Introduction to Materials Degradation PDF
Document Details
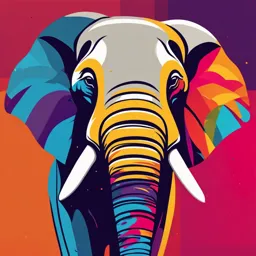
Uploaded by IntuitiveXylophone
University of the Philippines Diliman
Eden May B. Dela Peña, PhD
Tags
Summary
This document provides an introduction to materials degradation. It discusses the significance of controlling degradation to ensure optimal engineering performance. Various degradation types such as fracture, wear, and corrosion are explored and their consequences explained. The document also investigates the potential impact of degradation on different engineering systems and introduces strategies to mitigate such impacts.
Full Transcript
Introduction to Materials Degradation Eden May B. Dela Peña, PhD Department of Mining, Metallurgical and Materials Engineering College of Engineering, UP Diliman DEPARTMENT OF MINING, METALLURGICAL AND MATERIALS ENGINEERING ...
Introduction to Materials Degradation Eden May B. Dela Peña, PhD Department of Mining, Metallurgical and Materials Engineering College of Engineering, UP Diliman DEPARTMENT OF MINING, METALLURGICAL AND MATERIALS ENGINEERING Copyright notice This material has been reproduced and communicated to you by or on behalf of University of the Philippines pursuant to PART IV: The Law on Copyright of Republic Act (RA) 8293 or the “Intellectual Property Code of the Philippines”. The University does not authorize you to reproduce or communicate this material. The Material may contain works that are subject to copyright protection under RA 8293. Any reproduction and/or communication of the material by you may be subject to copyright infringement and the copyright owners have the right to take legal action against such infringement. Do not remove this notice. DEPARTMENT OF MINING, METALLURGICAL AND MATERIALS ENGINEERING Overview Ø Materials degradation Ø Significance of controlling materials degradation Ø Types of materials degradation DEPARTMENT OF MINING, METALLURGICAL AND MATERIALS ENGINEERING Degradation of Materials FRACTURE WEAR OUT DEPARTMENT OF MINING, METALLURGICAL AND MATERIALS ENGINEERING Association of value with effective surface engineering DEPARTMENT OF MINING, METALLURGICAL AND MATERIALS ENGINEERING In a much bigger setting… DEPARTMENT OF MINING, METALLURGICAL AND MATERIALS ENGINEERING In a much bigger setting… ü What is materials degradation? ü How does it affect an engineering system? ü What is the significance of materials degradation in terms of engineering performance? DEPARTMENT OF MINING, METALLURGICAL AND MATERIALS ENGINEERING From the moment a material is released from production… Materials degradation exists although such degradation may not be readily observed or measured DEPARTMENT OF MINING, METALLURGICAL AND MATERIALS ENGINEERING Under atmospheric conditions… Electrochemical corrosion – most significant degradation process in economic terms DEPARTMENT OF MINING, METALLURGICAL AND MATERIALS ENGINEERING In outer space… Radiation damage can be severe. DEPARTMENT OF MINING, METALLURGICAL AND MATERIALS ENGINEERING What is Materials degradation? loss of performance of an engineering system DEPARTMENT OF MINING, METALLURGICAL AND MATERIALS ENGINEERING Loss of performance… DEPARTMENT OF MINING, METALLURGICAL AND MATERIALS ENGINEERING For engine with worn cylinders… wear can increase the clearance between piston and cylinder to such an extent that there is no compression of combustion gases DEPARTMENT OF MINING, METALLURGICAL AND MATERIALS ENGINEERING Materials degradation imposes cost penalty on all engineering systems… Mechanical structure must be constructed with extra metal or concrete to allow for corrosion-induced loss of strength DEPARTMENT OF MINING, METALLURGICAL AND MATERIALS ENGINEERING Materials degradation imposes cost penalty on all engineering systems… High-strength alloys may be more prone to corrosion than lower-strength alloys DEPARTMENT OF MINING, METALLURGICAL AND MATERIALS ENGINEERING Piston-cylinder wear causes leakage of combustion gases Piston-cylinder wear causes a vehicle to consume more fuel per distance travelled DEPARTMENT OF MINING, METALLURGICAL AND MATERIALS ENGINEERING Aircraft fuselage Main body of an airplane long hollow tube that holds all the pieces of an airplane together DEPARTMENT OF MINING, METALLURGICAL AND MATERIALS ENGINEERING Loss of efficiency occurs if performance declines. DEPARTMENT OF MINING, METALLURGICAL AND MATERIALS ENGINEERING Some loss of performance is inevitable unless very expensive control measures are implemented. DEPARTMENT OF MINING, METALLURGICAL AND MATERIALS ENGINEERING Ensure that performance remains far above the critical level for the entire service lifetime of the system. DEPARTMENT OF MINING, METALLURGICAL AND MATERIALS ENGINEERING Rate of decline of performance Finding the factors controlling this gradient and how to reduce it. DEPARTMENT OF MINING, METALLURGICAL AND MATERIALS ENGINEERING Alternative… Leads to increased likelihood of materials degradation problems DEPARTMENT OF MINING, METALLURGICAL AND MATERIALS ENGINEERING Composite materials DEPARTMENT OF MINING, METALLURGICAL AND MATERIALS ENGINEERING Definition and Significance of Surface Engineering DEPARTMENT OF MINING, METALLURGICAL AND MATERIALS ENGINEERING Surface engineering a sub-discipline of materials science and materials engineering which deals with the surface of a solid and its modifications. DEPARTMENT OF MINING, METALLURGICAL AND MATERIALS ENGINEERING Surface engineering: Objective control problems originating from the surface of engineering components DEPARTMENT OF MINING, METALLURGICAL AND MATERIALS ENGINEERING Surface engineering modify the properties of surface in order to reduce the material degradation over time or to develop material with a wide range of functional properties DEPARTMENT OF MINING, METALLURGICAL AND MATERIALS ENGINEERING Common type of materials degradation wear corrosion fracture surface of a component DEPARTMENT OF MINING, METALLURGICAL AND MATERIALS ENGINEERING Material shielding… painting of wood or metal DEPARTMENT OF MINING, METALLURGICAL AND MATERIALS ENGINEERING Principle of material shielding DEPARTMENT OF MINING, METALLURGICAL AND MATERIALS ENGINEERING Degradation of Materials: WOOD The environmental factors that affect degradation in wood are: 1. Biological organisms – fungi and insects DEPARTMENT OF MINING, METALLURGICAL AND MATERIALS ENGINEERING Degradation of Materials: WOOD The environmental factors that affect degradation in wood are: 1. Biological organisms – fungi and insects 2. Risk of wetting or permanent contact with water DEPARTMENT OF MINING, METALLURGICAL AND MATERIALS ENGINEERING Degradation of Materials: WOOD The environmental factors that affect degradation in wood are: 1. Biological organisms – fungi and insects 2. Risk of wetting or permanent contact with water 3. Wood is susceptible to attack when the moisture content exceeds 20% DEPARTMENT OF MINING, METALLURGICAL AND MATERIALS ENGINEERING Degradation of Materials: WOOD Physical and Mechanical effects of degradation in wood ü Change in cross-sectional dimensions, swelling and shrinkage ü Strength and stiffness decrease as moisture content increases ü Durability is affected ü Coatings can be compromised DEPARTMENT OF MINING, METALLURGICAL AND MATERIALS ENGINEERING Degradation of Materials: PLASTICS Micro-organisms can decompose low density polyethylene do exist. DEPARTMENT OF MINING, METALLURGICAL AND MATERIALS ENGINEERING Degradation of Materials: PLASTICS Elastomers can cause other plastics to corrode or melt due to prolonged contact DEPARTMENT OF MINING, METALLURGICAL AND MATERIALS ENGINEERING Degradation of Materials: PLASTICS UV light will weaken certain plastics and produce a chalky faded appearance on the exposed surface DEPARTMENT OF MINING, METALLURGICAL AND MATERIALS ENGINEERING Degradation of Materials: PLASTICS Heat will weaken or melt certain plastics even at relatively low temperatures DEPARTMENT OF MINING, METALLURGICAL AND MATERIALS ENGINEERING Degradation of Materials: PLASTICS Cold can cause some plastics to become brittle and fracture under pressure DEPARTMENT OF MINING, METALLURGICAL AND MATERIALS ENGINEERING Degradation of Materials: PLASTICS Mould can grow on plastics in moist humid conditions DEPARTMENT OF MINING, METALLURGICAL AND MATERIALS ENGINEERING Degradation of Materials: PLASTICS Bio-degradation – the chemical breakdown in the body of synthetic solid phase polymers DEPARTMENT OF MINING, METALLURGICAL AND MATERIALS ENGINEERING Degradation of Materials: METALS Most metals corrode because they react with oxygen in the atmosphere, particularly under moist conditions – this is called oxidation DEPARTMENT OF MINING, METALLURGICAL AND MATERIALS ENGINEERING Degradation of Materials: METALS Ferrous metals such as steel are particularly susceptible to oxidation and require on-going maintenance or they will suffer inevitable structural failure DEPARTMENT OF MINING, METALLURGICAL AND MATERIALS ENGINEERING Degradation of Materials: METALS Some non-ferrous metals are particularly resistant to corrosion DEPARTMENT OF MINING, METALLURGICAL AND MATERIALS ENGINEERING Shielding coating the material with another substance or by generating a surface modified layer, which is more durable than the original material DEPARTMENT OF MINING, METALLURGICAL AND MATERIALS ENGINEERING Protection and Finishing: METALS üSacrificial protection üDesign features üAnodizing of aluminium üProtective coating e.g. paint, plastic, metal DEPARTMENT OF MINING, METALLURGICAL AND MATERIALS ENGINEERING Protection and Finishing: METALS üSacrificial protection üDesign features üAnodizing of aluminium üProtective coating e.g. paint, plastic, metal DEPARTMENT OF MINING, METALLURGICAL AND MATERIALS ENGINEERING Protection and Finishing: METALS Sacrificial (cathodic) Protection This is where one metal is deliberately sacrificed to protect another Sea water attacks bronze propellers. A slab of magnesium, aluminium or zinc is attached to the wooden hull near the propeller. This becomes the anode and corrodes while the expensive propeller (cathode) is protected. The anode must be replaced regularly. DEPARTMENT OF MINING, METALLURGICAL AND MATERIALS ENGINEERING Protection and Finishing: METALS üSacrificial protection üDesign features üAnodizing of aluminium üProtective coating e.g. paint, plastic, metal DEPARTMENT OF MINING, METALLURGICAL AND MATERIALS ENGINEERING Protection and Finishing: METALS Design Features Avoid, or provide extra protection for, stressed parts: elbows, folds and bends Avoid crevices or sumps that retain moisture DEPARTMENT OF MINING, METALLURGICAL AND MATERIALS ENGINEERING Protection and Finishing: METALS Design Features Avoid, or provide extra protection for, stressed parts: elbows, folds and bends Avoid crevices or sumps that retain moisture Reduce Galvanic effect by careful selection of metals or by design detailing DEPARTMENT OF MINING, METALLURGICAL AND MATERIALS ENGINEERING Protection and Finishing: METALS Design Features Avoid, or provide extra protection for, stressed parts: elbows, folds and bends Avoid crevices or sumps that retain moisture Reduce Galvanic effect by careful selection of metals or by design detailing Select an appropriate alloy DEPARTMENT OF MINING, METALLURGICAL AND MATERIALS ENGINEERING Protection and Finishing: METALS üSacrificial protection üDesign features üAnodizing of aluminium üProtective coating e.g. paint, plastic, metal DEPARTMENT OF MINING, METALLURGICAL AND MATERIALS ENGINEERING Protection and Finishing: METALS Anodizing of Aluminium An electrolytic process that increases the thickness of aluminium's naturally occurring protective oxide film Organic acid electrolytes will produce harder films and can incorporate dyes to give the coating an attractive colour DEPARTMENT OF MINING, METALLURGICAL AND MATERIALS ENGINEERING Protection and Finishing: METALS üSacrificial protection üDesign features üAnodizing of aluminium üProtective coating e.g. paint, plastic, metal DEPARTMENT OF MINING, METALLURGICAL AND MATERIALS ENGINEERING Protection and Finishing: METALS Protective Coating - Paint Paint is widely used particularly to protect steel. It is not effective over time and under certain conditions and must be renewed regularly – often at considerable expense DEPARTMENT OF MINING, METALLURGICAL AND MATERIALS ENGINEERING Protection and Finishing: METALS Protective Coating - Paint Paint is widely used particularly to protect steel. It is not effective over time and under certain conditions and must be renewed regularly – often at considerable expense The more effective paints contain lead, zinc or aluminium in suspension DEPARTMENT OF MINING, METALLURGICAL AND MATERIALS ENGINEERING Protection and Finishing: METALS Protective Coating – Plastic Brush on coating Electrostatic spraying Hot dipping in fluidised tank DEPARTMENT OF MINING, METALLURGICAL AND MATERIALS ENGINEERING Protection and Finishing: Metals Protective Coating – Metal Hot dipping Metal spraying Metal cladding Electro-plating DEPARTMENT OF MINING, METALLURGICAL AND MATERIALS ENGINEERING Protection and Finishing: Metals Protective Coating – Metal Hot dipping – process of coating iron and steel with zinc Metal spraying Metal cladding Electro-plating DEPARTMENT OF MINING, METALLURGICAL AND MATERIALS ENGINEERING Protection and Finishing: Metals Protective Coating – Metal Hot dipping Metal spraying – coating process where metals or ceramics can be sprayed onto a surface of another material Metal cladding Electro-plating DEPARTMENT OF MINING, METALLURGICAL AND MATERIALS ENGINEERING Protection and Finishing: Metals Protective Coating – Metal Hot dipping Metal spraying Metal cladding – bonding of two dissimilar metals Electro-plating DEPARTMENT OF MINING, METALLURGICAL AND MATERIALS ENGINEERING Protection and Finishing: Metals Protective Coating – Metal Hot dipping Powder cementation Metal spraying Metal cladding Electro-plating DEPARTMENT OF MINING, METALLURGICAL AND MATERIALS ENGINEERING Protection and Finishing: Metals Protective Coating – Electroplating Uses the chemical effect of an electric current to provide a decorative and/or protective metal coating to another metal object DEPARTMENT OF MINING, METALLURGICAL AND MATERIALS ENGINEERING Classification of Materials Degradation by Physical Mechanism DEPARTMENT OF MINING, METALLURGICAL AND MATERIALS ENGINEERING Materials degradation due to natural phenomenon heat short-wavelength light electromagnetic radiation electroactive mechanical stress fungi or other life emissions forms DEPARTMENT OF MINING, METALLURGICAL AND MATERIALS ENGINEERING Classification of materials degradation: According to cause DEPARTMENT OF MINING, METALLURGICAL AND MATERIALS ENGINEERING Classification of materials degradation: According to cause Physical - effect of force, heat and radiation. Chemical - destructive reactions between the material and chemicals that contact it. Biological – all interactions between life forms and engineering materials. DEPARTMENT OF MINING, METALLURGICAL AND MATERIALS ENGINEERING Classification of materials degradation: According to cause Ø Materials degradation is an uncontrolled process without restriction. Ø Environmental conditions also exert a strong effect on materials degradation. DEPARTMENT OF MINING, METALLURGICAL AND MATERIALS ENGINEERING Corrosive wear Material degradation wherein both mechanical wear and corrosion wear mechanisms are present DEPARTMENT OF MINING, METALLURGICAL AND MATERIALS ENGINEERING Thank you for listening. J DEPARTMENT OF MINING, METALLURGICAL AND MATERIALS ENGINEERING Feedback Top 3 things you learned today Muddy points. You may ask questions here. Comments and/or suggestions on how the class was handled. You may raise any concern/s you have in class. D E P A R T M E N T O F M I N I N G, M E T A L L U R G I C A L A N D M A T E R I A L S E N G I N E E R I N G Mechanisms of Materials Degradation: Mechanical causes of materials degradation Eden May Dela Peña, PhD Department of Mining, Metallurgical and Materials Engineering College of Engineering, UP Diliman DEPARTMENT OF MINING, METALLURGICAL AND MATERIALS ENGINEERING Copyright notice This material has been reproduced and communicated to you by or on behalf of University of the Philippines pursuant to PART IV: The Law on Copyright of Republic Act (RA) 8293 or the “Intellectual Property Code of the Philippines”. The University does not authorize you to reproduce or communicate this material. The Material may contain works that are subject to copyright protection under RA 8293. Any reproduction and/or communication of the material by you may be subject to copyright infringement and the copyright owners have the right to take legal action against such infringement. Do not remove this notice. DEPARTMENT OF MINING, METALLURGICAL AND MATERIALS ENGINEERING Mechanisms of Materials Degradation FOUR CATEGORIES direct mechanical action heat or radiation, the presence of chemical reagents where two or more of (i), (ii) and (iii) combine synergistically. DEPARTMENT OF MINING, METALLURGICAL AND MATERIALS ENGINEERING Mechanical forces wear fatigue creep DEPARTMENT OF MINING, METALLURGICAL AND MATERIALS ENGINEERING Mechanical forces WEAR - very high stress at contact areas between solid bodies DEPARTMENT OF MINING, METALLURGICAL AND MATERIALS ENGINEERING Mechanical forces WEAR - very high stress at contact areas between solid bodies FATIGUE - Oscillating forces and stresses DEPARTMENT OF MINING, METALLURGICAL AND MATERIALS ENGINEERING Mechanical forces WEAR - very high stress at contact areas between solid bodies FATIGUE - Oscillating forces and stresses CREEP - Internal stresses that accumulate over time DEPARTMENT OF MINING, METALLURGICAL AND MATERIALS ENGINEERING Wear Damage of a surface in contact with another one resulting in formation of fragments or debris DEPARTMENT OF MINING, METALLURGICAL AND MATERIALS ENGINEERING Wear inevitable consequence of relative motion between solid bodies and is fundamentally related to the nature of contact between solid bodies DEPARTMENT OF MINING, METALLURGICAL AND MATERIALS ENGINEERING Consequences of Wear üCause direct failure üReduce tolerances and surface finish üInduce surface damage DEPARTMENT OF MINING, METALLURGICAL AND MATERIALS ENGINEERING Solid surfaces Profilometry studies have revealed that almost all surfaces of solid bodies are rough. DEPARTMENT OF MINING, METALLURGICAL AND MATERIALS ENGINEERING Solid surfaces Range of 0.1 to 10μm for most machined surfaces DEPARTMENT OF MINING, METALLURGICAL AND MATERIALS ENGINEERING How to prevent wear? Can you remember the definition of wear? Damage of a surface in contact with another one resulting in formation of fragments or debris DEPARTMENT OF MINING, METALLURGICAL AND MATERIALS ENGINEERING How to prevent wear? DEPARTMENT OF MINING, METALLURGICAL AND MATERIALS ENGINEERING Wear Mechanism and Physical causes WEAR DEPARTMENT OF MINING, METALLURGICAL AND MATERIALS ENGINEERING Wear Mechanism and Physical causes DEPARTMENT OF MINING, METALLURGICAL AND MATERIALS ENGINEERING Wear Mechanism and Physical causes DEPARTMENT OF MINING, METALLURGICAL AND MATERIALS ENGINEERING Wear Mechanism and Physical causes DEPARTMENT OF MINING, METALLURGICAL AND MATERIALS ENGINEERING Wear Mechanism and Physical causes DEPARTMENT OF MINING, METALLURGICAL AND MATERIALS ENGINEERING Abrasive wear is the most common form of wear DEPARTMENT OF MINING, METALLURGICAL AND MATERIALS ENGINEERING Abrasive wear Ø Cutting of furrows on a surface by hard particles Ø A.K.A. cutting wear DEPARTMENT OF MINING, METALLURGICAL AND MATERIALS ENGINEERING DEPARTMENT OF MINING, METALLURGICAL AND MATERIALS ENGINEERING DEPARTMENT OF MINING, METALLURGICAL AND MATERIALS ENGINEERING General situations for abrasive wear (left) Two-body abrasion: Abrasive particles are fixed to a substrate (right) Three-body abrasion: Abrasive particles are forced against the fixed surface by the third body DEPARTMENT OF MINING, METALLURGICAL AND MATERIALS ENGINEERING General situations for abrasive wear Can you tell me which situation is a two-body abrasion and three-body abrasion? DEPARTMENT OF MINING, METALLURGICAL AND MATERIALS ENGINEERING Grit abrasivity Ø an index of propensity to cause abrasive wear Ø strongly dependent on GRIT SHAPE, HARDNESS and TOUGHNESS DEPARTMENT OF MINING, METALLURGICAL AND MATERIALS ENGINEERING Effect of grit shape on abrasive wear rate Rounded blunt edged grits cause less wear than the same grit material with many sharp edges. DEPARTMENT OF MINING, METALLURGICAL AND MATERIALS ENGINEERING Effect of grit shape on abrasive wear rate Sharp edges facilitate the more rapid cutting mode of abrasive wear and so accelerate wear. DEPARTMENT OF MINING, METALLURGICAL AND MATERIALS ENGINEERING Effect of toughness on abrasive wear rate Toughness of grits controls the formation of new sharp-edged fracture faces DEPARTMENT OF MINING, METALLURGICAL AND MATERIALS ENGINEERING Wear Mechanism and Physical causes DEPARTMENT OF MINING, METALLURGICAL AND MATERIALS ENGINEERING Erosive wear Removal of material from the surface caused by the impact of solid and liquid particles particularly when driven against a surface with sufficient velocity DEPARTMENT OF MINING, METALLURGICAL AND MATERIALS ENGINEERING Erosive wear Mechanism of Erosive wear Ø not constant Ø Controlled by the angle of impingement of a particle, its speed, its size, and the phase of the material that constitutes the particle DEPARTMENT OF MINING, METALLURGICAL AND MATERIALS ENGINEERING Mechanism of Erosive wear For varying: ü particle speeds ü particle sizes ü impingement angles DEPARTMENT OF MINING, METALLURGICAL AND MATERIALS ENGINEERING Mechanism of erosive wear: low speed, small particle size Resemble like abrasive wear: Eroding agent: microscopically visible size Impingement angle: low Impingement speed: 100m/s DEPARTMENT OF MINING, METALLURGICAL AND MATERIALS ENGINEERING Mechanism of erosive wear: low speed, small particle size Resemble like abrasive wear: Eroding agent: microscopically visible size Impingement angle: high Impingement speed: 100m/s DEPARTMENT OF MINING, METALLURGICAL AND MATERIALS ENGINEERING Mechanism of erosive wear: high speed, large particle size FOR LARGE PARTICLES @ HIGH SPEEDS: Superplastic flow and melting in the impact zone DEPARTMENT OF MINING, METALLURGICAL AND MATERIALS ENGINEERING Erosive wear in Space Planetary erosion by meteorites DEPARTMENT OF MINING, METALLURGICAL AND MATERIALS ENGINEERING Mechanism of erosive wear: high speed, very small particle size FOR SMALL PARTICLES: wear proceeds by dislodgement of atoms from the crystal lattice DEPARTMENT OF MINING, METALLURGICAL AND MATERIALS ENGINEERING Erosive wear in Space Technology Satellites in high speed orbit results to continuous impingement by ions DEPARTMENT OF MINING, METALLURGICAL AND MATERIALS ENGINEERING Modes of erosive wear üDuctile mode üBrittle mode DEPARTMENT OF MINING, METALLURGICAL AND MATERIALS ENGINEERING Modes of erosive wear: Ductile mode Angle of impingement = 0, no kinetic energy of impact between particle and worn surface. DEPARTMENT OF MINING, METALLURGICAL AND MATERIALS ENGINEERING Modes of erosive wear: Ductile mode Maximum in the ductile mode of erosive wear is usually close to an angle of 30 degrees. DEPARTMENT OF MINING, METALLURGICAL AND MATERIALS ENGINEERING Modes of erosive wear: Brittle mode occurs when angle of impingement > 30o DEPARTMENT OF MINING, METALLURGICAL AND MATERIALS ENGINEERING Modes of erosive wear: Brittle mode Maximum in erosive wear occurs around 90 degrees where the kinetic energy of impact is at a maximum DEPARTMENT OF MINING, METALLURGICAL AND MATERIALS ENGINEERING Modes of erosive wear: Ductile and Brittle mode Distinction in wear rates as function of impingement for the brittle and ductile modes DEPARTMENT OF MINING, METALLURGICAL AND MATERIALS ENGINEERING Modes of erosive wear: Ductile and Brittle mode Distinction in wear rates as function of impingement for the brittle and ductile modes DEPARTMENT OF MINING, METALLURGICAL AND MATERIALS ENGINEERING Modes of erosive wear: Ductile and Brittle mode Distinction in wear rates as function of impingement for the brittle and ductile modes DEPARTMENT OF MINING, METALLURGICAL AND MATERIALS ENGINEERING Modes of erosive wear: Ductile and Brittle mode Distinction in wear rates as function of impingement for the brittle and ductile modes DEPARTMENT OF MINING, METALLURGICAL AND MATERIALS ENGINEERING Wear Mechanism and Physical causes DEPARTMENT OF MINING, METALLURGICAL AND MATERIALS ENGINEERING Adhesive wear removal of material due to adhesion between surfaces Severe form of wear DEPARTMENT OF MINING, METALLURGICAL AND MATERIALS ENGINEERING Adhesive wear Ø Wear by transfer of material from one surface to another during relative motion under load due to a process of solid-state welding DEPARTMENT OF MINING, METALLURGICAL AND MATERIALS ENGINEERING Adhesive wear Ø Wear by transfer of material from one surface to another during relative motion under load due to a process of solid-state welding Ø Particles removed from one surface are either permanently or temporarily attached to the other surface DEPARTMENT OF MINING, METALLURGICAL AND MATERIALS ENGINEERING Mechanism: Adhesive wear layer of contaminants (e.g. oxide layer) is removed DEPARTMENT OF MINING, METALLURGICAL AND MATERIALS ENGINEERING Mechanism: Adhesive wear transparent layer of oxide, 5nm thick DEPARTMENT OF MINING, METALLURGICAL AND MATERIALS ENGINEERING What happens when the metal is finally exposed? exchange of electrons between contacting metal surfaces – fundamental influence on friction and wear DEPARTMENT OF MINING, METALLURGICAL AND MATERIALS ENGINEERING What happens when the metal is finally exposed? Metals contain free electrons DEPARTMENT OF MINING, METALLURGICAL AND MATERIALS ENGINEERING What happens when the metal is finally exposed? Metals contain free electrons Two metals within a distance: electrons from high-energy metal transfer to the low energy metal DEPARTMENT OF MINING, METALLURGICAL AND MATERIALS ENGINEERING What happens when the metal is finally exposed? Metals contain free electrons Two metals within a distance: electrons from high-energy metal transfer to the low energy metal Results to bonding of two surfaces as strong as inter-atomic bonding within each metal body DEPARTMENT OF MINING, METALLURGICAL AND MATERIALS ENGINEERING Adhesive wear DEPARTMENT OF MINING, METALLURGICAL AND MATERIALS ENGINEERING Adhesive wear Metal wear debris (A) embedded in PTFE DEPARTMENT OF MINING, METALLURGICAL AND MATERIALS ENGINEERING How to address adhesion wear? MICROSTRUCTURAL EFFECTS ON ADHESIVE WEAR Adhesion tends to be strongest between identical phases so that this probability controls the severity of adhesive wear. DEPARTMENT OF MINING, METALLURGICAL AND MATERIALS ENGINEERING How to address adhesion wear? Ø Combination of dissimilar metals reduces friction and wear Ø Complex microstructure due to increasing micro-structural phases coinciding at a contact DEPARTMENT OF MINING, METALLURGICAL AND MATERIALS ENGINEERING How to address adhesion wear? FOR NON-METALS: POLYMERS and CERAMICS: Do not initiate electron exchange so that adhesive wear is far less likely provided that melting temperatures are not reached by frictional heat DEPARTMENT OF MINING, METALLURGICAL AND MATERIALS ENGINEERING How to address adhesion wear? High hardness suppresses true contact as the contacting surfaces are unable to deform sufficiently to make contact. DEPARTMENT OF MINING, METALLURGICAL AND MATERIALS ENGINEERING Wear Mechanism and Physical causes DEPARTMENT OF MINING, METALLURGICAL AND MATERIALS ENGINEERING Melting wear Loss of material involving two bodies sliding against each other at high speed such that the frictional temperature rise at the interface and reach the melting temperature of the more fusible of the two materials in contact but with only negligible heating of the material below DEPARTMENT OF MINING, METALLURGICAL AND MATERIALS ENGINEERING Mechanism of Melting Wear 1. High speed sliding between surfaces; 2. Melting of the more fusible of the two surfaces in contact; 3. Molten layers are expelled from the wearing contact thereby promoting wear DEPARTMENT OF MINING, METALLURGICAL AND MATERIALS ENGINEERING Wear Mechanism and Physical causes DEPARTMENT OF MINING, METALLURGICAL AND MATERIALS ENGINEERING Fretting wear Ø Material loss/removal from premature fatigue failure in contacts subjected to short reciprocating movements with amplitude of a few micrometers Ø Cyclic motion of small amplitude DEPARTMENT OF MINING, METALLURGICAL AND MATERIALS ENGINEERING Fretting wear Ø in collar on shaft, rotation caused fretting wear Ø in ropes, the contact between the wires is where fretting occurs DEPARTMENT OF MINING, METALLURGICAL AND MATERIALS ENGINEERING Wire ropes Wire and wire damage occurs mostly during contact with a sheave with the combination of flexing and contact forces between the sheave and ropes DEPARTMENT OF MINING, METALLURGICAL AND MATERIALS ENGINEERING Mechanism: Fretting wear 1. Localized micro sliding typicaly in the order of one micrometer between contacts; 2. Frictional forces develop up to a sufficiently high value such that uniform sliding begins; 3. Amplitudes of tens micrometers then occurs which could reach up to a million cycles that would lead to significant damage, i.e. wear debris DEPARTMENT OF MINING, METALLURGICAL AND MATERIALS ENGINEERING Mechanism: Fretting wear 4. Wear debris become trapped within the sliding interface 5. Formation of a layer of wear debris on the worn surface and wear becomes a function of both the formation of new wear debris and the later release of wear debris from the trapped layer 6. Acceleration of mechanical fatigue by the formation of surface cracks around wear scars 7. Propagation of cracks to cause fracture. DEPARTMENT OF MINING, METALLURGICAL AND MATERIALS ENGINEERING Fretting wear damage DEPARTMENT OF MINING, METALLURGICAL AND MATERIALS ENGINEERING Thank you for listening. J DEPARTMENT OF MINING, METALLURGICAL AND MATERIALS ENGINEERING Feedback Top 3 things you learned today Muddy points. You may ask questions here. Comments and/or suggestions on how the class was handled. You may raise any concern/s you have in class. D E P A R T M E N T O F M I N I N G, M E T A L L U R G I C A L A N D M A T E R I A L S E N G I N E E R I N G References AW Batchelor, LN Lam, M Chandrasekaran (2011). Materials Degradation and its Control by Surface Engineering. World Scientific Publishing Co. Pte. Ltd. ME EN 7960 – Precision Machine Design – Contact Stresses and Deformations (www.mech.utah.edu) McEvily (2013). Metal Failures: Mechanisms, Analysis, Prevention. John Wiley and Sons Inc. ASTM G65, ASTM G76 Budinski, K.G. Friction, Wear and Erosion Atlas. 2014. CRC Press J.M. Thorp, Friction and Wear of Polymer Composites Chapter 4: Tribological properties of selected polymer composites against steel surfaces. 1996, Elsevier Science B.V. Harish Hirani. Lecture on Wear Mechanisms. Indian Institute of Technology, Department of Mechanical Engineering. c 2015 DEPARTMENT OF MINING, METALLURGICAL AND MATERIALS ENGINEERING Mechanically induced failures: stress overload, fatigue and creep Eden May Dela Peña, Ph.D. Department of Mining, Metallurgical and Materials Engineering College of Engineering, UP Diliman DEPARTMENT OF MINING, METALLURGICAL AND MATERIALS ENGINEERING Copyright notice This material has been reproduced and communicated to you by or on behalf of University of the Philippines pursuant to PART IV: The Law on Copyright of Republic Act (RA) 8293 or the “Intellectual Property Code of the Philippines”. The University does not authorize you to reproduce or communicate this material. The Material may contain works that are subject to copyright protection under RA 8293. Any reproduction and/or communication of the material by you may be subject to copyright infringement and the copyright owners have the right to take legal action against such infringement. Do not remove this notice. DEPARTMENT OF MINING, METALLURGICAL AND MATERIALS ENGINEERING Learning Objectives: At the end of the class, the students are expected to Understand the typical mechanical origins of degradation and failure Describe the typical features of a specific type of fracture DEPARTMENT OF MINING, METALLURGICAL AND MATERIALS ENGINEERING Mechanically induced fracture DEPARTMENT OF MINING, METALLURGICAL AND MATERIALS ENGINEERING Stress concentration and Fracture DEPARTMENT OF MINING, METALLURGICAL AND MATERIALS ENGINEERING Griffith experiments TESTED THE STRENGTH OF A GLASS FIBER AS A FUNCTION OF SIZE DEPARTMENT OF MINING, METALLURGICAL AND MATERIALS ENGINEERING Griffith experiments 𝝈𝑼𝑻𝑺 = 𝑬⁄𝟏𝟎 𝝈𝑼𝑻𝑺 ≪ 𝑬⁄𝟏𝟎 Deflection DEPARTMENT OF MINING, METALLURGICAL AND MATERIALS ENGINEERING Griffith Theory This weakness is due to the presence of FLAWS in the material! Griffith explains that all materials are fabricated with a multitude of cracks! CRACKS ARE CONSIDERED STRESS CONCENTRATORS! DEPARTMENT OF MINING, METALLURGICAL AND MATERIALS ENGINEERING The Inglis solution STRESS CONCENTRATES or is AMPLIFIED at the CRACK TIP STRESS diminishes away from the TIP INGLIS SOLUTION æ aö æ aö s max = s o ç1 + 2 ÷ = s o çç1 + 2 ÷ ÷ è bø è r ø DEPARTMENT OF MINING, METALLURGICAL AND MATERIALS ENGINEERING Fracture Topography: Tensile overload, Torsion overload, fatigue and creep DEPARTMENT OF MINING, METALLURGICAL AND MATERIALS ENGINEERING Fracture mode and fracture mechanism FRACTURE MODE üHow did the product fail? üMacromechanism DEPARTMENT OF MINING, METALLURGICAL AND MATERIALS ENGINEERING Fracture mode and fracture mechanism FRACTURE MECHANISM CORROSION üWhat phenomenon lead to failure? ELECTRICAL OVERSTRESS üMicromechanism ELECTROSTATIC DISCHARGE DEPARTMENT OF MINING, METALLURGICAL AND MATERIALS ENGINEERING Fracture mode and fracture mechanism FRACTURE MODE FRACTURE MECHANISM üHow did the product üWhat phenomenon fail? lead to failure? üMacromechanism üMicromechanism DEPARTMENT OF MINING, METALLURGICAL AND MATERIALS ENGINEERING Tensile Overload FRACTURE TOPOGRAPHY DEPARTMENT OF MINING, METALLURGICAL AND MATERIALS ENGINEERING Tensile Overload Assumptions: v Uniaxial external loading v Monotonically increasing load Fracture Surface depends on: v Type of material v Microstructure v Testing conditions DEPARTMENT OF MINING, METALLURGICAL AND MATERIALS ENGINEERING Modes of failure DUCTILE BRITTLE FRACTURE FRACTURE DEPARTMENT OF MINING, METALLURGICAL AND MATERIALS ENGINEERING Brittle Fracture MODE OF FAILURE (TENSILE OVERLOAD) DEPARTMENT OF MINING, METALLURGICAL AND MATERIALS ENGINEERING Brittle Fracture FLAT AND ABSENCE OF GROSS GRAINY PLASTIC DEFORMATION FRACTURE BEFORE FRACTURE SURFACE DEPARTMENT OF MINING, METALLURGICAL AND MATERIALS ENGINEERING Types of Brittle Fracture TRANSGRANULAR/ INTERGRANULAR – CUTS CLEAVAGE - CUTS ACROSS BETWEEN GRAINS (THRU GRAINS GB) DEPARTMENT OF MINING, METALLURGICAL AND MATERIALS ENGINEERING FEATURES OF BRITTLE TRANSGRANULAR FRACTURE DEPARTMENT OF MINING, METALLURGICAL AND MATERIALS ENGINEERING Brittle fracture (Trans): Cleavage Transgranular brittle fracture – Occurs along the (100) crystallographic planes of the ferrite in steel Source: McEvily (2013) DEPARTMENT OF MINING, METALLURGICAL AND MATERIALS ENGINEERING Brittle fracture (Trans): River patterns A number of tear lines that merges and disappears – Useful aid in the determination of the local direction of crack propagation since tear lines tend Source: McEvily (2013) to be perpendicular to the crack front DEPARTMENT OF MINING, METALLURGICAL AND MATERIALS ENGINEERING Brittle fracture (Trans): Chevron Markings macroscopic tear lines that run perpendicular to the curved crack and diverge as the crack Source: realiabilityweb.com extends tips of the chevrons point toward the origin of the fracture DEPARTMENT OF MINING, METALLURGICAL AND MATERIALS ENGINEERING Brittle fracture (Trans): Chevron Markings Very important feature in reconstructing the path and locating the fracture origin DEPARTMENT OF MINING, METALLURGICAL AND MATERIALS ENGINEERING Brittle Intergranular Fracture Due to weak grain boundaries. DEPARTMENT OF MINING, METALLURGICAL AND MATERIALS ENGINEERING Brittle Intergranular Fracture Occur because of a weakness of the grain boundaries, which is often due to the segregation of impurity elements to the grain boundaries during processing and heat treatment DEPARTMENT OF MINING, METALLURGICAL AND MATERIALS ENGINEERING FEATURE OF BRITTLE INTERGRANULAR FRACTURE DEPARTMENT OF MINING, METALLURGICAL AND MATERIALS ENGINEERING Brittle Fracture (Inter): Rock candy Source: siamkaewkumsai.blogspot Source: Plymouth University DEPARTMENT OF MINING, METALLURGICAL AND MATERIALS ENGINEERING Ductile Fracture MODE OF FAILURE (TENSILE OVERLOAD) DEPARTMENT OF MINING, METALLURGICAL AND MATERIALS ENGINEERING Ductile Fracture NECKING INDICATES PLASTIC DEFORMATION CUP AND CONE FRACTURE PRESENCE OF A SIGNIFICANT AMOUNT OF DEFORMATION BEFORE FRACTURE DEPARTMENT OF MINING, METALLURGICAL AND MATERIALS ENGINEERING Crack propagation in ductile fracture a) necking b) cavity formation c) cavity coalescence to form cracks d) crack propagation e) fracture DEPARTMENT OF MINING, METALLURGICAL AND MATERIALS ENGINEERING FEATURE OF DUCTILE FRACTURE DEPARTMENT OF MINING, METALLURGICAL AND MATERIALS ENGINEERING Ductile fracture: cup and cone Cup and cone with flat central portion of the fracture – Transgranular, noncrystallographic voids are formed by the void linking process Source: Vermont Technical College DEPARTMENT OF MINING, METALLURGICAL AND MATERIALS ENGINEERING Ductile fracture: dimples Linked-up voids give rise to this feature – circular in shape at the flat part of the fracture Source: McEvily (2013) DEPARTMENT OF MINING, METALLURGICAL AND MATERIALS ENGINEERING Ductile fracture: dimples Linked-up voids give rise to this feature – elongated in the cone portion of the fracture rupture where shearing is dominant Source: McEvily (2013) DEPARTMENT OF MINING, METALLURGICAL AND MATERIALS ENGINEERING Ductile fracture: dimples Source: Filho, et. al (2011) DEPARTMENT OF MINING, METALLURGICAL AND MATERIALS ENGINEERING Torsion Overload FRACTURE TOPOGRAPHY DEPARTMENT OF MINING, METALLURGICAL AND MATERIALS ENGINEERING Torsion Overload σ1 Appearance depends on the nature of the material (brittle vs. Ductile) σ1 DEPARTMENT OF MINING, METALLURGICAL AND MATERIALS ENGINEERING Mode of failure in Torsion Ductile Fracture Brittle Fracture DEPARTMENT OF MINING, METALLURGICAL AND MATERIALS ENGINEERING Failure in Torsion: Ductile Fracture e.g. low-carbon steel twisted through several revolutions before failure – Failure is in plane of maximum shear stress at right angles to the axis of the bar – there is little reduction in area and little, if any, elongation DEPARTMENT OF MINING, METALLURGICAL AND MATERIALS ENGINEERING Failure in Torsion: Brittle Fracture e.g. gray cast iron twisted to fracture – the strains involved are much less and the failure is of helical nature – fracture plane is at 45o to the axis of the bar, perpendicular to the direction of the principal tensile stress Source: failurecriteria.com DEPARTMENT OF MINING, METALLURGICAL AND MATERIALS ENGINEERING Torsion Overload Swirl pattern Splined shaft which broke in torsion overload made of 6118 steel [23 Rockwell C]. DEPARTMENT OF MINING, METALLURGICAL AND MATERIALS ENGINEERING Torsion Overload 45º Fracture Origin AISI 10B62 Steel wire fractured in a 1035 Steel Drive Shaft failed in a ductile manner. brittle manner DEPARTMENT OF MINING, METALLURGICAL AND MATERIALS ENGINEERING Fatigue FRACTURE TOPOGRAPHY DEPARTMENT OF MINING, METALLURGICAL AND MATERIALS ENGINEERING Fatigue The process of progressive localized permanent structural change occurring in a material subjected to conditions that produce fluctuating stresses and strains at some point or points and that may culminate in cracks or complete fracture after a sufficient number of fluctuations. Source: Metals Handbook, ASTM 1985. DEPARTMENT OF MINING, METALLURGICAL AND MATERIALS ENGINEERING Fatigue fracture: 2 distinct features 1. Smooth or burnished – result of rubbing of the bottom and top of the crack – crack propagation – Fatigue zone 2. Granular – due to rapid failure of the material – indicates brittle failure – Rupture zone DEPARTMENT OF MINING, METALLURGICAL AND MATERIALS ENGINEERING Fatigue fracture: 2 distinct features 1. Smooth or burnished – result of rubbing of the bottom and top of the crack – crack propagation – Fatigue zone 2. Granular – due to rapid failure of the material – indicates brittle failure – Rupture zone DEPARTMENT OF MINING, METALLURGICAL AND MATERIALS ENGINEERING Fatigue fracture: 2 distinct features 1. Smooth or burnished – result of rubbing of the bottom and top of the crack – crack propagation – Fatigue zone 2. Granular – due to rapid failure of the material – indicates brittle failure – Rupture zone DEPARTMENT OF MINING, METALLURGICAL AND MATERIALS ENGINEERING FEATURES OF FATIGUE FRACTURE DEPARTMENT OF MINING, METALLURGICAL AND MATERIALS ENGINEERING Fatigue Fracture: Beach marks a.k.a. clamshell marks seen on parts that are used for a period of time, allowed to rest for an equivalent time period and then loaded again crack grows intermittently during random variation in the loading pattern DEPARTMENT OF MINING, METALLURGICAL AND MATERIALS ENGINEERING Fatigue Fracture: Beach marks a.k.a. clamshell marks seen on parts that are used for a period of time, allowed to rest for an equivalent time period and then loaded again crack grows intermittently during random variation in the loading pattern source: learncrew.com bridge of eyeglasses DEPARTMENT OF MINING, METALLURGICAL AND MATERIALS ENGINEERING Fatigue Fracture: Beach marks source: learncrew.com DEPARTMENT OF MINING, METALLURGICAL AND MATERIALS ENGINEERING Fatigue Fracture: Striations considered steps in crack propagation where the distance depends on the stress range one beach mark may contain thousands of striations represent crack growth, i.e. crack at constant amplitude loading DEPARTMENT OF MINING, METALLURGICAL AND MATERIALS ENGINEERING Fatigue Fracture The relative size of the rupture zone compared with the fatigue zone relates the degree of overstress applied and also about the variation in loading pattern –HIGHLY OVERSTRESSED Area of the fatigue zone is very small compared with the area of rupture zone DEPARTMENT OF MINING, METALLURGICAL AND MATERIALS ENGINEERING Fatigue Fracture The relative size of the rupture zone compared with the fatigue zone relates the degree of overstress applied and also about the variation in loading pattern –MEDIUM OVERSTRESS Size or area of both zones are nearly equal DEPARTMENT OF MINING, METALLURGICAL AND MATERIALS ENGINEERING Fatigue Fracture The relative size of the rupture zone compared with the fatigue zone relates the degree of overstress applied and also about the variation in loading pattern –LOW OVERSTRESS Area of rupture zone is very small DEPARTMENT OF MINING, METALLURGICAL AND MATERIALS ENGINEERING Creep FRACTURE TOPOGRAPHY DEPARTMENT OF MINING, METALLURGICAL AND MATERIALS ENGINEERING Creep involves the continuous extension or compression of a material until it finally fractures associated with relatively high temperatures DEPARTMENT OF MINING, METALLURGICAL AND MATERIALS ENGINEERING Creep controlled by the ratio of service temperature to the melting point of the material – 40% of the melting point of the material DEPARTMENT OF MINING, METALLURGICAL AND MATERIALS ENGINEERING Creep Failure DEPARTMENT OF MINING, METALLURGICAL AND MATERIALS ENGINEERING Creep Failure DEPARTMENT OF MINING, METALLURGICAL AND MATERIALS ENGINEERING Creep Rupture DEPARTMENT OF MINING, METALLURGICAL AND MATERIALS ENGINEERING Thank you for listening. J DEPARTMENT OF MINING, METALLURGICAL AND MATERIALS ENGINEERING References “Advance Introduction to Fatigue” ESDEP lecture notes [WG12] Gerard Hawkins, “Reformer Tube Metallurgy: Design Considerations, Failure Mechanisms, Inspection Methods.” GBH Enterprises Ltd. AW Batchelor, LN Lam, M Chandrasekaran (2011). Materials Degradation and its Control by Surface Engineering. World Scientific Publishing Co. Pte. Ltd. DEPARTMENT OF MINING, METALLURGICAL AND MATERIALS ENGINEERING Wear Prevention: Coating Technologies Eden May Dela Peña, PhD Department of Mining, Metallurgical and Materials Engineering College of Engineering, UP Diliman DEPARTMENT OF MINING, METALLURGICAL AND MATERIALS ENGINEERING Copyright notice This material has been reproduced and communicated to you by or on behalf of University of the Philippines pursuant to PART IV: The Law on Copyright of Republic Act (RA) 8293 or the “Intellectual Property Code of the Philippines”. The University does not authorize you to reproduce or communicate this material. The Material may contain works that are subject to copyright protection under RA 8293. Any reproduction and/or communication of the material by you may be subject to copyright infringement and the copyright owners have the right to take legal action against such infringement. Do not remove this notice. DEPARTMENT OF MINING, METALLURGICAL AND MATERIALS ENGINEERING In this lecture… Discrete coatings Integral coatings DEPARTMENT OF MINING, METALLURGICAL AND MATERIALS ENGINEERING An engineer should know at least… üWhich coating offers a particular form of protection, e.g. wear or corrosion? üHow is the coating be generated? üWhat resources of material and equipment are required for the coating process? DEPARTMENT OF MINING, METALLURGICAL AND MATERIALS ENGINEERING Discrete coatings range from the familiar paint, varnish and enamel to advanced coatings DEPARTMENT OF MINING, METALLURGICAL AND MATERIALS ENGINEERING Classification of Discrete Coatings Technologies DEPARTMENT OF MINING, METALLURGICAL AND MATERIALS ENGINEERING Classification of Discrete Coatings Technologies DEPARTMENT OF MINING, METALLURGICAL AND MATERIALS ENGINEERING Paints and varnishes Paints and other organic coatings are deposited on a surface in a liquid state to form a liquid film that is distributed over a surface-by surface tension forces. DEPARTMENT OF MINING, METALLURGICAL AND MATERIALS ENGINEERING Mechanism of Film Formation Polymerization reactions in this liquid film that are initiated by contact with e.g. atmospheric oxygen, ultra-violet light then converts the liquid film to a more durable solid film. DEPARTMENT OF MINING, METALLURGICAL AND MATERIALS ENGINEERING Ingredients of paints DEPARTMENT OF MINING, METALLURGICAL AND MATERIALS ENGINEERING Solvents Ø provide liquid medium during storage and deposition. DEPARTMENT OF MINING, METALLURGICAL AND MATERIALS ENGINEERING Solvents Ø provide liquid medium during storage and deposition. Ø can be an organic fluid such as white spirit, water or a mixture of both. Other organic solvents used are xylene, toluene, ketones, alcohols and halogenated compounds DEPARTMENT OF MINING, METALLURGICAL AND MATERIALS ENGINEERING Solvents Ø provide liquid medium during storage and deposition. Ø can be an organic fluid such as white spirit, water or a mixture of both. Other organic solvents used are xylene, toluene, ketones, alcohols and halogenated compounds Ø During coating, the solvent evaporates after a short period of exposure to air and serves no further purpose to the organic coating. DEPARTMENT OF MINING, METALLURGICAL AND MATERIALS ENGINEERING Ingredients of paints DEPARTMENT OF MINING, METALLURGICAL AND MATERIALS ENGINEERING Binder resin Ø polymerizes or “cures” to form a solid matrix for the organic coating. DEPARTMENT OF MINING, METALLURGICAL AND MATERIALS ENGINEERING Binder resin Ø polymerizes or “cures” to form a solid matrix for the organic coating. Ø Phenolic resins, cellulose derivatives, melamine derivatives, epoxy resins and elastomeric resins are all used as binder resins. DEPARTMENT OF MINING, METALLURGICAL AND MATERIALS ENGINEERING Ingredients of paints DEPARTMENT OF MINING, METALLURGICAL AND MATERIALS ENGINEERING Pigments Ø provide color to the paint but may also provide an anticorrosion effect.. ØInorganic metal salts, e.g. zinc phosphate and zinc chromate is widely used as pigments. DEPARTMENT OF MINING, METALLURGICAL AND MATERIALS ENGINEERING Ingredients of paints DEPARTMENT OF MINING, METALLURGICAL AND MATERIALS ENGINEERING Extenders Ø finely ground material that provides easier application of paint, greater adhesive properties and water resistance Økaolin (white clay), mica, talc, calcium carbonate (chalk). DEPARTMENT OF MINING, METALLURGICAL AND MATERIALS ENGINEERING Ingredients of paints DEPARTMENT OF MINING, METALLURGICAL AND MATERIALS ENGINEERING Dryers Øadded in small quantities to the paint to control the drying and polymerization process. Øusually fatty acid esters of cobalt, manganese, lead, vanadium and other metals. DEPARTMENT OF MINING, METALLURGICAL AND MATERIALS ENGINEERING Ingredients of paints DEPARTMENT OF MINING, METALLURGICAL AND MATERIALS ENGINEERING Other Additives ØFUNGICIDES: prevent moulds from growing on the paint surface. DEPARTMENT OF MINING, METALLURGICAL AND MATERIALS ENGINEERING Advantages of paints ü range of size of painted components is also much larger than most other coating technologies DEPARTMENT OF MINING, METALLURGICAL AND MATERIALS ENGINEERING Advantages of paints ü range of size of painted components is also much larger than most other coating technologies ü no requirement for specialized and restrictive technology as is the case with vacuum deposition DEPARTMENT OF MINING, METALLURGICAL AND MATERIALS ENGINEERING Advantages of paints ü range of size of painted components is also much larger than most other coating technologies ü no requirement for specialized and restrictive technology as is the case with vacuum deposition ü cheaper and more convenient to use DEPARTMENT OF MINING, METALLURGICAL AND MATERIALS ENGINEERING Advantages of paints ü range of size of painted components is also much larger than most other coating technologies ü no requirement for specialized and restrictive technology as is the case with vacuum deposition ü cheaper and more convenient to use ü do not normally react with a substrate DEPARTMENT OF MINING, METALLURGICAL AND MATERIALS ENGINEERING Advantages of paints ü range of size of painted components is also much larger than most other coating technologies ü no requirement for specialized and restrictive technology as is the case with vacuum deposition ü cheaper and more convenient to use ü do not normally react with a substrate ü normally performed at ambient temperature DEPARTMENT OF MINING, METALLURGICAL AND MATERIALS ENGINEERING Categories of coatings Ø Decoration Ø Protection of wood Ø Vehicles and aircraft Ø Industrial use Ø Marine use Ø Anti-corrosion DEPARTMENT OF MINING, METALLURGICAL AND MATERIALS ENGINEERING Decorative brightly colored vehicles brightly colored buildings DEPARTMENT OF MINING, METALLURGICAL AND MATERIALS ENGINEERING Categories of coatings Ø Decoration Ø Protection of wood Ø Vehicles and aircraft Ø Industrial use Ø Marine use Ø Anti-corrosion DEPARTMENT OF MINING, METALLURGICAL AND MATERIALS ENGINEERING Protection of wood DEPARTMENT OF MINING, METALLURGICAL AND MATERIALS ENGINEERING Categories of coatings Ø Decoration Ø Protection of wood Ø Vehicles and aircraft Ø Industrial use Ø Marine use Ø Anti-corrosion DEPARTMENT OF MINING, METALLURGICAL AND MATERIALS ENGINEERING Vehicles and aircraft UNDERBODY PAINT: resistance to chipping and blistering AIRCRAFT COATING: resistance from water droplets at speeds of 200m/s or more DEPARTMENT OF MINING, METALLURGICAL AND MATERIALS ENGINEERING Categories of coatings Ø Decoration Ø Protection of wood Ø Vehicles and aircraft Ø Industrial use Ø Marine use Ø Anti-corrosion DEPARTMENT OF MINING, METALLURGICAL AND MATERIALS ENGINEERING Industrial use coatings sewage processing oil refinery equipment Ø to prevent a metal component from corrosion in a severe environment DEPARTMENT OF MINING, METALLURGICAL AND MATERIALS ENGINEERING Categories of coatings Ø Decoration Ø Protection of wood Ø Vehicles and aircraft Ø Industrial use Ø Marine use Ø Anti-corrosion DEPARTMENT OF MINING, METALLURGICAL AND MATERIALS ENGINEERING Marine use Ø resistant to salt water corrosion Ø resistant to the mechanical stresses at ‘splash zone’ Ø resistant to ‘biocidal affect’ DEPARTMENT OF MINING, METALLURGICAL AND MATERIALS ENGINEERING Categories of coatings Ø Decoration Ø Protection of wood Ø Vehicles and aircraft Ø Industrial use Ø Marine use Ø Anti-corrosion DEPARTMENT OF MINING, METALLURGICAL AND MATERIALS ENGINEERING Anti-corrosion coatings Ø organic coatings, which do not merely act as passive separators of metal substrate and corrosive reagents but also actively suppress corrosion. DEPARTMENT OF MINING, METALLURGICAL AND MATERIALS ENGINEERING Usage of organic coatings as a function of resin type DEPARTMENT OF MINING, METALLURGICAL AND MATERIALS ENGINEERING Deposition of paints manual brushing adsorbent roller spraying DEPARTMENT OF MINING, METALLURGICAL AND MATERIALS ENGINEERING More environmentally friendly alternative high solid paints powder coating DEPARTMENT OF MINING, METALLURGICAL AND MATERIALS ENGINEERING High solid paints Ø a paint that is formulated to have a higher concentration of resin and a smaller concentration of volatile organic compounds (VOC). Ø Most aircraft paint manufacturers offer some type of high solids paint product. DEPARTMENT OF MINING, METALLURGICAL AND MATERIALS ENGINEERING Spray coatings Ø deposited on the substrate by electrostatic spraying to ensure uniform coverage Ø large-scale manufacture of metal items such as cars DEPARTMENT OF MINING, METALLURGICAL AND MATERIALS ENGINEERING Corrosion problems of organic coatings not completely impermeable to water and oxygen DEPARTMENT OF MINING, METALLURGICAL AND MATERIALS ENGINEERING Classification of Discrete Coatings Technologies DEPARTMENT OF MINING, METALLURGICAL AND MATERIALS ENGINEERING Electrochemical coatings DEPARTMENT OF MINING, METALLURGICAL AND MATERIALS ENGINEERING Electroplating of metals Øcaused by cathodic reactions leading to the reduction of metal from solution and evolution of hydrogen or oxygen. Ø nickel, chromium and cadmium DEPARTMENT OF MINING, METALLURGICAL AND MATERIALS ENGINEERING Electroplating of metals Large tanks of metal salt solution with attached power supply DEPARTMENT OF MINING, METALLURGICAL AND MATERIALS ENGINEERING Chromium plating Ø for decorative and industrial purposes Ø trivalent or hexavalent chromium can be used DEPARTMENT OF MINING, METALLURGICAL AND MATERIALS ENGINEERING Anodizing Øapplication of anodic electrochemical reactions to form a coating on a metal substrate DEPARTMENT OF MINING, METALLURGICAL AND MATERIALS ENGINEERING Anodizing ØCoating formation rates are approximately 1μm/min at a current density of 25 A/m2 and coating thickness of 20μm are typical. DEPARTMENT OF MINING, METALLURGICAL AND MATERIALS ENGINEERING Electroless coatings Ø similar to electroplated coatings with no power supply needed Ø wide variety of applications: metal coatings on plastics and ceramic substrates DEPARTMENT OF MINING, METALLURGICAL AND MATERIALS ENGINEERING Mechanism of electroless plating BASIC PRINCIPLES: spontaneous deposition of metal from a solution (e.g. hydrophospate) DEPARTMENT OF MINING, METALLURGICAL AND MATERIALS ENGINEERING Classification of Discrete Coatings Technologies DEPARTMENT OF MINING, METALLURGICAL AND MATERIALS ENGINEERING Plasma spraying The picture can't be displayed. Ø spraying of molten or heat softened material onto a surface to provide a coating. Material in the form of powder is injected into a very high temperature plasma flame, where it is rapidly heated and accelerated to a high velocity. DEPARTMENT OF MINING, METALLURGICAL AND MATERIALS ENGINEERING Plasma spraying the droplets of coating remain liquid transfer of material as discrete for a sufficient period of time to merge droplets from coating source to and form a continuous surface layer substrate. DEPARTMENT OF MINING, METALLURGICAL AND MATERIALS ENGINEERING Plasma spaying apparatus DEPARTMENT OF MINING, METALLURGICAL AND MATERIALS ENGINEERING Adhesion mechanism: coating and interface Ø Mechanical interlock is a physical keying between an often deliberately roughened substrate and a coating that is in very close contact with the substrate. DEPARTMENT OF MINING, METALLURGICAL AND MATERIALS ENGINEERING Major limitation? Ø substrate must have a moderately high melting point Ø APPLICATIONS: Aerospace components, orthopedic endoprostheses DEPARTMENT OF MINING, METALLURGICAL AND MATERIALS ENGINEERING D-gun Ø Detonation gun DEPARTMENT OF MINING, METALLURGICAL AND MATERIALS ENGINEERING D-gun Ø Detonation gun Ø based on a cyclic detonation of combustible gas in a chamber with an exit directed at the substrate DEPARTMENT OF MINING, METALLURGICAL AND MATERIALS ENGINEERING D-gun Ø Detonation gun Ø based on a cyclic detonation of combustible gas in a chamber with an exit directed at the substrate Ø substrate is blasted with a hot gas containing molten droplets of coating. DEPARTMENT OF MINING, METALLURGICAL AND MATERIALS ENGINEERING Mechanism of D-gun deposition particles of coating must deform to a lamellar shape in order to form a coherent strong coating DEPARTMENT OF MINING, METALLURGICAL AND MATERIALS ENGINEERING Classification of Discrete Coatings Technologies DEPARTMENT OF MINING, METALLURGICAL AND MATERIALS ENGINEERING Vacuum deposition Ø coating metal is electrically heated in a crucible until it either melts or otherwise begins to release large quantities of vapor, i.e. sublime. DEPARTMENT OF MINING, METALLURGICAL AND MATERIALS ENGINEERING Principles of vapor deposition vapor spreads to fill the entire vacuum chamber metal coatings are deposited in this manner with no significant thermal damage to the substrate DEPARTMENT OF MINING, METALLURGICAL AND MATERIALS ENGINEERING In this lecture… Ø Discrete coatings Ø Integral coatings DEPARTMENT OF MINING, METALLURGICAL AND MATERIALS ENGINEERING Integral Coatings coatings that have no distinguishable boundary with the substrate DEPARTMENT OF MINING, METALLURGICAL AND MATERIALS ENGINEERING Integral Coatings PROBLEM: Boundary between a coating and substrate is often the greatest source of weakness for a coating DEPARTMENT OF MINING, METALLURGICAL AND MATERIALS ENGINEERING Integral Coatings SOLUTION: Create a diffuse interface where a distinct boundary is absent DEPARTMENT OF MINING, METALLURGICAL AND MATERIALS ENGINEERING Integral Coatings: Categories DEPARTMENT OF MINING, METALLURGICAL AND MATERIALS ENGINEERING Integral Coatings boundary between coating and its substrate– greatest source of weakness Hardness of coatings and substrates are usually different and high mechanical stresses can be generated if hardness transition is abrupt DEPARTMENT OF MINING, METALLURGICAL AND MATERIALS ENGINEERING Strength mechanism of integral coating Integral coatings are often stronger than the corresponding discrete coating of identical chemical composition because of the lack of acute stress gradient at the substrate-coating boundary. DEPARTMENT OF MINING, METALLURGICAL AND MATERIALS ENGINEERING Categories: Microstructurally modified surface layers ü Shot peening ü Surface hardening by laser or electron beam DEPARTMENT OF MINING, METALLURGICAL AND MATERIALS ENGINEERING Categories: Microstructurally modified surface layers ü Shot peening ü Surface hardening by laser or electron beam DEPARTMENT OF MINING, METALLURGICAL AND MATERIALS ENGINEERING Shot peening Ø process where a metal specimen is impacted by a larger number of small steel balls with diameter ranging from 0.18 to 2.00 mm. DEPARTMENT OF MINING, METALLURGICAL AND MATERIALS ENGINEERING Shot peening PURPOSE: Ø introduce residual compressive stresses in the surface of the component. Ø This residual compressive stress delays fatigue crack initiation thereby increasing their fatigue life. DEPARTMENT OF MINING, METALLURGICAL AND MATERIALS ENGINEERING DEPARTMENT OF MINING, METALLURGICAL AND MATERIALS ENGINEERING Applications of Shot Peening Helical springs Torsion bars for automotive and aerospace applications Transmission shafts DEPARTMENT OF MINING, METALLURGICAL AND MATERIALS ENGINEERING Metallurgical cross section of a shot-peened steel DEPARTMENT OF MINING, METALLURGICAL AND MATERIALS ENGINEERING Categories: Microstructurally modified surface layers ü Shot peening ü Surface hardening by laser or electron beam DEPARTMENT OF MINING, METALLURGICAL AND MATERIALS ENGINEERING Electron beam hardening üshort surface hardening procedure for martensitically hardenable ferrous materials using the energy transferred by electron beams DEPARTMENT OF MINING, METALLURGICAL AND MATERIALS ENGINEERING Laser beam hardening üshort surface hardening procedure for martensitically hardenable ferrous materials using the energy transferred by laser beams DEPARTMENT OF MINING, METALLURGICAL AND MATERIALS ENGINEERING Laser beam hardening DEPARTMENT OF MINING, METALLURGICAL AND MATERIALS ENGINEERING EB Hardening vs LB Hardening EB Hardening LB Hardening needs vacuum does not need vacuum distance between source and distance between source and component is relatively small component is relatively high beam guidance by beam guidance by mirrors electromagnetic coils and lenses bulk components can not be bulk components can be hardened due to inability to hardened easily place them in vacuum high efficiency low efficiency DEPARTMENT OF MINING, METALLURGICAL AND MATERIALS ENGINEERING Integral Coatings: Categories DEPARTMENT OF MINING, METALLURGICAL AND MATERIALS ENGINEERING Hot-dipping Ø most effective when there is a large difference between the melting point of the coating metal and the melting point of the substrate metal. DEPARTMENT OF MINING, METALLURGICAL AND MATERIALS ENGINEERING Hot-dipping DEPARTMENT OF MINING, METALLURGICAL AND MATERIALS ENGINEERING Hot-dipping: Galvanization Øspecialized form of hot-dipping, develops alloyed and intermetallic compound layers on metal surfaces by dipping the entire metal component into a bath of molten metal. DEPARTMENT OF MINING, METALLURGICAL AND MATERIALS ENGINEERING Hot-dipping: Galvanization Øprocess of applying a protective zinc coating to prevent rusting. Øcommon application are zinc on steel and tin on steel. DEPARTMENT OF MINING, METALLURGICAL AND MATERIALS ENGINEERING Structure of Hot-Dipped Coating Ø has a multi-phase laminar microstructure Ø possesses very strong bonding to the substrate because of the reaction between iron and zinc and so almost never peels off the substrate. DEPARTMENT OF MINING, METALLURGICAL AND MATERIALS ENGINEERING Feedback Top 3 things you learned today Muddy points. You may ask questions here. Comments and/or suggestions on how the class was handled. You may raise any concern/s you have in class. D E P A R T M E N T O F M I N I N G, M E T A L L U R G I C A L A N D M A T E R I A L S E N G I N E E R I N G Thank you for listening. J DEPARTMENT OF MINING, METALLURGICAL AND MATERIALS ENGINEERING