ME511 Thermal Interface Materials PDF
Document Details
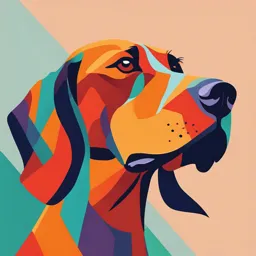
Uploaded by PromptReasoning1901
Purdue University
2022
Justin A Weibel
Tags
Related
- Chapter 4: Thermal Recovery Processes PDF
- Thermal Flooding Notes (PDF)
- Knight Chapter 12 Thermal Properties of Matter PDF
- Knight Chapter 12 Thermal Properties of Matter OCR PDF
- Building Utilities 2 – Electrical, Electronics, and Mechanical Systems Module 1: Thermal Comfort PDF
- CompTIA Chapter 5 Firmware PDF
Summary
This document presents lecture notes for a course on thermal interface materials. It covers the properties and characterization of these materials, with examples of different types and applications. The course is ME511, Fall 2022 at Purdue University.
Full Transcript
ME511: THERMAL INTERFACE MATERIALS Justin A Weibel School of Mechanical Engineering, Purdue University ME 511, Fall 2022 It’s the Interfaces*… A primary challenge in thermal management lies at its rich variety of thermal interfac...
ME511: THERMAL INTERFACE MATERIALS Justin A Weibel School of Mechanical Engineering, Purdue University ME 511, Fall 2022 It’s the Interfaces*… A primary challenge in thermal management lies at its rich variety of thermal interfaces across the many packaging levels These mitigated with the use of sophisticated “thermal interface materials” placed between surfaces to enhance thermal conductance Materials may form temporary or permanent bonds, depending on the application and location. Package-external interfaces, e.g., attachment of external heat sink (‘TIM2’) *Garimella, “The Package-internal interfaces, e.g., Challenge of Thermal attachment of die to integrated Management,” 2016 ITherm Achievement heat spreader (‘TIM1’) Award Presentation. ME 511, Fall 2022, Purdue University 2 Thermal Interface Materials (TIMs) Interface Phase Change Materials Thermal Gap Pad Dispensable Gap Fillers Thermal Grease/ Paste/ Compound https://www.newark.com/bergquist/ https://pm.lairdtech.com/ thermal-interface-materials/ https://pm.lairdtech.com/ thermal-interface-materials/ https://www.epoxysetinc.com/ ME 511, Fall 2022, Purdue University 3 TIM Pros & Cons Adapted from *R. Prasher, Proceedings of the IEEE. 94 (2006) 1571–1586. General TIM Type Advantages Disadvantages Characteristics Greases Typically silicone-based High bulk thermal conductivity; thin BLT Susceptible to grease pump-out and phase matrix loaded with with minimal attach pressure separation particles to enhance Low viscosity enables matrix material to Considered messy in a manufacturing thermal conductivity easily fill surface crevices environment due to a tendency to migrate No cure required Delamination is not a concern Phase Polyolefin, epoxy, low Higher viscosity leads to increased Lower thermal conductivity than molecular weight stability and hence less susceptible to greases Change polyesters, acrylics pump-out Surface resistance can be greater than greases. Materials typically with fillers Application and handling is easier Requires attach pressure to increase thermal compared to greases effectiveness hence can lead to increased No cure required; mechanical stresses Delamination is not a concern Adhesives Typically high- Conform to surface irregularity before Cure process needed conductivity particles in a cure Delamination post reliability testing is a concern cured epoxy matrix No pump out Since cured epoxies have high post cure modulus, No migration CTE mismatch induced stress is a concern ME 511, Fall 2022, Purdue University 4 Thermal Interface Materials (TIM) Total thermal resistance: Interface RTIM =Rbulk + Rc,1 + Rc,2 Rc,1 Thermal resistance due to Position Rbulk conduction across the bond Bond Line Thickness (BLT) line thickness dBLT Rbulk = kTIM Rc,1, Contact resistances between Rc,2 Rc,2 the TIM and the contacting surfaces due to non-perfect wetting Temperature ME 511, Fall 2022, Purdue University 5 Particle-Filled TIMs The thermal conductivity of TIMs is often increased by mixing with high-thermal-conductivity particles. Thermal resistances of the TIMs is governed by the: Effective thermal conductivity of the particle-polymer matrix Rheology (determines the bond line thickness and contact resistance as a function of pressure) Prediction of the thermal and mechanical behavior of TIMs (like many topics in the course) is an active area of research and development. Kanuparthi, Subbarayan, et al. IEEE CPMT 31 (2008) 611–621. One general prediction approach is offered here; there are many expressions for effective conductivity and rheology of such composites. ME 511, Fall 2022, Purdue University 6 Effective Thermal Conductivity Particle-filled TIMs treated as composites with an effective thermal conductivity Effective Conductivity Model Predictions Maxwell (kp > km): Carson et al., IJHMT 48 2km+kp−2(km−kp)(1−ε) (2005) 2150–2158. kTIM = km 2km+kp+(km−kp)(1−ε) Effective Medium Theory: (kp−kTIM) (km−kTIM) 0 = (1−ε) +ε (kp+2kTIM) (km+2kTIM) **These expressions are typically only valid for TIMs with low particle loadings; commercial TIMs often exceed 60% loading ε ME 511, Fall 2022, Purdue University 7 Predicting Thermal Conductivity Bruggeman model: km−kTIM k −k (no particle-to-particle 1−ϕ + ϕ p TIM = 0 km+2kTIM kp+2kTIM thermal resistance) (1+2𝛼𝛼) 3/(1−𝛼𝛼) Bruggeman asymmetric model: 3 km (1−𝛼𝛼) kTIM − kp(1−α) 1−ϕ = (includes particle-to-particle kTIM km − kp(1−α) thermal resistance) kTIM 1 Rbkm for kp >> km = 𝛼𝛼 = km 1−ϕ 3(1−𝛼𝛼)⁄(1+2𝛼𝛼) d ϕ: particle volume fraction kTIM , km , kp: thermal conductivity of the TIM, matrix, and particles d: particle diameter Rb: interfacial resistance between matrix and particles R. Prasher, Proceedings of the IEEE. 94 (2006) 1571–1586. ME 511, Fall 2022, Purdue University 8 Near-Percolation Transport Due to the high particle loadings, TIMs sometimes treated using models that are appropriate near or above the percolation threshold. Random Network Models Schematic Example of Percolation Predominant resistance to heat flow is constriction through particle-to-particle contacts; accurately A. Devpura, P.E. Phelan, R.S. Prasher, ITherm 2000. represented by resistance networks. See* *P.K. Vaitheeswaran, G. Subbarayan, J. Electron. Packag. 140 (2018). ME 511, Fall 2022, Purdue University 9 Predicting Bond Line Thickness Silicone-based particle-loaded TIMs have non-Newtonian behavior (typically behave as a Herschel–Bulkley (H–B) fluid that has a finite bond line thickness at some applied force). Prasher et al.* shows that bondline thicknesses predicted by H-B theory did not accurately predict the bond line and proposed an empirical correlation (70 kPa to 1.4 MPa): dBLT: bond line thickness τy 0.166 τy: yield stress dBLT=C P P: pressure *R.S. Prasher, J. Shipley, S. Prstic, P. Koning, J. Wang, J. Heat Transfer. 125 (2003) C: 1.31×10−4 meters 1170–1177. ME 511, Fall 2022, Purdue University 10 Predicting TIM Contact Resistances Contact resistance with the mating surfaces: σ: rms roughness kTIM