CAB6 MAC Seminar Notes PDF
Document Details
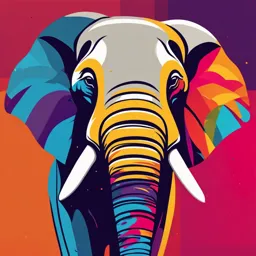
Uploaded by ChasteRhodonite
Hanze University of Applied Sciences Groningen
Tags
Summary
These seminar notes cover various topics in manufacturing accounting. They discuss inventory types, relevant costs, manufacturing costs, and different costing methods like process costing and standard costing. The notes also introduce budgeting concepts and considerations.
Full Transcript
CAB6 MAC Seminar Notes Week 1: Types of inventory: - Raw Materials Inventory (RM): includes materials used to make a product - Work-in-Progress Inventory (WIP): includes goods that are in the manufacturing process but are not yet complete - Finished Goods Inventory (FG): incl...
CAB6 MAC Seminar Notes Week 1: Types of inventory: - Raw Materials Inventory (RM): includes materials used to make a product - Work-in-Progress Inventory (WIP): includes goods that are in the manufacturing process but are not yet complete - Finished Goods Inventory (FG): includes completed goods that have not yet been sold Direct cost- a cost that can be easily and cost-effectively traced to a cost object - Ex. cost of flour used in producing a pizza Indirect cost- costs that cannot easily or cost-effectively be traced directly to a cost object - Ex. cost of electricity spent on baking one pizza Manufacturing costs: Direct materials cost (DM)- cost of raw materials used in production - Ex. cost of cheese Direct labor cost (DL)- cost of labor involved in production - Ex. worker’s salaries Manufacturing overhead cost (MOH)- indirect product costs associated with production including: - Indirect materials: o Ex. costs such as salt using in baking a pizza - Indirect labor: o Ex. salary of the cleaning personnel that works in the pizzeria - Factory costs, rent, utilities, insurance etc. Prime costs- combines the direct costs of direct materials and direct labor Conversion costs (CC)- combines direct labor and manufacturing overhead - CC = DL + MOH Period costs- non-manufacturing costs - Ex. selling expenses, interest expense, income tax expense or administrative expenses Product costs- manufacturing costs - Ex. direct materials, direct labor, manufacturing overhead Equivalent units of production (EUP): - Measures the amount of materials added to or work done on partially completed units during a period - Expresses in terms of fully complete units of output Production cost report- shows the calculations for the physical flows and the cost flows of the products. Including 4 steps: 1. Summarize the flow of physical units 2. Compute output in terms of equivalent units of production (EUP) 3. Compute the cost per equivalent unit of production 4. Assign costs to units completed and units in progress Week 2: Process costing- figuring out how much it costs to produce something How can the production cost report be used to make decisions? - Controlling costs - Evaluating performance - Pricing products - Identifying the most profitable products - Preparing the financial statements Week 3: Budget components: Standard cost system- an accounting system that uses standards for product costs- direct materials, direct labor, and manufacturing overhead. Each input has both a cost standard and an efficiency standard Static budget- a budget prepared for only one level of sales volume - Based on the expected number of units sold Example: Flexible budget- a budget prepared for various levels of sales volume within a relevant range - This is useful for what if analysis Example: Variance- a difference between the actual amount of costs/revenues/profits and the corresponding budgeted amounts - Favourable (F) o When actual costs < budgeted costs ▪ Or o When actual revenues > budgeted revenues - Unfavourable (U) o When actual costs > budgeted costs ▪ Or o When actual revenues < budgeted revenues Flexible budget variance- difference between the actual figures and the budgeted figures for the actual units sold Sales volume variance- difference between that static budget and the flexible budget for the actual units sold Cost variance- measures how well the business keeps units costs of materials and labor within standards (within budget) Cost variance= (actual cost – standard cost)*actual quantity - Cost variance= (AC-SC)*AQ Efficiency variance- measures how efficient the business uses its materials or human resources Efficiency variance= (Actual quantity – standard quantity) * standard cost - Efficiency variance= (AQ-SQ)*SC Week 4: FAC (accidentally did it in the wrong document) Operating cash flows (OCF): includes marginal revenues and marginal costs that occur during the investment period Terminal cash flow- includes the sale of the fixed asset at the end of the investment project Operating cash flow= net operating profit + depreciation expense Types of cashflows: Sunk costs- cash outlays that have already been made (past outlays) and cannot be recovered, whether or not the firm follows through and makes an investment - Sunk costs are irrelevant and should not be included in a project’s incremental cash flows Opportunity costs- cash flows that could have been realized from the best alternative use of an owned asset - Opportunity costs are relevant and should be included as part of the cash flow projections when determining a project’s net cash flows Week 4: MAC Standard cost system: an accounting system that uses standards for product costs. Standard such as price, cost, or quantity that is expected under normal conditions. Each input has both a cost standard and an efficiency standard Cost variance- measures how well the business keeps unit costs of materials and labor within standards. The cost variance measures the difference in actual and standard costs based on the actual amount used Cost variance: More difficult formula but better for plugging numbers in: Efficiency variance- measures how efficient the business uses its materials or human resources. The efficiency variance measures the difference in the actual amount used and the standard amount allowed based on the standard cost Efficiency variance: More difficult formula but better for plugging numbers in: