Technologie - PDF
Document Details
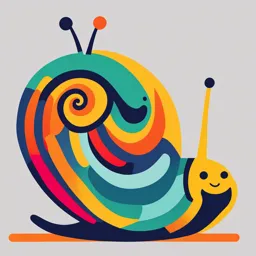
Uploaded by ImpressedAntigorite7047
Tags
Summary
This document presents a selection of materials from a course on modern technologies. It covers diverse topics such as metallurgy, material science, and additive manufacturing. Key processes, properties of materials, and applications are discussed to provide a general overview of the field.
Full Transcript
NOWOCZESNE TECHNOLOGIE – EGZAMIN Arkadiusz Klimczyk 1. Klasyfikacja procesów metalurgicznych. 2. Materiały wsadowe i paliwa w procesach metalurgicznych (rudy, odpady, paliwa, złom, etc…). 3. Technologie przygotowania materiałów wsadowych do procesów metalurgicznych....
NOWOCZESNE TECHNOLOGIE – EGZAMIN Arkadiusz Klimczyk 1. Klasyfikacja procesów metalurgicznych. 2. Materiały wsadowe i paliwa w procesach metalurgicznych (rudy, odpady, paliwa, złom, etc…). 3. Technologie przygotowania materiałów wsadowych do procesów metalurgicznych. 4. Ciągi technologiczne produkcji wyrobów końcowych. 5. Technologie produkcji metali i stopów na poszczególnych etapach procesów. 6. Kierunki rozwoju procesów metalurgicznych a ekologia i ochrona środowiska. Piotr Migas 1. Technologie alternatywne oraz wodorowe produkcji surowego żelaza. Rodzaje nowych technologii alternatywnych, wady, zalety Charakterystyki wybranych technologii np.: Corex, Hyl III, HIsmelt, Hybrit 2. Wytwarzanie proszków metali, materiały wsadowe, typy technologii atomizacyjnych (m.in. z ciekłych stopów metali, inne) Rodzaje technologii oraz metody atomizacji stopów metali Cechy jakościowe, behawioralne proszków metali 3. Odpady w procesach metalurgicznych, recycling odpadów oraz możliwości ich utylizacji. Rozdaje powstających odpadów, charakterystyki Miejsca ich powstawania w ciągach technologicznych produkcji żelaza, stali, miedzi Możliwości recyclingu oraz utylizacji Beata Dubiel 1. Prasowanie, spiekanie i formowanie wtryskowe proszków metali 2. Mechaniczna synteza 3. Podstawowe procesy wytwarzania przyrostowego wyrobów metalowych 4. Metody bezwiązkowe wytwarzania przyrostowego wyrobów metalowych 5. Spiekanie, stapianie i osadzanie laserowe 6. Technologie wytwarzania przyrostowego wykorzystujące wiązkę elektronów 7. Wytwarzanie przyrostowe z wykorzystaniem łuku elektrycznego i plazmy 8. Procesy drukowania 3D z ciekłego metalu, technologie Binder jet i FDM 9. Metody wytwarzania nanomateriałów top-down i bottom-up 10. Formowanie polimerów termoplastycznych i termoutwardzalnych 11. Formowanie elastomerów 12. Kompozyty umocnione dużymi cząstkami i cząstkami dyspersyjnymi 13. Wytwarzanie i właściwości kompozytów wzmacnianych włóknami 14. Wytwarzanie wyrobów ceramicznych 15. Właściwości układów o wielkościach nanometrycznych 1. Podział procesów metalurgicznych: A. Procesy cieplne, procesy fizyczne, procesy mechaniczne B. Procesy piroetalurgiczne, elektrometalurgiczne, hydrometalurgiczne oraz metalurgia proszków C. Przeróbka plastyczna, spiekanie, spalanie, ługowanie 2. Rodzaje surowców metalurgicznych: A. Surowce metalodajne (np. rudy, namiastki rud, atom metaliczny), topniki, paliwo B. Rudy metaliczne, rudy niemetaliczne C. Rudy wielometaliczne, paliwo 3. Składniki paliw stałych: A. Składniki węglowe, domieszki substancji mineralnych B. Domieszki obniżające zawartość składników palnych, siarka w postaci soli C. Składniki palne, domieszki obojętne, domieszki szkodliwe 4. Własności fizyko-chemiczne węgli: A. Twardość węgla, spiekalność węgla, odgazowanie węgla B. Plastyczność węgla, wydymanie się węgla, spiekalność węgla, odgazowanie węgla C. Jakość węgla, twardość węgla, spiekalność węgla, odgazowanie węgla 5. Metody otrzymywania stali dzielimy na: A. Procesy konwertorowe, proces martenowski (historyczny), procesy elektrotermiczne B. Proces wielkopiecowy, proces konwertorowy z dolnym dmuchem, procesy elektrotermiczne C. proces martenowski (historyczny), proces konwertorowy z górnym dmuchem, procesy w piecach indukcyjnych 6. Ostatnim etapem technologicznym produkcji stali jest jej odlewanie: A. na maszynie do ciągłego odlewania stali (COS) B. do form końcowych C. klasyczne do wlewnic bądź na maszynie do ciągłego odlewania (COS) 7. Wskaż poprawne sformułowania: A. Żadne sformułowanie nie jest poprawne B. Stal uspokojona - odtleniona dostateczną ilością Si, Mn, Al. Stal półuspokojona - częściowo w ogóle nie odtleniona, Stal nieuspokojona - odtleniona w niewielkim stopniu Mn C. Stal uspokojona - odtleniona dostateczna ilością Si, Al. Stal nieuspokojona – w ogóle nieodtleniona 8. Stopy żelaza to: A. Surówki, Stale, Żeliwa, Staliwa, Żelazostopy B. Stal stopowa i niestopowa C. Stale konstrukcyjne, narzędziowe, przemysłowe oraz o szczególnych właściwościach 9. Czynnikiem decydującym o rodzaju przeróbki plastycznej jest tak zwana: A. temperatura topnienia B. temperatura Curie C. temperatura rekrystalizacji 10. Jedna z klasyfikacji procesów przeróbki plastycznej dotyczy rodzaju ruchu względnego. Należy do niej: A. Kształtowanie powierzchniowe, kształtowanie jako bryły, kształtowanie powłok B. walcowanie, ciągnienie, kucie, tłoczenie C. wgłębianie, przesuwanie, zakrzywianie 11. Rodzaje procesów kucia: A. Kucie swobodne, kucie półswobodne, kucie matrycowe, kucie złożone B. Spęczanie, wydłużanie, wyciskanie, odlewanie C. Proces cięcia, proces kształtowania 12. Odgazowanie ciekłej stali. Do procesów próżniowych należą: A. Proces wielkopiecowy i proces stalowniczy B. Proces konwertorowy i ciągłe odlewanie (COS) C. Proces odgazowania strumieniowego, proces odgazowania komorowego, proces odgazowania obiegowego 13. Wielki piec jest agregatem A. do produkcji stali B. pracy ciągłej w przeciwprądzie C. do wytwarzania spieku 14. Do paliw zastępczych stosowanych na skale przemysłową w procesie wielkopiecowym należą: A. Gaz ziemny, olej, pył węglowy, mieszanka oleju z węglem B. Drewno, papier, odpady palne, odpady komunalne, węgiel drzewny C. Żadne z powyższych 15. BAT (Najlepsze Dostępne Techniki - Best Available Technology) to: A. Najbardziej efektywny oraz zaawansowany poziom technologii czysto teoretyczny, wykorzystywany jako podstawa granicznych wielkości emisyjnych mających na celu zapobieganie emisjom i wpływu na środowisko. B. Instrument formalno-prawny wprowadzony do prawa unijnego Dyrektywą Unii Europeiskiej nr 96/61/WE zwana Dyrektywa IPPC wydaną w 1996 roku, natomiast do prawa polskiego zostały, transponowane (dostosowane) ustawa z dnia 27 kwietnia 2001 r. - Prawa ochrony środowiska. Techniki te wymagane są przy prowadzeniu instalacji, której funkcjonowanie może powodować znaczne zanieczyszczenie poszczególnych elementów przyrodniczych lub środowiska jako całości. C. Najbardziej efektywny oraz zaawansowany poziom technologii i metod prowadzenia danej działalności wykorzystywany jako podstawa granicznych wielkości emisyjnych mających na celu zapobieganie emisjom lub, jeżeli jest to praktycznie niemożliwe, ograniczenie emisji i wpływu na środowisko jako całość. Piotr Migas 1. Technologie alternatywne oraz wodorowe produkcji surowego żelaza. a. Rodzaje nowych technologii alternatywnych, wady, zalety, b. Charakterystyki wybranych technologii np.: Corex, Hyl III, HIsmelt, Hybrit, 2. Wytwarzanie proszków metali, materiały wsadowe, typy technologii atomizacyjnych (m.in. z ciekłych stopów metali, inne). a. Rodzaje technologii oraz metody atomizacji stopów metali, b. Cechy jakościowe, behawioralne proszków metali 3. Odpady w procesach metalurgicznych, recycling odpadów oraz możliwości ich utylizacji. a. Rozdaje powstających odpadów, charakterystyki, b. Miejsca ich powstawania w ciągach technologicznych produkcji żelaza, stali, miedzi, c. Możliwości recyclingu oraz utylizacji Beata Dubiel 1. Prasowanie, spiekanie i formowanie wtryskowe proszków metali Etapu procesu wytwarzania wyrobów z proszków metali: 1) Wytwarzanie i rozdrabnianie proszku Do rozdrabniania proszku najczęściej stosuje się młyny kulowe, wypełnione kulami stalowymi i proszkiem. W wyniku oddziaływania kul na materiał następuje rozdrobnienie proszku. Właściwości proszku: Skład chemiczny – zdolność do zagęszczania i spiekania Kształt cząstek proszku - sypkość proszku oraz jego podatność do formowania Sferoidalny - rozpylanie gazem obojętnym, wodą, ultradźwiękami, rozkład karbonylków metali 𝑀𝑒𝑛 (𝐶𝑂)𝑚 Gąbczasty, strzępiasty – redukcja Dendrytyczny – elektroliza Talerzykowaty, wielościenny - Rozdrabnianie mechaniczne w młynach wirowo-udarowych, wibracyjnych lub kulowych Płatkowy - Rozdrabnianie mechaniczne w moździerzach Gęstość nasypowa - stosunek masy proszku zasypanego przez znormalizowany przyrząd do objętości zajmowanej przez ten proszek ( luźny układ cząstek ) Sypkość proszku – decyduje o szybkości i jednorodności wypełnienia matrycy Zagęszczalność proszku - podatność do zmniejszenia objętości w wyniku prasowania w matrycy 2) Prasowanie proszków za pomocą sztywnych narzędzi (stempli) izostatyczne, które polega na zagęszczaniu proszku umieszczonego w formie odkształcalnej na zimno a) w matrycy mokrej b) w matrycy suchej na gorąco a) napełnianie pojemnika b) odpowietrzenie próżniowe c) prasowanie izostatyczne na gorąco d) usunięcie pojemnika Podczas prasowania izostatycznego proszek umieszcza się w pojemniku, który po odpompowaniu powietrza szczelnie się zamyka. Pojemnik umieszcza się w komorze wysokociśnieniowej, w której w temperaturze spiekania proszku pojemnik jest ściskany przez gaz lub ciecz pod wysokim ciśnieniem. 3) Spiekanie proszków Polega na wygrzewaniu proszku lub uformowanej wypraski przez określony czas w odpowiedniej temperaturze i atmosferze. W wyniku procesów fizykochemicznych zachodzących podczas spiekania otrzymuje się materiał spiekany, odznaczający się pewną spoistością (w przypadku proszku) lub zwiększoną wytrzymałością wypraski. Wypraski (kształtki) są spiekane w celu uzyskania żądanej mikrostruktury i właściwości. Dyfuzja atomów po powierzchni cząstek proszków do punktów, w których cząstki się stykają prowadzi w początkowym okresie spiekania do tworzenia mostków między cząstkami. Dzięki niej po powierzchniach cząstek i utworzonych granicach miedzy cząstkami zachodzi kurczenie się porów, ich zaokrąglanie i wzrost gęstości wyrobu. Podczas spiekania wymiary wypraski znacznie się zmniejszają. W celu ograniczenia do minimum obróbki wykańczającej należy przy opracowaniu technologii dokładnie określić zmiany wymiarów spowodowane skurczem. Określone są przez: temperaturę, czas spiekania i skład chemiczny atmosfery pieca Rodzaje spiekania: w fazie stałej - prowadzone w zakresie 0,4−0,8 temperatury topnienia metalu spiekanego z udziałem fazy ciekłej - w temperaturze, w której część składników mieszanki proszkowej przechodzi w stan ciekły z udziałem zanikającej fazy ciekłej - gdy składniki mieszanki proszkowej tworzą roztwory w stanie stałym (np. Fe-Cu, Fe-P, Cu-Sn) i zachodzi dyfuzja składnika ciekłego w głąb fazy stałej Wyroby otrzymywane przez prasowanie i następnie spiekanie zawierają pory powodujące, że ich wytrzymałość na rozciąganie jest mała. Ilość i wielkość porów w wyrobach można znacznie zmniejszyć poprzez jednoczesne prasowanie i spiekanie (prasowanie na gorąco). Ostatnim etapem jest OBRÓBKA WYKAŃCZAJĄCA Formowanie wtryskowe Ang. Metal Injection Moulding (MIM) pozwala na seryjną produkcję elementów: o dowolnej geometrii (zróżnicowanych kształtach i wymiarach) o dużej odporności na obciążenia z wykorzystaniem dowolnych proszków metali Etapy wytwarzania w procesie MIM: 1. mieszanie proszku z lepiszczem termoplastycznym 2. formowanie poprzez wtryskiwanie mieszaniny do formy 3. usuwanie lepiszcza 4. spiekanie 2. Mechaniczna synteza MA to metoda otrzymywania stopów z proszków czystych metali i proszków przedstopowych w procesie mielenia w wysokoenergetycznych młynach kulowych w atmosferze gazu obojętnego, najczęściej argonu. Jest powtarzającym się procesem zgrzewania, kruszenia oraz ponownego zgrzewania cząstek proszków. Wytwarza się tą metodą : stopy na osnowie faz międzymetalicznych stopy pierwiastków wzajemnie nierozpuszczalnych w stanie ciekłym lub stałym, a także o różniącej się znacznie temperaturze topnienia stopy umocnione dyspersyjnie tlenkami (ODS) na osnowie niklu, żelaza i aluminium materiały amorficzne kompozyty na osnowie metalowej stopy nanokrystaliczne wysokotopliwe azotki, węgliki, borki i tlenki 3. Podstawowe procesy wytwarzania przyrostowego wyrobów metalowych ❖ WAM - Wire Arc Additive Manufacturing Drut metalowy jest stopiony za pomocą łuku elektrycznego i nanoszony na podłoże w celu tworzenia warstw. Jest to stosunkowo szybki i ekonomiczny proces, który umożliwia produkcję dużych, metalowych elementów. ❖ EBFFF - Electron Beam Freeform Fabrication Proces, w którym wiązka elektronowa jest używana do stopienia i nanoszenia metalu w postaci drutu lub proszku. Wiązka elektronowa jest skierowana na powierzchnię podłoża, powodując topnienie metalu i tworzenie warstw. EBFFF umożliwia produkcję trójwymiarowych, metalowych struktur o skomplikowanych kształtach. ❖ DMD - Direct Metal Deposition Metalowy proszek jest nanoszony za pomocą strumienia nośnika (np. gaz lub proszek) i stopiony za pomocą wiązki laserowej lub łuku plazmowego. Metoda ta pozwala na naprawę, naprawę awaryjną lub tworzenie struktur metalowych z użyciem różnych materiałów i wielu osi. ❖ LENS - Laser Engineered Net Shaping Wykorzystuje skierowany laser do stopienia i nanoszenia metalowego proszku na podłoże. Laser jest skanowany po powierzchni, a stopiony metal tworzy warstwy, tworząc pożądane geometryczne struktury. LENS jest stosowany do naprawy uszkodzonych elementów, napraw awaryjnych oraz tworzenia kompleksowych części metalowych. ❖ LC - Laminated Composite Manufacturing Polega na warstwowym składaniu i łączeniu cienkich folii metalowych. Każda warstwa jest wycięta lub sfałdowana w odpowiedni kształt, a następnie łączona z poprzednimi warstwami, tworząc trójwymiarowy model. LC może być stosowane do produkcji metalowych kompozytów, struktur złożonych i mikrosystemów. ❖ SLM - Selektywne spiekanie laserowe Polega na stopniowym topieniu i spajaniu metalowego proszku za pomocą skierowanego lasera. Laser jest skanowany po warstwie proszku, tworząc kolejne warstwy, aż do uzyskania pożądanego kształtu wyrobu. Jest to jedna z najbardziej popularnych technologii wytwarzania przyrostowego dla metali ❖ EBM - Electron Beam Melting Wykorzystuje wiązkę elektronową do stopienia i splotu metalowego proszku. Wiązka elektronowa jest skierowana na warstwę proszku, powodując stopienie i spajanie metalu. EBM jest wykorzystywane do produkcji metalowych części o złożonych kształtach, a także do tworzenia biokompatybilnych implantów medycznych. ❖ DMLS - Direct Metal Laser Sintering Wykorzystuje laser do stopienia i splotu metalowego proszku. Laser jest skierowany na warstwę proszku, który jest lokalnie stopiony i utwardzany, tworząc kolejne warstwy materiału. DMLS jest powszechnie stosowany w przemyśle do produkcji metalowych prototypów, narzędzi, a nawet końcowych produktów 4. Metody bezzwiązkowe wytwarzania przyrostowego wyrobów metalowych ❖ SIS - Selective Inhibition Sintering Polega na bezpośrednim stopieniu metalowych cząstek proszku w odpowiednich miejscach za pomocą lasera lub wiązki elektronowej. Proces ten wykorzystuje dodatkowe inhibitory, które utrzymują określone obszary w stanie sypkim podczas spiekania. Pozostałe obszary są stopione, co pozwala na tworzenie warstw i budowanie wyrobu metalowego. ❖ SDM - Sheet Lamination Składanie cienkich arkuszy metalu lub folii w warstwy i łączeniu ich za pomocą technik spajania lub zastosowania energii termicznej. Warstwy są stopniowo nakładane na siebie, a następnie spajane lub utrwalane, tworząc trójwymiarowy wyrob metalowy. Metoda ta jest często stosowana do wytwarzania prototypów i modeli metalowych ❖ EFAB - Electrochemical Fabrication Wykorzystuje procesy elektrochemiczne do stopienia i nanoszenia metalu na podłoże. Metoda ta wykorzystuje kontrolowany przepływ prądu elektrycznego, aby wydzielanie metalu w postaci jonów i ich osadzanie na podłożu. Poprzez kontrolę procesu elektrochemicznego, możliwe jest tworzenie warstw i budowanie trójwymiarowych wyrobów metalowych. ❖ 3DP - 3D Printing Ogólna nazwa dla technologii druku 3D, która obejmuje różne metody wytwarzania przyrostowego, w tym także dla metalu. W przypadku wytwarzania przyrostowego wyrobów metalowych, proces 3DP wykorzystuje metalowy proszek lub drut, który jest stopiony lub skonsolidowany za pomocą lasera lub wiązki elektronowej, aby tworzyć warstwowe struktury metalowe. ❖ S3DP - Selective 3D Printing Pozwala na selektywne nanoszenie materiałów na podłoże. Może obejmować nanoszenie proszku metalowego lub innych materiałów, takich jak ceramika czy polimer, w wybranych miejscach za pomocą drukarki 3D. Następnie materiał jest utrwalany, tworząc warstwowe struktury. ❖ CSAM - Cold Spray Additive Manufacturing Natrysk cząstek metalowych w stanie sypkim na podłoże przy użyciu sprężonego gazu. W procesie CSAM cząstki metalu są przyspieszane do dużych prędkości, a następnie nanoszone na podłoże. Energia kinetyczna cząstek powoduje ich adhezję i utwardzenie, tworząc warstwowe struktury metalowe. ❖ AFSD - Adaptive Freeform Solidification Wykorzystuje energetyczną wiązkę elektronów do stopienia i spajania metalowego drutu lub proszku. W procesie AFSD, wiązka elektronów jest skanowana po powierzchni, stopiąc metal i tworząc warstwy. Metoda ta umożliwia tworzenie trójwymiarowych, metalowych struktur o złożonych kształtach. ❖ UAM - Ultrasonic Additive Manufacturing Wykorzystuje ultradźwięki do stopienia i spajania metalowych folii. Proces UAM polega na nakładaniu cienkich warstw metalowych folii na podłoże, a następnie ich spajaniu za pomocą ultradźwięków. Powtarzając ten proces warstwowo, można tworzyć trójwymiarowe wyroby metalowe o złożonej geometrii. ❖ FSAM – Freeform Selective Area Metallurgy Selektywne nanoszenie metalu w określonych obszarach. Proces FSAM polega na wykorzystaniu wiązki laserowej lub wiązki elektronowej, aby stopić metalowy drut lub proszek w celu naniesienia go na podłoże w wybranych miejscach. ❖ Liquid metal jetting ❖ Nanoparticle injet printing ❖ Aoerosol jest process 5. Spiekanie, stapianie i osadzanie laserowe Procesy przyrostowe z wykorzystaniem lasera dzielimy na: Spiekanie laserowe (laser sintering) - łączy proszkowe cząstki Stapianie laserowe (laser melting) - topi metal w celu tworzenia pożądanych kształtów Osadzanie laserowe (laser deposition) - nanosi warstwami materiał na podłoże w celu budowy trójwymiarowych przedmiotów LPBF Cząstki proszku materiału metalicznego w zależności od mocy lasera są topione tylko w strefie przypowierzchniowej lub ulegają w całości topieniu. Poprzez topienie w strefie przypowierzchniowej cząstki proszku ulegają połączeniu poprzez spiekanie (ang. Selective Laser Sintering, SLS). Gdy cząstki proszku są w całości topione, ich połączenie następuje wskutek ich przetapiania (ang. Selective Laser Melting, SLM) Oddziaływanie skupionego źródła energii z powierzchnią warstwy proszku: Skupiona wiązka energii oddziałuje z warstwą proszku i tworzy się jeziorko ciekłego metalu Efektami towarzyszącymi topieniu proszku i przemieszczaniu się wiązki, a z nią jeziorka, są: parowanie ciekłego metalu odrywanie się od jeziorka kropel ciekłego metalu odrywanie się od powierzchni krystalizującej warstwy odprysków metalu w stanie stałym 6. Technologie wytwarzania przyrostowego wykorzystujące wiązkę elektronów Wiązka elektronów jest używana w selektywnym spajaniu warstw proszku (PBF - EB), a także osadzenie z topnieniem skupioną wiązką energii (EBDED). PBF Proces wytwarzania przyrostowego PBF (selektywne spajanie warstw proszku) stosuje się dla większości wyrobów o małych rozmiarach i małej chropowatości ich powierzchni. Materiał podawany jest w postaci proszku warstwa po warstwie i następnie w kolejnych warstwach jest selektywnie spajany skupioną wiązką energii. Źródłem energii do spajania proszku jest wiązka lasera lub elektronów. Proces EBPBF ▪ Źródłem energii jest wiązka elektronów emitowana z działa elektronowego i przyspieszana napięciem o wartości 30 – 60 kV o ostatecznej mocy między 50 – 1000 W ▪ W kolumnie elektronowej występuje obniżone ciśnienie − próżnia ma wartość co najmniej 10−4 Pa i zapobiega rozpraszaniu się elektronów na cząstkach gazów zawartych w powietrzu ▪ W komorze wytwarzania wyrobów jest obniżone ciśnienie o wartości około 0,2 Pa ▪ Następnie wprowadza się do komory niewielką objętość helu dla ograniczenia parowania niektórych składników ciekłego metalu ▪ Tolerancja wymiarowa 0,06 – 0,2 mm ▪ Prędkość skanowania 10 – 1000 mm/s ▪ Materiał wsadowy to proszek DED Większe elementy o mniejszej dokładności ich wymiarów zazwyczaj wytwarza się w procesie DED (ukierunkowanego osadzania z topieniem skupioną wiązką energii) – szybszym i tańszym, zwłaszcza przy użyciu materiału wsadowego w postaci drutu. Proces DED z zastosowaniem proszku ma mniejszą wydajność w porównaniu do procesu z użyciem drutu. Zaletą procesu DED jest możliwość stosowania do osadzania warstw zarówno na powierzchni płaskiej, jak również na powierzchni o różnej krzywiźnie. Stąd proces ten jest stosowany zarówno do wytwarzani nowych wyrobów, jak również do regeneracji uszkodzonych elementów maszyn. Proces EBDED ▪ Materiał wsadowy to proszek lub drut ▪ Moc między 1000 – 20 000 W ▪ Prędkość skanowania 1 – 10 mm/s ▪ Tolerancja wymiarowa 1,0 – 1,5 mm 7. Wytwarzanie przyrostowe z wykorzystaniem łuku elektrycznego i plazmy Oba są wykorzystywane w celu ukierunkowania osadzenia z topnieniem skupioną wiązką energii (DED). Łuk elektryczny to GMA DED. Metalowy drut jest stopniowo podgrzewany za pomocą łuku elektrycznego, który topi i osadza materiał, tworząc trójwymiarowe obiekty. Proces ten jest wykorzystywany do wytwarzania dużych i wytrzymałych metalowych konstrukcji, takich jak części samolotów, narzędzia przemysłowe i formy odlewnicze. Plazma to PA DED. Wykorzystuje plazmę do topienia i osadzania materiału. Plazma to jonizowany gaz, który jest podgrzewany za pomocą elektrycznego łuku, tworząc bardzo wysoką temperaturę. Dzięki temu procesowi można tworzyć trójwymiarowe obiekty z metalu, ceramiki lub innych materiałów, które są odporne na wysokie temperatury, takie jak elementy termiczne czy części silników Dla obu: ▪ Materiał wsadowy to drut ▪ Moc między 1000 – 3000 W ▪ Prędkość skanowania 5 – 15 mm/s ▪ Tolerancja wymiarowa 1,0 – 2,0 mm 8. Procesy drukowania 3D z ciekłego metalu, technologie Binder jet i FDM FDM Technologia FDM nazywana potocznie „drukiem 3D z filamentu”. W procesie FDM materiałem wsadowym są tworzywa sztuczne termoplastyczne, które przy określonej wartości temperatury i ciśnienia mają właściwości lepkiego płynu. wyroby powstają poprzez nakładanie kolejnych warstw półpłynnego materiału, który jest wytłaczany (“ekstrudowany“) z podgrzewanej dyszy. Materiał ma formę żyłki o stałej średnicy (1,75 mm lub 2,85 mm) nawiniętej na szpulę – jego zwyczajowa nazwa to „filament”. Kroki składające się na FDM: Szpula z filamentem jest zawieszana na ramieniu drukarki 3D Prowadzony przez rurkę filament Ekstruder - mechanizm złożony z koła zębatego i łożyska, pomiędzy które wprowadzana jest żyłka filamentu Łożysko jest dociskane do koła zębatego za pomocą sprężyny. Koło zębate jest poruszane przez silnik krokowy, który wprowadza filament do głowicy drukującej drukarki 3D Głowica drukująca jest rozgrzewana do temperatury potrzebnej przetopić dany filament (w większości 190 - 260˚C), porusza się nad stołem roboczym w osiach XY filament jest przekształcany do stanu półpłynnego – wystarczającego by móc “rysować” kształt na stole roboczym drukarki 3D Filament który zostaje wyekstrudowany na stół roboczy – praktycznie od razu zastyga (na podgrzanym stole zostaje plastyczny) Gdy nałożona jest pierwsza warstwa, w zależności od konstrukcji drukarki 3D stół roboczy opuszcza się lub głowica podnosi się, w osi Z i nakładana jest kolejna warstwa modelu 3D FDMet Wykorzystany proces FDM w celu wydruku wyrobów metalowych. Dla zapewnienia odpowiedniej spójności i kształtu wyrobów wytwarzanych metodą FDM konieczne jest odpowiednie przygotowanie materiału wsadowego oraz dobranie parametrów drukowania. Pojęcie „extrudability” = wytłaczalność odnosi się do filamentów z proszkami metali. Obecnie dostępne są filamenty zawierające proszki różnych metali i stopów z lepiszczem PLA oraz ABS, które można stosować w każdej drukarce 3D FDM. Koszt wydruku FDMet jest mniejszy niż w przypadku PBF i DED, ale mają gorsze właściwości, zwłaszcza mechaniczne. Do procesu FDMet nie jest potrzebna forma, tylko filament będący mieszaniną proszku metalu z lepiszczem. Po wydrukowaniu wyrób poddaje się wygrzewaniu w celu usunięcia lepiszcza, a następnie spiekaniu. Lepiszcza używane w filamentach z metalem: PLA poliaktyd, kwas polimlekowy Jest w pełni biodegradowalnym termoplastycznym poliestrem. Otrzymywany z odnawialnych surowców naturalnych jak np.: mączka kukurydziana. Jako filament ma mniejszą temperaturę topnienia (150-180˚C) niż ABS i jest od niego bardziej kruchy, przy tym nie wymaga podgrzewanego stołu w procesie wydruku ABS akrylonitrylo-butadieno-styren Tworzywo amorficzne służące między innymi jako filament. Materiał posiada dużą twardość, jest odporny na zarysowania, bardzo dobre właściwości izolacyjne. Materiał jest mniej kruchy niż PLA, jednakże potrzebuje wyższej temperatury między 215-250 ˚C do roztopienia Kroki składające się na FDMet: Drukowanie z filamentu (stan „zielony”). Podczas drukowania lepiszcze jest w stanie ciekłym, a cząstki proszku metalowego pozostają w stanie stałym Usuwanie lepiszcza (stan „brązowy”). Podczas wygrzewania usuwana jest tylko część lepiszcza. Pozostałe lepiszcze jest niezbędne do utrzymania kształtu wyrobu i zespojenia cząstek proszku Spiekanie w wysokiej temperaturze prowadzi do koalescencji cząstek proszku i uzyskania wymaganej gęstości wyrobu Zalety procesu FDMet ✓ wyroby w stanie „zielonym” mogą być wytwarzane w temperaturze nieco wyższej od temperatury topnienia polimerowego lepiszcza (zazwyczaj poniżej 300˚C) ✓ Usuwanie lepiszcza i spiekanie w wysokiej temperaturze można przeprowadzać dla wielu wyrobów na raz, co umożliwia obniżenie kosztów zużycia energii MagnetoJet Pierwszym systemem druku 3D z ciekłego metalu oparty na magnetohydrodynamicznym (MHD) wyrzucaniu kropel na ruchome podłoże. Proces: Materiał wsadowy jest podawany w postaci drutu topiony indukcyjnie. Pulsujące pole magnetyczne generuje w ciekłym metalu zmienne pole elektryczne, które z kolei generuje magnetohydrodynamiczną siłę Lorentza. Składowa siły działająca wzdłuż promienia komory z cieczą wytwarza ciśnienie, które wyrzuca krople ciekłego metalu przez otwór Wyrzucane krople osadzają się na podłożu, gdzie łączą się i krzepną Przy użyciu ruchomego podłoża można tą metodą wytwarzać trójwymiarowe wyroby warstwa po warstwie Binder jet Połączenie technologii formowania w złożu proszkowym (PBF) i natryskiwania. Proces: Na platformę roboczą nakładana jest warstwa proszku, która jest wyrównywana za pomocą rolki. Głowica drukująca z jedną lub kilkoma dyszami, podobna do tej, jaka jest używana w drukarkach atramentowych, porusza się na określonej wysokości nad warstwą proszku wzdłuż ścieżki zadanej dla wykonywanego przekroju budowanego wyrobu w płaszczyźnie X-Y i dozuje krople materiału spoiwa, który wiąże cząstki proszku. Platforma robocza obniża się w płaszczyźnie Z, nakładana jest kolejna warstwa proszku, głowica nanosi kolejną ścieżkę spoiwa i proces powtarza się aż do wybudowania gotowego wyrobu. Po wydrukowaniu wyrób pozostaje w maszynie do czasu utwardzenia spoiwa. Następnie wydrukowany produkt jest wyjmowany i czyszczony z nadmiaru niezwiązanego proszku za pomocą sprężonego powietrza Po wydrukowaniu przeprowadza się obróbkę wykańczającą W przypadku wyrobów metalowych po wydrukowaniu przeprowadza się obróbkę wykańczającą obejmującą spiekanie lub infiltrację stopem niskiej temperaturze topnienia. Stosowane materiały: stal austenityczna odporna na korozję, nadstopy niklu Zalety o Jest około 10 razy tańszy niż L-DED i L-PBF o Rozmiary wyrobów mogą być większe niż w przypadku ww. technologii o Szybkość drukowania jest większa o Zazwyczaj nie są konieczne struktury podporowe o Naprężenia własne w wyrobach są dużo mniejsze niż przy użyciu innych technologii o Technologia jest odpowiednia do produkowania wyrobów metalowych o małej i średniej masie. Wady o Mała wytrzymałość wyrobów, porównywalna z wytrzymałością odlewów ciśnieniowych 9. Metody wytwarzania nanomateriałów top-down i bottom-up Top – down Z litego materiału do nanocząsteczek. Polega na zmniejszeniu wymiarów makroskopowych klasycznego materiału objętościowego w wyniku powszechnie stosowanych mechanicznych metod przetwarzania ciał stałych Metody: Mielenie Gruboziarnisty materiał w formie proszku jest rozdrabniany między dwoma obracającymi się żarnami ze stali lub węglika wolframu Odbywa się bez dostępu powietrza Duże odkształcenie plastyczne prowadzi do powstania nanostruktury Wykorzystywana na dużą skalę Cięcie Skrawanie Walcowanie na zimno Skręcanie pod wysokim ciśnieniem Cykliczne wyciskanie ściskujące Wyciskanie hydrostatyczne Bottom - up Z cząsteczek prekursora do nanocząsteczek (proces agregacji). Budowanie od podstaw (atom po atomie) - opiera się na budowaniu nanostruktur z atomów lub cząsteczek, wytwarzanie nanomateriałów metalicznych, ceramicznych i polimerowych. Metody: Osadzanie z fazy gazowej Fizyczne (PVD) Poprzez kondensację par związków na powierzchni substratu materiał stały przechodzi w gaz, następuje jego chłodzenie i osadzanie na podłożu Chemiczne (CVD) Otrzymywanie materiałów stałych o dużej czystości Wykorzystywany do wytwarzania cienkich filmów półprzewodników Substrat jest eksponowany na działanie jednego lub więcej lotnych prekursorów, które reagują i/lub ulegają dekompozycji na powierzchni substratu powodując powstawanie odpowiednich produktów Osadzanie na podłożu produktów reakcji w temperaturze od 500-1000˚C substancji będących w fazie gazowej Metoda zol-żel Osadzanie elektrochemiczne Strącanie z roztworów Proste i niedrogie Wykorzystywane do produkcji nanokryształów metali i półprzewodników Chemiczna redukcja Metoda mikroemulsyjna każda kropla stanowi nanoreaktor, w którym mogą zachodzić reakcje w fazie wodnej, w odpowiednim dla kontrolowanego procesu nukleacji i wzrostu cząstek środowisku Metoda hydrotermalna 10. Formowanie polimerów termoplastycznych i termoutwardzalnych Polimery termoplastyczne (termoplasty) O budowie liniowej miękną ze wzrostem temperatury, a po ostudzeniu powtórnie twardnieją. Jest to proces odwracalny i powtarzalny. Formowanie odbywa się zwykle w temperaturze nieco niższej lub wyższej od temperatury topnienia, dlatego ich zachowanie jest zbliżone do gumy lub cieczy Jeżeli formowanie odbywa się pod ciśnieniem, to podwyższone ciśnienie musi być utrzymywane do czasu obniżenia temperatury w celu usztywnienia polimeru, aby formowany element nie zmienił kształtu, gdy polimer jest miękki Odpady mogą być użyte ponownie do formowania wyrobów -straty surowca są niewielkie Techniki formowania: Przez wtrysk Proces: I. Odpowiednia ilość surowca jest dostarczana w postaci granulek z leja zasypowego do cylindra. Ładunek jest podgrzewany w komorze grzewczej, gdzie zmienia się w lepką ciecz II. Stopiony polimer zostaje wtłoczony przez dyszę do zimnej formy, w której w miarę stygnięcia staje się coraz bardziej sztywny. Po uzyskaniu odpowiedniej sztywności, wyrób jest wyjmowany z formy Bardzo powszechny proces wytwarzania termoplastów (analogiczny do odlewania metali pod ciśnieniem do form metalowych). Sieciowanie odbywa się pod ciśnieniem w podgrzewanej formie, co powoduje, że czas formowania jest dłuższy niż czas formowania polimerów termoplastycznych. Przez wytłaczanie (wyciskanie) Proces: I. Polega na wypychaniu przez dysze lepkiego polimeru termoplastycznego (podobny do formowania metali przez wyciskanie) II. Ślimak przepycha przez komorę grzewczą materiał w postaci granulek, gdzie zachodzi mieszanie, zagęszczanie i topienie, a w dyszy – formowanie lepkiej cieczy III. Twardnienie wyciskanego materiału zachodzi pod wpływem nadmuchu powietrza lub strumienia wody tuż za dyszą Nadaje się szczególnie do wytwarzania długich wyrobów o stałych przekrojach poprzecznych, np. prętów, rur, taśm, arkuszy lub włókien. może być stosowane do wytwarzania powłok izolacyjnych na drutach i kablach. Cienkie włókna lub folie formuje się wytłaczając ciekły polimer przez dyszę z bardzo dużą ilością małych otworów lub przez wąskie szczeliny. Ze względu na kształt wyrobu jego chłodzenie i twardnienie po wytłoczeniu zachodzi bardzo szybko. Przez rozdmuchiwanie Proces: I. Materiał wyjściowy do produkcji pojemników (butelek) ma kształt rury, którą umieszcza się w dwuczęściowej formie, a następnie wdmuchuje się do niej gaz II. Wywierane ciśnienie wymusza odwzorowanie powierzchni formy przez ścianki rury Przez odkształcenie plastyczne (za pomocą próżni) Proces: I. Arkusz jest zamocowany nad formą, a po nagrzaniu arkusza włącza się układ próżniowy, który usuwając powietrze z wykroju powoduje formowanie wyrobu Mogą być również formowane podobnie jak metale. Do formowania wyrobów z arkuszy stosuje się zwykle proces próżniowy. Formowanie ze wzrostem wytrzymałości polimerów termoplastycznych Znaczny wzrost wytrzymałości wyrobów z polimerów termoplastycznych jest możliwy dzięki wyciągnięciu makrocząsteczek w kierunki działania sił rozciągających. Podczas eksploatacji włókna i pręty są obciążane siłami rozciągającymi równoległymi do osi włókien czy prętów, dlatego jest korzystnie, jeżeli makrocząsteczki są wyciągnięte równolegle do osi. Folie i arkusze są obciążane siłami rozciągającymi działającymi w ich płaszczyźnie, dlatego korzystnie jest, gdy makrocząsteczki są rozciągnięte równolegle do płaszczyzny folii. Podczas wytwarzania włókien, prętów, arkuszy i folii należy dążyć do takiego przebiegu procesu formowania, aby w ukształtowanych wyrobach makrocząsteczki miały korzystną orientację. Polimery termoutwardzalne (duroplasty) O usieciowanej strukturze cząstek są amorficzne i kruche. Dzielą się na polimery termoutwardzalne i chemoutwardzalne. Poddane odkształceniu zachowują nieodwracalnie swój kształt. Utwardzenie w procesie formowania zachodzi dzięki tworzeniu się wiązań poprzecznych (ogranicza możliwości formowania) Techniki formowania: Prasowanie Proces: I. Ściśle odmierzona ilość polimeru lub żywicy i utwardzacza, dokładnie wymieszanych z dodatkami, zostaje umieszczona w formie między jej górną a dolną częścią II. Obie części formy są podgrzewane III. Pod wpływem wywieranego ciśnienia podgrzany polimer płynie, wypełniając wykrój w matrycy Nie jest odpowiednie do formowania wyrobów o dużych przekrojach lub z dużymi zmianami tych przekrojów, ponieważ żywice charakteryzują się małą przewodnością cieplną (gruby przekrój – ciepło nie dociera, brak pełnego sieciowania). Problem nie występuje przy formowaniu przez wyciskanie do formy (proszek żywicy jest podgrzewany aż do uzyskania plastyczności, potem wyciskany do wykroju, w którym zachodzi sieciowanie). Techniki mogą być stosowane dla termoplastów, ale są bardziej kosztowne i czasochłonne. Wytłaczanie do formy (odlewanie) Mogą być formowane przez odlewanie do formy (termoplasty tez), ale nie jest to specjalnie stosowane. Odlewa się je, gdy istnieje potrzeba wytworzenia niewielkiej liczby części o takim samym kształcie, a nieopłacalne jest wykonanie drogiego oprzyrządowania koniecznego do użycia przy innych technikach formowania 11. Formowanie elastomerów Właściwości elastomerów po znacznych odkształceniach wracają do swej pierwotnej postaci lub bardzo do niej zbliżonej wysoko elastyczne, sprężyste, które dodatkowo charakteryzuje wysoka odporność termiczna (od -40°C do 100°C) i chemiczna temperatura mięknięcia elastomerów jest niższa od temperatury pokojowe termoplastyczne elastomery = termoplastycznymi kauczukami (skrót TPE) dzielą się na wulkanizujące i niewulkanizujące odpady nie mogą być użyte ponownie do wytwarzania wyrobów są formowane poprzez prasowanie z jednoczesnym ogrzewaniem mieszanki elastomeru ze środkiem wulkanizującym mieszanki kauczuku i twardych materiałów termoplastycznych, np. poliamidu, polipropylenu, z dodatkiem odpowiednich modyfikatorów i wypełniaczy Proces Wulkanizacji W podwyższonej temperaturze, polega na kowalencyjnym wiązaniu sąsiednich makrocząsteczek, w miejscach nienasyconych wiązań, za pomocą siarki, tlenu, selenu lub telluru Prawie każdy gatunek gumy otrzymuje się z kauczuku poprzez wulkanizację. Kauczuk składa się z ułożonych obok siebie bardzo długich łańcuchów - poliolefin powoduje tworzenie się stosunkowo niewielkiej liczby mostków chemicznych między tymi łańcuchami, na skutek czego powstaje przestrzenna sieć Zastosowanie: ▪ budownictwo – uszczelki do drzwi i okien, różnego rodzaju podkładki i membrany ▪ motoryzacja – uszczelki do szyb samochodowych, osłony i pokrywy, maty wewnątrz aut ▪ sport – akcesoria sportowe, elementy do sprzętu sportowego ▪ opakowania – trwałe i elastyczne pojemniki na różne produkty ▪ zabawki 12. Kompozyty umocnione dużymi cząstkami i cząstkami dyspersyjnymi Kompozyt Materiał utworzony z co najmniej dwóch komponentów (faz) o różnych właściwościach w taki sposób, że ma właściwości lepsze od możliwych do uzyskania w każdym z komponentów osobno i lepsze od wynikających z prostego sumowania tych właściwości. Właściwości kompozytów zależą od rodzaju faz składowych, ich udziału i rozmieszczenia oraz sił wiązań na granicy cząstka-osnowa Osnowa – faza ciągła. Odpowiedzialna za przenoszenie naprężeń do fazy wzmacniającej , ochrone przed szkodliwym działaniem otoczenia Podział od skrótów: MMC (metal), CMC (ceramika) PMC (polimer) Faza wzmacniająca - polepszenie właściwości osnowy W zależności od rodzaju osnowy powoduje wzrost: MMC – wytrzymałości CMC – odporności na pękanie PMC – modułu Younga i wytrzymałości Podział kompozytów: Ze względu na pochodzenie o Naturalne np. drewno, kość o Zaprojektowane wytwarzane przez człowieka Ze względu na osnowę o O osnowie metalowej Osnowę stanowią: żelazo i jego stopy, stopy niklu, metale nieżelazne i ich stopy, fazy międzymetaliczne. Powszechnie stosowane stopy, zapewniające odpowiednie właściwości wytrzymałościowe, technologiczne i eksploatacyjne. o O osnowie ceramicznej Do osnowy ceramicznej w materiałach kompozytowych możemy zaliczyć ceramikę techniczną – głównie 𝐴𝑙2 𝑂3 i azotek krzemu 𝑆𝑖3 𝑁4 , szkła i tworzywa szklano -ceramiczne oraz węgiel o O osnowie polimerowej żywice termoutwardzalne: fenoplasty i aminoplasty żywice chemoutwardzalne: poliestrowe, epoksydowe i silikonowe tworzywa termoplastyczne: poliamidy, polipropylen, poliestry termoplastyczne, poliwęglan oraz w mniejszych ilościach polimery styrenowe Podział ze względu na materiał wzmacniający: Cząsteczkami Dyspersyjnie Włóknami Wzmacniane konstrukcyjnie Umacnianie dużymi cząsteczkami Inaczej kompozyty agregatowe. Cząstki umacniające mają wielkość powyżej 1μm, a ich udział objętościowy może dochodzić do 90%. Różnicą w stosunku do kompozytów umacnianych dyspersyjnie jest fakt, że w tych kompozytach obciążenia przenoszone są przez osnowę i cząstki, w związku z tym ulega także zmianie mechanizm oddziaływania cząstek z osnową. Dodaje się duże cząstki o znacznym rozmiarze do macierzy. Te cząstki mogą być wykonane z różnych materiałów, takich jak metal, ceramika lub inne polimery. Duże cząstki są równomiernie rozłożone w macierzy, a ich obecność prowadzi do zwiększenia wytrzymałości i innych właściwości mechanicznych kompozytu. Przykłady to kompozyty metaliczne wzmocnione włóknami, w których włókna metalowe pełnią rolę agregatów. Umocnienie wynika z: A. Oddziaływania sprężystego cząstek z osnową B. Ograniczenia ruchu dyslokacji C. utworzenia ciągłego szkieletu cząstek fazy umacniającej W zależności od kompozytu mogą ograniczać odkształcenia. W przypadku kompozytów ceramicznych są one wprowadzane w celu zwiększenia odporności Umacnianie cząsteczkami dyspersyjnymi Stosuje się małe cząstki, nazywane również cząstkami dyspersyjnymi, które są równomiernie rozproszone w macierzy. Cząstki dyspersyjne mogą być nanocząstkami, mikrocząstkami lub cząstkami o innych rozmiarach i wykonane z różnych materiałów, takich jak nanorurki węglowe, włókna ceramiczne lub polimerowe. Obecność tych cząstek w kompozycie prowadzi do poprawy właściwości, takich jak twardość, wytrzymałość, odporność na korozję lub stabilność termiczna. 13. Wytwarzanie i właściwości kompozytów wzmacnianych włóknami Dominują obecnie na rynku materiałów kompozytowych. Włókna stosowane do ich produkcji mogą być ciągłe lub nieciągłe, czyli krótkie lub cięte. Ich udział objętościowy może dochodzić do 90%. Obciążenia przenoszone są przez włókna. Wytrzymałość kompozytu umacnianego włóknami rośnie w miarę wzrostu udziału objętościowego włókien. Aby osiągnąć efekt umocnienia, udział objętościowy włókien musi przekroczyć tzw. objętość krytyczną. Długość włókna, powyżej której następuje wzmocnienie kompozytu nazywana jest długością krytyczną. Określa się ją w zależności o rodzaju osnowy – plastycznej lub sprężystej. Proces: I. Wybór włókien wzmacniających np. węglowych, szklanych, aramidowych, czy ceramiki, ze względu na właściwości, które chcemy umocnić II. Włókna muszą zostać odpowiednio przygotowane przed połączeniem z matrycą. Etapy przygotowania mogą obejmować czyszczenie, pokrycie powłoką lub impregnację III. Włókna są następnie łączone z matrycą, tworząc kompozyt wzmacniany włóknami Formowanie na gorąco – układane w odpowiedniej konfiguracji, następnie matryca jest topiona i przelewana do formy, gdzie zostaje utwardzona Przepływ matrycy – włókna są przepływane przez matryce metalową lub polimerową tworząc kompozyt o pożądanym kształcie i strukturze Nakładanie warstw – włókna i matryca są układane na przemian, a następnie poddawane presji i utwardzane Właściwości: Wytrzymałość i sztywność Odporność na korozję Są znacznie lżejsze niż tradycyjne materiały konstrukcyjne Przewodnictwo cieplne i elektryczne Bardziej trwałe w przypadku cyklicznego obciążenia mechanicznego 14. Wytwarzanie wyrobów ceramicznych Etapy: 1. Wytwarzanie proszków i mas 2. Formowanie 3. Suszenie 4. Kształtowanie półfabrykatów w stanie niewypalonym 5. Wypalanie 6. Nanoszenie pokryć ceramicznych 7. Kształtująca obróbka końcowa ❖ Ceramiki i szkła to materiały inżynierskie najwcześniej stosowane przez człowieka, odporne na działanie środowiska ❖ Materiały ceramiczne stosowane są w przemyśle lotniczym, kosmicznym i elektronicznym ❖ Materiały ceramiczne i szkła posiadają wysoką odporność na korozję i na ścieranie, są twarde, kruche, o wysokiej temperaturze topnienia, małej przewodności cieplnej i elektrycznej ❖ Kompozyty o osnowie ceramicznej mogą być odporne na pękanie Rodzaje: Ceramiki krystaliczne – krzemiany, tlenki, związki nie zawierające tlenu Szkła – niekrystaliczne ciała stałe o składzie zbliżonym do ceramik krystalicznych Tworzywa szklano-ceramiczne – kształtowane w stanie szklistym, a następnie poddawane obróbce mającej na celu spowodowanie krystalizacji 15. Właściwości układów o wielkościach nanometrycznych Układy o skali nanometrycznej mają dużą powierzchnię w stosunku do objętości; umożliwia to interakcje z innymi cząstkami Mogą wykazywać efekty kwantowe, takie jak tunelowanie kwantowe, efekt plazmoniczny czy efekt kwantowego punktu zerowego – wpływające na ich zachowanie elektronowe i optyczne Wysoka reaktywność chemiczna - większa zdolność do adsorpcji cząsteczek, interakcji z innymi substancjami i zmiany swoich właściwości w obecności środowiska Właściwości mechaniczne mogą być kontrolowane przez manipulację ich strukturą i kompozycją Właściwości optyczne - efekt plazmoniczny, fluorescencję, absorpcję światła Mogą mieć lepszą przewodność cieplną lub elektryczną