries now have modern installatio...
Helwan University Faculty of Applied Arts Fashion and Textile Printing Program Freshmen Year Terminology of Specialty Field Code: HUM003 Prepared by Prof. Dalia Maamoun 1 Both industrialized and developing countries now have modern installations capable of highly efficient fabric production. In addition to mechanical improvements in yarn and fabric manufacture, there have been rapid advances in development of new fibers, processes to improve textile characteristics, and testing methods allowing greater quality control. The modern textile industry is still closely related to the apparel industry, but production of fabrics for industrial use has gained in importance. The resulting wide range of end uses demands a high degree of specialization. In the most technically advanced communities, the industry employs technicians, engineers, and artists; and a high degree of consumer orientation leads to emphasis on marketing operations. Fibers and Yarns Fiber Fiber is a natural or man-made material that is significantly longer than it is wide. Fibers are often used to make other materials. Natural Fibers The fiber that is produced from nature like plants, animals, and geological processes is called natural fiber. Example- Cotton, Wool, Silk, etc. Natural Vegetable Fibers These are normally comprised of cellulose and include the following: Bamboo, Coir, Cotton, Flax, Hemp, Jute, Kenaf, Linen, Manila, Pina, Raffia, Ramie, and Sisal. Natural Animal fibers Animal fibers consist of animal hairs and fibers from animals' secretion. Their main chemical components are proteins that are formed by a series of amino acids through polymerization of peptide bonds into macromolecular chains; thus, animal fibers are also called natural protein fibers. The animal fibers are mainly classified as hair fibers and silk fibers. For a long period, animal fibers are good raw textile materials because of their high elasticity, warmth 2 retention, water absorption, and soft luster. They can be interlaced into many types of high level of yarns and garments throughout four seasons of a year and surely other decorative and technical textiles. Synthetic fibers The fiber that is produced from different chemical composition, structure, and properties is significantly modified during the manufacturing process is called synthetic fiber. Example- Polyester, Acrylic, etc. Filament A fiber of an indefinite or extreme length, such as one found in plant or animal structures. Manufactured fibers are extruded into filaments that are converted into filament yarn, staple, or tow. If the filament fiber is cut into different lengths, it becomes the staple fiber. Multifilament A yarn consisting of many strands, as opposed to monofilament, which is one strand. Most textile yarns are multifilament. Staple fiber Staples refer to fibers of individual lengths and can be any composition. Individual fibers such as natural silk or synthetics are known as filaments rather than staple fibers. Blending The combining of staple fibers of different physical characteristics to assure a uniform distribution of these fibers throughout the yarn. Microfiber Microfiber is a synthetic fiber that is finer than one denier or decitex / thread and having a diameter of fewer than ten micrometers. This is smaller than the diameter of a strand of silk, which is itself around 1/5 the diameter of a human hair. The most common types of microfibers are made from polyester, polyamide. 3 Yarn A long continuous length of interlocked fibers that is suitable for use in the production of textiles, sewing, crocheting, knitting, weaving, embroidery, or rope making is called yarn. Bicomponent Yarns Spun or filament yarns of two generic fibers or two variants of the same generic fiber. Sliver A continuous bundle of loosely assembled untwisted fibers. These are fibers that are drawn from the card by the drawing frames and are eventually twisted into a yarn during the sliver knitting process. Moisture Regain The percentage of water present in the textile material of oven-dry weight is called moisture regain. Say, Oven dry weight = D Water weight = W (Original weight- oven dry weight) Moisture Regain = MR Moisture Regain (MR) = Water weight (W) / Oven dry weight (D) Then, MR (%) = 100 W/ D. Moisture Content The weight of water in the material expressed as a percentage of the total weight is called moisture content. Say, Oven dry weight = D Water weight = W (Original weight- oven dry weight) Moisture Content = MC Moisture Content (MC) = Water weight (W) / (Water weight + Oven dry weight) Then, MC (%) = 100 W / (W + D). Pilling A tangled ball of fibers that appear on the surface of a fabric as a result of wear or continued friction or rubbing of the surface of the cloth. 4 Thread Count It is calculated by counting the number of threads per square inch of the fabric in both directions. The number of threads is the total of threads in the warp is added to the number of threads in the weft (i.e., 110 x 90) = 200 TC High Tenacity This is a fiber property that measures strength. The property is determined by the force required to rupture of break the fiber. Typically, this measure is grams per denier (g/d). Tensile strength measures textile strength, measured in pounds per square inch to break a fabric. Hydrophilic Fibers Fibers that absorb water easily, take longer to dry, and require more ironing. These fibers denote a finish that improves wearing comfort. Hydrophobic Fibers Fibers that lack the ability to absorb water. These fibers denote a finish normally applied to create water-repellent products. Nanofiber Refers to fibers that are typically manufactured through an electrospinning process, which spins fibers in diameters ranging from 10 nm (nanometers) to several hundred nanometers, but usually less than 1,000 nm. In scientific terms, nanofibers are generally considered as having a diameter of less than one micron. The name nanofiber comes from the nanometer, which is a scientific unit of measurement representing a billionth of a meter, or three to four atoms wide. Current uses for nanofiber technology are in the fields of medical products, consumer products, industrial products, and high-tech applications for aerospace, capacitors, transistors, drug delivery systems, battery separators, energy storage, filtration, fuel cells, and information technology. 5 Textile Spinning & Weaving Spinning This final operation in the production of a natural yarn, consists of the drawing, twisting, and the winding of the newly spun yarn onto a device such as a bobbin, spindle, cop, tube, cheese, etc. In manufactured fibers, the spinning process is the extrusion of a spinning solution into a coagulation bath, a heated air chamber, or a cooling area in order to form a continuous filament or tow. Weaving Weaving is a technique of textile production where two sets of yarns or threads are interlaced at right angles to create a fabric or cloth. Longitudinal threads are called the warp and lateral threads are the weft. The basic weaves are plain weave, satin weave, or twill weave. Plain Weave Each filling yarn passes successfully over and under each warp yarn, alternating each row. Twill Weave A fundamental weave characterized by diagonal lines produced by a series of floats staggered in the warp direction. Satin Weave The face of the fabric consists almost completely of warp, or filling floats produced in the repeat of the weave. Satin weave fabric has a characteristic smooth, luxurious surface and has a considerably greater number of yarns in the set of threads (either the warp or filling) that forms the face than in the other set. Cotton Gin A machine that quickly removes seeds from newly harvested cotton is a cotton gin. Before the invention of the mechanical cotton gin, handheld versions were used to clean the fluffy fibers. 6 Loom Machines for weaving fabric by interlacing a series of vertical parallel yarns (the warp) with a series of horizontal parallel yarns (the filling). The warp yarns from a beam pass through the heddles and reed, and the filling is passed through the “shed” of warp threads by means of a shuttle, or other device and is settled into place by the reed and lay. The primary distinction between different types of looms is the manner of filling insertion. Filling (Pick or Weft) In woven fabric, the yarn running from selvage to selvage at right angles to the warp. Each crosswise length is called a pick. In the weaving process, a shuttle, rapier, or other type of yarn carrier carries the filling yarn. Warp The set of yarn in all woven fabrics, that runs lengthwise and parallel to the selvage and is interwoven with the filling. Sizing A generic term for compounds that are applied to warp yarn to bind the fiber together and to stiffen the yarn to provide better abrasion resistance. The process of applying sizing compounds such as starch or polyvinyl alcohol. Knitting A method of constructing fabric by interlocking series of loops of one or more yarns. Knitting Types: Warp Knitting – A type of knitting in which the yarns generally run lengthwise in the fabric. The yarns are prepared as warps on beams with one or more yarns for each needle. Weft Knitting – A common type of knitting, in which one continuous thread runs crosswise in the fabric making all the loops in one course. An example is Circular Knitting, where the fabric produced on the knitting machine is in the form of a tube, the threads running continuously around the fabric. 7 Jacquard A system of weaving that utilizes a highly versatile pattern mechanism to permit the production of large, intricate designs and (at Bally Ribbon Mills) shapes. The weave controls the action of one warp yarn for the passage of one pick. Each card perforation machine may carry a large number of cards, depending upon the design, because there is a separate card for each pick in the pattern. Textile Processing Any mechanical operation used to translate a textile fiber or yarn to a fabric or other textile material. This includes such operations as opening, carding, spinning, plying, twisting, texturing, coning, quilling, beaming, slashing, weaving, braiding, and knitting. Carding A process of opening and cleaning textile fibers - usually cotton - which separates fibers from each other, lays them parallel, forms them into a thin web, and then condenses them into a single continuous untwisted strand or bundle of fibers called a "sliver". Combed Cotton Combed cotton is an extremely soft version of cotton made by using a production process whereby the cotton fibers undergo a specialty treating before they are spun into yarn. Combed cotton is softer and stronger than conventional cotton because the shorter, breakable fibers are removed during the combing process. In addition, the straightened fibers lie closer together after combing, making the combed cotton fabric less likely to fray and unravel. Products containing combed cotton, are usually identified, because the process removes volume and adds an extra production step. As a result, combed cotton products are also slightly more expensive than conventional cotton products. 8 Nonwoven Fabric A textile structure held together by interlocking of fibers in a random web, accomplished by mechanical, chemical, thermal, or solvent means. Generally, crimped fibers that range in length from 0.75 to 4.5 inches are used. Smart Textiles Textiles that can sense and react to changes in the environment, such as changes from mechanical, thermal, chemical, magnetic, and other sources. Tapestry A heavy, often hand-woven, ribbed fabric, featuring an elaborate design depicting a historical or current pictorial display. The weft-faced fabric design is made by using colored filling yarns, only in areas where needed, that are worked back and forth over spun warp yarns, which are visible on the back. End-uses include wall hangings and upholstery. Twist The number of turns about its axis per unit of length of a yarn, or textile strand. Twist is expressed as turns per inch (tpi), turns per meter (tpm) or turns per centimeter (tpc). Winding The creation of large yarn packages that can be easily unwound, is called winding. This makes using the yarn on subsequent machines both easier and more economical. So, we can say that the process of transferring yarns from ring, bobbin, hank into a suitable package is called winding. Beam A cylinder of wood or metal, usually with a circular flange on each end, on which warp yarns are wound for slashing, weaving, and warp knitting. Cone A conical package of yarn, usually wound on a disposable paper core. Drape A term to describe the way a fabric falls while it hangs; the suppleness and ability of a fabric to form graceful configurations. 9 Fiber Number The linear density of a fiber expressed in units such as denier or Tex. Denier The weight, in grams, of 9000 meters of yarn. The lower the denier number the finer the size of yarn, and the higher the number the larger the size of yarn. In countries other than the USA, Denier is replaced by the Tex system. Tex A unit for expressing linear density, equal to the weight in grams of one kilometer of yarn, filament, fiber or another textile strand. Greige Fabric (pronounced gray) An unfinished fabric just off the loom or knitting machine. Inspection The process of examining textiles for defects at any stage of manufacturing and finishing. Lot A unit of production, or group of other units, or packages that is taken for sampling, statistical examination, having one or more common properties and being separable from other similar lots. Seamless A term that describes a tubular knit, or woven fabric without seams, e.g., seamless hosiery, or seamless woven tube. Selvage The narrow edge of woven fabric that runs parallel to the warp. It is made with stronger yarns in a tighter construction than the body of the fabric to prevent unraveling. A fast selvage encloses all, or part of the picks, and a selvage is not fast when the filling threads are cut at the fabric edge after each pick. Shuttle A boat-shaped device usually made of wood with a metal tip that carries filling yarns through the shed in the weaving process. 10 Shuttless Loom A loom in which a device other than a shuttle is used for weft insertion. Tear Strength The force required beginning or continuing a tear in a fabric under specified conditions. Tensile Strength In general, the strength shown by a specimen subjected to tension as distinct from torsion, compression, or shear. Texture A term describing the surface effect of a fabric such as dull, lustrous, wooly, stiff, soft, fine, course, etc. Velvet A medium weight short cut-pile constructed fabric in which the cut pile stands up very straight in a succession of rows that stand so close together as to give an even, uniform surface. It is woven using two sets of warp yarns; the extra set creates the pile. Velvet, a luxurious fabric, is commonly made with a filament fiber for high luster and a smooth, soft hand. Textile Coloration Textile printing It is the process of applying color to fabric in definite patterns or designs. In properly printed fabrics the color is bonded with the fiber, so as to resist washing and friction. Textile printing is related to dyeing but in dyeing properly the whole fabric is uniformly covered with one color, whereas in printing one or more colors are applied to it in certain parts only, and in sharply defined patterns. In printing, wooden blocks, stencils, engraved plates, rollers, or silkscreens can be used to place colors on the fabric. Colorants used in printing contain dyes thickened to prevent the color from spreading 11 by capillary attraction beyond the limits of a pattern or design. Traditional textile printing techniques may be broadly categorized into three styles: Direct printing, in which colorants containing dyes, thickeners, and the mordants or substances necessary for fixing the color on the cloth are printed in the desired pattern. Resist dyeing, in which a wax or other substance is printed onto fabric which is subsequently dyed. The waxed areas do not accept the dye, leaving uncolored patterns against a colored ground. Discharge printing, in which a bleaching agent is printed onto previously dyed fabrics to remove some of the color by converting the dye into a water soluble substance that can be removed by washing off.. Burn-out A brocade-like pattern effect created on the fabric through the application of a chemical, instead of color, during the burn-out printing process. (Sulfuric acid, mixed into a colorless print paste, is the most common chemical used.) Many simulated eyelet effects can be created using this method. In these instances, the chemical destroys the fiber and creates a hole in the fabric in a specific design, where the chemical comes in contact with the fabric. The fabric is then over-printed with a simulated embroidery stitch to create the eyelet effect. However, burn-out effects can also be created on velvets made of blended fibers, in which the ground fabric is of one fiber like a polyester, and the pile may be of a cellulosic fiber like rayon or acetate. In this case, when the chemical is printed in a certain pattern, it destroys the pile in those areas where the chemical comes in contact with the fabric but leave the ground fabric unharmed. Dyeing It is the application of dyes or pigments on textile materials such as fibers, yarns, and fabrics with the goal of achieving color with desired color fastness. Dyeing is normally done in a special solution containing dyes and particular chemical material. 12 Dye molecules are fixed to the fiber by absorption, diffusion, or bonding with temperature and time being key controlling factors. The bond between dye molecule and fiber may be strong or weak, depending on the dye used. Dyeing and printing are different applications; in printing, color is applied to a localized area with desired patterns. In dyeing, it is applied to the entire textile. Substrate Fabric on which coloration, coating or other treatments are applied. Affinity The attraction between a substrate and a dye or other substance. Absorbency The ability of a fabric to take in moisture. Absorbency is a very important property, which affects many other characteristics such as skin comfort, static build-up, shrinkage, stain removal, water repellency, and wrinkle recovery. Abrasion Resistance The degree by which a fabric is able to withstand loss of appearance through surface wear, rubbing, chafing, and other frictional actions. Bleeding Loss of color by a fabric or yarn when immersed in water, a solvent, or similar liquid medium, as a result of improper dyeing or the use of dyes of poor quality. It causes staining on other colors and fabrics. Color Strength (K/S) It is known to us that when reflectance is more, absorbance is less and when reflectance is less, absorbance is more. The color strength of a dye is a measure of its ability to impart color to other materials. It is measured using devices called Spectrophotometers. Color fastness Resistance to fading, i.e., the ability of a dye to retain its color when the dyed or printed textile material is exposed to conditions or agents such as light, perspiration, crocking (rubbing), or washing that can remove color. 13 Color Fastness to Crocking / Rubbing Crocking means the transfer of color from one fabric onto another by rubbing. A fabric with poor color fastness would transfer its color easily onto other fabrics, especially to white color fabrics. Natural Dyes Dyes that are made from mineral, vegetable (plant) or animal; otherwise obtained from natural sources. The most common types include Indigo, Cochineal, Lac, Logwood, Madder, Munjeet, Catechu, Brazilwood, Osage Orange, Fustic, Weld, Tannin, Turmeric and Henna. Indigo A dye with a distinctive blue color. The chemical compound that constitutes the indigo dye is called indigotin. Historically, indigo played an important role in many countries' economies because natural blue dyes are rare. Among other uses, it is used in the production of denim cloth for blue jeans. Sustainable / Eco / Green Textiles that are produced in ethically responsible ways, or textile production processes that do not cause harm to the environment. Curing / Steaming / Thermofixation In ageing or steaming process, the dyes and chemicals present superficially on the surface of the fabric are transferred into the fabric. The dried printed fabric has pigments or dyes, thickeners such as starch, gum etc. and printing auxiliaries on its surface. Steaming enhances the absorption of dyes or pigments on the fabric. In steaming or ageing, the dried printed fabric is exposed to steam at atmospheric or higher pressure for different time intervals. Steaming can be carried out continuously or batch-wise. Textile Finishing Finish 1. A substance or mixture of substances added to textile materials to impart desired properties. 14 2. A process, physically, or chemically performed on textile materials to produce a desired effect. 3. A property, such as smoothness, drape, luster, water repellency, flame retardancy, or crease resistance that is produced by 1 and/or 2. Singeing A process to burn off protracting fibers from the body of the fabric, to give a smooth surface. Cotton is by nature a hairy product. Desizing It involves impregnation of the fabric with the desizing agent, allowing the desizing agent to degrade or solubilize the size material, and finally to wash out the degradation products. The major desizing processes are: enzymatic desizing of starches on cotton fabrics, oxidative and acid desizing. Carbonizing Carbonizing is a chemical process for eliminating cellulosic matter from a mixture of animal or synthetic matter. The process involves acid treatment and, in this process, hydrochloric acid or sulfuric acid are used. Scouring An operation to remove the sizing and tint used on the warp yarn in weaving and, in general, to clean the fabric prior to dyeing. Bleaching A process of whitening fibers, yarns, or fabrics by removing the natural and artificial impurities to obtain clear whites for finished fabric, or in preparation for dyeing and finishing. The materials may be treated with chemicals or exposed to sun, air, and moisture. Mercerization This is used to describe a process of treating a thread, yarn, or fabric to increase its luster on the surface of the fabric and its color retention and durability. The fabric is immersed in sodium hydroxide and then neutralized in acid. This causes the fiber to permanently swell. 15 Stentering A fabric is passed through a machine called a stenter to smooth out the fabric, because after bleaching the cloth gets creased and wrinkled. This also controls the finished width of the fabric by tension. Monomer The simple, unpolymerized form of a compound from which a polymer can be made. Thermoplastic A term used to describe a plastic material that is permanently fusible, i.e., manufactured fibers that will soften at higher temperatures. Thermoset A term used to describe a plastic that, once formed, will not melt. Elastomers Synthetic polymers having properties of natural rubber such as stretchability and recovery. Coating The application of a semi-liquid material such as rubber, polyvinyl chloride, or polyurethane to one or both sides of the textile material. Once the coating has dried (cured) it forms a bond with the fabric. Air Permeability The porosity, or the ease with which air passes through material. Air permeability determines such factors as the wind resistance of sailcloth, the air resistance of parachute cloth, and the efficiency of various types of air filtration media. It is also a measure of warmness or coolness of a fabric. Anti-Bacterial (Anti-Microbial) A fabric that has been chemically treated by incorporating the anti-bacterial chemical agent into the fiber formula, making the finished fiber or fabric resistant to, or inhibiting the growth of micro-organisms. 16 Waterproof A term applied to fabrics whose pores have been closed (using padding in resins’ solution, and therefore, will not allow water or air to pass through. Anti-Static Can be either a fiber or fabric that does not allow the build-up of static electricity to occur when the fiber or fabric experiences friction or rubbing. Natural substrates generate minimum statics due to their hydrophilic nature. Durability The ability of a fabric to resist wear through continual use. Durable Press More or less interchangeable with the term permanent press, but actually more precise. Durable press implies that the shape retention properties of a garment are excellent and durable for the life of the garment. Calendar A machine used in finishing to impart a variety of surface effects to fabrics. A calendar essentially consists of two or more heavy rollers, sometimes heated, through which the fabric is passed under heavy pressure. Special effects may be produced such as: high luster, glazing, moiré, and embossed effects. Dimensional Stability The ability of textile material to maintain or return to its original geometric configuration. Heat Setting The process of conferring dimensional stability and other desirable properties (wrinkle resistance and improved heat resistance) by means of either moist or dry heat. Elongation The deformation in the direction of load caused by a tensile force. Elongation is measured in units of length (inches, millimeters) or calculated as a percentage of the original specimen length. Elongation may be measured at a specific load or at the breaking point. 17 Flame Retardant A chemical compound that can be incorporated into a textile fiber during manufacture, or applied to a fiber, fabric, or other textile item during processing to reduce its flammability. UV Protection (UPF) Designed for sun protection, these specialty fabrics are produced for their level of ultraviolet (UV) protection. A novel weave structure, combined with a high denier count (related to thread count per inch) may assist in producing sun protective properties in fabrics. Hand The tactile qualities of a fabric, e.g., softness, firmness, elasticity, fineness, resilience, and other qualities perceived by touch. Soil Release Finish A finish that has the purpose of increasing the absorbency of a fabric on durable press blends. The finish allows the stain to leave the fabric faster, increases the wicking action for improved comfort, and therefore imparts greater ease in cleaning. Some soil release finishes also provide resistance to soiling as well as ease of soil removal. Surfactant A surface-active agent, i.e., a product that acts by modifying the surface or boundary between two phases. Swelling In textile usage, expanding of a fiber caused by the influence of a chemical, solvent, or agent. A property often used to facilitate dyeing. Ultraviolet Resistance The ability to retain strength and resist deterioration on exposure to sunlight. Micro-encapsulation A method of enclosing polymer additive materials in microscopic capsules, which can then be released under certain conditions to enhance performance properties. 18 Biotechnology Biotechnology already plays an important role in the textile industry. Enzymes are used routinely to wash and bleach textiles, to give jeans a denim look or to prevent wool from shrinking. A new wave of technology could take this a step further. In a not-so-distant future, our clothes will be made and dyed by living microbes, ditching many of the chemical processes that make fashion one of the most polluting industries in the world. 19