Determination of Setting Time of Hydraulic Cement PDF
Document Details
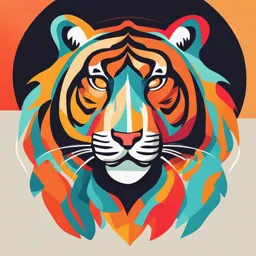
Uploaded by PicturesqueSugilite7005
Western Mindanao State University
TAIB, NUR- SALYN J.
Tags
Summary
This presentation details the determination of the setting time of hydraulic cement, a crucial aspect of concrete. It covers topics like the chemical composition of hydraulic cement (including various compounds like alites and belites), and its uses in different construction applications. The presentation also touches on important considerations for using hydraulic cement in different settings.
Full Transcript
Determination of Setting Time of Hydraulic Cement WMSU Presented by: TAIB, NUR- SALYN J. Cement vs. Concrete Cement is defined as a binding agent that is used to bind various construction materials. Given its adhesive and cohesive pr...
Determination of Setting Time of Hydraulic Cement WMSU Presented by: TAIB, NUR- SALYN J. Cement vs. Concrete Cement is defined as a binding agent that is used to bind various construction materials. Given its adhesive and cohesive properties, it is an essential ingredient of concrete and mortar. Concrete is created by mixing hydraulic cement, water and aggregate, such as sand or gravel. Difference Between Non-Hydraulic Cement & Hydraulic Cement Non-Hydraulic Cement does not require water to harden. Instead, all it needs are dry conditions and the presence of carbon dioxide (CO₂) to set and cure. Hydraulic cement is an inorganic mineral material that reacts with water under ambient conditions forming a hardened and water- resistant product. The cement hardens by hydration in the presence of water. WHAT IS HYDRAULIC CEMENT? Hydraulic cement is a type of cement that sets and hardens when mixed with water. It usually consists of a fine powder made from limestone, clay or gypsum. Composed of hydraulic calcium silicates (generally containing calcium sulfate), hydraulic cement is a non-corrosive, non-rusting and non-shrink substance widely used in construction. This type of cement is especially good for structures that are constantly in contact with water because it is impermeable to water. How Hydraulic Cement Works? Hydraulic cement’s working principle is based on the process of hydration, which means the product hardens when water is added. Certain substances present in hydraulic cement initiate reactions due to the application of water, causing the mixture to set and harden very quickly with reduced curing time. Chemical Composition of Hydraulic Cement The four main components of hydraulic cement are 1. Alite (3CaO·SiO2) - is an impure form of tricalcium silicate, Ca3SiO5 2. Belite (2CaO·SiO2) - its main constituent is dicalcium silicate, Ca 2SiO4 3. Tricalcium aluminate/ Celite (3CaO·Al2O3) 4. Tetra-calcium aluminoferrite/ Brownmillerite (4CaO·Al2O3·Fe2O3) ❖ In an abbreviated notation differing from the normal atomic symbols, these compounds are designated as C3S, C2S, C3A, and C4AF, where C stands for calcium oxide (lime), S for silica, A for alumina, and F for iron oxide. Chemical Composition of Hydraulic Cement C3S (Tricalcium Silicate). This compound is crucial for the early strength of cement. It hydrates quickly, contributing to the initial setting and strength development of concrete. C2S (Dicalcium Silicate). This compound hydrates more slowly than C3S and is primarily responsible for the long-term strength of cement. It generates less heat during hydration, making it more resistant to chemical attacks. C3A (Tricalcium Aluminate). This compound reacts quickly with water and contributes to the setting of cement. However, it can lead to rapid strength gain and high heat generation, which may not be desirable in all situations. C4AF (Tetra-calcium Aluminoferrite). This compound also hydrates quickly and contributes to the strength of cement. It has a moderate heat generation and provides some resistance to chemical attacks. When to Use Hydraulic Cement? The right type of cement is to be selected based on the nature of the construction work. Different blends of hydraulic cement contain varying ratios of chemical components to suit specific needs. Its ability to provide strength is immense, so hydraulic cement can be used for the construction of highly durable structures. The cement is not flexible, so it can only be used to provide mechanical support to structures. Being impermeable to water, it can be used in constructing structures that are in constant contact with water. This type of cement does not corrode or rust, hence it retains its strength even when submerged in water. It is also extremely useful for water-proofing. This type expanding hydraulic cement is very useful for sealing concrete leaks and repair work. The Uses and Types of Hydraulic Cement (Normal) Hydraulic Cement This is the common form of hydraulic cement that lacks any situation-specific tweaks to its formula. It is used on a smaller scale for home, building, and structural repairs. Ex. Ordinary Portland Cement (OPC) White Hydraulic Cement This type of hydraulic cement is identical to normal hydraulic cement utility-wise. However, it contains less magnesium and iron than regular hydraulic cement, which changes its color from gray to white. Ex. White Portland Cement and Lafarge White Cement High Early Strength Hydraulic Cement Although hydraulic cement becomes solid quickly, it can still take around a month for it to complete the curing process. High early strength hydraulic cement reduces the curing time to about a week. Ex. Rapid Set Cement and Type III Portland Cement Moderate Heat of Hydration Hydraulic Cement In some larger constructions, including sizeable foundations and high retaining walls, too much heat could end up leading to more cracks and weakening. This is of course counterproductive when you are trying to create a strong structure. Moderate heat of hydration hydraulic cement is thus used to make those large structures stable. Ex. Type II Portland Cement Low Heat of Hydration Hydraulic Cement This form of hydraulic cement takes the concept of minimizing water reaction heat even further. It is needed for building giant structures, such as gravity dams, which would not be able to remain secure if a lot of heat was generated as the cement solidified. Ex. Type IV Portland Cement Moderate Sulfate-Resistant Hydraulic Cement Moderate sulfate resistant hydraulic cement remains sturdy around sulfates because it has chlorides added into it. This hydraulic cement is useful for structures that are built along coastlines, since they may come into contact with more water than the average structure. Ex. Type II Portland Cement with Sulfate Resistance High Sulfate-Resistant Hydraulic Cement Similar to low heat of hydration hydraulic cement, it gains this advantage in exchange for gaining a longer curing time. A structure that will be exposed to sulfates frequently and in high quantities, such as a dock, can benefit from being constructed with this type of hydraulic cement. Ex. Lafarge High HS kalicrete How to Apply Hydraulic Cement? Preparation ✓ The surface on which the cement is to be applied should be clean. Dirt, oil, grease and loose particles will prevent the cement from adhering to the surface properly. ✓ It is imperative for the temperature to be maintained between 45°F (7°C) and 90°F (32°C) during initial curing since the cement will not be durable on frozen surfaces. ✓ The area should be saturated for 24 hours before applying cement there. ✓ Small cracks and holes should be enlarged prior to the cement application. V-shaped cuts are to be avoided. Mixing Cement ✓ A mechanical mixer with rotatory blades is recommended for mixing the cement to get a uniform mix. ✓ The mixer should be saturated and drained of excess water prior to mixing. ✓ Following the manufacturer’s instruction, the required amount of water is to be added to the proper amount of dry hydraulic cement. However, once it begins to set, water should not be added anymore. ✓ It is recommended that small amounts of cement be mixed at a time since it hardens very quickly and has to be placed within 10-15 minutes. ✓ The cement mix should be blended at a relatively low speed. Applying Hydraulic Cement ✓ The hydraulic cement mix should be applied as quickly as possible. ✓ Excessive blending will cause bleeding and segregation. ✓ Any other additives or admixtures should not be added unless mentioned in the manufacturer’s instructions. SETTING TIME OF HYDRAULIC CEMENT What is setting time? When water is mixed with cement, it forms a paste that can be molded into any shape due to its plasticity. But after some time the cement will lose its plasticity and starts setting. This entire cycle is known as setting time. In simple terms, it is the time required for cement to lose its plasticity is known as setting time. Setting time is categorized into the Initial setting time and the Final setting time of cement. What is the Initial setting time and the Final setting time of cement? These two properties of cement are very useful in deciding the time required for transportation, placing, and compaction of cement concrete. Initial setting time of cement – it is the time required for the cement to be able to mold into any desired shape. Final setting time of cement - it is the time at which cement starts hardening and completely loses its plasticity. Factors affecting setting time of cement? ❑ Mineral composition of cement ❑ Amount of gypsum in the cement ❑ Cement fineness ❑ Water required for mixing (water-cement ratio) ❑ Admixtures What is water cement ratio ? It is the ratio of the mass of water to the mass of cement added to concrete. The water cement ratio formula directly affects the strength & durability of the concrete. The typical water-cement ratio varies between 0.40 - 0.60 for different grades of concrete mix. Water cement ratio = Weight of water/Weight of cement For example if the water-cement ratio is 0.50 for concrete and cement added is 50 kg (weight of 1 bag of cement). Water required for concrete will be: Water / cement = 0.50 Water / 50kg = 0.50 Water = 0.50 x 50 = 25 liters. Setting time tests Setting tests are used to characterize how a particular cement paste sets. For construction purposes, the initial set must not be too soon and the final set must not be too late. Additionally, setting times can give some indication of whether or not a cement is undergoing normal hydration. Standard Tests: AASHTO T 131 and ASTM C 191: Time of Setting of Hydraulic Cement by Vicat Needle AASHTO T 154: Time of Setting of Hydraulic Cement by Gillmore Needles ASTM C 266: Time of Setting of Hydraulic-Cement Paste by Gillmore Needles Vicat Needle AASHTO T131 is a standard test method used to determine the time of setting of hydraulic cement, such as Portland cement, by using a Vicat needle apparatus. This test is essential for assessing the rate at which cement paste stiffens and hardens, providing valuable information for concrete mix design, construction scheduling, and quality control. The primary objective of this test is to determine the initial and final setting times of hydraulic cement paste. The initial setting time is the time elapsed between the initial contact of cement and water and the time when the Vicat needle penetrates the paste to a specified depth. The final setting time is the time when the Vicat needle no longer makes an indentation on the paste surface. Vicat Apparatus Test Procedure Preparation 1) First, take 300 grams of Cement in a pan and mix with the known percentage of water by weight of Cement, assume starting from 26% and then increase it by every 2% until the normal Consistency is achieved. 2) With continuous mixing. 3) Start the Stopwatch as soon as the water added to Cement. 4) Now fill the paste into the Mould with a non-porous plate below. Level and Smoothen the surface of the paste. Initial Setting Time Test 1) Place the mould in the Vicat Apparatus allow the Needle to touch the surface of paste and then quickly release allowing it to freely sink into paste. 2) Repeat this procedure until the needle when released fails to penetrate the block beyond 5mm from the bottom of the mould. 3) Record this time and this shall be the Initial setting Time. Test Procedure Final Setting Time Test 1) Replace the needle by final setting time needle. 2) The cement shall be considered as finally set when, upon applying the needle gently on the surface of the test block, the needle makes an impression and fails to penetrate. 3) The time elapsed between the time when water is added and the time at which the needle makes an impression on the surface of the test block shall be considered as Final Setting Time of Cement sample. Calculation of Initial setting time and the Final setting time of cement Gillmore Needle The Gillmore needle apparatus is used to determine the setting time of cement. The vertical support shaft has a device to maintain the horizontal arms in alignment. The adjustable support has horizontal arms to guide two weighted needles with flat-end cylindrical stainless steel tips. The base has an ample flat shelf for positioning specimens. The initial setting needle is 2.12mmin diameter and weighs 113g. The final setting needle is 1.06mm in diameter and weighs 453.6g. The Gillmore needle apparatus is a widely used tool in cement testing to determine the initial and final setting times of cement. It provides valuable information about the time required for cement paste to transition from a plastic, workable state to a hardened state. This information is essential for various construction applications, as it helps determine the optimal time for various operations, such as mixing, placing, and finishing concrete. The Gillmore needle apparatus consists of two needles—a reference needle and a test needle—and a needle holder. The initial setting time is defined as the time at which the test needle ceases to make a perceptible impression on the cement paste. It indicates the point at which the cement begins to lose its plasticity and starts to harden. The final setting time is the time at which the test needle fails to penetrate the paste, indicating the completion of the hardening process. Gillmore Apparatus Flat Trowel Mixer, Bowl, Paddle, and Scraper Glass Graduates Mass Determining Devices Plane Nonabsorptive Plates Gillmore Needles Test Procedure Preparation 1) Prepare a batch of paste by mixing 650g of cement with the percentage of mixing water required for normal consistency as described in ASTM C187 OR At the option of the tester, use the paste remaining from the batch used for autoclave expansion or normal consistency. 2) From the cement paste, make a pat with a flat top and the sides tapering to a thin edge on a plane non-absorptive plate. 3) In molding the pat, flatten the paste first on the plate and then form the pat by drawing the trowel from the outer edge toward the center then flattening the top. 4) Dimensions of the pat? Base diameter 76±13 mm (3±0.5 in), top diameter 50±13mm (2±0.5i n), and center thickness 13±3mm. 5) Immediately after molding, place the test specimen and plate in the moisture cabinet or moisture Initial Setting Time Test 1) Determine the time of setting by holding the needle in a vertical position and lightly applying it to the surface of the pat. 2) Using the Initial Gillmore needle, determine the Gillmore Initial Time of setting end point to be the first penetration measurement that does not mark the specimen surface with a complete circular impression. 3) Verify the Initial set by performing two additional penetration measurements on different areas of the specimen surface within 90 sec of the first measurement. The elapsed time between the initial contact of cement and water and the end point is the Gillmore Initial time of setting. Final Setting Time Test 1) Using the Final Gillmore needle, determine the Gillmore Final Time of setting end point to be the first penetration measurement that does not mark the specimen surface with a complete circular impression. 2) Verify the Final set by performing two additional penetration measurements on different areas of the specimen surface within 90 sec of the first measurement. The elapsed time between the initial contact of cement and water and the end point is the Gillmore Final time of setting. EXAMPLE. Table 1 shows ASTM C 150 specified set times. Importance of Determination of Setting Time of Hydraulic Cement Helps determine the appropriate timing for mixing, transporting, placing, and finishing concrete. Helps verify the consistency and performance of cement. Ensures that concrete is placed and finished before it sets, preventing Prevents accidents and injuries. Ensures adherence to industry standards and regulations. Helps avoid delays and rework, reducing overall project costs. Reference https://www.astm.org/standards/c191 https://standards.globalspec.com/std/9945585/aashto-t-154 https://www.astm.org/standards/c266 https://civiltoday.com/civil-engineering-materials/cement/hydraulic-cement/103-how- to-apply-hydraulic- cement?fbclid=IwY2xjawE5KBlleHRuA2FlbQIxMAABHaiYUS7DuWIRR- jVdt58jVZ__177g21LDMWZ3VQ5ujGxWpTdMUfp0X0i4g_aem_t8nh_y3sEYAO0UXZ dXp9Rw#google_vignette https://civiltoday.com/civil-engineering-materials/cement/111-properties-of-cement- physical-chemical-properties https://www.odot.org/materials/C97001_WEB_REP/TECH_EVAL_CLISTS/CLISTS/0 0033.pdf THANK YOU!!!