SOP.PRD.018 HSD 3 & 4 PDF
Document Details
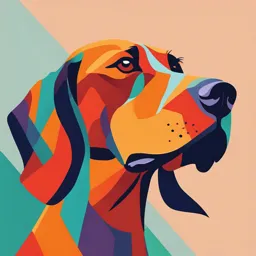
Uploaded by YoungLithium
Tags
Summary
This document provides standard operating procedures for high-speed dispersors (HSD 3 and 4). It includes safety precautions, definitions, responsibilities, and operational procedures.
Full Transcript
AkzoNobel India Limited Metal Coatings STANDARD OPERATING PROCEDURE MANUAL – OPERATIONS Section No.: SOP.PRD.018 Ref. ISO 9001 & AN HSES Manual Review...
AkzoNobel India Limited Metal Coatings STANDARD OPERATING PROCEDURE MANUAL – OPERATIONS Section No.: SOP.PRD.018 Ref. ISO 9001 & AN HSES Manual Review Date: 20/01/2022 Issue Date: 28/11/2019 Page No.: 1 of 8 Rev No.3 HIGH SPEED DISPERSOR (HSD 3 & 4) Sr. No Rev 1.0 PURPOSE To ensure safe handling and operation of HSD 3 and HSD 4 2.0 SCOPE This SOP is applicable for operation and cleaning of HSDs. 3.0 DEFINATIONS / ABBREVIATIONS *TA Trained & Authorized Person QO Quality Officer PO -Production Officer PM Production manager ETF Emergency Task Force *TA- Trained and authorized person is the person who has got proper training of doing the particular activity and is validated for the same. 4.0 RESPONSIBILITIES Responsibility Activity Primary Secondary Information Reference Safe handling and operation of HSD 3 Equipment and HSD 4 TA PO PM Manual 5.0 HAZARDS Static Fire– Failure of continuity of portable earthing & bonding clamp can cause a 5.1 fire. Limit Switch (injury to body part) - Malfunctioning of the Limit Switch can cause 5.2 damage equipment and body injury 5.3 Hydraulic - Malfunctioning of Hydraulic can cause a spill. 5.4 Switches – Malfunctioning of switches can cause a spill and loss. 5.5 LOPC – Follow SOP for spill management Injury to people. - Incorrect Isolation can lead to injury to people and damage 5.6 equipment Ergonomic Risk Hazard – Precautions should be taken to ensure that manual 5.7 handling is done inline with good manual handling practices. Reviewed by: Kiran Patil Approved by Danny D’Souza AkzoNobel India Limited Metal Coatings STANDARD OPERATING PROCEDURE MANUAL – OPERATIONS Section No.: SOP.PRD.018 Ref. ISO 9001 & AN HSES Manual Review Date: 20/01/2022 Issue Date: 28/11/2019 Page No.: 2 of 8 Rev No.3 HIGH SPEED DISPERSOR (HSD 3 & 4) PPEs: Safety shoes, high visibility jackets & safety goggle always in the plant, cut resistance gloves while handling wooden pallet, empty bucket, filled bucket, HOPT, Barrel tilter, Scrapper, pigments/powder bags, samplers and sample tins manual handlings, Vapor mask, vapor cartridge mask for chemical charging, Helmet, long sleeves. Nitrile gloves wherever contact with Chemical. Face shield while charging of solvent from tank farm 5.8 to tote and Vessel and Hose connection and removal during unloading Line of fire during HOPT Operation - HOPT operation should be in pallet movement 5.9 on floor. 5.10 Noise – Stirring operation of mixers, AODD pump all contribute to noise. Electrical Shock (injury to body part)– All machine panels should be locked, and 5.11 check earthing cable for any loose conation and broken wire Hygiene – Ensure all vessel are in close condition 5.12 Injury - Fall of materials from height – Use of Helmet when operating in plant is 5.13 mandatory. 5.14 VOC – Exposure to VOC can cause human health issue. 6.0 Method 6.1 INITIAL START UP Use safety shoes, Helmet, safety glasses, hand gloves and Mask as per PPEs 6.1.1 displayed board Reviewed by: Kiran Patil Approved by Danny D’Souza AkzoNobel India Limited Metal Coatings STANDARD OPERATING PROCEDURE MANUAL – OPERATIONS Section No.: SOP.PRD.018 Ref. ISO 9001 & AN HSES Manual Review Date: 20/01/2022 Issue Date: 28/11/2019 Page No.: 3 of 8 Rev No.3 HIGH SPEED DISPERSOR (HSD 3 & 4) Keep pinch point hazards in mind while working with drums or vessels. 6.1.2 Ensure the waste bins are available for effective segregation of waste. 6.1.3 6.1.4 Ensure fume/ dust extraction system is ON while machine is on 6.1.5 Food contact Product batch card printed in yellow color 6.2 OPERATIONS LIMITS: - Select appropriate vessel as per the batch size maximum up to 1000 Liters for HSD03 & 200 Liters for HSD04 with maximum machine rpm of 1200. 6.2.1 Ensure the vessel is empty and cleaned. Ensure the vessel bottom valve is closed Move the vessel on the weighing scale of 2000 kg capacity Check the charge prep as per mention in batch card and picking list 6.2.2 Record relevant information (quantity charged, lot no, RPM, Temperature) in the batch 6.2.3 card. Charge the Raw materials refer sequence provided in the batch card into the Vessel. Solvents are charged through mass flow meter (weights to be set in batch controllers) 6.2.4 Other materials are charged by placing the vessel on the weighing scale or pre weigh the quantity to be charged in a separate container and charge into the vessel. Reviewed by: Kiran Patil Approved by Danny D’Souza AkzoNobel India Limited Metal Coatings STANDARD OPERATING PROCEDURE MANUAL – OPERATIONS Section No.: SOP.PRD.018 Ref. ISO 9001 & AN HSES Manual Review Date: 20/01/2022 Issue Date: 28/11/2019 Page No.: 4 of 8 Rev No.3 HIGH SPEED DISPERSOR (HSD 3 & 4) Ensure earthing to be connected whenever material is transferred from one container to another To charge the liquids from the barrel (200 kgs drums) use drum lifter (refer procedure). While processing follows the manufacturing instruction as mentioned in the batch card. Move the vessel to the HSD. Ensure Local isolation in place before placing the portable under the HSD. 6.2.5 Lift the shaft by operating panel switch and ensure that it has reached the maximum allowed height. Place the vessel in the position, secure the vessel using vessel clamps and attach the earthing clamp. Lower the shaft by pressing DOWN button and ensure that shaft and lid has been completely lowered to fit exactly on top of the vessel 6.2.6 Ensure earthing and green light is in on condition. Secure pot with strapping belt Reviewed by: Kiran Patil Approved by Danny D’Souza AkzoNobel India Limited Metal Coatings STANDARD OPERATING PROCEDURE MANUAL – OPERATIONS Section No.: SOP.PRD.018 Ref. ISO 9001 & AN HSES Manual Review Date: 20/01/2022 Issue Date: 28/11/2019 Page No.: 5 of 8 Rev No.3 HIGH SPEED DISPERSOR (HSD 3 & 4) To start the impeller first remove Local isolation by issuing local isolation key by PO and handover return after work complete and release emergency and press the start push button and increase the RPM and set it at the level as mentioned in the batch card. Allow it to mix as per the time mentioned in the batch card. Add the required RM in the sequence as mentioned in the batch card To stop the impeller, press the Stop push button, the impeller RPM will gradually come down then it will stop For Sampling put local isolation first and open the hatch and ensure that the shaft has completely stopped use sampler to collect sample from sampling point which is provided on the HSD and clean the sampler after use with cleaning solvent. And collected sample to send QC Lab for Quality check. 6.2.7 Reviewed by: Kiran Patil Approved by Danny D’Souza AkzoNobel India Limited Metal Coatings STANDARD OPERATING PROCEDURE MANUAL – OPERATIONS Section No.: SOP.PRD.018 Ref. ISO 9001 & AN HSES Manual Review Date: 20/01/2022 Issue Date: 28/11/2019 Page No.: 6 of 8 Rev No.3 HIGH SPEED DISPERSOR (HSD 3 & 4) ABNORMAL CONDITIONS 1. While Stirring any breakdown or issue will be arise, turn off the switch of stirrer and inspect the issue and solve on the spot or inform to superior. 6.3 2. In case of Spillage, immediate inform to SO and start to clean and collect spilled material. 3. In case of breakdown happen in stirrer or any other component of operation, and then switch vessel to another stirrer. 4. In case of Lid stuck during lifting and lowering report to Engineering. 6.4 EMERGENCY SHUTDOWN – Fire Alarm or Spillage 1. In case any abnormal is noticed or in the event of any incident shut down the HSD by pushing emergency shut off switch. 2. Report the matter to the line manager and / or HSES staff and act as per the 6.4.1 instruction. 3. In case of an emergency shut down the operation safely and gather at assembly point for further instruction.9 Operator should evacuate along with secondary labours who are working on m/c to the 6.4.2 assembly point. CAUTION POINTS Wrong Equipment –The equipment to be selected after checking the batch. Wrong 6.4.3 HSD selection can lead to wrong batch processing. Cleaning of HSD – Before start cleaning activity put Local isolation. 6.4.4 Reviewed by: Kiran Patil Approved by Danny D’Souza AkzoNobel India Limited Metal Coatings STANDARD OPERATING PROCEDURE MANUAL – OPERATIONS Section No.: SOP.PRD.018 Ref. ISO 9001 & AN HSES Manual Review Date: 20/01/2022 Issue Date: 28/11/2019 Page No.: 7 of 8 Rev No.3 HIGH SPEED DISPERSOR (HSD 3 & 4) Ensure HSD shaft as it ground position and press Emergency Butten. that HSD’s blades are cleaned properly. Contaminated HSD can lead quality issue in product. Spill/leakages from Product Vessel – Ensure that vessel’s valves are closed 6.4.5 properly and valve cap close. Leakage valve can lead to spill of product from vessel. 6.4.6 Impact to Quality – wrong charging can lead to quality issue in product Machine guarding -- Ensure that all the machine guards are in place and properly 6.4.7 fixed before starting the machine. In case of any deviation do not start the machine and inform the SI Hygiene standard- Ensure that while using equipment and pot is properly clean and 6.4.8 there is not contamination in between. 6.5 EMERGENCY SHUT DOWN 6.5.1 In case of a fire: shut operation safely and follow emergency response plan In case of a loss of containment: raise alarm / Inform SO. Close valves. Attempt control 6.5.2 of leakage by closing appropriate valve. Collect spill as per spill control procedure. In case of any splash / exposure wash with enough water and inform SO. Consult 6.5.3 medical center if required. In case of external emergency, the process may be stopped at any point, to be 6.5.4 resumed later as per the original sequence. Follow emergency evacuation procedure. NORMAL SHUTDOWN Ensure all portables containing material are closed with a lid, 6.6 Outlet valves closed and cap fixed. Turn off HSD properly and confirm and put operation lock and handover key to issuer. Press emergency switch. STARTUP AFTER NORMAL SHUT DOWN 6.7 Released the emergency switch. Remove the covered lids from vessels/containers. And start work MEASURES IN CASE OF LOSS OF UTILITY 6.8 Electricity- In case of power failure when power resume release Emergency of m/c & to complete remaining work & follow normal operation. Reviewed by: Kiran Patil Approved by Danny D’Souza AkzoNobel India Limited Metal Coatings STANDARD OPERATING PROCEDURE MANUAL – OPERATIONS Section No.: SOP.PRD.018 Ref. ISO 9001 & AN HSES Manual Review Date: 20/01/2022 Issue Date: 28/11/2019 Page No.: 8 of 8 Rev No.3 HIGH SPEED DISPERSOR (HSD 3 & 4) 6.9 AUTHORIZATION FOR WORK 6.9.1 Under breakdown machine can be operate by Train and authorized person. Required LSR for this Process 6.9S.2 Reviewed by: Kiran Patil Approved by Danny D’Souza