Standalone Incinerators Project Proposal PDF
Document Details
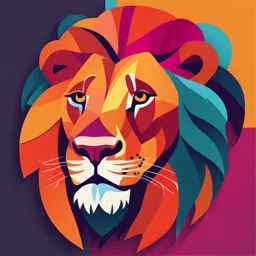
Uploaded by UndisputedEucalyptus3158
Durban University of Technology
2025
Yuashin Sewsunker
Tags
Summary
This project proposal describes Standalone Incinerators designed for efficient waste disposal, reducing environmental impact. The process is continuous, involving waste loading, primary chamber combustion, secondary chamber function, and auxiliary heat & exhaust.
Full Transcript
09 02 2025 ─ Yuashin Sewsunker 1 Standalone Incinerators 1. System Overview Macrotec’s Standalone Incinerators are designed to dispose of various wastes efficiently while reducing environmental impact...
09 02 2025 ─ Yuashin Sewsunker 1 Standalone Incinerators 1. System Overview Macrotec’s Standalone Incinerators are designed to dispose of various wastes efficiently while reducing environmental impact. The process operates on a continuous feed basis, which means: Waste Loading: Waste is periodically loaded (either manually or automatically) into the primary combustion chamber without halting the process. Primary Chamber Combustion: The waste is spread over a large hearth in a chamber lined with high-temperature alumina-silicate refractory. Here, high-velocity combustion air is injected to promote turbulence and ensure optimal oxygen mixing. Secondary Chamber Function: After initial combustion, combustion products pass into a secondary chamber that provides a two‑second retention time to allow particulate matter to settle out. Auxiliary Heat & Exhaust: Auxiliary burners (diesel, LPG, or natural gas) preheat and maintain the chamber temperatures, while a tall flue gas chimney (7–15 m or taller) increases draft, ensuring efficient removal and dispersion of exhaust gases. This design not only improves combustion efficiency and fuel consumption (by eliminating repetitive preheating) but also significantly lowers emissions. 2. Component Details Below are the key components and instruments used in the system, along with their specific names and functions: A. Incinerator Chambers Primary Chamber (Combustion Chamber): ○ Exact Component: Incinerator hearth lined with high-temperature alumina-silicate refractory. 2 ○ Function: Distributes waste evenly for combustion. The refractory (with a cold crushing strength of 80 MPa and service temperature up to 1,500˚C) protects the structure and maintains high temperatures. Secondary Chamber (Settling Chamber): ○ Exact Component: Secondary chamber designed for a two-second reaction (retention) time. ○ Function: Allows particulates to settle out, ensuring complete combustion and reduced particulate emissions. B. Thermal Protection Refractory Lining: ○ Exact Material: High-temperature alumina-silicate refractory. ○ Function: Provides thermal resistance, structural durability, and protection against abrasion and acid exposure. Insulation: ○ Exact Material: 100 mm low-density insulation. ○ Function: Offers an R-value of approximately 1.54 m²K/W to minimize heat loss, thereby reducing fuel consumption and enhancing operational safety. C. Fuel and Combustion Control Auxiliary Burners: ○ Exact Options: Diesel, LPG, or Natural Gas burners with integrated burner fuel trains. ○ Function: Preheat the incinerator before waste feeding begins and maintain a stable, high combustion temperature throughout the process. Feeding Systems: ○ Manual Feeder: Function: Provides a cost-effective and safe method for operators to load waste into the incinerator without exposure to direct heat. ○ Auto Feeder: Function: Automates waste feeding. Once loaded and the safety button is engaged, it controls the feed rate to prevent overfeeding and to ensure consistent combustion. D. Air and Exhaust Management Combustion Air Fans: ○ Exact Instrument: High-velocity centrifugal or axial fans (commonly available from manufacturers like Greenheck or Twin City Fan). 3 ○ Function: Deliver high-speed air into the primary chamber to induce turbulence and improve the mixing of oxygen with combustion gases. Flue Gas Chimney (Stack): ○ Exact Component: Stack with configurable heights (standard 7–15 m, with taller options available). ○ Function: Enhances the draft to achieve high flue gas velocity and ensures efficient dispersion of exhaust gases. The design is guided by EPA recommendations (calculation based on H + 1.5L). E. Containerised Installation (Optional) Containerised Incinerator Package: ○ Exact Components: Includes an insulated platform, diesel run-off area, weather louvres, extractor fans, a DB panel mounted on the container wall, cable trays, chimney flashing, fire extinguishers, safety signs, a solenoid valve on the diesel line (per BS EN746-2), and a 1,000L diesel tank. ○ Function: Allows for quick transport and installation on-site, particularly in remote or emergency situations. F. Sensors & Instrumentation Temperature Sensors: ○ Exact Instrument: Omega K-Type thermocouples. ○ Function: Monitor combustion chamber temperatures to ensure efficient combustion and safe operation. Pressure Sensors: ○ Exact Instrument: Honeywell industrial pressure transducers. ○ Function: Monitor pressure within the combustion chambers and ductwork, ensuring system integrity. Flow Sensors: ○ Exact Instrument: Siemens or Emerson flow meters. ○ Function: Measure the velocity and volume of combustion air, critical for maintaining the right oxygen-to-fuel ratio. Emission Sensors: ○ Exact Instrument: Testo gas analyzers. ○ Function: Monitor the levels of CO, NOₓ, and other by-products to ensure compliance with environmental regulations. G. Control and Networking Equipment Programmable Logic Controller (PLC): 4 ○ Exact Options: Siemens S7 series or Allen-Bradley ControlLogix. ○ Function: Acts as the central controller, gathering data from sensors, processing it through programmed logic, and issuing commands to actuators to maintain optimal system performance. Human-Machine Interface (HMI): ○ Function: Provides operators with a visual display of real-time process data, system status, and control options. Industrial Ethernet Switches: ○ Exact Instrument: Devices such as Cisco Industrial Ethernet or Siemens SCALANCE. ○ Function: Facilitate reliable communication between the PLC, sensors, and HMI using protocols like Modbus/TCP, Ethernet/IP, or PROFINET. 3. PLC Functionality The Programmable Logic Controller (PLC) is the “brain” of the incinerator system. Its basic flow of operations includes: 1. Input Collection: ○ Sensors (temperature, pressure, flow, and emissions) continuously send analog/digital signals to the PLC. 2. Processing & Decision-Making: ○ The PLC runs pre-programmed logic to compare sensor readings against setpoints. If values deviate, it calculates the necessary adjustments. ○ For example, if the temperature drops, the PLC might increase the auxiliary burner output or adjust the speed of the combustion air fans. 3. Output Execution: ○ The PLC issues control commands to various actuators: Variable Frequency Drives (VFDs): Adjust fan speeds. Feeder Controls: Regulate waste input. Burner Controls: Modulate the auxiliary burners. ○ This ensures the system stays within the optimal combustion range, maintaining energy efficiency and low emissions. 4. Feedback Loop & Monitoring: ○ The system operates as a closed-loop, where sensor feedback is continuously processed, enabling real-time adjustments. ○ Data is relayed to the HMI, allowing remote monitoring and diagnostics. 5 5. Networking: ○ The PLC communicates over an industrial network (using Ethernet switches and protocols like Modbus/TCP) with other system components, ensuring integrated, reliable operation. 4. Interview Preparation Potential Interview Questions with Optimal Answers Q1: Can you explain the overall operational flow of Macrotec’s Standalone Incinerator? A: "Macrotec’s Standalone Incinerator operates on a continuous feed basis. Waste is loaded into a primary chamber where a large hearth ensures even distribution. High-velocity air is injected to create turbulence and mix oxygen with the waste, initiating efficient combustion. The combustion gases then move into a secondary chamber designed for a two‑second retention time, allowing particulates to settle. Auxiliary burners preheat and maintain the required temperature, while a tall flue gas stack ensures proper exhaust dispersion. Throughout the process, sensors monitor key parameters, and a PLC uses this data to control fans, feeders, and burners in a closed-loop system." Q2: What are the critical components of the incinerator, and what roles do they serve? A: "The system includes two primary chambers: the primary combustion chamber lined with high-temperature alumina-silicate refractory and a secondary settling chamber. Thermal protection is provided by the refractory and 100 mm low-density insulation. Auxiliary burners (diesel, LPG, or natural gas) preheat and stabilize combustion. Waste is fed through either a manual or auto feeder. High-velocity combustion air fans enhance the mixing of oxygen, and a flue gas chimney (7–15 m) ensures effective exhaust dispersion. Additional sensors (temperature, pressure, flow, and emission) continuously monitor system performance, feeding data to a central PLC for precise control." 6 Q3: How does the PLC manage the incinerator’s operations? A: "The PLC continuously gathers input from various sensors placed throughout the incinerator. It processes this data using pre-programmed control logic and makes real-time decisions to adjust system components. For example, if the temperature is too low, the PLC may increase auxiliary burner output or fan speed. Commands are sent to actuators such as VFDs, feeder controls, and burner controls. This closed-loop system ensures efficient combustion, minimizes emissions, and provides operators with real-time feedback through an HMI over an industrial network." Q4: Why is it beneficial to have both manual and auto feeder options in the system? A: "Offering both options provides operational flexibility. A manual feeder allows operators to load waste safely and cost-effectively, minimizing direct exposure to high temperatures. The auto feeder, on the other hand, automates the waste feed process, preventing overfeeding and ensuring a consistent, controlled input. This dual capability improves both safety and efficiency, particularly in varied operational scenarios." Q5: What networking protocols are typically used to connect the PLC with sensors and the HMI? A: "Common protocols include Modbus/TCP, Ethernet/IP, and PROFINET. These protocols offer robust, real-time communication between the PLC, sensors, and HMI, ensuring reliable data exchange and enabling remote monitoring and control—essential for systems operating in remote or harsh environments." Q6: How do the design features of the incinerator contribute to environmental protection? A: "The incinerator’s design incorporates large combustion and settling chambers, high-velocity air for optimal turbulence, and strategically placed auxiliary burners, all of which enhance complete combustion and reduce emissions. Continuous feed operation minimizes energy waste by avoiding repeated preheating cycles. Additionally, CFD simulations optimize chamber sizes and airflow patterns to eliminate cold spots and ensure thorough oxidation, ultimately lowering the environmental impact." 7 Incinerators with APC integrate 1. System Overview Basic Process Flow: Macrotec’s Incinerators with APC integrate a multi-stage waste destruction and emissions control process. The system comprises three primary sections: 1. Incineration Chamber: ○ Two-Chamber Combustion: Waste is continuously fed into a primary chamber (with under-fire and over-fire air) where complete combustion is initiated. The secondary chamber (with a designed two-second retention time) serves to promote thorough oxidation and particulate settling. 2. Flue Gas Cooling and Scrubbing: ○ Flue Gas Cooling: A shell and tube heat exchanger cools the hot exhaust gases, protecting downstream equipment and enhancing scrubbing efficiency. An optional second heat exchanger may preheat the combustion air using waste heat, increasing fuel efficiency. ○ Air Pollution Control (APC): The cooled flue gas then passes through a series of abatement steps that typically include dry gas scrubbing (which neutralizes acid gases and adsorbs heavy metals) and ceramic or bag filtration (to remove particulate matter down to below 3 mg/m³, including PM2.5). 3. Exhaust and Emissions Monitoring: ○ Induced Draught (ID) Fan and Main Stack: An ID fan (controlled by a variable frequency drive) creates a negative pressure to draw the cleaned gas through the system and eject it via a tall main stack. Critical instruments such as flow and flue gas analysers (including continuous emission monitoring systems—CEMS) are housed within the stack to ensure compliance with South African and EU standards. This continuous feed operation minimizes thermal cycling (no repeated pre-heating), which improves fuel efficiency and results in stable flue gas flow for consistent scrubbing and low emissions. 8 2. Component Details Each component is designed for efficiency, safety, and minimal maintenance: A. Incineration Section 1. Incinerator Chambers: ○ Primary Combustion Chamber: Exact Component: Fixed or moving grate incinerator (e.g., MacroBurn V500 for APC systems). Function: Waste is continuously loaded (via an auto feeder or manual feeder) and spread over a large hearth lined with high-temperature alumina-silicate refractory (cold crushing strength ~80 MPa, service temperature up to 1,500°C) to promote even combustion. ○ Secondary Chamber (Settling Chamber): Exact Component: Secondary chamber designed for a two-second retention time. Function: Allows for particulate settling and completes the oxidation of combustible gases. 2. Feeding Systems: ○ Auto Feeder: Exact Name: Macrotec AutoFeeder (with optional bin tipper). Function: Automates waste feeding to prevent overfeeding and improves operator safety by minimizing exposure to high temperatures. ○ Liquid Feeder (Optional): Exact Component: Custom-designed liquid feeders tailored to waste specifications (e.g., based on viscosity and calorific value). Function: Delivers liquid waste at controlled flow rates. 3. Stationary Hearth / Moving Grate: ○ Exact Options: Stationary hearth or reciprocating (moving) grate systems. ○ Function: Displaces waste for continuous combustion; reciprocating grates can improve mixing and stoking, enhancing combustion efficiency. B. Thermal Protection and Heat Management 1. Refractory Lining: ○ Exact Material: High-temperature alumina-silicate castable refractory. ○ Function: Withstands extreme temperatures, resists acid attack and abrasion, and prolongs incinerator life. 9 2. Insulation: ○ Exact Material: 100 mm low-density insulation achieving an R-value of ~1.54 m²K/W. ○ Function: Minimizes heat loss, reduces fuel consumption, and maintains a safe exterior temperature. 3. Heat Exchangers: ○ Shell and Tube Heat Exchanger: Exact Component: A shell and tube design that uses water (or thermal oil) as a coolant. Function: Cools down the flue gas, thus protecting subsequent APC components and improving scrubbing efficiency. ○ Pre-heated Combustion Air Exchanger (Optional): Function: Uses recovered waste heat to preheat combustion air, enhancing fuel efficiency and combustion quality. C. Air Pollution Control (APC) and Emissions Management 1. Dry Gas Scrubbing System: ○ Exact Component: Dry gas scrubber system (integrated with a ceramic filtration unit). ○ Function: Introduces a scrubber agent into the flue gas to neutralize acid gases (e.g., HCl) and adsorb heavy metals and dioxins without using water, simplifying operation and reducing secondary water treatment. 2. Ceramic Filtration: ○ Exact Component: Ceramic filter elements rated for temperatures up to 900°C and operating up to 450°C. ○ Function: Filters out particulate matter (including PM2.5) to below 3 mg/m³; the filter “cake” increases reaction time and surface area for enhanced gas scrubbing. 3. ID Fan (Induced Draught Fan): ○ Exact Instrument: Industrial-grade induced draught fan (with variable frequency drive control). ○ Function: Creates negative pressure to draw flue gas through the system and maintain a constant flow and pressure. 4. Main Stack: ○ Exact Component: Tall flue gas chimney (7–15 m standard, with taller options available). ○ Function: Releases cleaned flue gas into the atmosphere at a height ensuring effective dispersion and compliance with environmental regulations. 5. Continuous Emission Monitoring Systems (CEMS): 10 ○ Exact Instrument: Flue gas analysers and flow sensors integrated into the stack. ○ Function: Continuously measure concentrations of pollutants (e.g., CO, NOx, particulate matter) to ensure regulatory compliance. D. Control, Instrumentation, and Networking 1. Programmable Logic Controller (PLC): ○ Exact Options: Siemens S7 series or Allen-Bradley ControlLogix are common choices. ○ Function: Serves as the system “brain” by collecting data from sensors (temperature, pressure, flow, oxygen levels), processing the data via pre-programmed control logic, and sending commands to actuators (e.g., VFDs, feeder controls, burner modulation) in a closed-loop control manner. 2. Human-Machine Interface (HMI): ○ Exact Instrument: Touchscreen HMI integrated with the PLC control panel. ○ Function: Provides real-time process data, alarms, and diagnostics for operators, with user security levels (operators, site engineers) to control access. 3. Networking Equipment: ○ Exact Components: Industrial Ethernet switches (e.g., Cisco Industrial Ethernet or Siemens SCALANCE) and appropriate protocols (Modbus/TCP, Ethernet/IP, PROFINET). ○ Function: Ensures robust communication between sensors, the PLC, and remote monitoring systems for diagnostics and control. 3. PLC Functionality Simple Explanation and Basic Flow: Input Stage: ○ The PLC receives continuous analog and digital signals from sensors (e.g., temperature, pressure, oxygen, flow, emissions). Processing Stage: ○ The PLC runs control algorithms programmed into its memory. These algorithms compare real-time sensor values against predetermined setpoints. For example, if the incineration temperature drops, the PLC can signal an increase in burner output or adjust the combustion air fan speed. Output Stage: 11 ○ Based on the control logic, the PLC sends commands to actuators (such as variable frequency drives controlling fans, valves regulating waste feed, and burner control systems). Feedback Loop: ○ Sensor data is continually fed back into the PLC, which constantly refines its control actions to maintain optimal operating conditions, ensuring safe, efficient combustion and low emissions. Networking and HMI: ○ The PLC communicates over an industrial network with the HMI, allowing operators to monitor performance, access historical data logs, and execute remote diagnostics and adjustments. 4. Interview Preparation Below are sample interview questions along with optimal answers for a technical role related to these systems: Question 1: Q: Can you describe the overall operational flow of Macrotec’s Incinerator with Air Pollution Control? A: "The system operates on a continuous feed basis. Waste is fed into a dual-chamber incinerator where it is combusted on a refractory-lined hearth. Under-fire air improves combustion efficiency, while over-fire air enhances oxidation in the secondary chamber. The resulting hot flue gas is cooled using a shell and tube heat exchanger, then treated via a dry gas scrubber and ceramic filtration system to neutralize acid gases and remove particulates. Finally, an ID fan and tall main stack ensure the clean gas is released under optimal dispersion conditions. Throughout, sensors feed data to a PLC that manages and optimizes system performance in real time." 12 Question 2: Q: What are the key components in the APC system, and how does each contribute to emission reduction? A: "Key components include: Incinerator Chambers: Ensure complete combustion and controlled retention time for settling particulates. Heat Exchangers: Cool the flue gas for downstream protection and scrubbing efficiency. Dry Gas Scrubber: Neutralizes acid gases and captures heavy metals using a scrubber agent without water. Ceramic Filters: Remove fine particulates down to below 3 mg/m³. ID Fan and Main Stack: Provide consistent draft and release of clean exhaust. Each part is integrated into a closed-loop system that minimizes emissions and meets regulatory standards." Question 3: Q: How does the PLC integrate into the system, and what role does it play in ensuring safe operation? A: "The PLC is the control hub that receives data from sensors monitoring parameters such as temperature, pressure, and emissions. It processes this data against setpoints and then adjusts outputs like fan speeds, feeder rates, and burner controls to maintain optimal combustion conditions. This closed-loop control not only enhances efficiency but also triggers safety interlocks and alarms if abnormal conditions are detected, ensuring safe operation." Question 4: Q: What advantages does a continuous feed incineration system have over a batch system? A: "Continuous feed systems eliminate the need for repetitive preheating between batches, reducing fuel consumption and operating costs. They provide a stable, consistent flue gas flow, which improves the efficiency of the scrubbing and particulate removal processes, leading to lower emissions and more reliable operation." 13 Question 5: Q: Can you explain how the auto feeder and liquid feeder options improve system safety and performance? A: "An auto feeder automates waste input, reducing the risk of operator error and ensuring consistent loading, which maintains optimal combustion conditions. A liquid feeder, when required, is designed to handle specific waste characteristics (calorific value, viscosity) to control the flow rate precisely. Both systems help in preventing overfeeding and ensure a steady, controlled feed, which improves safety by minimizing direct human interaction with high-temperature zones." Summary This comprehensive overview covers: System Overview: A continuous feed incineration process with dual combustion chambers, flue gas cooling, and advanced APC (scrubbing and filtration). Component Details: Precise instrumentation including refractory chambers, heat exchangers, dry gas scrubbers, ceramic filters, ID fans, main stacks, and robust sensor networks integrated with a PLC and HMI. PLC Functionality: The PLC continuously monitors sensor data, executes control algorithms, and adjusts system components in a closed-loop to maintain optimal operation and safety. Interview Preparation: Sample questions and optimal answers that cover system operation, key component functions, and the role of the PLC in ensuring safety and efficiency. 14 Biomass Fired Incinerators 1. System Overview Macrotec’s Biomass Fired Incinerators are designed to operate using locally available biomass fuels. These fuels are used both to bring the incinerator up to the required operating temperature and as an auxiliary fuel during continuous operation. This design is ideal for remote sites, emergency deployments, mines, or military camps where conventional diesel or gas supplies are unavailable. The basic flow of the system is as follows: 1. Fueling and Heating: ○ Biomass (such as wood chips, agricultural residues, etc.) is introduced to preheat the combustion chamber. ○ This biomass serves as an auxiliary fuel, replacing diesel or gas, which simplifies installation since no separate fuel infrastructure is needed. 2. Continuous Feed Combustion: ○ The incinerator is built with two chambers. Primary Chamber: Waste (or biomass feed) is distributed on a large refractory-lined hearth. Secondary Chamber: Designed with a two‑second retention time, it promotes settling of particulate matter and ensures complete oxidation. ○ Combustion air is supplied via high‑velocity fans to create turbulence and proper mixing of oxygen and flue gases, improving combustion efficiency. 3. Exhaust and Dispersion: ○ After combustion, the hot flue gas exits through a chimney stack (typically 7–15 meters tall, with taller options as required) designed to enhance draft and ensure proper dispersion of emissions. This continuous feed process avoids the energy losses of repeated start–stop cycles and improves both fuel consumption and emission control. 15 2. Component Details Each component is chosen to maximize efficiency, safety, and ease of installation. Below are the key components with their exact names and functions: A. Combustion Chambers and Hearth Dual-Chamber Incinerator (Biomass_ABTF2): ○ Function: Primary Chamber: Houses a large refractory-lined hearth that evenly distributes the waste and biomass fuel for uniform combustion. Secondary Chamber: Provides a controlled two-second retention period that promotes settling of particulate matter and ensures complete combustion. ○ How It Works: The refractory lining (made of high-temperature alumina‑silicate castable refractory with a cold crushing strength of 80 MPa and a service temperature up to 1,500˚C) protects the structure and maintains high operating temperatures. A 100 mm layer of low-density insulation (R-value ~1.54 m²K/W) minimizes heat loss, thereby improving fuel efficiency and operator safety. B. Fuel and Air Supply Biomass Fuel Supply: ○ Function: Utilizes available biomass to preheat the incinerator and sustain combustion as an auxiliary fuel, reducing dependency on diesel or gas. ○ How It Works: Biomass is loaded continuously (using similar feeding systems as other incinerators) so that its inherent calorific value contributes significantly to the incineration process. High-Velocity Combustion Air Fans: ○ Exact Name: Industrial-Grade Combustion Air Fans ○ Function: Deliver combustion air at high speed to the primary chamber through a carefully designed nozzle array. ○ How It Works: 16 The high-velocity air creates turbulence, which ensures thorough mixing of oxygen with the combustion gases. This promotes complete oxidation of the fuel and improves overall combustion efficiency. C. Exhaust and Emissions Management Flue Gas Chimney Stack: ○ Exact Name: Flue Gas Chimney Stack ○ Function: Discharges combustion gases after treatment and ensures effective dispersion of emissions. ○ How It Works: With a standard height between 7 and 15 meters (adjustable based on site conditions using EPA’s H + 1.5L guideline), the stack increases the draft, which boosts the velocity of the exiting gases for better dispersion. D. Monitoring and Instrumentation (for Control and Safety) Temperature Sensors, Pressure Sensors, and Oxygen Sensors: ○ Function: Continuously monitor critical process parameters (chamber temperature, pressure, and oxygen levels) to ensure proper combustion and safe operation. ○ How They Work: These sensors feed real-time data to the control system (PLC), enabling automatic adjustments. PLC (Programmable Logic Controller) with HMI: ○ Exact Options: Often systems like Siemens S7 or Allen-Bradley ControlLogix are used. ○ Function: Acts as the control “brain” of the incinerator, processing sensor data, executing control algorithms, and adjusting actuators. ○ How It Works: The PLC receives inputs from sensors and, based on pre-set operating parameters, controls outputs such as fan speeds, feeder operation, and burner modulation. 17 3. PLC Functionality The PLC is critical for ensuring that the incinerator runs safely and efficiently. Its basic flow of operation is: 1. Input Collection: ○ The PLC collects real-time data from various sensors (e.g., temperature, pressure, and oxygen sensors) installed throughout the combustion chamber and exhaust system. 2. Processing and Control Logic: ○ The PLC uses pre-programmed control logic to compare incoming sensor data against established setpoints. ○ For example, if the temperature is lower than desired, the PLC may signal an increase in biomass feed rate or adjust the combustion air fan speed. 3. Output Actuation: ○ Based on the processing, the PLC sends commands to various actuators: Fan Speed Controllers (VFDs): Adjust the speed of combustion air fans. Feeder and Burner Controls: Regulate biomass feed and burner output. Alarms and Safety Interlocks: Activate if any parameter exceeds safe operating limits. 4. Feedback Loop and HMI Integration: ○ The PLC operates in a closed-loop, meaning it continuously receives updated sensor data and makes adjustments to maintain optimal operation. ○ The system’s HMI displays real-time information, historical logs, and diagnostic messages for operators, and supports remote monitoring via industrial networking protocols. 18 4. Interview Preparation Here are potential interview questions along with sample optimal answers: Question 1: Q: Can you describe the overall operational flow of a Biomass Fired Incinerator? A: "The Biomass Fired Incinerator is a continuous process system that uses locally available biomass as the primary fuel to preheat and maintain combustion. Waste is continuously fed into a dual‑chamber incinerator where the primary chamber, lined with high‑temperature refractory and insulated for efficiency, ignites the fuel. High‑velocity air fans deliver combustion air, ensuring complete mixing and oxidation. The hot flue gases exit via a tall chimney stack designed for optimal dispersion, which enhances combustion efficiency and minimizes emissions." Question 2: Q: What are the critical components in the Biomass Fired Incinerator, and what is their function? A: "Key components include: Dual-Chamber Incinerator (Biomass_ABTF2): Comprises a primary combustion chamber with a large refractory-lined hearth and a secondary chamber with a two‑second retention time, ensuring even combustion and particulate settling. High-Velocity Combustion Air Fans: Deliver air at high speeds for effective mixing and combustion. High‑Temperature Alumina-Silicate Refractory: Protects the incinerator structure and sustains high operating temperatures. Low-Density Insulation (100 mm, R-value 1.54 m²K/W): Reduces heat loss and improves fuel efficiency. Flue Gas Chimney Stack: Discharges cleaned flue gases, enhancing draft and dispersion. Sensors and Monitoring Instruments: Measure temperature, pressure, and oxygen levels to provide data for the PLC. PLC with HMI: Automates control, ensuring the system remains within set parameters." 19 Question 3: Q: How does the PLC in this system ensure safe and efficient operation? A: "The PLC is the central control unit that continuously gathers data from sensors distributed throughout the incinerator. It processes this information using pre-programmed logic to compare sensor readings with optimal setpoints. When deviations occur—such as a drop in temperature or insufficient oxygen—the PLC adjusts the operation of the combustion air fans, feeders, or burners accordingly. This closed-loop control, along with real-time monitoring via an HMI, ensures safe, efficient, and stable operation while also logging data for diagnostic purposes." Question 4: Q: What are the advantages of using biomass as the primary fuel in this incinerator design? A: "Using biomass as the primary fuel is particularly advantageous in remote or emergency scenarios where diesel or gas infrastructure is unavailable. Biomass is often readily available and renewable, reducing operating costs and the environmental footprint. Additionally, because the system is designed to operate continuously with minimal auxiliary fuel, it achieves high thermal efficiency and lower emissions compared to batch processes that require repeated preheating." Question 5: Q: How does the design of the flue gas chimney stack contribute to environmental performance? A: "The flue gas chimney stack is designed to be taller than many competitors’ stacks (ranging from 7 to 15 meters, or higher if needed). This increased height enhances the draft, which raises the velocity of the exiting flue gases. The higher release point ensures that pollutants are dispersed over a wider area, reducing ground-level concentrations and helping the system comply with strict environmental emission standards." 20 Summary System Overview: The Biomass Fired Incinerator uses available biomass to preheat and maintain combustion in a dual‑chamber, continuous feed system. High‑velocity air fans promote efficient combustion, while a tall flue gas stack ensures proper dispersion of emissions. Component Details: Key components include the dual‑chamber incinerator (Biomass_ABTF2) with refractory lining and insulation, high‑velocity combustion air fans, and a flue gas chimney stack. Supporting instrumentation (temperature, pressure, and oxygen sensors) and a robust PLC with HMI enable precise control. PLC Functionality: The PLC collects sensor data, processes it with pre‑programmed control logic, and adjusts actuators (fan speeds, burner settings, feeder operations) in a closed-loop system to maintain optimal performance and safety. Interview Preparation: The sample interview questions and answers address system flow, component functions, the role of the PLC, and the benefits of biomass fuel and design features, providing a solid foundation for technical discussions on this incinerator system. 21 Cremators 1. System Overview MacroBurn Cremators are engineered for the safe, efficient combustion of bodies to produce flue gas, ash, mineral fragments, and heat. They operate as continuous two‑chamber systems that are designed to minimize emissions and fuel usage while ensuring safe, reliable operation. The basic flow is as follows: Loading: The body (often on a bier) is positioned at the loading door of the cremator. This can be done manually or with an auto-loading bier. Combustion: Once loaded, the cremator’s primary chamber initiates combustion using modulating process burners. A large refractory-lined hearth ensures uniform combustion, while the secondary chamber—with a settling function—helps complete oxidation and allows particulate matter to settle. Air Management: A dedicated combustion fan delivers high‑velocity air through multiple nozzles (optimized by CFD analysis) for thorough mixing. Optional features include recirculated combustion air (to lower NOx/CO emissions) and pre-heated combustion air (using a shell‑and‑tube heat exchanger) to boost fuel efficiency. Exhaust: The flue gas, now containing minimal emissions, is vented through a tall flue gas chimney stack designed (7–15 m standard) to enhance draft and dispersion. Filtration (Optional): For additional emissions control, a Macrotec flue gas scrubbing and filtration system may be added. 2. Component Details Each component has been selected and designed to meet rigorous performance, safety, and emissions standards. A. Incineration and Combustion Components Dual‑Chamber Cremator: ○ Exact Name: MacroBurn Cremator (e.g., MacroBurn W150 for systems with filtration) 22 ○ Function: Consists of a primary combustion chamber for initiating combustion and a secondary chamber that allows a controlled retention time to ensure complete oxidation and particulate settling. Refractory Lining: ○ Exact Material: High‑temperature alumina‑silicate castable refractory ○ Function: Protects the structure, endures repeated thermal cycling, and is chemically resistant (to acids and alkalis) for extended durability. Insulation: ○ Exact Specification: Thick layer with an R‑value of 1.54 m²K/W ○ Function: Minimizes heat loss, reduces operating (OPEX) costs, and maintains safe external temperatures. Hearth: ○ Exact Feature: A robust combustion hearth with a liquid containment capacity of approximately 230 L ○ Function: Evenly distributes the body’s mass and contains any combustion liquids. B. Feeding and Access Systems Automated Hydraulic Door: ○ Exact Name: Automated Hydraulic Loading Door ○ Function: Provides safe, reliable opening/closing for loading bodies, reducing manual handling and increasing operational safety. Loading Bier: ○ Exact Options: Manual and Auto Loading Biers ○ Function: Assists staff in transferring the body from the hearse or mortuary into the cremator. The auto option uses hydraulic mechanisms not only to lift but also to push the bier into the chamber. C. Burner and Air Management Components Modulating Process Burners: ○ Exact Name: Fully Modulating Process Burners ○ Function: Provide controlled, adjustable heat with optimal burner placement (validated through CFD simulations) to eliminate cold spots and enhance fuel efficiency. Combustion Fan: ○ Exact Specification: High‑velocity combustion fan with multiple nozzles ○ Function: Supplies combustion air at high speed, ensuring thorough mixing of oxygen with flue gases. Nozzle size, positioning, and velocity are optimized via CFD analysis. 23 Recirculated Combustion Air (Optional): ○ Function: Uses a high‑temperature fan to draw a portion of the flue gas back into the chamber (mixing with fresh air), maintaining combustion air temperatures of around 200–250˚C. This reduces NOx and CO emissions. Pre‑Heated Combustion Air (Optional): ○ Exact Component: Shell and Tube Heat Exchanger ○ Function: Recovers waste heat from the flue gas to preheat the incoming combustion air (to about 250–300˚C), thereby improving fuel efficiency. D. Exhaust and Emissions Control Flue Gas Chimney Stack: ○ Exact Feature: Tall Flue Gas Chimney (standard height 7–15 m; taller stacks available as required) ○ Function: Increases draft and flue gas velocity, ensuring proper dispersion of exhaust gases in compliance with environmental standards (calculated per EPA’s H + 1.5L guideline). Filtration and Scrubbing System (Optional): ○ Exact Name: Macrotec Flue Gas Scrubbing and Filtration System ○ Function: Further minimizes emissions by scrubbing and filtering the flue gas, ensuring very low pollutant levels. 3. PLC Functionality The Programmable Logic Controller (PLC) is the system’s central brain, responsible for monitoring and controlling all key processes: 1. Input Acquisition: ○ Sensors (e.g., thermocouples measuring chamber temperature, oxygen sensors, pressure transducers) continuously send analog and digital signals to the PLC. 2. Processing & Decision-Making: ○ The PLC compares real‑time sensor data with preset parameters (such as temperature setpoints, burner modulation thresholds, and air flow rates). For example, if the combustion temperature drops or if the oxygen level is too low, the PLC adjusts the modulating process burners or the combustion fan speed. 3. Output Control: 24 ○ The PLC sends signals to actuators such as variable frequency drives (VFDs) controlling the combustion fan, hydraulic systems for the automated door, and controls for the modulating burners. 4. Closed‑Loop Feedback: ○ The system operates as a closed loop, meaning sensor data is continually fed back into the PLC, which then fine‑tunes its outputs to maintain optimal combustion, fuel efficiency, and low emissions. 5. User Interface and Networking: ○ A Human‑Machine Interface (HMI) touchscreen provides real‑time status updates, error logs, and diagnostic information. Networking components (industrial Ethernet switches using protocols such as Modbus/TCP or PROFINET) enable remote monitoring and control. 4. Interview Preparation Below are sample interview questions along with optimal answers that cover the MacroBurn Cremators system, its components, and PLC operation. Question 1: Q: Can you describe the overall flow of a MacroBurn Cremator system? A: "The MacroBurn Cremator is a continuous two‑chamber system designed for efficient cremation. Bodies are loaded via an automated hydraulic door and, optionally, an auto loading bier. In the primary chamber, modulating process burners initiate combustion on a refractory-lined hearth, and a secondary chamber ensures complete oxidation and particulate settling. High‑velocity combustion air is provided by a dedicated fan, with options for recirculated or pre‑heated air to improve efficiency and reduce emissions. The flue gas is then vented through a tall chimney stack, and an optional flue gas scrubbing and filtration system can further minimize emissions. All these processes are closely managed by a central PLC." 25 Question 2: Q: What are the key components in MacroBurn Cremators and their functions? A: "Key components include: Dual‑Chamber Cremator: Provides initial and complete combustion. Refractory Lining: Protects against high temperatures and chemical attack. Thick Insulation: Minimizes heat loss (R‑value of 1.54 m²K/W). Automated Hydraulic Door: Ensures safe and efficient loading. Loading Bier: Available in manual or automated forms to assist in body transfer. Modulating Process Burners: Offer precise heat control and fuel efficiency. Combustion Fan: Delivers high‑velocity air through optimized nozzles. Optional Recirculated and Pre‑Heated Air Systems: Enhance combustion and reduce emissions. Flue Gas Chimney Stack: Ensures proper exhaust dispersion. Optional Scrubbing and Filtration System: Provides additional emissions control." Question 3: Q: How does the PLC contribute to the safe and efficient operation of the cremator? A: "The PLC acts as the central control unit by continuously receiving data from various sensors (temperature, oxygen, pressure, etc.). It processes this data in real time using pre‑programmed logic and adjusts key outputs—such as modulating burner settings, fan speeds, and automated door operations—to maintain optimal combustion conditions. This closed‑loop control ensures consistent performance, improved fuel efficiency, and adherence to low emissions targets, while also alerting operators to any faults through an HMI interface." Question 4: Q: What benefits do the recirculated and pre-heated combustion air options offer? A: "Recirculated combustion air helps mix a portion of the hot flue gas back into the chamber, maintaining an optimal temperature range (around 200–250˚C) and reducing NOx and CO emissions. Pre‑heated combustion air, achieved through a shell and tube heat exchanger, raises the temperature of the incoming air to around 250–300˚C. Both options enhance fuel efficiency, improve combustion uniformity, and contribute to lower overall emissions." 26 Question 5: Q: How does CFD analysis support the design of MacroBurn Cremators? A: "Computational Fluid Dynamics (CFD) simulations are used to optimize several critical design factors including chamber dimensions (to minimize cold spots and shortcuts), burner placement (to achieve uniform thermal dispersion), and fan nozzle placement (to ensure thorough mixing of combustion air and flue gases). This analytical approach ensures that the system performs efficiently and consistently while meeting strict emission and safety standards." Summary System Overview: The MacroBurn Cremator operates as a dual‑chamber, continuous system that uses modulating burners, advanced refractory, and optimized air management (with options for recirculation and preheating) to efficiently and cleanly combust bodies. Component Details: Key elements include the refractory‑lined chambers, automated hydraulic door, loading biers, modulating process burners, optimized combustion fan, and a tall flue gas stack. Optional advanced features include recirculated/pre‑heated air and a flue gas scrubbing/filtration system. PLC Functionality: The PLC monitors sensor inputs, processes control algorithms, and adjusts actuators (burners, fans, doors) in a closed‑loop to maintain safe, efficient operation and minimal emissions. Interview Preparation: Sample questions with answers cover system flow, component functions, the role of the PLC, benefits of air management options, and the importance of CFD in design optimization. 27 Hot Gas Filtration system 1. System Overview Macrotec’s Hot Gas Filtration system is designed to meet increasingly strict air emission regulations by removing particulate matter and, when needed, acid gasses and heavy metals from hot flue gas. The basic flow is as follows: Flue Gas Entry: Hot flue gas (often at several hundred degrees Celsius) produced by incinerators, cremators, biomass boilers, or other industrial processes enters the filtration unit. Filtration Process: The gas is drawn into a filter housing that is split into “dirty” and “clean” compartments. Inside, it passes through hollow ceramic filter elements that capture fine particles (including PM2.5 and PM10) on their walls while allowing clean air to pass through. Reverse Pulse Cleaning: To maintain high efficiency (up to 99.99%), the ceramic elements are periodically cleaned by reverse pulse cleaning. Compressed air is injected to dislodge accumulated dust, which is then collected in a dedicated bin. Optional Gas Scrubbing: In applications requiring additional removal of acid gasses (e.g., HCl, SO₂, HF), dioxins, or heavy metals (Pb, Hg), a dry gas scrubber is integrated to adsorb or neutralize these contaminants. Exhaust: Finally, the clean, filtered gas is discharged through the stack in compliance with global emission limits (typically below 5 mg/m³ of particulate matter). This modular design—with robust ceramic elements that withstand high temperatures and harsh chemical environments—ensures both high removal efficiency and low maintenance. 2. Component Details Below are the key components and instruments used in the Hot Gas Filtration system, along with their exact names and functions: 28 A. Ceramic Filter Elements (Glosfume Ceramic Elements) Exact Name: Glosfume Ceramic Filter Elements Function: ○ These hollow, tubular ceramic elements are the core of the filtration system. ○ They allow hot flue gas to pass through while capturing fine particulate matter (down to sub-micron levels) on their porous walls. ○ With an operating temperature capability of up to 1,000°C and a removal efficiency of up to 99.99%, they are the only reliable option for high-temperature applications. ○ They are non-flammable and highly resistant to acids and alkalis, ensuring longevity even in harsh environments. B. Filter Housing Exact Name: Dual-Compartment Filter Housing Function: ○ The housing is divided into a “dirty” side (where the gas enters and contacts the ceramic filters) and a “clean” side (from which filtered air exits). ○ It is typically constructed from carbon steel (standard, for up to 450°C) or 3CR12 steel (for higher temperature applications up to 700°C), ensuring durability and corrosion resistance. C. Reverse Pulse Cleaning System Exact Name: Compressed Air Pulse Cleaning System Function: ○ Periodically, a burst of compressed air is released into the filter housing. ○ This reverse pulse cleans the ceramic filter elements by dislodging the accumulated particulates, which then fall into a collection bin. ○ This automated cleaning maintains a consistent high filtration efficiency without manual intervention. 29 D. Optional Dry Gas Scrubber Exact Name: Dry Gas Scrubbing Unit Function: ○ When the process requires additional removal of acid gases, dioxins, or heavy metals, a dry gas scrubber is integrated downstream of the ceramic filters. ○ It works by injecting a scrubber agent that either adsorbs or neutralizes contaminants such as HCl, SO₂, HF, Pb, and Hg. E. Monitoring Instruments Flue Gas Analyzer / Continuous Emission Monitoring System (CEMS): ○ Exact Name: Flue Gas Analyzer (or full CEMS, as applicable) ○ Function: These instruments continuously monitor key parameters (e.g., particulate concentration, acid gas levels, oxygen, and temperature) in the filtered flue gas. They help verify that emissions remain below regulated limits and alert operators to any filter leakage or performance issues. Dust Measurement Devices: ○ Exact Name: Filter Leakage and Dust Sensors ○ Function: Installed on the clean side of the filter, these sensors detect any particulate breakthrough, ensuring the system’s integrity and compliance with emission standards. 3. PLC Functionality In a Hot Gas Filtration system, a Programmable Logic Controller (PLC) provides the necessary automation and process control: 1. Input Acquisition: ○ The PLC continuously receives signals from various sensors (e.g., temperature sensors, dust detectors, pressure transducers, and flow meters) installed throughout the filtration unit. 2. Data Processing and Control Logic: 30 ○ Using pre-programmed algorithms, the PLC compares real‑time sensor data against preset operating thresholds. ○ For example, if sensor data indicates that particulate buildup is approaching a threshold, the PLC can trigger the reverse pulse cleaning cycle. ○ It also monitors flue gas composition via the flue gas analyzer to ensure emissions are within legal limits. 3. Output Control: ○ Based on the processed data, the PLC sends control signals to actuators such as: Compressed Air Valves: to initiate reverse pulse cleaning. Variable Speed Drives (VSDs): to adjust fan speeds for optimal gas flow. Alarms/Indicators: to alert operators if system performance deviates from the norm. 4. Feedback Loop and HMI Integration: ○ The PLC operates in a closed-loop configuration, continuously updating control actions as conditions change. ○ It interfaces with a Human-Machine Interface (HMI) that provides real‑time monitoring, diagnostic logs, and operator control over the system. ○ Networking via industrial protocols (e.g., Modbus/TCP, Ethernet/IP) enables remote monitoring and data logging. 4. Interview Preparation Below are sample interview questions with optimal answers to help you prepare for discussions on Hot Gas Filtration systems and PLC integration. Question 1: Q: Can you describe the overall operation of the Hot Gas Filtration system? A: "The Hot Gas Filtration system is designed to clean high-temperature flue gas from industrial processes. Hot gas enters the ‘dirty’ side of the filter housing, passes through high‑efficiency ceramic filter elements that capture particulate matter, and emerges as clean air from the ‘clean’ side. The system periodically cleans the filters using a compressed air reverse pulse mechanism, ensuring sustained high efficiency. Optionally, a dry gas scrubber can be integrated to neutralize acid gases and heavy metals, making the system adaptable to various emission requirements." 31 Question 2: Q: What are the key components of the Hot Gas Filtration system, and how does each work? A: "Key components include: Glosfume Ceramic Filter Elements: They are the heart of the system, capturing particulates with a high efficiency of 99.99% even at temperatures up to 1,000°C. Dual-Compartment Filter Housing: It separates the incoming dirty gas from the clean, filtered gas. Compressed Air Pulse Cleaning System: Automatically dislodges accumulated dust from the ceramic filters. Optional Dry Gas Scrubber: Neutralizes acid gases and removes heavy metals. Flue Gas Analyzer / CEMS: Continuously monitors the quality of the filtered gas to ensure compliance with emission standards." Question 3: Q: How does the PLC contribute to the system’s performance and reliability? A: "The PLC is central to the system’s automation. It continuously monitors inputs from sensors (temperature, pressure, particulate levels, etc.) and, based on its programmed logic, adjusts the operation of key components such as the reverse pulse cleaning valves and the combustion fans. This closed-loop control ensures that the filters remain effective, the system operates efficiently, and any deviations are quickly addressed through alarms or corrective actions via the HMI." Question 4: Q: Why are ceramic filter elements preferred over conventional bag filters in hot gas applications? A: "Ceramic filter elements can withstand temperatures up to 1,000°C, whereas conventional bag filters typically fail above 140°C to 180°C. They offer exceptional efficiency (up to 99.99%) in capturing fine particulates (PM2.5), are non-flammable, and are resistant to both acidic and alkaline environments. This makes them ideal for high-temperature processes where reliability and long-term performance are critical." 32 Question 5: Q: What role does the reverse pulse cleaning system play in the overall performance of the filtration unit? A: "The reverse pulse cleaning system is crucial for maintaining high filtration efficiency. As ceramic filter elements accumulate dust over time, their performance can degrade. The system periodically injects compressed air to dislodge these particles, which are then collected in a dedicated bin. This automated cleaning process ensures that the filters continue to operate at optimal efficiency without the need for manual cleaning, thus reducing downtime and maintenance costs." Summary System Overview: The Hot Gas Filtration system draws hot flue gas into a dual‑compartment housing where ceramic filter elements capture particulates. A reverse pulse cleaning system periodically cleans the filters, and optional dry gas scrubbers can further remove acid gases and heavy metals. Component Details: ○ Glosfume Ceramic Filter Elements capture sub-micron particles at high temperatures. ○ Dual-Compartment Filter Housing directs gas flow between dirty and clean sides. ○ Compressed Air Pulse Cleaning System maintains filter performance. ○ Optional Dry Gas Scrubber neutralizes acid gases. ○ Flue Gas Analyzer / CEMS monitors emissions for compliance. PLC Functionality: The PLC monitors sensor data, processes it according to pre-set control logic, and drives actuators to manage reverse cleaning cycles, fan speeds, and alarms—all integrated via an HMI and robust industrial networking. Interview Preparation: The provided questions and answers cover the operation, components, and PLC’s role, offering a solid foundation for discussing the system in a technical interview. 33 Gold Recovery Incinerator 1. System Overview The Carbon Fines Gold Recovery Incinerator is a continuous‐operation thermal process designed to recover gold from carbon fines generated in gold mining operations. Its basic flow is as follows: Feed Stage: Carbon fines are continuously fed into the incinerator. The system’s design maximizes energy efficiency by relying primarily on the oxidation (burning) of the carbon itself to provide the required heat. Combustion Stage: Within a refractory‑lined combustion chamber, high‑efficiency modulating burners ignite the carbon fines. This controlled combustion burns off the carbon and combustibles while leaving behind a concentrated gold ash. The design minimizes residual unburnt carbon and effectively separates most grit and silica from the ash. Filtration Stage: The hot flue gas carrying the gold ash passes through a high‑efficiency filtration unit. Here, the gas is drawn through hollow ceramic filter elements that capture fine particles (including sub-micron particles) on their walls. Periodic reverse pulse cleaning removes the built‑up ash and deposits it into a collection bin for subsequent processing. Exhaust Stage: Cleaned flue gas is discharged through an exhaust stack designed to optimize draft and dispersion while meeting strict environmental emissions limits. This continuous and simplified design (with few moving parts) ensures low operating costs, high gold recovery rates (85–95%), and minimal environmental impact. 2. Component Details Each component is selected to optimize recovery efficiency, fuel economy, and reliability. 34 A. Incineration Unit C100 Carbon Fines Incinerator: ○ Function: The main combustion unit where carbon fines are thermally processed. ○ How it Works: A continuous feed of carbon fines enters a refractory‑lined combustion chamber. Modulating process burners supply precise heat, causing the carbon to oxidize. This thermal process burns off combustibles and liberates the embedded gold, which remains in the ash. Modulating Process Burners: ○ Exact Name: High‑Efficiency Modulating Process Burners ○ Function: Provide controlled heat output to achieve complete combustion with minimal unburnt carbon. ○ How it Works: These burners adjust fuel delivery (via gas or diesel) in real time to maintain optimal temperatures, ensuring efficient oxidation and high fuel efficiency. Refractory Lining: ○ Exact Material: High‑Temperature Alumina‑Silicate Castable Refractory ○ Function: Protects the combustion chamber from extreme heat and chemical attack while ensuring long-term durability. ○ How it Works: Cast directly into the combustion chamber, the refractory material withstands high thermal cycling and minimizes heat loss. B. Air and Combustion Control Combustion Air System: ○ Components: High‑Velocity Combustion Fan: Delivers the necessary oxygen for complete combustion. Optimized Nozzle Array: (Configured via CFD analysis) ensures uniform distribution of air. ○ Function: Supplies fresh air to sustain the combustion process and promote even burning. C. Filtration and Ash Recovery High‑Efficiency Filtration Unit: ○ Exact Name: Ceramic Filter Elements (manufactured by Glosfume) within a dual‑compartment filter housing 35 ○ Function: Captures the gold-containing ash and other particulates from the hot flue gas. ○ How it Works: Ceramic Filter Elements: These hollow, tubular filters operate at very high temperatures (up to 1,000°C) and capture particles as small as PM2.5 with efficiencies up to 99.99%. Dual‑Compartment Housing: The flue gas enters the “dirty” side where particulates adhere to the filter walls; clean gas then passes to the “clean” side and exits the system. Reverse Pulse Cleaning System: A compressed air pulse periodically cleans the ceramic elements, dislodging built‑up ash which is then collected for further processing. D. Exhaust and Emissions Control Flue Gas Chimney Stack: ○ Exact Name: Flue Gas Chimney Stack (standard height: 7–15 m; taller as needed) ○ Function: Safely discharges the cleaned flue gas into the atmosphere with improved dispersion. ○ How it Works: The stack is designed based on engineering guidelines (e.g., EPA’s H + 1.5L rule) to maintain sufficient draft and meet environmental regulations. E. Monitoring and Control Instruments Monitoring Instruments: ○ Temperature Sensors: Monitor combustion chamber temperatures. ○ Pressure Sensors: Ensure proper airflow and system stability. ○ Flue Gas Analyzers / Emission Sensors: Continuously measure particulate levels and gas composition for regulatory compliance. PLC and Control System: ○ Exact Name: Programmable Logic Controller (PLC) integrated with a Human‑Machine Interface (HMI) ○ Function: Automates and controls the entire incineration and filtration process. ○ How it Works: See the next section on PLC Functionality. 36 3. PLC Functionality The PLC serves as the system’s central control unit, ensuring optimal operation and safety. Its operation can be summarized in four steps: 1. Input Acquisition: ○ The PLC continuously collects real‑time data from sensors (temperature, pressure, flow, emission levels) placed in the combustion chamber and filtration unit. 2. Processing and Decision-Making: ○ Using pre‑programmed control logic, the PLC compares sensor data against set thresholds. For example, if the temperature falls below the optimal level, it increases the burner output; if particulate buildup is detected, it triggers a reverse pulse cleaning cycle. 3. Output Control: ○ The PLC sends control signals to actuators such as variable speed drives for the combustion fan, burner control systems, and cleaning system valves. This ensures that the process stays within the desired operating parameters. 4. Feedback and HMI Integration: ○ The system operates as a closed loop, with continuous feedback allowing the PLC to adjust operations in real time. An HMI touchscreen displays process data, alarms, and diagnostic logs, while industrial networking (via protocols like Modbus/TCP) enables remote monitoring and control. 4. Interview Preparation Below are sample interview questions along with optimal answers for discussing the Carbon Fines Gold Recovery Incinerator system: Question 1: Q: Can you describe the overall operation of the Carbon Fines Gold Recovery Incinerator? A: "The incinerator is a continuous process unit designed to recover gold from carbon fines. Carbon fines are continuously fed into a refractory-lined combustion chamber where modulating process burners oxidize the carbon, burning off combustibles and leaving behind gold ash. The hot flue gas passes through a high-efficiency filtration unit with 37 ceramic filter elements that capture the ash. The cleaned gas is then exhausted through a well-designed stack. This process not only achieves high gold recovery rates (85–95%) but also minimizes fuel usage and environmental impact." Question 2: Q: What are the key components of the system, and what does each component do? A: "Key components include: C100 Carbon Fines Incinerator: The primary combustion chamber designed for processing carbon fines. Modulating Process Burners: Provide controlled heat to ensure complete combustion with minimal unburnt carbon. Refractory Lining: Protects the chamber and maintains high thermal efficiency. Combustion Air System: Comprising a high‑velocity fan and nozzle array to supply oxygen uniformly. High‑Efficiency Filtration Unit: Uses Glosfume Ceramic Filter Elements housed in a dual-compartment system to capture gold ash and particulates. Reverse Pulse Cleaning System: Periodically cleans the filters with compressed air. Flue Gas Chimney Stack: Releases the clean exhaust gas while ensuring proper dispersion. Monitoring Instruments: Sensors (temperature, pressure, emission) provide real-time data. PLC and HMI: Automate process control, ensuring optimal combustion and filtration." Question 3: Q: How does the PLC ensure the system operates safely and efficiently? A: "The PLC gathers data from various sensors in the combustion and filtration stages. It processes this information against preset setpoints using programmed logic. For example, if the temperature drops or particulate levels rise, the PLC automatically adjusts burner output or initiates a reverse pulse cleaning cycle. This closed-loop control maintains optimal conditions, ensures high recovery rates, minimizes auxiliary fuel use, and keeps emissions low. The HMI allows operators to monitor the process in real time and intervene if necessary." Question 4: 38 Q: What are the advantages of a continuous thermal process for carbon fines incineration? A: "A continuous process means that most of the energy for combustion is generated by the carbon itself, leading to lower auxiliary fuel consumption and operating costs. It also ensures steady, predictable operating conditions, which simplifies control and improves overall gold recovery efficiency. Continuous operation minimizes downtime and provides a consistent product output, making it ideal for high-volume gold recovery applications." Question 5: Q: Why are ceramic filter elements chosen for the filtration unit, and how do they work? A: "Ceramic filter elements are chosen because they can operate at extremely high temperatures (up to 1,000°C) and offer very high particulate capture efficiency (up to 99.99%). Their porous structure allows hot flue gas to pass through while trapping fine particles, including gold ash. They are non-flammable and resistant to acidic and alkaline conditions. Periodic reverse pulse cleaning keeps them operating efficiently without manual intervention, which is critical for continuous processing." Summary System Overview: The Carbon Fines Gold Recovery Incinerator is a continuous, energy‑efficient system that combusts carbon fines to liberate gold. The process features a refractory‑lined combustion chamber with modulating burners, an optimized combustion air system, and a high‑efficiency filtration unit that uses ceramic filter elements to capture gold ash. Cleaned gas is expelled through an exhaust stack, ensuring low emissions and high recovery rates. Component Details: The system includes the C100 Incinerator, high‑efficiency modulating burners, refractory lining, combustion air system, ceramic filter-based filtration unit with a reverse pulse cleaning mechanism, exhaust stack, and various monitoring instruments—all controlled by an integrated PLC and HMI. PLC Functionality: The PLC collects sensor data, processes it with pre‑programmed logic, and controls actuators (burners, fans, cleaning valves) in a closed-loop manner. It ensures that the system remains within optimal operating conditions and interfaces with operators via an HMI. 39 Interview Preparation: The sample questions cover overall system operation, key component functions, PLC roles, advantages of continuous processing, and the reasons for using ceramic filters—providing a well-rounded foundation for technical interviews on this topic.