Joinery Midterm PDF
Document Details
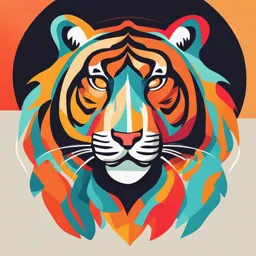
Uploaded by ImprovingBlankVerse4580
BCIT
Tags
Summary
This document provides information on Design & Millwork Drawings, types of saw blades and woodworking joints. It covers architectural and residential millwork, types of communication, and important considerations like budgets and design changes.
Full Transcript
Design & Millwork Drawings Architectural millwork Communication is between the Architect and millwork company Usually more information Design is usually set before the estimating phase AWMAC (Architectural Woodwork Manufacturers Association of Canada) Residential millwork...
Design & Millwork Drawings Architectural millwork Communication is between the Architect and millwork company Usually more information Design is usually set before the estimating phase AWMAC (Architectural Woodwork Manufacturers Association of Canada) Residential millwork Communication between owner, designer and millwork company Design can change at the estimating phase More variation in construction standards CKCA (Canadian Kitchen Cabinet Association Type of communication : RFI:( request info) - Written communication used to gather information that wasn’t initially included in the scope of the construction contract - Find missing specifications like hardware, appliances, finishes etc. - Clarify aspects of the project - Make substitutions where needed IFA:( issue for approval) - Document or drawing issued for client, designer, architect or organization to review and make changes - Drawings contain all information necessary for construction - Sometimes RFI questions may be asked within - Can go back and forth between client and millwork company once or tens of times IFC( issued for construction): - Have been modified to include all changes, relevant addenda, selection of alternate pricing options, and accurate site measurements Millwork shop drawing : - These are the shop drawings the millwork company will build from Design Drawings Design drawings will come with a spec package that should contain all information needed by the millwork company to complete shop drawings on their end. Information commonly missing that will hold up production: Finishing schedule Hardware (pulls in particular) Accurate appliance specs. Puck lights Adequate details IFA revisions : These drawings can contain minor changes to reflect site measurements or major design changes based on design conflicts, needs of the client, budget or time constraints. Reviewing and returning IFA drawings as soon as possible to the millwork company is crucial in maintaining build schedules. IFC & millwork shops drawings : The final drawings the millwork shop will build off of and must be exact. They are often very different from the original design drawings. Budget is the most common reason for major design changes. The way a designer can minimize necessary design changes include: Take material size into consideration. Designing outside of standard thicknesses, widths and lengths are very expensive and are often the first thing to change Provide accurate specs EARLY in the process Be familiar with the site conditions and sizes of the space Plan for things like plumbing, electrical, hardware and attachment method limitations Types of Saw Blades The most common types of saw blades are the rip blade, the crosscut blade and the combination blade, which combines certain features of the other two. In addition to these three main types, there are many specialty blades and tooth shapes. Rip blade The rip blade is designed to cut in the direction of wood grain. Its large, chisel-like teeth have sharply angled hooks and deep gullets, which can take out long lengths of wood fiber as they move through the wood. The resulting cut is not particularly smooth, but the blade cuts quickly along the grain. Most often, the rip blade is easily distinguished from the crosscut blade by examining the tooth shape and the hook angle. On a rip blade, all or most of teeth are flat-topped, and there is a pronounced, positive (forward leaning) hook angle. In theory, the greater the angle of the hook, the more freely the ripsaw cuts and the smaller the demand on power to drive it. This is true only to a point, however. If the angle of the hook is too great, the saw will vibrate at the tooth and cause a rough cut. Therefore, the maximum hook angle for fast ripping very soft wood is 30° and for harder wood 20°. For extremely hard wood, the angle should be reduced to between 10° and 15°. Crosscut blade The crosscut blade (Figure 3) produces a fairly smooth edge and is designed for cutting across wood grain. The teeth are often smaller than those on a ripsaw blade and are greater in number. They are also ground to a sharp point so that they will sever wood fibers. Because only a small amount of fine sawdust is produced by each tooth, the gullets are small. For this reason a crosscut blade should never be used for ripping, as the gullets would soon become clogged and the blade would bind. The friction would also cause the outside of the blade to heat up rapidly, and because the centre of the blade would remain cool, the blade could crack or warp and be rendered useless. Woodworkers should always be wary if they find wood difficult to feed into a crosscut blade or if the wood starts to smoke. These signs indicate that either the blade is too dull or the wrong type of blade has been installed. Whatever the case, you should stop cutting, switch off the machine and correct the problem before finishing the cut. Like the rip blade, the crosscut blade is recognized by examining the tooth shape and the angle of the hook. Teeth on a crosscut blade are angled alternately to the left and to the right (Figure 3). This configuration is known as ATB (Alternate Tooth Bevel). Whereas the teeth on the rip blade have a pronounced positive hook, the teeth on the crosscut blade typically have a smaller (less than 10°), neutral (0°) or negative hook (the teeth lean backwards). Combination blade The combination blade (Figure 4) may be used for both ripping and crosscutting, but the quality and speed of the cuts are not as good and as fast as those made by the rip and the crosscut blades. There are various kinds of combination blades. One of the most common types has teeth arranged in sets of five (Figure 4), with each set consisting of four crosscut teeth and one ripping tooth with a single large gullet. Triple chip tooth A newer tooth design, known as a triple chip (Figure 7), is most often found in combination with rip or even crosscut teeth, but can be found as the only tooth shape on a saw blade. Depending on the combination, this type of tooth can be incorporated into blades used for either ripping or for crosscutting. The most common use of the triple chip tooth is in combination with flat topped (rip) teeth in a blade used for cutting composite materials such as MDF and particle board. This combination of teeth is also appropriate in a rip blade for softer woods, where the triple chip design aids in breaking up softwood fibers. For veneered or melamine covered composite boards, the triple chip tooth may be seen in combination with crosscut (ATB) teeth Sheet Goods sheet goods refer to materials that come in flat sheets. The term also includes some sheet products that can be rolled. Common example: Less common : Compose board: Sheet goods made from fibers, chips or flakes are known as composition boards: MDF Common trade names include Medite* and Ranger* board Sizes of MDF: Thickness From 2.5 mm (1/10”) to 50 mm (2”) with the most common being: 6mm (1/4”) 12mm (1/2”) 19 mm (3/4”) 25 mm (1”) Most sheets can be purchased 2mm +/- (1/16”) undersize for thicknesses Width & Length Like most composite boards, MDF sheets are sold approximately 25 mm (1”) oversize in width and length Standard press widths are for an oversized 4’ (1220 mm) or 5’ (1520) Standard press length is for an oversized 18’ (5490) sheet Particle board Sizes of Particle board: Thickness Typical thicknesses are 3/8” (10mm) to 1 5/8” (41mm) with door core as thick as 2 ¼” 57mm) New processes can produce sheets as thin as 1/32” (0.8mm) For veneering, most thicknesses are available in 1/16” (2mm) increments Width & Length Press widths allow oversized 4’ or 5’ panels (1220 or 1520) A wide range of lengths, usually 8’, 10’, 12’, 14’ Like MDF, widths and lengths are always 1’ (25mm) oversize Plywood Plywood is a type of sheet goods tat has a minimum of 3 layers: Wood veneer on the front and back faces A core layer that can also be wood veneer, composition board, solid wood or a combination Plywood veneer core construction Layers of veneer are glued at right angles to each other. A greater number of piles usually result in greater stability. All construction methods must be balanced to prevent the sheet from warping Classes of plywood Construction & Industrial (aka softwood plywood) Used where strength is more important than appearance Primarily softwood veneers & most panels are unsanded. Examples include sheathing, roofing and floor underlayment in wood frame construction Some of the upper grades are sanded and may be used in millwork and sign making. This class includes overlay plywoods and some inexpensive hardwood plywoods, like poplar and aspen. Most are made with a waterproof adhesive. Hardwood & Decorative (aka hardwood plywood) Appearance is the priority over strength A wide variety of cores used Primarily hardwood veneer faces (some high-end softwoods) Mainly interior use – usually not a waterproof glue Sizes of plywood: Thickness A wide range, usually from 1/8” (3mm) to 1 ½” (38mm) Width & Length Most common is 4’ x 8’ (1220mm x 2440mm) Plywood with a composition core is made 1” oversize in width and length Some fir plywood available as 4’ x 10’ (1220mm x 3048mm Overlay plywood Used for signs and smooth concrete formwork, refers to softwood plywood with a special, resin impregnated overlay material on one or both sides. It comes in two grades: Medium Density Overlay (MDO) is the most common High Density Overlay (HDO) has a very smooth, hard, chemically resistant face Veneer & Veneer Patterns Veneer Veneer is thin sheets of solid wood cut or sliced from a log called a flitch. A flitch is the term used for the stack or bundle of veneers cut from a log. Hardwood or softwood face veneer may be sliced as thin as 1/40 of an inch or even thinner in the case of some imported plywood. Softwood interior piles (veneer) are usually rotary cut and can be up to 3/16 of an inch thick. Shown above are hardwood flitches that will be made into face veneer. Advantages to using veneer Good use of declining resources Can be used for curved work Matching techniques are much easier to achieve with veneer than solid wood Various backing materials and adhesives can be used for a wide range of applications Veneer cutting methods: Rotary cut : Rotary cut veneer is produced by mounting the log section on a lathe and rotating it against a stationary knife Most softwood veneer is rotary cut, along with some hardwood species Flat cut : Flat-cut veneer is taken from a half log and cut parallel to the center of the log This slicing technique produces definite cathedrals on the veneer faces. Most hardwood face veneer is cut using this method Half round : Half-round cut veneer is produced by mounting a half-log section on a lathe-arm and rotating it against a stationary knife The pattern produced with this cutting method is similar to flat sliced but the leaves are wider Quarter sliced: Quarter-sliced veneer is taken from a quartered log and cut roughly parallel to the rays. Some species produce a narrow stripe figure from this technique, others with interlocked grain produce a pattern referred to as a ribbon stripe. This cutting technique is very common for species like oak and mahogany. Rift cut : Rift-cut veneer is also taken from a quartered log but cut at roughly 45 degrees to the rays and growth rings This cutting technique is often used for oak to minimize large ray flecks. When the grain is straight and fine textured the pattern is called a comb grain. Plywood face matching methods Once the veneer log or part has been sliced by any of the previous methods (except rotary cut), the slices (or leaves): Are kept in a sequenced stack called a flitch. Joined together into faces or backs by one of the matching methods described next. Main face matches: Book Match This is the most common pattern. Every second piece is turned over like opening a book which forms a mirrored pattern. Slip Match Each piece is slid without flipping, so that the left side of each piece is joined to the right side of the next Random Match Less common match. Gives a casual, unmatched effect. No attempt is made to match colours or grains. Pleasing Match Similar to random match, but should have a similar colour on all leaves. Other Veneer Patterns Methods for veneer assembly The 3 main methods are stitching, taping and edge gluing. Stitching is done on the back side of the veneer while taping is done on the face and then sanded off after pressing. TapingStitching To prevent splits during handling and pressing, all methods should have veneer tape for the full width at each end. Adhesives for veneering For hot pressing: Cross-linked PVA or Urea Formaldehyde For cold pressing: Any good wood glue, but hard setting glues like UF 109 are best The use of contact cement is NOT recommended (or accepted by the Architectural Woodwork Institute) Woodworking Joints Some joints are very precise (like the dowel joint) and others allow movement during assembly (like a spline or biscuit joint) Purpose of joints: Hold and support These joints add strength to the connection point of two pieces Decorative Decorative joints can be used to highlight beautiful joinery or to hide methods of construction Frame joints These joints are used when constructing items like window frames or doors Casework joints Casework joints are used to connect and strengthen cabinet parts, boxes and shelves. Common joints seen in industry are dowel joints, dados, rabbets, groves, splines and biscuit joints. A dado is a three-sided recess that travels across the grain of a piece of lumber while a groove runs with the grain. A rabbet is a recess that runs along the edge of a board and is open on one side. Mechanical fasteners Casework joints can be made using mechanical fasteners which come in a wide variety of styles and attachment methods. Drawer joints Drawers can be constructed using a variety of joints Drawer bottoms are: Set into a groove on all 4 sides for premium grade Set into a groove on the 2 sides and the front for custom Mill option for economy Other useful joints