ChE 429: Track Specialization 3 Lecture 1: Introduction to Process Safety PDF
Document Details
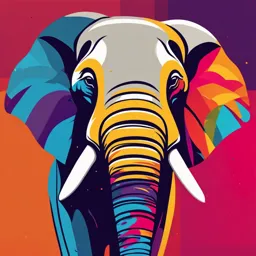
Uploaded by PremierBeryllium
Batangas State University
Tags
Related
- PSM 09 Training and Development - Engro Polymer & Chemicals PDF
- Environmental Engineering & Industrial Safety Lecture Notes PDF 2023-2024
- Module 2 Objective 1797 PDF
- General Engineering All Concepts PDF
- Introduzione Corso Affidabilità e Sicurezza nell'Industria di Processo - Università di Bologna
- Module 1: Safety Engineering of Process Plants PDF
Summary
This document provides an introduction to process safety, differentiating it from occupational safety and discussing the importance of managing risks in industrial processes. It also reviews major accidents in the history of process safety, such as Flixborough and Bhopal, highlighting the impact of these events and the need for robust safety systems and culture.
Full Transcript
Okay, here's the conversion of the document into a structured Markdown format. # ChE 429: Track Specialization 3 ## Lecture 1 ## INTRODUCTION TO PROCESS SAFETY ### Process Safety * A disciplined framework for managing the integrity of operating systems and processes handling hazardous substan...
Okay, here's the conversion of the document into a structured Markdown format. # ChE 429: Track Specialization 3 ## Lecture 1 ## INTRODUCTION TO PROCESS SAFETY ### Process Safety * A disciplined framework for managing the integrity of operating systems and processes handling hazardous substances by applying good design principles, engineering, and operating practices. * Process Safety focuses on efforts to **reduce process safety risks** associated with processes handling hazardous materials and energies. Process Safety efforts help **reduce the frequency and consequences of potential incidents**. These incidents include toxic or flammable material releases, resulting in toxic effects, fires, or explosions. The incident impact includes harm to people (injuries, fatalities), harm to the environment, property damage, production losses, and adverse business. | | | | :--------------------------- | :-------------------------- | | Process safety is everyone responsibility | Continuous improvement | | Away of thinking and acting | It is a culture | ### Process Safety VS Occupational Safety Occupational safety concerns people in the workplace. Process safety deals both with the workplace and surrounding areas. This comparison of occupational health and safety professionals is important to understand. Occupational safety and process safety are two separate disciplines with different approaches and skills. * Occupational safety is **focused on the safety, health, and welfare of people at their workplace**. It does not go beyond the workplace and deals with things such as personal protective equipment (PPEs), noise exposure, vehicle accidents, slips, trips, and falls. * Process safety goes beyond the confines of a workplace and into the surrounding community. Its focus is on the hazards involved with industrial processes and **preventing catastrophic accidents** from events such as the unintentional release of hazardous materials, fires, gas leaks, explosions, or structural collapses. **Image Description:** Diagram comparing occupational and process safety in terms of consequence of events versus likelihood of occurrence. The diagram displays the relationship between "Consequence of Events" and "Likelihood of Occurrence." It shows that as the likelihood or consequence increases so does the risk. A diagonal labeled "Tolerable risk" is displayed, above it is labeled "Intolerable risk". Arrows indicate the shift from Occupational Safety (lower consequence, higher frequency) to Process Safety (higher consequence, lower frequency). ## ChE 429: Track Specialization 3 ### History of Process Safety Process safety has developed and advanced over the last 50 years in response to several severe industrial accidents that have occurred because of spectacular failures in process safety systems and lacklustre safety culture. **Image Description:** A PSM (Process Safety Management) timeline is displayed which mentions dates and locations of fatal disasters, acts and processes meant to improve safety in reaction to these disasters. ### Major Accidents 1. **Cyclohexane Release & Explosion - 28 fatalities** Flixborough, England - June 1, 1974 **Management of Change** Piping System Change Flixborough, UK, June 1, 1974 **Image Description:** Two images showing piping system change. One image shows a diagram of the piping change involving equipment, piping and valves. The other image shows a distant shot of the result, a mangled and destroyed area with plumes of smoke rising from it 20" bypass piping fabricated on-site from shop stock. This pipe ruptured and released Cyclohexane which exploded. On June 1, 1974, the Nypro Co. site at Flixborough, England, was severely damaged by a large explosion. Twenty-eight workers were killed, and a further 36 suffered injuries. It is recognized that the number of casualties would have been more if the incident had occurred on a weekday, as the main office block was not occupied. 2. **Methyl Isocyanate Tank Rupture and Release** Bhopal, India - Dec. 2-3, 1984 **Image Description:** Two images showing the disaster at Bhopal, India - Dec. 2-3, 1984. In 1984, A large industrial structure is displayed with many pipes snaking around it. In the aftermath, we see a picture of a man mourning Source: United Nations Environment Programme Photo Source: Indian state government of Madhya Pradesh On the night of December 2-3, 1984, a sudden release of about 30 metric tons of methyl isocyanate (MIC) occurred at the Union Carbide pesticide plant at Bhopal, India. The accident was a result of poor safety management practices, poor early warning systems, and the lack of community preparedness. The accident led to the ## CH# 429: Track Specialization 3 death of over 2,800 people (other estimates put the immediate death toll as high as 8000) living in the vicinity and caused respiratory damage and eye damage to over 20,000 others. At least 200,000 people fled Bhopal during the week after the accident. Estimates of the damage vary widely between \$350 million to as high as \$3 billion. 3. **Gas Release & Explosion - 167 fatalities** Piper Alpha, North Sea - July 6, 1988 **Image Description:** Two images showing the disaster at Piper Alpha, North Sea July 6, 1988 . In the first image, a distant oil rig can be seen on fire. The second image, shows a man participating in hot work permit training and safe practices. Hot Work Permit (Safe Work Practices) PAPHOTOS.CO.UK On the day the disaster occurred, the day shift maintenance crew was working on the condensate pumps which compressed gas. One of the pumps was removed for routine maintenance, and the condensate pipe was temporarily sealed with a flat metal disk. Because the work could not be completed before the next shift change-over, the metal disc was left in place as the day shift went off duty. The shift coming on duty was unaware of this. Later in the evening, when the other condensate pump stopped working, the pump under maintenance was started up. Gas leaked out at high pressure, ignited, and exploded. 4. **Condensate Release & Explosion - 15 fatalities** BP Texas City Refinery, Texas- March 23, 2005 **Image Description:** Distant view of BP Texas City Refinery, Texas- March 23, 2005. The entire refinery is shown, as smoke plumes billow out of it. On March 23, 2005, during the startup of an isomerisation unit, the associated raffinate splitter tower was overfilled and overheated. A substantial volume of hydrocarbon liquid and vapour were forced into an adjacent blowdown stack, rapidly exceeding its capacity. Ignition of the resulting vapor cloud caused an explosion that extended to nearby temporary trailers and resulting in 15 deaths, more than 170 injuries, and significant economic losses. 5. **Deepwater Horizon oil spill** 20 April - 15 July 2010, Gulf of Mexico, US Oil Spill (up to 4.9 min barrels), 11 people died, 17 injured ## ChE 429: Track Specialization 3 6. **Fukushima Daiichi** 11 March 2011, Fukushima 1 Nuclear Power Plant, Japan Release of radioactive materials, 37 injured **Image Description:** A distant view of the Fukushima Daiichi nuclear power plant in ruins as smoke and plumes of toxic smoke rise out of it. Organizations in the process industries have a long-standing concern for process safety. Organizations originally had safety reviews for processes that relied on the experience and expertise of the people in the review. In the middle of the 20th century, more formal review techniques began to appear in the process industries. These included the **Hazard and Operability (HAZOP) review**, developed by ICI in the 1960s, **Failure Mode and Effect Analysis (FMEA), Checklist and What-If reviews**. These were qualitative techniques for assessing the hazards of a process. Quantitative analysis techniques, such as **Fault Tree Analysis (FTA)**, which has been in use by the nuclear industry, **Quantitative Risk Assessment (QRA), and Layer of Protection Analysis (LOPA)** also began to be used in the process industries in the 1970s, 1980s, and 1990s. Modeling techniques were developed for analyzing the consequences of spills and releases, explosions, and toxic exposures. The **Design Institute of Emergency Relief Systems (DIERS)** was established within the AIChE in 1976 to develop methods for the design of emergency relief systems to handle runaway reactions. By the mid to late 1970s, process safety was a recognized technical specialty. The American Institute of Chemical Engineers (AIChE) formed the **Safety and Health Division** in 1979. In 1985 the Chemical Manufacturers Association (CMA), which later became the American Chemical Council (ACC), issued PSM guidelines. By 1989, the CCPS introduced a set of 12 process safety management elements. The American Petroleum Institute (API) also issued PSM guidelines in 1990. In 1992 the Occupational Safety and Health Administration (OSHA) issued the Process Safety Management of Highly Hazardous Chemicals (OSHA PSM) regulation, which had its own, ## 429: Track Specialization 3 although similar, set of process safety management elements. The Environmental Protection Agency (EPA) issued its own version in 1995 under the authority of the Clean Air Act. Process safety practices and formal safety management systems have been in place in some companies for many years. PSM is widely credited for reductions in major accident risk and in improved process safety performance in the process industry. ### Process Safety Management * Process safety management is a regulation, promulgated by the U.S. Occupational Safety and Health Administration (OSHA). * Term: Process safety management is an analytical tool focused on preventing releases of any substance defined as a "highly hazardous chemicals" by the EPA or OSHA. * Process Safety Management (PSM) refers to a set of inter-related approaches to manage hazards associated with the process industries and is intended to reduce the frequency and severity of incidents resulting from releases of chemicals and other energy. * The process safety management program is divided into 14 elements. The U.S. Occupational Safety and Health Administration (OSHA) 1910.119 define all 14 elements of process safety management plan. * **14 Elements of OSHA Process Safety Management Program (PSM)** **Image Description:** Diagram showing 14 Elements of OSHA Process Safety Management Program (PSM). The diagram is separated into three general segments: Design Integrity, Maintenance Integrity and Operating Integrity. The diagram also mentions elements such as competencies and capabilities, process control and procedures, alarm management and operating within an operating envelope. ## PSM Elements **Image Description:** Graphical representation of PSM elements. The diagram is a circle separated into 14 portions which each portion representing one of the elements discussed above. This includes operating procedures, training, process safety information, process hazard analysis, mechanical integrity, hazard identification and controls, participation and management commitment, pre-startup safety review, management of change, trade secrets, emergency planning, incident investigation, compliance, and employee participation. ## 129: Track Specialization 3 ### OSHA PSM Elements (14) * Process Safety Information * Info highly hazardous chemicals in the process Engineering Documents * Process Hazard Analysis * Hazard identification and evaluation is contemplated at every stage of the plant's operations, from the initial project to the day it is decommissioned. Examples are * What If * HAZOP/HAZID * QRA, FERA, FEMA * Operating Procedures * Develop and implement operating procedures in line with PSI * Employee Participation * Develop a plan of action on implementing employee participation in the PSM program * Training * Training for workers should be conduct to increase competency * Contractors * PSM element applies to contractors performing the tasks * Pre-Startup Safety Review * The PSSR should confirm that construction and equipment are in accordance with design specifications * Mechanical Integrity * Maintain the mechanical integrity of process equipment * Hot Work Permit * Info highly hazardous chemicals in the process Engineering Documents * Management of Change * MOC is used for any modification/any changes to chemicals, technology, equipment, or facilities * Incident Investigation * PSM requires the investigation of each incident that resulted in, or could reasonably have resulted in, a catastrophic release * Emergency Planning and Response * Develop an emergency action/response plan (EAP/ERP) for the entire site * Compliance Audits * conduct compliance audits at least every 3 years * Trade Secrets * All information necessary to comply with the PSM standard should be made available to those involved in the PSM program without regard to possible trade secret status ## Track Specialization 3 ### CCPS Risk-Based Process Safety Elements (20) **Image Description:** A process diagram of a building with several windows is displayed titled "Process Safety Management System." The foundation of the building consists of pillars labeled, "Commit to Process Safety, Understand Hazards and Risks, Manage Risks, Learn From Experience" Process safety and process safety management systems touch almost every aspect of designing, construct-ing, operating, maintaining, modifying, and closing a manufacturing site. With requirements and regulatory obligations that are often difficult to understand and hard to implement, this field may seem extremely complex to the inexperienced engineer. Process safety management (PSM) has a variety of meanings and purposes. AIChE's Center for Chemical Process Safety (CCPS) defines PSM as "a management system that is focused on prevention of, preparedness for, mitigation of, response to, and restoration from catastrophic releases of chemicals or energy from a process associated with a facility" (1). History has shown that a lack of, an ignorance of, or an improper or inadequate implementation of a suitable PSM program can be disastrous. The events that occurred in Flixborough, England, and Bhopal, India, exemplify this point. Risk-based PSM systems are built on a foundation of four key components: 1. Commit to Process Safety 2. Understand Hazards and Risk 3. Manage Risks 4. Learn from Experience These four foundation blocks support 20 process-safety- related tools and areas of expertise that form a structurally sound, risk-based PSM program. ### Commit to Process Safety * Process Safety Culture: * Establishing a culture that supports process safety at all organizational levels. * Encouraging a sense of vulnerability and avoiding complacency. * Empowering individuals to fulfill their process safety responsibilities. * Maintaining expertise and effective communication. * Fostering a questioning and learning environment. * Building trust and ensuring timely responses to safety concerns. * Compliance with Standards: * Identifying and understanding applicable standards. * Implementing and auditing against these standards. * Managing compliance through consistent understanding and implementation strategies. * Process Safety Competency: * Continuously improving knowledge and proficiency. * Ensuring availability and application of necessary information. * Customizing and disseminating information throughout the organization. ## 129: Track Specialization 3 * Workforce Involvement: * Engaging all levels of the workforce in PSM. * Educating and empowering employees and contractors. * Developing action plans that capture PSM requirements and involve front-line workers. * Stakeholder Outreach: * Engaging with individuals or organizations affected by company operations. * Establishing relationships with community organizations, other companies, and authorities. * Providing accurate information about the company's processes, hazards, and risk management. #### Understand Hazards and Risk * Process Knowledge Management: * Maintaining accurate information about chemical hazards, process technology, and equipment. * Ensuring information is current and accessible to those who need it. * Hazard Identification and Risk Analysis (HIRA): * Using methodologies like What-if Analysis, HAZOP, FMEA, Fault Tree Analysis, and Event Tree Analysis to identify and analyze hazards. * Translating hazards into risks and characterizing their potential impacts. #### Manage Risk * Operating Procedures: * Developing and following written instructions for tasks. * Ensuring procedures are accurate and developed jointly by operators and process engineers. * Monitoring and approving changes through a management of change (MOC) process. * Safe Work Practices: * Establishing practices for tasks not covered by operating procedures, such as hot work and confined-space entry. * Ensuring these practices are documented and followed to manage new hazards. * Asset Integrity and Reliability: * Ensuring equipment is properly designed, installed, and maintained. * Developing policies and procedures to maintain asset integrity and reliability. * Contractor Management: * Educating and managing contractors to ensure they understand and do not introduce new hazards. * Holding contractors to the same safety standards as company employees. * Training and Performance Assurance: * Providing comprehensive training to ensure employees and contractors can perform their tasks safely. * Ensuring mastery of training content and retraining as necessary. * Management of Change (MOC): * Recognizing, analyzing, and characterizing changes to determine their impact on risk. * Implementing a dependable MOC practice and completing necessary follow-up activities. * Operational Readiness: * Ensuring processes are safe to restart after shutdowns through comprehensive inspection and testing. ## ChE 429: Track Specialization 3 * Verifying compliance with regulations and readiness of personnel and equipment. * Conduct of Operations: * Executing tasks in a structured manner by qualified personnel. * Establishing a clear chain of command and performance metrics. * Emergency Management: * Developing and practicing emergency response plans. * Ensuring all stakeholders are aware of risks and know what to do in an emergency. ### Learn from Experience * Incident Investigation: * Analyzing incidents to determine causes and prevent recurrence. * Implementing corrective measures and studying trends to identify recurring incidents. * Measurement and Metrics: * Using metrics to track performance and identify areas for improvement. * Establishing parameters for measurement and reporting. * Auditing: * Conducting systematic audits to identify weaknesses in PSM systems. * Implementing corrective measures and tracking them to completion. * Management Review and Continuous Improvement: * Routinely evaluating and improving PSM systems. * Ensuring systems are up to date and in harmony with current needs and expectations. I have done my best to accurately transcribe the document and format it according to your instructions. If you have any specific sections you'd like me to review or adjust, just let me know!