MAE 1351 Summary (1) PDF
Document Details
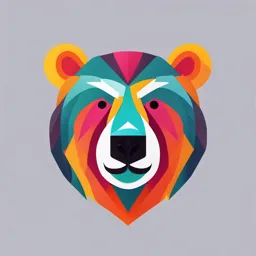
Uploaded by HandsomeOnyx7940
Ole Miss
Tags
Summary
This document provides a summary of engineering graphics, covering key concepts, historical development, and recent advancements. It explores the role of engineering graphics in communication, record-keeping, and analysis within the engineering field. Includes information regarding engineering definitions and the historical context of engineering graphics.
Full Transcript
1.2 Key Concepts Engineering Graphics: A specialized tool used by engineers to communicate, document, and analyze ideas and designs. The Role of Engineering Graphics Communication: Conveying concepts without words. Record Keeping: Documenting ideas for future reference....
1.2 Key Concepts Engineering Graphics: A specialized tool used by engineers to communicate, document, and analyze ideas and designs. The Role of Engineering Graphics Communication: Conveying concepts without words. Record Keeping: Documenting ideas for future reference. Analysis: Assessing shapes, sizes, and other critical variables in engineered systems. Historical Development of Engineering Graphics Ancient to Medieval Periods Cave Paintings: Early forms of graphical communication. Egyptian and Native American Pyramids: Notable large structures requiring precision and planning. Roman Engineering: Developed techniques such as the Roman arch and structured roads for military and civil use. Renaissance Advancements Leonardo da Vinci's Drawings: Represented innovative ideas and proposed devices, emphasizing the importance of accurate graphic representation. Descriptive Geometry: Developed by Gaspard Monge for analyzing complex structures and facilitating more precise engineering designs. The Industrial Revolution Transition to Mechanical Engineering: Resulted from the military weapon demand. Introduction of mass production techniques, leading to standardized designs. Modern engineering drawings evolved, incorporating multiple views, precise sizes, and production specifics. Recent Advancements in Engineering Growth of disciplines such as Electrical Engineering, Chemical Engineering, Industrial Engineering, and new fields like Bioengineering, MEMS, and Nano- engineering. Engineering Dynamics Collaborative efforts among various disciplines are essential for large-scale projects, reflecting the integrated nature of modern engineering challenges. Summary & Key Takeaways Engineering graphics is crucial for communication, record-keeping, and analysis in the engineering field. Historical developments highlight a progression from simple forms of communication to complex engineering drawings and modern technical standards. Recent advancements have necessitated interdisciplinary collaboration to address the complexities of current engineering challenges. NOTE Objectives of Engineering Graphics After completing the chapter, students should be able to explain how engineering graphics is a vital tool for engineers. Students will learn to define and illustrate the use of engineering visualization, modeling, and graphics in engineering practices. A historical perspective on the development of engineering graphics will be provided, highlighting its evolution over time. Historical Context of Engineering Graphics Engineering graphics has a rich history that reflects technological advancements and changing methodologies over time. The method of graphical communication has transformed considerably, adapting to new tools and techniques, making it crucial for effective engineering. Ancient History of Graphical Communication The earliest graphical communication examples include cave paintings depicting organized social behavior and tool usage, although they lack detailed fabrication instructions. Significant large structures like the Egyptian pyramids and Native American pyramids highlighted the need for precise planning and construction, showcasing early engineering principles. Engineering Definitions and Roles of Graphic Communication Engineering is defined as the application of scientific knowledge to develop materials and systems for human benefit, stemming from the Latin "ingenerare." Engineering graphics serves three primary roles: communication of concepts accurately, record-keeping of designs, and supporting analysis of engineered systems. Modern engineering relies on advanced tools like computers and three-dimensional modeling for effective design and visualization. Medieval Period Engineering Innovations The medieval architectural innovations, such as the flying buttress, allowed for larger, more complex buildings like cathedrals. The construction methods of the Roman arch and roads facilitated the expansion of the Roman Empire, showcasing effective design and functional engineering. Diagrams of structures like windmills reflected the application of engineering principles to enhance agricultural productivity in Europe and Asia. The Renaissance and Advancements in Engineering The Renaissance marked a significant shift toward empirical observation and mathematical reasoning in predicting physical system behaviors. Leonardo da Vinci’s contributions to drawing and conceptualization of devices were pivotal, even if some proposals lacked practical viability. Advancements in fortification design during this period required more complex geometrical understanding and led to the development of descriptive geometry. The Industrial Revolution's Impact on Engineering The Industrial Revolution necessitated the transition from bespoke craftsmanship to mass production, requiring standardized designs and engineering drawings. The need for effective communication among varied skill sets prompted the development of precise engineering drawings, which depicted essential sizes and specifications. Patents emerged as a critical component of innovation, with distinct differences between patent drawings and formal engineering designs. Emergence of Specialized Engineering Disciplines The late 19th and early 20th centuries saw the birth of electrical, chemical, and manufacturing engineering in response to industrial needs. Recent decades introduced diverse fields such as bioengineering and nano-engineering, requiring interdisciplinary collaboration for complex projects. Modern engineering projects, such as space exploration, showcase the necessity of multi- disciplinary skills working together effectively. 1.4-5 Key Concepts Concurrent Engineering Definition: A collaborative approach where engineers from all project phases participate early in the design process. Example: Manufacturing engineers advise on part designs to facilitate easier fabrication while also designing necessary tools concurrently. Benefits and Drawbacks Advantages: Reduced product development time. Disadvantages: Significant design errors lead to costly changes in production tooling. Engineering Graphics Technology Definition: The use of instruments to create precise engineering drawings, enhancing design accuracy and communication. Historical Context: Up to the Renaissance, drawings were hand-made, often leading to distortion due to lack of standardized measurements. Instrumentation in Drawing Instruments: Straightedges, compasses, protractors, drafting boards, etc. Instrument Purpose Drafting Board Flat surface for alignment T-square For drawing horizontal and vertical lines Protractor Measuring angles Compass Creating arcs and circles Transition to CAD Computer-Aided Drawing (CAD): Emergence in the 1970s, allowing for easy data storage, precise drawings, and data manipulation. Workstation Development: Freestanding computer-drawing stations made software affordable and user-friendly. Solid Modeling Definition: A form of computer modeling that allows engineers to visualize parts and assemblies in 3D. Parametric Design: Linking features to variables for easy modifications. Graphics as Analysis Tools Finite Element Analysis (FEA): Evaluating mechanical properties and stress distributions within models. Presentation Techniques Graphical Data Representation: Use of charts and graphs to communicate technical data effectively. Modern Role of Engineering Graphics Historically pivotal for communication and documentation of designs, the field has evolved with technology to enhance functionality and efficiency in engineering tasks. Summary & Key Takeaways Concurrent Engineering facilitates early-stage collaboration, reducing product development time but may incur costs due to design errors. Engineering Graphics Technology has shifted from manual instruments to powerful CAD systems, maintaining precision while improving communication efficacy. Solid Modeling allows for comprehensive visualization and manipulation, enhancing understanding during the design process. Modern engineering graphics focus on visualization skills, analysis through FEA, and effective communication of complex data via charts and graphs. NOTE Concurrent Engineering Concurrent engineering involves collaboration among engineers from all phases of a project, allowing for early involvement of manufacturing engineers with designers. For instance, a manufacturing engineer may suggest modifications to a part's design to facilitate easier fabrication. While the integration of multiple engineering disciplines can expedite product development, significant design errors can be costly due to necessary changes in production tooling. Engineering Graphics Technology The advancement of mechanical drawing instruments has significantly enhanced the precision and reproducibility of engineering graphics, reducing distortion and aiding accurate analyses. Prior to the Renaissance, drawings were handmade, often leading to distortions reliant on the draftsman’s skill. Early drawings were primarily two-dimensional (2-D), making depth representation challenging. Italian polymath Leonardo da Vinci was adept at creating more accurate depth representations, but standard units of measurement were not established until later, complicating the interchangeability of parts. Instrument Drawing The first drawing instruments included straightedges, compasses, dividers, and protractors; these were often custom-made and not widely available until the Industrial Revolution. Standardized units and precise drawings enabled different manufacturers to produce interchangeable parts. The introduction of quality drawing instruments improved dramatically through the late 20th century, culminating in the 1970s when they became widely adopted. The Computer Revolution The 1970s saw major developments in computer-aided drawing (CAD), which offered advantages like data storage and easy modifications, yet the transition from traditional tools was gradual. Nonetheless, as personal computers proliferated in the 1980s, CAD systems became more affordable and user-friendly, leading to a swift shift from drafting boards to CAD software. Notable CAD software like Autodesk’s AutoCAD played a crucial role in popularizing computer graphics among engineers and small companies. Graphics as a Design Tool The 1980s marked the beginning of computer-based 3D modeling, moving beyond 2D CAD drawings to solid models that convey true object geometry. This innovation allowed engineers to visualize parts and assemblies in three dimensions, facilitating a better understanding of fit and function. Solid modeling’s capacity for dynamic viewing and parametric design further enhanced engineers' ability to manipulate designs efficiently. Graphics as an Analysis Tool Before inexpensive digital tools made numerical analysis feasible, many mathematical problems were traditionally addressed through graphical techniques. Despite diminished usage in mechanical engineering, descriptive geometry continues to find applications in large-scale civil projects. Solid modeling has improved the analysis of mechanical properties, including calculating volume and mass, particularly for complex geometries. Graphics as a Presentation Tool Engineers must accurately present technical data derived from both empirical results and analytical calculations, often using charts and graphs. Three-dimensional modeling software can also create geometric models for finite element analysis (FEA), which visually represents engineering data like stress distribution. Effective communication of engineering data is essential, and visual tools like stress contour plotting significantly enhance understanding. The Modern Role of Engineering Graphics Engineering graphics is essential for communicating design ideas and technical information. Modern graphics allow for rapid creation and manipulation of 3D models. The recording and transmission of design histories have shifted from physical hard copies to electronic files, which are easier to manage and share. The focus of modern engineering graphics education emphasizes visualization, analysis, and optimization of designs over traditional drawing techniques, encouraging hands-on experiences and sketching to develop spatial reasoning. Glossary of Key Terms Assembly: A collection of parts that work together for specific functions. CAD: Computer-aided drawing systems that facilitate the creation and storage of engineering drawings. Descriptive Geometry: Techniques for analyzing three-dimensional objects through two- dimensional drawings. Solid Modeling: A three-dimensional visualization method used for parts and assemblies in various engineering disciplines. Visualization: The ability to mentally manipulate and envision designs in three dimensions. Chapter Summary Engineering graphics has become increasingly vital with advancements in tools and technology enabling fast, accurate communication, visualization, and analysis. New computer-based technologies allow engineers to focus on functionality and design optimization, with a shift in responsibility towards data management and model accuracy in engineering tasks. 5.4 The Engineering Design Process Overview The engineering design process is a multistep approach used to develop new products or improve existing ones. While the sequence may vary, the essential stages typically involve: 1. Identify: Define the need or problem. 2. Conceptualize: Generate innovative ideas. 3. Prototype: Create models to visualize concepts. 4. Analyze: Evaluate designs for feasibility. 5. Document: Prepare detailed drawings for production. 6. Produce: Manufacture or construct the final product. 7. Iterate: Revise based on findings. This process is often non-linear, allowing designers to revisit and refine earlier stages as necessary. Stages of the Design Process Stage 1: Problem Identification Purpose: Establish a clear need for the product. Activities: o Conduct market surveys. o Address the problem from both the client and engineer's perspectives. Example: A county requests a new water distribution system, specifying functional needs. Stage 2: Concept Generation Purpose: Brainstorm creative solutions. Activities: o Use methods such as brainstorming and sketching. o Focus on quantity over quality initially to maximize ideas. Outcome: Selection of main ideas for further development. Stage 3: Concept Selection and Refinement Purpose: Identify final concepts for design. Activities: o Employ a weighted decision table to evaluate options based on attributes like aesthetics and ergonomics. o Refine ideas using 3D modeling for better visualization. Example: Using a scoring system to compare design attributes among prototypes. Stage 4: Design Evaluation and Analysis Purpose: Validate design concepts through analysis. Activities: o Utilize numerical methods to assess mechanical properties and performance using simulation. o Perform various tests (e.g., FEA for stress analysis). Tools Used: CAD software for computational analysis. Stage 5: Physical Prototyping Purpose: Create tangible models of the design. Activities: o Construct scale models or prototypes via CNC machining or 3D printing. Benefit: Enhances understanding of form and function. Stage 6: Design Documentation Purpose: Provide detailed drawings needed for production. Activities: o Create blueprints that convey essential manufacturing information. o Include dimensions and tolerances critical for production accuracy. Stage 7: Production Purpose: Transition from design to actual manufacturing or construction. Activities: o Implement various fabrication methods such as machining or casting. o Document changes through as-built drawings reflecting actual construction. Relevance: Ensures operational continuity and aids future maintenance. Key Terms Life Cycle: The duration a product is designed to be effective before replacement. Green Engineering: Incorporates environmental considerations throughout the design process. Summary & Key Takeaways The design process is iterative, often requiring repetition of stages. Each stage serves a purpose—from identifying needs to production. Documentation is critical for ensuring design intent is preserved through manufacturing. Understanding the perspective of both customers and engineers is vital for successful design outcomes. NOTE Engineering Design Process Overview The engineering design process is a multi-step process, but the exact number of stages can vary based on different interpretations. It typically follows a sequence from identifying the problem to producing the final product, but the steps may not always be linear. A design team may need to revisit earlier steps if significant problems arise during later stages. The stages mentioned are not definitive; different textbooks may outline alternative names and numbers of stages. The overall understanding of the design process is more critical than memorizing the specific stages and labels. Stages of the Engineering Design Process **Stage 1: Problem Identification** **Stage 2: Concept Generation** **Stage 3: Concept Selection and Refinement** **Stage 4: Design Evaluation and Analysis** **Stage 5: Physical Prototyping** **Stage 6: Design Documentation** **Stage 7: Production** 6.4-6 A Parametric Solid Model Overview Creating a parametric feature-based solid model involves utilizing solid modeling software on a capable computer. Users interact with a graphical user interface (GUI) that displays the model in a 3-D context, allowing manipulation of the object. Initial Setup When beginning a new model, the software presents: 3-D Cartesian Coordinate System: x-, y-, and z-axes. Modeling Planes: Principal viewing planes aiding visualization. Sketch Creation 2-D Sketching: Most solid modeling begins with sketches on the modeling planes. Sketching Editor: Automatically rectifies sketches to enforce horizontal or vertical orientations. Valid Profiles To create a solid feature (extrusion or revolution): Closed Loop Requirement: The profile must be a closed loop, without overlapping or gaps. Solid Creation Processes 1. Extrusion: A profile is pulled straight out to create a solid. a. Requires specification of the profile's geometry and extrusion length. b. Resulting solid is bounded by the surfaces of the extruded profile. 2. Revolution: The profile is rotated about an axis. a. The rotation can be about an edge within the profile or offset from it. b. Geometry of the profile and the angle of rotation need to be defined. Precision in Modeling Feature Specification: All features must be explicitly defined before analysis or fabrication. Orientation: Placement of sketches relative to the coordinate system influences the solid's orientation. Constraints in Sketches Geometric Constraints: Govern relationships between points, lines, and curves. o Examples include: ▪ Coincident: Forces points to coincide. ▪ Tangent: Ensures curves or lines meet tangentially. ▪ Equal Length: Forces line segments to be the same length. Dimensional Constraints Defined measurements to control position and size of sketch entities: Linear Constraints: Measure distances or segment lengths. Radial/Diametral Constraints: Define radii or diameters. Angular Constraints: Specify angles between non-parallel lines. Constraint Uniqueness Several different constraint sets can yield the same geometry. The choice of constraints depends on: Design intent Future model modifications Analysis and manufacturing considerations Associative Constraints Utilizes algebraic relationships among dimensional constraints, allowing for automatic updates of dependent dimensions when driving dimensions change. Combining Profile Constraints A complete profile is achieved by a combination of geometric and dimensional constraints. Special attention is required to prevent over- or under-constraint situations. Features and Complexity Features: Distinctive geometric shapes that make up the model, such as holes or protrusions. o Utilizing sketches on any planar surface allows more complex modeling beyond basic extrusions and revolutions. Extrusion and Cut Options Different termination options for extrusions include: Blind Extrusion: Extends to a specified length. Extrude to Next Surface: Stops at the next encountered surface. Through All: Extends through all solid features. Double-Sided Extrusion: Extends in both directions from a profile. Practical Application Example L-Bracket Design: Adjusting dimensions while maintaining constant material thickness through appropriate constraints. Summary & Key Takeaways Parametric modeling emphasizes precise constraints for geometry control. Profile creation requires careful sketching and a closed-loop design. Various extrusion and revolution techniques cater to diverse modeling needs. Understanding constraints is crucial for achieving desired outcomes and robust designs. NOTE Creating a Parametric Solid Model To create a parametric feature-based solid model, solid modeling software and a capable computer are required. The software displays a 3D image of the object, viewable from multiple angles, facilitating interaction via a graphical user interface (GUI) with various tools available. New models typically open with a 3D coordinate system and principal modeling planes (XY, YZ, XZ) to aid in visualizing the modeling space. Solid modelers utilize 2D sketches as the foundation for creating solid features, usually performed on the modeling planes with a sketching editor similar to 2D CAD software. Sketching and Profile Creation Sketches start without precise dimensions; the sketching editor corrects orientations, enhancing accuracy (e.g., almost vertical or horizontal lines are adjusted to true vertical or horizontal). A valid profile must be a closed loop; issues such as extra lines, gaps, or overlaps in profiles may lead to geometric errors in models. A solid model can be created from a closed profile using methods like extrusion or revolution, where the profile can be extended or rotated around an axis to form three-dimensional shapes. Key Processes in Modeling Extrusion involves pulling the profile straight out of the sketching plane to form a solid, requiring both profile geometry and extrusion length to be defined. Revolution simulates shapes like vases, created by rotating a profile around an axis; care must be taken to ensure profiles do not cross the axis of rotation to avoid errors. Constraints in Solid Modeling Before fabrication or analysis, models need specifications for sizes and locations of all features, necessitating the orientation and placement of sketches within the coordinate system. Geometric constraints control the relationships among sketch entities, including coincidences, parallelism, and symmetry; these constraints can be implicitly or explicitly defined within the modeling software. Dimensional constraints specify sizes and positions of sketch entities using units of measurement like millimeters or inches, including linear, radial, diametral, and angular types. Managing Constraints The relationship between geometric and dimensional constraints is not unique; multiple constraint sets can yield the same sketch geometry. This complexity impacts how models respond to future changes. Associative or algebraic constraints can link dimensional constraints together, allowing dynamic updates to related dimensions as one is altered. Strategies for applying constraints begin with "ground constraints," which fix the geometry in space and set the foundation for other constraints to be built around. Advanced Techniques and Protrusions More complex models can be created by adding or subtracting material from the original model using protrusions (adding material) and cuts (removing material). Protrusions and cuts require fully defined profiles using constraints and can be located on any planar surface of the existing model, rather than being restricted to basic models' planes. The profile for protrusions or cuts must ensure new edges or vertices are aligned with the surfaces being used for sketching; strategically, coincident constraints are commonly applied. Examples of Modeling Techniques Figures illustrating various techniques (e.g., extrusion cuts, revolved protrusions) help visualize the applications of these methods. Common options for defining extrusion length include blind extrusions, which create features to a specified length or depth. Changing dimensional constraints dynamically alters the geometry of the model, emphasizing the advantages of parametric modeling, which allows flexibility in design intent and modifications. Practice Exercises A practice exercise involves applying geometric constraints to a rough sketch to develop a fully constrained profile, correlating concepts learned in dimensional and geometric constraints to real modeling scenarios. 6.7-8 Key Concepts Features in Solid Modeling Definition: Features are distinctive geometric shapes in a model, analogous to features on a face (e.g., eyes, nose). Importance: Recognizing features is foundational in solid modeling, as they define the part’s geometry and functions. Base Feature Description: The initial shape from which other features are derived; represents the part's overall geometry. Creation: Identified through a process of studying the part and can use extrusions or rotations for base definition. Form Features Purpose: Areas on the part with specific functions or manufacturing processes. Geometric Relationships: Often include constraints or relations among the shapes within the feature. Common Types of Features Rounds, Fillets, and Chamfers: o Rounds: Smooth radius transitions on external edges. o Fillets: Smooth transitions on internal edges. o Chamfers: Angled cuts at intersections of surfaces. Holes: Variants such as blind, through, tapped, counterbored, and countersunk holes are standard in part designs. Shells Definition: Removing most interior volume to create thin-walled shapes utilized for cases and containers. Ribs and Webs Ribs: Thin protrusions added for support and stiffening. Webs: Thin materials connecting heavier parts. Datums in Modeling Types: Points, axes, and planes used to define and assist in the creation of complex shapes. Examples: o Datum Point: Defined at vertices or specified distances from edges. o Datum Axis: Created between points or along edges. o Datum Plane: Formed through non-collinear points or offset from existing surfaces. Arrays and Mirrored Features Feature Array: Replicates a master feature across specified spacings. Mirrored Features: Creates duplicates by reflecting across a defined plane. Advanced Features: Blends and Sweeps Blends: Complex transitions between at least two sketches, requiring equal vertices for smooth transitions. Sweeps: Created by extruding a profile along a defined non-linear path, such as a helical trajectory for springs. Cosmetic Features Description: Surface-modifying features like threads and knurls that enhance appearance without altering object size or shape. Understanding Features and Functions Engineers must familiarize themselves with features to ensure effective communication and integration of engineering functions into models. Process Illustrations Protrusion Examples: Various figures provide visual guidance on creating complex protrusions and cuts using sketches on different planes. Summary & Key Takeaways Features define geometry in solid modeling and are critical for designing functional parts. A solid model begins with identifying the base feature and adding functional features like holes, ribs, and aesthetic enhancements. Familiarity with operations such as shelling and using denser geometric constructs like datums aids in creating intricate designs. Leveraging arrays and mirrored features contributes to efficient modeling practices. NOTE Features in Solid Modeling Features in solid modeling are geometrical shapes that define the distinct characteristics of a manufactured part. They are integral to the model and include various protrusions and cuts on the main body. Examples of features include simple holes such as cylindrical cuts that serve specific functions, like receiving fasteners (bolts or screws). Features can also be complex arrangements of shapes, as seen in gear teeth or turbine blades, necessitating the designer to both identify and incorporate these into the model effectively. Base Features Every solid model begins with a base feature, which is the fundamental shape that defines the overall structure of the part. Selection of the base feature is critical as it should encompass the most functional detail that can be created utilizing a single extrusion or rotation. After establishing the base feature, additional form features can be added or subtracted to modify the shape of the part as needed. Edge Transitions (Chamfers, Rounds, and Fillets) Edge transitions such as rounds, fillets, and chamfers are vital for ensuring smoothness and safety on manufactured parts. Rounds create a smooth transition on external edges while fillets soften internal edges. Both rounds and fillets are characterized by their radius size, while chamfers involve an angled cut providing alternate edge transitions. Practical applications include using fillets on internal edges to minimize break risk and using rounds or chamfers on external edges to reduce sharpness that can lead to injuries. Types of Holes in Modeling Holes are prevalent in many manufactured parts and can be modeled as various types, including blind, through, tapped, counterbored, and countersunk holes. The design of a countersunk hole, for instance, can be achieved using revolved cuts or standard hole features, simplifying the modeling task. Utilizing built-in hole features in solid modeling software optimizes the process by incorporating required geometry without needing extensive manual definition. Shells in Solid Modeling Shelling is a technique that removes most of the internal volume from a solid model, maintaining a thin wall that mirrors the external shape of the part, such as a soda bottle. The shell typically has a constant wall thickness, and at least one surface will be open to allow access to the interior. This operation is often applied on the entire model, influencing the sequence of feature creation to achieve the desired shape. Ribs and Webs Ribs and webs are features added to parts to provide structural support and enhance functionality. Ribs are thin protrusions that reinforce a part, while webs are thin sections connecting thicker areas. These features must be defined by their geometry, thickness, and specific location within the model. Their role in stability and heat transfer highlights their importance in effective solid modeling design. Additional Feature Types Other less common features include bosses (raised areas for flat surfaces), draft angles for mold removal, grooves (shallow cuts), and various slots or keyways. These specialized features serve distinct functions and often dictate the manufacturing process for the part. Understanding these feature types is essential for precise modeling, particularly when some may not be readily available in modeling software. Cosmetic Features Cosmetic features modify a part's surface appearance without changing its size or shape, akin to cosmetic alterations on a human body. They encompass details like threads and knurls, which are often not fully modeled due to the fineness of the changes but are still noted for subsequent fabrication processes. The Role of Datums in Modeling Datums serve as reference geometries facilitating the creation of complex features. They include datum points, axes, and planes, which help define and locate new features accurately. Various ways to define datums exist, such as positioning them at vertices or intersections, or offsetting them from surfaces. Chaining datums can streamline feature creation by building upon previously defined geometries to enhance the precision and control over the modeling process. Advanced Feature Creation Techniques Techniques such as using feature arrays (rectangular or circular) enable the efficient replication of features, saving time while ensuring consistency across the model. Mirrored features allow for the easy creation of symmetrical components by reflecting an existing feature across a defined mirror plane. Blends involve smooth transitions between profiles, necessitating the accurate definition of vertices across multiple sketches for seamless modeling. 17.2-5 Overview of Fastening Methods in Design Fastening methods are essential in product design, impacting durability, reliability, cost, and assembly processes. Different techniques are employed based on the number of components, permanence of the assembly, and the required security. Types of Fasteners Mechanical Fasteners: Manufactured parts that join two or more components. Permanent Fasteners: Intended for non-disassembly (e.g., welding, gluing, riveting). Temporary Fasteners: Allow future disassembly (e.g., screws, bolts, pins). Fastener Selection Considerations Functionality: Ease of assembly/disassembly. Cost: Includes fastener price and assembly processes. Assembly Speed: Important in manufacturing and maintenance. Screw Thread Fundamentals Definition Screw threads form a helix or conical spiral used for various applications, such as fastening and adjusting components. Thread Terminology Term Explanation Axis Longitudinal center line of the thread. Crest The top of the external threads. Root The bottom cut on external threads. Major Diameter Largest diameter, measured from crest to crest. Minor Diameter Smallest diameter, measured from root to root. Pitch Distance from one thread point to the next. Lead Distance a thread advances in one full rotation. Thread Classifications Single Thread: One continuous ridge; pitch equals lead. Multiple Threads: Two or more ridges side by side; lead increases with the number of threads (e.g., double lead = twice the pitch). Types of Threads Right-Hand Threads: Engage clockwise. Left-Hand Threads: Engage counterclockwise. Thread Standards Whitworth Threads: Early UK standardization. Unified Screw Threads (1948): Compromise between US and UK standards. ISO Metric Threads: International standard for metric screw threads. Common Thread Forms Unified Threads: Standard for threaded fasteners. Acme Threads: Used for power transmission; commonly found in jacks. Buttress Threads: Designed for high-stress applications. Rolled Threads: Made from sheet metal, often seen in consumer goods. Thread Cutting Techniques Taps and Dies: Tools for internal/external threads. Through Holes: Go completely through an object. Blind Holes: Do not go completely through; often drilled deeper. Modeling and Documenting Screw Threads CAD Representation Simplified representations of threads are often used to avoid cumbersome modeling while still conveying necessary information. Thread Notes ISO Metric Threads: Notation includes major diameter, pitch, tolerance, and thread depth. Unified National Threads: Notation specifies major diameter, threads per inch, type, and tolerance information. Example Notation ISO Example:M 10 x 1.5 – 6gfor an external metric thread with a major diameter of 10 mm and pitch of 1.5 mm. ANSI Example:3/8 – 16 UNC – 2A LHfor a left-hand external unified thread. Summary & Key Takeaways Understanding fastening systems is crucial for product assembly and disassembly efficiency. Key classifications of fasteners differentiate between permanent and temporary methods. Familiarity with screw threads and their properties facilitates proper selection and application in design. Utilize standard thread notations for clarity in communication and documentation within engineering practices. NOTE Fastening Methods in Product Assembly Various methods exist for joining multiple sheets of paper, including paper clips for temporary holding, staples for more security, and binders or books for larger collections. Manufactured products are generally assemblies of numerous parts; hence, determining the method for fastening components is crucial in their design. Fastening methods can vary in permanence, with temporary fasteners like screws and bolts designed for disassembly, and permanent fasteners like welding and gluing meant to stay intact. A mechanical fastener is any manufactured part whose primary role is to join two or more parts, emphasizing the need to understand different types for effective design. Classification of Fasteners Fasteners are categorized into two major types: permanent and temporary. Permanent fasteners include methods such as welding, gluing, stapling, nailing, and riveting, used when parts will not be disassembled. Temporary fasteners, such as screws, bolts, keys, and pins, are utilized when future disassembly is expected. Snap fasteners are also common and incorporated into designs to reduce the number of parts in an assembly and will be covered in more detail in the chapter. Screw Threads and Their Functionality Screw threads are designed as a helix or conical spiral on the surface of shafts and play various roles, primarily for fastening parts together, making adjustments, and transmitting power. Common applications include the fastening of nuts and bolts, leveling adjustments, and components such as screw jacks or micrometers. Examples of screw threads include the use in surveyor’s transits for fine adjustments and on lathes for transmitting motion with automatic threading attachments. Thread Terminology Essential terms related to thread geometry include axis, root, crest, major diameter, minor diameter, pitch diameter, pitch, depth of thread, angle of thread, body, and chamfer. The axis refers to the longitudinal centerline, while the root and crest indicate the bottom and top of an external thread. The major and minor diameters define the largest and smallest dimensions of screw threads, respectively. Thread depth signifies the distance between crest and root, while chamfers aid in engaging threads. Characteristics of Single and Multiple Threads Most threads are single, defined by a continuous ridge where the lead equals the pitch. Multiple threads can consist of two or more ridges side by side; a good example includes the threading on a ballpoint pen, designed for quick assembly. The lead is critical in determining installation speed and travel distance, essential in various mechanical applications. Right-Hand and Left-Hand Threads Right-handed threads engage by rotating clockwise, while left-handed threads engage counterclockwise, which is useful in specific applications. Recognizing these threads can be simplified using a rule: if a thread leans left, it is right- handed; if it leans right, it is left-handed. Historical Context and Standards of Threads Inconsistencies among thread standards were prevalent until Sir Joseph Whitworth's 1841 standardization in England. The American Standard thread was introduced in 1935, followed by the Unified Screw thread created in 1948 for compatibility among the U.S., Canada, and Great Britain. The ISO metric system has also been developed for international consistency, indicating a transitional state between various standards. Types of Thread Forms Common thread forms include Unified threads (standard fasteners), American National threads (similar but with a flat root), and ISO metric threads with slightly less depth than Unified threads. Power transmission threads like square, Acme, and buttress threads have specific shapes effectively used in machinery for strength and power transmission. Rolled threads, often seen in light bulbs and sockets, represent a unique manufacturing technique distinct from traditional cutting methods. 9.3-4 Fabrication Processes Overview Fabrication Methods Cross Geometry Modification: Adapting designs with rounded edges for versatile production, suitable for both low-volume and high-volume methods. Prototyping vs. Production: Understanding why certain geometries face challenges across different production techniques. Production Process Types Low-Volume Production Characteristics: Suitable for unique or prototype parts (e.g., one-off items). Equipment: Uses general-duty machines with common fixtures. Workpiece Definition: The raw material piece before final fabrication. Standard Commercial Shapes Raw Materials: Metals (e.g., steel, aluminum) and plastics (e.g., polycarbonate) delivered in uniform shapes (e.g., bars, sheets). Efficiency: Starting with slightly larger commercial shapes reduces material removal efforts. Common Low-Volume Processes Process Advantages Disadvantages Sawing Fast Poor accuracy, limited to linear cuts Turning Excellent Limited to axially accuracy for axes symmetric geometries Drilling Quick and precise Limited to axial holes only Milling Versatile; creates High costs, complex shapes especially for multi- axis mills EDM Great accuracy on Slow, limited to odd shapes conductive materials Broaching Fast for 2-D Requires custom shapes tools Rapid Prototyping Creates intricate Slow, limited shapes materials available Welding/Brazing Fast for complex Can distort parts, geometries high-temperature drawbacks Grinding High precision Slow; mainly for finishing Standard Manufacturing Techniques Higher-Volume Production Involves significant tooling investment, generally used when production volume justifies cost. Raw Material Forms: Ingot, powder, or rough forms, reformed at high temperatures or pressures. Common High-Volume Production Processes Process Advantages Disadvantages Sand Casting Inexpensive Poor accuracy and molds, versatile surface finish Investment Casting High detail and Slow due to manual accuracy handling Extrusion Constant cross- Expensive tooling section shapes Drawing Very accurate for Limited to circular circular shapes geometries Rolling Accurate Limited shapes thickness profiles Die Casting/Molding Creates complex Molds expensive, shapes may have porosity Forging Strengthens Limited detail in material shapes Stamping Fast; can create Limited to sheet complex shapes metal Sintering High detail on Porous, limited to small parts shallow features Burr Removal Importance: Sharp edges and burrs can impair functionality and safety. Methods: Hand tools for low-volume, tumbling for medium to high-volume production. Summary & Key Takeaways Adaptable Designs: Rounded edges enhance production flexibility. Material Selection: Using standard shapes minimizes waste. Precision Techniques: Various processes serve different production scales and accuracy needs. Burr Management: Essential for functionality and safety, employing tailored removal techniques according to production scale. NOTE Fabrication Process Modifications The geometry of parts can be improved for fabrication by introducing rounded edges, making them suitable for both low and high-volume production methods. This design modification allows for the same geometry to be utilized effectively during both prototyping stages and mass production phases. Understanding the relationship between geometry and production methods is crucial for optimizing fabrication outcomes. Fabrication Process Families Various fabrication processes exist, which can be grouped into families based on speed, precision, cost of secondary equipment, and the feasibility of geometrical modifications once production has begun. The chapter acknowledges the existence of many processes but notes that a complete listing would be extensive and impractical for inclusion in a single chapter. Reference materials like Machinery’s Handbook provide deeper insights into these processes. Low-Volume Production Parts produced at a rate of a few per day are typically made using low-volume processes. These processes are well-suited for unique items and prototypes that are later suitable for high-volume production. Machines employed for low-volume processes are commonly found in fabrication shops and designed for diverse geometries, requiring minimal specialized tools. Fixtures, devices used to hold workpieces during shaping, are essential in these operations. Standard Commercial Shapes Common materials for engineered parts include metals (like steel and aluminum) and plastics (such as polycarbonate and nylon), delivered in standard shapes such as bars, tubes, and plates. These shapes facilitate easier fabrication, with the selection process ideally starting with a standard size slightly larger than the target dimension to minimize waste. Sawing Operations Sawing is a common process for cutting workpieces to rough sizes using a multitoothed blade. It offers rapid operation, but precision is limited, typically achieving sizes accurate to within 1 mm easily and 0.1 mm with difficulty. Sawing paths are generally restricted to straight lines and large-radius curves. Turning Operations Turning is a technique used on lathes to form axially symmetrical features by rotating the workpiece while cutting tools remove material in radial and axial directions. The process allows for the creation of grooves, threads, and various shaft shapes, yielding high accuracy and excellent surface finishes. Drilling Techniques Drilling involves creating cylindrical holes in stationary workpieces using a rotating drill bit. High accuracy can be achieved through different setups, such as using a drill press where hole locations can be controlled with precision. Milling Processes Milling utilizes machines to remove material via rotating tools called end mills, capable of producing complex part geometries in both axial and transverse directions. Both manually controlled and numerically controlled machines are discussed, with notes on their capabilities to create intricate shapes. EDM uses a charged electrode and dielectric fluid to erode material from electrically conductive workpieces, allowing for precise shaping of complex geometries. While capable of yielding fine details, the rate of material removal is relatively slow, influenced by the thickness of the workpiece. Broaching Operations Broaching is used for creating specific shapes by sliding a broach through a workpiece, suitable for both prototyping and high-volume production despite the need for custom tools. Various rapid prototyping processes, such as stereolithography (SLA) and fused deposition modeling (FDM), allow for the quick creation of parts with complex geometries. While they are not typically used for high-volume production due to cost and speed limitations, they offer valuable methods for initial model creation. Welding and Brazing Processes Unlike processes that remove material, welding and brazing involve joining materials together. Welding melts the pieces at the joints, integrating filler material for strength, while brazing uses a lower-temperature filler alloy to bond materials without melting them. Both processes have potential drawbacks, including distortion and the introduction of flaws in the finished product.