Operations and Supply Chain Management Textbook PDF
Document Details
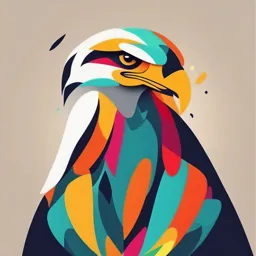
Uploaded by InvaluableTransformation927
2021
David A. Collier, James R. Evans
Tags
Summary
This is a textbook about Operations and Supply Chain Management, focusing on process selection, design, and improvement. It covers different types of processes and provides key insights on operations management, supply chain, and process design.
Full Transcript
Insert textbook image here Operations and Supply Chain...
Insert textbook image here Operations and Supply Chain Management, 2e Chapter 7a: Process Selection, Design, and Improvement ©2021 Cengage Learning. All Rights Reserved. May not be scanned, copied or duplicated, or posted to a publicly accessible website, in whole or in part. 1 Learning Outcomes 1. Be able to identify and define the three process choice decisions as well as the four principle process types (and how they relate to each other); understand as well as differentiate between process design, process mapping, and value stream mapping (Chapter 7a Video). 2. ©2021 Cengage Learning. All Rights Reserved. May not be scanned, copied or duplicated, or posted to a publicly accessible website, in whole or in part. 2 1. Processes Choosing the appropriate processes and designing them to work effectively with each other is the basis of an efficient value chain. Process design is an important operational decision that affects the cost of operations, customer service, and sustainability. Process Choice Decisions Process Design Mistake-Proofing Processes ©2021 Cengage Learning. All Rights Reserved. May not be scanned, copied or duplicated, or posted to a publicly accessible website, in whole or in part. 3 Process Choice Decisions Custom (Make-to-Order): “Generally produced and delivered as one of a kind or in small quantities and are designed to meet specific customer’s specifications” (e.g., custom cabinets: nonstandard sizes/style; any color). Option (Assemble-to-Order): “Configurations of standard parts, sub- assemblies, or services that can be selected by customers from a limited set” (e.g., semi-custom cabinets: standard sizes; color and style options). Standard (Make-to-Stock): “Made according to a fixed design and the customer has no options from which to choose” (e.g., pre-made cabinets). ©2021 Cengage Learning. All Rights Reserved. May not be scanned, copied or duplicated, or posted to a publicly accessible website, in whole or in part. 4 Principle Process Type (1): Projects Projects: “Large-scale, customized initiatives that consist of many smaller tasks and activities that must be coordinated and completed to finish on time and within budget.” Projects are generally used for custom goods and services and even occasionally for semi-custom products such as “market homes” that are built from a standard design. ©2021 Cengage Learning. All Rights Reserved. May not be scanned, copied or duplicated, or posted to a publicly accessible website, in whole or in part. 5 Principle Process Type (2): Job Shop Job Shop: “Organized around particular types of general-purpose equipment that are flexible and capable of customizing work for individual customers.” Job shops produce a wide variety of goods and services, often in small quantities. Thus, they are often used for custom or option type products. Customer orders are generally processed in batches. Orders may require a different sequence of processing steps and movements to work areas. ©2021 Cengage Learning. All Rights Reserved. May not be scanned, copied or duplicated, or posted to a publicly accessible website, in whole or in part. 6 Principle Process Type (3): Flow Shop Flow Shop: “Organized around a fixed sequence of activities and process steps to produce a limited variety of similar goods or services.” An assembly line is a common example of a flow shop process. Many large-volume, option-oriented and standard goods and services are produced in flow shop settings. Often use highly productive, specialized equipment and computer software. ©2021 Cengage Learning. All Rights Reserved. May not be scanned, copied or duplicated, or posted to a publicly accessible website, in whole or in part. 7 Principle Process Type (4): Continuous Flow Continuous Flow: “Create highly standardized goods or services, usually around the clock in very high volumes.” The sequence of work tasks is very rigid and processes use highly specialized, automated equipment that is frequently controlled by computers with minimal human oversight. ©2021 Cengage Learning. All Rights Reserved. May not be scanned, copied or duplicated, or posted to a publicly accessible website, in whole or in part. 8 Process Design Goal: To create the right combination of equipment, labor, software, work methods, and environment to produce and deliver goods and services that satisfy both internal and external customer requirements. Can have a significant impact on cost, flexibility, and quality of the output. We can think about work at four hierarchical levels: 1. Task 2. Activity 3. Process 4. Value Chain ©2021 Cengage Learning. All Rights Reserved. May not be scanned, copied or duplicated, or posted to a publicly accessible website, in whole or in part. 9 Process Design Goal: To create the right combination of equipment, labor, software, work methods, and environment to produce and deliver goods and services that satisfy both internal and external customer requirements. Can have a significant impact on cost, flexibility, and quality of the output. We can think about work at four hierarchical levels: 1. Task: “A specific unit of work required to create an output.” 2. Activity: “A group of tasks needed to create and deliver an output.” ©2021 Cengage Learning. All Rights Reserved. May not be scanned, copied or duplicated, or posted to a publicly accessible website, in whole or in part. 10 Process Design Goal: To create the right combination of equipment, labor, software, work methods, and environment to produce and deliver goods and services that satisfy both internal and external customer requirements. Can have a significant impact on cost, flexibility, and quality of the output. We can think about work at four hierarchical levels: 3. Process: “A sequence of activities that is intended to create a certain result.” 4. Value Chain: “A network of facilities and processes that describe the flow of materials, finished goods, services, information, and financial transactions from suppliers, through the facilities and processes that create goods and services and those that deliver them to the customer.” ©2021 Cengage Learning. All Rights Reserved. May not be scanned, copied or duplicated, or posted to a publicly accessible website, in whole or in part. 11 Process and Value Stream Mapping 1. Define the purpose and objectives of the process. 2. Create a detailed process or value stream map that describes how the process is currently performed (if new; then it is create proposed map). 3. Evaluate alternative process designs. 4. Identify and define appropriate performance measures for the process. 5. Select the appropriate equipment and technology. 6. Develop an implementation plan to introduce the new or revised process design, including performance criteria to monitor and control the process. ©2021 Cengage Learning. All Rights Reserved. May not be scanned, copied or duplicated, or posted to a publicly accessible website, in whole or in part. 12 Process and Value Stream Mapping 1. Define the purpose and objectives of the process. 2. Create a detailed process or value stream map that describes how the process is currently performed (if new; then it is create proposed map). 3. Evaluate alternative process designs. 4. Identify and define appropriate performance measures for the process. 5. Select the appropriate equipment and technology. 6. Develop an implementation plan to introduce the new or revised process design, including performance criteria to monitor and control the process. ©2021 Cengage Learning. All Rights Reserved. May not be scanned, copied or duplicated, or posted to a publicly accessible website, in whole or in part. 13 Process Mapping Process Map: “Describes the sequence of all process tasks and activities necessary to create and deliver a desired outcome.” Documents how work either is, or should be, accomplished and how the transformation process creates value. Process maps also delineate boundaries: Process Boundary: “The beginning or end of a process.” ©2021 Cengage Learning. All Rights Reserved. May not be scanned, copied or duplicated, or posted to a publicly accessible website, in whole or in part. 14. ©2021 Cengage Learning. All Rights Reserved. May not be scanned, copied or duplicated, or posted to a publicly accessible website, in whole or in part. 15 Value Stream Mapping Value Stream: “Refers to all value-added activities involved in designing, producing, and delivering goods and services to the customers.” A value stream map shows the process flows in a manner similar to an ordinary process map; the difference lies in that value stream maps highlight value-added versus nonvalue-added activities and include the costs associated with both value- and nonvalue-added work activities. ©2021 Cengage Learning. All Rights Reserved. May not be scanned, copied or duplicated, or posted to a publicly accessible website, in whole or in part. 16. ©2021 Cengage Learning. All Rights Reserved. May not be scanned, copied or duplicated, or posted to a publicly accessible website, in whole or in part. 17 Mistake-Proofing Processes Humans tend to make mistakes inadvertently. Typical mistakes are setup errors, missing or wrong parts, incorrect adjustments, or omitted steps in a process. Preventing mistakes can be done in three ways: 1. Designing potential defects and errors out of the process; 2. Identifying potential defects and errors and stopping a process before they occur; and 3. Identifying defects and errors soon after they occur and quickly correcting the process. ©2021 Cengage Learning. All Rights Reserved. May not be scanned, copied or duplicated, or posted to a publicly accessible website, in whole or in part. 18 Mistake-Proofing Processes: Poka-Yoke Poka-Yoke: “An approach for mistake-proofing processes using automatic devices or simple methods to avoid human error.” Focuses on two aspects: 1. Prediction, or recognizing that a defect is about to occur and providing a warning; and 2. Detection, or recognizing a defect has occurred and stopping the process. ©2021 Cengage Learning. All Rights Reserved. May not be scanned, copied or duplicated, or posted to a publicly accessible website, in whole or in part. 19 Chapter 7a Summary Choosing the appropriate processes and designing them to work effectively with each other is the basis of an efficient value chain. Process design is an important decision that affects the cost of operations, customer service, and sustainability. The goal of process design is to create the right combination of equipment, labor, software, work methods, and environment to produce and deliver goods and services that satisfy both internal and external customer requirements. Humans tend to make mistakes inadvertently. Typical mistakes are omitted steps in a process, setup errors, missing or wrong parts, or incorrect adjustments. ©2021 Cengage Learning. All Rights Reserved. May not be scanned, copied or duplicated, or posted to a publicly accessible website, in whole or in part. 20 Insert textbook image here Operations and Supply Chain Management, 2e Chapter 7b: Process Selection, Design, and Improvement ©2021 Cengage Learning. All Rights Reserved. May not be scanned, copied or duplicated, or posted to a publicly accessible website, in whole or in part. 21 Learning Outcomes 1. 2. Be able to identify the Product Life Cycle phases as well as interpret both the Product-Process Matrix and the Service-Positioning Matrix (Chapter 7b Video). ©2021 Cengage Learning. All Rights Reserved. May not be scanned, copied or duplicated, or posted to a publicly accessible website, in whole or in part. 22 2. Product and Service Process Matrices Approaches to help understand the relationship between product characteristics for goods/services and process choice decisions: Product-Process Matrix Service-Positioning Matrix ©2021 Cengage Learning. All Rights Reserved. May not be scanned, copied or duplicated, or posted to a publicly accessible website, in whole or in part. 23 Product Life Cycle Product Life Cycle (PLC): “A characterization of product growth, maturity, and decline over time.” It is important to understand the PLCs because when goods and services change and mature, so must the processes and value chains that create/deliver them. ©2021 Cengage Learning. All Rights Reserved. May not be scanned, copied or duplicated, or posted to a publicly accessible website, in whole or in part. 24 Product-Process Matrix Product-Process Matrix: “A model that describes the alignment of process choice with the characteristics of the manufactured good.” The product process matrix merges the product lifecycle, which encompasses all aspects of the product development process - from introduction to growth and/or decline - with the process lifecycle, the progression towards a more cost-effective and productive standardized structure. Essentially, the purpose of this matrix is to serve as a guide for selecting the most appropriate manufacturing process based on product volume and characteristics. ©2021 Cengage Learning. All Rights Reserved. May not be scanned, copied or duplicated, or posted to a publicly accessible website, in whole or in part. 25 Product-Process Matrix: “A model that describes the. alignment of process choice with the characteristics of the manufactured good.” ©2021 Cengage Learning. All Rights Reserved. May not be scanned, copied or duplicated, or posted to a publicly accessible website, in whole or in part. 26 As one moves down the diagonal, the emphasis on both product and process. structure shifts from low volume and high flexibility to higher volumes and more standardization. ©2021 Cengage Learning. All Rights Reserved. May not be scanned, copied or duplicated, or posted to a publicly accessible website, in whole or in part. 27 By selectively positioning a business off the diagonal (i.e., “positioning strategy”), a company can differentiate itself from its competitors…. Therefore, off-diagonal positioning strategies are becoming more viable for many companies and allow for mass-customization strategies and capabilities. ©2021 Cengage Learning. All Rights Reserved. May not be scanned, copied or duplicated, or posted to a publicly accessible website, in whole or in part. 28 Service-Positioning Matrix Service-Positioning Matrix: “A model that describes the relationship between service encounter levels and management service design to meet customers technical and behavioral needs.” Pathway: “A unique route through a service system.” − Customer Routed Services − Provider Routed Services ©2021 Cengage Learning. All Rights Reserved. May not be scanned, copied or duplicated, or posted to a publicly accessible website, in whole or in part. 29 Service- Positioning Matrix: “A model that describes the relationship between service. encounter levels and management service design to meet customers technical and behavioral needs.” ©2021 Cengage Learning. All Rights Reserved. May not be scanned, copied or duplicated, or posted to a publicly accessible website, in whole or in part. 30 The position along the horizontal axis is described by the sequence of service encounters.. The position along the vertical axis of the figure reflects the number of pathways built into the service system design by management. ©2021 Cengage Learning. All Rights Reserved. May not be scanned, copied or duplicated, or posted to a publicly accessible website, in whole or in part. 31 The more unique the service encounter, the less repeatable it is, and vice versa.. ©2021 Cengage Learning. All Rights Reserved. May not be scanned, copied or duplicated, or posted to a publicly accessible website, in whole or in part. 32 The more unique the service encounter, the less repeatable it is, and vice versa. A high degree of. repeatability: ©2021 Cengage Learning. All Rights Reserved. May not be scanned, copied or duplicated, or posted to a publicly accessible website, in whole or in part. 33 The more unique the service encounter, the less repeatable it is, and vice versa. A high degree of. repeatability: A low degree of repeatability: ©2021 Cengage Learning. All Rights Reserved. May not be scanned, copied or duplicated, or posted to a publicly accessible website, in whole or in part. 34 Matrices Comparison (Similarities) 1. Superior performance occurs by generally staying along the diagonal of the matrices. 2. Midrange portions of the matrices contains a broad range of intermediate design choices. 3. Venturing far off the diagonal may cause a company to be unable to achieve its priorities. ©2021 Cengage Learning. All Rights Reserved. May not be scanned, copied or duplicated, or posted to a publicly accessible website, in whole or in part. 35 Chapter 7b Summary Product Life Cycle (PLC): “A characterization of product growth, maturity, and decline over time.” Product-Process Matrix: “A model that describes the alignment of process choice with the characteristics of the manufactured good.” Service-Positioning Matrix: “A model that describes the relationship between service encounter levels and management service design to meet customers technical and behavioral needs.” ©2021 Cengage Learning. All Rights Reserved. May not be scanned, copied or duplicated, or posted to a publicly accessible website, in whole or in part. 36