OSCM221-PRELIM-modue-1-4 PDF
Document Details
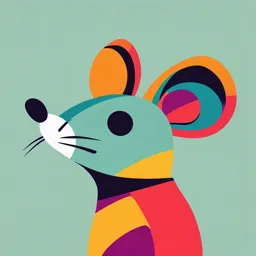
Uploaded by RelaxedSardonyx8144
Tags
Related
- EL CONCEPTO DE CALIDAD HISTORIA EVOLUCIÓN E IMPORTANCIA PARA LA COMPETITIVIDAD PDF
- Quality Improvement in the Modern Business Environment PDF
- Managerial Accounting and the Business Environment PDF
- Historical Background Of Management PDF
- Chapter 9 Empowerment in the Workplace and the Quality Imperative PDF
- Module 5 - Chapter 4 - Quality Concepts PDF
Summary
This document discusses quality in business, including the current business environment, the importance of quality, and various approaches to improvement in organizations. It also touches upon competition in various industries and the concept of quality.
Full Transcript
LESSON 1: Understanding quality QUALITY, COMPETITIVENESS AND C. Adoption of Improvement CUSTOMERS Approaches A. Current Business Environment - Many organizations have Organizations are experiencing responded to t...
LESSON 1: Understanding quality QUALITY, COMPETITIVENESS AND C. Adoption of Improvement CUSTOMERS Approaches A. Current Business Environment - Many organizations have Organizations are experiencing responded to these challenges by significant changes in their adopting various improvement markets and operations. methodologies, such as: Both international and Total Quality Management domestic competition have (TQM) intensified, creating a turbulent Business Process Re- and hostile environment. engineering (BPR) Technological advancements Business Excellence have accelerated rapidly. Performance Excellence Customers have become more Lean Thinking demanding. Six Sigma Competition is increasingly Statistical Process Control intense and sophisticated. (SPC) Regulators and consumer groups add to the pressures - Although the range of quality faced by businesses. initiatives can be overwhelming, they share common principles and elements found in TQM. B. Importance of Quality Quality performance has always been essential for D. Competition Across Sectors business success. All organizations—whether in In the 21st century, quality is banking, healthcare, more important than ever to education, or manufacturing— remain competitive globally. now face competition. Organizations must focus on They compete for customers, quality to succeed in a students, patients, resources, competitive market. and funding. E. Quality as a Competitive Before anyone will buy the idea that Advantage quality is an important consideration, An organization's reputation for they would have to know what was meant quality, reliability, price, and by it. delivery is crucial for sustained competitive advantage. Quality strategies help What is quality? organizations win customers, - Quality starts with understanding secure resources or funding, customer needs and ends when those and remain competitive. needs are satisfied. Focusing on quality improves overall performance, including - ‘Is this a quality watch?’ Pointing to my reliability, delivery, and price. wrist, I ask this question of a class of students – undergraduates, postgraduates, experienced managers – it Reputations for poor quality last for a long matters not who. The answers vary: time and good or bad reputations can ‘No, it’s made in Japan.’ become national or international. Yet the ‘No, it’s cheap.’ management of quality can be learned ‘No, the face is scratched.’ and used to improve reputation. For any ‘How reliable is it?’ organization, there are several aspects of ‘I wouldn’t wear it.’ reputation which are important: 1. It is built upon the competitive A. Concept of Quality elements of being ‘On-Quality; On- “My watch has been insulted all over the Time; On-Cost’. world – London, New York, Paris, Sydney, 2. Once an organization acquires a Dubai, Brussels, Amsterdam, Leeds” poor reputation for product or service quality or reliability, it takes The quality of a watch, or any a very long time to change it. product, depends on the 3. Reputations, good or bad, can requirements of the wearer. quickly become national For some, a watch might be a reputations. piece of jewelry that gives an 4. The management of the impression of wealth. competitive weapons, such as Others may value specific quality, can be learned like any features, such as a digital display, other skill and used to turn round a or water resistance up to 50 poor reputation. meters. These individual needs and “Quality should be aimed at the preferences define what "quality" needs of the consumer, present means. and future” – Deming, another B. Perception of Quality early doyen of quality Quality is often associated with management. excellence, as in phrases like “The total composite product and "Rolls-Royce quality" or "top service characteristics of quality." marketing, engineering, In manufacturing, quality may refer manufacture and maintenance to conformance to specific, through which the product and detailed physical characteristics service in use will meet the or tight specifications. expectation by the customer” – In other settings, like hospitals, Feigenbaum, the first man to quality might represent publish a book with ‘Total Quality’ professionalism. in the title. C. Defining Quality for Management “Conformance to requirements” – Purposes Crosby, an American consultant To manage quality effectively, it is famous in the 1980s. crucial to assess the true ”Degree to which a set of inherent requirements of the customer. characteristics fulfils Quality should meet the needs and requirements” – ISO (EN) expectations of the customer, not 9000:2000 Quality Management just technical specifications or Systems – Fundamentals and perceptions of excellence. Vocabulary. Quality expressed in many ways by other authors: D. Reliability Reliability refers to a product or “Fitness for purpose or use” – service's ability to function Juran, an early doyen of quality satisfactorily over a period of time. management. It is closely related to quality, as “The totality of features and both are crucial factors in characteristics of a product or purchasing decisions. service that bear on its ability to The product or service consistently satisfy stated or implied needs” – meets the customer’s BS 4778. 1987 (ISO 8402, 1986) requirements over time. Quality Vocabulary; Part 1, International Terms. Although quality and reliability are needs develop a reputation for often used interchangeably, they excellence. have distinct meanings. This reputation for excellence E. Connection Between Quality and often leads to customer loyalty, Reliability which is a key factor in the success Many general management issues of an organization. related to product or service quality also apply to achieving reliability. Research shows that focus on customer Reliability ranks equally with loyalty can provide several commercial quality in importance for decision- advantages: making when customers consider Customers cost less to retain than alternatives. acquire. F. Broader Definition of Quality The longer the relationship with Quality is not limited to the the customer, the higher the functional characteristics of a profitability. product or service. A loyal customer will commit more For some products, like antiques, spend to its chosen supplier. certain clothing, or status symbols About half of new customers come (e.g., executive cars, bank through referrals from existing accounts, charge cards), quality is clients (indirectly reducing associated with the satisfaction of acquisition costs). ownership rather than Many companies use measures of functionality. customer loyalty to identify The true requirement of a product customers which are ‘completely or service, including status or satisfied’, would ‘definitely emotional fulfillment, is critical recommend’ and would ‘definitely when assessing its quality. repurchase’. G. Delighting the Customer and Creating Excellence By consistently meeting customer requirements, organizations can elevate customer satisfaction to a higher level, even delighting them. Companies that excel at consistently fulfilling customer UNDERSTANDING AND BUILDING THE doing with those trays?’ ‘We will have QUALITY CHAINS indigestion by the time we’ve landed.’ - The ability to meet the customer The problem was perceived by many on requirements is vital, not only between the aeroplane to be one of delivery or two separate organizations, but within the service. They could smell food but they same organization. weren’t getting any of it, and they were When the air stewardess pulled back the getting really wound up! The air hostess, curtain across the aisle and set off with a who had suffered the embarrassment of trolley full of breakfasts to feed the early being the purveyor of defective product morning travellers on the short domestic and service, was quite wound up and flight into an international airport, she flushed herself, as she returned to the was not thinking of quality problems. curtain and almost ripped it from the Having stopped at the row of seats hooks in her haste to hide. She was heard marked 1ABC, she passed the first tray to say through clenched teeth, ‘What a onto the lap of the man sitting by the bloody mess!’ window. By the time the second tray had A problem of quality? Yes, of course, reached the lady beside him, the first tray requirements not being met, but where? was on its way back to the hostess with a The passengers or customers suffered complaint that the bread roll and jam from it on the aircraft, but in part of were missing. She calmly replaced it in another organization there was a man her trolley and reached for another whose job it was to assemble the – which also had no roll and jam. breakfast trays. On this day the system had broken down – perhaps he ran out of The calm exterior of the girl began to bread rolls, perhaps he was called away evaporate as she discovered two more to refuel the aircraft (it was a small trays without a complete breakfast. Then airport!), perhaps he didn’t know or she found a good one and, thankfully, understand, perhaps he didn’t care. passed it over. This search for complete Three hundred miles away in a chemical breakfast trays continued down the factory... ‘What the hell is Quality aeroplane, causing inevitable delays, so Control doing? We’ve just sent 15,000 much so that several passengers did not litres of lawn weed killer to CIC and there receive their breakfasts until the plane it is back at our gate – they’ve returned it had begun its descent. At the rear of the as out of spec.’ This was followed by an plane could be heard the mutterings of avalanche of verbal abuse, which will not discontent. ‘Aren’t they slow with be repeated here, but poured all over the breakfast this morning?’ ‘What is she shrinking quality control manager as he backed through his office door, followed failure. Not doing it right the first time at by a red faced technical director every stage of the process. advancing menacingly from behind the Why do we accept failure in the bottles of sulphuric acid racked across production of artefacts, the provision of a the adjoining laboratory. service, or even the transfer of ‘Yes, what is QC doing?’ thought the information? In many walks of life we do production manager, who was behind a not accept it. We do not say, ‘Well, the door two offices along the corridor, but nurse is bound to drop the odd baby in a could hear the torrent of language now thousand – it’s just going to happen’. We being used to beat the QC man into an do not accept that! admission of guilt. He knew the poor devil In each department, each office, even couldn’t possibly do anything about the each household, there are a series of rubbish that had been produced except suppliers and customers. The PA is a test it, but why should he volunteer for the supplier to the boss. Are the requirements unpleasant and embarrassing ritual now being met? Does the boss receive error- being experienced by his colleague – for free information set out as it is wanted, the second time this month. No wonder when it is wanted? If so, then we have a the QC manager had been studying the quality PA service. Does the air steward middle pages of the Telegraph on receive from the supplier to the airline the Thursday – what a job! correct food trays in the right quantity, at Do you recognize these two situations? the right time? Do they not happen every day of the week – possibly every minute somewhere in manufacturing or the service industries? Is it any different in banking, insurance, health services? The inquisition of checkers and testers is the last bastion of desperate systems trying in vain to catch mistakes, stop defectives, hold lousy materials, before they reach the external customer – and woe betide the idiot who lets them pass through! Two everyday incidents, but why are events like these so common? The answer is the acceptance of one thing – A. Quality Chains in Organizations customers, whether they are internal or external. This mindset encourages quality Across all types of organizations— at every level. whether manufacturing companies, banks, retail stores, universities, hospitals, or hotels—there exists a series D. Managing Quality of quality chains made up of customers and suppliers. These chains, both Quality doesn’t occur by chance—it must internal and external, can be disrupted at be actively managed and involve every any point if one person or one piece of employee throughout the organization. equipment fails to meet customer Even employees who don’t directly requirements. This failure tends to affect handle the final product or service, such the organization's interface with external as those processing purchase orders or customers, leading to issues that often invoices, are part of the quality chain. For manifest at the customer-facing level, example, if **every fourth invoice** such as with service staff (e.g., air contains an error, the overall image of the hostesses). This forms the core concept organization's quality is tarnished. of Total Quality Management (TQM). E. The Ripple Effect of Failure B. Internal and External Customers Failure to meet requirements in any part Internal customers are just as important of the quality chain **multiplies**, as external ones. The word "customer" causing problems in other areas. These should not only refer to the outsiders who failures build on each other, creating even purchase a product or service but also to more problems. To counteract this, anyone within the organization who quality management requires **constant receives services, parts, or information. evaluation** of requirements and a These internal customers rely on each proactive approach to meeting them. person in the chain to deliver quality results. F. Continuous Improvement The pursuit of meeting requirements at C. Motivation and Quality every stage leads to a philosophy of Employee motivation is often treated as a continuous improvement. The benefits separate issue, but in reality, it is closely of ensuring that quality standards are met tied to quality management. Motivation consistently are vast, including: improves when everyone in the Increased competitiveness organization has clearly defined Higher market share Within organizations, between internal Reduced costs customers and suppliers, the transfer of Improved productivity information regarding requirements is Better delivery performance frequently poor to totally absent. How Elimination of waste many executives really bother to find out what their customers’ – their PA’s or secretary’s Meeting the Requirements – requirements are? Can their If quality is meeting the customer handwriting be read, do they leave clear requirements, then this has wide instructions, does the PA/secretary implications. The requirements may always know where the boss is? Equally, include availability, delivery, reliability, does the PA/secretary establish what the maintainability and cost- effectiveness, boss needs – error-free word processing, among many other features. The first item clear messages, a tidy office? Internal on the list of things to do is find out what supplier-customer relationships are often the requirements are. If we are dealing the most difficult to manage in terms of with customer-supplier relationship establishing the requirements. To achieve crossing two organizations, then the quality throughout an organization, each supplier must establish a ‘marketing’ person in the quality chain must activity or process charged with this task. interrogate every interface as follows: Marketing processes establish the true requirements for the product or service. These must be communicated properly Customers throughout the organization in the form of Who are my immediate specifications. customers? The marketing process must of course What are their true requirements? understand not only the needs of the How do or can I find out what the customer but also the ability of their own requirements are? organization to meet them. If my How can I measure my ability to customer places a requirement on me to meet the requirements? run 1,500 metres in 4 minutes, then I Do I have the necessary capability know I am unable to meet this demand, to meet the requirements? (If not, unless something is done to improve my then what must change to improve running performance. Of course I may the capability?) never be able to achieve this requirement. Do I continually meet the requirements? (If not, then what prevents this from happening, when the capability exists?) Quality of Design - We are all familiar How do I monitor changes in the requirements? with the old story of the tree swing (Figure 1.2), but in how many places in how many organizations is Suppliers this chain of activities taking place? To discuss the quality of – say – a chair it is Who are my immediate suppliers? necessary to describe its purpose. What it What are my true requirements? is to be used for? If it is to be used for How do I communicate my watching TV for 3 hours at a stretch, then requirements? the typical office chair will not meet this How do I, or they, measure their requirement. The difference between the ability to meet the requirements? quality of the TV chair and the office chair Do my suppliers have the is not a function of how it was capability to meet the manufactured, but its design. requirements? Do my suppliers continually meet the requirements? How do I inform them of changes in the requirements? - The measurement of capability is extremely important if the quality chains are to be formed within and without an organization. Each person in the - Quality of design is a measure of how organization must also realize that the well the product or service is designed to supplier’s needs and expectations must achieve the agreed requirements. The be respected if the requirements are to be beautifully presented gourmet meal will fully satisfied. not necessarily please the recipient if he - To understand how quality may be built or she is travelling on the motorway and into a product or service, at any stage, it is has stopped for a quick bite to eat. The necessary to examine the two distinct, most important feature of the design, with but interrelated aspects of quality: regard to achieving quality, is the specification. Specifications must also Quality of design exist at the internal supplier-customer Quality of conformance to design. interfaces if one is to achieve a total quality performance. For example, the substantially changes the operational company lawyer asked to draw up a facilities. contract by the sales manager requires a specification as to its content: Quality of Conformance to Design 1. Is it a sales, processing or consulting type of contract? This is the extent to which the product or 2. Who are the contracting parties? service achieves the quality of design. 3. In which countries are the parties What the customer actually receives located? should conform to the design, and 4. What are the products involved (if operating costs are tied firmly to the level any)? of conformance achieved. Quality cannot 5. What is the volume? be inspected into products or services; 6. What are the financial aspects, the customer satisfaction must be e.g. price escalation? designed into the whole system. The conformance check then makes sure that The financial controller must issue a things go according to plan. specification of the information he or she needs, and when, to ensure that foreign A high level of inspection or checking at exchange fluctuations do not cripple the the end is often indicative of attempts to company’s finances. The business of inspect in quality. This may well result in sitting down and agreeing a specification spiralling costs and decreasing viability. at every interface will clarify the true The area of conformance to design is requirements and capabilities. It is the concerned largely with the quality vital first stage for a successful total- performance of the actual operations. It quality effort. may be salutary for organizations to use There must be a corporate understanding the simple matrix of Figure 1.3 to assess of the organization’s quality position in how much time they spend doing the the market place. It is not sufficient that right things right. A lot of people, often marketing specifies the product or service through no fault of their own, spend a ‘because that is what the customer good proportion of the available time wants’. doing the right things wrong. There are There must be an agreement that the people (and organizations) who spend time doing the wrong things very well, operating departments can achieve that and even those who occupy themselves requirement. Should they be incapable of doing the wrong things wrong, which can doing so, then one of two things must be very confusing! happen: either the organization finds a different position in the market place or specification on that particular day. This is not quality control, it is detection – wasteful detection of bad product before it hits the customer. There is still a belief in some quarters that to achieve quality we must check, test, inspect or measure – the ritual pouring on of quality at the end of the process. This is nonsense, but it is frequently practiced. In the office one Figure 1.3 finds staff checking other people’s How much time is spent doing the right things work because they expect errors, right? validating computer data, checking invoices, word processing etc. There is also quite a lot of looking for things, MANAGING QUALITY chasing why things are late, apologizing to customers for lateness A. The Daily Battle Over Quality and so on. Waste, waste, waste! Every day two men who work in a certain factory scrutinize the results of the examination of the previous day’s production and begin the ritual battle C. Shifting from Detection to over whether the material is suitable Prevention for dispatch to the customer. One is To get away from the natural tendency to called the production manager, the rush into detection mode, it is necessary other the quality control manager. to ask different questions in the first They argue and debate the evidence place. We should not ask whether the job before them, the rights and wrongs of has been done correctly, we should ask the specification, and each tries to first ‘Are we capable of doing the job convince the other of the validity of his correctly?’ This question has wide argument. Sometimes they nearly implications, and this book is devoted start fighting. largely to the various activities necessary to ensure that the answer is yes. B. Detection, Not Quality Control However, we should realize straight away This ritual is associated with trying to that such an answer will only be obtained answer the question, ‘Have we done by means of satisfactory methods, the job correctly?’, correctly being a materials, equipment, skills and flexible word, depending on the interpretation given to the instruction, and a satisfactory output from an earlier process. At every ‘process’. supplier-customer interface then there resides a transformation process (Figure 1.4), and every single task throughout an Quality and Processes organization must be viewed as a process in this way. A. Quality Chains and Processes in Organizations - As we've seen, quality chains extend B. The Voice of the Customer and the throughout an organization's business Process or service processes. A process is the transformation of a set of inputs into voice of the customer- is a outputs that satisfy customer needs fundamental requirement to good and expectations, whether in the form process management. of products, information, or services. voice of the process- provides key Everything we do within an feedback to the supply side of the organization is a process. Each area or process equation: right Suppliers + function involves multiple processes. correct Inputs = correct Outputs + For example, in a finance department, satisfied Customers (SIPOC). there are processes for: Budgeting Accounting Salary and wage management Costing etc. Each process in each department or area can be analysed by an examination of the inputs and outputs. This will determine some of the actions necessary to improve quality. There are also cross- functional processes. Figure 1.4 The output from a process is that which is transferred to somewhere or to someone A process – SIPOC the customer. Clearly to produce an Once we have established that our output that meets the requirements of the process is capable of meeting the customer, it is necessary to define, requirements, we can address the next monitor and control the inputs to the question, ‘Do we continue to do the job process, which in turn may be supplied as correctly?’ which brings a requirement to monitor the process and the controls on well if its mission and objectives are to be it. If we now re-examine the first question, achieved. The area will be dealt with in ‘Have we done the job correctly?’ we can some detail later on in the book. It is see that, if we have been able to answer crucial if the management of quality is to the other two questions with a yes, we be integrated into the strategy for the must have done the job correctly. Any organization. other outcome would be illogical. By The control of quality can only take place asking the questions in the right order, we at the point of operation or production have moved the need to ask the – where the letter is word-processed, ‘inspection’ question and replaced a strategy of detection with one of the sales call made, the patient prevention. This concentrates attention admitted, or the chemical on the front end of any process – the manufactured. The act of inspection is inputs – and changes the emphasis to not quality control. When the answer to making sure the inputs are capable of ‘Have we done the job correctly?’ is meeting the requirements of the process. given indirectly by answering the questions of capability and control, then This is a managerial responsibility and is we have assured quality, and the activity discharged by efficiently organizing the of checking becomes one of quality inputs and its resources and controlling assurance – making sure that the product the processes. or service represents the output from an These ideas apply to every transformation effective system to ensure capability and process; they all must be subject to the control. It is frequently found that same scrutiny of the methods, the organizational barriers between people, skills, equipment and so on to functional or departmental empires has make sure they are correct for the job. A encouraged the development of testing person giving a conference presentation and checking of services or products in a whose audio/ visual equipment will not vacuum, without interaction with other focus correctly, or whose material is not departments. appropriate, will soon discover how Quality control then is essentially the difficult it is to make a presentation that activities and techniques employed to meets the requirements of the audience. achieve and maintain the quality of a In every organization there are some very product, process, or service. It includes a large processes – groups of smaller monitoring activity but is also concerned processes often called core business with finding and eliminating causes of processes. These are activities the quality problems so that the requirements organization must carry out especially of the customer are continually met. Quality assurance is broadly the suitability of the product or service in the prevention of quality problems through eyes of the customer. This may, of course, planned and systematic activities call for the use of market research (including documentation). These will techniques, data gathering and analysis include the establishment of a good of customer complaints. If necessary, quality management system and the quasi-quantitative methods may be assessment of its adequacy, the audit of employed, giving proxy variables that can the operation of the system and the be used to grade the characteristics in review of the system itself. importance, and decide in which areas superiority over competitors exists. It is often useful to compare these findings with internal perceptions. Excellent communication between QUALITY STARTS WITH customers and suppliers is the key to a UNDERSTANDING THE NEEDS total quality performance; it will The marketing processes of an eradicate the ‘demanding nuisance/idiot’ organization must take the lead in view of customers, which even now still establishing the true requirements for the pervades some organizations. Poor product or service. Having determined the communications often occur in the need, the organization should define the supply chains between organizations, market sector and demand, to when neither party realizes how poor they determine such product or service are. Feedback from both customers and features as grade, price, quality, timing, suppliers needs to be improved where etc. For example, a major hotel chain dissatisfied customers and suppliers do thinking of opening a new hotel or not communicate their problems. In such refurbishing an old one will need to cases, non-conformance of purchased consider its location and accessibility products or services is often due to before deciding whether it will be customers’ inability to communicate their predominantly a budget, first- class, requirements clearly. If these ideas are business or family hotel. also used within an organization, then the internal supplier/customer interfaces will The organization will also need to establish customer requirements by operate much more smoothly. reviewing the market needs, particularly All the efforts devoted to finding the in terms of unclear or unstated nature and timing of the demand will be expectations or preconceived ideas held pointless if there are failures in by customers. It is central to identify the communicating the requirements key characteristics that determine the throughout the organization promptly, clearly and accurately. The marketing mechanisms for gathering, analyzing and processes should be capable of responding to information on new producing a formal statement or outline employees, then frustration and conflict of the requirements for each product or will replace communication and co- service. This constitutes a preliminary set operation. of specifications, which can be used as One aspect of the analysis of market the basis for service or product design. demand that extends back into the The information requirements include: organization is the review of market 1. Characteristics of performance readiness of a new product or service. and reliability – these must make Items that require some attention reference to the conditions of use include and any environmental factors that assessment of: 1. The suitability of the distribution may be important. and customer-service processes. 2. Aesthetic characteristics, such 2. Training of personnel in the ‘field’. as style, colour, smell, task, feel, 3. Availability of ‘spare parts’ or etc. support staff. 3. Any obligatory regulations or 4. Evidence that the organization is standards governing the nature of capable of meeting customer the product or service. requirements. The organization must also establish All organizations receive a wide range of systems for feedback of customer information and reaction, and these information from customers through systems should be designed on a invoices, payments, requests for continuous monitoring basis. Any information, complaints, responses to information pertinent to the product or advertisements and promotions, etc. An service should be collected and essential component of a ‘customer collated, interpreted, analyzed and relationship management’ system for the communicated, to improve the response analysis of demand is that this data is to customer experience and channelled quickly into the appropriate expectations. These same principles areas for action and, if necessary, must also be applied inside the response. organization if continuous improvement There are various techniques of research, at every transformation process interface which are outside the scope of this book, is to be achieved. If one function or but have been well documented department in a company has problems elsewhere. It is worth listing some of the recruiting the correct sort of staff, for most common and useful general example, and HR has not established methods that should be considered, both Everyone experiences – almost accepts – externally and internally: problems in working life. This causes people to spend a large part of their time Surveys – questionnaires, etc. on useless activities: Panel or focus group techniques In-depth interviews correcting errors Brainstorming and discussions looking for things, finding out why Role rehearsal and reversal things are late Interrogation of trade associations. checking suspect information rectifying and reworking The number of methods and techniques apologizing to customers for for researching the market is limited only mistakes by imagination and funds. The important poor quality and lateness. point to stress is that the supplier, whether the internal individual or the The list is endless, and it is estimated that external organization, keeps very close to about one-third of our efforts are still the customer. Good research, coupled wasted in this way. In the service sector it with analysis of CRM data, is an essential can be much higher. part of finding out what the requirements Quality, the way we have defined it as are, and breaking out from the obsession meeting the customer requirements, with inward scrutiny that bedevils quality. gives people in different functions of an organization a common language for improvement. It enables all the people, with different abilities and priorities, to QUALITY IN ALL FUNCTIONS communicate readily with one another, in pursuit of a common goal. When business For an organization to be truly effective, and industry were local, the craftsman each component of it must work properly could manage more or less on his own. together. Each part, each activity, each Business is now so complex and employs person in the organization affects and is so many different specialist skills that in turn affected by others. Errors have a everyone has to rely on the activities of way of multiplying, and failure to meet others in doing their jobs. the requirements in one part or area Some of the most exciting applications of creates problems elsewhere, leading to TQM have materialized from groups of yet more errors, yet more problems and people that could see little relevance so on. The benefits of getting it right first when first introduced to its concepts. time everywhere are enormous. Following training, many different parts of organizations can show the usefulness of problems are departmental or the techniques: functional when, in fact, the opposite is true – most problems are inter- Sales staff can monitor and departmental. The commitment of all increase successful sales calls. members of an organization is a Office staff have used TQM requirement of ‘organization-wide methods to prevent errors in word- quality improvement’. Everyone must processing and improve inputting work together at every interface to to computers. achieve improved performance and that customer-service people have can only happen if the top management is monitored and reduced really committed. complaints. distribution has controlled lateness and disruption in deliveries. It is worthy of mention that the first points of contact for some outside customers are the telephone operator, the security people at the gate or the person in reception. Equally the e-business, paperwork and support services associated with the product, such as websites, invoices and sales literature and their handlers, must match the needs of the customer. Clearly TQM cannot be restricted to the ‘production’ or ‘operations’ areas without losing great opportunities to gain maximum benefit. Managements that rely heavily on exhortation of the workforce to ‘do the right job right the first time’, or ‘accept that quality is your responsibility’, will not only fail to achieve quality but may create division and conflict. These calls for improvement infer that faults are caused only by the workforce and that LESSON 2 : Models and frameworks for Total Quality Management In the early 1980s when organizations in the 8. Drive out fear, so that everyone may work West seriously became interested in quality effectively for the company. and its management there were many 9. Break down barriers between departments. attempts to construct lists and frameworks to 10. Eliminate numerical goals, posters and help this process. In the West the famous slogans for the workforce asking for American ‘gurus’ of quality management, such new levels of productivity without providing as W. methods. Edwards Deming, Joseph M. Juran and 11. Eliminate work standards that prescribe Philip B. Crosby started to try to make sense numerical quotas. of the labyrinth of issues involved, including 12. Remove barriers that stand between the the tremendous competitive performance of hourly worker and his right to pride of Japan’s manufacturing industry. Deming and workmaQanship. Juran had contributed to building Japan’s 13. Institute a vigorous programme of education success in the 1950s and 1960s and it was and retraining. appropriate that they should set down their 14. Create a structure in top management that ideas for how organizations could achieve will push every day on the success. above thirteen points. Juran’s ten steps to quality improvement were: Deming had fourteen points to help 1. Build awareness of the need and opportunity management as follows: for improvement. 2. Set goals for improvement. 1. Create constancy of purpose towards 3. Organize to reach the goals (establish a improvement of product and service. quality council, identify problems, 2. Adopt the new philosophy. We can no longer select projects, appoint teams, designate live with commonly accepted facilitators). levels of delays, mistakes, defective 4. Provide training. workmanship. 5. Carry out projects to solve problems. 3. Cease dependence on mass inspection. 6. Report progress. Require, instead statistical 7. Give recognition. evidence that quality is built in. 8. Communicate results 4. End the practice of awarding business on the 9. Keep score. basis of price tag. 10. Maintain momentum by making annual 5. Find problems. It is management’s job to work improvement part of the regular continually on the system. systems and processes of the company. 6. Institute modern methods of training on the job. 7. Institute modern methods of supervision of production workers. The responsibility of foremen must be changed from numbers to quality. Phil Crosby, who spent time as Quality Director of 14. Do it all over again to emphasize that the ITT, had ‘four absolutes:’ quality improvement programme never ends. Definition – conformance to requirements. System – prevention. Performance standard – zero defects. Measurement – price of non-conformance. He also offered management fourteen steps to improvement: 1. Make it clear that management is committed to quality. 2. Form quality improvement teams with representatives from each department. 3. Determine where current and potential quality problems lie. 4. Evaluate the cost of quality and explain its use as a management tool. 5. Raise the quality awareness and personal concern of all employees. 6. Take actions to correct problems identified through previous steps. 7. Establish a committee for the zero defects programme. 8. Train supervisors to actively carry out their part of the quality improvement programme. 9. Hold a ‘zero defects day’ to let all employees realize that there has been a change. 10. Encourage individuals to establish improvement goals for themselves and their groups. 11. Encourage employees to communicate to management the obstacles they face in attaining their improvement goals. 12. Recognize and appreciate those who participate. 13. Establish quality councils to communicate on a regular basis. Our understanding of ‘total quality QUALITY AWARD MODELS management’ developed through the 1980s and in earlier editions of this Starting in Japan with the Deming Prize, author’s books on TQM, a broad companies started to get interested in perspective was given, linking the TQM quality frameworks that could be used approaches to the direction, policies essentially in three ways: and strategies of the business or i. as the basis for awards organization. These ideas were captured ii. as the basis for a form of ‘self-assessment’ in a basic framework – the TQM Model iii. as a descriptive ‘what-needs-to-be-in- (Figure 2.1) which was widely promoted place’ model. in the U.K. through the activities of the UK Department of Trade and Industry The earliest approach to a total quality (DTI) ‘Quality Campaign’ and ‘Managing audit process is that established in the into the 90s’ programmes. These Japanese-based ‘Deming Prize’, which is approaches brought together a number based on a highly demanding and of components of the quality approach, intrusive process. including quality circles (teams), The categories of this award were problem solving and statistical process established in 1950 when the Union of control (tools) and quality systems, such Japanese Scientists and Engineers (JUSE) as BS5750 and later ISO 9000 instituted the prize(s) for ‘contributions to (systems). It was recognized that quality and dependability of product. culture played an enormous role in whether organiza- tions were successful As the Deming Award guidelines say, there is or not with their TQM approaches. Good no easy success at this time of communications, of course, were seen constant change and no organization can to be vital to success but the most expect to build excellent quality important of all was commitment, not management systems just by solving only from the senior management but problems given by others: from everyone in the organization, particularly those operating directly at 1. They need to think on their own, set lofty the customer interface. The goals and drive themselves to challenge customer/supplier or ‘quality chains’ for achieving those goals. For these were the core of this TQM model. organizations that introduce and implement TQM in this manner, the Many companies and organizations in Deming Prize aims to be used as a tool for the public sector found this simple improving and transforming their business framework useful and it helped groups management. of senior managers throughout the world get started with TQM. The key was to integrate the TQM activities, based on the framework, into the business or organization strategy and this has always been a key component of the author’s approach. The Baldrige Performance Excellence These are embodied in a framework of seven Program, as it is now known, aims to: categories which are used to assess organizations: help improve organizational performance 1. Leadership practices, capabilities and results organizational leadership facilitate communication and sharing of public responsibility and citizenship best practices information serve as a working tool for understanding 2. Strategic planning and managing performance and for guiding, strategy development planning and opportunities for learning. The strategy deployment award criteria are built upon a set of inter- related core values and concepts: 3. Customer focus visionary leadership customer and market knowledge customer-driven excellence customer relationships and satisfaction 4. Measurement, analysis and knowledge management measurement and analysis of organizational performance information management 5. Work force focus work systems employee education training and development employee well-being and satisfaction Figure 2. 6. Operations focus product and service processes Baldrige criteria for performance excellence business processes framework support processes organizational and personal learning 7. Results valuing employees and partners customer focused results agility financial and market results focus on the future human resource results managing for innovation organizational effectiveness results. management by fact public responsibility and citizenship focus on results and creating value systems developments. Figure 2.3 Figure 2.4 The simple model for improved performance The EFQM Excellence Model holistic business models, rather than just quality models and mutated into frameworks for (Business) Excellence. The NIST and EFQM have worked together well over recent years to learn from each other’s experience in administering awards and supporting programmes, and from organizations which have used their frameworks ‘in anger’. The EFQM publications on the Excellence Model capture much of this learning and provide a framework which organizations can use to follow ten steps: Figure 2.5 1. set direction through leadership 2. establish the results they want to achieve 3. establish and drive the strategy The framework for total quality management 4. set up and manage appropriately their approach to processes, Planning – the development and deployment people, partnerships and resources of policies and strategies; setting up appropriate partnerships and resources; and 5. deploy the approaches to ensure achievement of designing in quality. the strategies and Performance – establishing a performance thereby the results measure framework – a ‘balance scorecard’ for 6. assess the ‘business’ performance, in terms of the organization; carrying out self-assessment, customers, their own audits, reviews and benchmarking. people and society results Processes – understanding, management, 7. assess the achievements of key performance results design and redesign; quality management 8. review performance for strengths and areas for systems; continuous improvement. improvement People – managing the human resources; 9. innovate to deliver performance improvements culture change; teamwork; communications; innovation and learning. 10. learn more about the effects of the enablers on the results. LESSON 3 : Continuous improvement – the basics APPROACHES, METHODOLOGIES AND TOOLS Continuous improvement is a term in common use throughout most industries and the public sector. It can become a meaningless term unless it is linked to organizational strategy, has a defined structure, a chosen approach, a methodology and an associated tool kit. Figure 13.1 provides a generic eight-stage structure that may be applied to most organizations. It begins unsurprisingly with leadership and the top-down cascade of objectives, particularly those related to achieving on-quality, on-time, on- cost delivery of products and services, chosen to boost customer confidence and drive Figure 13.1 efficiency improvements. Unfortunately at this point An overall approach structure for continuous improvement the senior management in many organizations rush or even Lean Sigma. To go with the overall approach a closed loop fact based improve- ment straight to the ‘instruction manual’ to implement methodology is needed. This can be provided by the traditional Six Sigma method of DMAIC stages – approaches such as ‘Lean’ and ‘Six Sigma’ without 1. Define establishing the much needed managerial 2. Measure 3. Analyse infrastructure of stage 2. Good programme and 4. Improve and Control (see later section in this chapter). systems management will be essential, as will The fourth stage of the structure outlined in Figure 13.1 is skilled improvers – people, trained, qualified and ‘living in the organization’, as opposed to being part of a separate improvement communications with people inside and outside on task force of some kind. We are not all naturally born with the ability to make improvements in a structured and effective way and, as we need to be trained and what the chosen approach and even ‘brand’ means. developed to be engineers, chemists, dentists or lawyers, we need to be trained and developed to be improvers, whether we are engineers, chemists, dentists or lawyers. The third stage requires careful choice of a pragmatic, The best people to work on improving an engineering design process are the engineers fact-based improvement methodology which, who work in the process, who have been trained and developed how to make those improvements effectively, rather than an ‘outside team’ who are not fully conversant with hopefully, will yield rapid results using proven how the process operates. That is not to say there is no place for an ‘external task force’, to tackle certain situations, but the norm should be that we expect the ‘experts’ who methodologies, supported by fact and data-based, function in the process every day to make the changes required. hands-on tools and techniques to be recommended. If this choice is based on the need to improve on- quality, on-time and on-cost delivery (Figure 13.2 ) then approaches that reduce the wastage of time and reduce variation to improve quality will be appropriate. Moreover, as these approaches also reduce costs, then overt cost-reduction programmes can be avoided since these often merely knock out capability and render the organization incapable of functioning properly – the equivalent of going to the doctor for help in reducing body weight only for him to chop off your left arm! Lean approaches are designed Figure 13.2 CI approach to delivering OQ OT OC to eliminate non-value added time and Six Sigma approaches are designed to reduce variation, so a combination of the two can provide an excellent ready-made solution for the CI approach – the so- called Lean Six Sigma The development of a widely shared continual T HE ‘DRIVER’ FRAMEWORK FOR CONTINUOUS improvement culture, with shared commitment to IMPROVEMENT constant improvements in performance is the fifth stage in Figure 13.1. The author and his colleagues have developed a The leadership plays a key role here, of course, fully closed loop improvement methodology establishing the ‘norms’ by asking for each and every which brings together the best of Lean, Six Sigma improvement project to be properly defined and and Cost of Quality approaches – DRIVER with tackled using the chosen methodology, by properly the stages of Define, Review, Investigate, Verify, trained improvers and specific expected outcomes Execute and Reinforce. This well-established approach, which has been used in literally people soon change their behaviour when they hundreds of organizations, prevents people get clear messages about what the top people jumping from the problem to the want and expect. solution without considering the improvement The sixth stage of circulation of talent refers to options: situations where you do have specifically trained improvement task forces, such as the Black Belts DEFINE – the scope and goals of the process to trained in GE, and it is necessary to ensure they do be improved, in terms of the customer not see their role as a dead-end job. requirements and the processes that deliver them Jack Welsh famously made the GE Six Sigma REVIEW – understand the ‘as-is’ processes and programme successful by insisting that the HR measure the current process performance to policies not only supported these trained and appreciate the ‘value add’ and ‘waste’ experienced improvers returning to line INVESTIGATE – analyse the gap between the management, but stipulated that managers current and desired performance, prioritize would not get promoted unless they had served problems and identify root causes time as a Black Belt in GE. VERIFY – generate the improvement solutions, including the ‘to-be’ processes, to fix the Only now are we ready to move to the seventh problems and prevent them from recurring stage of making measurable improvements in the EXECUTE – implement the improved processes in production, operations or service areas. Rushing the pathway in a way that ‘holds the gains’ into this without the establishment of the REINFORCE – capitalize on the improvement by previous six stages usually results in ‘learning the lessons’ and establishing a re- disappointment and the claim that SPC is too assessment process for continuous statistical to work here, Six Sigma is Greek for us improvement. or Lean is too ‘mean’ for our organization. Continuous improvement does mean sustained improvements on a lifetime journey. In the short- term world we live in this can be a challenge but do look around and accept that truly great organizations have developed a solid culture of doing the right things right every time. In a rapidly changing world, the only way this can be achieved is by having a culture of continually improving what is done for all customers and other stakeholders. T HE NEED FOR DATA AND SOME BASIC TOOLS AND TECHNIQUES In the never-ending quest for improvement in In addition to the basic elements of a quality the ways processes are operated, numbers management system that provide a framework and information should form the basis for for recording, there exists a set of methods the understanding, decisions and actions; and a Japanese quality guru Ishikawa has called the thorough data gathering, recording and ‘seven basic tools’. These should be used to presentation system is essential: interpret and derive the maximum use from data. The simple methods listed below, of which there are clearly more than seven, will Record data – all processes can and should offer any organization means of collecting, be measured – all measurements presenting and analysing most of its data: should be recorded. Use data – if data are recorded and not used they will be abused. Process mapping or flowcharting – what is Analyse data – data analysis should be done? carried out by means of some basic Check sheets/tally charts – how often is it systematic tools. done? Act on the results – recording and analysis Histograms – what do overall variations look of data without action leads to like? frustration. Scatter diagrams – what are the relationships between factors? Figure 13.4 Define Stratification – how is the data made up? Figure 13.3 DRIVER – the dynamic improvement methodology (together with recommended tools & Pareto analysis – which are the big problems? techniques) Root cause and effect analysis and brainstorming (including CEDAC, NGT, RCA and the five whys) – what causes the problems? Force-field analysis – what will obstruct or help the change or solution? Emphasis curve – which are the most important factors? Control charts – which variations to control and how? Sometimes more sophisticated techniques, The teams must then be provided with such as analysis of variance, regression good leadership and the right tools to analysis and design of experiments, need to tackle the job. be employed. The systematic approach of Figure 13.1 The effective use of the tools requires their should lead to the use of factual application by the people who actually work information, collected and presented by on the processes. Their commitment to this means of proven techniques, to open a will be possible only if they are assured that channel of communications not available management cares about improving quality. to the many organizations that do not Managers must show they are serious by follow this or a similar structured approach establishing a systematic approach and to problem solving and improvement. providing the training and implementation Continuous improvements in the quality support required. of products, services and processes can Improvements cannot be achieved without often be obtained without major capital specific opportunities, commonly called investment, if an organization marshals problems, being identified or recognized. A its resources, through an understanding focus on improvement opportu- nities leads to and breakdown of its processes in this the creation of teams whose membership is way. determined by their work on and detailed knowledge of the process, and their ability to By using reliable methods, creating a take improvement favourable environment for team-based problem solving and continuing to improve using systematic techniques, the never- ending improvement helix (see Chapter 3) will be engaged. This approach demands the real time management of data, and actions focussed on processes and inputs rather than outputs. It will require a change in the language of many organizations from percentage defects, percentage ‘prime’ product and number of errors, to process capability. The climate must change from the traditional approach of ‘If it meets the specification, there are no problems and no further improvements are necessary’. Figure 13.5 Review action. Figure 13.6 Investigate It originated in Japan in 1972 at Mitsubishi’s Kobe shipyard, but it has been developed in numerous ways by Toyota and its suppliers, and many other organizations. The house of quality (HoQ) concept, initially referred to as quality tables, has been used successfully by manufacturers of integrated circuits, synthetic rubber, construction equipment, engines, home appliances, clothing and electronics, mostly Japanese. Ford and General Motors use it, and other organizations, including AT&T, Bell Laboratories, The driving force for this will be the need for better Digital Equipment, Hewlett- Packard, internal and external customer satisfaction levels, Procter & Gamble, ITT, Rank Xerox and which will lead to the continuous improvement Jaguar have applications. In Japan, its question, ‘Could we do the job better?’ design applications include public services and retail outlets. In the construction sector the application of LESSON 4 : Quality Function Deployment QFD is limited to companies that have specialized in a specific market sector; (House of Quality) for example, in Japan and Brazil it has been used to design apartment layouts, and it has application for areas of mass QUALITY FUNCTION DEPLOYMENT (QFD) THE production of products and materials. HOUSE OF QUALITY Quality function deployment (QFD) is a ‘system’ for designing a product or service, based on customer The ‘house of quality’ is the framework of requirements, with the participation of an approach to design management known members of all functions of the supplier as quality function deployment (QFD). organization. It translates the Dr Yoji Akao originally developed QFD in customer’s requirements into the Japan in 1966, combining his work on appropriate technical requirements for quality assurance and quality control with each stage. function deployment as used in value engineering. Data Collection and Review of Customer These are performed by people with different Expectations, Needs, Requirements, and skills in a team whose Specifications composition depends on many factors, including the products or services being 1. First, survey both the expressed and latent quality developed and the size of the operation. In demands of con- sumers in your target marketplace. many industries, such as cars, electronic Then decide what kinds of “things” equipment and computers, ‘engineering’ to make. designers are seen to be heavily into ‘designing’. But in other industries and 2. Study the other important characteristics of your service operations designing is carried out target market and make a demanded quality function bypeople who do not carry the word deployment chart that reflects both the demands and ‘designer’ in their job title. characteristics of that market. The failure torecognize the design inputs they make, and to provide appropriate 3. Conduct an analysis of competing products on the training and support, will limit the success of market, which we call a competitive analysis. the design activities and result in some Develop a quality plan and deter- mine the selling offering that does not necessarily satisfy the features (sales points). customer. This is particularly true of services generally. 4. Determine the degree of importance of each demanded quality. The QFD team in operation 5. List the quality elements and make a quality elements deployment chart. The first step of a QFD exercise is to form a cross-functional QFD team. Its purpose 6. Make a quality chart by combining the demanded is to take the needs of the market and translate them into such a form that they quality deploy- ment chart and the quality elements can be satisfied within the operating unit deployment chart. and delivered to the customers. As with all organizational problems, the 7. Conduct an analysis of competing products to see structure of the QFD team must be how other com- panies perform in relation to each of decided on the basis of the detailed these quality elements. requirements of each organization. One thing, however, is clear – close liaison 8. Analyze customer complaints. must be maintained at all times between the design, marketing and operational 9. Determine the most important quality elements as functions represented in the team. indicated by customer quality demands and complaints. The QFD team must answer three questions – 10. Determine the specific design quality by studying WHO, WHAT and HOW, i.e. the quality characteristics and converting them into 1. WHO are the customers? quality elements. 2. WHAT does the customer need? 3. HOW will the needs be satisfied? 11. Determine the quality assurance method and the test methods. WHO may be decided by asking ‘Who will The HoQ provides an organization with the benefit from the successful introduction of this means for inter-departmental or inter- functional product, service or process? Once the planning and communications, starting with the customers have been identified, so-called customer attributes (CAs). These are WHAT can be ascertained through phrases customers use to describe product, interview/questionnaire/focus group processes, process and service characteristics. or from the knowledge and judgement of the A complete QFD project will lead to the QFD team members. HOW is more difficult to construction of a sequence of house of quality determine, and will depend on the attributes of diagrams, which translate the customer the product, service or process under requirements into specific operational process development. This will constitute many of the steps. For example, the ‘feel’ that customers like action steps in a ‘QFD strategic plan’. on the steering wheel of a motor car may WHO, WHAT and HOW are entered into a QFD translate into a specification for 45 standard matrix or grid of ‘house of quality’ (HoQ), which degrees of synthetic polymer hardness, which in is a simple ‘quality table’. The WHATs are turn translates into specific manufacturing recorded in rows and the HOWs are placed in process steps, including the use of certain the columns. catalysts, temperatures, processes and additives. Similarly in construction, the acoustic The house of quality provides structure to the privacy that home-owners demand is translated design and development cycle, often likened to into a measurable decibel transfer rate and the construction of a house, because of the specific construction systems to achieve it. The shape of matrices when they are fitted together. first steps in QFD lead to a consideration of the The key to building the house is the focus on the product as a whole and subsequent steps to customer requirements, so that the design and consideration of the individual components. For development processes are driven by what the example, a complete hotel service would be customer needs as well as innovations in considered at the first level, but subsequent QFD technology. This ensures that more effort is exercises would tackle the restaurant, bedrooms used to obtain vital customer information. It and reception. Each of the sub-services would may increase the initial planning time in a have customer requirements, but they all would particular development project, but the overall need to be compatible with the general service time, including design and redesign, taken to concept. bringing a product or service to the market will be reduced. This requires that marketing people, design staff (including architects, engineers, physicists, chemists, etc), and production/operations personnel work closely together from the time the new service, process or product is conceived. It will need to replace in many organizations the ‘throwing it over the wall’ approach, where a solid wall exists between each pair of functions Figure 6.3 ‘Throw it over the wall.’ The design and development process is sequential and walled into separate functions The QFD or house of quality tables Figure 6.4 shows the essential components of the quality table or HoQ diagram. The construction begins with the customer requirements, which are determined through the ‘voice of the customer’ – the marketing and market research activities. These are entered into the blocks to the left of the central relationship matrix. Understanding and prioritizing the customer requirements by the QFD team may require the use of competitive and complaint analysis, focus groups, and the analysis of market potential. The prime or broad requirements should lead to the detailed WHATs. Once the customer requirements have been determined and entered into the table, the importance of each is rated and rankings are added. The use of the ‘emphasis technique’ or paired comparison may be helpful here (see Chapter 13). Each customer requirement should then be examined in terms of customer rating; a group of customers may be asked how they perceive the performance of the organization’s product or service versus those of competitors. These results are placed to the right of the central matrix. Hence the customer requirements’ importance rankings and competition ratings appear from left to right across the house. The WHATs must now be converted into the HOWs. These are called the technical design requirements and appear on the diagram from top to bottom in terms of require- ments, rankings (or costs) and ratings against competition (technical benchmarking, see Chapter 9). These will provide the ‘voice of the process’. The technical design requirements themselves are placed immediately above the central matrix and may also be given a hierarchy of prime and detailed requirements. Immediately below the customer requirements appear the rankings of technical difficulty, development time or costs. These will enable the QFD team to discuss the efficiency of the various technical solutions. Below the technical rankings on the diagram comes the benchmark data, which compares the technical processes of the organization against its competitors. The central relationship matrix is the working core of the house of quality diagram. Here the WHATs are matched with the HOWs, and each customer requirement is systematically assessed against each technical design requirement. The nature of any relationship – strong positive, positive, neutral, negative, strong negative – is shown by symbols in the matrix. The QFD team carries out the relationship estimation, using experience and judgement, the aim being to identify HOW the WHATs may be achieved. All the HOWs listed must be necessary and together sufficient to achieve the WHATs. Blank rows (customer requirement not met) and columns (redundant technical characteristics) should not exist. The roof of the house shows the interactions between the technical design requirements. Each characteristic is matched against the others, and the diagonal format allows the nature of relationships to be displayed. The symbols used are the same as those in the central matrix. The complete QFD process is time-consuming, because each cell in the central and roof matrices must be examined by the whole team. The team must examine the matrix to determine which technical requirement will need design attention, and the costs of that attention will be given in the bottom row. If certain technical costs become a major issue, the priorities may then be changed. It will be clear from the central matrix if there is more than one way to achieve a particular customer requirement, and the roof matrix will show if the technical requirements to achieve one customer requirement will have a negative effect on another technical issue. The very bottom of the house of quality diagram shows the target values of the technical characteristics, which are expressed in physical terms. They can only be decided by the team after discussion of the complete house contents. While these targets are the physical output of the QFD exercise, the whole process of information gathering, structuring and ranking generates a tremendous improvement in the team’s cross-functional understanding of the product/service design delivery system. The target technical characteristics may be used to generate the next level house of quality diagram, where they become the WHATs, and the QFD process determines the further details of HOW they are to be achieved. In this way the process ‘deploys’ the customer requirements all the way to the final operational stages. Figure 6.5 shows how the target technical characteristics, at each level, become the input to the next level matrix. QFD progresses now through the use of the ‘seven new planning tools’ and other standard techniques such as value analysis, experimental design, statistical process control and so on. SPECIFICATIONS AND STANDARDS There is a strong relationship between These ideas are well illustrated by the standardization and specification. To construction sector’s approach worldwide to the adoption of performance-based specifications ensure that a product or a service is wherever possible. Performance- based standards standardized and may be repeated a encourage innovation against measurable and large number of times in exactly the transparent technical requirements. This allows manner required, specifications must be the opportunity for manufacturers with new written so that they are open to only one products and innovative solutions to have their interpretation. The requirements, and ideas accredited and gain market entry. In areas therefore the quality, must be built into like waterproofing, however, a building contractor the design specification. There are might prefer to be very prescriptive in specifying the precise technical solution he wants. This is a national and international standards particularly important area of construction where, which, used, help to ensure that based on everyday experience, we know that the specifications will meet certain accepted risk of failure is high and its consequences of criteria of technical or managerial water leaking through the roof or out of a performance, safety, etc. bathroom into adjoining rooms is simply unacceptable. In such areas, correct design and implementation is critical to managing an important area of risk for the general contractor It is possible to strike a balance between innovation and standardization; however, a sound approach to innovation clearly recognizes areas of design innovation that add value for the customer and areas of standardization that reduce risk in the production process. Clearly, it is desirable for designers to adhere where possible to past- proven materials and methods, in the interests of reliability, maintainability and variety control. Hindering designers from using recent developed materials, components or techniques, however, can cause the design process to stagnate technologically. A balance must be achieved by analysis of materials, products and processes Standardization does not guarantee that proposed in the design, against the background of the best design or specification is selected. their known reproducibility and reliability. If It may be argued that the whole process of breakthrough innovations are proposed, then standardization slows down the rate and analysis or testing should be indicated objectively, direction of technological development, justifying their adoption in preference to the and affects what is produced. If standards established alternatives. are used correctly, however, the process of drawing up specifications should provide opportunities to learn more about particular innovations and to change the standards accordingly. It is useful to define a specification. The To fulfil the purpose specifications must be International Standards Organization written in terminology that is readily (ISO) defines it in ISO 8402 (1986) as understood, and in a manner that is ‘The document that prescribes the unambiguous and so cannot be subject to requirements with which the product or differing interpretation. This is not an easy service has to conform’. A document not task, and one which requires all the giving a detailed statement or expertise and knowledge available. description of the requirements to which the product, service or process must It is in relation to the clear communication comply cannot be regarded as a of process specifications that the use of 3D specification, and this is true of much and virtual reality (VR) technolo