Metal Additive Manufacturing Powder/Wire Fed Systems PDF
Document Details
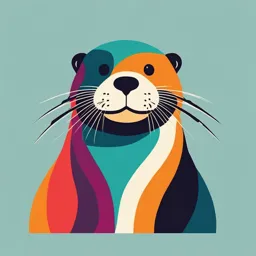
Uploaded by LuminousAllegory9463
IIT Kanpur
Dr. J. Ramkumar
Tags
Summary
This document presents a lecture on metal additive manufacturing (MAM), specifically focusing on powder feeders and delivery nozzles for direct energy deposition (DED) processes. The document discusses different types of powder feeders, such as mechanical wheel or screw feeders, gravity-based feeders, and fluidized bed feeders. It also touches upon wire-fed systems, positioning devices, and printheads in MAM.
Full Transcript
EL PT N Dr. J. Ramkumar Professor Department of Mechanical Engineering and Design IIT Kanpur ▪ Powder feeders and their classification EL ▪ Powder Delivery Nozzles ▪ Powder bed delivery and spreading system ▪ Wire Fed Systems...
EL PT N Dr. J. Ramkumar Professor Department of Mechanical Engineering and Design IIT Kanpur ▪ Powder feeders and their classification EL ▪ Powder Delivery Nozzles ▪ Powder bed delivery and spreading system ▪ Wire Fed Systems PT ▪ Positioning Devices ▪ Print-heads N ▪ The most significant pieces of equipment in a DED process are the powder feeders and delivery nozzles, which are essential EL to the delivery and deposition of the powders. ▪ A appropriate powder feeder is used to transport the powder during a typical powder-fed DED process, and a nozzle is ▪ PT subsequently used to deposit the powder onto the substrate. The fact that a carrier gas is given to move the powders from the feeders to the nozzles should also be noticed. N ▪ Powder flowability is influenced by the rheology, physical characteristics, size, and shape of the powder. ▪ Controlling the powder feed rate, which is based on the flow- EL ability of the used powders, is crucial for maintaining a stable powder stream. ▪ In order to precisely control the feed rate and produce a PT continuous and homogeneous powder stream during AM operations, various types of powder feeders have been developed. N 1. Classification of Powder Feeders EL 2. Powder Delivery Nozzles for DED 3. Powder Bed Delivery and Spreading Mechanisms 4. 5. PT Wire Feed System Positioning Devices and Scanners in Laser-Based AM N 6. Print-Head in Binder Jetting EL Powder feeders can be classified into the following classes: 1. Mechanical wheel or screw powder feeder 2. 3. PT Gravity-based Fluidized Bed Powder Feeder N 4. Vibratory-based powder feeder 1. MECHANICAL WHEEL OR SCREW POWDER FEEDER EL ▪ The mechanical wheel powder feeders consist of a container with a blade or screw operated at one end varying flow rates can be attained depending on the blade's arrangement. PT N Scheme of a mechanical wheel powder feeder E. Toyserkani, A. Khajepour, and S. Corbin, Laser cladding, 1st edition, CRC Press, 2004. https://doi.org/ 10.1201/9781420039177 1. MECHANICAL WHEEL OR SCREW POWDER FEEDER EL ▪ This kind of powder feeder can operate with a pressure differential between the inlet and outlet as low as zero and can handle powders of various sizes. ▪ PT Powders that are abrasive can wear down the blade, rising maintenance costs. For better and more consistent results, backpressure utilizing pressurized air or inert is N typically provided. 2. GRAVITY-BASED POWDER FEEDER ▪ Gravity causes powder particles with the right EL flowability to pass through an orifice in gravity feeders. By adjusting the orifice area, one can manage how much powder enters the delivery nozzle. ▪ PT Furthermore, external metering components can be added to achieve a high precision feed rate. N ▪ For instance, by adjusting the speed of a rotating disc with holes, a precise volumetric feed rate has been achieved. ▪ Based on this idea, other components of a similar nature have been created, replacing the rotating disc with a metering wheel or a lobe gear. 2. GRAVITY-BASED POWDER FEEDER EL PT N Schematic of gravity-based powder feeders with a rotating wheel for metering. E. Toyserkani, A. Khajepour, and S. Corbin, Laser cladding, 1st edition, CRC Press, 2004. https://doi.org/ 10.1201/9781420039177 2. GRAVITY-BASED POWDER FEEDER EL PT N Schematic of gravity-based powder feeders with a metering wheel. E. Toyserkani, A. Khajepour, and S. Corbin, Laser cladding, 1st edition, CRC Press, 2004. https://doi.org/ 10.1201/9781420039177 2. GRAVITY-BASED POWDER FEEDER EL PT N Schematic of gravity-based powder feeders with a lobe gear. E. Toyserkani, A. Khajepour, and S. Corbin, Laser cladding, 1st edition, CRC Press, 2004. https://doi.org/ 10.1201/9781420039177 3. FLUIDIZED BED POWDER FEEDER EL PT N Schematic of a fluidized bed powder feeder. E. Toyserkani, A. Khajepour, and S. Corbin, Laser cladding, 1st edition, CRC Press, 2004. https://doi.org/ 10.1201/9781420039177 3. FLUIDIZED BED POWDER FEEDER EL ▪ Based on a patent discovered from the fluidics principle, the fluidized bed powder feeder was created. ▪ The benefit of this powder feeder is that it doesn't use ▪ PT any mechanical components to deliver the powder, which lowers the cost of upkeep and part replacement. A very high coating quality is guaranteed by the uniform N and continuous powder stream. 3. FLUIDIZED BED POWDER FEEDER EL ▪ A specific volume of gas is delivered to a closed hopper that contains the powder as the basic operating principle. ▪ A filter at the bottom of the closed hopper diffuses the gas ▪ PT through the powder, fluidizing it. A pickup tube and a carrier gas are mounted on the top of the unit to deliver the fluidized powder under a shed and to N the feed hose, respectively. 4.VIBRATORY-BASED POWDER FEEDER EL ▪ It consists of a tray that oscillates at 50 or 60 Hz. The volume flow of the powder can be infinitely adjusted to ensure a steady-state powder flow as it moves from the hopper to the vibrating tray. PT N Schematic of a vibratory- based powder feeder. E. Toyserkani, A. Khajepour, and S. Corbin, Laser cladding, 1st edition, CRC Press, 2004. https://doi.org/ 10.1201/9781420039177 4.VIBRATORY-BASED POWDER FEEDER EL ▪ For better control of powder flow, some vibratory bed powder feeders have an oscillating tray with various plates arranged at various angles. ▪ PT With a ± 1%percent accuracy, the vibratory bed powder feeders can feed a variety of powders at speeds between 8 N and 2000 g/min. ▪ The interactions of powder particles with the laser beam, melt EL pool, and unmelted surfaces during LDED (powder-fed AM) are essential for the quality of the printed part. ▪ The type of nozzle, the angle between the powder delivery PT system and the deposition plate, and the diameter of the powder stream all have a significant impact on these interactions. N ▪ To ensure that the manufactured parts are of high quality, the appropriate nozzle must be chosen because it depends on the material and the manufacturing process. The delivery nozzles can have two different configurations: 1. Lateral EL 2. Coaxial PT N 1. LATERAL NOZZLE EL ▪ The powder is delivered from the side in the AM process when a later nozzle is used, and an inert gas that passes through the nozzle aids in the powder delivery stream while oxidation. preventing deposit PT N Schematic of a typical lateral nozzle. E. Toyserkani, A. Khajepour, and S. Corbin, Laser cladding, 1st edition, CRC Press, 2004. https://doi.org/ 10.1201/9781420039177 1. LATERAL NOZZLE EL ▪ The lateral nozzle's reliance on trajectory orientation is one of its problems. The way the power stream interacts with the melt pool will ▪ PT change if the lateral nozzle is fixed to the laser beam's axis and the trajectory is not linear. N ▪ Due to this problem, some businesses, including Optomec, have created a nozzle that has four lateral nozzles. 1. LATERAL NOZZLE As was mentioned in the previous section, the powder EL ▪ delivery system has a significant impact on the quality of AM-produced parts in terms of the powder stream diameter that must be deposited, the stability of the powder feed rate, the speed of the powder particles, and the uniformity of the powder's profile shape. PT N Powder feed profile characteristic E. Toyserkani, A. Khajepour, and S. Corbin, Laser cladding, 1st edition, CRC Press, 2004. https://doi.org/ 10.1201/9781420039177 1. LATERAL NOZZLE EL ▪ The powder stream profile could be described by a parabolic equation, according to research done using a different nozzle with different diameters. PT where d is the profile diameter at any z (mm). N λ is the powder profile's quality coefficient (1/mm), it is valid for a particular range where the powder stream is stable. d0 is the nozzle diameter (mm). z is the distance from the tip of the nozzle to the desired point (mm). 2. COAXIAL NOZZLE ▪ The coaxial nozzle has the same deposition rates in either direction and greater powder efficiency, which is the ratio of EL powder deposited on the workpiece to powder provided by the powder feeder at a particular time. ▪ A laminar powder stream at the nozzle outlet delivers a PT homogeneous powder stream and high-quality products. ▪ Focusing on the melt pool ensures optimum part quality and powder efficiency. N ▪ Choosing the correct nozzle tip can create laminar flow, powder stream patterns, and powder focus. ▪ Powder stream is shaped by a parabola. ▪ Unlike a lateral nozzle, the powder stream converges and then diverges. 2. COAXIAL NOZZLE EL PT N Schematic of a typical coaxial Powder stream at the nozzle nozzle. exit to a co-axial nozzle. E. Toyserkani, A. Khajepour, and S. Corbin, Laser cladding, 1st edition, CRC Press, 2004. https://doi.org/ 10.1201/9781420039177 EL ▪ In powder bed processes, a roller, wiper/Recoater, or doctor blade compacts a 20–100 μm layer of metal powder over the build platform. ▪ PT A laser beam melts the first layer of powder using a computer-generated path. N ▪ After the first laser scan, the build platform descends one layer, and a new powder layer is spread and selectively melted. Layer by layer, the part is made. ▪ The powder delivery system must maximize powder flowability, reduce particle clustering, and minimize shear forces. EL ▪ PBF is a complex process, so it's important to have homogenous powder thickness in each layer. ▪ Inert gases (argon and nitrogen) are introduced into the PT metal chamber to prevent oxidation of the melt pool and remove condensate. The density of LPBF parts depends on the speed of the N ▪ counter-rotating roller, roller properties, powder layer thickness, and powder particle size. ▪ Trail-and-error techniques, mathematical modelling, and simulation provide information on the compaction phenomenon. ▪ Recoaters can be soft or hard. EL ▪ Both spread powder particles evenly, but their interactions are different. Such differences affect the ‘compaction density’ of build chamber powders, which affects AM- ▪ made parts. PT Silicon, rubber, or soft carbon fiber are soft recoaters (e.g. brush recoater). N ▪ Due to its stretchability, the soft recoater behaves well in collisions with AM-built metal parts. EL PT N Illustration of a LPBF process system setup I. G. E. Gore, N. Branch, T. Roman, E. Orange, K. Wayne, and R. A. Gore, “United States Patent (19),” no. 19, 1998. This type of recoater may be ideal for concurrent additive EL ▪ manufacturing of different parts in the same build chamber. ▪ Hard recoaters made of HS steel or ceramic exert pressure ▪ PT on the powder bed. Unlike soft recoaters, this type prevents part deformation. When the recoater collides with a wrapped part, it jams or N parts are separated from the support structure and dragged across the powder bed. The latter damages the whole structure. EL ▪ Recoaters are useful when printing identical parts on the same platform. ▪ ▪ PT It may also increase build chamber compaction density, improving quality. Paralleling parts to the recoater can cause jamming. N ▪ For better recoater force distribution, they should be oriented around the Z-axis. ▪ In DED AM, a solid wire feedstock can be used instead of metal powders. The feedstock capture efficiency is 100%, and EL the deposit volume is the same as the feedstock wire. Powder- feed/bed and wire-feed processes have these features. ▪ Wire-feed EBF has a much higher deposition rate than ▪ PT powder-fed/bed. However, fabricated parts are less precise. In AM machines with a wire feeder, simple and complex geometries can be achieved. N ▪ However, the latter requires careful control of the process parameters, and it is not possible to obtain simultaneously high geometry accuracy and low porosity of the parts. EL ▪ Wire-based DED machines are used when pore-free parts and dimensional accuracy are not important criteria for production. Depending on the energy source used, wire-feed AM can be ▪ ▪ PT laser-based, arc welding-based, or electron beam-based. EBF is promising for aerospace applications because it can be N done in a vacuum. It is equipped with a wire feeder avoiding the use of powders difficult to be contained safely in low-gravity settings N PT EL EL PT N Schematic of a lateral wire-feed system equipped with EBM. Sciaky, “Sciaky’s Electron Beam Additive Manufacturing (EBAM®) Process.”[Online]. Available: https:// www.sciaky.com/additive-manufacturing/wire-vs-powder. ▪ This type of AM machine can have a lateral or coaxial wire feed system, which affects part quality. EL ▪ The second setup is Omni directional. ▪ The laser beam is split into three beams and focused on a circular focal point. ▪ the laser beam. ▪ PT The optical elements' precise location centers the wire feed in This configuration allows the wire to be fed into the center of the N laser-generated melt pool. ▪ Contact force must be kept constant to ensure AM part quality. ▪ Wire-fed AM isn't a good choice for smooth surfaces. ▪ This technology can't make complex parts. ▪ Making complex shapes may be difficult with a fixed contact force and a mobile feeding mechanism. EL PT N Schematic of a coaxial wire-feed system. “Durmat.”[Online]. Available: https://durmat.com/en/service/hard-facing / https://durmat.com/en/service/hard-facing ▪ AM machines make parts for various uses. The size of the EL machine and positioning of device elements limits the printing of large parts. ▪ Due to work-space constraints, the size and shape of objects to ▪ PT be printed are limited. CNC and robotic arms are used to handle the material delivery system or heat sources. N ▪ The positioning device should provide workspace, speed, and acceleration for building the parts. ▪ Positioning devices are connected to a controller that determines their movements, trajectories, speed, and accelerations. ▪ In laser powder bed fusion (LPBF), galvanometer scanners EL perform x and y laser scanning. ▪ A galvo system consists of a galvo motor, two mirrors controlled by the motor, and a "servo" driver board. Multiple coils in a ▪ PT magnetic field form Galvo DC motors. When a galvo motor senses an electric current flowing through a coil, it generates a torque proportional to the current, which N deflects the laser beam. ▪ A precision position detector on the shaft measures the mirrors' angular position for closed-loop servo control. ▪ Open-loop galvos are cheaper and less accurate than closed-loop galvos. EL PT N Schematic of a galvo scanner. Available: http://www.ii-vi.de/french/CO2-Laser-Optics/scanning-laser-system-optics.html. ▪ Powder Feeders and Delivery Nozzles Technology EL ▪ Wire fed systems ▪ CAD file formats and different software used for AM PT N ▪ Make a list of advantages and disadvantages of using an electron beam. EL ▪ Make a list of different types of nozzles used in the PBF process stating their advantages and disadvantages. PT N N PT EL EL PT N Dr. J. Ramkumar Professor Department of Mechanical Engineering and Design IIT Kanpur ▪ Manufacturing of metallic materials EL ▪ Conventional vs AM process ▪ Solidification of Metals ▪ Equilibrium and Non-equilibrium phases for solidification PT ▪ Theory and mechanism for solidification ▪ In equilibrium phase for AM ▪ In non-equilibrium phase for AM N ▪ Raw MAM printed parts 1. Conventional vs Additive Manufacturing EL 2. Conventional method 3. Additive manufacturing PT N EL PT N https://www.3deo.co/manufacturing/comparing-metal-parts-manufacturing-methods/ ▪ TECHNOLOGY COMPARISONS EL PT N https://www.3deo.co/manufacturing/comparing-metal-parts-manufacturing-methods/ TRADITIONAL VS AM SUPPLY CHAIN EL PT N https://www.stratasys.co.in/explore/blog/2018/business-considerations-for- production-tooling-conversion-to-additive-manufacturing 2. CONVENTIONAL METHOD ▪ Subtractive manufacturing EL PT N CONVENTIONAL METHOD ▪ Constant Volume Process EL Casting Forging No upper size limit in casting Mechanically stronger end weight PT Large amount of alloy choices product Better response to heat treatment N Tooling is less expensive Less need of expensive alloys Complicated parts are easier to Great wear and tear resistance manufacture 2. CONVENTIONAL METHOD ▪ Crushing, roasting, magnetic separation, flotation, and EL leaching are common beneficiation techniques. ▪ Melting and alloying are used to make metal ingots, which are then machined into parts and assembled. PT ▪ Casting involves melting metal alloys in a crucible. ▪ When a metal's heating temperature exceeds its freezing temperature, it melts. N ▪ Melting temperatures depend on the alloy composition. ▪ Heating above the melting point allows the alloy to cool throughout the pouring process. 2. CONVENTIONAL METHOD ▪ Once poured, the liquid metal quickly cools. EL ▪ Solidification begins when a metal's temperature drops below its melting point. ▪ As the temperature drops, the liquid metal loses energy PT and crystallization begins near the mould walls. ▪ These crystals will form grains in the final structure. After solidifying, the metal part is broken from the mould. N CONVENTIONAL MANUFACTURING PROCESSES: e.g., casting. EL PT N 3. ADDITIVE MANUFACTURING ▪ AM produces three-dimensional solid products from a EL digital model, unlike traditional fabrication methods. ▪ AM uses an additive method where materials are added in layers. PT ▪ Since 1995, AM has been able to produce metal components for engineered products and modern tech manufacturing. N https://www.mmsonline.com/articles/metal-additive-manufacturing-multitaskings-latest-trend 3. ADDITIVE MANUFACTURING EL ▪ AM metal powder manufacturing involves three steps: i. Mining and extracting ore to fabricate pure metal or alloy products (i.e., billet, ingot, and wire). PT ii. Powder production by either water atomization, plasma atomization, plasma rotate electrode process (PREP) atomization, rotating electrode process (REP) N atomization, gas atomization, or electrode induction melting inert gas atomization (EIGA). iii. Powder sorting, classification, and validation. 3. ADDITIVE MANUFACTURING Powder morphology: EL ▪ Powder morphology affects packing and flow. ▪ Spherical, regular, and equiaxed powders pack and PT organize better than irregular powders, but irregular powders flow well in many AM powder bed and powder- fed processes. N ▪ Powder morphology affects AM component density. Very spherical powders benefit AM processes, but this reduces the use of cheaper powder manufacturing methods. ▪ The more irregular the powder shape, the lower the product density, according to recent research. MANUFACTURING OF METALLIC MATERIALS EL 3. ADDITIVE MANUFACTURING Powder size: ▪ Powder size distribution is another crucial AM parameter. PT ▪ Depending on AM equipment, processes, and geometrical resolution, powder size is 15–100 μm. ▪ Powder size distribution affects layer thickness and AM N product detail. MANUFACTURING OF METALLIC MATERIALS 3. ADDITIVE MANUFACTURING EL PT N https://3dprintingindustry.com/news/incus-lithography-based-metal-3d-printing-technology-to-debut-at-formnext-2019-162753/ MANUFACTURING OF METALLIC MATERIALS EL AM powder production steps PT N J. Dawes, R. Bowerman, and R. Trepleton, “Introduction to the additive manufacturing powder metallurgy supply chain,” Johnson Matthey Technol. Rev., vol. 59, no. 3, pp. 243–256, 2015, doi: https://doi.org/ 10.1595/205651315X688686. SOLIDIFICATION OF METALS EL PT N https://www.dierk-raabe.com/laser-additive-manufacturing/ EL PT N https://www.dierk-raabe.com/laser-additive-manufacturing/ 3. ADDITIVE MANUFACTURING EL ▪ AM metal powder manufacturing involves three steps: i. Mining and extracting ore to fabricate pure metal or alloy products (i.e., billet, ingot, and wire). PT ii. Powder production by either water atomization, plasma atomization, plasma rotate electrode process (PREP) atomization, rotating electrode process (REP) N atomization, gas atomization, or electrode induction melting inert gas atomization (EIGA). iii. Powder sorting, classification, and validation. N PT EL SOLIDIFICATION OF METALS: EQUILIBRIUM ▪ After melting in conventional casting or laser/electron-beam AM, the liquid metal solidifies through cooling. ▪ Thermodynamically, solid and liquid have the same energy at their EL melting point, so both are steady. ▪ As the liquid metal cools, it loses latent heat. Low liquid temperature reduces the average interatomic space between movable and disordered atoms. PT ▪ As atoms cool, their interaction forces stop them from moving apart, N and the liquid turns solid. ▪ A large ingot of metal alloy is cast into a single crystal using a controlled solidification protocol. ▪ In practice, it's difficult to transform a homogeneous liquid into a perfect homogeneous solid. This requires knowledge at the angstrom, micron, meso, and macro levels. SOLIDIFICATION OF METALS: EQUILIBRIUM ▪ Angstrom-level atomic movement and conformation of the solid- liquid interface are important whether the crystal is growing or not. EL ▪ Also, crystal growth and nucleus formation should be studied. ▪ It's important to study the micron-level redistribution of solute if solid crystal structures have different chemical compositions than liquid. PT ▪ This can lead to undesirable segregation or extreme refinement of N solid, which must consider the situation where the solid/liquid interface becomes unstable and forms cellular or dendritic structures or crystal imperfections. ▪ Macro-level solidification knowledge is applied to heat and fluid flow in a liquid metal during cooling. SOLIDIFICATION IN ADDITIVE MANUFACTURING: NON-EQUILIBRIUM ▪ Since AM involves the rapid melting of metals, solidification theory is important for predicting and monitoring the process. EL ▪ Laser- or EB-based AM uses a moving heat source with a short interaction time. size. PT ▪ Laser powder bed fusion uses a 4 m/s laser with a 100 μm spot ▪ This means a 100 μm process zone is heated when its maximum N temperature can be reached in less than 25 μs. SOLIDIFICATION IN ADDITIVE MANUFACTURING: NON-EQUILIBRIUM Thermal Conductivity: EL ▪ Due to thermal conductivity, solidification and cooling can take twice as long as heating. ▪ Due to the substrate material, the surrounding heat cooling rates. PT conduction/convection regimes cause high solidification and ▪ The point heat source produces a highly localised heat flux in the N melt pool zone and a massive temperature gradient in the deposited layers. ▪ The substrate bottom has a higher temperature gradient than the deposited top. SOLIDIFICATION IN ADDITIVE MANUFACTURING: NON-EQUILIBRIUM Alloy Partition: EL ▪ During solidification, the alloy partition coefficient drops, rejecting solute atoms at the solid-liquid boundary. ▪ Solute concentration rises until the solution is stable. PT ▪ The solidification temperature at the solid-liquid boundary is affected by liquid composition, process speed, and boundary angle relative to the heat source centerline. N ▪ In AM, metallurgy is controlled by the chemistry of raw materials and the thermal history of the material during manufacturing. SOLIDIFICATION IN ADDITIVE MANUFACTURING: NON-EQUILIBRIUM Heat Transfer Mechanisms: EL ▪ LPBF and LDED may have different heat transfer mechanisms, but laser and EB AM have the same metallurgical principles for full melting. PT ▪ Cooling to ambient temperature after solidification controls the deposited layer's early phase distribution and grain morphology. ▪ Heat source speed, power, and size govern melt pool geometry, N which controls solidification kinetics. ▪ Thermal cycling and cooling control precipitation kinetics, phase growth, and grain growth. SOLIDIFICATION IN ADDITIVE MANUFACTURING: NON-EQUILIBRIUM AM vs casting solidification: EL ▪ In some cases, AM solidification differs from casting. ▪ For AM, the melt pool size ranges from hundreds of micrometres to millimetres, regardless of the final component size, and is PT therefore different from castings with larger melt pool areas. ▪ Small melt pools have less macrosegregation than larger castings. N ▪ In LPBF, the powder bed around the melt area has lower thermal conductivity (due to voids between particles) than bulk alloy material. SOLIDIFICATION IN ADDITIVE MANUFACTURING: NON-EQUILIBRIUM ▪ Laser and EB-AM processes can use a similar hypothesis. EL ▪ AM solidifies quickly. Metallic AM products undergo a complex thermal cycle, including: PT ▪ directional heat conduction, ▪ repeated heating and cooling, and ▪ rapid solidification. N SOLIDIFICATION IN ADDITIVE MANUFACTURING: NON-EQUILIBRIUM ▪ There are mainly two reasons for rapid solidification: EL 1. Enormous undercooling of the melt and 2. Fast-moving temperature fluxes. ▪ Rapid solidification is often accompanied by robust liquid ▪ These PT flow, such as Marangoni convection, which can reach 1–4 m/s. factors don't support the assumption that microstructural development and properties are the same as N conventional techniques. ▪ Rapid solidification reduces elemental partitioning, which extends solid solubility and causes metastable phases. SOLIDIFICATION IN ADDITIVE MANUFACTURING: NON-EQUILIBRIUM Heat conduction: EL ▪ Due to heat conduction, grain growth may be directional. ▪ Rapid and directional solidification and thermally-induced phase transformation affect the microstructure of deposited parts. PT ▪ Rapid solidification in the melt pool improves mechanical N properties by allowing more structural latitude than in conventional manufacturing. ▪ Undercooling liquid before nucleation and solidification growth rate cause these unique structures. SOLIDIFICATION IN ADDITIVE MANUFACTURING: NON-EQUILIBRIUM Cooling Rate: EL ▪ The cooling rate is vital to achieving the desired undercooling that eventually minimizes the increased temperature due to recalescence. ▪ Rapid PT solidification characteristics include microstructure refinement, increased solubility limits, reduced microsegregation, N and non-equilibrium metastable phase formation. ▪ Compared to standard casting methods, fast cooling reduces the formation of grains, lamellae, and second-phase particles. SOLIDIFICATION IN ADDITIVE MANUFACTURING: NON-EQUILIBRIUM EL ▪ Dendritic segregation can be reduced to achieve compositional homogeneity. ▪ AM solidification affects grain size, shape, distribution, PT growth kinetics, elemental segregation and precipitation, phase transformation, and material properties. N ▪ The key factors in this process are multiscale multiphysics phenomena (i.e., fluid flow, heat and mass transfer, beam interaction with the material) caused by AM's localized heating and cooling. EL PT N Fatoba, Olawale Samuel, Esther Titilayo Akinlabi, and Mamookho Elizabeth Makhatha. "Influence of rapid solidification on the thermophysical and fatigue properties of laser additive manufactured Ti-6Al-4V alloy." ALUMINIUM ALLOYS (2017): 181. EQUILIBRIUM SOLIDIFICATION THEORY AND MECHANISM Thermodynamics: ▪ Thermodynamics can analyze solidification kinetics. EL ▪ It evaluates alloy phase composition, solidification method, fundamental alloy properties, and solidus and liquidus line slopes. ▪ Pressure, temperature, and composition affect a material's free energy. PT ▪ When Gibbs free energy is low, equilibrium is reached. N ▪ Under the assumption of thermodynamic equilibrium, the equilibrium phase diagram can be used to estimate the solid and liquid alloy composition. ▪ A material's structure, a function of composition and temperature, can be identified from an equilibrium phase diagram using a slow transformation rate or a fast diffusion rate. EQUILIBRIUM SOLIDIFICATION THEORY AND MECHANISM COOLING CURVE AND PHASE DIAGRAM ▪ A cooling curve shows the EL phase transition temperature over time for pure metals or alloys as they cool. ▪ Pure liquid metal cools to its melting solidifying. point PT before N ▪ To understand the solidification of pure metals, a supercooling cooling curve Schematic of cooling curves during solidification is used, where the liquid metal cools from A to B. D. D. Gu, W. Meiners, K. Wissenbach, and R. Poprawe, “Laser additive manufacturing of metallic com- ponents: Materials, processes and mechanisms,” Int. Mater. Rev., vol. 57, no. 3, pp. 133–164, 2012, doi:https://doi.org/10.1179/1743280411Y.0000000014. https://www.3deo.co/manufacturing/comparing-metal-parts-manufacturing-methods/ EQUILIBRIUM SOLIDIFICATION THEORY AND MECHANISM COOLING CURVE AND PHASE DIAGRAM ▪ B and C must be undercooled. Since nucleation begins at point C, EL the liquid's temperature rises due to the latent heat of fusion. ▪ This is recalescence (from point C to D). From here, solidification continues at (Tm) until point E. PT ▪ The cooling rate indicates when the solid starts to cool. ▪ Based on the atomic configuration, solid and liquid metals have N different thermal conductivities. ▪ Different regions have different cooling curve slopes. ▪ Before solidification begins, the temperature falls below equilibrium cooling, known as "supercooling," to develop a thermodynamic driving force. EQUILIBRIUM SOLIDIFICATION THEORY AND MECHANISM COOLING CURVE AND PHASE DIAGRAM EL ▪ ‘Supercooling’ is also called ‘undercooling’, where the liquid temperature is lowered below the melting point without solidifying. ▪ Pure metal's cooling curve has zero slopes (constant temperature) PT N during solidification. Cooling curve for pure metals D. D. Gu, W. Meiners, K. Wissenbach, and R. Poprawe, “Laser additive manufacturing of metallic com- ponents: Materials, processes and mechanisms,” Int. Mater. Rev., vol. 57, no. 3, pp. 133–164, 2012, doi:https://doi.org/10.1179/1743280411Y.0000000014. EQUILIBRIUM SOLIDIFICATION THEORY AND MECHANISM COOLING CURVE AND PHASE DIAGRAM ▪ The alloy cools differently than pure metal as shown below. EL PT N Cooling curve for pure metals D. D. Gu, W. Meiners, K. Wissenbach, and R. Poprawe, “Laser additive manufacturing of metallic com- ponents: Materials, processes and mechanisms,” Int. Mater. Rev., vol. 57, no. 3, pp. 133–164, 2012, doi:https://doi.org/10.1179/1743280411Y.0000000014. EQUILIBRIUM SOLIDIFICATION THEORY AND MECHANISM COOLING CURVE AND PHASE DIAGRAM EL ▪ The alloy cools from a two-phase region, and solid precipitates are delayed in liquid through a ‘mushy’ zone. ▪ Metal alloys show a mushy zone between solidus and liquidus PT N temperatures, where solid and liquid phases concur during solidification. Mushy Zone D. D. Gu, W. Meiners, K. Wissenbach, and R. Poprawe, “Laser additive manufacturing of metallic com- ponents: Materials, processes and mechanisms,” Int. Mater. Rev., vol. 57, no. 3, pp. 133–164, 2012, doi:https://doi.org/10.1179/1743280411Y.0000000014. EQUILIBRIUM SOLIDIFICATION THEORY AND MECHANISM COOLING CURVE AND PHASE DIAGRAM EL ▪ Alloy cooling curves at different compositions. PT N Set of cooling curves to construct binary phase diagram. D. D. Gu, W. Meiners, K. Wissenbach, and R. Poprawe, “Laser additive manufacturing of metallic com- ponents: Materials, processes and mechanisms,” Int. Mater. Rev., vol. 57, no. 3, pp. 133–164, 2012, doi:https://doi.org/10.1179/1743280411Y.0000000014. EQUILIBRIUM SOLIDIFICATION THEORY AND MECHANISM COOLING CURVE AND PHASE DIAGRAM EL ▪ This region of the curve is non-linear due to the evolution of latent heat caused by the solidification process. ▪ The temperature from which the slope first deviates PT corresponds to the formation of the first solid and is called the liquidus temperature. N ▪ The alloy solidifies below the solidus temperature. EQUILIBRIUM SOLIDIFICATION THEORY AND MECHANISM EL COOLING CURVE AND PHASE DIAGRAM PT N Fe–C phase diagram D. D. Gu, W. Meiners, K. Wissenbach, and R. Poprawe, “Laser additive manufacturing of metallic com- ponents: Materials, processes and mechanisms,” Int. Mater. Rev., vol. 57, no. 3, pp. 133–164, 2012, doi:https://doi.org/10.1179/1743280411Y.0000000014. EQUILIBRIUM SOLIDIFICATION THEORY AND MECHANISM COOLING CURVE AND PHASE DIAGRAM EL ▪ A phase diagram shows how phases form and transform during heating and cooling with different alloy compositions. ▪ DifferentC contents affect alloy phase transformation temperatures. PT ▪ Optimizing AM process parameters and microstructure can help. N ▪ During laser-based AM stainless steel production, the laser input temperature must be optimized to control austenite and ferrite formation. EQUILIBRIUM SOLIDIFICATION THEORY AND MECHANISM COOLING CURVE AND PHASE DIAGRAM EL PT N Continuous cooling transformation diagram for steel. D. D. Gu, W. Meiners, K. Wissenbach, and R. Poprawe, “Laser additive manufacturing of metallic com- ponents: Materials, processes and mechanisms,” Int. Mater. Rev., vol. 57, no. 3, pp. 133–164, 2012, doi:https://doi.org/10.1179/1743280411Y.0000000014. EQUILIBRIUM SOLIDIFICATION THEORY AND MECHANISM COOLING CURVE AND PHASE DIAGRAM EL ▪ The continuous cooling transformation (CCT) diagram shows the phases that form in alloys at different cooling rates. ▪ Each deposited layer undergoes repeated thermal cycles and PT has different cooling rates in AM. ▪ At fast cooling rates, a complete martensitic structure forms, while bainite, ferrite, and pearlite form at slower rates. N ▪ In AM, the CCT diagram can be used to estimate phase formation when the thermal profile of each deposited layer is known. NON-EQUILIBRIUM SOLIDIFICATION EL PT N Time–temperature profile of a single-layer AM-manufactured Ti-6Al-4V alloy. W. E. Frazier, “Metal additive manufacturing: A review,” J. Mater. Eng. Perform. 2014, doi: https://doi.org/10.1007/s11665-014-0958-z. NON-EQUILIBRIUM SOLIDIFICATION THEORY AND MECHANISM ▪ Heating and cooling can cause suppressed phase changes or supersaturated phases during AM solidification. EL ▪ In AM, when every layer undergoes a repeated heating and cooling cycle, the temperature may exceed the phase transformation temperature. ▪ This PT causes multiple phase microstructure, and residual stress. transformations, intricate ▪ For example, a typical thermal profile for a single-layer Ti-6Al-4V N alloy manufactured in AM. ▪ The time-temperature profile fluctuates and reaches phase- change temperatures, causing phase change. ▪ Knowledge of phase transformation during fast solidification and repeated thermal cycles is essential for controlling microstructure in AM parts. NON-EQUILIBRIUM SOLIDIFICATION THEORY AND MECHANISM ▪ AM process optimization involves ▪ Equilibrium and non-equilibrium phase diagrams, EL ▪ Thermodynamics, ▪ Thermo-physical quantities, ▪ Laser/EB material interaction, PT ▪ Diffusion kinetics, etc. ▪ During rapid cooling, some phases that form under equilibrium N conditions may not form, causing metastable phases. ▪ Figure on the next slide compares the Ti-6Al-4V CCT diagram for standard casting and AM techniques. In AM, the alloy cools faster, forming a metastable martensitic structure. NON-EQUILIBRIUM SOLIDIFICATION THEORY AND MECHANISM EL ▪ Characteristics of metastable phases depend on alloy chemical structure and cooling method thermal behavior. PT N Time–temperature diagram presenting the nucleation onset of two dissimilar theoretical phases with unlike cooling behaviors. NON-EQUILIBRIUM SOLIDIFICATION THEORY AND MECHANISM ▪ From the time–temperature diagram, at cooling rate T1, the primary phase is nucleated as phase I, whenever at faster EL cooling rate T2, (T2 >> T1), another phase, phase II is nucleated by detouring phase I. ▪ Figure on the next slide shows a phase diagram with phase δ at equilibrium. PT ▪ Due to rapid cooling, a dashed metastable phase diagram may N be created. NON-EQUILIBRIUM SOLIDIFICATION THEORY AND MECHANISM EL PT N A comparative presentation of the theoretical equilibrium (solid lines) and metastable non-equilibrium phase diagram (dotted lines). ▪ AM Manufactured components after cooling just after being taken out from the built chamber without any post-processing. EL PT N https://www.twi-global.com/what-we-do/research-and-technology/technologies/additive-manufacturing ▪ Compare Manufacturing of metallic materials with rest to Conventional vs AM processes. EL ▪ Understand and write a note on solidification of metals. ▪ Compare Manufacturing of metallic materials with rest to Conventional vs AM processes. PT ▪ Understand and write a note on solidification of metals. ▪ What are the differences between equilibrium and non- equilibrium phases for solidification? N ▪ Explain the mechanism for solidification in equilibrium and non- equilibrium phases for AM. ▪ Understand and draw different cooling curves for pure metals and alloys ▪ Raw MAM printed parts N PT EL ▪ 1. Iron-Carbon EL ▪ 2. Aluminum alloy ▪ 3. Titanium alloy ▪ 4. Nickel alloy PT N A1: The upper limit of the ferrite/cementite phase field EL (horizontal line going through the eutectoid point). A2: The temperature where iron loses its magnetism (so- called Curie temperature). PT A3: The boundary between the γ austenite and the austenite/ ferrite field. A4: The point in this case where α changes to δ at high temperatures. N ACM: The boundary between the γ austenite and the austenite/cementite field. https://www.tf.uni-kiel.de/matwis/amat/iss/kap_6/illustr/s6_1_2.html N PT EL EL α: α-Ti, β: β-Ti, α2: Ti3Al, γ: TiAl, PT ε: TiAl3, L: liquid N Han, Q., and S. Viswanathan. "Analysis of the mechanism of die soldering in aluminum die casting." Metallurgical and materials transactions A 34.1 (2003): 139-146. High-pressure solidification EL produces grey, white, and black phases. Al3Ni is grey, α-Al is black, and Al3Ni2 is white. When the peritectic reaction PT cannot be carried out due to the primary phase's incapacity to touch the liquid phase, The growth of the peritectic phase can only be achieved through solid N phase diffusion (peritectic transformation) and direct solidification from the undercooled liquid phase. Wang, Xiaohong, et al. "Study on the Phase Selection and Debye Temperature of Hyper-Peritectic Al-Ni Alloy under High Pressure." Metals 11.1 (2021): 84. EL PT N https://www.scielo.org.mx/scielo.php?script=sci_arttext&pid=S1870-249X2016000200067 N PT EL N PT EL