Döküm Yöntemleri (Casting Methods) PDF
Document Details
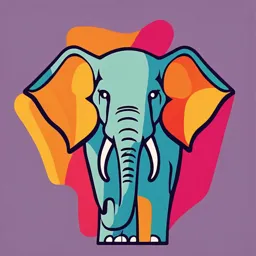
Uploaded by GodlikeRhodonite4589
Tags
Summary
This document discusses döküm yöntemleri, which translates to casting methods. It appears to detail different techniques or processes related to manufacturing or engineering.
Full Transcript
DÖKÜM YÖNTEMLERİ 1 DÖKÜM (CASTING) Ergimiş metalin kumdan, metalden, seramikten veya mumdan hazırlanmış bir kalıp içindeki boşluğa yerçekimi ivmesinden faydalanarak yada basınç etkisi ile doldurulması işlemidir. Döküm işlemi temelde dört alt basamağa sahiptir. ❑ Kalıp...
DÖKÜM YÖNTEMLERİ 1 DÖKÜM (CASTING) Ergimiş metalin kumdan, metalden, seramikten veya mumdan hazırlanmış bir kalıp içindeki boşluğa yerçekimi ivmesinden faydalanarak yada basınç etkisi ile doldurulması işlemidir. Döküm işlemi temelde dört alt basamağa sahiptir. ❑ Kalıp hazırlama ❑ Metal ergitme ❑ Erimiş metalin kalıba dökülmesi ❑ Katılaşma 2 Döküm Kum, ürününün metal, Alaşımın Ergimiş Yerçekimi malzemesine Kalıp seramik, Metalin türüne göre metalin ivmesi Katılaşma ve şekline hazırlama ergitilmesi kalıba bağlı olarak Ürün Nihai ürün alçı, elektrik, ark (gravite), dökülmesi basınç, belirli bir mum ocakları soğuma hızı ile katılaşma 3 Döküm ürünü iki grupta değerlendirilir; ❖İngot ❖Belirli geometride neredeyse bitmiş ürün (nihai ürün) ❖ İngot Daha sonra dövme, haddeleme vb. plastik şekillendirme işlemleri ile son şekillendirmenin yapılacağı işlemlerin ham malzemesi. Basit geometrik şekildedir. Genellikle dikdörtgenler prizması şeklindedir. ❖Nihai Ürün Dizayn mühendisinin tasarım aşamasında döküme ait katılaşma sonrası ölçüsel değişiklikleri de dikkate alarak belirlediği şekle sahip ürün. 4 Döküm Yöntemlerinin Avantajları ❑ Karmaşık şekilli ve içi boş parçaların üretimi için uygundur ❑ Bazı geometrik şekiller için nihai ürün üretimi için uygundur ❑ Ağırlık ve ölçü olarak talaşlı işlenmesi zor ürünler döküm yöntemi ile üretilebilir ❑ Eritilebilen tüm metaller için uygundur ❑ Çok küçük ve karmaşık parçalar için bazı döküm yöntemleri en uygun üretim yöntemidir. 5 METALLERİN DÖKÜMÜ 6 Kalıplama Yöntemine Göre; A. Bozulabilir kalıba döküm B. Kalıcı kalıba döküm 1. Kum kalıba döküm 1. Metal kalıba (kokil) döküm 2. Seramik kalıba döküm 2. Basınçlı Döküm 3. Alçı kalıba döküm 3. Savurma Döküm 4. Hassas döküm 5. Kabuk kalıba döküm 7 Dökümcülükte Kullanılan Temel Terimler ▪ Derece ▪ Model ▪ Yolluk sistemi ▪ Besleyici ▪ Gidici ▪ Maça ▪ Yaş kum ▪ Kuru kum ▪ Meydan kumu ▪ Pota ▪ Kum bileşenleri (kil, kum, su) 8 1. KUM KALIBA DÖKÜM 9 10 11 12 13 14 15 16 En eski geleneksel kalıplama yöntemlerinden biri olan ve ismini kalıplama materyalinden alan döküm yöntemidir. Yöntemi öne çıkaran faktörler başlıca; ❑ Ağırlıkça ve hacimce büyük döküm ürününü üretmek için tek yöntem olması ❑Ergime derecesine bakılmaksızın neredeyse her metalin dökülebiliyor olması (özellikle Ti alaşımları, çelik alaşımları, Ni alaşımları) 17 Kum kalıba döküm yöntemi dört temel aşamada gerçekleşir; ❑ Kum kalıplama ❑ Sıvı metalin kalıp boşluğuna dökülmesi ❑ Katılaşma süresi boyunca bekletme ❑ Kum kalıbın bozularak döküm ürününün çıkarılması 18 1. KALIP KUMLARI Dökümlerin büyük bir kısmı kum Kum kalıba dökümde hatasız ve kaliteli üretim kalıpta yapılır. Genel bir ortalama yapmak; olarak 1 ton döküm için 4-5 ton kum Alaşım bileşimine, gereklidir. Bu miktar; Ergitme yöntemine, Dökülen metalin cinsine, Döküm şekline, Parça büyüklüğüne, Katılaşmayı kontrol eden soğuma şekline, Kalıplama tekniğine, Kalıplama tekniğine, bağlıdır. Kalıp malzemesine, bağlıdır. 19 Kalıp malzemesinin esas görevi, döküm boşluğu şeklini meydana getirmek ve bu şekli, sıvı metal dökülüp katılaşana kadar muhafaza edebilmek. Kalıp malzemesi başlıca üç bileşenden meydana gelir; ❑ Gerekli refrakter özelliği sağlayan kum taneleri (Dökümcülükte kullanılan kum, silis kumu (SiO2) veya silisyumun diğer minerallerle yaptığı karışımdır), ❑ Kum içinde doğal olarak bulunan veya sonradan ilave edilen bağlayıcı, ❑ Bağlayıcı etkisi ile kum tanelerinin birbirini tutmasına imkan veren ve dolayısıyla kumu uygun bir kalıp malzemesi haline getiren su, 20 KUM NEDİR? Kum genel olarak 0.05 - 2mm boyutlarındaki mineral tanesidir. Döküm kumlarının büyük çoğunluğu SiO2 bileşimindedir. Bazı hallerde silis taneleri ile birlikte çok az miktarda feldspat, mika, ilmenit (FeO-TiO2), manyetit (Fe3O4), zirkon (Zr – SiO4) veya olivin (Mg -Fe2-TiO2) gibi minerallerde bulunabilir. Silis kumunun kullanılmasının başlıca nedenleri; ❑Kolay bulunuşu, ❑Ucuz oluşu, ❑Sıvı metalin etkilerine karşı koyabilecek yüksek refrakterlik özelliğidir. 21 KALIP KUMU KARIŞIMLARI Dökümhanelerde A. Doğal Kalıp Kumları Bu kumların kil oranı, doğal olarak ihtiva ettikleri kadardır. kullanılan kalıp kumları ❑ Bulundukları şekilde kullanılırlar, ancak istenen başlıca iki gruba ayrılırlar. özelliklerin sağlanması için su ilavesi yapılır. A. Doğal kalıp kumları, ❑ En büyük avantajı, nem miktarını uzun süre saklayabilmesidir. B. Sentetik kalıp kumları, ❑ En büyük dezavantajı ise, özelliklerinin değişken oluşu, istendiği gibi sabit tutulmamasıdır, bu değişikliğin kalıp özelliklerine ve dolayısı ile döküm kalitesine yansıyacağı açıktır. Doğal kalıp kumlarına bazen bentonit ilavesi yapılabilir. Bu tür hazırlanan kumlara yarı sentetik kum adı 22 verilir. B. Sentetik Kalıp Kumları Sentetik olarak adlandırılan kumlar, doğadan çok düşük oranda kil ihtiva eder şekilde çıkarılan kuma veya yıkanmış (bütün doğal kili giderilmiş) kuma bentonit gibi bir bağlayıcı ve su ilavesi ile elde edilen kumlardır. ❑Daha üniform tane boyutu, ❑Daha yüksek refrakterlik özelliği, ❑Daha az su, Sentetik kalıp kumlarının doğal kalıp kumlarına göre başlıca ❑Daha az bağlayıcı ilavesi, avantajları; ❑Çeşitli özelliklerin daha kolay kontrol edilebilmesi, ❑Daha az depolama alanı ❑Daha yüksek geçirgenlik 23 Yüzey ve Meydan Kumları Kalıp yaparken özellikleri aynı kalmak sureti ile iki ayrı kum kullanılır. Bunlar: 1. Yüzey kumu: Bu kum diğer kumla aynı olmakla beraber daha ince elenir. Kalıpçı, işe başlamadan önce meydan kumunu ince bir elekle yeteri kadar eler. Kalıp yapımı esnasında modelin etrafında 1-2 cm kabuk oluşturacak kadar bu kumdan kullanılır. Kalan kısmına dolgu olarak meydan kumu kullanır. Ancak kabuk kalıpçılığında yüzey kumu olarak kabuk kalıp kumu (shell kum) kullanılır. Dolgu olarak da normal meydan kumu kullanılır. 2. Meydan kumu: Kum karıştırma makinesinde karıştırılıp kalıplama sahasına getirilen kumdur. 24 Kumdan Beklenen Özellikler; Diğer özellikler arasında; A. Yaş mukavemet, a) Sıcak mukavemet, B. Geçirgenlik, b) Sinterleşme noktası, C. Kuru mukavemet, c) Deformasyon, D. Nem miktarı, d) Termal stabilite, E. Kil miktarı, e) Akıcılık ve elastikiyet, F. Tane inceliği ve dağılımı, f) Dağılabilme, g) Tekrar kullanılabilme sayısı 25 A) Kalıp Kumu Yaş Mukavemet Özellikleri Yaş mukavemet kalıp kumunun (tempersuyu) ilavesinden hemen sonraki mukavemettir. Bu, kalıbın hazırlanması esnasında ve sıvı metalin döküldüğü anda kalıbın şeklini muhafaza etmesi için gerekli olan mukavemettir. Yaş mukavemeti kontrol eden faktörler: ❑ Tane inceliği. ❑ Tane şekli. ❑ Bağlayıcı cinsi ve miktarı. ❑ Nem miktarı. 26 B) Gaz Geçirgenliği Gaz geçirgenliği kalıp kumunun hava, gaz veya buharın geçişine imkan verme özelliğidir. Kalıp kumuna bu özelliği kazandıran, kum taneleri arasındaki boşluklardır. Kalıp kumunda geçirgenliği kontrol eden başlıca dört faktör ❑ Kum tane inceliği, ❑ Tane şekli, ❑ Kullanılan bağlayıcı cinsi ve miktarı ❑ Nem miktarıdır. 27 C) Kuru Mukavemet Genel olarak kalıp kumunun kuru mukavemeti ile yaş mukavemet aynı faktörler tarafından ve benzer şekilde etkilenirler. Tane inceliği, tane şekli ve nem miktarının etkisi benzerdir. Ancak değişik bağlayıcılar, yaş ve kuru mukavemetleri değişik şekilde etkilerler. Örneğin Ca–bentonitleri, Na– bentonitlerine nazaran daha düşük kuru mukavemet fakat daha yüksek yaş mukavemet sağlarlar. Na–bentonitlerin yüksek kuru ve sıcak mukavemet sağlayan bentonitlerdir. Bentonitlere hububat ve dekstrin ilave edildiğinde, çok yüksek kuru mukavemet değerlerine erişilebilir. 28 D) Tane İnceliği E) Sıcak Mukavemet Kum kalıbın ergitilmiş metalin sıcaklığına eriştiği Belli miktarda bağlayıcı ve nem için andaki mukavemetidir ve sıvı metal katılaşana ince kum, kalın kuma nazaran (İri kadar şeklini koruyabilmesi için gereklidir. Sıcak taneli kum) daha mukavemetli ve mukavemet ile kuru mukavemet hemen hemen daha az geçirgen olacaktır. Tane aynı faktörlerden etkilenir ve sıcak mukavemet inceliği ayrıca, kaliteli bir döküm doğal olarak döküm yapılacak olan ergimiş yüzeyi için önde gelen bir etkendir. metal sıcaklığında yapılan test ile tespit edilir. Tane inceliği, arttıkça bir başka Sıcak mukavemet ile kuru mukavemet, genel deyimle taneler inceldikçe, döküm olarak aynı faktörler tarafından ve benzer yüzeyi daha düzgün olmaktadır. şekilde etkilenirler. 29 F) Dağılabilme Özelliği Dağılabilme özelliği, “katılaşırken büzülen dökümün doğurduğu gerilimlerin etkisi ile kalıbın dağılması” şeklinde tarif edilebilir. Dağılabilme özelliği, sıcak mukavemetten ayrı düşünülemez. Sıcak mukavemet arttıkça dağılabilme özelliğinin azalacağı açıktır. Dökümcülükte ideal olan, kalıp kumunun yüksek sıcak mukavemet ile iyi dağılabilme özelliğini bir arada bulundurmasıdır. Ancak böyle bir şart kolay elde edilemez. Yüksek sıcak mukavemet ve kötü dağılma özelliğinin en belirgin işareti dökümlerdeki sıcak yırtılma olayıdır. 30 G) Akıcılık ve Plastiklik H) Kil Miktarı Kalıp kumunun hem belli ölçüde akıcılığa sahip Kalıp kumuna ilave edilen olması dolayısıyla model etrafındaki şekli bağlayıcının cinsi ve miktarının alabilmesi, hem de bununla zıt olan diğer bir özelliklere olan etkisi, kil özelliğe (plastiklik) sahip olması beklenir. Plastiklik bağlayıcılarla ilgilidir. özelliği, kumun verilen şekli muhafaza edebilme AFS standardına göre kil miktarı, özelliği olarak tanımlanır. Bu iki özellik, kum tane su içindeki süspansiyonda inceliği, tane şekli ile karışımın ihtiva ettiği dakikada 2,54 cm hızla çökmeyen bağlayıcı cins ve miktarına bağlı olarak değişir. taneciklerdir. 31 K) Tane şekli Girintili-çıkıntılı yada karmaşık geometriye sahip kum tanelerinin kalıbın mukavemetinde olumlu etkileri bulunmaktadır. Ancak gaz geçirgenlikleri yuvarlak taneli kumlardan imal edilmiş kalıplara göre daha düşüktür. ✓ Kum yüzey alanı arttığında bağlayıcı Kum tane şekilleri, malzemelerinin (kil, vb. ve su) miktarı artmak a) Yuvarlak, zorundadır. b) Köşeli, ✓ Kumun tane şekli veya geri dönüştürülen maça c) Bileşik, kumu yüzdesinden dolayı yüzey alanında bir d) Yarı köşeli değişim bağlayıcı miktarındaki değişime sebep olur. 32 ❑ Yuvarlak taneler en düşük yüzey alanı - hacim oranına ve birbirine olan temas yüzeyine sahiptir. Bu sebepten yuvarlak taneler arasında boşluk diğer şekillere göre çok fazladır. Bu durum kumun gaz geçirgenlik özelliğini maksimuma taşırken dayanım özelliklerini minimuma düşürür. ❑ Yuvarlak taneli kumlar, düşük yüzey alanlarından dolayı en az bağlayıcı gereksinimi duyarlar. Bu sebepten kalıp kumlarına göre nispeten daha güçlü bağlayıcıların kullanıldığı maçaların üretiminde kullanılırlar. 33 Yarı köşeli kumlar, en çok kullanılan tane şekli sınıfıdır. ✓ Gaz geçirgenlik ve dayanım özellikleri yuvarlak ve köşeli kumların arasında seyreder. ✓ Tercih edilmelerinin sebebi hem dayanım hem de gaz geçirgenlik özelliklerinin kontrol edilebilmesidir. ❑ Döküm kumlarının şekli bileşik taneler hariç karışık olmalıdır. ❑ Döküm kumlarında tane boyutu dağılımının kontrolü tane şeklinin kontrolünden daha önemlidir. Çünkü döküm kumlarının sahip olması gereken özellikleri esas olarak tane boyut dağılımı belirler. ❑ Kum tane boyut ve şekil dağılımında, kumun ince ve kalın kısımlarının miktarı kalıp yoğunluğu ve gözenekliliği kontrol eder. 34 BAĞLAYICILAR Kalıp kumlarında bağlayıcılar iki ana gruba ayrılır. a) İnorganik bağlayıcılar b) Organik bağlayıcılar Kalıp kumlarında en çok kullanılan inorganik bağlayıcılar killerdir. Bunların arasında en çok tercih edilen is bentonitlerdir. 35 a) İnorganik Bağlayıcılar: Kalıp kumlarında en çok kullanılan inorganik bağlayıcılar killerdir. Bunların arasında en çok tercih edilen ise bentonitlerdir. Bentonitler dökümcülük açısından iki gruba ayrılırlar: 1) Na–bentonit 2) Ca–bentoniti Na’lular yeryüzünde daha az bulunan, su ilavesiyle kuru hacminin 5-6 katına şişebilen ve kalıp kumu özelliklerine katkıları açısından daha çok tercih edilenlerdir. 36 b) Organik Bağlayıcılar (Tahıl unları): Hububat, dekstrin vb. bağlayıcılar da, kum özelliklerini değiştirmek amacıyla kullanılır. Hububat bağlayıcılar daha ziyade buğday ve mısır unlarıdır. Mısır unu bağlayıcı, yaş ve kuru mukavemeti biraz arttırır. Buğday unu ise yaş mukavemete etkisi çok olmamakla birlikte kumun dağılabilme özelliğini yükseltmektedir. Dekstrin, hububat bağlayıcılara göre çok daha yüksek kuru mukavemet sağlar, ancak buna karşılık yaş mukavemette bir azalmaya sebep olur. 37 ✓ Tahıl unları; mısır unu, nişasta ve diğer tahıl unlarını içerir. ✓ Tahıl unları ıslatıldığında yapıştırıcı özelliği kazanır ve bağlayıcı etkisine sahip olur. ✓ Unlar kalıbın şekil alma kabiliyetini ve kumun içinde sertleşerek kuru dayanımı arttırır. Fakat kalıbın bozulmasını zorlaştırır. ✓ Fazla miktarlarda kullanımı gaz hatalarına neden olur. 38 Reçine bağlayıcılar kalıplarda bağlayıcı olarak kullanılırlar. Reçine bağlı bir kum pişirildikten sonra çok sert bir yüzeye sahip olur, ancak en büyük dezavantajı, durduğu yerde hızla nem absorblamasıdır; bu sebepten reçine bağlı kalıp veya maçalar pişirildikten hemen sonra kullanılmalıdır. 39 Karbon İçeren İlaveler ✓ Karbon içeren maddeler kalıba atmosfer kontrolü için ilave edilir. ✓ Karbonlu ilave döküm sırasında yanarak döküm parça ile kalıp yüzeyi arasında ince bir gaz film tabakası oluşturur. Oluşan bu gaz film tabakası sıvı metali oksitlere karşı korur. ✓ Karbon, çok ince öğütülmüş kömür ve petrol ürünlerinden (mazot, asfalt vs..) elde edilebilir. ✓ Kalıpta aşırı karbon, yüksek miktarda duman ve pis kokulu bir gaz oluşumuna ve dolayısı ile gaz hatalarına neden olur. Döküm kumuna uygun oranlarda karbon içeren malzeme ilavesi döküm yüzey kalitesini iyileştirir. 40 Selüloz Selüloz kalıp kumuna kum genleşmesini kontrol etmek ve su aralığını genişletmek için ilave edilir. Selüloz genellikle odun talaşı, yerfıstığı kabuğu ve fındık kabuğu şeklinde ilave edilir. ✓ Selüloz sıcak basma dayanımını azaltır ve kalıp bozulmasını kolaylaştırır. ✓ Selüloz yüksek sıcaklıklarda yanarak metal/kalıp ara yüzeyinde karbonlu ilavelere benzer şekilde film tabakası oluşturur ve metalin kalıbı ıslatmasını engeller. ✓ Kalıplama sırasında döküm kumunun akıcılığını arttırır. ✓ Fazla miktarlarda kullanıldığında duman ve yüksek miktarda gaz oluşumuna ve dolayısı ile gaz hatalarına neden olur. İlave olarak eğer kalıp içerisinde kil miktarı çok düşük ise kum inklüzyonları ve kum yalaması gibi hatalara neden olabilir. 41 ❑ Silis tozu sıcak mukavemeti arttırır. ❑ Demir oksit sıcak mukavemeti arttırır. ❑ Fuel oil akışkanlık ve plastiklik özelliğini arttırır. ❑ Mısır unu yaş ve kuru mukavemeti arttırır. ❑ Pulverize kömür döküm sıcaklığında kum tanelerinin çevresinde gaz filmi oluşturarak birbirine kaynaşmasını engeller böylelikle kumun yeniden kullanılabilmesini sağlar. ❑ Odun talaşı yüksek sıcaklıklarda yanarak kumun sıcak mukavemetini düşürür ve ısısal kararlılığını arttırır. ❑ Grafit tozu döküm yüzey kalitesini arttırmak için kullanılır çünkü yüksek yüzey gerilimi sayesinde sıvı metalin ıslatma özelliğini düşürür. ❑ Perlit alumina silikat minerali olan perlit sayesinde yüksek sıcakılık kararlılığı artar. 42 KUM KALIPLAMA 43 KUM KALIPLAMA Dereceler Kalıbın meydana getirilebilmesi için içerisinde kum sıkıştırılan amaca uygun özellikleri taşıyan çerçevelere derece denir. Derecelerin görevleri: Dereceler; ▪ Kalıpların yapılmasını, ▪ Kalıpların taşınmasını, ▪ Parçalara ayrılıp tekrar yerlerine oturtulmasını, ▪ Kalıp kumunun tutulmasını, sağlar. 44 45 Derecelerin Özellikleri Derecelerin, görevlerini yapabilmeleri için bazı özellikleri taşımaları gerekir. Derecelerde olması gereken özellikler; ▪ Sağlamlık Dereceler kendilerine etki eden çeşitli kuvvetler ile esnememeli ve çarpılmamalıdır. Çarpmalara dayanıklı olmalıdır. ▪ Hafiflik Sağlamlığın yanında, derecelerin hafif olması da istenir. ▪ Uygunluk Dereceler birbirlerine uyum sağlamalıdır. Birbiri üzerine oturan yüzeyler düzgün olmalı, mala yüzeyinden parçalara ayrılan kalıp, yerine tam olarak oturabilmelidir. Kalıbın kaliteli olmasında bu faktör etkilidir. 46 Dereceler aşağıdaki şekilde sınıflandırılır: 1. Teknolojik Amaçlarına Göre: Kalıplar genellikle iki parçadan meydana gelir. Ancak kalıplanacak parçanın durumuna göre üç, hatta daha fazla parçalı kalıplar da olabilir. Buna göre dereceler şu isimleri alır: Alt derece: Kalıbın alt parçasını içine alan dereceye bu isim verilir. Üst derece: Kalıbın üst kısmını içine alan derecedir. Orta derece: İkiden fazla kalıp ayırma yüzeyi (mala yüzeyi) olan kalıplarda, alt ve üst dereceler arasında kalan derecelere orta derece (ara derece) denir. 47 2. Kullanma durumlarına göre sınıflandırma: Dereceler kullanma durumlarına göre aşağıdaki gibi sınıflandırılabilirler: Sabit dereceler: Bunlar kalıbın yapımından sonra dökülünceye kadar kalıbı korumaya devam eder. Büyük parçaların kalıplanmasında veya kalıplanması zor parçaların kalıplanmasında sabit dereceler kullanılır. Bu durumda her kalıp için bir sabit derece takımı gereklidir. Çıkma dereceler: Birçok kalıbı, bir dereceden yararlanarak yapabilmek için bu dereceler kullanılır. Bu dereceler, kalıp hazırlanıp döküm alanındaki yerine konduktan sonra bağlantı parçası açılarak kalıptan çıkarılır, yeni bir kalıp yapımı için hazırlanır. Çıkma dereceler; ▪ Düz çıkma dereceler, ▪ Konik çıkma dereceler, 48 3. Biçimlerine göre sınıflandırma: Dereceler, dökülen parçaların ölçü ve şekillerine göre çok değişik biçimlerde yapılır. Bu sınıflandırma da aşağıdaki gibi yapılabilir: Parça biçimine uydurulan dereceler : Kalıplamayı kolaylaştırmak ve işçiliği azaltmak için dökülecek işe uygun, özel olarak hazırlanmış derecelerdir. Boğazlı dereceler : Daha çok demir olmayan metal ve alaşımların döküldüğü atölyelerde kullanılır. Çeşitli şekil ve biçimlerde yapılır. Ortak özelliği, küçük parçaların yatık kalıplanıp dik dökülmelerini sağlamasıdır. 49 Derecelerin Ek Kısımları Derecelerin gövdeleri çeşitli biçim ve boyutlarda çerçeve ve kasalardan meydana gelir. Kalıp bunların içinde kalır. Derecelerin görevlerini yapabilmeleri için pimleri, pimlerin kulakları, el sapları, vinç sapları (mapa) ve bölmeleri (travers) vardır. Bunlara derecelerin ek kısımları denir. Sabit pimler Traversli çelik derecede kulaklar ve vinç sapları Derecenin mapalardan kaldırılması Derece bölmeleri En ve boylarına göre yükseklikleri az olan derecelere bölmeler konur. Bölmeler dereceye sağlamlık kazandırır. Kumun derecelerden düşmesini önler. Kancaların atılmasına yardımcı olur. 50 Yüzey Ayırıcı Maddeler Kalıp ayırma yüzeylerinde kullanılır. Kalıplarda her bir yüzeyin kumlarının diğerine yapışmasını önlemek gerekir. Çünkü kalıbı sıkıştırdıktan sonra tekrar parçalara ayırıp içindeki modelin çıkartılması, gerekli tamiratların yapılması ve yolluk sisteminin uygun şekilde kalıba bağlanması gerekir. Bunun için kalıp yapılırken her bir kalıbın ayırma yüzeyinin mala ile düzleştirilip yüzeylere kalıp ayırıcı maddelerin serpilmesi gerekir. 51 Yüzey ayırıcı maddeler dökümde yanmış kumlar, kuru ince taneli silis kumu, sanayi talk pudrası, kömür tozu, grafit vb. maddelerdir. Bu maddelerin yüzey ayırıcı olarak kullanılabilmesi için; ▪ Sağlığa zararlı olmamaları, ▪ Döküm esnasında yanıcı gaz oluşturmamaları, ▪ Dökülen metal ve alaşımların bileşimini bozmamaları, ▪ Kum içerisinde birikip kumun özelliğini bozmaması, ▪ Ekonomik olması gerekir. 52 Yüzey ve Meydan Kumları Kalıp yaparken özellikleri aynı kalmak sureti ile iki ayrı kum kullanılır. Bunlar: 1.Yüzey kumu: Bu kum diğer kumla aynı olmakla beraber daha ince elenir. Kalıp yapımı esnasında bu kumdan modelin etrafında 1-2 cm kabuk oluşturacak kadar kullanılır. Kalan kısım için dolgu olarak meydan kumu kullanır. Ancak kabuk kalıpçılığında yüzey kumu olarak kabuk kalıp kumu (shell kum) kullanılır. Dolgu olarak da normal meydan kumu kullanılır. 2. Meydan kumu: Kum karıştırma makinesinde karıştırılıp kalıplama sahasına getirilen kumdur. 53 KALIP SIKILIĞI Kalıp ve maçaların yaş hâldeyken belli bir dayanıma sahip olmaları istenir. Kalıpların çok sıkı veya çok sert sıkıştırılması aşağıdaki hatalara neden olur. Kalıp Sıkılığının Az Olmasının Sakıncaları ❑Kalıplanan model, kalıptan çıktıktan sonra kumun kendi ağırlığı ile veya taşıma esnasında kolayca bozulması ❑Sıvı metalin kuma nüfuz etmesi dolayısı ile karıncalı döküm yüzeyinin oluşması 54 ❑Döküm esnasında sıvı metalin basıncı nedeni ile kalıp yüzeylerinin şişmesi dolayısı ile dökülen işlerde ölçü ve şekil bozukluğunun oluşması ❑Sıvı metalin akışı sırasında yolluk sisteminde (kalıbın sıvı metal ile dolmasını sağlayan düşey ve yatay kanallar) veya kalıpta oluşan erozyonun (yüzeyin aşınması), kalıba kum sürüklemesi 55 Kalıp Sıkılığının Çok Olmasının Sakıncaları ❑ Döküm esnasında meydana gelen gazlar kalıptan uzaklaştırılamaz. Dökülmüş işlerde gaz boşlukları oluşur. ❑ Modelin kumdan çıkarılması, özellikle grift (profilli, girintili çıkıntılı, karmaşık) modellerde zorlaşır. ❑ Dökümden sonra soğuma esnasında, bazı döküm parçalarda hacim küçülmesi nedeni ile oluşan basınca çok sıkıştırılmış kalıp kumu elastikiyet göstermeyebilir. Bu durumda parçalarda çatlamalar oluşur. ❑ Döküm esnasında ısıdan dolayı kalıp kumu genleşir. Kalıp sert sıkıştırıldığı için genleşmeyi karşılayamaz. Geniş yüzeyli işlerde kum kalkar ve metal, kumun arasına girer. Dart denilen döküm hataları oluşur. ❑ Dökümden sonra kalıpları bozmak zorlaşır. 56 MODELSİZ ŞEKİL YAPMA 57 MODEL İLE KALIPLAMA Modeller ucuz ve işlemesi kolay olduğu için ağaçtan, özel Modelin Tanımı durumlarda metalden, alçıdan, plastikten, polistren Döküm yolu ile üretilmek (ambalajlarda kullanılan köpük) den vb. gereçlerden istenen çeşitli parçaların yapılır. Modelin hangi gereçten ve ne şekilde yapılacağını çekme, işleme payları, belirleyen faktörler; kalıplama metotları dikkate alınarak ağaç, metal ve plastik ❑ Kaç adet döküleceği gibi gereçlerden yapılmış ❑ Döküm atölyesinin kalıplama düzeni benzerlerine model denir. ❑ Maliyet faktörü ❑ Döküm parçada aranılan özellikler 58 Model Çeşitleri Modeller genellikle aşağıda belirtilen şekillerde yapılabilir. a) Serbest modeller b) Eğreti (Ayrık) modeller c) İki ve daha çok levhalı modeller d) Tek levhalı modeller 59 Çok büyük ölçülerdeki döküm parçaların modellerinin yapımında iskelet veya karkas modeller kullanılır. Bu modellerde, modelin tamamı yapılmayıp ana ölçülere sahip iskelet şeklinde model yapılır. Karkas modeller, döküm parça modelinin bire bir iskeletini meydana getirir. Kalıplamada iskeletlerin arası kum ile doldurularak kalıba yapışmaması için yüzey ayırıcı serpilir. 60 60 Model Konikliği Koniklik, modelin yan yüzeylerine verilen eğimdir. Modele verilecek koniklik, modelin kumdan çıkarılması bakımından oldukça önemlidir. Yan yüzeylerine koniklik verilmemiş modellerin kumdan çıkarılması zordur. Yan yüzeylere verilen model konikliği, modelin durumuna göre değişir. Konikliğin derecesini etkileyen en önemli faktörler, modelin yüzey pürüzlülüğü ve kuma giren derinliğidir. Model konikliğinin az verilmesi durumunda modelin gereğinden fazla takalanması gerekir. Bu da modelin ömrünü kısaltır. 61 YOLLUK Ergiyik metalin kalıp boşluğuna gidişini sağlayan kanalların toplamına yolluk sistemi denir. Yolluk sistemleri, dökülen parçanın biçim ve boyutları ile alaşımın bileşimine göre çeşitli şekillerde olur. Potadan dökülen sıvı metal yolluk sistemini meydana getiren düşey ve yatay kanallardan geçerek kalıp boşluğunu doldurur. 62 63 64 Yolluk Sistemlerinin Bölümlenmesi Bir yolluk dört bölümden meydana gelir. Bu bölümler: Havşa, gidici ve cürufluk. Havşa ve Hazne Havşa sıvı madenin kalıba rahat dökülmesini sağlar. Silindirik olan gidicinin üst kısmı, genellikle kesik koni biçiminde genişletilerek meydana getirilmiştir. Havşanın görevi, potadan dökülen sıvı metalin etrafa sıçramadan dengeli bir şekilde gidiciye akışını sağlamaktır. Genellikle büyük parçaların dökümünde yukarıdaki amaçlar için havşalar büyütülür. Bunlara hazne (havuz) adı verilir. 65 Gidici Havşaya dökülen sıvı madenin cürufluğa ve yatay kanala gidişini sağlayan düşey kanala gidici adı verilir. Genellikle dairesel, bazen dikdörtgen kesitli olur. Topuk Gidicinin altına rastlayan bu oyuk kısma topuk adı verilir. Topuk, gidiciden düşen sıvı metalin yön değiştirirken hızının kesildiği yerdir 66 Cürufluk Mala yüzeyinde bulunan yatay kanallardır. Gidiciden inen sıvı metalin yönünü yataya dönüştürür. Cüruf tutma özelliğinden dolayı cürufluk ismini alır. Cüruflukların görevleri: Sıvı metalin içindeki cüruf ve pislikleri tam olarak tutmalı, Sıvı metalin soğumasına engel olmalı, Metalin katılaşmasında çekmenin etkisini azaltmalı, İnce parçalarda, büyük kesitli uzun cürufluklar; kalın parçalarda kısa cürufluklar kullanılmalıdır. 67 ÇOK MODELLİ KALIPLAMA Salkım Yolluk Sistemi Yolluk sistemi çeşitlerinden biri de salkım yolluk sistemidir. Değişik veya aynı cinsten birçok parça tek gidici ve tek curufluk (yatay kanal) ile dökülebilir. Parçalar ortak cürufluğa bağlanır. Küçük parçaların dökümünde çok iyi sonuçlar veren bu yolluklara salkım yolluklar denir. 68 Avantajları Dezavantajları ❑Dökümde yolluk için harcanan ❑Salkım yollukların kalın parçalara metal miktarı az olur, uygulanması sınırlıdır, ❑Kısa zamanda çok sayıda parça ❑Parçaların düzenli yerleştirilmemesi dökülür, hâlinde, sıvı metalin bütün kalıpları ❑Salkım yolluklarla dökülen kalıplar, doldurmama tehlikesi vardır, az yer tutar, ❑Bazı durumlarda metal sızdırma ❑Zaman, malzeme ve işçilikten tehlikesi vardır. tasarruf edilir, 69 Salkım Yolluk Çeşitleri Salkım yolluk sistemi düşey, tek sıralı ve çok sıralı olmak üzere üçe ayrılır. a) Düşey salkım yolluk Bir gidici etrafına sıralanan parçalar gidiciye bağlanır. Havşadan gidiciye inen metal yükselerek kalıpları doldurur. Kalıplar yatık kalıplanır ancak döküm dik olarak gerçekleştirilir. Düşey salkım yolluklar, aynı zamanda basınçlı döküm sağlar ve bir kaynak yolluk uygulamasıdır. b) Tek sıralı yatay salkım yolluk Bu yöntem, bir dereceye çok sayıda parça koyup tek gidiciden dökmenin basit bir uygulamasıdır. Yatık kalıplanıp yatık dökülür. Bu şekildeki salkım yolluklar, demir olmayan metal ve alaşımların dökümü için çok kullanılır. Yatay salkım yolluk uygulanan kalıpların üst üste konması ile tek gidiciden çok sayıda parçanın dökülmesi sağlanır. Bu şekildeki yolluklara çok sıralı yatay yolluklar denir. 70 71 Yolluk Sisteminin Görevleri 1. Kalıbın tam ve kusursuz dolmasını 7. Kalıp işçiliğini arttırmamak sağlamak 8. Metal kaybını en aza indirmek 2. Cüruf, oksit ve pisliklerin kalıp içine 9. Metalin kalıptan veya maçalardan sürüklenmesini önlemek parça koparmasını ve maçaları 3. Madenin akışında çarpma ve çalkantı yerinden oynatmasını önlemek meydana getirmemek 10.Aşırı ısı kaybına sebep olmamak 4. Sıvı metalin akış hızını ayarlamak 11.Kalıba giriş yerlerinde aşırı sıcak 5. Soğuma ve katılaşmanın dengeli bir kısımlar meydana getirmemektir. şekilde olmasını sağlamak 6. Hava ve diğer gazların kalıp içine sürüklenmesine engel olmak 72 7. Kalıp işçiliğini arttırmamak 8. Metal kaybını en aza indirmek 9. Metalin kalıptan veya maçalardan parça koparmasını ve maçaları yerinden oynatmasını önlemek 10.Aşırı ısı kaybına sebep olmamak 11.Kalıba giriş yerlerinde aşırı sıcak kısımlar meydana getirmemektir. 73 74 Çıkıcılar Döküm sırasında kalıp gazlarının kalıptan çıkmasını sağlamak için açılan kanallara çıkıcı denir. Kalıp gazları; kalıp boşluğundaki hava, kumdaki yanıcı maddeler, su buharı, sıvı metalin oksitlenmesiyle açığa çıkan gazlar ve dökülen metalin kalıba sürüklediği hava karışımıdır. Kalıp, sıvı metalle dolarken kalıp gazları giderek küçülen kalıp boşluğuna sıkışır. Kalıp içinde bir basınç meydana gelir. Bu basınç ve kalıptan çıkamayan gazlar çeşitli döküm hatalarına sebep olabilir. Sıkışan gazlar, kalıp kumunun taneleri arasındaki boşluklardan veya şiş deliklerinden, kalıbı terk ederler. Gaz çıkışı yeterli olmadığında uygun yerlere açılacak çıkıcılardan yararlanılır. Çıkıcının kalıp gazlarını boşaltma görevi yanında şu yararı da vardır: Kalıpta sıvı metalin yükselişi ve kalıbın doluşu, çıkıcılar yardımı ile çok iyi gözlemlenebilir. 75 Çıkıcıların Yerleri Kalıp sıvı metalle dolarken hava ve gazlar kalıp boşluğunun üst kısmında toplanacaktır. Buna göre çıkıcılar bu kısımlara, yani modellerin veya kalıpların en yüksek kısımlarına konur. Düz ve geniş yüzeyli parçalarda çıkıcılar, yolluğun karşı tarafına konur. Sıvı metal, yolluktan çıkıcıya doğru akarak gazları buraya doğru iter. Böylece gazların çıkışı sağlanır. Çıkıcıların Büyüklükleri Dökülen parçanın durumuna, kalıbın yapılışına ve bileşimine ve metalin ergitilişine göre gazlar çok değişik şartlarda oluşur. Bunun için çıkıcı ölçüleri daha çok deney ve tecrübelere bağlıdır. Çıkıcı kesiti küçük olursa sıvı metal erken katılaşarak çıkıcı ağzını tıkar. Çıkıcı görev yapamaz. Parçaya bağlandığı yerde bir gaz boşluğu meydana gelebilir. Ayrıca gaz sıkışması ile sıvı metal çıkıcıdan tehlikeli bir şekilde fışkırabilir. Çıkıcı kesiti büyük olursa parçaya bağlandığı yerde sıcak kısım ortaya çıkar. Katılaşma sırasında burada bir çöküntü boşluğu veya sıcak yırtılma meydana gelebilir. 76 BESLEYiCi Kalıba dökülen metal ve alaşımlar soğuyup katılaşırken hacimleri küçülür. Bunun sonucu olarak çöküntü adı verilen boşluklar meydana gelir. Çöküntüler, hatalı dökümlere sebep olur. Çöküntüsüz döküm parça elde etmek için, kalıbın uygun yerlerine besleyici adı verilen sıvı metal kütleleri bağlanır. Hacim küçülmesinden meydana gelen çöküntüler besleyicilerden gelen sıvı metalle karşılanır. Besleyiciler çok defa çöküntüyü önlemez ancak parça dışına çıkarırlar. Çöküntü besleyicide oluşur. 77 Çöküntünün meydana gelişi Kalıp duvarları havadan daha iletkendir. Soğuma ve katılaşma duvarlardan başlar, katmanlar hâlinde devam eder. Hacim küçülmeleri, henüz sıvı olan üst kısımdan beslenir. Çöküntü boşluğu burada meydana gelir. Buna dış çöküntü denir. Tamamı kapalı kalıpta ise çöküntü en son katılaşan bölge olan merkezde meydana gelir. Buna iç çöküntü adı verilir. 78 Besleyicinin Yerleri Besleyiciler döküm parçanın en son katılaşan kalın yerlerine konur. Kalın yerlerin üzerinde veya yanında olur. Döküm parçanın yanlarına konulan besleyicilerin döküm parça ile olan mesafesi besleyebilecek ölçüde olmalıdır. Bazı değişik kesit ve ölçülerdeki parçalara birden fazla besleyici verilebilir. Besleyici bütün parça, katılaşıncaya kadar sıvı kalmalı ve en son katılaşmalıdır. Dökülen alaşıma ve parçanın biçimine göre besleyiciler, aşağıdaki şekillerde olur. ▪ Açık Besleyiciler: Üst derecenin üstüne kadar açık olur. ▪ Kör Besleyiciler: Kalıp boşluğunun bir parçası gibi kalıp içinde kalır. Parçaya bağlanışına göre ▪ Üst (direkt) besleyiciler: Parçanın veya beslenecek kısmın üstüne konan besleyicilerdir. ▪ Yan besleyiciler: Parçalara yan taraflardan bağlanan besleyicilerdir. 79 Açık besleyicilerde gözenekli bir çubuk, besleyicinin üst kısmına konur. Maden içinde kalan kısım hemen sıvı metal sıcaklığına erişir. Bu kısmın etrafında bulunan metal katılaşmaz. Çubuğun gözenekleri yardımı ile hava, sıvı metal üzerindeki etkisini sürdürür. 80 MAÇA Döküm parçaların iç boşluklarını veya modelin kumdan sıyrılması sırasında bozulabilecek kalıp kısımlarını oluşturmak için kullanılan kalıp elemanlarına maça denir. Maça malzemeleri çoğunlukla kumdur. Fakat bu kumlar kalıp kumundan farklıdır. En önemli fark ise kalıp kumundaki kil yerine bağlayıcıların kullanılmasıdır. Maçalar maça kutusu veya maça sandığı adı verilen kalıplarda hazırlanır. Maçalar döküm esnasında sıvı metalin içinde kalırlar Sıvı metal maçanın üzerine ağırlığının 3-5 katı kadar bir kaldırma kuvveti etkisi uygular. Maça üzerine etki eden kaldırma kuvveti (F); basit olarak sıvı metal ağırlığı ile maça ağırlığı arasındaki farkın yerçekimi kuvveti ile çarpılması ile bulunur. İşte maçalara etki eden bu kuvveti karşılayacak şekilde desteklenmesi gerekir. Bunun için maçalar maça başlarıyla ve içlerinde teller yerleştirilerek asılmak suretiyle desteklenir. 81 Özellikleri ❑Sıvı metalin sıcaklığı ile şekil değiştirmemeli, Maça desteği kullanılmış kalıp ❑Döküm parça ile iyice kaynaşabilmelidir, Maça kullanılan kalıplarda sıvı metalin ❑Oksitlenmeye (paslanmaya) karşı kaldırma ve yüzdürme etkisine karşı dayanıklı olmalı, koyabilme (örneğin, kör maçalarda) ve ❑Maçanın ağırlığı ile şekli bozulmamalı, maçayı desteklemek amacı ile kullanılan ❑Kullanımları kolay olmalı, çeşitli tip ve ebatlarda üretilmiş olan metal ❑Ucuz olmalıdırlar, gereçlere maça desteği (sport) diyoruz. 82 Döküm sonrası maça kaynaklı hatalar; 1. Maçaların Yapışması: Maça kendisi, maça sandığından yapılırken sandığa yapışabilir. Bunun önüne geçmek için önceden yüzeyine benzin sürülür. 2. Maçalarda Karıncalaşma: Gaz geçirgenliği az olan maçaların yüzeyinde karıncalaşma oluşur. 3. Maçaların Yüzmesi: Maça başı yeterli yapılmayan, iyi şekilde desteklenmeyen maçalar, sıvı metalin içinde yüzebilir. 4. Maçaların Kırılması: Maçalarda yeterli mukavemet yoksa sıvı metal maçayı kırabilir. 5. Maçalarda Damarlar: Maçanın üzerindeki küçük çatlaklara sıvı metal girerek parça yüzeyinde çıkıntılı damarlar meydana gelmesine sebep olurlar. 6. Maçaların Çatlaması: Pişirme sırasında maçada çatlama olmuşsa o maça kesinlikle kullanılmamalıdır. 83 Bir kalıp içinde maçanın çeşitli fonksiyonları olabilir. 84 85