IMP Reviewer Midterms PDF
Document Details
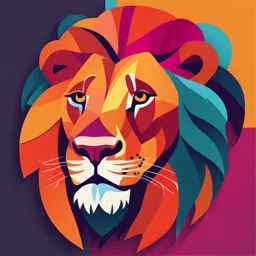
Uploaded by OrderlyZinc8744
Tags
Summary
This document provides an overview of industrial materials, manufacturing processes, and engineering metals. It details the history of materials and manufacturing, along with a classification of materials, manufacturing goods, and simplified steps of the product life cycle.
Full Transcript
History of Materials > Stone Age > Copper and Bronze Age > Iron Age > Steel Age ❑The current age is that of plastics, composite materials and exotic alloys. Materials, Manufacturing and the Standard Living MANUFACTURING GOODS ✓Producer goods: Intermediate goods used to manufacturer either prod...
History of Materials > Stone Age > Copper and Bronze Age > Iron Age > Steel Age ❑The current age is that of plastics, composite materials and exotic alloys. Materials, Manufacturing and the Standard Living MANUFACTURING GOODS ✓Producer goods: Intermediate goods used to manufacturer either producer or consumer goods ✓Consumer goods: Purchased directly by the consumer Simplified Steps of the Product life Cycle Start up - new product or new company, low volume, small company Rapid Growth - Products become standardized and volume increases rapidly. Maturation - standard designs emerge. Process development is very important. Commodity or Declined Commodity – long-life, standard of the industry type of product Decline - product is slowly replaced by improved products. MATERIALS AND PROCESSES Manufacturing cost is the largest cost in the selling price. - The largest manufacturing cost is material cost, not direct labor. ❑ Material, men, methods and equipment are interrelated factors in manufacturing that mustcombined properly to achieve low cost, superior quality and on-time delivery. ❑ Materials to be used must be selected and specified to meet the design engineer’s requirement. PRODUCTION SYSTEM-THE ENTERPRISE ❑People ❑Money ❑Equipment ❑Materials ❑Supplies ❑Markets ❑Management ❑Manufacturing System ❑All aspects of commerce BASIC MANUFACTURING SYSTEMS o Shaping o Drilling o Turning o Milling o Sawing o Broaching o Abrasive Machining 8 BASIC TYPES OF MACHINE TOOLS o Shapers (Planers) o Drill Presses o Lathes o Boring Machines o Milling Machines o Saws o Broaches o Grinders MANUFACTURING SYSTEM DESIGNS ❑ Job shop characterized by large varieties of components, general-purpose machines and a functional layout. - Machines are collected by function - Material is moved from machine to machine in carts or containers and is called the lot or batch. - To be the least cost-efficient of all the systems because of its design ❑ Flow shop are characterized by larger volumes of the same part or assembly, special-purpose machines and equipment, less variety, less flexibility and more mechanization. - Common light bulb - A transfer line producing an engine block - If interrupted, the line manufactures large lots but is periodically “change over” to run a similar but different component. ❑ Linked-cell shop is composed of manufacturing and subassembly cells connected to final assembly (linked) using a unique form of inventory and information called KANBAN. - Used in lean production systems where manufacturing processes and subassemblies are restructured into U-shaped cells so they can operate on a one piece flow basis, like final assembly. ❑ Project shop is characterized by the immobility of the item being manufactured. - In the construction industry, bridges and roads - In the manufacture of goods, large airplanes, ships, large machine tools and locomotives - Workers, machines, and materials come to the site - Job shop usually supplies parts and subassemblies to the project shop in small lots. ❑ Continuous process are used to manufacture liquids, oils, gases and powders. -Usually large plants producing goods for other producers or mass producing canned or Bottled goods for consumers. CHARACTERISTICS OF PROCESS TECHNOLOGY ❑ Mechanics (Static or dynamic) ❑ Economic or costs ❑ Time Spans ❑ Constraints ❑ Uncertainties and process reliability ❑ Skills ❑ Flexibility ❑ Process capability METALS IN ENGINEERING AND MANUFACTURING METAL - A metal is a type of material that conducts electricity and heat relatively well. When metal is freshly crafted, polished, or fractured, it exhibits a lustrous appearance. - usually have a high melting point and are less likely to degrade under high temperatures. Properties of Metals ❑ Physical Property - Physical characteristics of metals include things like their appearance, color, luster, weight, and texture. ❑ Mechanical Property - Mechanical properties of metals, such as hardness, ductility, malleability, and so on, represent their inherent capacity. ❑ Chemical Property - Chemical properties indicate how metals behave in different chemical processes. Types of Metals ❑ Steel - is a type of alloy of several chemical elements that are made of iron with carbon to improve its strength and fracture resistance. It is the most widely used material for building infrastructure and industries in the world. ❑ Carbon Steel - defined as steel that has its properties mainly due to its carbon content and does not contain more than 0.5% of silicon and 1.5% manganese. ❑ Alloy Steel – it has elements other than carbon added in sufficient quantity, in order to obtain special properties for the metal. ❑ Stainless Steel- It is defined as that steel when directly heat treated and finished resists oxidation and corroding from corrosive media. It is also known as rust-free steel because it contains a minimum of about 11% chromium that prevents iron from rusting and also provides heat-resistant properties. ❑ Iron – is a chemical element that is represented as the symbol Fe. Iron is the most commonly used and cheapest metal on Earth. ❑ Pig Iron - It is a crude form of iron and is used as a raw material for the production of various other ferrous metals, such as cast iron, wrought iron, and steel. ❑ Cast Iron - is obtained by further melting pig iron with coke and limestone in a furnace called a cupola. It is the primary allow of iron and carbon. The carbon contents in cast iron vary from 1.7% to 4.5%. ❑ Wrought Iron - it is a type of iron alloy that has a very low carbon content of about 0.08%. ❑ Aluminum - is a type of metal with the symbol Al and atomic number 13. It is a bluish-white, light metal having a specific gravity of 2.7 and a melting point is 658°C. ❑ Copper -. It is a soft, malleable, and ductile metal with a reddish-brown appearance. Its specific gravity is 8.9 and its melting point is 1083°C. ❑ Brass - is the most commonly used copper and zinc alloy. ❑ Bronze - These types of metals are comparatively hard, resist surface wear, and can be shaped or rolled into wires, rods, and sheets very easily. ❑ Cobalt - commonly found in plants and animals, air, water, soil, and rocks. It is used in many alloys that are used to make parts for aircraft engines, gas turbines, and high-speed steel. ❑ Magnesium - It is a lustrous gray solid that shares many physical and chemical properties. This is the lightest metal and has a tensile strength of the cast metal is 910 kg/cm2. ❑ Nickel - It is a silvery-white metal capable of taking a high polish. Its specific gravity is 8.85 and its melting point is 1452°C. ❑ Lead- is a chemical component with the symbol Pb and has the atomic number 82. ❑ Tin- it is a silver-colored metal that typically has a pale-yellow tinge. Tin is soft enough to be cut with little force and a strip of tin can be folded by hand with little effort. ❑ Zinc- it is represented as symbol Zn and atomic number 30. Zinc is a brittle metal and has a silver brown appearance when no oxidation occurs. The specific gravity of zinc is 7.1 and its melting point is 420°C. ❑ Titanium- is found in nature, it can be reduced to produce a lustrous transition metal with a silver color, low density, high strength, and corrosion-resistant. ❑ Tungsten - It is a rare metal that occurs naturally on Earth in the form of compounds with other elements. Tungsten has a melting point of 3,422 °C and also has the highest boiling point of 5,930 °C. ❑ Silicon- It is a type of chemical element with the symbol Si and atomic number 14. It is a hard, brittle, solid with a bluish-gray metal. Its melting point is 1414 °C and its boiling point is 3265 °C. ❑ Silver- It is a soft, white, lustrous transition metal, displaying the highest electrical conductivity and thermal conductivity. It is found in pure form in the earth’s crust and is the free native form of native silver. ❑ Gold - It is a type of transition metal and falls in the same periodic table column as silver and copper. Gold is a bright, light orange-yellow color, dense, soft, malleable, and ductile in the pure form of the metal. Metals in Engineering:” Properties, Processes, and Manufacturing Techniques" Properties and Uses of Common Engineering Metals o Steel (Carbon & Alloy Steel): High strength, used in structural frameworks, tools. o Aluminum: Lightweight, corrosion-resistant, used in aerospace, Automotive industries. o Copper: Excellent conductivity, used in electrical wiring, plumbing. O Titanium: High strength-to-weight ratio, used in aerospace, medical implants. o Cast Iron: High wear resistance, used in engine blocks, machine bases. o Nickel Alloys: Heat and corrosion resistance, used in jet engines and chemical processing. Casting and Forming Processes o Casting: Molten metal poured into molds to create complex shapes. Types: Sand casting, die casting, investment casting. Example Uses: Engine blocks, sculptures. o Forming: Metal shaped through deformation (forging, rolling, extrusion). Examples: Stamping for car panels, extrusion for aluminum frames. Machining Processes o Turning: Material removal using a rotating workpiece. Used for shaft sand cylindrical parts. o Milling: Rotating cutting tools remove material to create complex parts like gears. o Drilling: For hole-making, used in bolted connections. o Grinding: Used for surface finishing and precision. Joining and Finishing Operations o Welding: Melts metals to join parts, commonly used in structures and automotive. o Brazing & Soldering: Uses filler metal to join parts at lower temperatures (used in electronics and plumbing). o Surface Finishing: Polishing, anodizing, or electro plating to improve appearance and corrosion resistance. Processes and Techniques Related to Manufacturing o Heat Treatment: Changes metal properties through heating/cooling (annealing, tempering). Used to strengthen or soften metals. o Metal Injection Molding (MIM): Used for small, complex metal parts. o Powder Metallurgy: Produces metal parts by pressing/sintering powdered metal. o Additive Manufacturing (3D Printing): Builds metal parts layer by layer, used in aerospace and medical industries.