Sistemas de Propulsión: Tema 2 - Sistemas No Autónomos de Propulsión por Chorro PDF
Document Details
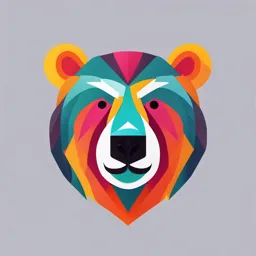
Uploaded by ErrFreeIron8371
Tags
Related
- Propulsion and Mixing of Food in the Alimentary Tract PDF
- Propulsion and Mixing of Food in the Alimentary Tract PDF
- Capítulo 64 Guyton PDF - Propución e Mezcla de Alimentos
- Cinemática Mandibular PDF
- Principios generales de la función intestinal, propulsión y mezcla - Seminarios Tercer registro_241112_231943 PDF
- Controllo della Pressione Arteriosa: Principi Fondamentali PDF
Summary
Este documento analiza los sistemas no autónomos de propulsión por chorro, enfocándose en los aero-reactores. Se describe la composición de los generadores de gas, los subsistemas fluidos, y los sistemas de control, destacando el funcionamiento de fanes y compresores.
Full Transcript
SISTEMAS DE PROPULSIÓN TEMA 2 SISTEMAS NO AUTÓNOMOS DE PROPULSIÓN POR CHORRO En este tema se van a analizar los sistemas no autónomos de propulsión por chorro, es decir, los aero- rreactores. Para ello, se emplea un enfoque de descomposición en subsistemas que lo componen. En primer lu...
SISTEMAS DE PROPULSIÓN TEMA 2 SISTEMAS NO AUTÓNOMOS DE PROPULSIÓN POR CHORRO En este tema se van a analizar los sistemas no autónomos de propulsión por chorro, es decir, los aero- rreactores. Para ello, se emplea un enfoque de descomposición en subsistemas que lo componen. En primer lugar, se analizan los componentes fundamentales del generador de gas de los aerorreactores (fan y compresor, cámara de combustión, turbina y sistema de transmisión); a continuación, se describen los subsistemas fluidos presentes en los aerorreactores (sistema de aire interno, sistema de combustible y sistema de lubricación); por último, se estudian los sistemas de control haciendo especial hincapié en los correspondientes a aerorreactores de uso civil. 2.1 COMPONENTES FUNDAMENTALES DE LOS AERORREACTORES Fanes y compresores Un compresor es un aparato que eleva la presión del fluido de trabajo que lo atraviesa (en el caso de aero- rreactores, el aire). El fan es un compresor de baja presión y elevado diámetro que está presente en la mayoría de aeromotores actuales (debido a la preeminencia del turbofán). En los grandes turbofanes actuales, el fan mueve una tonelada de aire por segundo y genera del orden del 75 % del empuje total del motor; además, la relación de compresión global (incluyendo los efectos del fan y del compresor) se acerca a 50:1, y la tempera- tura de salida del compresor puede llegar a ser superior a 700ºC. El diseño del sistema de compresión es una compleja tarea interdisciplinar. Durante este proceso, se rea- lizan modelos aerodinámicos, mecánicos, acústicos, de fabricación y de coste. La configuración óptima para cada aplicación queda determinada mediante la realización de estudios de sensibilidad que consideran todos los atributos fundamentales y requisitos del sistema, incluyendo el coste del ciclo de vida, el peso, las actuaciones y el ruido que genera. En el diseño de aerorreactores se utilizan tanto compresores axiales como centrífugos, e incluso la combina- ción de ambos (axi-centrífugo). Mientras que los antiguos aerorreactores empleaban compresores centrífugos, los actuales emplean casi exclusivamente compresores axiales, debido a que con ellos se alcanzan rendimien- tos de compresión más elevados. No obstante, los compresores centrífugos y los axi-centrífugos son todavía empleados en aplicaciones con compresores demasiado pequeños (turbofanes y turboejes muy pequeños), ya que los compresores axiales dejan de ser eficientes para tamaños de álabe inferiores al centímetro. Descripción de los subsistemas del compresor Un compresor puede comprender múltiples etapas, pero dentro de un sistema de compresión también pue- de haber múltiples compresores. Esta configuración multi-eje consiste en dos o más compresores cada uno de los cuales movido por su propia turbina a una velocidad óptima, permite alcanzar elevadas relaciones de compresión y proporciona una mayor flexibilidad operacional. Aunque los compresores multi-eje pueden em- plearse en turborreactores, son más adecuados en turbofanes en los que, aguas abajo del primer módulo de compresión (el fan) se separa el gasto de entrada en los gastos primario y secundario. El fan comprime todo el gasto de aire (los turbofanes en paralelo no son representativos), mientras que el compresor comprime sólo el gasto primario. Nótese que para turbofanes con alta relación de derivación, el gasto total es muy superior al 11 gasto primario. Algunos sistemas de compresión presentan un bloque de compresor ligado al eje del fan. A estas etapas se les suele denominar booster (en terminología anglosajona), y suelen emplearse en configuraciones bieje (ej: V2500, GP7000). Cono de morro El cono de morro proporciona una transición aerodinámica suave en la raíz de los álabes del fan, y debe aguantar impacto de pájaros, erosión y formación de hielo. Para cumplir con sus funcionalidades, el cono se fabrica en fibra de vidrio dispuesta y curvada de manera que se alcance su máxima resistencia. El espesor del cono se determina a partir de la experiencia adquirida en los ensayos de impacto de pájaros en motores anteriores; el ángulo se obtiene del compromiso entre optimizar ante impacto de pájaros y formación de hielo, y proporcionar un adecuado flujo de aire al fan. El cono tiene una punta de goma en su extremo para despegar cualquier acreción de hielo. También presenta una capa de poliuretano como protección frente a la erosión, y se encuentra unido al fan a través de una interfaz atornillada. Fan El sistema fan tiene como función principal comprimir los gastos secundario y primario. Ambos gastos pueden expandirse en toberas diferentes o en una misma tobera. Los fanes de alta relación de derivación amplia- mente utilizados en aeronaves civiles tienen una relación de compresión cercana a 2:1. Este gasto secundario comprimido se expande en la tobera secundaria y es responsable del 75 % del empuje total, aproximadamente. Los fanes de baja relación de derivación empleados en aeronaves militares presentan una relación de compre- sión típicamente entre 3:1 y 4:1, lo que determina que suelan ser multietapa. En ellos, es habitual que el gasto secundario se mezcle con el primario a la salida de la turbina y así el gasto total se expanda en una única tobera (una excepción sería el fan del Pegasus V/STOL montado en el Harrier). Adicionalmente, el gasto secundario se usa para el postcombustor y para refrigeración externa (del postcombustor y de la tobera). El fan tiene que cumplir con sus funciones con una elevada eficiencia aerodinámica, con un bajo coste del ciclo de vida, un bajo peso, un bajo diámetro, y con un bajo nivel de ruido (este último es un requisito civil, más que militar). Además, el fan debe presentar un margen de estabilidad adecuado para hacer frente a entornos de operación severos. El sistema debe pasar una serie de ensayos de certificación rigurosos: ingesta de agua y polvo, formación de hielo, operabilidad, requisitos de impacto de pájaros, contención de álabes en caso de desprendimiento, flujo de aire distorsionado resultante de maniobras o viento cruzado, actuaciones en diferentes altitudes, y compatibilidad con el sistema de inversión de empuje. 12 Los turbofanes civiles actuales presentan una configuración de alta relación de derivación. En esta confi- guración, el gasto de entrada pasa sólo por una etapa de compresión en el fan antes de dividirse, y la relación de derivación alcanza valores cercanos a 10 (Ej: PW1000G). Esta configuración resulta óptima para aviones de transporte de pasajeros y mercancías volando en régimen subsónico alto (M0 ∼ 0,85). En motores grandes se prefieren las configuraciones trieje, con un compresor de media presión y un compresor de alta presión comprimiendo el gasto primario (Ej: Trent 500). Los componentes principales de los fanes civiles son los álabes de fan, el disco del fan, la carcasa de con- tención, y la estructura de soporte del rodamiento frontal (que inlcuiría los álabes de estator tanto del flujo secundario como del primario). Para reducir el diámetro del fan, y por tanto su peso y su resistencia aerodinámica, se minimiza la relación entre los radios de raíz y de punta de álabe, sujeta a cumplir los criterios mecánicos de diseño de la raíz. El álabe del fan comprende un perfil aerodinámico y un anclaje en la raíz que lo fija al disco del fan. El rotor está unido al eje del fan, que a su vez está conectado a la turbina de baja presión. Todo el conjunto del rotor del fan está aguantado por el alojamiento del rodamiento frontal. Los álabes huecos y de cuerda ancha hacen posible un mayor gasto y un mayor rendimiento, además de ser más silenciosos que sus predecesores, los álabes con apoyos intermedios. Un álabe con apoyo intermedio consiste en un perfil aerodinámico sólido con dos apéndices que forman un ángulo recto con la dirección de envergadura del álabe y que se encuentran situados a tres cuatros de la altura del álabe, aproximadamente. Cuando se monta el álabe, dichos apéndices forman un apoyo que evita la torsión de los álabes cuando se les somete a cargas cíclicas asociadas a distorsiones aerodinámicas. También aumentan las frecuencias naturales del álabe (al rigidizarlos) y proporcionan una forma de amortiguamiento. La mera eliminación de los apoyos daría lugar a un diseño demasiado flexible (con frecuencias naturales demasiado bajas) y eliminaría el meca- nismo de amortiguamiento de las vibraciones del álabe. Para solucionarlo, se incrementa la cuerda del perfil, que tiene el doble efecto de rigidizar los álabes y permitir una reducción en el número de los mismos. La eliminación de los apoyos también supone una mejora en el rendimiento del fan, al eliminar las pérdidas aerodinámicas de los mismos y el efecto del bloqueo que obligaba a una mayor área frontal. Para evitar un aumento en el peso, los álabes son huecos, lo cual no sólo aligera los propios álabes, sino todo el sistema (disco, estructura frontal, carcasa de contención). Los procesos que hacen posible la fabricación de los álabes huecos son el conformado superplástico y la soldadura por difu- sión, ambos asociados a las propiedades del titanio. El disco del fan es uno de los componentes más críticos de todo el motor, y tiene las siguientes funcio- nes principales: Aguantar las cargas centrífugas de los álabes (tanto en operación normal como en el caso de desprendimiento de un álabe), proporcionar un anclaje a los álabes y una unión de los mismos al eje de baja presión; absorber cargas de impacto; y proporcionar un anclaje al cono de morro y otros componentes perifé- ricos. El disco, normalmente de titanio forjado, contiene una serie de ranuras en las que se anclan los álabes. El fallo de un disco pone en riesgo la integridad de la aeronave, de modo que se considera una parte crítica. Su diseño mecánico es clave no sólo por ser una pieza crítica, sino también por tratarse de un componente muy pesado. El papel de disco es garantizar que los álabes se mueven siguiendo una trayectoria circular y resistir las fuerzas centrífugas, que pueden llegar a ser del orden de cien toneladas en cada álabe. 13 Las tensiones totales en el disco son una combinación de los esfuerzos de inercia propios del disco y de los esfuerzos que imponen las fuerzas centrífugas en los álabes. Hay dos cuestiones claves que gobiernan los niveles de esfuerzos que tiene que soportar el disco. En primer lugar existe un criterio de rotura, de tal manera que si el disco se acelera demasiado no debe romperse, ya que comprometería la integridad del motor. Por otro lado, existe un criterio de vida del disco, que establece un umbral máximo a las tensiones; si no se cumple, se pueden emplear las siguientes estrategias: aumentar el tamaño del disco para reducir los niveles de tensión (la masa debe añadirse en el extremo), disminuir o eliminar los concentradores de tensión (como taladros o radios de acuerdo demasiado pequeños) y mejorar la resistencia del material. Nótese que si el requisito de vida se cumple holgadamente se puede reducir el tamaño del disco (y por ende su peso) hasta lo que exija el criterio de rotura por excesiva velocidad de giro. La carcasa del fan tiene como funciones primarias guiar el gasto de aire y contener un álabe de fan en caso de que se desintegre durante el vuelo. La carcasa debe ser capaz de absorber la energía de un álabe completo, sin liberar fragmentos del mismo o de la propia carcasa, y mantener la integridad del motor. La energía que libera un álabe de fan desprendido es equivalente a la enegía cinética de un turismo familiar a 100 km/h. Por todo ello, la carcasa debe presentar una alta resistencia y una alta ductilidad. La carcasa también proporciona una fijación para la caja de engranajes, equipos de apoyo en tierra y otros accesorios. El conjunto de la carcasa contiene unos elementos acústicos que ayudan a atenuar el ruido producido por el fan. Los paneles están for- mados por una estructura de panal de abeja hecha en material compuesto. El peso del sistema de contención es una función del cubo del diámetro del fan, de modo que turbofanes de elevada relación de derivación con elevados diámetros de fan disponen de sistemas de contención mucho más pesados. Compresor El sistema compresor tiene tres funciones principales: 1) elevar la presión del gasto suministrado a la cáma- ra de combustión y proporcionárselo a un número de Mach adecuado con adecuadas propiedades radiales; 2) proporcionar un gasto sangrado para el sellado del motor, el anti-hielo, la refrigeración y el control ambiental de la aeronave; y 3) proporcionar cualquier requisito de sangrado de potencia. Como el sistema fan, el compre- sor tiene que demostrar un elevado nivel de eficiencia aerodinámica, con un adecuado margen de estabilidad para todas las condiciones que pueda tener el gasto a la salida del fan, con un bajo coste de ciclo de vida y un bajo peso. Además, deberá cumplir requisitos de certificación similares. El sistema compresor puede constar de uno o dos módulos de compresor, cada uno movido por su pro- pia turbina. La relación de compresión de cada uno de los módulos se encuentra en el rango de 5 a 16. La configuración del sistema compresor dependerá de la aplicación del motor. La configuración óptima surge del compromiso entre actuaciones, peso, coste, estabilidad y vida útil. En motores civiles grandes, se recurre al empleo de dos bloques de compresor (configuración trieje) ya que proporciona un sistema eficiente, robusto y muy flexible, que permite que cada módulo gire a su velocidad óptima. Los motores civiles pequeños y los militares suelen tener una configuración bieje, con un único bloque de compresor. Los compresores axiales consisten en un conjunto rotor y un conjunto estator que contienen tantas etapas como sea necesario para alcanzar la relación de compresión deseada. Los componentes principales son el tam- bor del rotor, la carcasa y otros elementos estáticos, el pre-difusor de la cámara de combustión, y una o más estructuras de soporte. La configuración del rotor típicamente incluye de 3 a 12 discos, cada uno con un con- junto de álabes de rotor con una sección transversal de perfil aerodinámico. Los discos pueden ser atornillados o soldados para formar un tambor integral. Los motores militares ahora tienden a emplear blisks (blade+disks) para minimizar peso. También se requiere el uso de blisks cuando existen restricciones de espacio en el diáme- tro interior del disco, o cuando se requieren pequeños diámetros de raíz. Los álabes, los discos y los blisks se 14 fabrican de varios materiales. En aerorreactores modernos, las primeras etapas del compresor se suelen hacer de titanio, debido a su alta relación resistencia/peso. Las etapas posteriores suelen hacerse de aleaciones de níquel debido a las altas temperaturas de operación. La solución convencional formada por un disco que aloja los álabes es la típica en los diseños de compre- sores de aerorreactores civiles. Los álabes se unen normalmente al disco mediante una fijación en su raíz. En general, el objetivo es diseñar una estrategia de anclaje que imponga la menor carga posible en el disco para poder minimizar su peso. Existen dos métodos de fijación principales: La fijación axial y la fijación circunfe- rencial. En la fijación axial se mecanizan una serie de ranuras en el disco para admitir la fijación de la raíz del álabe (cola de milano). Las fijaciones axiales son más complejas y costosas; sin embargo, son las más robustas de cara a los daños causados por objetos extraños y son las que más facilitan el empleo de álabes de estator de incidencia variable. Las fijaciones circunferenciales suelen ser la opción más barata y sencilla, y son la solu- ción comúnmente empleada en las últimas etapas del compresor. Es relativamente sencillo mecanizar un surco en dirección circunferencial en la cabeza del disco. Los álabes se ensamblan aprovechando dicho surco. Las fijaciones de los álabes tienen la ventaja de una fácil mantenibilidad: los álabes dañados pueden ser fácilmente reemplazados. La penalización asociada a emplear fijaciones en la raíz estriba en que añaden peso muerto, lo que incrementa las cargas centrífugas aplicadas al disco. Como en el fan, el diseño mecánico del disco del compresor es una de las claves del diseño del mismo. El fallo de un disco comprometería seriamente la integridad del motor. Además, el peso del conjunto de discos supone una parte muy significativa del peso del compresor. Las tensiones en el disco son una combinación de esfuerzos impuestos por los álabes y los espaciadores, esfuerzos de inercia, y esfuerzos térmicos asociados a los gradientes de temperatura. Los esfuerzos térmicos se han vuelto cada vez más importantes a medida que han ido aumentando las temperaturas en el generador de gas. A rasgos generales, cuanto mayor es un disco, más lentamente responde ante cambios térmicos y, por tanto, mayores son los esfuerzos térmicos que aparecen. El diseño mecánico de los discos de las etapas posteriores del compresor es un reto debido a los siguientes tres factores: Las elevadas velocidades de giro, las elevadas temperaturas y las cargas adicionales impuestas por la conexión al eje que a su vez es movido por la turbina. En el futuro se podrán conseguir reducciones impor- tantes en el peso de los discos gracias a la aplicación de la tecnología bling (blisk+ring). Esto se conseguiría reeplazando las configuraciones actuales de disco con álabes (blisk) por un anillo reforzado de alta resistencia, con los álabes integrados en un único componente. La carcasa del compersor tiene similares funcionalidades y requerimientos que la del fan. Se diseña para tolerar cargas resultantes de las maniobras durante el vuelo. Además, debe contener materiales que se ajusten a la dilatación térmica y centrífuga asociadas al rotor, de cara a mantener unos niveles aceptables de holgura entre la carcasa y los álabes, tanto en régimen estacionario como en los transitorios. Un control inadecuado del ajuste entre el rotor y la carcasa durante los transitorios de la operación supondría una holgura excesiva en punta de álabe, lo que implicaría una merma en la estabilidad del compresor. Al igual que en el fan, la superfi- cie interior contiene materiales abrasibles que se depositan mediante proyección térmica (thermal spray) y que constituyen un recubrimiento esencial a la hora de garantizar la holgura adecuada. Hay varias configuraciones de diseño de carcasa que pueden emplearse: de doble piel, de piel simple e híbrida. La configuración de doble piel es más rígida que la de piel simple y por tanto es más adecuada para aguantar las cargas resultantes de las maniobras en vuelo. Esta configuración también proporciona una solu- ción sencilla para el sangrado de aire. La carcasa de piel simple es más barata, asociada a un menor número de piezas. Habitualmente hay muy poca diferencia entre el peso asociado a ambas configuraciones, ya que la configuración de piel simple lleva aparejada mayores espesores de pared. Algunos compresores emplean un diseño híbrido, combinación entre ambos, con una piel simple en la zona anterior y una piel doble en la zona 15 posterior. La carcasa puede partirse horizontalmente en dos piezas o incluso estar formada por varios anillos. Los materiales típicos empleados son titanio, acero y niquel. Los álabes de estator normalmente se anclan a la carcasa mediante una fijación con un surco en T o una cola de milano, con algún elemento que impida la rotación de los mismos. Estos álabes pueden estar en voladi- zo o anclados a ambos extremos. Los álabes anclados a ambos extremos suelen estar unidos a un disco interior también mediante una fijación con un surco en T o una cola de milano. El diámetro interior del anillo de fijación incorpora un material abrasible, lo que constituye una cara de sellado frente al laberinto de sellado del rotor, de cara a evitar que se escape el aire desde la salida del estator hasta la entrada del mismo. Los álabes anclados en ambos extremos se suelen emplear en las primeras etapas debido a su mayor resistencia al impacto. Los álabes de estator en voladizo son de construcción mucho más simple, y pueden ser usados en etapas intermedias y posteriores. Debido a su simplicidad y menor número de partes, suelen ser más baratos que los anclados en ambos extremos. Se le suele aplicar un recubrimiento al tambor del compresor para proteger el extremo del álabe de estator y ayudar a mantener la holgura adecuada en su extremo. Los materiales típicamente empleados son titanio y acero en las etapas anteriores, y niquel en las posteriores. Cuando se dispone de álabes de estator de incidencia variable, la carcasa se emplea también para montar el sistema de actuación. Cámara de combustión La cámara de combustión tiene la complicada tarea de quemar grandes cantidades de combustible con enormes cantidades de aire procedentes del compresor. El calor ha de liberarse de manera que los productos de la combustión se expandan formando un gasto uniformemente caliente, pero cumpliendo los siguientes requerimientos: Alta eficiencia de la combustión para asegurar una elevada liberación de calor. Rango amplio de estabilidad de modo que la llama permanezca encendida incluso en caso de ingesta de grandes cantidades de lluvia o polvo, y durante aceleraciones rápidas. Ignición fiable en días fríos. Capacidad de reencender el motor a elevadas altitudes. Pérdidas de presión suficientemente bajas para maximizar el rendimiento global del motor, pero sufi- cientes para llevar aire de refrigeración a las turbinas. Perfil de temperaturas a la salida de la cámara de combustión que se ajuste a los requisitos de vida útil de la turbina. Bajas emisiones contaminantes. Alta durabilidad para garantizar fiabilidad y elevada vida útil, y para minimizar las acciones de mante- nimiento. Bajo coste. Bajo peso para contribuir a un menor consumo de combustible, una mayor capacidad de carga y/o a una mayor relación empuje/peso en aviones militares. 16 Hay un equilibrio muy ajustado para garantizar que se cumplen todos estos requisitos de diseño. Las ac- tuaciones de la cámara de combustión se apoyan en cambios sutiles en la admisión de aire, el inyector de combustible y las características de refrigeración. Cualquier cambio que se realiza para mejorar uno de estos aspectos tiene, idefectiblemente, un impacto (a menudo adverso) en el resto. Además de los retos aerotermo- dinámicos, el entorno de alta temperatura, alta presión y alto nivel de vibraciones supone un desafío de gran dificultad desde el punto de vista de la integridad mecánica. Proceso de combustión En grandes turbofanes civiles, el aire puede salir del compresor a una velocidad aproximada de 150 m/s. Esta velocidad es demasiado elevada para que la combustión tenga lugar, de modo que el aire se hace pasar por el predifusor al final del compresor, que consigue reducir la velocidad a 110 m/s. Este valor sigue siendo demasiado elevado para que la llama se estabilice, dado que el frente de llama del queroseno avanza a una velocidad de 10 m/s. Así, una combustión estable sólo puede mantenerse creando regiones de recirculación con velocidades bajas inmediatamente aguas abajo del inyector de combustible. La sección de la cámara de combustión donde tiene lugar dicha recirculación se conoce como zona primaria. El chorro cónico de combustible proveniente de la tobera del inyector impacta con el torbellino de re- circulación en la zona primaria. Esta acción, unida a la turbulencia en la zona primaria, promueve la ruptura del chorro de combustible y su mezcla con el aire. Ambos aspectos son necesarios para asegurar un alto ren- dimiento de la combustión y bajas emisiones. Una chispa eléctrica proveniente del encendedor situado en la zona primaria inicia la llama, que desde entonces ha de ser autosostenida. La temperatura de los gases tras la combustión es de unos 2100 ºC, lo cual es excesivo para entrar direc- tamente en los primeros álabes de estator y en los primeros álabes de rotor de la turbina. Así, para reducir la temperatura del gas se introduce más aire en la zona secundaria de la cámara de combustión, inmediatamente aguas abajo de la zona primaria. Este aire, que accede a la zona secundaria a través de entradas intermedias, juega un papel clave en el control de las emisiones. Finalmente, en la zona de dilución cercana al extremo posterior se introduce más aire para controlar el perfil de temperaturas del gasto a la salida de la cámara de combustión. La combustión debe ser completa antes de que el aire de dilución se introduzca, para evitar que la llama se enfríe con dicho aire y que la combustión continúe en los componentes aguas abajo causándoles un sobrecalentamiento. Los componentes de los aerorreactores suelen poder escalarse para ajustarlos a diferentes ciclos de opera- ción; sin embargo, la cámara de combustión es la menos dada a este proceso de escalado. El parámetro de carga de la cámara de combustión afecta a parámetros operacionales tales como el rendimiento, y las capacidades de encendido y aceleración, de modo que suele usarse para escalar el volumen de la cámara de combustión. En particular, el parámetro de carga es proporcional al gasto másico e inversamente proporcional a la presión de entrada, a la velocidad y a la temperatura de entrada. El rendimiento de la cámara de combustión, que define el porcentaje de combustible quemado frente al total inyectado, es del 100 % en condiciones de despegue, pero se reduce a menores temperaturas y presiones, con mayores parámetros de carga. Para evitar la formación de humo blanco, el rendimiento debe situarse por encima de un 96 %, y desde luego no se acepta que en ningún punto del ciclo de operación adopte un valor inferior al 90 %. En caso de apagado en vuelo a elevada altitud, la cámara de combustión debe ser capaz de reencenderse y “acelerarse” en un tiempo suficientemente pequeño para conseguir que el motor recupere el nivel de empuje necesario para seguir volando. Este tiempo depende de la velocidad a la que puede propagarse la llama y generar calor, y por tanto está directamente relacionado con el rendimiento de la cámara de combustión en condiciones de ralentí. A medida que la presión disminuye, el volumen de una cámara de combustión fijado un parámetro de carga debe ser incrementado; por tanto, las 17 capacidades de encendido y “aceleración” a elevada altitud son clave en el dimensionado del volumen de la cámara de combustión. Arquitectura de la cámara de combustión Hay tres tipos principales de cámaras de combustión empleadas en aerorreactores: La cámara múltiple (o tubular), la cámara anular, y la cámara tubo-anular. La cámara de combustión múltiple, o tubular, está constituida por varias cámaras individuales situadas al- rededor del motor. Cada una tiene un tubo de llama interior con su propia carcasa. Un sistema de conductos dirige el aire desde el compresor hasta cada una de las cámaras, donde a su vez se reparte entre el interior del tubo de llama y la zona entre el tubo de llama y la carcasa de la cámara individual. Los tubos de llama indivi- duales se encuentran normalmente interconectados, lo que permite que la combustión se propague alrededor de los tubos de llama durante el arranque del motor, y también impone que los tubos operen a la misma presión. Esta configuración, que es un desarrollo directo de la cámara de combustión del motor de Whittle, ya no es adecuada para aplicaciones aeronáuticas. En aerorreactores antiguos las cámaras individuales estaban alinea- das paralelas al eje central del motor. Esta arquitectura reduce el tiempo de mantenimiento y puede acomodarse a cámaras de combustiones de mayor tamaño, lo cual puede resultar necesario para controlar las emisiones. Los ensayos de este tipo de cámaras de combustión durante su desarrollo también son más sencillos, ya que la mayoría pueden llevarse a cabo sobre una única cámara individual. La cámara de combustión tubo-anular supuso una evolución respecto de la cámara de combustión múlti- ple, y allanó el camino a las cámaras anulares. En las cámaras tubo-anulares, se disponen varios tubos de llama dentro de una misma carcasa que limita el flujo de aire. Ahora el flujo es similar al que se tiene en las cámaras múltiples, pero no todo el gasto entra en el interior de los tubos; una parte importante entra por el espacio lateral entre tubos de llama, de manera similar a las camaras anulares. La configuración tubo-anular combina la sencillez de realización de ensayos y de overhaul con la compacidad de las configuraciones anulares. La cámara de combustión anular consiste en un único tubo de llama de forma anular, que está contenido en una carcasa interior y otra exterior. La cámara se encuentra abierta en sus extremos frontal y posterior al com- presor y a la turbina, respectivamente. Este tipo de cámara de combustión es predominante en los aerorreactores actuales. Su principal ventaja estriba en que, para la misma potencia instalada, la longitud de la cámara sólo tiene que ser el 75 % de la longitud de una tubo-anular con el mismo diámetro. Esto da lugar a un motor más corto y más rígido, y a una considerable reducción en peso y coste de producción. Una cámara de combustión anular también presenta un área frontal menor que una tubo-anular que tenga el mismo volumen. Otra ventaja es la eliminación del problema de la propagación de la combustión de tubo de llama a tubo de llama. La cá- mara anular tiene una menor superficie de pared que una tubo-anular comparable, y requiere un 15 % menos de aire de refrigeración para evitar que se queme el tubo de llama. Dicho aire puede, por tanto, usarse en el proceso de combustión, lo que ayuda a aumentar el rendimiento de la combustión y a controlar emisiones. Las desventajas de la cámara anular son su mayor debilidad estructural, su mayor complejidad de fabricación y la mayor dificultad de controlar la temperatura de salida de los gases. Los ensayos de desarrollo también resultan más complejos. De hecho, aunque lo adecuado sería ensayar el sistema completo, las restricciones en tiempo y coste llevan a ensayar sectores que pueden contener sólo cuatro inyectores, cuando el sistema completo puede tener del orden de veinte. Las cámaras de combustión anular pueden presentar un diseño directo o de flujo invertido. Las cámaras de combustión de flujo invertido son particularmente compatibles con los compresores centrífugos, y permiten que la distancia entre la salida del compresor y la entrada de la turbina sea del orden de un tercio de la que 18 se tiene con compresores axiales. Este enfoque de diseño puede dar lugar a motores muy compactos, lo cual resulta crítico en el caso de los turboejes de helicópteros. Inyectores de combustible El combustible tiene que ser proporcionado a la cámara de combustión, donde debe mezclarse a fondo con el aire antes de la combustión. Para combustibles líquidos hay dos métodos diferentes de conseguirlo: vapori- zadores y toberas de pulverización. Los vaporizadores son estructuras simples, baratas y ligeras que sirven para mezclar el combustible y el aire. El combustible se inyecta a través de un tubo alimentador o pulverizador en un tubo con forma de L o T, que hace girar la mezcla 180 grados. Las esquinas del vaporizador son típicamente afiladas para la generación de vórtices que promueven la mezcla. Además, se incorporan alambres dentro del vaporizador, lo que aunmen- ta la turbulencia y la mezcla. Aunque se calienta la mezcla aire/combustible dentro del vaporizador, la mayoría de la mezcla abandona el vaporizador e impacta en la superficie de la cámara de combustión formando gotas que son calentadas y vaporizadas por las elevadas temperaturas que se tienen en la zona primaria. Algunos diseños de cámara de combustión requieren añadir funcionalidades específicas tales como anillos de soplado, para alejar el combustible de las paredes y mejorar el rendimiento. El vaporizador se refrigera con el combustible y tiene tendencia a sobrecalentarse cuando el motor se de- celera, debido a que los gases de la combustión en la zona primaria todavía están radiando y conduciendo calor, pero hay poco flujo de combustible para enfriar el vaporizador. También puede sobrecalentarse en caso de bloqueo del conducto de alimentación de combustible. Los vaporizadores han predominado en aplicaciones que requieren inyectores simples, baratos y ligeros, particularmente en turbofanes militares (Ej: Pegasus) o incluso en el Olympus 593 que se montó en el Concorde. No se han empleado en grandes turbofanes civiles por no satisfacer requisitos de durabilidad y emisiones. Aunque los vaporizadores son capaces de porporcionar grandes rendimientos y bajos humos a niveles razonablemente elevados de presión, son incapaces de producir un bajo nivel de humos a los niveles tan elevados de temperatura y presión que caracterizan a los turbofanes de última generación, tanto civiles como militares. Las toberas de pulverización atomizan el combustible para garantizar una rápida evaporación y combustión al mezclarse con el aire. La combustión es un proceso complicado por dos razones: la velocidad del gasto de aire proveniente del compresor crea un entorno hostil para la llama, y la corta longitud del sistema de combus- tión implica que hay muy poco tiempo para que tenga lugar la combustión. Una de las técnicas para atomizar el combustible es hacerlo pasar por una cámara de rotación en la que agujeros o surcos tangenciales le confieren vorticidad. Posteriormente, el combustible se hace pasar por un orificio de descarga donde el combustible se atomiza formando una pulverización cónica. Esta técnica es cono- cida como atomización mediante chorro a presión. La tasa de rotación y la presión del combustible en la tobera de pulverización son factores importantes para una buena atomización. De hecho, la forma de la pulverización es indicativa del nivel de atomización. La tobera de pulverización simplex es un atomizador mediante chorro a presión que tiene un sólo colector de combustible, una cámara de rotación y un único orificio de atomiza- ción de área fija. Empleado en los motores antiguos, este sistema daba buenos resultados a elevados flujos de combustible, pero no a bajos flujos (especialmente a elevadas altitudes). Las toberas de pulverización duplex y duple incluyen dos colectores de combustible, uno primario y otro principal, y dos orificios independientes, uno mucho menor que el otro. El orificio menor sería el responsable de proporcionar los flujos pequeños que procederían del colector primario. A medida que el flujo y la presión de alimentación aumentase, cada vez ten- drían más protagonismo el colector principal y el orificio mayor. Con este sistema se consigue que las toberas 19 de pulverización duplex y duple garanticen una atomización adecuada en un rango más amplio de gastos de combustible que la simplex. La diferencia entre ambas toberas de pulverización estriba en que la duple tiene dos cámaras de rotación, mientras que la duplex tiene sólo una. Las toberas de pulverización airspray emplean el aire a la salida del compresor para crear una pulveriza- ción de combustible finamente atomizada. Aireando la pulverizacióin se evitan las zonas con concentraciones ricas en combustible tan frecuentes en otros tipos de toberas pulverizadoras, lo que da lugar a una reducción en las deposiciones de hollín y en el humo a la salida. Este tipo de toberas de pulverización típicamente tienen dos o tres circuitos de rotación de aire. El combustible dispone de una sección de paso anular entre los circuitos de aire interior y exterior, lo que da lugar a la formación de una película de combustible que posteriormente se rompe en filamentos. A su vez, estos ligamentos se rompen en gotas en las intensas capas de cortadura del aire que presenta elevada vorticidad. En el diseño de las toberas de pulverización airspray no sólo es necesario optimizar la atomización del combustible, sino también hacia dónde se dirigen las gotas. Estas características admiten un ajuste fino controlando la cantidad de aire que entra y su rotación. Una ventaja adicional es que las bajas presiones requeridas para atomizar el combustible permiten el uso de bombas de engranaje, comparati- vamente más ligeras. Encendedores Hay dos tipos básicos de encendedores: los constricted air gap y los shunted surface discharge. El primero de ellos es similar a las bujías de los motores alternativos, pero presenta un espaciado mayor entre electrodos que deberá cubrir el arco voltaico. De hecho, se requieren saltos de tensión del orden de 25000 V para ionizar ese espacio de aire, lo que requiere un muy buen aislamiento en el circuito. El segundo presenta en la punta del aislador un semiconductor (carburo de silicio) que permite la derivación eléctrica del electrodo a alta tensión al cuerpo del encendedor. Esa derivación ioniza la superficie del semiconductor, dando lugar a un camino de baja resistencia para la chispa, lo que permite su operación con saltos de potencial de 2000 V únicamente. La tasa de chispa típica de un sistema de encendido se encuentran entre 60 y 100 chispas por minuto. Es necesario un reemplazo periódico del encendedor debido a la erosión de los electrodos causada por cada descarga. La punta del encendedor tiene un rango de inmersión en el tubo de llama de la cámara de combustión que depende del diseño de la cámara (afecta más o menos un milímetro). La descarga introduce la chispa otros 20 mm hacia el interior del motor, provocando la ignición de la mezcla y posterior propagación por toda la zona de combustión. Las cámaras de combustión anulares modernas suelen presentar dos encendedores diametralmente opuestos. Turbina La primera tarea de la turbina es sobrevivir: Los álabes al rojo vivo operan a temperaturas superiores a su punto de fusión, además de estar resistiendo fuerzas centrífugas del orden de 18 toneladas. La segunda tarea es mover el compresor. Las turbinas convencionales son un conjunto alterno de álabes de estator y álabes de rotor montados en discos que se encuentran conectados a los ejes. Los álabes de estator y de rotor están con- tenidos en una carcasa divergente. La turbina produce potencia mecánica (par aplicado a un eje que gira) que es empleada en mover el fan, el compresor y otros accesorios. En el caso de que no se trate de un aerorreactor, la turbina extrae toda la potencia que puede dejando un chorro muy poco acelerado; dicha potencia se emplea entonces en mover una hélice (sistemas turboeje más hélice), un generador (turbinas de gas industriales), etc. Los bloques de turbina se diseñan, fabrican y ensayan de acuerdo a los siguientes criterios: Proporcionar el empuje requerido. Minimizar el coste. 20 Minimizar el peso. Minimizar el consumo de combustible. Minimizar las emisiones contaminantes. Minimizar los tiempos de suministro. Principios básicos El conjunto turbina se monta aguas abajo de la cámara de combustión, formando el último tercio del gene- rador de gas. Después de haber sido muy comprimido, mezclado con el combustible vaporizado y participado en la combustión, los gases calientes que abandonan la cámara de combustión se expanden, a través de la turbina, hasta una presión y una temperatura más bajas. Esta expansión permite extraer potencia del gas para mantener girando el conjunto de álabes y discos de rotor, además de mover el compresor (y posiblemente otros sistemas) a través de un eje central. Los requisitos de mercado de aerorreactores civiles relativos a bajos consumos de combustible y bajos consumos específicos (por unidad de empuje) empujan el diseño de turbofanes hacia mayores relaciones de derivación. En turbofanes, las turbinas mueven tanto un fan (que produce la mayor parte del empuje) como un compresor de alta presión, que comprime un gasto de aire, dejándolo en unas condiciones adecuadas para el proceso de combustión; algunas turbinas mueven otro compresor entre el de baja (fan) y el de alta. Para producir el par necesario con un rendimiento adecuado las turbinas deben consistir en varias etapas, cada una de ellas formadas por una fila de álabes de estator (Nozzle Guide Vanes) seguida de una de álabes de rotor. El número de etapas empleadas depende de la potencia requerida, la velocidad de giro del eje y el diámetro admisible de turbina. A medida que el gas se expande y se extrae trabajo en cada etapa de turbina, la temperatura y la presión de operación disminuyen en consecuencia. Ello implica que la turbina de presión intermedia no necesite tanta refrigeración ni tan sofisticada como la turbina de alta presión; no obstante, las turbinas de media presión (e incluso las de baja en aerorreactores militares) siguen fabricándose de aleaciones de niquel resistentes a la oxi- dación para minimizar las necesidades de refrigeración y maximizar el rendimiento de la etapa. Aguas abajo, las turbinas de baja de los aerorreactores civiles pueden ser diseñadas para operar sin refrigeración además de que pueden fabricarse en aleaciones que soportan menores temperaturas, ya que la temperatura de los gases es inferior al límite del material. La temperatura de salida de la última etapa de turbina de baja es de unos 550 ºC aproximadamente. Refrigeración de turbinas A unos 1600ºC, los componentes de las turbinas de alta presión situados en la parte más caliente del gasto de aire se han diseñado para operar cinco veces más caliente que un horno convencional. Estas temperaturas son considerablemente mayores que el punto de fusión de las aleaciones de niquel con las que se fabrican dichos componentes. La solución a este problema viene de la mano de la refrigeración. El sistema de refrige- ración reduce en unos 400 ºC la temperatura de los álabes; así, si esta tecnología pudiese aplicarse a un álabe de hielo podría mantenerse congelado durante un tiempo indefinido incluso dentro de un horno doméstico a máxima potencia. Los álabes de la turbina de alta y los segmentos de sellado están, por tanto refrigerados interna y ex- ternamente mediante el empleo de aire más frío tomado de la salida del compresor de alta. Dicho gasto de 21 refrigeración se encuentra a unos 700 ºC (debido exclusivamente al proceso de compresión) y a presiones cer- canas a 4 MPa. La presión a la entrada de la turbina es unos 200 kPa inferior que a la salida de compresor, de modo que la presión de alimentación presenta un margen relativamente pequeño que resulta crítico para la operación. A la hora de decidir si un álabe va refrigerado o no es necesario tener en cuenta la elección del material, el empleo de recubrimientos de barrera térmica (Thermal Barrier Coating), los requisitos de actuaciones y el objetivo de coste del motor. No refrigerar un álabe da una mayor libertad en términos de diseño del perfil aerodinámico, tanto en su tamaño como en su forma, ya que no se tiene que moldear el sistema de refrigeración en su interior; por contra, limita las temperaturas de operación del componente, lo que afecta a sus actuaciones y limita el alcance de un posible crecimiento del motor en el futuro. Los recubrimientos de barrera térmica aisladamente considerados no proporcionan una mejora en la reducción de la temperatura del metal de los ele- mentos no refrigerados. Además, un componente no refrigerado podría tener que ser fabricado en un material mejor, lo que afectaría al coste y fabricabilidad del mismo. Los avances en metalurgía y en tecnologías de moldeo han hecho posible el uso de componentes monocris- talinos de aleaciones de niquel. Las mejoras resultantes en las propiedades del material permiten que dichos componentes puedan ser empleados en turbinas que operan a mayores temperaturas. El empleo de aleaciones de moldeo avanzadas mejora los límites de vida útil permitiendo un uso más eficiente del aire de refrigeración y dando al diseñador una mejor comprensión de las propiedades de los materiales. Las aleaciones de niquel son una solución casi universal para los primeros álabes de turbina de alta, debido a su elevada resistencia al fenómeno de fluencia por cedencia (creep) a alta temperatura. Los componentes monocristalinos presen- tan unas propiedades metalúrgicas superiores en todas las direcciones, pero implican un coste de fabricación mucho mayor. Se pueden moldear aleaciones similares utilizando el método de solidificación direccional, el cual es más barato que la tecnología de monocristal, a cambio de una pequeña reducción en las propiedades del material (además de la introducción de anisotropía), o incluso se puede moldear con granos equiaxiales, reduciendo bastante más el coste y las propiedades. En definitiva, el diseño de la turbina y la selección de los materiales depende del equilibrio entre temperatura de operación, vida útil deseada y coste admisible de los componentes. El diseño de la propia geometría de refrigeración se ha mejorado significativamente a lo largo de los años. Los diseños de agujeros de refrigeración taladrados mediante láser (laser-drilling) y las tecnologías de nú- cleo cerámico soluble han permitido mejores métodos de refrigeración con un mayor nivel de efectividad de la refrigeración en los álabes de rotor y estator. Además, estos métodos han permitido la reducción del gasto necesario para la refrigeración, como también lo ha hecho el empleo de recubrimientos cerámicos de barrera térmica. Los componentes refrigerados admiten una mayor temperatura de operación de la turbina, dando lugar a mayores niveles de empuje, siempre llegando a una solución de compromiso: Si hay que refrigerar un compo- nente es necesario equilibrar la cantidad de aire de refrigeración y la efectividad del diseño de refrigeración. Diseños con elevados flujos de refrigeración implican grandes sangrados del compresor antes de la combustión. Ello impacta en las actuaciones de la turbina de dos formas diferentes: por un lado, se incurre en una pena- lización en el ciclo termodinámico en tanto que no se puede usar el aire de refrigeración para la combustión, reduciéndose la energía transferible en la turbina; por otro lado, se tienen pérdidas aerodinámicas al reintrodu- cir este aire a través de los orificios de refrigeración. Los diseños que presentan la refrigeración más efectiva a menudo suponen incrementos en la complejidad de fabricación y, por tanto, en el coste de los componentes. 22 Componentes de la turbina Todos los componentes de la turbina se diseñan en línea con las reglas de diseño y requerimientos tan exigentes que impone el cliente en cuanto a actuaciones, coste, peso, vida útil y tiempos característicos de fabricación. Un conjunto típico de turbina puede descomponerse en cinco grandes tipos de componentes: car- casas y estructuras, discos, ejes, álabes de estator y álabes de rotor. Carcasas y estructuras Las carcasas forman la estructura exterior de la turbina y encierran los gases calientes que salen de la cámara de combustión. Normalmente se fabrican de acero forjado o de aleaciones de niquel que han de ser suficientemente resistentes para contener las presiones del interior de la turbina. La carcasa también tiene que contener cualquier trozo generado por el fallo de un componente. Las carcasas de las turbinas se diseñan para transmitir las cargas axiales y torsionales impuestas por el conjunto de la turbina. Las estructuras se diseñan para conectar estas carcasas a los rodamientos de soporte del eje interior, transmitiendo las cargas de los roda- mientos a la carcasa y rigidizando el conjunto. Los sistemas de refrigeración y de lubricación tienen que pasar a través de la estructura y de la carcasa. Los siguientes tipos de componentes estáticos se encajan en las carcasas para formar el montaje completo: álabes de estator, sellos y anillos de soporte. Estos componentes son fijados a la carcasa mediante una variedad de métodos incluyendo espigas, garfios y otros elementos. Los segmentos de sellado normalmente forman un anillo periférico de material abrasible alrededor de las puntas de los álabes de rotor. En algunos casos, las aletas de las puntas de los álabes de rotor cortan surcos en los panales de abeja abrasibles del segmento de sellado, generando un laberinto controlado que minimiza la fuga de aire a través de las puntas de los álabes de rotor. Es fundamental el control de las dilataciones de los sellos para que se mantenga una óptima holgura en la punta del álabe de rotor. La dilatación térmica de la carcasa se puede controlar usando aire de refrigeración para mantener unos es- paciados óptimos entre las puntas de los álabes de rotor y los sellos. Este aire de refrigeración se alimenta desde el compresor hasta unos colectores montados en la carcasa. Esto minimiza de manera efectiva las pérdidas en punta de álabe y ayuda a maximizar el rendimiento de la etapa. Estos métodos de control de la holgura pueden ser pasivos o activos y pueden controlarse mediante la modulación de la cantidad de aire de refrigeración. El control de la holgura de punta de álabes permite mayores temperaturas de operación de la turbina y mayores velocidades de giro, sobre todo cuando se emplean álabes de rotor en voladizo. Por último, cabe destacar que la instrumentación que forma parte del sistema de control del motor (ej: termopares) puede tener que atravesar la carcasa para llegar a los componentes estáticos que se encuentran en su interior. Discos La principal función de los discos de turbina es situar y retener los álabes de rotor, permitiendo que las fuerzas circunferenciales que actúan sobre ellos (y que dan lugar a la potencia extraída) sean transmitidas al compresor mediante los ejes centrales. Cada fila de álabes de rotor es anclada en el perímetro de un disco a través de anclajes en la raíz (típicamente en forma de abeto) diseñadas para aguantar las enormes cargas centrí- fugas ejercidas por los álabes girando a elevadas velocidades. Los discos se hacen típicamente de aleaciones de forja de niquel, siendo los materiales de partida cuidadosamente seleccionados e inspeccionados para asegurar la falta de grietas o defectos antes y durante la fabricación del disco. Se han desarrollado aleaciones específicas 23 para aplicaciones de alta resistencia. Las aleaciones actuales y la pulvimetalurgia han incrementado la resis- tencia del material, permitiendo alcanzar mayores velocidades de giro y mayores temperaturas de operación. Los discos de turbina se clasifican como partes críticas, al igual que los discos de fan y compresor. El riesgo de fallo de un disco se mitiga mediante una selección cuidadosa del material y el seguimiento estricto de los criterios de diseño. De hecho, hay que satisfacer los criterios de diseño en cuanto a tensión última a tracción, creep y fatiga. Ejes Los ejes de la turbina tienen tres funciones principales: transmitir el par de la turbina al compresor, trans- mitir las cargas axiales al compresor y a los rodamientos de posicionamiento y aguantar el conjunto formado por los discos y los álabes de rotor. El eje de turbina está montado sobre la estructura gracias a cojinetes lubricados y refrigerados mediante aceite. Pueden ser comunes a los ejes de compresor o estar unidos a los mismos. En turbofanes civiles modernos trieje, los tres ejes giran concéntricamente unos dentro de otros, cada uno a su velocidad óptima. En particular, en condiciones de despegue es típico que el eje de alta gire a unas 10000 rpm, el de media a unas 6000 rpm y el de baja a unas 3000 rpm. Los aerorreactores militares tienden a incluir únicamente dos ejes, cada uno girando a su velocidad óptima, y éstas bastante más elevadas que las de los turbofanes civiles, debido a que los motores tienen diámetros inferiores. Álabes de estator Los NGV se diseñan para convertir parte de la energía de presión y térmica del gasto de aire en energía cinética convenientemente ajustada para que los álabes de rotor puedan extraer potencia. Se diseñan de manera que se rota el fluido en la dirección de rotación del rotor, maximizando así el rendimiento del rotor. Haciendo esto, se incrementa la cantidad de movimiento tangencial del gas. Por tratarse de elementos estáticos son mon- tados en la carcasa, y se diseñan para aguantar las cargas axiales y de torsión que el gasto de aire les confiere, además de para reaccionar térmicamente sin inducir elevadas tensiones internas en el conjunto. Se posicionan mediante ganchos o raíles mecanizados que se fijan mediante espigas o pasadores, y se aguantan circunferen- cialmente gracias a mecanismos anti-rotación montados en la carcasa. Presentan el juego necesario para poder permitir dilataciones térmicas sin permitir que se den fugas de aire. El ensamblaje de una corona de álabes de estator da lugar a una serie de ventanas de paso del aire que constituyen “gargantas” desde el punto de vis- ta aerodinámico. Los álabes de estator actuales presentan unos perfiles aerodinámicos cada vez más complejos. Los álabes de estator de alta y media presión de los turbofanes civiles actuales suelen estar refrigerados, mientras que los de baja presión no lo suelen estar. Por su parte, los diseños militares presentan álabes de estator de alta y de baja refrigerados. Los componentes refrigerados internamente se fabrican mediante moldeo con moldes de geometrías complejas que maximizan la efectividad del aire comprimido que se emplea para refrigeración. Dicho aire se proporciona al álabe de estator a un nivel de presiones superior al del fluido que envuelve al álabe; de modo que la diferencia de presiones es el motor del movimiento del gas por el interior del álabe y a través de los orificios del mismo, envolviendo al componente en una capa fría sin la cual la tem- peratura del componente pronto superaría su punto de fusión. Para reducir las necesidades de gasto sangrado de refrigeración, las soluciones actuales incluyen el empleo de aleaciones monocristalinas de Niquel así co- mo recubrimientos cerámicos de barrera térmica. Esta última tecnología reduce la conductividad térmica del componente, dando lugar a una menor temperatura de equilibrio en la superficie del metal. 24 Álabes de rotor Los álabes de rotor de la turbina se diseñan para extraer potencia gracias a la generación de fuerzas aero- dinámicas circunferenciales en los perfiles aerodinámicos del disco que se encuentra girando. Los álabes de rotor se diseñan con perfiles aerodinámicos avanzados que proporcionan gargantas de paso entre cada par de álabes adyacentes a las que llega un fluido que ha sido acelerado hasta la velocidad adecuada para contrarrestar la rotación impuesta en el estator. Los álabes rotan en el interior de la carcasa a velocidades típicas de unos 450 m/s. A esta velocidad, la potencia extraída por un álabe de alta de un turbofán civil es diez veces superior a la de un automóvil familiar pequeño, y la fuerza transmitida por un sólo álabe al disco es aproximadamente de 180 MN. El diseño de la sección transversal de un álabe de rotor viene dada por las tensiones admisibles asociadas al material que se haya empleado y por el tamaño de los conductos longitudinales que se requieran para la refrigeración. Los álabes que operan a las mayores temperaturas se moldean a partir de aleaciones de níquel de alta temperatura, mediante la técnica de moldeo a la cera perdida, y suelen recubrirse de una TBC cerámica tanto en la zona de perfil aerodinámico como en sus bases. Al igual que los álabes de estator, las elevadas temperaturas de opera- ción fuerzan la necesidad de una refrigeración interna, que se consigue mediante un sistema de complicados canales internos que dirigen el aire de refrigeración hasta su salida a través de hileras de agujeros. El flujo de aire de refrigeración es perjudicial para las actuaciones de la turbina, de modo que debe regularse con especial cuidado. Aunque los álabes operen al rojo vivo tienen que ser capaces de aguantar las cargas centrífugas asociadas al giro y los momentos flectores asociados a las fuerzas aerodinámicas. Además, deberán resistir los fenómenos de fatiga, choque térmico, corrosión, oxidación y creep. De hecho la vida a creep y la resistencia a oxidación determinan la vida útil de los álabes de rotor. Típicamente, los álabes de rotor de turbofanes civiles se diseñan para trabajar en condiciones de operación durante 35000 horas antes de ser revisados o reemplazados. En una aeronave que vuele 14 horas al día, ese número suponen más de 6 años bajo las alas y 15 millones de millas de vuelo. Sistemas de transmisión La transmisión de potencia la llevan a cabo cuatro conjuntos de componentes: Las estructuras de soporte de rotor, las cajas de engranajes, los ejes de transmisión y los rodamientos. Estos grupos de componentes son muy diferentes en cuanto a forma, pero presentan dos funciones en común: la transmisión de potencia mecánica, así como el sostén y posicionamiento de otros componentes del motor. En los aerorreactores, las cajas de engranajes proporcionan potencia mecánica a ciertos accesorios movi- dos por el motor. La caja de engranajes externa proporciona un punto de unión de los accesorios y distribuye potencia mecánica hacia o desde cada unidad accesoria. Los ejes transmiten potencia tanto desde la turbina al compresor, que puede alcanzar del orden de 75 MW, como desde los engranajes cónicos hasta la caja de engra- najes externa. Por último, los rodamientos proporcionan el posicionamiento axial y radial de los componentes que rotan; los rodamientos de rodillos sólo proporcionan posicionamiento radial. Estructuras de soporte de rotor Principalmente, la estructura exterior del motor es un depósito a presión que contiene aire caliente circu- lando. Las estructuras de soporte del rotor se extienden hacia el interior del depósito a presión para sostener los componentes rotativos del motor, a la vez que permiten que el gasto primario del motor pase a través de 25 dichos componentes. Normalmente son circulares, con una serie de columnas o álabes de estator uniendo los anillos exterior e interior, y un alojamiento de rodamiento situado en el centro. Dentro de los alojamientos de rodamientos los rodamientos permiten una rotación libre de los rotores, aunque manteniendo un centrado pre- ciso. En el exterior, las estructuras de soporte pueden proporcionar puntos de anclaje para elementos externos del motor, o incluso puntos duros para la unión del motor al avión y la transmisión de las cargas de empuje del motor. Las estructuras de soporte se unen entre sí a través de las carcasas de compresor y turbina formando un armazón de soporte completo. Dicho armazón transmite las cargas generadas en los rotores a la estructura fija exterior del motor. Dicha estructura exterior recoge todas las cargas y las transmite al avión a través de los puntos duros (engine mounts). Nótese que ante maniobras del avión la estructura de soporte debe ser capaz de asegurar el correcto centrado de los elementos giratorios. Las cargas del rotor entran en las estructuras de soporte a través de los rodamientos, que se encuentran dentro del anillo por el que circula el gasto de aire. Son las columnas o álabes de estator los que transmiten las cargas, atravesando el gasto de aire, a la estructura fija exterior. Dichas columnas o álabes de estator deben minimizar las perturbaciones y las pérdidas de presión de remanso ocasionadas al gasto de aire. En particular, los álabes son más eficientes y se usan para redireccionar el flujo. Las columnas o álabes de estator también proporcionan un camino para que el aceite lubricante llegue a las cámaras de los rodamientos y vuelva de los mismos. El diseño mecánico de las estructuras de soporte debe ser tal que garantice un amplio rango de operación segura y fiable, además de dar lugar a estructuras lo más ligeras posible. En zonas más frías las aleaciones ligeras de aluminio o magnesio funcionan bien. En zonas con temperaturas moderadas, las aleaciones de Ti- tanio, aunque más caras, proporcionan las cualidades requeridas de elevada resistencia mecánica, bajo peso y resistencia térmica. En las zonas muy calientes, sólo las aleaciones pesadas como las de Niquel proporcionan suficiente resistencia a altas temperaturas. El empleo de Métodos de Elementos Finitos está a la orden del día para llegar a soluciones estructuralmente más eficientes. La zona más interior de la estructura es la cámara de rodamientos, que proporciona un entorno favorable para la operación de los mismos. En su interior las toberas de aceite distribuyen la lubricación necesaria a los rodamientos y los engranajes. Alrededor de los ejes, los sellos de laberinto evitan que el aceite se escape y limitan la entrada de aire caliente a dicha cámara. En las familias de turbofanes RB211 y Trent se emplean cuatro estructuras de soporte de los rotores: la estructura de soporte frontal, la carcasa intermedia, la estructura HP/IP y la estructura de soporte trasera. 1) La estructura de soporte frontal da apoyo a los rotores del fan (rotor LP) y del compresor de media presión (rotor IP). Así, la cámara de rodamientos contiene el rodamiento frontal del eje de baja y el rodamiento frontal del eje de intermedia. Los álabes de estator del fan juegan no sólo un papel aerodinámico sino también de conexión de las superficies interior, intermedia y exterior (transmiten cargas) y de rutado de aire y aceite. 2) La carcasa intermedia es una estructura entre el compresor de media y el de alta presión que aloja los principales rodamientos de transmisión del empuje y los puntos de anclaje del motor. Esta carcasa contiene los rodamientos de apoyo intermedio de los ejes de baja y de media, y de apoyo delantero del eje de alta. Estos rodamientos transmiten las fuerzas axiales de los tres rotores, de manera que deben restringir los movimientos a lo largo del propio eje (rodamientos de bolas). Por lo tanto, a diferencia del resto de estructuras de soporte, la carcasa intermedia debe aguantar cargas no sólo radiales sino también axiales, y podría decirse que es este elemento el que tira del avión en vuelo. La carcasa intermedia también aloja la caja de engranajes interna, que contiene un eje que acaba en un engranaje cónico y que conecta el rotor de alta presión con la caja de 26 engranajes externa; dicha conexión es esencial para el arranque del motor y para el sangrado de potencia para sistemas auxiliares (bomba de aceite, generadores, etc.). 3) La estructura de soporte HP/IP se localiza entre los discos de turbina de alta y de media presión para proporcionar apoyo trasero a los rotores de alta y de media. La particularidad de esta estructura de soporte con- siste en las condiciones de operación tan exigentes a las que está sometida. Está rodeada por elementos muy calientes y debe transmitir las cargas atravesando el gasto de salida de la turbina de alta, que puede considerarse entre los puntos más calientes del motor. Las columnas que conectan la estructura interna con la carcasa de la turbina sólo pueden ser refrigeradas con el aceite que circula hacia el interior, camino de los rodamientos. Debido a la interacción que la estructura de soporte establece entre la carcasa exterior y el rotor, su papel es esencial en el mantenimiento de una holgura adecuada en la punta de los álabes de rotor. Por ello, debe presen- tar una rigidez suficiente para aguantar maniobras extremas manteniendo una adecuada vida a fatiga. 4) La estructura de soporte trasera aguanta el extremo posterior del rotor de baja, y contiene los puntos de anclaje traseros. Una particularidad de esta estructura es que sus álabes de estator no sólo conducen aire y aceite sino también cables de instrumentación. Cajas de engranajes Al aerorreactor se le exige también que proporcione potencia mecánica a una serie de accesorios, que pue- den estar estrictamente relacionados con la operación del motor o bien prestar servicios al avión. Entre los accesorios típicos que dan servicio al motor podemos citar el arrancador, la bomba de combustible, la bomba de aceite, el alternador y el breather. Entre los accesorios típicos que dan servicio al avión destacan los genera- dores y las bombas hidráulicas. El elevado nivel de dependencia respecto de estas unidades requiere un sistema de transmisión extremadamente fiable que transfiera potencia desde la parte más interna del motor, la caja de engranajes interna, hasta la parte más externa, la caja de engranajes accesoria montada en la carcasa del fan. A modo de referencia, el consumo de potencia auxiliar en un turbofán trieje puede llegar a ser del orden de 350 kW, proporcionado a velocidades de giro que pueden llegar a ser del orden de 15000 rpm. Caja de engranajes interna Por un lado, la localización de la caja de engranajes interna viene impuesta por la necesidad de girar el rotor de alta presión para el arranque de los aerorreactores. Por otro lado, puede usarse cualquier rotor pa- ra sacar potencia para los elementos accesorios. Históricamente, la solución más sencilla ha sido emplear el mismo engranaje cónico tanto para sacar potencia como para el propio arranque. Las soluciones tecnológicas que sacan potencia de un eje distinto del que se gira para el arranque introducen la necesidad de engranajes cónicos adicionales (con el consiguiente aumento de complejidad). Sin embargo, extraer potencia accesoria del eje de media o incluso del eje de baja introduce una serie de ventajas que incluyen la reducción del consumo de combustible y la mejora en la operabilidad del motor. La lubricación y refrigeración de los engranajes cónicos y de los rodamientos se lleva a cabo gracias al suministro de aceite. El aceite empleado debe ser retirado, por un lado, para minimizar las pérdidas de poten- cia por fricción viscosa (entre el propio aceite y los elementos cercanos que se encuentran girando a elevada velocidad) y el consiguiente calentamiento del aceite. Esto se consigue gracias a una bomba que succiona el aceite a través de agujeros estratégicamente situados. Un eje radial transmite la potencia desde el engranaje cónico hasta la caja de engranajes accesoria, y trans- mite el par necesario para girar el eje de alta en el arranque del motor. Dicho eje debe ser todo lo esbelto que su 27 diseño mecánico permita, para que quepa en el interior de una columna (o álabe de estator) y cause la menor perturbación del gasto de aire posible. Normalmente, en turbofanes trieje, el eje radial se sitúa dentro de una de las columnas de la estructura de carcasa intermedia. Caja de engranajes intermedia Debido a que la caja de engranajes accesoria suele encontrarse relativamente lejos de la caja de engrana- jes interna, resulta necesario incluir una caja de engranajes intermedia, situada en la carcasa del compresor. Gracias a este punto intermedio se tiene un eje radial corto que opera a alta velocidad entre las cajas interna e intermedia, y un eje inclinado largo que opera a menor velocidad entre las cajas intermedia y accesoria. Al igual que el eje radial era rutado por una de las columnas fuseladas de la estructura de carcasa intermedia, el eje inclinado debe ser rutado por una columna que lo proteja del gasto secundario que sale del fan y le dé un contorno fuselado. Análogamente, interesa que el eje inclinado sea lo más esbelto posible para no obstruir ni perturbar demasiado el gasto secundario. Caja de engranajes accesoria Esta caja aloja los consumidores de potencia accesorios. Presenta una forma de luna para ajustarse a la carcasa del fan y que así la carena del motor tenga la menor área transversal posible (lo que reduce la resisten- cia aerodinámica). Se suele localizar en la parte inferior del motor, para permitir el acceso en tierra de cara a operaciones de mantenimiento. Para minimizar el riesgo de incendio, los equipos eléctricos deben estar lo más separados posible de los que trabajan con fluidos. Así se tienen un lado “seco”, con el generador de potencia eléctrica para el avión y un alternador de imanes permanentes para generar la potencia eléctrica de los equipos del motor, y el lado “mojado”, con las bombas de combustible, de hidráulica y de aceite. Los distintos ejes de transmisión a cada accesorio presentan una entalla, de tal manera que si el accesorio falla impidiendo su rotación, el eje principal de engranajes no se vería dañado. Esta característica no la tienen aquellos ejes destinados a mover unidades accesorias consideradas primarias para el motor, como son las bom- bas de combustible, ya que estas unidades son vitales para el funcionamiento del motor y su fallo podría hacer necesario el apagado del motor. El arrancador es el que impone los mayores momentos al sistema, de modo que es el que lo dimensiona en su diseño. De hecho, se suele situar lo más cercano posible al eje inclinado que viene de la caja de engranajes intermedia, para así evitar tener que reforzar todo el conjunto de engranajes (lo que implicaría un importante aumento de peso). Hay dos funciones adicionales que cumple la caja de engranajes accesorias, a través de dos de sus com- ponentes: el breather y el rotator. Por un lado, el breather permite que el aire a presión que ha escapado por los laberintos de sellado y ha llegado a la cámara de rodamientos escape sin arrastrar parte del aceite. Básica- mente, el aire y el aceite son separados por decantación mediante centrifugación. Por otro, el rotator permite la rotación a mano del motor durante labores de mantenimiento, lo que permite la inspección de los componentes rotativos del motor haciéndolos pasar por ciertos puntos de acceso. Ejes Los ejes internos de los aerorreactores son parte fundamental de los elementos rotativos. El primer objeti- vo es transmitir la potencia desde los productores (las turbinas) hasta los consumidores (compresores y fan), aunque también van a transmitir cargas axiales, transversales, de torsión y de flexión. El eje de alta presión es el más exterior (por lo tanto el de mayor diámetro) y el de menor longitud, con lo que resulta ser el más rígido. Por ello, las soluciones tecnológicas pasan por apoyarlo exclusivamente en dos puntos (sus extremos). 28 El eje de media presión es más largo y delgado, de modo que es demasiado flexible para sólo apoyarlo en sus dos extremos. Por ello se suele apoyar en un punto intermedio adicional. El eje de baja es todavía más largo y de menor diámetro, con lo que también resulta necesario apoyarlo en tres puntos. Nótese que el fan genera la mayor parte del empuje y absorbe la mayor parte de la potencia transmitida por los ejes, lo cual unido a que el eje es el de menor diámetro y el que gira más lento, da como resultado que en el eje de baja se tengan las mayores tensiones. El criterio de diseño más importante de los ejes es el de fallo seguro, para garantizar la integridad del avión en caso de fallo del motor. En cuanto a materiales empleados, lo habitual es recurrir a los aceros de alta resistencia, pero con recubrimientos (epoxy y aluminio) que mejoren la resistencia a corrosión. Al aumentar la relación de derivación cada vez se exigen mayores pares aplicados en menores diámetros de eje, lo que hace que la vida a fatiga comience a ser un problema. Por ello se está recurriendo a aleaciones de Niquel y Cromo para ejes de turbina, ya que incrementan la vida a fatiga y a creep a la vez que son resistentes a la corrosión. Otra alternativa son las aleaciones de acero basadas en hierro puro (refinado electrolíticamente) con pequeños contenidos en fósforo y azufre que le dan una alta resistencia a fatiga; sin embargo, la dureza de estas aleacio- nes es tal que la mecanización de las piezas es un verdadero reto. Los tres tipos básicos de unión de los ejes son las uniones atornilladas (las más baratas), los acanalados (similares a un engranaje) y los acoplamientos curvic. Rodamientos Los rodamientos porporcionan una forma de posicionar de manera precisa los rotores a la vez que se transmiten grandes fuerzas con muy poca oposición al giro. En los aerorreactores se suelen emplear mayorita- riamente los rodamientos, aunque en contadas ocasiones se han usado cojinetes de deslizamiento. En particular, se emplean rodamientos de bolas y rodamientos de rodillos. Los rodamientos de bolas soportan cargas radiales y axiales, mientras que los de rodillos sólo soportan cargas radiales al permitir el deslizamiento en la dirección del eje. Emplear un único rodamiento de bolas para la transmisión del empuje y uno o varios rodamientos de rodillos para aguantar el eje permite el posicionamiento en el rodamiento de bolas y la libertad del eje para alargarse o acortarse en los rodamientos de rodillos, evitando la aparición de fuerzas de reacción adicionales por imponer que la estructura sea hiperestática. Los rodamientos se pueden emplear tanto entre un elemento que gira y otro fijo, como entre dos elementos rotativos. Por ejemplo el rodamiento de transmisión de empuje del eje de baja en turbofanes trieje civiles pue- de montarse conectando los ejes de baja y de media. Además, todos los ejes giratorios que haya en el motor deben montarse en rodamientos, incluyendo los ejes radial e inclinado de transmisión de potencia a la caja de engranajes accesoria, así como los ejes dentro de la misma. Todos los rodamientos consisten en un anillo interno, otro externo, una jaula y los elementos que ruedan. Uno o ambos de los anillos presenta una acanaladura para guiar los elementos que ruedan. La jaula es necesaria para mantener el espaciado entre los elementos que ruedan, que se encuentran atrapados en unos vaciados. La jaula presenta una holgura respecto a ambos anillos, pero normalmente se encuentra fundamentalmente en uno o en otro anillo dependiendo de la aplicación concreta. Para asegurar que la jaula gira de manera concéntrica la holgura entre ésta y el anillo en que se sitúa es pequeña y se encuentra bien lubricada para evitar desgaste por rozamiento. Rodamientos de bolas 29 Los rodamientos de bolas, caracterizados porque sitúan axialmente los ejes y permiten la transmisión de fuerzas de empuje, se encuentran situados en la caja de engranajes interna en los turbofanes trieje y en la ma- yoría de los turbofanes bieje. Al estar situados en una zona relativamente fría del motor se simplifica el diseño de la transferencia de cargas en la estructura. El control preciso de la posición axial es fundamental para el control de las holguras de punta de álabe en el compresor. Los rodamientos de bolas se clasifican atendiendo a qué partes son divididas en varias piezas para su mon- taje. En los deep groove, los anillos interno y externo se hacen en una sola pieza, y es la jaula la que debe partirse en dos piezas para permitir su montaje. Las acanaladuras tienen un único radio de curvatura de modo que las bolas sólo presentan un punto de contacto con cada anillo. Por ello, su uso se restringe a aplicaciones con cargas radiales moderadas y cargas axiales pequeñas. En los de acanaladura en dos piezas, el anillo externo y la jaula se hacen en una sola pieza, mientras que el anillo interno está dividido en dos mitades, lo que permite el montaje del mismo. Cada mitad del anillo interno presenta una acanaladura con un sector de circunferencia que no tiene el mismo centro, de modo que la acanaladura final presenta una forma de arco ojival gótico, permi- tiendo que la bola tenga dos puntos de contacto y por tanto puedan soportarse mayores cargas radiales y axiales. Rodamientos de rodillos Los rodamientos de rodillos, caracterizados porque sólo soportan cargas radiales y permiten los cambios de longitud de los ejes debidos a dilataciones térmicas, suelen encontrarse situados en los extremos de los ejes de turbina y compresor. En estos rodamientos el anillo interno es en realidad parte integral del propio eje, lo que reduce complejidad, peso y acumulación de tolerancias de concentricidad. 30 2.2 SISTEMAS FLUIDOS Sistema de aire interno Parte del aire comprimido no contribuye directamente a la generación de empuje (o de potencia mecánica), sino que se usa para funciones vitales para la operación segura y eficiente del motor: refrigeración, sellado y control de las cargas sobre los rodamientos. Además, existe un sangrado asociado a las demandas de ciertas funcionalidades del avión. Estos flujos internos de aire, así como el conjunto de equipos físicos para direccio- narlos definen el sistema de aire interno del motor. Funciones del sistema de aire interno Refrigeración Las principales necesidades de refrigeración vienen impuestas por la cámara de combustión y la turbina (elementos que operan a las mayores temperaturas), aunque la cámara de combustión se refrigera con el propio gasto de aire principal. En cuanto a la refrigeración de los álabes de turbina cabe destacar que viene asociada a la voluntad de aumentar progresivamente la temperatura fin de combustión, acercándose progresivamente a la temperatura estequiométrica, para así incrementar el rendimiento motor. El empleo de refrigeración implica sangrados de aire que empeoran la operación del motor de modo que habrá que llegar a un compromiso en la selección de la temperatura fin de combustión y de las necesidades de refrigeración. Actualmente los álabes refrigerados emplean una serie de estrategias para maximizar la eficiencia de la refrigeración (con costes tanto mayores cuanto más compleja sea la estrategia): varias entradas de aire, varias pasadas dentro del álabe, creación de capa límite fría, empleo de materiales avanzados que simulan medios porosos. En cuanto a la refrigeración de discos y ejes de turbina, las necesidades vienen asociadas a los intensos fenómenos de conducción que se establecen con el gasto primario a través del área de contacto álabe-disco. El aire de refrigeración fluye axialmente por el diámetro interior del disco y radialmente por las caras del disco. La capacidad calorífica del disco combinada con la transferencia de calor por convección entre el aire y las caras del disco dan lugar a gradientes de temperatura en el mismo, sobre todo durante las fases de aceleración y deceleración. Esto genera unas cargas térmicas asociadas a las contracciones y expansiones no uniformes, que contribuyen a la tensión cíclica que aparece en los análisis de vida a fatiga. El aire de refrigeración que se suministra a la carcasa de la turbina atiende a tres razones: por un lado constituye una vía para hacérselo llegar a los álabes de estator, por otro lado proporciona refrigeración para mantener la resistencia del material de la carcasa y por último, permite controlar las dilataciones térmicas de la carcasa, controlando la holgura en las puntas de álabes de rotor durante los transitorios en la operación. Además, por razones de seguridad, las temperaturas externas del motor deben permanecer por debajo de la temperatura de ignición del combustible. Cabe destacar que ciertos accesorios (como el generador eléctrico) generan un flujo de calor significativo que se debe disipar para que la unidad se mantenga en una temperatura de operación aceptable. El aire de refri- geración puede tomarse directamente de etapas bajas del compresor o bien del exterior, para lo que es necesario sangrar parte del aire del compresor para inducir la entrada mediante efecto venturi de aire del exterior. 31 Sellado El sellado tiene como objetivo minimizar las penalizaciones asociadas a las pérdidas de aire hacia afuera, entre componentes del motor y entre etapas de la turbina. El sistema de aire interno incluye sellos entre partes rotando y partes estáticas, entre partes rotando en el mismo sentido, entre partes rotando en sentidos contrarios y entre partes estáticas. Los sellos deben garantizar también que un determinado nivel de gasto de aire de refri- geración sea rutado convenientemente hasta llegar a su objetivo. La segunda función de los sellos es evitar la pérdida de aceite de dentro de las cámaras de rodamientos, lo que podría provocar efectos no deseados (fuego en el motor, olor en cabina, humo visible). La última función de los sellos es minimizar la ingestión de aire del gasto primario en las cavidades de los discos de turbina. Control de las cargas en los rodamientos El gasto de aire pasando por los distintos componentes determina la aparición de una fuerza axial que actúa hacia adelante (como un empuje) en el compresor y el fan, y hacia atrás (como una resistencia) en la turbina. Los ejes que unen compresores y turbinas experimentan unas fuerzas axiales que son la suma de la que ejerce el compresor, la que ejerce la turbina y la que ejerce el aire de refrigeración sobre los discos de cada uno y sobre el propio eje. Mediante la modificación de la posición de los elementos de sellado se pueden controlar las cargas ejercidas por el sistema de aire interno, controlando así las cargas que aparecen sobre los rodamientos. Suministro de aire de sangrado para otras funcionalidades Se sangran cantidades significativas de gasto primario para servicios del avión, que incluyen presurización y acondicionamiento térmico de cabina, y antihielo del avión. El sistema de control del avión gestiona las demandas de aire de sangrado, tomándolo de las etapas de menor presión siempre que sea posible, de cara a minimizar las penalizaciones en eficiencia del motor. El sangrado del compresor afecta al sistema de aire in- terno al cambiar el punto de operación del compresor. Si el aire de sangrado externo se toma del mismo punto que el de refrigeración, la presión disponible para ese sistema de aire interno cambia al hacerlo las demandas de aire de sangrado externo. Elementos del sistema de aire interno Agujeros, conductos y surcos de área fija Para hacer llegar un flujo de aire de un punto a otro hay que generar un camino de paso, lo que en muchas ocasiones implica agujerear ciertos componenes que obstaculizan dicho paso de aire. Incluso en los casos más sencillos de agujeros circulares conectando dos regiones a diferente presión, el gasto de aire que circula depen- de de numerosos factores, entre ellos los efectos de viscosidad y compresibilidad. Puede decirse que el gasto de aire depende de la geometría del agujero (espesor, forma, perfil), el salto de presiones aguas arriba y aguas abajo, y la temperatura aguas arriba. La velocidad que traiga el aire también es un factor: no debe ser paralela al eje del agujero a menos que el agujero se sitúe en un elemento rotativo que gira a una velocidad diferente de la vorticidad que trae el aire incidente. Sellos rotativos Los sellos rotativos se sitúan entre dos partes, una o ambas de las cuales se encuentran girando (si ambas giran, debe haber una diferencia de velocidad y/o sentido de rotación). La mera consideración de una pequeña holgura entre un eje y un anillo ya constituye un sello, pero los sellos rotativos modernos incluyen caracte- 32 rísticas especiales que ayudan a minimizar las pérdidas de aire creando caídas de presión que suponen una resistencia al paso de aire. Los sellos tienen que ser capaces de soportar desplazamientos relativos axiales y radiales de los componentes durante el vuelo. Los sellos de laberinto son ampliamente usados en los aerorreactores. El principio de funcionamiento con- siste en crear una resistencia al paso de aire obligándolo a atravesar una serie de aletas situadas próximas al revestimiento exterior del sello. Las pérdidas de presión aparecen al obligar al aire a acelerarse y expandirse sucesivamente entre cada aleta. Para absorber movimientos radiales es necesario que, o bien las aletas nunca toquen el revestimiento, o bien que se empleen en el revestimiento materiales abrasibles que toleren un cierto roce. Lo habitual es que tras el arranque inicial del motor, las aletas dibujen unos surcos en el material abrasible llegando a la máxima penetración radial; de esta manera, en la operación posterior no vuelve a producirse roce, salvo en ciertos transitorios asociados a maniobras del avión o aterrizajes complicados. Cuando los sellos de laberinto se aplican a elementos en contrarrotación el material abrasible suele sustituirse por un fino anillo de aceite, de modo que si las aletas penetran en el aceite no se produce tanta disipación de calor como con el material abrasible. Los sellos de escobillas y láminas se caracterizan por presentar el contacto constante de unos alambres (o unas láminas, respectivamente) inclinados en la dirección de rotación del componente rotativo. Con este tipo de sellos se consiguen muy bajas fugas de aire, a la vez que se permiten desalineaciones y movimientos radiales relativos entre los dos componentes. Este tipo de sellos no se suelen emplear para sellar las cámaras de rodamientos, ya que los trozos de alambre rotos podrían contaminar el aceite y provocar fallos prematuros en los rodamientos. Los sellos de carbono suelen usarse en el sellado de aceite de las cámaras de rodamientos y en las cajas de engranajes. Se caracterizan porque se encuentran ligados al componente estático pero con un contacto perma- nente y a compresión sobre una superficie del elemento rotativo. Ello genera unas necesidades de refrigeración normalmente satisfechas mediante aceite. Algunos sellos de carbono consiguen generar unos colchones de aire que disminuyen considerablemente la fricción (casi la anulan) y las necesidades de refrigeración asociadas. Los sellos de anillo se emplean en el sellado de cámaras de engranajes formando una holgura muy pequeña entre el anillo estático y el eje rotativo. El anillo está algo suelto en su alojamiento en el elemento estático, de modo que puede moverse en caso de que el eje se desplaze y contacte con el anillo. Por último los sellos hidráulicos se suelen emplear en el sellado de cámaras de engranajes entre ejes rotan- do en el mismo sentido. En estos sellos se genera una película de aceite en el elemento más exterior debido a efectos centrífugos. En el elemento interior existe una aleta que gira sumergida en el aceite. La diferencia de presiones en el aire fuera y dentro de la cámara de rodamientos se compensa mediante el establecimiento de una diferencia en el nivel del aceite a ambos lados de la aleta. El aceite es progresivamente repuesto durante la operación para evitar su calentamiento excesivo. Sellos estáticos Se suelen emplear entre estructuras que no han podido ser unidas de otra forma debido a necesidades de montaje o para absorber movimientos asociados a dilataciones térmicas, como carcasas de turbina, segmentos de álabes de estator, plataformas de álabes de rotor, etc. Se denominan estáticos haciendo referencia a la au- sencia de movimiento relativo, aunque ambas partes pudiesen estar girando conjuntamente. 33 Cavidades Entre los discos de turbina y compresor y las estructuras estáticas se forman cavidades que constituyen conductos a través de los cuales se suministra el aire. Los requisitos del sistema de aire interno no influyen fuertemente sobre el tamaño, forma y disposición de estas cavidades, pero se debe tener en cuenta el efecto de las mismas en la actuación del sistema de aire interno. Algunos elementos pueden requerir modificaciones para aprovecharse o protegerse (según corresponda) de dichos efectos. Sistema de combustible La tencnología moderna de computadores digitales, en la forma del sistema FADEC (Full Authority Digital Engine Control) ha ofrecido la oportunidad de reducir enormemente la complejidad de los sistemas hidrome- cánicos y neumáticos a la vez que se añade flexibilidad al avión. El controlador electrónico del motor (EEC) es la inteligencia central de control en un sistema FADEC, con el software del EEC sustituyendo a la mayoría de elementos neumáticos e hidromecánicos del sistema de combustible. El sistema de combustible FADEC consiste en un circuito de baja presión y un circuito de alta presión. El combustible se proporciona desde los tanques de combustible a la bomba de combustible de baja presión través del sistema de combustible del avión. La bomba de combustible de baja presión proporciona la presión suficiente para superar las pérdidas en el sistema de baja presión y proporciona combustible presurizado a la bomba de alta presión. El intercambiador de calor entre el combustible y el aceite (Fuel Oil Heat Exchanger, FOHE) proporciona refrigeración del aceite y calentamiento del combustible. El filtro principal de baja presión protege la bomba de alta presión y los elementos aguas abajo de los contaminantes que lleve el combustible. La bomba de combustible de alta presión proporciona combustible a presiones superiores a la que se tiene en la cámara de combustión para garantizar un gasto de combustible suficiente para satisfacer las demandas del motor. La unidad de dosificación del combustible (Fuel Metering Unit, FMU) controla el gasto de combustible consumido en respuesta a las demandas del FADEC. El filtro de alta presión proporciona la protección final a los inyectores de combustible. El colector de combustible distribuye el combustible a los diferentes inyectores, cuyo funcionamiento ya se ha explicado. Operación del sistema de combustible Un vuelo típico consiste en diferentes fases que se han de considerar al diseñar el sistema. En el arranque se abren la válvula de dosificación del FMU y la válvula de corte (shut off ), permitiendo que el combustible sea suministrado desde las bombas hasta la cámara de combustión sin ningún tipo de dosificación (operación en bucle abierto). A continuación del arranque, el combstible comienza a ser dosificado y el sistema se controla en bucle cerrado. El motor funciona a ralentí durante la fase de taxi, y se calienta el sistema de lubricación hasta la temperatura adecuada para la aceleración de despegue. Al demandar potencia de despegue, el sistema de combustible es capaz de suministrar el gasto máximo de combustible a la presión máxima. A medida que el avión sube tras el despegue, el gasto de combustible y la presión necesarios disminuyen hasta que se alcanza la altitud de crucero. A la altitud de crucero, la temperatura del aire ambiente puede provocar que el combustible baje a -35ºC debido a que se enfríe durante un crucero de largo alcance. Ese enfriamiento requiere considera- ciones especiales durante la fase de diseño del sistema de combustible. El calentamiento de la estructura del ala debido a efectos aerodinámicos hace que tal límite inferior no se suela violar. Por otra parte, en días calurosos, la temperatura máxima que puede alcanzar el combustible es 55ºC. Después de la fase de crucero, la posición de palanca del motor se reduce para permitir el descenso y aterrizaje del avión. 34 Debido a la interconexión que impone el FOHE y el rango tan amplio de gastos de combustible que se experimentan durante el vuelo completo, las temperaturas del combustible pueden variar significativamente en las diferentes fases del vuelo. Las temperaturas resultantes de aceite y combustible son claves en el diseño del sistema de combustible y en la gestión del calor. Sistema de combustible del avión e interacción motor-avión El sistema de combustible del avión consta de tres conjuntos de subsistemas asociados al cumplimiento de las funciones de almacenaje, distribución e indicación del combustible. Por un lado, el almacenaje del combustible tiene lugar en los tanques, situados en las alas. El tanque de cada ala alimenta a los motores que tiene asociados. Si se emplea un tanque central, éste alimenta todos los motores y es el primero en vaciarse (por motivos aerodinámicos y de seguridad). A la salida de cada tanque se sitúan válvulas de corte (shut-off ) asociadas las líneas de alimentación de cada motor para aislar el suministro de combustible a los motores. Los tanques también disponen de válvulas de venteo que permiten igualar su presión a la atmosférica y así ajustarse a los cambios de presión que aparecen al cambiar de altitud y al llenarse o vaciarse. Por otro lado, la distribución del combustible tiene lugar mediante conductos y bombas. Cada tanque sue- le contener un par de bombas de combustibles situadas o bien en un extremo del tanque, o bien dentro de un compartimento que siempre se encuentra lleno de combustible (y que asegura que la bomba se encuentra siempre sumergida). Además, se incorpora un sistema de transferencia de combustible que permite trasvasar combustible de un tanque a cualquier otro para corregir casos de asimetría en el vaciado o para hacer posible lo que se conoce como alimentación cruzada (que un tanque alimente a otro motor no asociado). Las bombas son controladas desde cabina. La red de alimentación del avión al motor merece especial consideración debido a las pérdidas de presión debidas a fricción en los conductos y cambios de altura en los mismos. Con las bombas de combustible eléctricas se asegura que el combustible se encuentra a una presión considerablemente por enci- ma de la presión mínima requerida para garantizar que el combustible no está aireado ni contiene vapores libres. Por último, el contenido de combustible está monitorizado de cara a su indicación en cabina, para lo que se emplean distintos tipos de dispositivos de medida de dicho nivel. También se monitoriza la temperatura del tanque de modo que salta un mensaje de aviso si la temperatura desciende por debajo de un umbral (lo que puede suceder en cruceros largos a elevadas altitudes) o si asciende por encima de otro umbral, lo que podría indicar que cierta cantidad de combustible calentado está volviendo a los tanques. También se monitoriza la presión de las bombas de combustible sumergidas en los tanques. Cuando se instalan los motores en un avión los dos sistemas de combustible deben funcionar como un todo, de tal manera que sus interacciones deben estudiarse en el diseño de ambos sistemas de combustible. Entre las interacciones que existen podemos citar las siguientes: 1) Operación de succión: La bomba de baja presión proporciona el combustible a una presión suficien- temente elevada como para garantizar que la bomba de alta presión suministra una cantidad suficiente de combustible a los inyectores. Sin embargo, en caso de fallo de las bombas de los tanques puede que esto no se garantice si el combustible está bastante aireado o con vapores libres. La bomba de baja debe garantizar que suministra el combustible a suficiente presión en toda su envolvente de operación; ésta se determina en los ensayos en vuelo del avión. 2) Factores de carga negativos: Ciertas maniobras extremas del avión pueden provocar una interrupción 35 en el suministro de combustible al sistema de combustible del motor, lo que puede implicar el consiguiente apagado de la llama y pérdida de empuje. 3) Reencendido: Como se ha indicado, ciertos factores pueden desencadenar una interrupción en el sumi- nistro de combustible, como por ejemplo el cierre accidental de la válvula de alimentación del avión al motor o ingestión de aire cuando se activa la válvula de alimentación cruzada. A continuación de un apagado, el sistema de combustible tiene que ser capaz de suministrar al motor el gasto de combustible necesario para permitir el reencendido del motor y su posterior operación normal. 4) Picos de presión: Los picos de presión (asociados al efecto de golpe de ariete) se crean siempre que se altera el flujo. Cuando se produce un cambio drástico de caudal el pico de presión en el combustible puede ser muy grande en valor absoluto. Pueden experimentarse picos de presión en los sistemas de combustible del avión y del motor debido a las interconexiones de los sistemas de combustible. 5) Contaminación: Como el combustible se proporciona al motor desde los tanques, el motor se puede encontrar con contaminantes provenientes del mismo, tanto sólidos (polvo, suciedad, desperdicios) como agua o hielo. Descripción del sistema de combustible en motores con FADEC Los sistemas de combustible de motores actuales presentan los siguientes componentes: Bomba de baja presión El