Milling: Chapter 2 - Industrial Pharmacy I PDF
Document Details
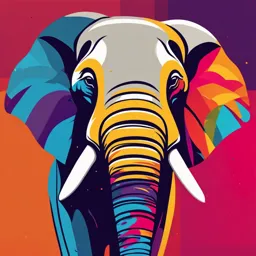
Uploaded by RadiantHyena
Tags
Summary
This document is a chapter on milling in industrial pharmacy. It discusses the importance of particle size reduction in various pharmaceutical applications, including dissolution, extraction, and drying, and details different milling techniques, and equipment used for milling.
Full Transcript
Industrial Pharmacy I Milling Chapter 2 |Milling Chapter 2 | Milling Contents : Milling 3 Pharmaceutical applications 6 Size distribution & measurement 11 Theory of comminution 14 Equipment 22 Techniques of milling 45 Selection of a mill 49 Chapter 2 | Milling Milling : Milling is the mechanical pro...
Industrial Pharmacy I Milling Chapter 2 |Milling Chapter 2 | Milling Contents : Milling 3 Pharmaceutical applications 6 Size distribution & measurement 11 Theory of comminution 14 Equipment 22 Techniques of milling 45 Selection of a mill 49 Chapter 2 | Milling Milling : Milling is the mechanical process of reducing the particle size of solids. Various terms (comminution, crushing, disintegration, dispersion, grinding, and pulverization) have been used synonymously with milling depending on the product, equipment, and the process. Milling equipment is classified as coarse, intermediate and fine according to the size of the final product. Chapter 2 | Milling Size is conventionally expressed in terms of mesh (number of opening per inch square). 1. Coarse for particles size larger than 20-mesh. 2. Intermediate (20-200) mesh (74 -840 micron). 3. Fine for particles size smaller than 200-mesh A given mill can be used successfully to prepare particles in more than one class. (ex. Hammer mill used for granulation (16-mesh) and for milling crystalline API to a 120-mesh powder). Pharmaceutical applications Chapter 2 | Milling Pharmaceutical Applications : Numerous examples have been quoted to stress the importance of fine particles in pharmacy and milling or grinding offers a method by which these particles can be produced. The surface area per unit weight, which is known as the specific surface, is increased by size reduction. In general, a 10-fold increase in surface area has been given by a 10-fold decrease in particle size. This increased surface area affects: 1) Dissolution and therapeutic efficacy: Dissolution and therapeutic efficiency of medicinal compounds that possess low solubility in body fluids are increased due to increase in the area of contact between the solid and the dissolving fluid. Chapter 2 | Milling 2) Extraction: Extraction or leaching from animal glands (liver and pancreas) and crude vegetable drugs is facilitated by comminution. The time required for extraction is shortened by the increased area of contact between the solvent and the solid and the reduced distance the solvent has to penetrate into the material. 3) Drying: The drying of wet masses may be facilitated by milling, which increases the surface area and reduces the distance that the moisture must travel within the particle to reach the outer surface. In the manufacture of compressed tablets by wet granulation process, the sieving of the wet mass is done to ensure more rapid and uniform drying. Chapter 2 | Milling 4) Flowability: The flow property of powders and granules is affected by particle size and size distribution. The freely flowing powders and granules in high-speed filling equipment and tablet presses produce a uniform product. 5) Mixing or blending: The mixing or blending of several solid ingredients of a pharmaceutical is easier and more uniform if the ingredients are of approximately the same size. This provides a greater uniformity of dose. Solid pharmaceuticals that are artificially coloured are often milled to distribute the colouring agent to ensure that the mixture is not mottled and uniform from batchto-batch. Chapter 2 | Milling 6) Formulation: Lubricants used in compressed tablets and capsules function by virtue of their ability to coat the surface of the granulation or powder. A fine particle size is essential if the lubricant is to function properly. The milling of ointments, creams, and pastes provides a smooth texture and better appearance in addition to improved physical stability. Also, the sedimentation rate of suspensions and emulsions is a function of particle size and is reduced by milling. Size distribution & measurement Chapter 2 | Milling Size distribution & measurement : Naturally occurring particulate solids & milled solids, the shape of particles is irregular & the size of the particles varies within the range of the largest & smallest particles. There is no known method of defining an irregular particle in geometric terms ; however statistical methods have been developed to express the size of an irregular particle in terms of diameter. For an irregular particle an equivalent particle with the same surface or volume may be substituted Chapter 2 | Milling For convenience of mathematical treatment, an irregular particle is considered in terms of an equivalent sphere. So the irregular particle expressed as diameter. Methods of diameter measurement : 1. Microscopy. 2. Sieving. 3. Sedimentation. Theory of comminution Chapter 2 | Milling Theory of comminution The mechanical behavior of solids, under stress are strained and deformed, is shown in the stress-strain curve. Fig. 2.1: Stress-strain diagram for a solid Chapter 2 | Milling The initial linear portion of the curve is defined by Hooke‟s law (stress is directly proportional to strain), and Young‟s modulus (slope of the linear portion) expresses the stiffness or softness of a solid in dynes per square centimeter. The stress-strain curve becomes nonlinear at the yield point, which is a measure of the resistance to permanent deformation. With still greater stress, the region of irreversible plastic deformation is reached. The area under the curve represents the energy of fracture and is an approximate measure of the impact strength of the material. Chapter 2 | Milling In all milling processes, it is a random matter if and when a given particle will be fractured. If a single particle is subjected to a sudden impact and fractured, it yields a few relatively large particles and a number of fine particles, with relatively few particles of intermediate size. If the energy of the impact is increased, the larger particles are of a smaller size and greater number, and although the number of fine particles is increased appreciably, their size is not greatly changed. It seems that the size of the finer particles is related to the internal structure of the material, and the size of the larger particles is more closely related to the process by which comminution is accomplished. Chapter 2 | Milling If the force of impact does not exceed the elastic limit, the material is reversibly deformed or stressed. When the force is removed, the particle returns to its original form, and the mechanical energy of stress in the deformed particle appears as heat. A force that exceeds the elastic limit fractures the particle, as fracture occurs, the points of application of the force are shifted. The energy for the new surfaces is partially supplied by the release of stress energy The useful work in milling is proportional to the length of new cracks produced. Chapter 2 | Milling A particle absorbs strain energy and is deformed under shear or compression until the energy exceeds the weakest flaw and causes fracture or cracking of the particle. The strain energy required for fracture is proportional to the length of the crack formed, since the additional energy required to extend the crack to fracture is supplied by the flow of the surrounding residual strain energy to the crack. Chapter 2 | Milling Mechanisms of Comminution : Mills are equipment designed to impart energy to the material and cause its size reduction. There are four main methods of effecting size reduction, involving different mechanisms: 1) Cutting: It involves application of force over a very narrow area of material using a sharp edge of a cutting device. 2) Compression: In compression, the material is gripped between the two surfaces and crushed by application of pressure. Chapter 2 | Milling 3) Impact: It involves the contact of material with a fast moving part which imparts some of its kinetic energy to the material. This causes creation of internal stresses in the particle, there by breaking it. 4) Attrition: In attrition, the material is subjected to pressure as in compression, but the surfaces are moving relative to each other, resulting in shear forces which break the particles. Equipment Chapter 2 | Milling Equipment : A mill consists of three basic parts: (1) Feed chute, which delivers the material, (2) Grinding mechanism, usually consisting of a rotor and stator, and (3) A discharge chute. The principle of operation depends on cutting, compression, impact from a sharp blow, and attrition. In most mills, the grinding effect is a combination of these actions. If the milling operation is carried out so that the material is reduced to the desired size by passing it once through the mill, the process is known as open-circuit milling. Chapter 2 | Milling A Closed circuit mill is the one in which the discharge from the milling chamber is passed through a size-separation device or classifier, and the oversize particles are returned to the grinding chamber for further reduction of size. Closed-circuit operation is most valuable in reduction to fine and ultrafine size. The classification of most commonly used mills in pharmaceutical manufacturing is given in Fig. 2.4. Chapter 2 | Milling Mills Cutting Compression Impact Attrition Homogenization Cutter Roller Hammer Pin Ball Pin Vibro-energy Ball Vibro-energy Fluid-energy Fluid-energy Spiral jet Spiral jet Simple Silverson Simple Ultrasonic Silverson High Ultrasonic pressure Microfluidizer High pressure Low-pressure Microfluidizer cyclone Low-pressure cyclone Colloid Edge & end runner Chapter 2 | Milling Cutter Mill : The rotary knife cutter has a horizontal rotor with 2 to 12 knives spaced uniformly on its periphery turning from 200 to 900 rpm and a cylindrical casing having several stationary knives. The bottom of the casing holds a screen that controls the size of the material discharged from the milling zone. Cutting mills are used for tough, fibrous materials and provide a successive cutting or shearing action rather than attrition or impact. Chapter 2 | Milling Fig. 2.5: Diagrammatic representation of cutter mill Chapter 2 | Milling Roller mill : It consists of two to five smooth roller operating at different speed. Mechanism by combination of compression and shearing action. Two cylindrical rolls mounted horizontally and rotated about their long axes. One of the rolls is driven directly while the second is rotated by friction as material is drawn through the gap between the rolls. Chapter 2 | Milling A form of roller mill used for milling ointments, pastes and suspension where both rolls are driven but at different speeds, so that size reduction occurs by attrition. Chapter 2 | Milling Hammer Mill Construction and working : The hammer mill is an impact mill using a high speed rotor (up to 10,000 rpm) to which a number of swinging hammers are fixed. The material is fed at the top or center, thrown out centrifugally, and ground by impact of the hammers or against the plates around the periphery of the casing. The clearance between the housing and the hammers contributes to size reduction. The material is retained until it is small enough to fall through the screen that forms the lower portion of the casing. Chapter 2 | Milling Particles fine enough to pass through the screen are discharged almost as fast as they are formed. Fig. 2.7: Diagrammatic representation of hammer mill Chapter 2 | Milling The particle size that can be achieved will depend on the type of milling tool selected, rotor speed (calculated as tip speed at the outermost rotating part), and solid density in the mill or solid feed rate. Important processing variables for hammer mills are hammer tip speed and hammer mill screen size. As can be seen in : Figure (a) & Figure (b) Chapter 2 | Milling Figure (a) an increase in hammer tip speed contributes to a higher particle size reduction and thus a relatively fine mash. With an increase in hammer tip speed, the particles will follow a pathway closer to the screen due to the centrifugal force. Chapter 2 | Milling Figure (b) : shows that an increase in hammer mill screen thickness will also result in a relatively finer mash, as the coarser particles can only pass through the screen under a relatively narrow range of angles. Chapter 2 | Milling Applications : The hammer mill can be used for almost any type of size reduction. Its versatility makes it popular in the pharmaceutical industry, where it is used to mill dry materials, wet filter-press cakes, ointments, and Slurries, also a hammer mill can be used for granulation and close control of the particle size of powders. Advantages and disadvantages : Hammer mills are compact with a high capacity. Size reduction of 20 to 40 μm may be achieved, however, a hammer mill must be operated with internal or external classification to produce ultrafine particles. Chapter 2 | Milling Because the inertial forces vary with mass as the inverse cube of the diameter, small particles with a constant velocity impact with much less kinetic energy than larger ones, and the probability that particles less than a certain size will fracture decreases rapidly. In addition, small particles pass through the screen almost as fast as they are formed. Thus, a hammer mill tends to yield a relatively narrow size distribution. Hammer mills are simple to install and operate. The speed and screen can be rapidly changed. They are easy to clean and may be operated as a closed system to reduce dust and explosion hazards. Chapter 2 | Milling Ball Mill Construction and working : The ball mill consists of a horizontally rotating hollow vessel of cylindrical shape with the length slightly greater than its diameter. The mill is partially filled with balls of steel or pebbles, which act as the grinding medium Most ball mills utilized in pharmacy are batch-operated, however, continuous ball mills are available, which are fed through a hollow trunnion at one end, with the product discharged through a similar trunnion at the opposite end. The outlet is covered with a coarse screen to prevent the loss of the balls. Chapter 2 | Milling In a ball mill rotating at a slow speed, the balls roll and cascade over one another, providing an attrition action. As the speed is increased, the balls are carried up the sides of the mill and fall freely onto the material with an impact action, which is responsible for most size reduction. The factor of greatest importance in the operation of the ball mill is the speed of rotation. 1- At low angular velocities (Fig. a) the balls move with the drum until the forcem due to gravity exceeds the frictional force of the bed on the drum, and the balls then slide back to the base of the drum. Chapter 2 | Milling This sequence is repeated, producing very little relative movement of balls so that size reduction is minimal. 2- At high angular velocities (Fig. b) the balls are thrown out on to the mill wall by centrifugal force and no size reduction occurs. 3- At about two-thirds of the critical angular velocity where centrifuging occurs (Fig. c), a cascading action is produced. Chapter 2 | Milling Advantages and disadvantages : In addition to being used for either wet or dry milling, the ball mill has the advantage of being used for batch or continuous operation In a batch operation, unstable or explosive materials may be sealed within an inert atmosphere and satisfactorily ground. Ball mills may be sterilized and sealed for sterile milling in the production of ophthalmic and parenteral products. The installation, operation, and labor costs involved in ball milling are low. Finally, the ball mill is unsurpassed for fine grinding of hard and abrasive materials. Chapter 2 | Milling Fluid-energy Mill Construction and working : In the fluid-energy mill or micronizer, the material is suspended and conveyed at high velocity by air or steam, which is passed through nozzles at pressures of 100 to 150 pounds per square inch (psi). The violent turbulence of the air and steam reduces the particle size chiefly by inter particular attrition. Air is usually used because most pharmaceuticals have a low melting point or are thermo labile. Chapter 2 | Milling As the compressed air expands at the orifice, the cooling effect counteracts the heat generated by milling. Fig. 2.14: Diagrammatic representation of fluid-energy mill Chapter 2 | Milling The most important machine-related factors are the grinding chamber geometry and the number and angle of the nozzles. In selecting fluid energy mills for production, the cost of a fluid-energy source and dust collection equipment must be considered in addition to the cost of the mill. Advantages and Disadvantages : Powders with all particles below a few micrometers may be quickly produced by this method. The disadvantage of high capital and running costs may not be so serious in the pharmaceutical industry because of the high value of the materials which are often processed. Chapter 2 | Milling One drawback of this type of mill is the potential for build-up of compressed product in the mill. This can affect milled particle size by changing the open volume in the mill or open area in the classifier, especially if classifier vanes or gas nozzles become plugged or blocked. Techniques of milling Chapter 2 | Milling Techniques OF Milling : In addition to the standard adjustments of the milling process (i.e., speed, screen size, design of rotor and load), special techniques of milling may be Useful. 1) Special Atmosphere: Hygroscopic materials can be milled in a closed system supplied with dehumidified air. Thermolabile, easily oxidizable, and combustible materials should be milled in a closed system with an inert atmosphere of carbon dioxide or nitrogen. Almost any fine dust (dextrin, starch, sulfur) is a potential explosive mixture under certain conditions and especially if static electrical charges result from the processing. Chapter 2 | Milling 2) Temperature Control: As only a small percentage of the energy of milling is used to form new surface, the bulk of the energy is converted to heat. This heat may raise the temperature of the material by many degrees, and unless the heat is removed, the solid will melt, decompose, or explode. To prevent these changes in the material and avoid stalling of the mill, the milling chamber should be cooled by means of a cooling jacket or a heat exchanger. 3) Pretreatment: For a mill to operate satisfactorily, the feed should be of the proper size and enter at a fairly uniform rate. If granules or intermediate sized particles are desired with a minimum of fines, pre-sizing is vital. Pretreatment of fibrous materials with high pressure rolls or cutters facilitates comminution. Chapter 2 | Milling 4) Subsequent Treatment: If extreme control of size is required, it may be necessary to recycle the larger particles, either by simply screening the discharge and returning the oversized particles for a second milling. 5) Wet and Dry Milling: The choice of wet or dry milling depends on the use of the product and its subsequent processing. If the product undergoes physical or chemical change in water, dry milling is recommended. Wet grinding is beneficial in further reducing the size, but flocculation restricts the lower limit to approximately 10 μm. Wet grinding eliminates dust hazards, and is usually done in low-speed mills, which consume less power. Selection of mills Chapter 2 | Milling Selection of mills : In general, the materials used in pharmaceuticals may be reduced to a particle size less than 40-mesh by means of ball, roller, hammer, and fluidenergy mills. The choice of a mill is based on : (1) Product specifications (size range, particle size distribution, shape, moisture content and physical and chemical properties of the material). (2) Capacity of the mill and production rate requirements. (3) Versatility of operation (wet and dry milling, rapid change of speed and screen, safety features). Chapter 2 | Milling (4) Dust control (loss of costly drugs, health hazards and contamination of plant). (5) Sanitation (ease of cleaning and sterilization). (6) Auxiliary equipment (cooling system, dust collectors, forced feeding and stage reduction). (7) Batch or continuous operation. (8) Economical factors (cost, power consumption, space occupied and labor cost).