Lean Practitioner – Practise PDF
Document Details
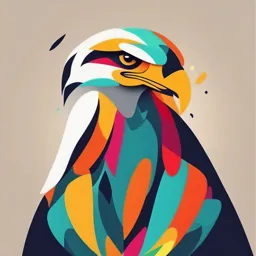
Uploaded by AdvancedMorningGlory3205
Tags
Summary
This document provides an overview of Gemba walks, a Lean management practice focused on observing real work processes. It explains the importance of going to the Gemba (the real place), asking "why", and respecting people in the process. The document also covers steps to properly conduct a Gemba walk, including preparing a team and focusing on processes, not people.
Full Transcript
Going to a Gemba Walk: See Where the Real Work Happens Gemba walk is an opportunity to capture topics and concerns related to how effectively your team is performing. Learn what you should do when doing a Gemba walk. Go back...
Going to a Gemba Walk: See Where the Real Work Happens Gemba walk is an opportunity to capture topics and concerns related to how effectively your team is performing. Learn what you should do when doing a Gemba walk. Go back to all Getting Started Value and Waste Pull Systems Continuous Improvement What Is Kaizen? What Is Continuous Improvement? Built-In Quality Management What Is the Poka-Yoke Technique? What Is the PDCA (Plan Do Check Act) Cycle? 5 Whys: The Ultimate Root Cause Analysis Tool Gemba Walk: Where the Real Work Happens A3 Problem-Solving: Fight the Root Cause Root Cause Analysis Hoshin Kanri Lean Transformation Continuous Flow What Is Lean Six Sigma? Lean Project Management Share on: Insanity is doing the same thing over and over again and expecting different results. From such a perspective, most of the contemporary managers seem to be insane. Why? Because you cannot expect different results from your team by sitting in your corner office and only attending KPI meetings. Instead, you need to see where the real work happens. You need to do Gemba walks. The Gemba walk is an essential part of the Lean management philosophy. Its initial purpose is to allow managers and leaders to observe the actual work process, engage with employees, gain knowledge about the work process, and explore opportunities for continuous improvement. Let’s explore the Gemba walk in detail. What Is a Gemba Walk Actually? The term “Gemba” comes from Japanese, and it means “the real place”. In Lean management, “Gemba” is the most important place for a team as it is the place where the real work happens. Quite simply, for rock bands, the “Gemba” is the recording studio. For Formula 1 teams, the “Gemba” is wherever the car is. For manufacturers, it’s the factory floor and so on. In other words, it is where the real work happens, so you can observe and analyze it. The Gemba walk is a concept developed by Taiichi Ohno, who is often considered the father of Just-in-time production. By developing such a concept, Ohno offers a real opportunity for executives to leave their daily routine, see where the real work happens, and build relationships with workers based on mutual trust. There are 3 important elements of this lean manufacturing tool: 1. Go and see. The main idea of the Gemba walk is for managers and leaders on every level to take regular walks around the shop floor and to be involved in finding wasteful activities. 2. Ask why. A Gemba walk's main objective is to explore the value stream in detail and locate its problematic parts through active communication. A good leader is always eager to listen rather than talk. Here is why you may use different techniques such as 5 whys in order to identify problematic parts of the process. 3. Respect people. Keep in mind that a Gemba walk is not a “boss walk”. Pointing fingers and blaming people is exactly what you don’t have to do. You are not there to judge and review results. You are there to collaborate with the team and find problems together. Try to focus on finding the weak spots of the process, not of the people. 7 Steps to Follow When You Go to Gemba Before you walk the shop floor, you need to make a plan and follow the steps. The plan should depend on your goals and objectives. Sometimes it may be unstructured, for example, if you are new to the organization, while in other cases, your plan will be much more precise because you will be more familiar with the details. In any case, be prepared for the Gemba walk. Otherwise, it will be inefficient. Now, let’s define some basic steps. 1. Pick a theme When you go to Gemba, you have to choose a theme. This will help you focus all your efforts and be effective. There are different themes you may want to explore, such as productivity, cost efficiency, safety and etc. In order to be as precise as possible, you will also need to prepare a list of questions you are going to ask. 2. Prepare your team The team that will be observed should be prepared for what is going to happen. All team members need to have a clear understanding that the Gemba walk is a common process where the final destination is continuous improvement. This way, workers will feel much more comfortable and willing to collaborate. 3. Focus on the process, not on people You need to remember that a Gemba walk is not the right time to evaluate your team's performance. The main purpose is to observe, understand, and improve the process. If you focus on people’s personal abilities, you will only face resistance. 4. Be where the value stream is Following the value stream chain will give you the best opportunities to identify areas with a high potential for waste activities. Eliminating those activities will help you improve your overall performance. 5. Record your observations. Don’t make suggestions during the walk Write down everything that grabs your attention or even record it with your smartphone. In some cases, you will probably be tempted to offer a solution immediately, but this would be wrong. Leave the analysis for later. You will be much more precise after you have all the facts available. Furthermore, the broad overview can offer you opportunities to use effective problem-solving tools such as the PDCA cycle. Much better than an instant gut feeling. 6. An extra pair of eyes It may be a good idea to invite a colleague from another department. Someone with totally different daily tasks. People who are less familiar with the processes usually have a fresh perspective and ask different questions that you may never ask. 7. Follow-up Even if you don’t find anything significant during your Gemba walk, you need to share with the team what you have learned or seen. Otherwise, the team will only have the feeling of being watched. If you are going to take action after the walk, inform the team about the upcoming changes and why they are necessary. 10 Years Kanban Experience In 1 Free Book. Project Manager's Guide to Kanban Download your free ebook Gemba Walk Checklist Every time when you perform a Gemba walk, you need to prepare a checklist in advance. This list will help you focus and target your efforts. The checklist has to include questions that will help you understand the process you are going to observe in a better way. Your questions may vary depending on the theme of your Gemba walk. Here are some basic Gemba walk checklist questions: These questions will defer when exploring different areas such as problem-solving, innovation, resources, tools and etc. So before you go, Gemba, prepare your checklist carefully based on the area you want to investigate. Post-Gemba Walk Before you take any actions based on your Gemba walk observations, you will need some time to organize your thoughts and notes. Feedback is important, but early feedback may be devastating. Here is why you need to sit down with the leadership team and carefully analyze the situation. You can even invite some of the workers who you’ve observed. For example, the ones who gave you the most insightful information. Use all the data that you collected as part of your continuous improvement process, also known as a Gemba Kaizen circle. It is a meeting held after each Gemba walk that may include a few participants from different departments. The main purpose is to have as many different points of view as possible to make the best decision. A decision that will actually bring improvement. It is important to go around the shop floor and collect insightful information about what needs improvement. However, what matters most is to go back to where you started. A post-Gemba walk closes the loop and shows respect to the people who have been observed. This will make it much easier to lead a successful Gemba walk in the future. Businessmap is the most flexible software platform for outcome-driven enterprise agility. Try Businessmap for free In Summary Performing Gemba walks on a regular basis can offer some significant advantages like: Building stable relationships with those who actually do the work and create value. Identifying problems and taking actions for achieving continuous improvement much faster. Clearly communicating goals and objectives leading to increased employee engagement. Definition of KAIZEN™ Over 50 years ago, Masaaki Imai introduced the term KAIZEN™ to the western world with his groundbreaking book ‘Kaizen: The Key to Japan’s Competitive Success’. Today, KAIZEN™ is recognized worldwide as a pillar of organizations’ long-term competitive strategy. “KAIZEN™ means improvement. Moreover, it means continuing improvement in personal life, home life, social life, and working life. When applied to the workplace KAIZEN™ means continuing improvement involving everyone – managers and workers alike.” Masaaki Imai, Founder of Kaizen Institute The Core of KAIZEN™ Download PDF Know your customer Always put the customer first. Let it flow Optimize processes for continuous workflow. Go to Gemba Observe the challenges firsthand on site. Empower people Encourage the active participation of all employees. Be transparent Adopt an open and honest communication approach. KAIZEN™ Methodology Development History The KAIZEN™ methodology has gradually developed over many decades. It was publicly and officially introduced to the world in the 1980s as a systematic methodology through the best-selling book “KAIZEN™” by Masaaki Imai, the founder of Kaizen Institute. 1930 Masaaki Imai is born in Tokyo, Japan. The first domestic automotive production is planned in Japan, and the Just-In-Time concept is observed. 1940 World War II to post-war economic reform period commences in Japan. 1950 Imai works at the Japan Productivity Center in the USA and accompanies Japanese executives to visit and learn from US manufacturers. Japanese companies gain strength in their quality and worldwide competitiveness. 1960 Imai works with Shoichiro Toyoda to observe the American way of business. 1980 Imai works internationally with Taiichi Ohno to spread the message of the Toyota Production System (TPS). 1986 KAIZEN™ is introduced to the world for the first time, as a systematic management methodology. 1990’s KAIZEN™ appears for the first time as a word in the Oxford dictionary. The term Lean was coined. Lean concepts are promoted through various publications, to include Imai’s GEMBAKAIZEN™ book. Tools, such as Six Sigma, gain popularity though clouding the importance of a systematic approach. Kaizen Institute continues to offer practical, hands-on methods that fit the local culture and business practice, when implementing KAIZEN™ within organizations. 2000’s KAIZEN™ Management System (KMS) is developed, to help companies to improve based on a systematic QCD Model. KAIZEN™ Change Model (KCM) is added to enhance a KAIZEN™ culture, mindset and behaviors of the organization. Many corporations start developing their own improvement strategies based on KAIZEN™, seeking to gain sustainable improvements and a competitive advantage within their markets. Today KAIZEN™ Business System (KBS) supports organizations to achieve Continuous Improvement and sustainable growth. Kaizen Institute continues to spearhead global development for the KAIZEN™ methodology, bringing awareness to Everyone, Everywhere, Everyday. The Most Important Lean KPIs You Need to Track for Your Business Dimitar Karaivanov CEO and Co-founder of Businessmap 8 mins read Published on: March 25, 2019 Last updated: May 14, 2024 Table of Contents: 1. Lean KPIs for Your Workflow 2. Lean KPIs for Your Digital Marketing 3. What’s the Bottom Line? You don't know whether you are successful or not if you don’t measure success. If you have a clear idea of what metrics describe success, then you can track progress and improve work process in order to achieve the desired outcome. As Peter Drucker said, "you can't manage what you can't measure." No matter the industry, you need to have a clear idea of how to measure success. This article will address what kind of Lean KPIs your company needs to track in order to make sure all parts of the business are doing fine. These KPIs will help you identify problems in the workflow, discover the full potential of a team and achieve continuous improvement. In the first part of the article, we will explore some lean metrics examples that will help you analyze your work processes and improve your workflow. After this, we will take a look at the metrics that play a crucial role in marketing performance. Before we start, let’s clarify that lean metrics are those ones, which can assist you in identifying true value from the perspective of your customer. Lean KPIs focus on measuring value and help you eliminate waste. Let's get rolling without further introductions. Lean KPIs for Your Workflow Average Lead Time [Days/Hours] One of the most important lean KPIs (if not the most important) to track is your average lead time to production. In a perfect world, this would mean the time it takes an idea to be converted to an actual product and deployed to production. In reality, the lead time is usually calculated as the time between the moment you start working on an idea to its full realization (the time it spends waiting is ignored because the customer doesn't care about it). If you are able to quickly convert ideas or users' feedback into an actual product, you will be a star and people will love you. On the contrary, if you are slow to deliver what your customers are asking for, then you risk losing them and making your competition happy. With this in mind, always track your lead times and try to improve them. It might be a good idea to classify your items into different classes so that metrics don't get skewed; e.g. average lead time per size, per priority, per customer, etc. Average Cycle Time [Days/Hours] Cycle time is another important lean metric you need to follow. Basically, cycle time begins at the moment when a new task enters “in progress” stage and somebody is actually working on it. If your workflow consists of several different sub-stages, then the lead time is practically the sum of the cycle times of all sub-processes that form the entire process of delivering goods. Let's explain that further. Suppose your entire process is "idea generation" -> "idea implementation" -> "feedback/testing" -> "deployment". The time a task spends in each of the stages is called cycle time and the sum of all cycle times equals the lead time. It's easy to realize that reducing the cycle time of all stages will lead to reduced lead time in the end. Try to reduce cycle time as much as possible, but at the same time be careful not to create local sub-optimums. For example, if "deployment" takes 10 days on average, but all other stages take only two, then reducing the cycle time of anything else besides the deployment phase will make things worse. In other words, be careful and optimize only where it makes sense. Distribution of Effort [%] What if you have the best lead and cycle times, but you only work on defects? This is obviously not acceptable and you should have a good idea of the time you spend working on value added activities vs. non-value added ones. This is easily achievable with any of the tools like Kanbanize by Businessmap - just put a type on each task (ticket) and then use the analytics module to review the data. The target is obvious: more features and fewer defects. Number of Items in Progress [Count] The big amount of work in progress is an enemy of your productivity as a company. The greater the number of items you work on at the same time, the more often your team will multitask. This will lead to more context switching between different tasks. Respectively, the cycle times will increase and therefore the lead times will follow. We've already explained that long lead times are bad, right? Consider imposing WIP (work in progress) limits to the different stages of your workflow by adopting the Kanban method. This will reduce stress and will improve the quality of your work. If you have WIP limits already, make sure that you always comply with them. Number of Open Issues [Count] This lean metric can be considered as appropriate for the SaaS industry. However, this is not strictly a SaaS KPI because issues appear in every business, no matter the industry. So let’s keep exploring. If you ship with known issues in your product, things are bad. Having a dozen open issues is somewhat okay. However, deploying with tens of open issues or hundreds of them (God forbid) is something you MUST tackle right away. Poor quality will kill you in the long run, and you should definitely take a closer look at the number of issues. Define a limit that must never be crossed and make sure to invest in fixing as many of the issues as you can (or makes sense). Number of Customer-reported (Open) Issues [count] This lean KPI is crucial and it will keep you on the right track. Nowadays, customer satisfaction is more important than ever before. Customer issues must be your top priority. Period. If a customer suffers, you are losing business and if you get too many complaints, you will soon be looking for another job. Define the target of 0 and work towards it. It may not always be possible to have zero open defects, but 90% of the time it should be like that. Track it, optimize it, control it. Number of Recurring Issues If there is anything worse than a customer issue, it is a recurring customer issue. The customer has reported it, you have fixed it, the customer was happy for a month, but then that same nasty issue reappeared. The customer is already asking herself "Do they know what they are doing at all?". You MUST NEVER allow that. It will happen once in a while, but when it does, be dead serious about it and do whatever it takes to prevent it from happening again. This is an important KPI for software development, but not only. So, track the number of recurring issues and if it becomes higher than zero you should do something about it. Cumulative Flow Diagram (Bonus) Many companies start using Kanban boards, so they can visualize their workflow and acquire a better understanding of their work processes. These businesses have the advantage of using cumulative flow diagrams (CFD). This diagram shows you the current state of your work. It can help you decide whether you need to speed up the peace, restructure your work, or increase your capacity. You can get actionable advice on where you need to focus your efforts in order to improve your process in a single glance. In the second part of our Lean KPIs article, we will talk about digital marketing. Nowadays, everyone who has managed a company knows that at some point, you must start investing in marketing and business development much more than in product/service development. Digital marketing has become an integral part of the marketing mix. Both for B2C and B2B. Growing your website’s visitors, brand awareness and, respectively, your company is probably the hardest thing you have to do, and the goal of this post is to suggest key metrics that you should collect, monitor, and act upon. Lean KPIs for Your Digital Marketing It’s All About Active Users You need to measure users. Nothing is more important than that, at least from the marketing point of view. The more users you get, the more you convert into customers, the more successful your company is. Be careful, though. If you focus on the total number of users or new users or anything else that doesn’t give you a good idea about the number of ACTIVE users, you might be the victim of your own self-deception. Total users always grow, new users, by definition, are something good. You may have 1,000,000 users, and you may be getting 100,000 more each month, but you would be horrified to discover that you have just 1,000 active! Measure whatever you want to measure, but make sure to know how many active users you have. Website Visits (+Unique Visitors + %New Visits) If you are in the e-commerce or SaaS industry, by definition, your website is your most important weapon. But even if you are in the FMCG or another sector, still your website is of the highest importance. If you do not track the number of visits, then you might not know whether your business is growing or shrinking. You can do that with Google Analytics or a similar tool but definitely track that on a regular basis. Pay attention to the number of unique visits. If you have a lot of visits from a handful of people, you might not be able to scale your company. Always remember that you need more and more new users, and therefore the unique visitors must also grow. Of course, you need to track the percentage of new users each week/month. Try to keep it constant or a growing number. If your new visits start going down, you should probably consider a marketing campaign (link building, paid campaigns, guest blogging, etc.). Bounce Rate The bounce rate is a lean metric that shows you how many people landed on your site and left it without going to another page. The lower your bounce rates are the better (it is usually % of all visits). A Bounce rate of 0-30% is good, 30-60% is tolerable but something to improve and anything above 60% is not good (all of these come from my own experience, numbers can vary from business to business). A key element to tackle the bounce rate is to experiment with your website – change your slogan, front page, registration form, etc. The obvious goal is to improve, but if you happen to make things worse, make sure to detect that ASAP and take the necessary steps to revert the breaking changes. This is only achievable through regular collection and analysis of the KPIs that we talk about. Again, don’t focus on the totals only. Your site is likely to have more than one landing page and each page has its own bounce rate. If your homepage has great bounce rate, but your pricing page performs terrible, you should probably think about your pricing, right? Last Page to Visit Visitors’ flow is somewhat hard to get in a comprehensive way, but a very important part of exploring your users' behavior. If there is a page on your website that visitors get to, but always leave after that, try to figure own why that happens. I will go no further with this part, because there are thousands of possible interpretations and I risk to mislead you, but please make some efforts to investigate. Social Engagement and Growth Just a few words here. If you have a social presence (Facebook, Twitter, G+, Linkedin, etc.) make it measurable, especially if you put a lot of effort into it. You might be active, but if your users’ engagement is low, there is probably something to be changed. Don’t just throw content out there, make it a quality work and not quantity work. From our own experience, people engage more easily on Twitter and Facebook, so you may start with them first. What’s the Bottom Line? All KPIs should be reviewed on a regular basis, preferably weekly. If a KPI looks bad, act on it, don't just wait to see if things got better by themselves. They won't :) Do whatever you can do to affect the numbers positively, experiment and track how your changes affect the status quo. There are probably many more lean KPIs that you can or should track. Each business is unique and the things that make sense monitoring vary. Start with your best guess and improve! Do you have a comment? We would be glad to see your replies in the comment section below. Muda (無駄) Muda means wastefulness, uselessness and futility, which is contradicting value-addition. Value-added work is a process that adds value to the product or service that the customer is willing to pay for. There are two types of Muda, Type 1 and Type 2. Muda Type 1 includes non-value-added activities in the processes that are necessary for the end customer. For example, inspection and safety testing does not directly add value to the final product; however, they are necessary activities to ensure a safe product for customers. Muda Type 2 includes non-value added activities in the processes, but these activities are unnecessary for the customer. As a result, Muda Type 2 should be eliminated. There are seven categories of waste under Muda Type 2 that follow the abbreviation TIMWOOD. The seven wastes are (1) Transport i.e. excess movement of product, (2) Inventory i.e. stocks of goods and raw materials, (3) Motion i.e. excess movement of machine or people, (4) Waiting, (5) Overproduction, (6) Over-processing, and (7) Defects. Mura (斑) Mura means unevenness, non-uniformity, and irregularity. Mura is the reason for the existence of any of the seven wastes. In other words, Mura drives and leads to Muda. For example, in a manufacturing line, products need to pass through several workstations during the assembly process. When the capacity of one station is greater than the other stations, you will see an accumulation of waste in the form of overproduction, waiting, etc. The goal of a Lean production system is to level out the workload so that there is no unevenness or waste accumulation. Mura can be avoided through the Just-In-Time ‘Kanban’ systems and other pull-based strategies that limits overproduction and excess inventory. The key concept of a Just-In-Time system is delivering and producing the right part, at the right amount, and at the right time. Muri (無理) Muri means overburden, beyond one’s power, excessiveness, impossible or unreasonableness. Muri can result from Mura and in some cases be caused by excessive removal of Muda (waste) from the process. Muri also exists when machines or operators are utilized for more than 100% capability to complete a task or in an unsustainable way. Muri over a period of time can result in employee absenteeism, illness, and breakdowns of machines. Standardize work can help avoid Muri by designing the work processes to evenly distribute the workload and not overburden any particular employee or equipment. What is 5S? More 5S Education 5S is a system for organizing spaces so work can be performed efficiently, effectively, and safely. This system focuses on putting everything where it belongs and keeping the workplace clean, which makes it easier for people to do their jobs without wasting time or risking injury. 5S Translation The term 5S comes from five Japanese words: Seiri Seiton Seiso Seiketsu Shitsuke In English, these words are often translated to: Sort Set in Order Shine Standardize Sustain Each S represents one part of a five-step process that can improve the overall function of a business. The Origins of 5S – 5S & Lean Manufacturing 5S began as part of the Toyota Production System (TPS), the manufacturing method begun by leaders at the Toyota Motor Company in the early and mid-20th century. This system, often referred to as Lean manufacturing in the West, aims to increase the value of products or services for customers. This is often accomplished by finding and eliminating waste from production processes. Lean manufacturing involves the use of many tools such as 5S, kaizen, kanban, jidoka, heijunka, and poka-yoke. 5S is considered a foundational part of the Toyota Production System because until the workplace is in a clean, organized state, achieving consistently good results is difficult. A messy, cluttered space can lead to mistakes, slowdowns in production, and even accidents, all of which interrupt operations and negatively impact a company. By having a systematically organized facility, a company increases the likelihood that production will occur exactly as it should. Benefits of 5S Over time, the 5S methodology leads to many benefits, including: Reduced costs Higher quality Increased productivity Greater employee satisfaction A safer work environment What Are the 5 S's? The 5S concept might sound a little abstract at this point, but in reality, it's a very practical, hands-on tool that everyone in the workplace can be a part of. 5S involves assessing everything present in a space, removing what's unnecessary, organizing things logically, performing housekeeping tasks, and keeping this cycle going. Organize, clean, repeat. Let's take a closer look at each of the parts of 5S. Sort The first step of 5S, Sort, involves going through all the tools, furniture, materials, equipment, etc. in a work area to determine what needs to be present and what can be removed. Some questions to ask during this phase include: What is the purpose of this item? When was this item last used? How frequently is it used? Who uses it? Does it need to be here? These questions help determine the value of each item. A workspace might be better off without unnecessary items or items used infrequently. These things can get in the way or take up space. Keep in mind the best people to assess the items in space are the people who work in that space. They are the ones who can answer the above questions. When a group has determined that some items aren't necessary, consider the following options: Give the items to a different department Recycle/throw away/sell the items Put items into storage For cases when an item's value is uncertain — for example, a tool hasn't been used recently, but someone thinks it might be needed in the future — use the red tag method. Red tags are usually cardboard tags or stickers that can be attached to the items in question. Users fill out the information about the item such as Location Description Name of person applying the tag Date of application Then the item is placed in a "red tag area" with other questionable items. If after a designated amount of time (perhaps a month or two) the item hasn't been used, it's time to remove it from the workspace. It's not worth hanging onto things that never get used since they just take up space. Tip: Set a reminder—on your phone or computer, or posted somewhere in the workspace—to check back in with the red tag area so it doesn't get forgotten. Set in Order Once the extra clutter is gone, it's easier to see what's what. Now work groups can come up with their strategies for sorting through the remaining items. Things to consider: Which people (or workstations) use which items? When are items used? Which items are used most frequently? Should items be grouped by type? Where would it be most logical to place items? Would some placements be more ergonomic for workers than others? Would some placements cut down on unnecessary motion? Are more storage containers necessary to keep things organized? During this phase, everyone should determine what arrangements are most logical. That will require thinking through tasks, the frequency of those tasks, the paths people take through the space, etc. Businesses may want to stop and think about the relationship between the organization and larger Lean efforts. What arrangement will cause the least amount of waste? In Lean manufacturing, waste can take the form of: Defects Waiting time Extra motion Excess inventory Overproduction Extra processing Unnecessary transportation Unutilized talents Tip: For 5S, specifically consider how the layout and organization of an area could increase/decrease waiting time, motion, and unnecessary transportation. Shine Everyone thinks they know what housekeeping is, but it's one of the easiest things to overlook, especially when work gets busy. The Shine stage of 5S focuses on cleaning up the work area, which means sweeping, mopping, dusting, wiping down surfaces, putting tools and materials away, etc. In addition to basic cleaning, Shine also involves performing regular maintenance on equipment and machinery. Planning for maintenance ahead of time means businesses can catch problems and prevent breakdowns. That means less wasted time and no loss of profits related to work stoppages. Shining the workplace might not sound exciting, but it's important. And it shouldn't just be left up to the janitorial staff. In 5S, everyone takes responsibility for cleaning up their workspace, ideally daily. Doing so makes people take ownership of the space, which in the long run means people will be more invested in their work and the company. Tip: How to clean may seem obvious, but make sure people know how to properly Shine their spaces. Show employees — especially new employees — which cleaners to use, where cleaning materials are stored, and how to clean equipment, particularly if it's equipment that could be easily damaged. Standardize Once the first three steps of 5S are completed, things should look pretty good. All the extra stuff is gone, everything is organized, spaces are cleaned, and equipment is in good working order. The problem is, when 5S is new at a company, it's easy to clean and get organized…and then slowly let things slide back to the way they were. Standardize makes 5S different from the typical spring-cleaning project. Standardize systematizes everything that just happened and turns one-time efforts into habits. Standardize assigns regular tasks, creates schedules, and posts instructions so these activities become routines. It makes standard operating procedures for 5S so that orderliness doesn't fall by the wayside. Depending on the workspace, a daily 5S checklist or a chart might be useful. A posted schedule indicating how frequently certain cleaning tasks must occur and who is responsible for them is another helpful tool. Initially, people will probably need reminders about 5S. Small amounts of time may need to be set aside daily for 5S tasks. But over time, tasks will become routine and 5S organizing and cleaning will become a part of regular work. Tip: Visual cues such as signs, labels, posters, floor marking tape, and tool organizers also play an important role in 5S. They can provide directions and keep items in place, in many cases without words. Sustain Once standard procedures for 5S are in place, businesses must perform the ongoing work of maintaining those procedures and updating them as necessary. Sustain refers to the process of keeping 5S running smoothly, but also of keeping everyone in the organization involved. Managers need to participate, as do employees out on the manufacturing floor, in the warehouse, or in the office. Sustain is about making 5S a long-term program, not just an event or short-term project. Ideally, 5S becomes a part of an organization's culture. And when 5S is sustained over time, that's when businesses will start to notice continuous positive results. Tip #1: To help sustain 5S practices, make sure all new employees (or employees who switch departments) receive training about their area's 5S procedures. Tip #2: Keep things interesting. Look at what other companies are doing with 5S. New ideas for organization can keep things improving and keep employees engaged. Safety – The 6th S Some companies like to include a sixth S in their 5S program: Safety. When safety is included, the system is often called 6S. The Safety step involves focusing on what can be done to eliminate risks in work processes by arranging things in certain ways. This might involve setting up workstations so they're more ergonomic, marking intersections—such as the places where forklifts and pedestrians cross paths—with signs, and labeling the storage cabinet for cleaning chemicals so people are aware of potential hazards. If the layout of the workplace or the tasks people perform are dangerous, those dangers should be reduced as much as possible. That's what the sixth S focuses on. Some people consider safety an outcome of performing the other five S's appropriately, and as a result say a sixth S isn't necessary. They think if the workspace is properly organized and cleaned and uses helpful visual safety cues, a separate safety step is unnecessary. Neither approach to safety is right or wrong. But however a business wants to approach safety, it should be aware that paying attention to safety is important. Tip: If mishaps and accidents do happen, stop to consider whether a 5S improvement could have prevented it. Could less clutter, cleaner walking surfaces, or better signs and labels have made a difference? Getting Started with 5S Even though 5S is a fairly simple concept, beginning a new 5S program can feel daunting. It's like undertaking a big cleaning project in the garage or the basement at home; there's a lot of stuff to deal with, and getting started probably doesn't sound fun. Start with practical steps such as deciding which departments and individuals will be involved, what training is needed, and what tools to use to facilitate the process. Determining these concrete things will help begin the process of 5S implementation. Who Should Participate in 5S? Here's the short answer to this question: everyone. If a department is starting 5S, managers and all other employees should be included. If anyone is left out, this could lead to confusion or to messes that people don't want to take ownership of. It is possible that some people will play a bigger role in 5S than others, which is fine. There might be 5S coordinators who are in charge of installing and maintaining 5S labeling, keeping tracking of assigned tasks, or introducing new department members to the 5S system. These people will obviously spend a lot of time thinking about 5S compared to others. Everyone should think about 5S regularly, though. 5S might initially take place as an event, but ideally it becomes a part of daily work for everyone. It's also important to remember that company leaders should participate in 5S, especially if 5S is a company-wide effort. When people see their superiors taking 5S seriously by participating in it, they'll be more likely to take it seriously, too. 5S Training Anyone who will participate in 5S activities needs to receive training. This could be done in a classroom setting, with a training DVD, and/or through hands-on activities. A demonstration of how 5S could occur at a workstation might also be useful. For employees to understand why the company is going to start using 5S and why it's important, they should be given a brief history of 5S, its parts, and its benefits. It's quite possible that the way 5S is carried out at one organization or even one department will be different from others, so groups performing 5S for the first time may need to work out the best way to perform the steps of 5S in their spaces. In any case, everyone should receive training when 5S is new, and then any new employees who come onboard later should receive training about 5S as well. 5S & Visual Communication A key part of 5S is that it makes spaces cleaner and therefore easier to navigate. That means people can more easily get their work done. Visual communication tools such as labels, floor markings, cabinet and shelf markings, and shadow boards can make navigating spaces even simpler. Plus, these tools can help keep the workspace organized. A workplace that uses visual management in this way is often referred to as a visual workplace. Some common visual tools used in 5S are: Floor Marking Tape These tapes can be used to outline work cells, mark the locations where equipment or materials are placed, or highlight hazards. They come in a variety of colors and patterns, and can also be used on shelves, workbenches, cabinets, and other surfaces. Labels and Signs These visuals use text, colors, and symbols to convey information. They can indicate the contents of drawers, call out hazards, or tell people where to store parts. Many styles and sizes exist, and some businesses even choose to make these in-house with a label and sign printer. Shadow boards & Toolbox Foam These visuals are helpful in workspaces with a lot of tools. Shadow boards use cutouts of tools that are placed behind the spot where a tool hangs on a pegboard. Toolbox foam works similarly, except it fits into a toolbox drawer. The tool's shape is cut out of a top layer of foam, so a bright bottom layer of foam shows through. Both of these methods highlight missing tools and tell people exactly where tools should be placed when they're finished using them. Businesses may choose to use some or all of these visual tools. All of them help achieve the often-cited saying of 5S: “A place for everything, and everything in its place.” These tools make it clear where things belong, so clutter doesn't become a problem so easily. Tip: If you use color-coded floor markings, tapes, or other visual cues, make sure everyone understands them. Post a color chart if necessary. 5S Outside Manufacturing – In Healthcare, the Office, or Government 5S originated in the manufacturing industry at Toyota and it has proven useful for manufacturers in many industries, not just the automobile industry. In recent decades, 5S has moved beyond manufacturing to other industries such as healthcare. Many offices also employ 5S, as do some schools and other government organizations. The basic steps of 5S can be applied to any workplace. An office can use 5S to keep supplies organized, as can hospitals and medical clinics. 5S can even be used in a communal kitchen to keep the fridge from filling up with expired food. It's really just a matter of determining what workspaces and work processes will benefit most from improved workplace organization. 5S Example Look at the example below to see 5S in action. Before 5S, spaces are cluttered and confusing. After 5S, everything has an assigned place, which is often marked with floor marking tape, labels, and other visual cues. When 5S is used in the workplace, it's easier to detect abnormalities and spot potential problems before they grow into significant issues. The Costs of 5S vs. Long-Term Savings Business leaders considering using 5S may wonder if 5S is expensive to implement. Generally, it's not. There may be an up-front investment in tools like floor marking tape and labels, and some time does need to be spent on training and on 5S activities, which takes up employees' time. In the long run, though, 5S makes processes run more smoothly and prevents mishaps, and those things usually save businessFebruary 28, 2022 Improving efficiency within any process, whether it be for manufacturing, distribution, or another business objective, is an essential step in improving the bottom line for companies. Efficiency improvement also enables businesses to deliver quality products to their customers in a consistent manner. The road to quality management, quality assurance, and overall plant success begins with the elimination of downtime. There are numerous different aspects of work that have the potential to cause slowdowns and disruptions of work. Unfortunately, bottlenecks are some of the most strenuous situations of downtime a company can face, resulting in low performance and productivity capabilities. With the right Lean management tools, you can improve your understanding of what causes bottlenecks, how to get to any root causes, and prevent a blockage from occurring in the future. What is a Bottleneck (or Constraint) in Manufacturing? A bottleneck is any area along the production line where the number of tasks to be completed becomes too much for the maximum workload capacity. This problem often results in delaying subsequent steps in the workflow. Bottlenecks can stem from an entire stage of work, not enough employees, a lack of resources, and even computer issues. There are three different classifications of bottlenecks that businesses can run into on any given day. Those include: 1. Production line bottlenecks – When the output of one process is faster than another it leads to an increase in material piling up, waiting to be used. 2. Supply chain bottlenecks – A poorly designed material flow from suppliers is what results in a supply chain bottleneck. This can be the result of lackluster inventory management, changing products frequently, financing issues, or an incorrect forecast of demand. 3. Bottlenecks caused by People – A lack of effective training leads to inefficient work, which causes ineffective communication. Both are attributed to low employee morale due to constant work interruptions. Short-term vs Long-term Bottlenecks Aside from the different causes of bottlenecks identified above, there are also two different classifications that bottlenecks fit into. Those are: 1. Short-term bottlenecks – These types of bottlenecks are caused by short-term problems. For example, a bottleneck can occur if an employee is out sick for the day or if a delivery is running late. These usually aren’t cause for concern, although you may do well to have a backup plan if something like this does occur. 2. Long-term bottlenecks – These types of bottlenecks are more cause for concern. Long-term bottlenecks require management techniques such as root cause analysis or the creation of a fishbone diagram to get to the bottom of the issue. Long-term bottlenecks may come about because of an exhaustive audit procedure, a disorganized inventory system, or even an entire lack of real-time data that identifies issues. Long-term bottlenecks are the types of bottlenecks that should be investigated immediately to reduce wasteful practices. Causes of Bottleneck Bottlenecks during the manufacturing process can arise from various factors that stall the smooth flow of production. Here are some of the most common causes: Communication Breakdowns Effective communication between teams or departments is very important. Communicating through verbal exchanges or paper documentation can cause a significant bottleneck within the manufacturing process, such as an operator taking a break or the misplacement of a clipboard. A solution to this lies in the implementation of automated machine data collection systems. The manual compilation of production data not only consumes valuable time but is also susceptible to inaccuracies, resulting in compromised communication and understanding. Unclear Processes Having unclear processes and old equipment really messes things up in manufacturing. Think about how long those machines have been running and how often they get checked or fixed up. Take a good look at how things are done to figure out where things are getting stuck. Also, if the factory setup is poor, like if there's no storage to put materials, that's going to cause more delays and damage. Bad Forecasting It is essential for manufacturing companies to bring in components and materials efficiently in order to avoid excess storage and ensure readiness for use. Failure to prepare necessary materials can lead to bottlenecks in production. Predicting high demand through forecasting and prediction is crucial. Utilizing analytics tools and monitoring customer behaviors and industry trends are necessary for effective long-term planning and prevention of bottlenecks in manufacturing companies. Limited Machine Capacity As the deadlines draw near, your equipment may need to exceed the normal operational capacity to meet the requirements. Such behavior can lead to the likelihood of machinery breakdown. Whether you are overloading a single stage or all stages of the production process, the danger of causing a critical bottleneck remains consistent. Lack of Automation Relying too much on people doing things manually instead of using automation tools increases the likelihood of mistakes in important parts of the production process. Automation, whether it's machines or computer software, is good for performing repetitive tasks without needing to make important decisions. Workplace Organization Guide: Learn simple strategies for long-term success When your workplace is cluttered, processes aren’t as efficient as they could be. This free Quick Guide to an Organized Workplace covers simple tools and strategies you can use to keep workbenches, storage areas, work cells, and other locations organized and looking professional. Get my free guide Common Mistakes to Avoid During Bottleneck Analysis Bottlenecks can affect your business growth; therefore, it is important to address them accurately to avoid common errors that may arise. Ignoring Small Bottlenecks mall interruptions in the workflow may be easy to ignore, but just a five-minute delay happening multiple times daily can ultimately result in the loss of an hour of productivity. If you observe that your team wastes a few minutes each day waiting for a slow software to load, address the issue promptly and find a quicker alternative. Overlooking Employee Input Managers often concentrate solely on data analysis while neglecting the valuable insights provided by their staff members. It is essential to remember that your team members are the ones directly facing operational challenges and obstacles. For instance, a sales representative currently dedicates a significant amount of time to manual data entry. Implementing automation in this process could potentially enable him to allocate more time to engage in sales activities. Focusing on Symptoms, Not Causes A drop in sales could seem to be an issue with your sales team, but it might also be the result of a bottleneck in product development that is causing shipments to be delayed. Investigate more thoroughly and look past the cursory examination. Ignoring Stakeholders Reviews Management's failure to listen to the feedback and insights of employees directly engaged in the process can result in the oversight of valuable information and potential solutions to improve efficiency and productivity. Employees have firsthand experience and insight into the difficulties within their roles or departments. Ignoring their input could result in missed chances to recognize and resolve bottlenecks, ultimately causing prolonged delays, decreased output, and decreased overall performance. Neglecting Data Analysis Insufficient or full of error data often hinders the effectiveness of bottleneck analysis. Using outdated or partial data may result in incorrectly pinpointing bottlenecks, which leads to ineffective solutions. Overreliance on Technology It is commonly believed by many that technology is the ultimate solution for all obstacles, yet sometimes a simple adjustment in processes can be effective. In some cases, the effectiveness of a routine team meeting can outweigh the benefits of getting a new project management tool. The critical factor lies in creating a balance between utilizing technological resources and human problem-solving capabilities to achieve the most efficient solutions. What is a Bottleneck Analysis Identifying the cause of a bottleneck requires the company to perform a bottleneck analysis. Like a risk assessment, a bottleneck analysis is used to identify a problem. However, in this case, that problem is a slowdown in the workflow rather than a hazard that poses a risk to employee safety. Once the cause of the bottleneck is identified, the company can start to work towards potential solutions to be able to push product through the production line at a more consistent rate again. Benefits of a Bottleneck Analysis In addition to eliminating the bottleneck at its source and achieving a steadier workflow, a facility can enjoy the following additional advantages: Waste elimination – Bottlenecks are often caused by unnecessary or inefficient processes, which can result in a variety of types of waste. Being aware of any waste is the first step in making improvements to the existing processes. Increased knowledge - The more a company knows about a specific process, the easier it is to make smart decisions and take control of the throughput capacity. Knowledge provides advantages not only when it comes to eliminating bottlenecks, but also when making large process improvement decisions in general. The productivity of a facility depends on how much value it can produce for its clients. As waste becomes more rare and the knowledge base of the workers increases, they then become able to produce consistent and highly-valuable materials. Performing a Bottleneck Analysis Specifically used to identify the cause of a bottleneck, or to identify where a bottleneck is likely to occur in the future, bottleneck analyses are an essential tool for all businesses that work with sequential steps to complete a product or service. In the end, no matter what the reason was for conducting this analysis, its completion will provide important information about how a product moves through the production process, and how processes can be improved. Talking about performing a bottleneck analysis and following through with performing one is often one of the most difficult parts of the process. The following examples of performing a bottleneck analysis will help you start your very own elimination process for bottleneck problems. Gathering Information Performing a bottleneck analysis is a detailed operation that begins with the company gathering as much information as possible about the manufacturing flow of a particular product or process. When performing a bottleneck analysis, it is important to look at both the specific step where the bottleneck is occurring as well as the entire manufacturing process. Looking at the entire process will provide essential information about the steps leading up to the bottleneck, the bottleneck itself, and what takes place directly after the bottleneck. It is also necessary to note that if a bottleneck early in the production process is eliminated, that action may result in a new one forming further down the line. A properly performed analysis will not only help to find solutions to the existing bottleneck, but it will also help to prevent new ones from forming. Using Lean Manufacturing Tools Some bottlenecks can be identified and resolved quickly and without any need for extensive analysis. In most cases, the tools used for this process are going to be either a written flowchart or a computer program. Computer programs geared towards process flow management allow a company to enter in information gathered from each step of a process so that it provides a visual display of what is happening along the workflow. Bottlenecks can easily be detected if the business utilizes the Kanban method. By implementing this technique, visualizing the flow of work on a Kanban board or within a software program allows employees to see where tasks are piling up within a production process or within a supply chain. For that reason, Kanban is an excellent tool for continuous improvement endeavors regarding consistent and efficient workflow. Other bottleneck analysis tools available to use include the DMAIC method and the Theory of Constraints method. These are only some of the tools that can be used in an analysis but finding the right one is important for maximizing positive results. For a simple situation, using a template can be an effective choice. However, when there are multiple products or different flows, a more advanced set of tools should be used. Avoiding Future Bottlenecks Completing a bottleneck analysis is the first step in a longer process of continuous improvement regarding the efficiency of production. Taking the information gathered from the analysis and using it to make process changes is the next task that must be completed. Companies that take the time to analyze this type of information and use it to avoid bottlenecks in facility operations will benefit from a more efficient process long into the future. That said, rather than just identifying what appears to be the surface cause of a bottleneck, it is better to take the time to really dig into the data to discover the root cause of the manufacturing constraint. This will not only get rid of the bottlenecks as soon as possible, but also set the processes up to prevent them from occurring again in the future. Dealing with Bottlenecks: Examples of Solutions In addition to identifying exactly where a bottleneck forms, bottleneck analyses also aim to identify potential solutions. Every company is going to have its own way of solving this type of problem, but the following are some common options that should be considered whenever looking for ways to eliminate bottlenecks in the workflow. Add additional capacity – If a bottleneck is being caused at a specific step in the production process, consider adding additional capacity. For example, bottlenecks can occur during painting tasks because it may take a longer time than other steps. Adding a second painting station will effectively double capacity and should eliminate the bottleneck problem. Eliminate wasteful steps – Some products may have extra features that customers don't want or need. If these types of steps are causing a bottleneck, it is a good idea to eliminate them all together to keep work moving along smoothly. Eliminating waste is an important part of fixing bottlenecks and improving efficiency. Add staff – One of the most common causes of a bottleneck is insufficient staffing to complete a task. Hiring additional employees to work in a specific area is an excellent solution. Reduce production – While reducing the rate of production is not typically a good long-term solution, it is better to reduce production rates than to have huge amounts of inventory building up along the production line. Adjust the flow – It is often possible to adjust the workflow to keep things moving. When a bottleneck forms, see if the step where it is occurring can be skipped and then completed later. This is only a good solution for situations where a temporary bottleneck forms for some reason, such as a broken machine or absent employees. Brainstorm ways to remedy process constraints when they occur. It will help improve manufacturing operations and help the team keep product demand in check. Bottleneck Analysis Tools and Softwares Bottleneck analysis can be complex, but there are tools available to facilitate this process and identify mistakes in your operation. Here are some of the common types of bottleneck analysis tools and software: Process mining software: This software analyzes data from your enterprise resource planning (ERP) system and other sources to identify bottlenecks in your workflows. Process mining software can help you to visualize your processes, identify areas for improvement, and track the impact of changes you make. Task mining software: This software uses task capture technology to analyze user interactions and activities within business applications. Task mining software can help you to identify bottlenecks in tasks and processes that are not captured by traditional ERP systems. Process simulation software: This software allows you to create a digital model of your production process. You can then use the software to simulate different scenarios and identify potential bottlenecks before they occur. Business intelligence (BI) tools: BI tools can be used to collect and analyze data from a variety of sources, including production data, sales data, and customer data. BI tools can help you to identify trends and patterns that may indicate bottlenecks in your operation. Low-code/no-code workflow management software:This type of software allows you to easily create and automate workflows. Workflow management software can help you to identify and eliminate bottlenecks in your processes by streamlining the flow of work. The best bottleneck analysis tool for you will depend on your specific needs and budget. However, all of the tools listed above can be helpful in identifying and eliminating bottlenecks in your manufacturing operation. Training Teams to Watch for Bottlenecks Far too many companies wait until a serious bottleneck occurs before taking action. It is important to act quickly when this occurs to avoid slowdowns, but it is even better to avoid bottlenecks entirely. The best way to do that is to have employees watching out for early signs of a problem. Training teams to watch for bottlenecks will typically involve department managers first informing front line employees on what to watch for. Some common recognizable features include the following: Trouble keeping up - If one department or step in a workflow process is constantly falling behind and other areas don't have this issue, it is an early sign of a bottleneck problem. Shuffling staffing - If a floor manager needs to take staffing from one area of the facility and move it to another to help keep up, this can be another sign of a problem. Shuffling staffing can be an effective temporary solution before a more long-term fix can be identified.li> Short staff - When employees from a specific area call in sick or take a vacation day, does it cause an unreasonable burden to other team members? If so, the staffing or workflow should be evaluated for improvement opportunities. Other - In general, listening to the concerns of employees can be one of the best ways to discover potential issues. Employees are typically the first to notice that there are problems and can be an excellent 'alarm' to watch out for future problems. Anytime issues like these are found, it is a good time to perform a full bottleneck analysis on the process in question. Since the problem isn't a serious issue yet, the company will have some extra time to be able to perform a full analysis without interrupting workflow. es money. Relationship between Muda, Mura and Muri Muda, Mura, and Muri are interrelated. Eliminating one of them will affect the other two. For example, a firm that needs to transport 6 tons of materials to a customer has several options (Lean Enterprise Institute, 2016). The first option is to load one truck with all 6 tons and make a single trip. However in this example, it would be considered Muri due to the overburden of the truck. This excess load can lead to a breakdown. The second option is to divide the transportation into two trips. One with two tons and the other with four tons. This would be considered Mura since the unevenness of the arrival of materials to the customer can lead to problems at the receiving dock. In the first trip, the delivery may be too little for the production necessary on-site. In the second trip, the amount of delivered material may be too much for on-site storage and material handling. This leads to Muri since one of the truck is overburden and the receiver is also overburden for that delivery. Additionally, Muda can be seen from the uneven workload. This can cause employees who receive the materials to wait around. The third option is to load two tons on each truck and make three trips. Even though this option has no Mura and Muri, it has Muda since the truck would not be fully loaded on each trip. Each truck can carry up to 3 tons of material and this option makes one unnecessary trip. The fourth option is to deliver the materials with two trucks each with 3 tons. In this example, this would be the optimal level that minimizes Muda, Mura, and Muri. Muda does not exist because the trucks are carrying the loads at their maximum capacity. There is no excess capacity nor unnecessary trips with this strategy. Mura does not exist because the workload between the two deliveries are uniform. As a result, there is no unevenness. And finally, Muri is absent from this option because both the truck and the operators are not working beyond their capacity. In real world applications of Lean, it is not always easy or possible to find an optimal solution. Reducing Muda can lead to Muri. The existence of Mura can be seen as a waste in Muda. And finally Muri can lead to a breakdown in the system that will result in a large amount of Muda and Mura. Since real world problems are dynamic and the needs of customers are always changing, our work processes must also change as well. As we design our processes and standardize our work, we must look at the resulting system from the lens of these three concepts. Only by considering the impacts of Muda, Mura, and Muri and optimizing our production strategy can we develop an efficient Lean system. Continuous Flow: Toyota’s Way to Deliver Value Faster The continuous flow of work is vital for the successful implementation of Lean. In this section, you will learn the fundamentals required to achieve it. Go back to all Getting Started Value and Waste Pull Systems Continuous Improvement Root Cause Analysis Hoshin Kanri Lean Transformation Continuous Flow What Is Cycle Time? What Is Little's Law? What Is Takt Time? What Is Heijunka? What Is Jidoka? What Is Andon? What Is Lean Six Sigma? Lean Project Management An essential aspect of maintaining client loyalty is delivering the right value at the right time. In pursuit of this goal, Toyota developed a method called "continuous flow" in the mid-20th century. This approach offers an alternative to the traditional batching method commonly used in process management. In this article, you will learn how to optimize continuous flow by implementing various Lean methodologies. What Is Continuous Flow? Continuous flow is a Lean method that moves a single product through every step of the process continuously, without batching, allowing for uninterrupted production and frequent delivery of value to customers. It is as simple as it sounds. Once you start working on a product, you keep focused on it until it is ready to be delivered to your customer. At first, the concept of continuous flow may sound less efficient than processing work in batches because, with it, you are delivering smaller amounts of value to the market at a time. However, it actually allows you to provide value to customers more often and reduce the time they spend waiting to receive their orders. In addition, it is a fantastic way to minimize the waste of your process. Continuous flow is especially useful for reducing inventory costs and the wait time for your work items. What Is Takt Time? To make the most of continuous flow, you need to define a takt time for your assignments. Takt time is the rate at which a product needs to be completed to meet customer demand. The term originates from the German word "takt," which literally means "pulse" or "beat." Briefly explained, your takt time is your sell rate. For example, if your company has a takt time of 2 days, you need to finish producing a product every 2 days because, on average, a customer is buying your product every 2 days. You can calculate takt time by dividing the total available time for production by the required production units. Often confused with cycle time, takt time is one of the most important metrics for maintaining a continuous flow. It allows you to utilize your capacity to meet customer demand in the best possible way. Learn more about Takt Time What Is Heijunka? To help you optimize your workflow continuously for takt time, Lean offers a production leveling solution called Heijunka. As demand is rarely steady, you need to adapt your process to any fluctuations. Heijunka is a method for reducing the unevenness (Mura) of your process and preventing overburden (Muri). It means "leveling" and is critical for maintaining a stable Lean system. Heijunka allows you to produce intermediate goods at a steady rate so that you can satisfy fluctuations according to your average customer demand. For that purpose, the method has two ways of leveling production: 1. Leveling by volume 2. Leveling by type Leveling by volume In its pure form, Lean teaches us to pull work only when there is a demand for it, or in other words, when customers request it. However, in some industries, processing work this way is not practical when there is a constant stream of new orders. Irrelevant of your industry, it is highly unlikely to receive an equal number of orders each day, week, or month. To achieve a continuous flow of work, Heijunka provides you with the opportunity to level your production volume depending on the average demand. So, if you receive 10 orders per week on average, but their number fluctuates by the day (e.g., Monday 5; Tuesday 1; Wednesday 2, etc.), you need to adjust your capacity to meet the average demand. In a continuous flow, this would mean producing 2 products per day (in case of a 5-day work week) to meet demand. Leveling by type Things can be quite tricky when you manage a portfolio of products and distribute capacity according to demand. To address this issue, Toyota implemented a Heijunka box to ensure a steady workflow that meets customers’ demands. Heijunka box Basically, it is a system that visualizes the demand for each product. Based on the average demand, it levels a production sequence to achieve an optimal flow. Learn more about Heijunka What Is Jidoka? Meeting demand is important, but delivering a product with unquestionable value is even more so. This is where Jidoka comes in. It is a method for ensuring a product's built-in quality. Also known as "autonomation," Jidoka allows you to stop the production process as soon as you see an imperfection. It has 4 distinctive steps: 1. Discover an abnormality 2. Stop the production process 3. Fix the immediate problem 4. Investigate and correct the root cause Although it may temporarily disturb your process's continuous flow, implementing Jidoka will help you ensure that the product you deliver meets your customers' quality expectations. Learn more about Jidoka Continuous flow is an important part of Lean management and Lean product development in particular. By optimizing your work process to deliver the right value to your customers at the right time, you will be more likely to ensure their loyalty and grow your business. Takt Time: What Is It and How to Measure It? Understand how the Lean concept of takt time can help you improve your work efficiency and reduce waste while meeting your customer demand. Go back to all Getting Started Value and Waste Pull Systems Continuous Improvement Root Cause Analysis Hoshin Kanri Lean Transformation Continuous Flow What Is Cycle Time? What Is Little's Law? What Is Takt Time? What Is Heijunka? What Is Jidoka? What Is Andon? What Is Lean Six Sigma? Lean Project Management Share on: A great deal of Lean management’s success lies in pulling new work in progress rather than pushing it. This allows you to create and deliver value only when there is a demand. However, managing a pull system wouldn’t be possible without maintaining a continuous flow of work. This is not an easy task, as demand is in a constant state of flux. To meet demand and run your process in the most efficient way, you need to define the time for your work process. In this article, we’ll discuss takt time, how to measure it, and offer some practical examples. What Is Takt Time? Takt time is a key concept in Lean manufacturing, which is a systematic approach to reducing waste and improving efficiency in production processes. Takt time is the rate at which you need to complete a product or service to satisfy customer demand. By aligning production rate to customer demand, organizations can avoid overproduction, reduce inventory costs, and improve overall efficiency. In other words, a takt time is your production rate and can easily be categorized as the heartbeat of your work process. It allows you to optimize your capacity to meet demand without overproducing or underproducing. The term originates from the German word "takt", which means a beat or a pulse. Takt time was first used as a metric in the 1930s in Germany for airplane manufacturing. Twenty years later, it contributed significantly to Toyota's rise from a small Japanese carmaker to the largest automobile company in the world. Takt Time Formula Explained The takt time formula in Lean is: Takt Time = Available Production Time / Average Customer Demand Available Production Time: the total amount of time available for production during a specific period. Customer Demand: the amount of products or services that customers require during the same period. This is usually expressed as a rate or quantity, such as units per day, hours per week, or calls per hour. For example, if you receive a new product order every 4 hours, your team needs to finish a product in 4 hours or less to meet demand. Takt Time = 480 minutes / 2 orders Takt Time = 240 minutes per order This means that the company must complete one order every 240 minutes (about 4 hours) to meet customer demand without overproducing or underproducing. If they can produce orders faster than 4 hours, it may indicate that they are overproducing and creating unnecessary inventory. If they cannot produce the order within 240 minutes, they may not be meeting customer demand and may need to adjust their production processes or increase resources. How to Calculate Takt Time? Takt time is calculated as the available production time divided by the customer demand. Takt time formula Define production time and customer demand: To receive an accurate result using this takt time formula, you should put both the production time available and the customer demand into frames. Exclude planned downtime: We advise you to include only the time your team will be actively working on creating value for your customers, excluding breaks, scheduled maintenance, or shift changeovers. Use short time frames for customer demand: When calculating takt time, you should include a relatively short time frame for the average customer demand (e.g., a week or a month). What Is a Takt Time Example? Let’s calculate the takt time for an imaginary company developing 3D printing machinery. The workweek is five days long, and the company operates in a single nine-hour shift that includes a 60-minute lunch hour break and two 15-minute breaks in the morning and the afternoon. On average, the company receives orders for 10 machines per week. To define the takt time that the team needs to maintain, we simply apply the above-mentioned formula. The total available work time is 7 hours, 30 minutes per day. Breaking it down into minutes gives us exactly 450 minutes per day, which is 2250 minutes per week. By dividing 2250 by 10 (average number of orders), we get a takt time of 225 minutes to complete a single 3D printing machine. Dividing 225 by 60 (minutes in an hour) gets us to a maximum takt time of 3 hours 45 minutes per order. 2250 / 10 = 225 minutes Takt time As you can see, defining the takt time required to meet customer demand is not rocket science. With this data available, you can make well-informed choices for managing your team’s capacity according to customer demand. Why Is Takt Time Important? Defining takt time is crucial for optimizing your team’s capacity and reducing process waste. Takt time can help you maintain a continuous flow of work and reduce Mura (unevenness) in your workflow. Nonetheless, takt time is valuable for optimizing storage costs as it will help you avoid overproduction. What Are the Benefits of Takt Time There are several important benefits of using takt time in Lean: Aligned Production to Customer Demand By calculating takt time, teams can understand the rate at which they need to produce goods or services to meet customer demand. This ensures that production is aligned with actual customer needs, reducing the risk of overproduction or underproduction. Reduced Waste Takt time helps eliminate waste in production processes by ensuring that only the necessary amount of value is created to meet customer demand. This reduces the amount of excess inventory that can be costly to store, transport, and manage. Improved Predictability By aligning production to customer demand and reducing waste in each process, organizations establish a takt time leading to an improved predictability. Improved Efficiency Takt time can improve production efficiency by optimizing production rates to match customer demand. This can reduce waiting times, bottlenecks, and other inefficiencies in the process. Continuous Improvement Takt time provides a clear target for teams to work towards, making it easier to identify areas for continuous improvement. By progressively improving their value creation process, teams can reduce costs, increase efficiency, and improve customer satisfaction. What Are the Limitations of Takt Time? While takt time can be a useful tool for improving production efficiency and reducing waste, it does have some limitations. Here are some of the main limitations of takt time: Assuming Stable Demand Takt time is based on the assumption that customer demand is stable and predictable. However, this is not always the case and can hinder production efficiency. Assuming Production Processes Are Consistent and Predictable Takt time does not account for the variability of processes and demand and can lead to overproduction or underproduction. Assuming External Factors Can Be Always Controlled Machine breakdowns, shortages, and employees leave cannot always be anticipated or avoided. Takt Time vs. Cycle Time vs. Lead Time Takt time, lead time, and cycle time are essential Lean metrics; however, there is a tendency to confuse their meaning. While lead time and cycle time indicate how work progresses through your workflow, takt time focuses on the actual production rate of a team or a process. Lead time is the time frame between an order being received and the client getting their value. The lead time focuses on the time it takes to fulfill customer orders. Cycle time is the time your team spends actively working on a customer order. Takt time is the maximum amount of time you need to comply with to meet customer demand. As a Lean manager, you should consider all three metrics as key performance indicators of your workflow. Takt Time Frequently Asked Questions (FAQ) What Is the Takt Time Concept? The takt time concept refers to the rate at which a product or service should be produced to meet customer demand. Takt time is used to set the pace of production and ensure that products and services are created at the right speed to comply with the customer needs. How Is Takt Time Calculated? Takt time is calculated by dividing the total available production time by the average customer demand. What Is an Example of Takt Time? If you receive a new order every 4 hours, it means that your team needs to finish an order in 4 hours or less to meet demand. In other words, your team’s take time should be within or less than 240 minutes (4 hours). Value Stream Mapping: 4 Steps to Get Started with VSM What is the value stream mapping process? Discover the benefits, use cases and learn how to implement VSM in practice. Go back to all Getting Started Value and Waste What Is Value in Lean? 7 Wastes of Lean What Is Mura? What Is Muri? What Is 5S? What Is the Cost of Delay? What Is Value Stream Mapping? Pull Systems Continuous Improvement Root Cause Analysis Hoshin Kanri Lean Transformation Continuous Flow What Is Lean Six Sigma? Lean Project Management Share on: As the market is getting more saturated by the day, customers are becoming increasingly demanding and difficult to convince that you can provide the value they are looking for. An effective technique originating from manufacturing has proven to get organizations ahead of the competition. By visualizing the end-to-end value creation flow, value stream mapping allows organizations to streamline operations and improve efficiency. What Is Value Stream Mapping (VSM)? Value stream mapping is a Lean management tool used to visualize, analyze and improve all the steps in a product or service delivery process. Also known as material or information flow mapping, VSM represents the entire flow of goods, materials, or information from the supplier to the customer. The technique is also part of the Six Sigma and Lean Six Sigma methodologies for process improvement. VSM involves creating a detailed map of all the important steps of your work process necessary to deliver value from start to finish. By doing so, you can easily identify waste, inefficiencies, and opportunities for improvement. It is essential to clarify that value in Lean is everything that the customer would pay for. However, when it comes to mapping a value stream, some steps may not bring direct value to your customer but help ensure that you will deliver the final product or service. A clear example of such steps is the quality inspections that are irreplaceable in every production process. Of course, your customer is not paying you to do these checks, but if you deliver a final product that doesn’t meet their quality standard or expectations, they will be less willing to buy from you ever again. History of Value Stream Mapping Value stream mapping became a popular practice with Lean's rise in the second half of the 20th century. It was one of the foundations that made the Toyota Production System a manufacturing sensation, although, by that time, the term VSM was not present. The original Kanban System, Source: TOYOTA Global Website However, it is a common misconception that Toyota invented the practice associated with visually mapping a workflow. There are records of diagrams showing the flow of materials and information in a 1918 book called Installing Efficiency Methods by Charles E. Knoeppel. By the 1990s, the value stream mapping process became part of the lives of many western managers. Its popularity started to outgrow manufacturing and eventually spread into knowledge work industries such as product and software development, IT operations, as well as healthcare, logistics, and many others. What Is the Purpose of VSM? The primary purpose of creating a value stream map is to show you where you can improve your process by visualizing both its value added and non-value added steps. To get started, you need to display every vital step of your workflow, activities, or resources involved and evaluate how that brings value to your customer. This would enable an in-depth analysis of your process and provide you with precise insights into the areas that need to improve. Additionally, VSM can help organizations to better assess the impact of changes in the process and identify more ways to continuously improve. What Are the Benefits of Value Stream Mapping? The essential benefits of using value stream mapping include the following: Identifying and eliminating waste: With the help of VSM, you can better understand where waste is accumulating in your process, including waiting, overproduction, unnecessary processing. Visualizing the entire value stream: The value stream map shows all the steps in a process, including the value-adding and non-value-adding activities and provides a common understanding of the entire workflow. Enabling continuous improvement: VSM highlights the current workflow and brings the focus on future improvement. 10 Years Kanban Experience In 1 Free Book. Project Manager's Guide to Kanban Download your free ebook Value Stream Mapping Examples VSM can be applied and bring value to various industries and processes. VSM in service industries: VSM can be used in banking, insurance, or procurement to map the flow of work and identify inefficiencies such as unnecessary steps or long waiting times for approval. Eliminating such causes can help you streamline your work and improve customer satisfaction. VSM in pharma and healthcare: Similarly, by mapping the patient flow, VSM can help you better understand where the bottlenecks lie in your process. A value stream map can indicate that you need to reduce the patient waiting time, focus on patient outcomes, or focus on your staff productivity. VSM in logistics: Value stream mapping can unlock insights about where in your process costly delays occur, whether is there overstocking or unnecessary transportation, so that you can address these weak links directly. By doing so, organizations can improve their process flow, operations visibility, and control. Why Value Stream Mapping Works Well in Knowledge Work? Value stream mapping is gaining popularity in knowledge work because it allows teams that work in a siloed environment to visualize their work and collaborate better. Even individual contributors can have a bird’s eye overview of how the team’s work is progressing. As a result, teams can increase work handoffs' efficiency, which is a major culprit for accumulating wait time in your system. Waiting is one of the 7 wastes of Lean, and therefore it should be everyone’s priority to minimize it. Mapping your process can help you visualize where handoffs occur, so you can also discover where the bottlenecks (queues) of your process are and come up with a way to minimize their damage to your team’s productivity. How to Create a Value Stream Map with Kanban? Kanban is probably one of the most reliable value stream mapping tools. Especially if you want to visualize a knowledge work process. It is very intuitive to work with and allows you to make changes easily. Basic Kanban board To map your process with Kanban, you need just two elements – a Kanban board and Kanban cards for all your team assignments. Here are the steps to start mapping your value stream and a few examples. 1. Create a Kanban Board If you are new to workflow visualization, it is better to start small. Start by creating a Kanban board, preferably for a single team or department. Be sure to select the most convenient way to map your workflow. You can choose a physical board or a digital software solution such as Businessmap (formerly Kanbanize). 2. Define VSM Purpose and Expectations Afterward, gather the team and clearly explain the purpose of value stream mapping and what you expect to achieve by implementing it. 3. Visualize the Key Stages of Your Workflow Then, bind your process together. By default, a Kanban board comes with three work item states: To Do, In Progress, and Done. Your focus should be on breaking down In Progress into multiple columns to represent your workflow’s most crucial value stream steps. For example, a software development process usually contains the following steps: Tech Design, Coding, Testing, and Code Review. You can add as many columns to your Kanban board as needed. In turn, the "In Progress" area of a procurement team process, for instance, might include the following stages: Request for Quotation, Waiting, and Purchase Order. Procurement process mapped using a Kanban board More precise mapping will logically give you a more comprehensive view and, therefore, more indications of where you can improve your performance. Mapping an entire end-to-end value delivery flow Place special attention on queue stages of your process (ex. "Ready for Review") where work handovers occur. 4. Perform Value Stream Map Analysis When you’ve got a bound process, be sure to select a range of performance metrics to monitor. A simple set of workflow key performance indicators is: Lead time vs. cycle time of your assignments Throughput of your system Amount of work in progress You should always aim to keep lead time and cycle time close to one another. So even if you are super-efficient at processing work, but you’ve got a long backlog that results in customers waiting for too long to receive their order, it won’t matter. When it comes to throughput, you need to keep it as high as possible without sacrificing the quality of the value you deliver to the customer. Work in progress is a key indicator in Lean and Kanban in particular because the more you have of it, the more wait time you will accumulate. So be sure to regulate the number of assignments your team can have in progress simultaneously and adjust them according to your workflow data. VSM Frequently Asked Questions (FAQ) What Is Value Stream Mapping (VSM)? Value stream mapping is a Lean manufacturing tool that helps organizations identify and eliminate waste in their processes and improve operational efficiency. It involves creating a visualization map of the entire end-to-end value delivery process. One way to start using VSM is by mapping your flow on a physical or digital Kanban board. What Are the 4 Steps of Value Stream Mapping? You can implement value stream mapping using Kanban in four steps. Start by creating a basic Kanban board by mapping the Requested, In Progress, and Completed stages of your process. Next, ensure that everyone on your team understands the purpose of applying the VSM tool. Move on to further detail your visualization map to include all critical stages in your process, and finally, set the performance metrics to monitor and assess your progress. What Is the Meaning of VSM? VSM is an acronym for value stream mapping. VSM is a Lean management technique for analyzing the end-to-end process involved in the delivery of a product or a service. A key attribute of the method involves creating a detailed map of all the important steps in every business process that adds value to a product or service. What Are the 3 Types of VSM? There are three types of value stream maps: current state, ideal state, and future state map. The current state map describes the ongoing value delivery process steps. The ideal state map depicts the perfect conditions where no constraints or bottlenecks occur. The future state map is a realistic representation of the organization’s value delivery process. What is a Swimlane Diagram What are your swimlane diagram needs? I'm new to swimlane diagrams and want to learn more. I want to make my own swimlane diagram in Lucidchart. I want to make a swimlane diagram from a Lucidchart template. Contents What are swimlane diagrams? History of swimlanes Swimlane purposes and benefits Attributes and elements of swimlane diagrams Swimlanes as an element of BPMN 2.0 diagram How to do research for a swimlane diagram (a.k.a., Rummler-Brache Diagram) Steps to draw and use a swimlane diagram Making swimlane diagrams with Lucidchart Swimlanes add an extra level of clarity about who does what to process flowcharts. If you're not familiar with using a swimlane diagram tool like Lucidchart, here's everything you need to know, including what they are, and how to create your own swimlane diagram. 6 minute read Want to make a swimlane diagram of your own? Try Lucidchart. It's quick, easy, and completely free. Make a swimlane diagram What are swimlane diagrams? A swimlane diagram is a type of flowchart that delineates who does what in a process. Using the metaphor of lanes in a pool, a swimlane diagram provides clarity and accountability by placing process steps within the horizontal or vertical “swimlanes” of a particular employee, work group or department. It shows connections, communication and handoffs between these lanes, and it can serve to highlight waste, redundancy and inefficiency in a process. This type of diagram is also known as a Rummler-Brache diagram or a cross-functional diagram (swimlanes are sometimes called functional bands). Swimlanes (also written as "swim lanes") are used as a valuable element in Business Process Model and Notation (BPMN and BPMN 2.0); its software design counterpart, Unified Modeling Language (UML); and process flow diagrams (PFDs.) Standard symbols used in all these types of diagrams, combined with the swimlanes, can provide an easy-to-read visual representation of responsibilities in a process. History of swimlanes In the 1940s, a variation of early flow process charts called multi-column process charts began appearing. They were used to spell out processes involving more than one unit or department, similar in purpose if not appearance to today’s swimlane diagrams. In 1990, Geary Rummler and Alan Brache published their book Improving Processes and highlighted swimlane diagrams. The diagrams now are sometimes called Rummler-Brache diagrams after the authors. In Microsoft Office Visio, they’re called cross-functional diagrams. In computer engineering, the swimlane term also appears in JBoss Process Definition Language. This history shows efforts to solve a continuing business problem of process clarity and accountability, leading to today’s well-established usages. Swimlane purposes and benefits In today’s organizations with multiple work groups or departments, this diagramming can help in various ways: It can help to ensure that the right hand knows what the left is doing in an organization. Swimlane Diagrams, and swimlanes used in other diagram types, highlight which process steps or sub-processes are assigned to a particular actor in the organization. By spelling this out in a diagram, you can highlight redundancies between different lanes and identify bottlenecks, waste and other inefficiencies. This sometimes reveals duplicative or unnecessary steps in a process, such as different departments performing the same task. It also can highlight process delays or capacity constraints within a particular swimlane so that they can be addressed and resolved. This can increase performance and quality and reduce unnecessary work and costs. You can use a second Swimlane Diagram to model a better way to structure the process or to account for changing circumstances, such as staffing changes or technology changes. Like other diagrams, Swimlane Diagrams can communicate in clearer terms than a narrative description would. Swimlane Diagrams can be formalized as a way to integrate processes between teams or departments, resulting in cleaner processes on an ongoing basis. Attributes and elements of swimlane diagrams Using standard symbols of whatever type of process flow chart is being produced, swimlanes introduce parallel or vertical or horizontal lines grouping the process steps by actor, such as employee, work group department or even an information system. Each lane is labeled by that actor. Sometimes, but not always, horizontal lanes are more practical given that desktop computer screens are wider than tall. Process steps are spelled out within their respective lanes, and also shown are the interconnection of steps between lanes. This shows how the different actors interact to keep a process rolling efficiently. Want to make a swimlane diagram of your own? Try Lucidchart. It's quick, easy, and completely free. Make a swimlane diagram Swimlanes as an element of BPMN 2.0 diagram In BPMN 2.0, pools/swimlanes are of one of four element types for Business Process Diagrams. A pool represents major participants in a process. A different pool may be in a different company or department, but still involved in the process. Swim lanes within a pool show the activities and flows for a certain role or participant, defining who is accountable for what parts of the process. The three other element types are: 1. Flow objects: events, activities and gateways 2. Connecting objects: sequence flow, message flow, and association 3. Artifacts: data object, group, and annotation You can learn more about BPMN symbols here. How to do research for a swimlane diagram (a.k.a., Rummler-Brache Diagram) 1. Determine your goal and what process or processes should be studied to achieve that goal. Think about what leve