QBA Exam Revision PDF
Document Details
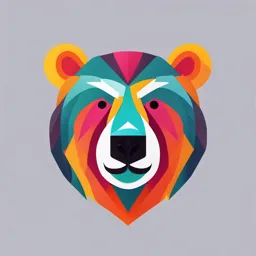
Uploaded by EvaluativeMorganite9649
American University of Nigeria
Tags
Summary
This document covers product development concepts, including product decisions, strategy options, life cycles, and quality function deployment. It also discusses generating new products, and quality management, including various tools and processes
Full Transcript
QBA REVISION-CHAPTER 5 ====================== - **Product Decision**: The objective of the product decision is to develop and implement a product strategy that meets the demands of the marketplace with a competitive advantage - **Product Strategy Options** - Differentiation: Shouldi...
QBA REVISION-CHAPTER 5 ====================== - **Product Decision**: The objective of the product decision is to develop and implement a product strategy that meets the demands of the marketplace with a competitive advantage - **Product Strategy Options** - Differentiation: Shouldice Hospital - Low cost: Taco Bell - Rapid response: Toyota - **Product Life Cycles** - May be any length from a few days to decades - The operations function must be able to introduce new products successfully - **Life Cycle and Strategy** - **Introductory Phase** Fine tuning may warrant unusual expenses for - Research - Product development - Process modification and enhancement - Supplier development - **Growth Phase** - Product design begins to stabilize - Effective forecasting of capacity becomes necessary - Adding or enhancing capacity may be necessary - **Maturity Phase** - Competitors now established - High volume, innovative production may be needed - Improved cost control, reduction in options, paring down of product line - **Decline Phase** - Unless product makes a special contribution to the organization, must plan to terminate offering - **Product-By-Value Analysis** - Lists products in descending order of their individual dollar contribution to the firm - Lists the total annual dollar contribution of the product - Helps management evaluate alternative strategies - **Generating New Products** - Understanding the customer - Economic change - Sociological and demographic change - Technological change - Political and legal change - Market practice, professional standards, suppliers, distributors - **Quality Function Deployment** - **Quality function deployment (Q F D)** - Determine what will satisfy the customer - Translate those customer desires into the target design - **House of quality** - Utilize a planning matrix to relate customer **wants** to **how** the firm is going to meet those **wants** - **Quality Function Deployment** - Identify customer **wants** - Identify **how** the good/service will satisfy customer wants - Relate customer wants to product **hows** - Identify relationships between the firm's **hows** - Develop **our** importance ratings - Evaluate competing products - Compare performance to desirable technical attributes - **Organizing for Product Development** - Traditionally -- distinct departments - Duties and responsibilities are defined - Difficult to foster forward thinking - A Champion - Product manager drives the product through the product development system and related organizations - Team approach - Cross functional -- representatives from all disciplines or functions - Product development teams, design for manufacturability teams, value engineering teams - Japanese "whole organization" approach - No organizational divisions - Product development teams - Market requirements to product success - Cross functional teams often involving vendors - Open, highly participative environment - Concurrent engineering - Simultaneous performance of product development stages - **Manufacturability and Value Engineering** - Benefits: - Reduced complexity of the product - Reduction of environmental impact - Additional standardization of components - Improvement of functional aspects of the product - Improved job design and job safety - Improved maintainability (serviceability) of the product - Robust design - **Issues for Product Design** - Robust design - Product is designed so that small variations in production or assembly do not adversely affect the product - Typically results in lower cost and higher quality - Modular design - Products designed in easily segmented components - Adds flexibility to both production and marketing - Improved ability to satisfy customer requirements - Computer-aided design (C A D) - Using computers to design products and prepare engineering documentation - Shorter development cycles, improved accuracy, lower cost - Information and designs can be deployed worldwide - Computer-aided manufacturing (C A M) - Utilizing specialized computers and program to control manufacturing equipment - Often driven by the C A D system (C A D / C A M) - Virtual reality technology - Computer technology used to develop an interactive, 3 - D model of a product from the basic C A D data - Allows people to 'see' the finished design before a physical model is built - Very effective in large-scale designs such as plant layout - Value analysis - Focuses on design improvement during production - Seeks improvements leading either to a better product or a product which can be produced more economically with less environmental impact - Sustainability and Life Cycle Assessment (L C A) - **Sustainability** means meeting the needs of the present without compromising the ability of future generations to meet their needs - L C A is a formal evaluation of the environmental impact of a product - **Extensions of C A D** - 3 - D Object Modeling - Small prototype development - Design for Manufacturing and Assembly (D F M A) - Solve manufacturing problems during the design stage - C A D through the internet - International data exchange through S T E P - 3 - D printing - **Benefits of C A D/C A M** - Product quality - Shorter design time - Production cost reductions - Database availability - New range of capabilities - **Product Development Continuum** - Product life cycles are becoming shorter and the rate of technological change is increasing - Developing new products faster can result in a competitive advantage - **Time-based competition** - Purchasing technology by acquiring a firm - Speeds development - Issues concern the fit between the acquired organization and product and the host - Joint Ventures - Both organizations learn - Risks are shared - Alliances - Cooperative agreements between independent organizations - Useful when technology is developing - Reduces risks - **Defining a Product** - First definition is in terms of **functions** - Rigorous specifications are developed during the design phase - Manufactured products will have an **engineering drawing** - **Bill of material (B O M)** lists the components of a product - **Product Documents** - Engineering drawing - Shows dimensions, tolerances, and materials - Shows codes for Group Technology - Bill of Material - Lists components, quantities and where used - Shows product structure - **Make-Or-Buy Decisions** - Produce components themselves or buy from an outside source - Variations in - Quality - Cost - Delivery schedules - Critical to product definition **Group Technology** - Parts grouped into families with similar characteristics - Coding system describes processing and physical characteristics - Part families can be produced\ in dedicated manufacturing cells **Group Technology Benefits** 1. Improved design 2. Reduced raw material and purchases 3. Simplified production planning and control 4. Improved layout, routing, and machine loading 5. Reduced tooling setup time, work-in-process, and production time **Documents for Production** - Assembly drawing - Shows exploded view of product - Details relative locations to show how to assemble the product - Assembly chart - Identifies the point of production where components flow into subassemblies and ultimately into the final product - Route sheet - Lists the operations and times required to produce a component - Work order - Instructions to produce a given quantity of a particular item, usually to a schedule - Engineering change notices (E C N s) - A correction or modification to a product's definition or documentation - Engineering drawings - Bill of material - **Quite common with long product life cycles, long manufacturing lead times, or rapidly changing technologies** **Configuration Management** - The need to manage E C N s has led to the development of configuration management systems - A product's planned and changing components are accurately identified - Control and accountability for change are identified and maintained **Product Life-Cycle Management (P L M)** - Integrated software that brings together most, if not all, elements of product design and manufacture - Product design - C A D/C A M - D F M A - Product routing - Materials - Layout - Assembly - Maintenance - Environmental **Service Design** - Service typically includes direct interaction with the customer - **Process -- chain -- network (P C N)** analysis focuses on the ways in which processes can be designed to optimize interaction between firms and their customers **Process-Chain-Network (P C N) Analysis** 1. **Direct interaction** region includes process steps that involve interaction between participants 2. The **surrogate (substitute) interaction** region includes process steps in which one participant is acting on another participant's resources 3. The **independent processing** region includes steps in which the supplier and/or the customer is acting on resources where each has maximum control 4. All three regions have similar operating issues but the appropriate way of handling the issues differs across regions -- service operations exist only within the area of **direct** and **surrogate interaction** 5. P C N analysis provides insight to aid in positioning and designing processes that can achieve strategic objectives **Adding Service Efficiency** - Service productivity is notoriously low partially because of customer involvement in the **design** or **delivery** of the service, or both - Complicates product design - Limit the options - Improves efficiency and ability to meet customer expectations - Delay customization - Modularization Eases customization of a service - Automation - Reduces cost, increases customer service - Moment of truth - Critical moments between the customer and the organization that determine customer satisfaction **Documents for Services** - High levels of customer interaction necessitates different documentation - Often explicit job instructions - Scripts and storyboards are other techniques **Application of Decision Trees to Product Design** - Particularly useful when there are a series of decisions and outcomes that lead to other decisions and outcomes A diagram shows a decision tree. A decision node branches into two chance nodes. Each chance node branches into two outcomes. - **Procedure** 1. Include all possible alternatives and states of nature -- including "doing nothing" 2. Enter payoffs at end of branch 3. Determine the expected value of each branch and "prune" the tree to find the alternative with the best expected value **Transition to Production** - Know when to move to production - Product development can be viewed as evolutionary and never complete - Product must move from design to production in a timely manner - Most products have a trial production period to insure producibility - Develop tooling, quality control, training - Ensures successful production - Responsibility must also transition as the product moves through its life cycle - Line management takes over from design - Three common approaches to managing transition - Project managers - Product development teams - Integrate product development and manufacturing organizations CHAPTER 6 ========= **Quality and Strategy** - Managing quality supports **differentiation**, **low cost**, and **response** strategies - Quality helps firms increase sales and reduce costs - **Building** a quality organization is a demanding task  **The Flow of Activities** A chart illustrates the activities necessary to achieve total quality management, as summarized in order below. Organizational practices. Leadership, mission statement, effective operating procedures, staff support, training. Yields. What is important and what is to be accomplished. Quality principles. Customer focus, continuous improvement, benchmarking, just in time, tools of T Q M. Yields. How to do what is important and to be accomplished. Employee fulfillment. Empowerment, organizational commitment. Yields. Employee attitudes that can accomplish what is important. Customer satisfaction. Winning orders, repeat customers. Yields. An effective organization with a competitive advantage. **Defining Quality** - **An operations manager's objective is to build a total quality management system that identifies and satisfies customer needs** - The totality of features and characteristics of a product or service that bears on its ability to satisfy stated or implied needs **Different Views** - **User based:** better performance, more features - **Manufacturing based:** conformance to standards, making it right the first time - **Product based:** specific and measurable attributes of the product **Implications of Quality** 1. Company reputation 1. Perception of new products 2. Employment practices 3. Supplier relations 2. Product liability 4. Reduce risk 3. Global implications 5. Improved ability to compete **I S O 9000 International Quality Standards** - International recognition - Encourages quality management procedures, detailed documentation, work instructions, and recordkeeping - 2015 revision gives greater emphasis to **risk-based thinking** - Over one million certifications in 206 countries - Critical for global business - Management principles - Top management leadership - Customer satisfaction - Continual improvement - Involvement of people - Process analysis - Use of data-driven decision making - A systems approach to management - Mutually beneficial supplier relationships **Costs of Quality** - **Prevention costs** - reducing the potential for defects - **Appraisal costs** - evaluating products, parts, and services - **Internal failure costs** - producing defective parts or service before delivery - **External failure costs** - defects discovered after delivery **Takumi** - A Japanese character that symbolizes a broader dimension than quality, a deeper process than education, and a more perfect method than persistence **Ethics and Quality Management** - Operations managers must deliver healthy, safe, quality products and services - Poor quality risks injuries, lawsuits, recalls, and regulation - Ethical conduct must dictate response to problems - All stakeholders must be considered **Total Quality Management** - Encompasses entire organization from supplier to customer - Stresses a commitment by management to have a continuing companywide drive toward excellence in all aspects of products and services that are important to the customer **Deming\'s Fourteen Points** 1. Create consistency of purpose 2. Lead to promote change 3. Build quality into the product; stop depending on inspections to catch problems 4. Build long-term relationships based on performance instead of awarding business on price 5. Continuously improve product, quality, and service 6. Start training 7. Emphasize leadership 8. Drive out fear 9. Break down barriers between departments 10. Stop haranguing workers 11. Support, help, and improve 12. Remove barriers to pride in work 13. Institute a vigorous program of education and self-improvement 14. Put everyone in the company to work on the transformation **Seven Concepts of T Q M** 1. Continuous improvement - Never-ending process of continuous improvement - Covers people, equipment, suppliers, materials, procedures - Every operation can be improved - **Kaizen** describes the ongoing process of unending improvement - **T Q M** and **zero defects** also used to describe continuous improvement 2. Six Sigma - Two meanings - **Statistical** definition of a process that is 99.9997% capable, 3.4 defects per million opportunities (D P M O) - A **program** designed to reduce defects, lower costs, save time, and improve customer satisfaction - A comprehensive system for achieving and sustaining business success - Originally developed by Motorola, adopted and enhanced by Honeywell and G E - Highly structured approach to process improvement - A strategy - A discipline -- D M A I C - A set of 7 tools - **Defines** the project's purpose, scope, and outputs, then identifies the required process information keeping in mind the customer's definition of quality - **Measures** the process and collects data - **Analyzes** the data ensuring repeatability and reproducibility - **Improves** by modifying or redesigning existing processes and procedures - **Controls** the new process to make sure performance levels are maintained 3. Employee empowerment - Getting employees involved in product and process improvements - 85% of quality problems are due to materials and process - Techniques - Build communication networks that include employees - Develop open, supportive supervisors - Move responsibility to employees - Build a high-morale organization - Create formal team structures 4. Benchmarking: Selecting best practices to use as a standard for performance - Determine what to benchmark - Form a benchmark team - Identify benchmarking partners - Collect and analyze benchmarking information - Take action to match or exceed the benchmark 5. Just-in-time (J I T) - 'Pull' system of production scheduling including supply management - Production only when signaled - Allows reduced inventory levels - Inventory costs money and hides process and material problems - Encourages improved process and product quality - Relationship to quality: - J I T cuts the cost of quality - J I T improves quality - Better quality means less inventory and better, easier-to-employ J I T system 6. Taguchi concepts - Engineering and experimental design methods to improve product and process design - Identify key component and process variables affecting product variation - Taguchi Concepts - **Quality robustness** Ability to produce products uniformly in adverse manufacturing and environmental conditions - Remove the **effects** of adverse conditions - Small variations in materials and process do not destroy product quality - **Target-oriented quality** - Shows that costs increase as the product moves away from what the customer wants - Costs include customer dissatisfaction, warranty\ and service, internal\ scrap and repair, and costs to society - Traditional conformance specifications are too simplistic - **Quality loss function** 7. Knowledge of T Q M tools - Tools for Generating Ideas - Check Sheet: An organized method of recording data - Scatter Diagram: A graph of the value of one variable vs. another variable - Cause-and-Effect Diagram: A tool that identifies process elements (causes) that may effect an outcome - Tools to Organize the Data - Pareto Chart: A graph to identify and plot problems or defects in descending order of frequency - Flowchart (Process Diagram): A chart that describes the steps in a process - Tools for Identifying Problems - Histogram: A distribution showing the frequency of occurrences of a variable - Statistical Process Control Chart: A chart with time on the horizontal axis to plot values of a statistic **Quality Circles** - Group of employees who meet regularly to solve problems - Trained in planning, problem solving, and statistical methods - Often led by a **facilitator** - Very effective when done properly **Best Practices for Resolving Customer Complaints** +-----------------------------------+-----------------------------------+ | - **Best Practice** | - **Justification** | +===================================+===================================+ | - Make it easy for clients to | - It is free market research | | complain | | +-----------------------------------+-----------------------------------+ | - Respond quickly to complaints | - It adds customers and loyalty | +-----------------------------------+-----------------------------------+ | - Resolve complaints on first | - It reduces cost | | contact | | +-----------------------------------+-----------------------------------+ | - Use computers to manage | - Discover trends, share them, | | complaints | and align your services | +-----------------------------------+-----------------------------------+ | - Recruit the best for customer | - It should be part of formal | | service jobs | training and career | | | advancement | +-----------------------------------+-----------------------------------+ **Internal Benchmarking** - When the organization is large enough - Data more accessible - Can and should be established in a variety of areas **Flow Charts** - M R I Flowchart 1. Physician schedules M R I 2. Patient taken to M R I 3. Patient signs in 4. Patient is prepped 5. Technician carries out M R I 6. Technician inspects film 7. If unsatisfactory, repeat 8. Patient taken back to room 9. M R I read by radiologist 10. M R I report transferred to physician 11. Patient and physician discuss **Statistical Process Control (S P C)** - Uses statistics and control charts to tell when to take corrective action - Drives process improvement - Four key steps - Measure the process - When a change is indicated, find the assignable cause - Eliminate or incorporate the cause - Restart the revised process **Control Charts** Control Chart for Percentage of Free-throws Missed by the Orlando Magic in Their First Nine Games of the New Season. **Inspection** - Involves examining items to see if an item is good or defective - Detect a defective product - Does not correct deficiencies in process or product - It is expensive - Issues - When to inspect - Where in process to inspect **When and Where to Inspect** 1. At the supplier's plant while the supplier is producing 2. At your facility upon receipt of goods from your supplier 3. Before costly or irreversible processes 4. During the step-by-step production process 5. When production or service is complete 6. Before delivery to your customer 7. At the point of customer contact - Many problems - Worker fatigue - Measurement error - Process variability - Cannot inspect quality into a product - Robust design, empowered employees, and sound processes are better solutions **Source Inspection** - Also known as **source control** - The next step in the process is your customer - Ensure perfect product to your\ customer - **Poka-yoke** is the concept of foolproof devices or techniques designed to pass only acceptable products - **Checklists** ensure consistency and completeness **Service Industry Inspection** +-----------------------+-----------------------+-----------------------+ | - **Organization** | - **What Is | - **Standard** | | | Inspected** | | +=======================+=======================+=======================+ | - Alaska Airlines | - Last bag on | - Less than 20 | | | carousel | minutes after | | | | arrival at the | | | - Airplane door | gate | | | opened | | | | | - Less than 2 | | | | minutes after | | | | arrival at the | | | | gate | +-----------------------+-----------------------+-----------------------+ | - Jones Law Office | - Receptionist | - Phone answered by | | | performance | the second ring | | | | | | | - Billing | - Accurate, timely, | | | | and correct | | | - Attorney | format | | | | | | | | - Promptness in | | | | returning calls | +-----------------------+-----------------------+-----------------------+ | - Hard Rock Hotel | - Reception desk | - Use customer's | | | | name | | | - Doorman | | | | | - Greet guest in | | | - Room | less than 30 | | | | seconds | | | - Minibar | | | | | - All lights | | | | working, spotless | | | | bathroom | | | | | | | | - Restocked and | | | | charges | | | | accurately posted | | | | to bill | +-----------------------+-----------------------+-----------------------+ | - Organization | - What Is Inspected | - Standard | +-----------------------+-----------------------+-----------------------+ | - Arnold Palmer | - Billing | - Accurate, timely, | | Hospital | | and correct | | | - Pharmacy | format | | | | | | | - Lab | - Prescription | | | | accuracy, | | | - Nurses | inventory | | | | accuracy | | | - Admissions | | | | | - Audit for | | | | lab-test accuracy | | | | | | | | - Charts | | | | immediately | | | | updated | | | | | | | | - Data entered | | | | correctly and | | | | completely | +-----------------------+-----------------------+-----------------------+ | - Olive Garden | - Busboy | - Serves water and | | Restaurant | | bread within 1 | | | - Busboy | minute | | | | | | | - Waiter | - Clears all entrée | | | | items and crumbs | | | | prior to dessert | | | | | | | | - Knows and suggest | | | | specials, | | | | desserts | +-----------------------+-----------------------+-----------------------+ | - Organization | - What Is Inspected | - Standard | +-----------------------+-----------------------+-----------------------+ | - Nordstrom | - Display areas | - Attractive, | | Department\ | | well-organized, | | Store | - Stockrooms | stocked, good | | | | lighting | | | - Salesclerks | | | | | - Rotation of | | | | goods, organized, | | | | clean | | | | | | | | - Neat, courteous, | | | | very | | | | knowledgeable | +-----------------------+-----------------------+-----------------------+ **Attributes Versus Variables** - **Attributes** - Items are either good or bad, acceptable or unacceptable - Does not address **degree** of failure - **Variables** - Measures dimensions such as weight, speed, height, or strength - Falls within an acceptable range - Use different statistical techniques **T Q M In Services** - Service quality is more difficult to measure than the quality of goods - Service quality perceptions depend on - **Intangible differences between products** - **Intangible expectations customers have of those products** **Service Quality** - The operations manager must recognize: - The tangible component of services is important - The service process is important - The service is judged against the customer's expectations - Exceptions will occur **Determinants of Service Quality** - **Reliability** involves consistency of performance and dependability - **Responsiveness** concerns the willingness or readiness of employees to provide service - **Competence** means possession of the required skills and knowledge to perform the service - **Access** involves approachability and ease of contact - **Courtesy** involves politeness, respect, consideration, and friendliness - **Communication** means keeping customers informed and listening to them - **Credibility** involves trustworthiness, believability, and honesty - **Security** is the freedom from danger, risk, or doubt - **Understanding/knowing the customer** involves making the effort to understand the customer\'s needs - **Tangibles** include the physical evidence of the service **Service Recovery Strategy** - Managers should have a plan for when services fail - Marriott\'s **Learn** routine - Listen - Empathize - Apologize - React - Notify