Hydraulic Systems PDF
Document Details
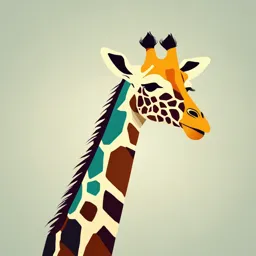
Uploaded by SmoothDahlia3403
2022
Juan Cano
Tags
Summary
This document is a textbook on hydraulic systems. It covers topics such as fluid theory, pressure, flow, and viscosity. Includes definitions, diagrams, and examples to help the reader to understand. The book appears to be authored by Juan Cano.
Full Transcript
MICHELIN NORTH 1 OF 2 AMERICA TITLE: Hydraulic Systems Edition Date: 2022...
MICHELIN NORTH 1 OF 2 AMERICA TITLE: Hydraulic Systems Edition Date: 2022 PAGE Entity: NA/TTG Author: Juan Cano Validator: Bruce Dennis Classification: D3 Hydraulic Systems Ret. Code RA Printed copies of this document are uncontrolled Copyright © 2012 Michelin North America. All rights reserved. No part of this material may be reproduced or distributed in any form or by any means, or stored in any data base or retrieval system, without the prior written permission from Michelin 800 E. Faris Rd Greenville, SC 29607 MICHELIN NORTH 2 OF 2 AMERICA TITLE: Hydraulic Systems Edition Date: 2022 PAGE Entity: NA/TTG Author: Juan Cano Validator: Bruce Dennis Classification: D3 This page intentionally left blank. Ret. Code RA Printed copies of this document are uncontrolled Copyright © 2012 Michelin North America. All rights reserved. No part of this material may be reproduced or distributed in any form or by any means, or stored in any data base or retrieval system, without the prior written permission from Michelin 800 E. Faris Rd Greenville, SC 29607 MICHELIN NORTH PAGE 1 OF 24 AMERICA TITLE: Hydraulic Systems Edition Date: 2022 Entity: NA/TTG Author: Juan Cano Validator: Bruce Dennis Classification: D3 Fluid Theory Ret. Code RA Printed copies of this document are uncontrolled Copyright © 2012 Michelin North America. All rights reserved. No part of this material may be reproduced or distributed in any form or by any means, or stored in any data base or retrieval system, without the prior written permission from Michelin 800 E. Faris Rd Greenville, SC 29607 MICHELIN NORTH PAGE 2 OF 24 AMERICA TITLE: Hydraulic Systems Edition Date: 2022 Entity: NA/TTG Author: Juan Cano Validator: Bruce Dennis Classification: D3 This page intentionally left blank. Ret. Code RA Printed copies of this document are uncontrolled Copyright © 2012 Michelin North America. All rights reserved. No part of this material may be reproduced or distributed in any form or by any means, or stored in any data base or retrieval system, without the prior written permission from Michelin 800 E. Faris Rd Greenville, SC 29607 MICHELIN NORTH PAGE 3 OF 24 AMERICA TITLE: Hydraulic Systems Edition Date: 2022 Entity: NA/TTG Author: Juan Cano Validator: Bruce Dennis Classification: D3 Table of Contents Pressure / Force / Area....................................................................................................................... 5 Introduction to Fluid Power............................................................................................. 6 Physical Properties of a Fluid.......................................................................................... 6 Different Types of Fluids............................................................................................. 6 Molecular Energy......................................................................................................... 6 Compressibility............................................................................................................ 7 Force Transmission...................................................................................................... 7 Pressure / Force / Area................................................................................................. 8 Pressure / Force / Area Exercises............................................................................... 11 Pressure / Flow.................................................................................................................................. 13 The Relationship between Pressure and Flow in a System........................................... 14 Flow............................................................................................................................... 14 Velocity...................................................................................................................... 14 Flow Rate................................................................................................................... 14 Pressure.......................................................................................................................... 14 Fluid Flow Paths........................................................................................................ 16 Parallel Flow Path...................................................................................................... 16 Series Flow Path......................................................................................................... 17 Viscosity / Temperature.................................................................................................................... 19 Petroleum Based Hydraulic Fluids................................................................................ 20 Fluid Properties.............................................................................................................. 21 Viscosity........................................................................................................................ 21 Measuring Viscosity................................................................................................... 21 Saybolt Universal Seconds......................................................................................... 21 Kinematic Viscosity................................................................................................... 22 Factors that affect viscosity........................................................................................ 24 Temperature............................................................................................................... 24 Viscosity Index........................................................................................................... 24 Ret. Code RA Printed copies of this document are uncontrolled Copyright © 2012 Michelin North America. All rights reserved. No part of this material may be reproduced or distributed in any form or by any means, or stored in any data base or retrieval system, without the prior written permission from Michelin 800 E. Faris Rd Greenville, SC 29607 MICHELIN NORTH PAGE 4 OF 24 AMERICA TITLE: Hydraulic Systems Edition Date: 2022 Entity: NA/TTG Author: Juan Cano Validator: Bruce Dennis Classification: D3 This page intentionally left blank. Ret. Code RA Printed copies of this document are uncontrolled Copyright © 2012 Michelin North America. All rights reserved. No part of this material may be reproduced or distributed in any form or by any means, or stored in any data base or retrieval system, without the prior written permission from Michelin 800 E. Faris Rd Greenville, SC 29607 MICHELIN NORTH PAGE 5 OF 24 AMERICA TITLE: Hydraulic Systems Edition Date: 2022 Entity: NA/TTG Author: Juan Cano Validator: Bruce Dennis Classification: D3 Pressure / Force / Area Ret. Code RA Printed copies of this document are uncontrolled Copyright © 2012 Michelin North America. All rights reserved. No part of this material may be reproduced or distributed in any form or by any means, or stored in any data base or retrieval system, without the prior written permission from Michelin 800 E. Faris Rd Greenville, SC 29607 MICHELIN NORTH PAGE 6 OF 24 AMERICA TITLE: Hydraulic Systems Edition Date: 2022 Entity: NA/TTG Author: Juan Cano Validator: Bruce Dennis Classification: D3 Introduction to Fluid Power Machinery was invented to perform work and may use mechanical, electrical or fluid power to accomplish that work. The study of Hydraulics deals with the use and characteristics of a fluid and how it can be used to perform work. Hydraulics is the transmission of power through the use of a confined liquid. In industry, the use of fluid power is advantageous in some areas as a source of energy to power a machine. There are several advantages to using hydraulic systems, some are listed below; Variable speed control Reversible motion of prime movers System overload protection High power output in a small package Power components can stall out Motion can be transmitted without the slack or clearances needed in mechanical equipment Fluids don’t wear out like mechanical machines Versatile, smooth, uniform action for many applications Can span great distances Fluid power is so widely used as a source of energy we will begin by studying fluids and their characteristics. Physical Properties of a Fluid Different Types of Fluids A fluid is a substance that can flow and possess no definite shape. A fluid may be a liquid or gas. Molecular Energy Any substance is made up of molecules. The molecular energy of any type of substance will define it and create the characteristics used in any application. When we consider the molecular energy you have to look at the three basic types of matter. The molecules of a solid have a very strong attraction force. They are so closely attracted to each other and barely vibrate creating the molecular energy of a solid. The molecules of a gas aren’t attracted to one another, as a matter of fact the molecules will repel each other. Constantly expanding its boundaries and bouncing off other molecules or the container walls. This is the molecular energy of a gas. However unlike a gas, the molecules of a liquid are more closely attracted to each other. They are not in a rigid position nor do they have an attraction such as a solid. Ret. Code RA Printed copies of this document are uncontrolled Copyright © 2012 Michelin North America. All rights reserved. No part of this material may be reproduced or distributed in any form or by any means, or stored in any data base or retrieval system, without the prior written permission from Michelin 800 E. Faris Rd Greenville, SC 29607 MICHELIN NORTH PAGE 7 OF 24 AMERICA TITLE: Hydraulic Systems Edition Date: 2022 Entity: NA/TTG Author: Juan Cano Validator: Bruce Dennis Classification: D3 Liquid molecules are a combination of the molecular energy of a solid and a gas. Liquid molecules are continuously moving, slipping and sliding past one another, even when the liquid is at rest, creating the molecular energy of a liquid. Since this slipping and sliding action of a liquid is continuously happening, it will take the shape of any container. It may or may not fill up the container depending on the volume of liquid. The liquids ability to accomplish this is what creates one of the first basic differences between a gas and a liquid. Compressibility The primary difference between a gas and a liquid is their compressibility. With the molecules of a gas trying to always expand to fill their container a gas is considered compressible. With the molecules of a liquid in close contact with one another, liquids will exhibit one characteristic of a solid. Liquids are considered non-compressible. Since liquids are relatively incompressible and can take the shape of their container, they possess certain advantages for transmitting a force. Force Transmission When a force is transmitted through a solid, the result will be a force in the same direction and the same magnitude (disregarding any frictional loss). This is an example of a mechanical source of energy; belts & pulleys, chains & sprockets, gear drives, etc. When a force is transmitted through a confined fluid it reacts in a special way. When a force is applied to a confined gas, the gas will compress and that same force (intensity) will be transmitted equally in all directions. When a force is applied to a confined liquid, the liquid will not compress and that same force (intensity) will be transmitted equally in all directions. The only difference between the two fluids would be their compressibility. The advantage fluid energy has over a mechanical source of energy is the mechanical energy is transmitted in one direction, where as the fluid energy is transmitted equally in all directions. Before we can discuss force transmission we have to define a force. Ret. Code RA Printed copies of this document are uncontrolled Copyright © 2012 Michelin North America. All rights reserved. No part of this material may be reproduced or distributed in any form or by any means, or stored in any data base or retrieval system, without the prior written permission from Michelin 800 E. Faris Rd Greenville, SC 29607 MICHELIN NORTH PAGE 8 OF 24 AMERICA TITLE: Hydraulic Systems Edition Date: 2022 Entity: NA/TTG Author: Juan Cano Validator: Bruce Dennis Classification: D3 The force (intensity) created inside the liquid is based upon the principle discovered in the 17th century by the French scientist Blaise Pascal. Pascal’s Law states; the force applied to a confined fluid is transmitted equally in all directions in the form of fluid pressure. Pressure / Force / Area Pressure is a measure of a force’s intensity. To measure pressure, the total force is divided by the area on which it is acting. The mathematical expression that describes Pascal’s Law is: Force lbs Force kg = = Area in Area cm To solve for any other unknown: = "# =$ ∙! "# &= ! $ US ISO Force Pounds (lbs) Kilogram (kg) Area Square inches (in²) Square centimeters (cm²) Pressure lbs/in² or PSI kg/cm² To better understand the effect of pressure, we’ll look at a more practical example of two pistons; one large, one small connected together by a fluid filled tube. Ret. Code RA Printed copies of this document are uncontrolled Copyright © 2012 Michelin North America. All rights reserved. No part of this material may be reproduced or distributed in any form or by any means, or stored in any data base or retrieval system, without the prior written permission from Michelin 800 E. Faris Rd Greenville, SC 29607 MICHELIN NORTH PAGE 9 OF 24 AMERICA TITLE: Hydraulic Systems Edition Date: 2022 Entity: NA/TTG Author: Juan Cano Validator: Bruce Dennis Classification: D3 The amount of surface area for the pressure to act on allowed the larger force to be supported. Since surface area was a key in supporting the larger force, then the amount of surface area (effective area) is just as important as the pressure or force values. Next we need to look at determining the surface area in an application. The surface area of a particular application may or may not be a given value. Surface area in hydraulic actuators usually revolves around calculating the value from a given diameter. Typical cylinder call-outs (information) in industry, as illustrated below, use diameter as a basis for size. For example; the three most important values required from a cylinder application would be piston/cylinder/bore diameter, rod diameter and stroke length. If the rod diameter is of a standard size, for the cylinder size, then it may be omitted and the call-out may be simplified to piston/cylinder/bore diameter and stroke length. Once the diameter is known the surface area can be calculated. The following are three of the most common area formulas used in fluid power. * &'() = * ∙ # + ,' &'() = -+ ∙.. 0123 ,' &'() = -+ ∙ 3 Ret. Code RA Printed copies of this document are uncontrolled Copyright © 2012 Michelin North America. All rights reserved. No part of this material may be reproduced or distributed in any form or by any means, or stored in any data base or retrieval system, without the prior written permission from Michelin 800 E. Faris Rd Greenville, SC 29607 MICHELIN NORTH PAGE 10 OF 24 AMERICA TITLE: Hydraulic Systems Edition Date: 2022 Entity: NA/TTG Author: Juan Cano Validator: Bruce Dennis Classification: D3 The area relationship inside most hydraulic cylinder applications is not the same from one side to the other. The rod consumes some of the available (effective) surface area on one side of the piston (cylinder). A different approach is used to calculate the area on one side than the other. The difference in surface area from one side to another dictates that different terminology be used to distinguish the two sides. Major/Cap side is used where the full amount of surface area is fully utilized, whereas Minor/Rod side is used where the surface area is diminished. Ret. Code RA Printed copies of this document are uncontrolled Copyright © 2012 Michelin North America. All rights reserved. No part of this material may be reproduced or distributed in any form or by any means, or stored in any data base or retrieval system, without the prior written permission from Michelin 800 E. Faris Rd Greenville, SC 29607 MICHELIN NORTH PAGE 11 OF 24 AMERICA TITLE: Hydraulic Systems Edition Date: 2022 Entity: NA/TTG Author: Juan Cano Validator: Bruce Dennis Classification: D3 Pressure / Force / Area Exercises 1. Calculate the missing information to extend or to retract the cylinder using the given information. Pressure Piston Dia. Rod Dia. Force a. P1 = 445 2.0” 1400 lbs (5.08 cm) (635.03 kg) 845 b. P2 = 2.0” 1 3/8” 1400 lbs (5.08 cm) (3.49 cm) (635.03 kg) 223.5 c. P1 = 3 1/2” 2150 lbs (8.89 cm) (975.22 kg) d. P2 = 297.94 3 1/2” 1 3/4” 2150 lbs (8.89 cm) (4.45 cm) (975.22 kg) 4 e. P1 = 1025 psi 12880.56 lbs (72.06 bar) (5842.52 kg) f. P2 = 1025 psi 4.0” 2 9660.42 lbs (72.06 bar) (10.16 cm) (4381.89 kg) 16689.75 g. P1 = 850 psi 5.0” (59.76 bar) (12.7 cm) 12517.31 h. P2 = 850 psi 5.0” 2 1/2” (59.76 bar) (12.7 cm) (6.35 cm) Ret. Code RA Printed copies of this document are uncontrolled Copyright © 2012 Michelin North America. All rights reserved. No part of this material may be reproduced or distributed in any form or by any means, or stored in any data base or retrieval system, without the prior written permission from Michelin 800 E. Faris Rd Greenville, SC 29607 MICHELIN NORTH PAGE 12 OF 24 AMERICA TITLE: Hydraulic Systems Edition Date: 2022 Entity: NA/TTG Author: Juan Cano Validator: Bruce Dennis Classification: D3 Pressure / Force / Area Exercises (Continued) 1. Calculate the missing information to extend or to retract the cylinder using the given information. Pressure Piston Dia. Rod Dia. Force i. P1 = 1800 1 1/2” 3180.87 lbs (3.81 cm) (1442.82 kg) 2178.15 j. P2 = 1 1/2” 5/8” 3180.87 lbs (3.81 cm) (1.58cm) (1442.82 kg) 5890.5 k. P1 = 1200 psi 2 1/2” (84.37 bar) (6.35 cm) 3004.16 l. P2 = 1200 psi 2 1/2” 1 3/4” (84.37 bar) (6.35 cm) (4.45cm) m. P1 = 884.19 6.0” 25000 lbs (15.24 cm) (11339.81 kg) n. P2 = 1178.9 6.0” 3” 25000 lbs 2 (15.24 cm) (7.62 cm) (11339.81 kg) o. P1 = 575 psi 8.0 28902.72 lbs (40.43 bar) (13110.05 kg) p. P2 = 575 psi 8.0” 5.5 15241.67 lbs (40.43 bar) (20.32 cm) (6913.51 kg) Ret. Code RA Printed copies of this document are uncontrolled Copyright © 2012 Michelin North America. All rights reserved. No part of this material may be reproduced or distributed in any form or by any means, or stored in any data base or retrieval system, without the prior written permission from Michelin 800 E. Faris Rd Greenville, SC 29607 MICHELIN NORTH PAGE 13 OF 24 AMERICA TITLE: Hydraulic Systems Edition Date: 2022 Entity: NA/TTG Author: Juan Cano Validator: Bruce Dennis Classification: D3 Pressure / Flow Ret. Code RA Printed copies of this document are uncontrolled Copyright © 2012 Michelin North America. All rights reserved. No part of this material may be reproduced or distributed in any form or by any means, or stored in any data base or retrieval system, without the prior written permission from Michelin 800 E. Faris Rd Greenville, SC 29607 MICHELIN NORTH PAGE 14 OF 24 AMERICA TITLE: Hydraulic Systems Edition Date: 2022 Entity: NA/TTG Author: Juan Cano Validator: Bruce Dennis Classification: D3 The Relationship between Pressure and Flow in a System Flow Flow in a hydraulic system is created by the pump. Flow and pressure are the kinetic energy that allow a system to perform work. Flow from the pump, or system, is essential to cause movement of any actuator. There are two ways to measure the flow of a fluid; velocity and / or flow rate. Velocity Velocity is the average speed of the fluid passing a point or the average distance it travels per unit of time. It is usually measured in feet per second (ft/sec), feet per minute (ft/min), inches per second (in/sec), meters per second (m/sec), meters per minute (m/min), centimeters per second (cm/sec). Flow Rate Flow rate is a measure of the volume of fluid passing a point in a given time. It is usually measured in gallons per minute (gpm) or liters per minute (lpm). The actual speed of any actuator is dependent upon two factors; size of the actuator and the rate of flow (Volume) into it. When relating to flow in a hydraulic system there are two fundamental principles; 1) “Flow makes it go”. For anything to move in a hydraulic system the actuator must be supplied with fluid. 2) Rate of flow determines actuator speed. Changes in pump, or system, output flow will change the speed of the actuator. Actuator speed will always be directly related to “how much you put into or how much you let out of the actuator.” Pressure Pressure in a hydraulic system is directly related to the degree or amount of resistance to flow. Pressure gives the actuator it’s force, remember P/F/A relationships. The pump is producing flow, not pressure. To help illustrate this point; Ret. Code RA Printed copies of this document are uncontrolled Copyright © 2012 Michelin North America. All rights reserved. No part of this material may be reproduced or distributed in any form or by any means, or stored in any data base or retrieval system, without the prior written permission from Michelin 800 E. Faris Rd Greenville, SC 29607 MICHELIN NORTH PAGE 15 OF 24 AMERICA TITLE: Hydraulic Systems Edition Date: 2022 Entity: NA/TTG Author: Juan Cano Validator: Bruce Dennis Classification: D3 In this illustration pump flow is allowed to return back to tank/reservoir unrestricted. The amount of pressure created to push the fluid through the system is very low. In this illustration pump flow is returning back to tank/reservoir but it encounters a restriction. The amount of pressure created is directly related to the degree of restriction. The pump has to create more pressure than before because of the extra resistance to flow in the system. In this illustration pump flow is not allowed to return back to tank/reservoir but is completely blocked. Because of the blockage in the line system pressure will continue to rise as the pump continues to add fluid to the system. Pressure will continue to rise until it the system or a component fails. All resistance to flow in a system creates pressure; including, transmission lines, components and fluid changing direction (such as elbows) are accumulative and contribute to total system pressure. In summary; pressure relates directly to the force generated by an actuator, whereas flow rate relates directly to the speed an actuator operates at. Ret. Code RA Printed copies of this document are uncontrolled Copyright © 2012 Michelin North America. All rights reserved. No part of this material may be reproduced or distributed in any form or by any means, or stored in any data base or retrieval system, without the prior written permission from Michelin 800 E. Faris Rd Greenville, SC 29607 MICHELIN NORTH PAGE 16 OF 24 AMERICA TITLE: Hydraulic Systems Edition Date: 2022 Entity: NA/TTG Author: Juan Cano Validator: Bruce Dennis Classification: D3 Fluid Flow Paths An inherent characteristic of a liquid is their ability to always take the path of least resistance. Parallel Flow Paths When two or more pathways exist the factor that determines the fluids flow path will be the degree of resistance. In the illustration below the fluid has three different flow paths. Parallel Flow Paths Ret. Code RA Printed copies of this document are uncontrolled Copyright © 2012 Michelin North America. All rights reserved. No part of this material may be reproduced or distributed in any form or by any means, or stored in any data base or retrieval system, without the prior written permission from Michelin 800 E. Faris Rd Greenville, SC 29607 MICHELIN NORTH PAGE 17 OF 24 AMERICA TITLE: Hydraulic Systems Edition Date: 2022 Entity: NA/TTG Author: Juan Cano Validator: Bruce Dennis Classification: D3 Series Flow Path When the circuit components are connected in series the resistance to flow/pressures add up. In the illustration below the valves are connected in series. Pressure gauges are placed through- out the circuit to show the different pressure values within the different sections. The pressure gauges will show the pressure required to open each valve, plus the back pressure generated from the valves downstream. The pressure at the pump would be the total pressure required to open all the valves and create flow. Series Flow Path Ret. Code RA Printed copies of this document are uncontrolled Copyright © 2012 Michelin North America. All rights reserved. No part of this material may be reproduced or distributed in any form or by any means, or stored in any data base or retrieval system, without the prior written permission from Michelin 800 E. Faris Rd Greenville, SC 29607 MICHELIN NORTH PAGE 18 OF 24 AMERICA TITLE: Hydraulic Systems Edition Date: 2022 Entity: NA/TTG Author: Juan Cano Validator: Bruce Dennis Classification: D3 This page intentionally left blank. Ret. Code RA Printed copies of this document are uncontrolled Copyright © 2012 Michelin North America. All rights reserved. No part of this material may be reproduced or distributed in any form or by any means, or stored in any data base or retrieval system, without the prior written permission from Michelin 800 E. Faris Rd Greenville, SC 29607 MICHELIN NORTH PAGE 19 OF 24 AMERICA TITLE: Hydraulic Systems Edition Date: 2022 Entity: NA/TTG Author: Juan Cano Validator: Bruce Dennis Classification: D3 Viscosity / Temperature Ret. Code RA Printed copies of this document are uncontrolled Copyright © 2012 Michelin North America. All rights reserved. No part of this material may be reproduced or distributed in any form or by any means, or stored in any data base or retrieval system, without the prior written permission from Michelin 800 E. Faris Rd Greenville, SC 29607 MICHELIN NORTH PAGE 20 OF 24 AMERICA TITLE: Hydraulic Systems Edition Date: 2022 Entity: NA/TTG Author: Juan Cano Validator: Bruce Dennis Classification: D3 Petroleum Based Hydraulic Fluids The most common type of oil used in an industrial hydraulic system will be a petroleum based fluid. A petroleum based hydraulic fluid has many primary functions it may perform in the system; Acts as a means of energy transmission Cools the system by removing heat Seals clearances between components Lubricates moving components Reduces friction A petroleum based hydraulic fluid has many other secondary or quality type functions it may perform in the system; Cleans the system by washing away contamination Prevent rust, corrosion, pitting Prevent sludge, gumming, varnishing Reduce foaming Maintain stability over wide temperature ranges Separate water Be compatible with seals and gaskets Ret. Code RA Printed copies of this document are uncontrolled Copyright © 2012 Michelin North America. All rights reserved. No part of this material may be reproduced or distributed in any form or by any means, or stored in any data base or retrieval system, without the prior written permission from Michelin 800 E. Faris Rd Greenville, SC 29607 MICHELIN NORTH PAGE 21 OF 24 AMERICA TITLE: Hydraulic Systems Edition Date: 2022 Entity: NA/TTG Author: Juan Cano Validator: Bruce Dennis Classification: D3 Fluid Properties The various properties of a hydraulic fluid that allow it satisfy its primary and some of the secondary functions; Viscosity Pour Point Lubricating ability Oxidation Resistance Rust & Corrosion Protection Demulsify Viscosity Of all the properties a hydraulic fluid may exhibit viscosity is, in most applications, the most important characteristic. Viscosity is the measure of a fluid’s resistance to flow or ability to flow. If a fluid flows easily, it has a low viscosity or is a thin fluid. If a fluid has difficulty flowing, it has a high viscosity or is a thick fluid. The right viscosity for any application is always a compromise to satisfy the system requirements. Measuring Viscosity Many different methods exist to measure or define viscosity. Some of the most common are; Absolute (Dynamic) viscosity, Kinematic viscosity, Saybolt Universal Seconds and SAE values used for automotive oils. In the United States, hydraulic fluid viscosities are usually specified in Saybolt Universal Seconds or Kinematic viscosity. Saybolt Universal Seconds The Saybolt Universal Second system was created by George M. Saybolt in 1919 and is widely used in the United States. It is a measure of a fluids relative viscosity and uses SUS or SSU as an identifying abbreviation. A Saybolt Viscosimeter, invented by George M. Saybolt, is used to measure a fluids viscosity. The viscosimeter measures, in seconds, how long it takes for 60 ml of liquid to flow out of a restriction from a constant temperature bath. (Reference following picture) Ret. Code RA Printed copies of this document are uncontrolled Copyright © 2012 Michelin North America. All rights reserved. No part of this material may be reproduced or distributed in any form or by any means, or stored in any data base or retrieval system, without the prior written permission from Michelin 800 E. Faris Rd Greenville, SC 29607 MICHELIN NORTH PAGE 22 OF 24 AMERICA TITLE: Hydraulic Systems Edition Date: 2022 Entity: NA/TTG Author: Juan Cano Validator: Bruce Dennis Classification: D3 Kinematic Viscosity The Kinematic Viscosity is the most widely used system worldwide. It is measured by the amount of time needed for a fixed volume of oil to flow through a capillary tube. The coefficient of absolute viscosity, when divided by the density of the liquid is called kinematic viscosity. Kinematic viscosity expresses the total resistance to fluid flow including internal fluid friction plus the effect of mass or weight of the fluid. The official ISO unit is meters squared per second (m²/sec), but the centistoke (cSt) is commonly used in international fluid power industry. A centistokes is millimeters squared per second (mm²/sec). Ret. Code RA Printed copies of this document are uncontrolled Copyright © 2012 Michelin North America. All rights reserved. No part of this material may be reproduced or distributed in any form or by any means, or stored in any data base or retrieval system, without the prior written permission from Michelin 800 E. Faris Rd Greenville, SC 29607 MICHELIN NORTH PAGE 23 OF 24 AMERICA TITLE: Hydraulic Systems Edition Date: 2022 Entity: NA/TTG Author: Juan Cano Validator: Bruce Dennis Classification: D3 Ret. Code RA Printed copies of this document are uncontrolled Copyright © 2012 Michelin North America. All rights reserved. No part of this material may be reproduced or distributed in any form or by any means, or stored in any data base or retrieval system, without the prior written permission from Michelin 800 E. Faris Rd Greenville, SC 29607 MICHELIN NORTH PAGE 24 OF 24 AMERICA TITLE: Hydraulic Systems Edition Date: 2022 Entity: NA/TTG Author: Juan Cano Validator: Bruce Dennis Classification: D3 Factors that affect viscosity Several factors affect a fluids viscosity; listed below are some. Of all the factors that affect a fluids viscosity, temperature may have the most impact. Type of fluid Temperature Pressure Additives Contamination Temperature As with all liquids, hydraulic fluids are made up of molecules which are attracted to one another. The attraction force is not as strong as the molecules of a solid, but stronger than a gas. Heating any liquid will make the molecules travel faster and allow the fluid to flow easier, or have a lower viscosity. While cooling, any liquid will make the molecules travel slower and force the fluid to have more difficulty flowing, or a higher viscosity. In general, as temperature increases the viscosity of a liquid decreases; and as temperature decreases the viscosity of a liquid increases. Not only can temperature have an effect on the fluids viscosity, but it can also affect other parts of the system. Viscosity Index Since the viscosity of a hydraulic fluid is an important factor and viscosity would change in relation to temperature. Any system which would have temperature changes or cannot maintain a constant temperature would need a fluid that could remain relatively stable over a given temperature range. Viscosity index (VI) is a measure of a fluid’s resistance to viscosity change with temperature changes. A fluid with a stable viscosity over extreme temperature changes has a high viscosity index value. A fluid that does not have a stable viscosity over extreme temperature changes has a low viscosity index value. Ret. Code RA Printed copies of this document are uncontrolled Copyright © 2012 Michelin North America. All rights reserved. No part of this material may be reproduced or distributed in any form or by any means, or stored in any data base or retrieval system, without the prior written permission from Michelin 800 E. Faris Rd Greenville, SC 29607 MICHELIN NORTH PAGE 1 OF 22 AMERICA TITLE: Hydraulic Systems Edition Date: 2022 Entity: NA/TTG Author: Juan Cano Validator: Bruce Dennis Classification: D3 Conditioning Ret. Code RA Printed copies of this document are uncontrolled Copyright © 2012 Michelin North America. All rights reserved. No part of this material may be reproduced or distributed in any form or by any means, or stored in any data base or retrieval system, without the prior written permission from Michelin 800 E. Faris Rd Greenville, SC 29607 MICHELIN NORTH PAGE 2 OF 22 AMERICA TITLE: Hydraulic Systems Edition Date: 2022 Entity: NA/TTG Author: Juan Cano Validator: Bruce Dennis Classification: D3 This page intentionally left blank. Ret. Code RA Printed copies of this document are uncontrolled Copyright © 2012 Michelin North America. All rights reserved. No part of this material may be reproduced or distributed in any form or by any means, or stored in any data base or retrieval system, without the prior written permission from Michelin 800 E. Faris Rd Greenville, SC 29607 MICHELIN NORTH PAGE 3 OF 22 AMERICA TITLE: Hydraulic Systems Edition Date: 2022 Entity: NA/TTG Author: Juan Cano Validator: Bruce Dennis Classification: D3 Table of Contents Conditioning......................................................................................................................................... 5 The Effects of Contamination on Hydraulic Equipment................................................. 6 Definition of Contamination........................................................................................ 7 Sources of Contamination............................................................................................ 7 Hydraulic Filters.............................................................................................................. 7 Filter Location/Position in a System............................................................................ 8 Filter Ratings................................................................................................................ 8 Filter Element Ratings.................................................................................................. 9 Filter Efficiency Standards......................................................................................... 10 Beta Ratio................................................................................................................... 10 ISO Cleanliness Code................................................................................................. 12 Filter Bypass Valves................................................................................................... 15 Heat Exchange................................................................................................................................... 17 Hydraulic Reservoir....................................................................................................... 18 Heat Exchanger.............................................................................................................. 19 Heaters........................................................................................................................ 19 Air Cooler................................................................................................................... 19 Water Cooler.............................................................................................................. 20 Heat Exchangers in a Circuit...................................................................................... 21 Ret. Code RA Printed copies of this document are uncontrolled Copyright © 2012 Michelin North America. All rights reserved. No part of this material may be reproduced or distributed in any form or by any means, or stored in any data base or retrieval system, without the prior written permission from Michelin 800 E. Faris Rd Greenville, SC 29607 MICHELIN NORTH PAGE 4 OF 22 AMERICA TITLE: Hydraulic Systems Edition Date: 2022 Entity: NA/TTG Author: Juan Cano Validator: Bruce Dennis Classification: D3 This page intentionally left blank. Ret. Code RA Printed copies of this document are uncontrolled Copyright © 2012 Michelin North America. All rights reserved. No part of this material may be reproduced or distributed in any form or by any means, or stored in any data base or retrieval system, without the prior written permission from Michelin 800 E. Faris Rd Greenville, SC 29607 MICHELIN NORTH PAGE 5 OF 22 AMERICA TITLE: Hydraulic Systems Edition Date: 2022 Entity: NA/TTG Author: Juan Cano Validator: Bruce Dennis Classification: D3 Conditioning Ret. Code RA Printed copies of this document are uncontrolled Copyright © 2012 Michelin North America. All rights reserved. No part of this material may be reproduced or distributed in any form or by any means, or stored in any data base or retrieval system, without the prior written permission from Michelin 800 E. Faris Rd Greenville, SC 29607 MICHELIN NORTH PAGE 6 OF 22 AMERICA TITLE: Hydraulic Systems Edition Date: 2022 Entity: NA/TTG Author: Juan Cano Validator: Bruce Dennis Classification: D3 The Effects of Contamination on Hydraulic Equipment Several factors are considered when dealing with contamination in hydraulic equipment. There are four primary functions of a hydraulic fluid; transmit power, cool or dissipate heat, lubricate moving parts and seal clearances between parts. Contamination can interfere or diminish the fluids ability to perform these functions. Dirt interferes with the transmission of energy by blocking/plugging small orifices in hydraulic components; such as pressure controls, flow controls, pressure compensating pumps or any other component that depends on small orifices for control. Even air in the fluid can lead to damage from cavitation, reduced lubricity or erratic operation of components. The components then become non-productive, unpredictable and unsafe. A hydraulic fluid’s viscosity, system friction and changing fluid direction all generate heat during system operation. Dirty fluid interferes with the fluids ability to absorb heat from the system and a dirty reservoir will not allow the heat to dissipate from the fluid to the surrounding environment. Clean hydraulic systems run cooler than dirty systems. The most serious effect that contamination can have on a system is when it interferes with the fluids ability to lubricate internal, moving parts. When lubricity is reduced or compromised excessive wear, slow response, erratic operation and premature component failure will be the result. Ret. Code RA Printed copies of this document are uncontrolled Copyright © 2012 Michelin North America. All rights reserved. No part of this material may be reproduced or distributed in any form or by any means, or stored in any data base or retrieval system, without the prior written permission from Michelin 800 E. Faris Rd Greenville, SC 29607 MICHELIN NORTH PAGE 7 OF 22 AMERICA TITLE: Hydraulic Systems Edition Date: 2022 Entity: NA/TTG Author: Juan Cano Validator: Bruce Dennis Classification: D3 Definition of Contamination A contaminant is any foreign material that has a detrimental effect on the fluid’s performance in the system. Contamination may exist as a gas, liquid or solid state in a system. A gas can either be in a dissolved state or entrained in the fluid as bubbles. A liquid, depending on its compatibility with the oil, can be in a free state or can be in a dissolved (emulsified) state. A solid, also may be known as particulate matter, can be characterized with it’s density, hardness, ability to settle, ability to compact, ability to be transported, size, shape and concentration. Sources of Contamination Contamination has several ways to enter a hydraulic system; Built-in to the system Added to the system Generated within the system Hydraulic Filters All hydraulic fluids contain dirt to some degree and a large majority of component and system malfunctions are caused by particles of dirt. The need for a filter to reduce or remove contaminants is essential for system performance and dependability. Filter, Filter w/By-pass check valve IN OUT There may be two different types of filtration devices located in a system; filters or strainers. A filter is a device whose primary function is to trap, by some type of porous medium, contaminants from the fluid. A strainer is simply a very coarse filter. Each will usually have a different purpose in a system which usually will dictate a different position for each in the system. To put it in simple terms, whether it is a filter or strainer, their function is to trap contaminants. Ret. Code RA Printed copies of this document are uncontrolled Copyright © 2012 Michelin North America. All rights reserved. No part of this material may be reproduced or distributed in any form or by any means, or stored in any data base or retrieval system, without the prior written permission from Michelin 800 E. Faris Rd Greenville, SC 29607 MICHELIN NORTH PAGE 8 OF 22 AMERICA TITLE: Hydraulic Systems Edition Date: 2022 Entity: NA/TTG Author: Juan Cano Validator: Bruce Dennis Classification: D3 Filter Location/Position in a System There are four typical areas for locating a contamination control component; inlet line (inlet strainer or suction filter), pressure line and return line. Cylinder Cylinder Pressure Return Line Filter Line Filter A B DCV pcv P T prime mover pump Return Pressure Line Filter Line Filter Inlet/Suction Line Filter PCV Pressure Gauge Prime M Pump Inlet Mover Strainer Inlet/Suction Line Filter Inlet Strainer Ideally each component should be equipped with its own filter, but this is usually impractical. To obtain the best results a balanced/strategic approach is used to locate the filters for necessary protection and maximum system efficiency. Filter Ratings Filter manufacturers commonly provide users with ratings/values that define the proper filter for any application. Flow ratings, in gpm or LPM, are used to size the filter properly for the required flow in the system. Pressure ratings are used to size the filter for the maximum pressure value experienced in the system. The filter element (medium) also receives rating to define the filters actual/approximate contamination removal ability or efficiency to provide adequate protection. Ret. Code RA Printed copies of this document are uncontrolled Copyright © 2012 Michelin North America. All rights reserved. No part of this material may be reproduced or distributed in any form or by any means, or stored in any data base or retrieval system, without the prior written permission from Michelin 800 E. Faris Rd Greenville, SC 29607 MICHELIN NORTH PAGE 9 OF 22 AMERICA TITLE: Hydraulic Systems Edition Date: 2022 Entity: NA/TTG Author: Juan Cano Validator: Bruce Dennis Classification: D3 Filter Element Ratings The function of the filter element is to remove contamination/dirt from the fluid. Depending on the location/position in the system, which determines purpose, there are two different numbers; a mesh number and a micron value. A screen or strainer will use a mesh rating/number or a standard sieve number. The higher the mesh or sieve number the finer the screen/strainer, the lower the mesh or sieve number the more course the screen/strainer. A filter will use a micron rating/number. The micron is referring to the measurable value in the metric system of the micrometre. One micrometre, one micron, is equal to one millionth of a meter or thirty-nine millionths of an inch. The micron rating/number refers to the hole/pore size created by the particular element material. When a filter is specified with a micron rating/number, it usually refers to one of two different element/media rating systems, the nominal or absolute rating system. The filter element/media will be given a nominal rating if the material does not have consistent hole or pore size, thus the nominal rating is based on an average hole/pore size. The filter element/media will be given an absolute rating if the material does have consistent hole or pore size, thus the absolute rating is based on the absolute largest hole/pore size. Ret. Code RA Printed copies of this document are uncontrolled Copyright © 2012 Michelin North America. All rights reserved. No part of this material may be reproduced or distributed in any form or by any means, or stored in any data base or retrieval system, without the prior written permission from Michelin 800 E. Faris Rd Greenville, SC 29607 MICHELIN NORTH PAGE 10 OF 22 AMERICA TITLE: Hydraulic Systems Edition Date: 2022 Entity: NA/TTG Author: Juan Cano Validator: Bruce Dennis Classification: D3 Filter Efficiency Standards Filters are made of a lot of different materials, such as Cellulose Media, Synthetic fibers, Wire-mesh, etc. All filters (surface or depth) are going to let some contaminant particles to go through them. The terms, absolute and nominal, have no standard definition regarding to filter performance and can vary from one manufacturer to another. Because of this, the filter performance should not be evaluated based on such ratings. To truly evaluate the performance of filters, the capture efficiency, at a given particle size, must be obtained. Modern filters are engineered to meet the specific requirements of equipment manufacturers and are required to have exacting efficiency ratings. Hydraulic filters are rated according to the size of the particles they remove and the efficiency with which they remove them. Filter efficiency can be expressed either as a beta ratio for a given particle size or as a percentage of particles captured. Beta Ratio Until recently there has not been any universally accepted test method to measure or describe the media pore size or the size of particles a filter media can capture and hold. A test procedure called multi-pass testing or Beta ratio testing is a universally accepted test method that yields readily comparable test results. It was introduced with the object of giving both filter manufacturer and user an accurate and representative comparison amongst filter media. Multi-pass testing uses a specified contaminate, of known sizes, added regularly in measured quantities to the fluid which is pumped continuously through the filter. Measured samples of the fluid are then taken at timed intervals from both the downstream and the upstream of the filter simultaneously, particles are measured and counted by electronic means using automatic particles counters. Beta ratio is the number of particles, at the given size, that enter the filter divided by the number of particles that pass through the filter. The bellow picture shows an example of a filter with a 50 Beta ratio Ret. Code RA Printed copies of this document are uncontrolled Copyright © 2012 Michelin North America. All rights reserved. No part of this material may be reproduced or distributed in any form or by any means, or stored in any data base or retrieval system, without the prior written permission from Michelin 800 E. Faris Rd Greenville, SC 29607 MICHELIN NORTH PAGE 11 OF 22 AMERICA TITLE: Hydraulic Systems Edition Date: 2022 Entity: NA/TTG Author: Juan Cano Validator: Bruce Dennis Classification: D3 2 Particles 100 Particles (40 µm) (40 µm) 100:2 = 100 = 50 2 Therefore, the beta rating of this filter is β40=50 The beta ratio is an indicator of how well a filter controls particulate: i.e., if one out of every two particles in the fluid pass through the filter, the beta ratio is 2, if one out of every 200 of the particles pass through the filter the beta ratio is 200. Therefore, filters with a higher beta ratio retain more particles and have higher efficiency. Efficiency for a given particle size can be derived directly from the beta ratio by the following equation: For the previous filter example β40=50 the efficiency of the filter removing particles of 40µm will be: 50 1 49 % 100% 100% 98% 50 50 To remove confusion, manufacturers should describe the performance of the media used inside a filter by its 'beta ratio'. ISO 16889 (International Standard Organization) lists eight common Beta ratios used to report filter efficiency: Beta 2, 10, 20, 75, 100, 200, 1000 and 2000. Ret. Code RA Printed copies of this document are uncontrolled Copyright © 2012 Michelin North America. All rights reserved. No part of this material may be reproduced or distributed in any form or by any means, or stored in any data base or retrieval system, without the prior written permission from Michelin 800 E. Faris Rd Greenville, SC 29607 MICHELIN NORTH PAGE 12 OF 22 AMERICA TITLE: Hydraulic Systems Edition Date: 2022 Entity: NA/TTG Author: Juan Cano Validator: Bruce Dennis Classification: D3 Filter beta ratios and their corresponding efficiency percentages are shown in the following table. Rating Efficiency 2 50.0% 10 90.0% 75 98.7% 100 99.0% 200 99.5% 1000 99.9% Even poor-quality filters can trap some level of 5 micron particles, but the Beta Ratio will be in the 2-10 range, which is not acceptable. Most experts agree a Beta Ratio for a given particle size should be at least 75 to achieve a reasonable level of effectiveness. High quality, efficient filter assemblies can achieve 200 to 2000 Beta Ratio for a given particle size. ISO Cleanliness Code Since filters are not 100% efficient, they can let pass some small particles that could not represent a big problem for some hydraulic components, but too many of these small particles could carry catastrophic failures due to sludge buildup and/or varnishing. While filter manufacturers publish beta ratings for filter media to describe efficiency performance levels, the ISO cleanliness code determine how clean the fluid is, because of this a direct connection between the beta rating scale and the ISO rating scale cannot be made. The International Standards Organization standard ISO 4406 is the preferred method of quoting the number of solid contaminant particles in a sample. The code is constructed from the combination of three scale numbers selected from the following table. Ret. Code RA Printed copies of this document are uncontrolled Copyright © 2012 Michelin North America. All rights reserved. No part of this material may be reproduced or distributed in any form or by any means, or stored in any data base or retrieval system, without the prior written permission from Michelin 800 E. Faris Rd Greenville, SC 29607 MICHELIN NORTH PAGE 13 OF 22 AMERICA TITLE: Hydraulic Systems Edition Date: 2022 Entity: NA/TTG Author: Juan Cano Validator: Bruce Dennis Classification: D3 ISO Cleanliness Code 4406 for Hydraulic Fluid Contamination ISO code Number of particles per ml number More than Up to and including 22 20,000 40,000 21 10,000 20,000 20 5,000 10,000 19 2,500 5,000 18 1,300 2,500 17 640 1,300 16 320 640 15 160 320 14 80 160 13 40 80 12 20 40 11 10 20 10 5 10 09 2.5 5 08 1.3 2.5 07 0.64 1.3 ISO Cleanliness Level Particle/Milliliter ISO Code ≥ 4µm ≥ 6µm ≥ 14µm 23/21/18 80,000 20,000 2,500 22/20/18 40,000 10,000 2,500 22/20/17 40,000 10,000 1,300 22/20/16 40,000 10,000 640 20/18/15 10,000 2,500 320 19/17/14 5,000 1,300 160 18/16/13 2,500 640 80 17/15/12 1,300 320 40 16/14/12 640 160 40 16/14/11 640 160 20 15/13/10 320 80 10 14/12/9 160 40 5 13/11/8 80 20 2.5 12/10/8 40 10 2.5 12/10/7 40 10 1.3 12/10/6 40 10 0.64 Note: The old ISO standard utilized 2μm, 5μm and 15μm instead. Ret. Code RA Printed copies of this document are uncontrolled Copyright © 2012 Michelin North America. All rights reserved. No part of this material may be reproduced or distributed in any form or by any means, or stored in any data base or retrieval system, without the prior written permission from Michelin 800 E. Faris Rd Greenville, SC 29607 MICHELIN NORTH PAGE 14 OF 22 AMERICA TITLE: Hydraulic Systems Edition Date: 2022 Entity: NA/TTG Author: Juan Cano Validator: Bruce Dennis Classification: D3 The following charts shows the suggested acceptable contamination codes for the most industrial hydraulic components and cross reference between the ISO and SAE Standards. ISO code numbers Typical components Sensitivity Flow control valves 20 / 18 / 15 Average Cylinders 19 / 17 / 14 Gear pumps/motors Important High pressure vane and 18 / 16 / 13 Critical piston pumps/ motors Directional and pressure 18 / 16 / 13 Critical control valves 17 / 15 / 12 Proportional valves Critical 16 / 14 / 11 Industrial servovalves Critical NOTE: The three figures of the ISO code numbers represent ISO level contamination grades for particles of >4μm, >6μm and >14μm respectively. ISO 4406 SAE 749 14 / 12 / 09 0 15 / 13 / 10 1 16 / 14 / 11 2 17 / 15 / 12 3 18 / 16 / 13 4 19 / 17 / 14 5 20 / 18 / 15 6 NOTE: The comparisons relate to particle count data only. To conform to any particular standard, reference should be made to the recommended experimental procedure. Ret. Code RA Printed copies of this document are uncontrolled Copyright © 2012 Michelin North America. All rights reserved. No part of this material may be reproduced or distributed in any form or by any means, or stored in any data base or retrieval system, without the prior written permission from Michelin 800 E. Faris Rd Greenville, SC 29607 MICHELIN NORTH PAGE 15 OF 22 AMERICA TITLE: Hydraulic Systems Edition Date: 2022 Entity: NA/TTG Author: Juan Cano Validator: Bruce Dennis Classification: D3 Filter Bypass Valves Most, if not all, hydraulic filters have a bypass valve incorporated into the assembly to eliminate the possibility of element collapse or rupture when the element becomes clogged or when the fluid is very viscous. A bypass valve is basically a fail-safe device. As the filter element fills with dirt, the pressure required to flow through the element increases. When the pressure across the filter element is large enough to unseat the bypass valve and bypass the filter element completely. The bypass feature allows the fluid to bypass, instead of pushing the contamination through the filter element and re-entering the system or breaking down the element with higher than normal pressure which would destroy the element eventually. Although fluid should never be allowed to bypass the filter it does protect the filter and system components from excessive pressure. The whole key to filter maintenance/performance revolves around cleaning or replacing the filter when needed. That’s why most filters come equipped with filter bypass indicators to alert maintenance to a bypass situation. Bypass check valve Inlet Outlet Ret. Code RA Printed copies of this document are uncontrolled Copyright © 2012 Michelin North America. All rights reserved. No part of this material may be reproduced or distributed in any form or by any means, or stored in any data base or retrieval system, without the prior written permission from Michelin 800 E. Faris Rd Greenville, SC 29607 MICHELIN NORTH PAGE 16 OF 22 AMERICA TITLE: Hydraulic Systems Edition Date: 2022 Entity: NA/TTG Author: Juan Cano Validator: Bruce Dennis Classification: D3 This page intentionally left blank. Ret. Code RA Printed copies of this document are uncontrolled Copyright © 2012 Michelin North America. All rights reserved. No part of this material may be reproduced or distributed in any form or by any means, or stored in any data base or retrieval system, without the prior written permission from Michelin 800 E. Faris Rd Greenville, SC 29607 MICHELIN NORTH PAGE 17 OF 22 AMERICA TITLE: Hydraulic Systems Edition Date: 2022 Entity: NA/TTG Author: Juan Cano Validator: Bruce Dennis Classification: D3 Heat Exchange. Ret. Code RA Printed copies of this document are uncontrolled Copyright © 2012 Michelin North America. All rights reserved. No part of this material may be reproduced or distributed in any form or by any means, or stored in any data base or retrieval system, without the prior written permission from Michelin 800 E. Faris Rd Greenville, SC 29607 MICHELIN NORTH PAGE 18 OF 22 AMERICA TITLE: Hydraulic Systems Edition Date: 2022 Entity: NA/TTG Author: Juan Cano Validator: Bruce Dennis Classification: D3 Hydraulic Reservoirs The hydraulic reservoir has many primary and secondary functions it serves. One function is to provide an opportunity for the fluid to transfer system heat from the fluid to the environment. By transferring heat through the reservoir walls it acts as a heat exchanger. Even-though the reservoir can be effective in removing heat from the system, sometimes it is incapable of removing all the heat. If this is the case, then a heat exchanger may be incorporated. Ret. Code RA Printed copies of this document are uncontrolled Copyright © 2012 Michelin North America. All rights reserved. No part of this material may be reproduced or distributed in any form or by any means, or stored in any data base or retrieval system, without the prior written permission from Michelin 800 E. Faris Rd Greenville, SC 29607 MICHELIN NORTH PAGE 19 OF 22 AMERICA TITLE: Hydraulic Systems Edition Date: 2022 Entity: NA/TTG Author: Juan Cano Validator: Bruce Dennis Classification: D3 Heat Exchanger Even well designed hydraulic systems can be expected to turn some part of it’s energy/power into heat, which contributes to the system inefficiency. Since no system is 100 percent efficient, heat is a major problem. When the fluid must be temperature conditioned, we typically think of cooling. In fact heat exchangers are commonly called coolers, because of their more frequent application – cooling the fluid. However there are some applications that require the fluid to be heated. The three types of heat exchangers are; heaters, air coolers and water coolers. Heaters A heater is installed in the reservoir, below the fluid level, and usually close to the pump inlet or pick-up line. Operates much like a heating coil or element in a household type water heater. Air Cooler An air cooler is typically used when cooling with water isn’t practical or water isn’t available. The hydraulic fluid is pumped through the tubes of the cooler and transfers the heat to the tubes/fins. Aluminum is frequently used as the basic material for the tubes because of aluminum’s ability to absorb/transfer heat quickly. Then a fan or blower is used to move air across the tubes/fins to increase the heat transfer rate to the outside air. The operation is the same as an automobile radiator. An air cooler isn’t a true heat exchanger since it cools the fluid and usually doesn’t heat the fluid. Generally it isn’t practical to add heat to the fluid in this manner. Air coolers tend to be less efficient than water coolers and are ineffective in areas where a high ambient air temperature exists. Ret. Code RA Printed copies of this document are uncontrolled Copyright © 2012 Michelin North America. All rights reserved. No part of this material may be reproduced or distributed in any form or by any means, or stored in any data base or retrieval system, without the prior written permission from Michelin 800 E. Faris Rd Greenville, SC 29607 MICHELIN NORTH PAGE 20 OF 22 AMERICA TITLE: Hydraulic Systems Edition Date: 2022 Entity: NA/TTG Author: Juan Cano Validator: Bruce Dennis Classification: D3 Water Cooler A water cooler is a true heat exchanger since it has the ability to cool or heat the fluid. The hydraulic fluid is pumped through the housing of the exchanger and heat is transferred to the tubes/fins. The heat is removed by the cooling water circulating through the tubes/fins. This type can be more efficient because the cooling water can be much colder than air used as a cooling medium. This type is also known as a shell and tube type heat exchanger. Oil