Milling, Mixing PDF
Document Details
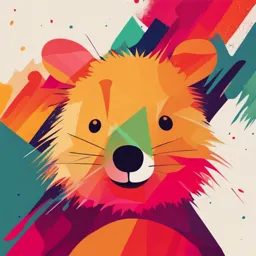
Uploaded by HumbleActionPainting2756
Trinity College Dublin
Tags
Summary
This document is a transcript of a lecture on milling and mixing within pharmaceutical manufacturing. It details different types and mechanisms of milling and mixing, including reasons for particle size reduction and types of stress, as well as methods for achieving a suitable degree of mixing.
Full Transcript
Transcript Milling, Mixing Slide 1: Introduction............................................................................................................ 3 Slide 2: Pharmaceutical Manufacturing Train................................................................... 3 Slide 3:...
Transcript Milling, Mixing Slide 1: Introduction............................................................................................................ 3 Slide 2: Pharmaceutical Manufacturing Train................................................................... 3 Slide 3: Section 1: Milling.................................................................................................... 4 Slide 4: Reasons for Particle Size Reduction..................................................................... 4 Tab 1: Topical Preparations.............................................................................................. 5 Tab 2: Aerosols.................................................................................................................. 5 Tab 3: Suspension Formulations...................................................................................... 6 Tab 4: Drying Processes.................................................................................................... 7 Tab 5: Blending Powders.................................................................................................. 7 Tab 6: Tinted Preparations............................................................................................... 8 Tab 7: Flow Characteristics............................................................................................... 8 Slide 5: Mechanisms of Particle Size Reduction............................................................... 9 Tab 1: Elastic Behaviour................................................................................................... 9 Tab 2: Plastic Deformation............................................................................................. 10 Tab 3: Heat...................................................................................................................... 11 Tab 4: Fracture or Failure............................................................................................... 11 Slide 6: Types of Stress..................................................................................................... 12 Tab 1: Compression........................................................................................................ 13 Tab 2: Tensile.................................................................................................................. 13 Tab 3: Shear.................................................................................................................... 14 Slide 7: Free and Packed Crushing.................................................................................. 15 Slide 8: Wet and Dry Grinding........................................................................................... 16 Slide 9: Section 2: Mixing.................................................................................................. 17 Slide 10: Mixing.................................................................................................................... 17 Slide 11: Classification of Mixing........................................................................................ 18 Tab 1: Positive................................................................................................................. 19 Tab 2: Negative................................................................................................................ 19 Tab 3: Neutral.................................................................................................................. 20 Slide 12: Reasons for Mixing.............................................................................................. 21 Slide 13: Solid-Solid Mixing................................................................................................. 21 Tab 1: Point Uniformity.................................................................................................... 22 Tab 2: Random Mix......................................................................................................... 23 Slide 14: Scale of Scrutiny.................................................................................................. 24 Tab 1: Size of Sample..................................................................................................... 24 1 Transcript Tab 2: Example................................................................................................................ 25 Slide 15: Degree of Mixing.................................................................................................. 26 Tab 1: Variance Plot........................................................................................................ 27 Slide 16: Index of Mixing..................................................................................................... 27 Tab 1: Lacey Index........................................................................................................... 28 Tab 2: Plot........................................................................................................................ 29 Slide 17: Properties of Materials that Influence Mixing.................................................... 30 Slide 18: Powder Segregation............................................................................................. 31 Slide 19: Mechanisms of Mixing......................................................................................... 31 Slide 20: Summary............................................................................................................... 32 2 Transcript Slide 1: Introduction Hello and welcome, my name is Anne Marie Healy and I will be leading you through this session on Milling and Mixing. Slide 2: Pharmaceutical Manufacturing Train Going back to the Pharmaceutical Manufacturing train from the previous session, we’ll now move onto two further unit processes, milling and mixing. 3 Transcript Slide 3: Section 1: Milling The first unit process that I’m going to discuss in this lecture is milling, which can also be referred to as grinding, comminution or simply particle size reduction. In a pharmaceutical context, there's a number of reasons why we might want to size reduce materials. Slide 4: Reasons for Particle Size Reduction Particle size reduction may be required for clinical or formulation performance reasons. For example, particle size can impact on dissolution rate. Dissolution rate will be dependent on both the solubility of the API and the surface area that is in contact with the dissolution medium. So if we're dealing with a very poorly soluble drug, for example, 4 Transcript and we want to improve its dissolution rate, if we size reduce the material and increase the surface area per unit weight or per unit volume, we can, in many cases, significantly increase the dissolution rate of the API from the drug product. Click each tab for more examples of why particle size reduction may be needed. Tab 1: Topical Preparations In the case of topical preparations, like ointments, or lotions, if we want to get absorption through the skin from that topical preparation, we should increase the surface area that is in contact with the skin when the formulation is applied, and so we size reduce the material. Size reduction of any material that's suspended in a topical formulation will also improve the feel of that preparation when it's applied to the skin. Tab 2: Aerosols 5 Transcript In terms of aerosols for oral inhalation where we are looking for the drug to get down into the lungs, the particle size is critical. For those types of inhaler formulations, the aerodynamic particle diameter must be between 0.5 and 5 micrometres. So a very, very small and very narrow, particle size and particle size distribution is required to ensure deposition down into the lungs. Tab 3: Suspension Formulations There are also physicochemical reasons for size reducing materials. Particle size is important to the physical stability of suspension formulations. Here, we want to make sure that the particle size is small enough that once the product is shaken particles in suspension will stay suspended for a sufficient period of time for a patient to withdraw a homogenous dose from the formulation. 6 Transcript Tab 4: Drying Processes Particle size can be important in drying processes. If we size reduce the material, we increase the surface area available for the heat and mass transfer processes that are so critical to a drying process. By size reducing the material and increasing the surface area, we can improve the drying rate. Tab 5: Blending Powders In the case of blending powders, and we’ll see this when we come to look at mixing as a unit process, the particle size and the particle size distribution of the different powders that you're trying to mix or blend, is critical. It's much easier to mix together powders that are of the same or similar particle size. So often a milling step will precede a mixing step, to get the different powders down to a similar size or similar size range. 7 Transcript Tab 6: Tinted Preparations It’s important to note that particle size can affect the appearance of tinted preparations. If you have coloured components, be it an API or an excipient in, for example, a tablet formulation, a differing particle size for that colour component may result in a different colour to the final formulation. Tab 7: Flow Characteristics The particle size can also have a significant impact on flow characteristics. While we may want to size reduce material for a number of reasons, it's important to note that particle size can have a significant impact on powder flowability. The smaller the particle size gets, generally, the more difficult flow becomes and the poorer the flow characteristics are. So, we may have to balance a particle size reduction or a low particle size with appropriate or acceptable flow characteristics. 8 Transcript Slide 5: Mechanisms of Particle Size Reduction Let's look now at the mechanisms of particle size reduction. Particle size reduction involves applying a stress or force to the material that we want to size reduce, stress being the average force exerted per unit area. When we apply stress to a material, it experiences a strain. We can see in this stress- strain curve here, the different types of behaviour that can exist as different levels of stress are applied to a material. Click each tab for more information and when you’re ready click next to continue. Tab 1: Elastic Behaviour In this case, as we apply stress in the region from A to B, the material exhibits a strain. 9 Transcript But that strain is manifested as elastic behaviour. What that means is that if we remove the stress that we're applying, the strain is fully recoverable. If, for example, you have a crystalline material, a crystal of an API. If you apply a force or you apply a stress to that material, you will cause a strain in the crystal lattice. The crystal lattice will become distorted. It will be shifted. It will move. But if you remove the stress, that is take away the force that you're applying, the strain is fully recoverable, and the crystal lattice will recover. It will, if you like, bounce back to its original position. And this is what's referred to as elastic behaviour. Tab 2: Plastic Deformation Now, beyond this region of elastic behaviour, which runs from A to B, you get to a point C, which is the elastic limit or the yield point. Point C represents the end of the elastic behaviour region. And beyond this point, C, we no longer have elastic behaviour where the strain is fully recoverable. Instead, we have what's called plastic deformation. And when we have plastic deformation, if you release the stress, so, for example, at this point here D, the strain is not fully recoverable and that's illustrated by this dotted line here. If we continue to apply stress, and increase the amount of stress that's applied, we will reach a point where we get fracture or failure of the material, and the material breaks. 10 Transcript Tab 3: Heat Now, stress energy in reversible deformation before the yield point, manifests as heat. In a grinding process, in a size reduction process where you're applying a stress, and exerting a force on the material, in most instances the material heats up. And this is important because if you're dealing with thermosensitive or thermolabile materials, you may want to be careful about the amount of grinding force that you apply because the heat that's generated may be detrimental to the material that you're processing. Tab 4: Fracture or Failure We can broadly categorise material that is size reduced into two classes, one is ductile materials and one is brittle materials. With ductile materials, we see an extensive period of plastic deformation and they can absorb a lot of strain before they break. Whereas with brittle materials point C and E, so the yield point and the point of fracture almost 11 Transcript coincide. In size reducing materials, when causing fracture or failure, the fracture or failure will be concentrated initially at any natural flaws or cracks that are present in the material and failure will occur along these flaw lines. In other words, the stress is concentrated in the vicinity of the flaw. And that's where the size reduction, the fracture, the failure will take place, certainly initially. Most materials are not perfect. Even if you have a crystalline material, it's rare that you will get a whole batch of crystals that are perfectly formed without any natural cracks or flaws in them. And the more cracks or flaws that are naturally present, the easier it is to get size reduction of that material because you get fracture along the crack or the flaw which propagates through the particles, and reaches other cracks or flaws. And so, you get size reduction as a single particle breaks up into smaller particles and those smaller particles break up into smaller particles again. The initial size reduction is the easiest part to effect, and it becomes more and more difficult as the grinding process progresses to get further size reduction, as you've consumed or used up all these natural failure lines or flaw lines. Slide 6: Types of Stress In terms of the different types of stress then that can be applied and can be used in grinding equipment to effect particle size reduction or milling - we have compressive stress and impact, which is a type of compressive stress. We have tensile stress. We also have shear stress and attrition, which is a type of shear stress. Click each tab to learn more, when you are ready, click next to continue. 12 Transcript Tab 1: Compression In compression, particle size reduction occurs by applying a force slowly to the particle in a direction towards the centre of the particle, as is indicated here. In impact, which is more commonly seen with particle size reduction equipment, particle size reduction is achieved by applying an instantaneous force perpendicular to the surface of the particle. So we apply a force rapidly, directed to the centre of the particle, but remove it immediately afterwards. Apply again, remove again and so on. Tab 2: Tensile Tensile stress is seen where we're ripping the material apart. We're applying a force away from the centre trying to pull the material apart. Tensile stress is actually quite difficult to achieve in standard grinding or size reduction equipment. 13 Transcript Tab 3: Shear Shear stress is where we get particle size reduction by applying a force in a direction parallel to the particle surface. Shear stress can arise because of particles shearing along the wall of the grinding chamber, for example. Another type of shear stress that we see is attrition. Attrition is where shear force arises from particle-particle contact. So particles shearing against one another. If we get a lot of attrition arising in a grinding process, that results in very fine grinding, and we can expect to get very small particle sizes, and very fine material generated. Often in a particular piece of grinding equipment, in a particular grinding process, we will have a mixture of different types of stress, although one may be predominant over the others. We often will get a mixture of, for example, impact and shear or impact and attrition. 14 Transcript Slide 7: Free and Packed Crushing Comminution or grinding can be a free or a packed process. With, what’s called, free crushing the stress is removed as soon as the particles are ground, but with packed crushing application of stress continues on the crushed bed of particles. Free crushing is seen where we have a continuous grinding process with continuous feed into the grinding chamber of the material to be size reduced and continuous exiting of the size reduced material. The material moves in a continuous fashion in and out of the grinding chamber. It doesn't sit within the grinding chamber to be continuously and further size reduced. Whereas with a packed crushing system, the application of stress continues on a crushed bed of particles. So here you introduce the material to be size reduced into the grinding chamber and grind for a fixed period of time. You then stop the process and recover the size reduced material. A problem that can sometimes arise with packed crushing, is that the smaller particles, as they’re produced, tend to adhere onto the surface of the larger particles and they can cushion those larger particles and protect them from further size reduction. 15 Transcript Slide 8: Wet and Dry Grinding Another option that we have in terms of grinding is to do a wet grinding process as opposed to a dry grinding process. With dry grinding, if we were size reducing a powder, we would just introduce that powder in the dry state, into the grinding chamber of the mill. But the problem is that many materials will have poor flow characteristics. And with most of these grinding processes, we need the material to move freely and easily within the grinding chamber in order to be effectively size reduced. Poor flow properties are often as a result of high cohesive forces between particles, and this can be accentuated if the material is a little bit damp, if it contains a significant amount of moisture or solvent, for example between 5 and 20%. If a drying process precedes the grinding process, then you may not have this problem. If you don't want to introduce a drying process prior to milling, you can undertake a wet grinding or wet milling process. Wet grinding overcomes some of the problems with trying to encourage material to readily and easily move within the grinding chamber. In a wet grinding or a wet milling process, what we do is we make up a slurry or concentrated suspension of the material to be size reduced, by suspending the material in a liquid in which it won't dissolve. And in fact, in some cases we can feed liquid with crystallised material straight from a crystalliser into a wet milling step. Advantages of wet grinding are that it tends to be a lower energy process than dry grinding. There's easier handling of material, you can load more into the mill and you eliminate any dust hazards that arise as a result of dry grinding processes. But a disadvantage is that you may have to perform a drying step after grinding, depending on the next stage in the manufacturing process. There also tends to be more wear and tear on the equipment, on the inner walls of the grinding chamber. There are various types of grinding equipment that can be used for size reducing pharmaceutical materials. In this session the focus is on large-scale processing equipment. Obviously, in a small scale, at the lab scale, we have things like mortars and pestles which can size reduce 16 Transcript material and can inform us how a material will behave on size reduction. Material can be classified as ductile or brittle, but there are also different levels of hardness of material. And so, if you want to get a sense of how hard a material is and how difficult it will be to size reduce often you would start off with investigations at a lab scale. Please see the study section on your session homepage to view recordings on different types of mills. Slide 9: Section 2: Mixing Mixing is the second unit process that I’m going to deal with in this lecture. Slide 10: Mixing Mixing is an operation in which two or more ingredients are treated so that each particle, 17 Transcript if it's solids we're talking about, or each molecule, if it's fluids, of any one ingredient is as nearly as possible adjacent to a particle or a molecule of each of the other ingredients. Mixing can also be referred to as blending. And the opposite of mixing, is demixing or segregation. When you're conducting a mixing process, you have to watch for the point where demixing or segregation starts to occur, and for material that you have already mixed, you have to watch out that segregation of that material, doesn't subsequently happen. Slide 11: Classification of Mixing Mixing can be classified into three different types: Positive, negative and neutral. Click each tab to learn more, when you are ready, click next to continue. 18 Transcript Tab 1: Positive Positive mixing applies to systems which, if given sufficient time, would spontaneously and irreversibly mix by diffusional processes, for example, miscible fluids. If miscible fluids (gases or liquids) are put side by side, they will naturally mix by diffusion. How long it takes for them to mix will depend on the conditions in which they are held and their diffusion coefficients. In this case, mixing equipment, which involves inputting energy into the system, can be used to speed up the mixing process. Tab 2: Negative Negative mixing, then, is where you have systems where separation of phases occurs, unless there's continuous input of energy in the form of agitation. An example of this is when you have phases of different densities. For example, a liquid and a solid phase as you have in a solid suspension. So as soon as you make up a solid suspension and put it 19 Transcript to rest, you will immediately start to get phase separation or separating out of the solid and the liquid phase. And in order to keep that suspension in exactly the same homogenous state as it started out in, you have to input energy into the system. You have to agitate the system. Tab 3: Neutral Neutral mixing, then, is where nothing happens, neither positive nor negative mixing, unless a force is exerted. Neutral mixing would apply in the case of mixing of two or more solids, for example. So, if you sit those materials side by side, they have no tendency to mix spontaneously, nor will they have a tendency to separate from one another, once there has been input of work to mix them. However neutral mixes are capable of demixing if there is an energy input. 20 Transcript Slide 12: Reasons for Mixing There are different reasons or purposes for undertaking mixing or blending processes. An important reason is to produce uniformity of composition of the mixed system. So if you're developing a pharmaceutical product which comprises, not just the API but the API mixed with a number of different excipients, as is the case for most pharmaceutical products, then you need to ensure that you have a uniform mix to ensure you have uniform composition in the formulation, which will in turn give you uniform dosing from that formulation. Mixing can also be used to promote physical or chemical reactions. So to promote things like crystallisation or dissolution, you would mix the system. Slide 13: Solid-Solid Mixing 21 Transcript With solids, a mix can be defined as being either a perfect mix, a random mix or something in between. If, for example, we have two different solid materials, one represented by the white squares here or in three dimensions, white cubes, one represented by the black squares or, in three dimensions, black cubes - this might be an excipient and an API. Click each tab to learn more, when you are ready, click next to continue. Tab 1: Point Uniformity This schematic represents a system that has point uniformity. If you look at any individual particle in this system, it is surrounded on all sides by a particle of the other component. Each black cube is surrounded on all sides and in all dimensions by a white cube or white particle. And this is what's regarded as a perfect mix. However, a perfect mix with point uniformity is virtually impossible to achieve in practice in pharmaceutical processing. 22 Transcript Tab 2: Random Mix However, you can hope to achieve what's called random mix, as shown in this schematic, where the probability of finding one type of particle at any point in the mixture is equal to the proportion of that particle in the system. So, if you were to take largeish sections out of this mix and count the number of black particles and the number of white particles, then you should get a 50/50 ratio or close to a 50/50 ratio. However, as we start to look at smaller and smaller regions within the mix, we see that the 50/50 proportion doesn't always hold up. If you scrutinise any mixture at a small enough scale, unless it has point uniformity, you will see regions of segregation. So, we need to be able to define when mixing is deemed to be complete. In other words, when we have a sufficiently random mix. 23 Transcript Slide 14: Scale of Scrutiny Sampling of the mixture is critical, and the size of the sample that you take from the mixture is critical. Ideally sampling is best done from a flowing powder, from powder that's actually moving, powder that isn't static. But if you do have to sample from a static powder, then you use what's referred to as a sample thief, as is shown here with an operator using a sample thief to sample from this drum of powder. Click each tab to learn more, when you are ready, click next to continue. Tab 1: Size of Sample After we take samples from the mix we can assay the amount of API, in that sample, if for 24 Transcript example it’s a mixture of API and excipients. There are statistical tools which can tell us how many samples to take, but the other question is what size sample to take. The size of sample depends on the scale of scrutiny, and the scale of scrutiny can be regarded as the minimum sample size to regard the mixture as insufficiently mixed. So, the minimum sample size, which will tell us whether or not we have achieved a good enough mix, a good enough random mix. Tab 2: Example If we take, as an example, a tablet, which has a compression weight of 200 milligrams, and for the sake of simplicity, let's say it has 50 percent drug in it and 50 percent diluent. So 50 percent excipient or mixtures of excipients. In any 200 milligram sample of the mixed powder before it's compressed into a tablet, you should have, within very narrow limits, a hundred milligrams of drug and a hundred milligrams of diluent. The way in which the two components are dispersed in that two hundred milligrams is actually not of importance from a uniformity of composition viewpoint as long as the tablet isn't divided or broken before it's taken by the patient. In this case, the scale of scrutiny is determined by the weight of the tablet. We need to show that for a 200 milligram sample, we have 100 milligrams of drug and 100 milligrams of diluent. There's no point in taking, for example, a 500 milligram sample and showing that we have 250 milligrams of drug and 250 milligrams of excipient. Because, if you were to subdivide that down into a 200 milligram sample size, you may not necessarily have the hundred milligrams drug, hundred milligrams diluent that you need. Likewise, there's no point in going down to a smaller sample size. There's no point in assaying, we'll say, 50 milligrams of powder and proving that you have 25 milligrams of drug and 25 milligrams of excipient, because we don't need to look at that small a scale. 25 Transcript Slide 15: Degree of Mixing Now, we need then to be able to determine, in the course of a mixing process, when we have achieved a sufficient level of randomness. When have we got to the state of having a random mixture? To do this, we need to be able to monitor the mixing process and determine the degree of mixing that's achieved. In order to monitor a mixing process to determine: the extent of mixing, when the system is sufficiently mixed, the efficiency of a mixer, or the appropriate time for a mixing process, we need to be able to determine the degree of mixing. For solids, the degree of mixing is measured by the statistical variation in composition amongst samples withdrawn at any time from a mix. If s is the standard deviation of the samples, which can be calculated from this equation here. Then s squared is what's called the variance for the mixture. In these equations, x is the sample measurement, x bar is the mean of the sample measurements and n is the number of samples. So, if you're mixing a drug with an excipient in a blender, and at different time intervals, you take maybe 20 samples from that mix. What you do is assay each of those samples, perhaps by HPLC or some other quantitative assay method, and determine the amount of drug that's in each sample. So that's your sample measurement. X bar then, will be the mean of the sample measurements and n will be the number of samples that you've taken. A variance of zero means that the numbers in a set are all the same. There's no difference between any of your samples and you have a perfect mix. The larger the variance, the more spread out the dataset. If you have a wide range of different assay results, you'll expect to see a large variance figure. So, with this type of analysis, what we're looking for is the change in variance with mixing time. This is normally how we determine the extent of mixing or when a system is sufficiently mixed or the efficiency of a mixer or the appropriate time for a mixing process. 26 Transcript Click the tab for more information, when you are ready, click next to continue. Tab 1: Variance Plot This plot shows the variance of the lactose content versus time of mixing when lactose is mixed with another excipient, cornstarch, and shows results from two different trials for the same mixing process. The variance falls reasonably rapidly initially, then levels out and then starts to creep up again. This creeping up again is when we're starting to get demixing or segregation occurring, and so we've passed the point for optimum mixing, when the variance is minimised. When the variance is minimised we've achieved as much randomness in the mix as we can hope to achieve. And this is where we should stop our mixing process. Slide 16: Index of Mixing 27 Transcript When a material is partly mixed and we have yet to achieve a full random mix, then an index of mixing can be used to represent the degree of mixing. Click each tab for more information, when you’re ready, click next to continue. Reference(s): 1. Lacey, P.M.C. The mixing of solids, Transactions of the Institution of Chemical Engineers, 21 (1943) 53-59. 2. Lacey, P.M.C. Development in the theory of particle mixing, Journal of Applied Chemistry 4 (1954) 257-268. 3. Poole, K. R., Taylor, R. F., and Wall, G. P. 1964. Mixing powders to fine scale homogeneity: studies of batch mixing. Transactions of the Institution of Chemical Engineers 42: T305-T315 Tab 1: Lacey Index This is one index of mixing which was proposed by Lacey and is commonly used. M1 is the index of mixing and is determined based on measurements of sample variance. M1 is equal to So2 minus SACT2 divided by So2 minus SR2 where, So2 is the variance of samples drawn from the unmixed material, where the materials are completely separated or segregated before the mixing process is initiated, SACT2 is the variance of samples taken from the mix under investigation and SR2 is the variance of samples from a fully random mix. In practical terms the Lacey mixing index is the ratio of ‘mixing achieved’ to ‘mixing possible’. A Lacey mixing index of zero would represent complete segregation and a value of 1 would represent a completely random mixture. Practical values of this mixing index are often found to lie in the range 0.75 to 1.0. A simpler form of this index of mixing is given by the second equation shown here, where the mixing index (M2) is determined from SR divided by SACT, where SACT is the standard deviation of samples taken from the mix under investigation and SR is the standard deviation of samples from a fully random mix. This index (which is the inverse 28 Transcript of the index originally proposed by Poole et al.) gives better discrimination for practical mixtures and approaches unity for completely random mixtures. So, you'll see that, as the mixing process proceeds, the standard deviation (and variance) of samples taken from the mix will decrease. It will fall off until it levels out at the minimum point, which is the SR value, the standard deviation of samples from a fully random mix. Tab 2: Plot For either mixing index, the Lacey Mixing Index, M1, or for M2, the index will tend to zero for an unmixed material. So, at the start of the process, M should be close to zero, and as the mixing progresses and you get closer and closer to a random mix, M will approach one. So, with efficient mixing or increasing randomization, the mixing index will approach unity. That's what's shown in this plot here, where there was a spectroscopy measurement used to determine the level of mixing or the degree of mixing, and Lacey's mixing index is plotted versus time of mixing. And you'll see that it approaches, but doesn't quite reach one, as the mixing proceeds and we get closer and closer to a random mix. 29 Transcript Slide 17: Properties of Materials that Influence Mixing So what are the properties of materials that can influence the ease of mixing? Well, for solids, it's things like the particle size, the density, the relative density, the shape and the stickiness of the materials. And usually the closer these are to one another for different components of the mixture, the easier it is to blend the solid materials together. So, the particle sizes should be similar, densities should be similar, shapes should be similar. If you have any disparities in any of these parameters, it will make mixing more difficult as the differing particles with different characteristics will tend to separate from one another Stickiness is really a measure of the cohesiveness of the material, its tendency to stick together and to agglomerate. Agglomeration can interfere with good mixing because, in order to achieve a good random mix, individual particles should behave as individual particles and not have a tendency to agglomerate, aggregate or stick together. If you manage to deagglomerate the material and get particles of different components to come together, rather than particles of the same component, then once you've achieved that mix, it is more difficult for that system to demix. So stickiness or cohesiveness of materials can interfere with good mixing initially, but can prevent demixing of a mixed system. When we're talking about mixing of fluids, then we're looking at parameters of the fluids, such as the viscosity and again, the density or the relative density and the miscibility or immiscibility of the fluids. The closer these parameters are to one another, the easier the mixing process. It's easier to mix miscible liquids than immiscible liquids because, with miscible liquids, you will have a positive mixing process, while with immiscible liquids we have to effect an emulsification process where we can stabilise one liquid in another liquid. If we're trying to mix a solid and a liquid together, then density and relative densities of the different phases are important, as is viscosity. 30 Transcript Slide 18: Powder Segregation Powder segregation is a problem that we have to overcome if we're dealing with solid blending or solid mixing because, if it occurs, an already formed random mix may change to a non-random mix. Or alternatively, a random mix may never be achieved because segregation starts to occur before you get to the point where you've achieved a random mix. A further discussion of segregation in powder blending and different segregation mechanisms is available in the study section for this session. Slide 19: Mechanisms of Mixing In terms of mechanisms of mixing then and the different mechanisms which we see in 31 Transcript use in the different types of pharmaceutical mixers or blenders, there are three different types: convective, diffusive and shear. In convective mixing we see the transfer of groups of adjacent particles, if it's a solid- solid mixing process, or groups of adjacent molecules in the case of liquids. With diffusive mixing, we have individual particles or molecules diffusing to new areas in the blend or in the mix. Diffusive mixing or at least an element of diffusive mixing is required for good random mixing, and particularly if the scale of scrutiny is very small. Shear mixing then occurs when there's a displacement of two regions relative to each other to form a slip plane. All of these take place to varying extents in mixing processes and in the different types of equipment. All of these mechanisms are relatively mild. For solid materials which tend to aggregate it may be necessary to grind and mix simultaneously. It may not be enough simply to use a blending or a mixing process because you may need to use some element of impact and attrition to aid or to facilitate the mixing process. In this session the main focus has been on solid-solid mixing. Please see the study section on your session home page to view a video which provides further information on liquid-liquid and liquid-solid mixing, and on the the different types of pharmaceutical equipment used for mixing. Slide 20: Summary Having completed this session you should now be able to: Identify when and why particle size reduction may be required Describe the mechanisms of particle size reduction and the types of stress involved Differentiate between the classifications of mixing 32 Transcript Evaluate a mixing process in terms of the degree of mixing, using an appropriate scale of scrutiny and an index of mixing. And identify the material properties which affect mixing. 33