Cost Accounting Principles - PDF
Document Details
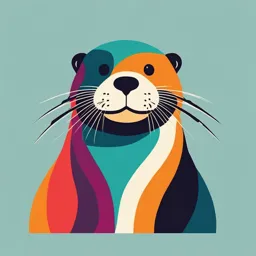
Uploaded by AffableAgate9582
Tags
Summary
This document offers a comprehensive overview of cost accounting principles, including essential concepts like direct and indirect costs, and manufacturing costs, essential for sound business decision-making. Key areas covered include an introduction to costing concepts, cost behavior, and how costs flow through the financial statements. It also features detailed examples clarifying these concepts with case studies and analysis of both variable and fixed costs.
Full Transcript
Okay, here is the structured markdown conversion of the information in the images. ### **Figure 1.4** Costs flowing from production into financial statements (the company manufactures and sells chairs) The image shows a flow diagram of costs in a chair manufacturing business. - **Stage 1** Ra...
Okay, here is the structured markdown conversion of the information in the images. ### **Figure 1.4** Costs flowing from production into financial statements (the company manufactures and sells chairs) The image shows a flow diagram of costs in a chair manufacturing business. - **Stage 1** Raw Material: Wood (R), Steel (R), Fabric (R) - **Stage 2**: Labour, Supervision, Electricity - **Overheads** in the Middle of the above two stages - **Stage 3**: Leads to Total Production Costs. The final products are: - To finished goods until sold (Statement of financial position) - To cost of goods sold when sold. Leads to Statement of Comprehensive Income ## 2 INTRODUCTION The collection, classification, and analysis of costs are fundamental to management accountants as it assists them in planning, control and decision making. Understanding these basic concepts is essential because of the multiple and diverse needs in cost accumulation, planning, control and decision making. You should realise that information used to record the transactions of a business and the subsequent compilation of the annual financial statements is not necessarily the only information used by management in making decisions. Management accounting information should provide relevant facts, whether financial or non-financial, actual or estimated, to enable management to make decisions that will create value over the long term for a company. A lot of reference is made with respect to "big data'' in business circles these days. "Big data" refers to large volumes of data that are available to companies by means of analysed data obtained from loyalty cards, social media, business-to-business machines, etc. The importance is not the volume of available data but how management uses the data to make better decisions, to explore new strategies and so forth, for the purpose of creating value over time for a company. Decision making is reserved for more advanced studies, but it is necessary to create awareness of some of these concepts at this stage. Cost concepts frequently used in planning and decision making include the following: * **Behaviour of cost** in relation to changes in volume/activity. Fixed, variable and mixed costs are discussed later in this chapter. * **Relevance of cost**: Relevant costs are costs that will change in future because of a decision made. The same principle applies to relevant revenue or income. * **Sunk costs**: Sunk costs are costs that are unaffected by a choice between different decisions and usually would have been included in the past. * **Opportunity cost**: Opportunity cost is revenue forfeited because one decision is selected above another. Opportunity cost is not a cost that can be obtained from the accounting system but it is used in decision making. * **Incremental cost**: An incremental cost is the cost of producing an additional group or batch of units of production. The same principle applies to incremental revenue or income. Cost accumulation involves the calculation of product costs for inventory valuation and profit measurement. This chapter examines the characteristics of costs incurred by a typical manufacturing company and how the information about such costs is gathered. Although this textbook will largely use a manufacturing company as an example to explain the cost accounting environment, it is equally applicable to any other type of company (e.g. a service company providing cellular services, a supermarket buying and selling inventory, etc.). The material presented in this chapter is an overview of costing concepts that will be covered thoroughly in the chapters to follow. In addition, the different ways to classify costs are introduced. Costs are classified according to a specific purpose: if the purpose is to determine the manufacturing costs of a cost object, the classification will be categorised in manufacturing or non-manufacturing cost. Another way to classify costs ## WHAT IS MEANT BY COST? According to the Chartered Institute of Management Accountants (CIMA), the word "cost" can be used in two contexts: it can be used as a noun, referring to the cost of an item, but it can also be used as a verb when we attempt to cost something. CIMA's definition of cost in these two contexts is as follows: * **As a noun**: the amount of expenditure incurred on, or attributable to, a specific cost object or activity. * **As a verb**: to ascertain the cost of a specific cost object or activity. ### 2.3 COSTING CONCEPTS #### 2.3.1 Cost unit A cost unit is a unit of output (product/service) for an organisation, for example the cost of a ton of gold from a gold mine or the cost per book of a title published by a publisher. Costs are constantly associated with some object or function or service (see paragraph 2.3.3). There are various ways in which the cost of a unit of output can be determined. For example, costs can be accumulated per cost centre (department), per batch of products, etc., and then down to the cost per unit of output. ### 2.3.2 Cost Centre A cost centre can be defined as follows: * A production or service location, function, activity or item or equipment for which costs are accumulated separately * A collection point or pool created to accumulate costs A cost centre is not necessarily a department. A department could consist of a number of cost centres, for example different production lines within a department have their own cost centres, each being responsible for their own activities that contribute to the value of a company. An advantage of a cost centre is that a company can control its total costs better if it is broken down into smaller segments (i.e. cost centres). The manager of a cost centre is responsible for the accounting of costs only (not, for example, for revenues and profits). There are many different kinds of cost centre, a few of which are listed below:Van Schaik | Type of cost centre | Examples | | :------------------ | :---------------- | | Service location | Stores, canteen | | Function | Marketing division | | Activity | Quality control | | Item of equipment | Packing machine | #### 2.3.3 Cost object Managers want to know how much a particular "item" (product or service) costs. We call this "item" a cost object. Examples of cost objects are the cost of a product, the cost of operating a particular department or the cost of rendering services. Knowing the cost of a specific object enables management to control costs, to determine selling prices and to evaluate performance (see Table 2.1). Table 2.1 Examples of cost objects | Cost object | Example | | :----------------------------------------- | :------------------------------------------------------------------------ | | Project | Construction of a highway from Upington to Namibia | | Programme | An engineering degree at a university | | Service | Flights from Johannesburg to Athens | | Product | Electric toothbrush | #### 2.3.4 Cost pool A cost pool can be described as a grouping of various individual cost items. Cost pools are mainly used in an activity-based costing system. For example, all costs related to ordering and receiving of inventory items could be “pooled” together. Examples of the individual cost items that will be “pooled” together in this case could be the salaries of warehouse foremen, the cost of placing an order, salaries of clerks receiving inventory items, etc. All these cost items are related to ordering and receiving of inventory, and therefore pooled together. ## 2.4 COST ASSIGNMENT Cost assignment is a general term that encompasses both * *tracing* accumulated costs that have a *direct* relationship to a cost object, and * *allocating* accumulated costs that have an *indirect* relationship to a cost object. #### 2.4.1 Cost tracing The term cost tracing is used to describe the assignment of direct costs to a particular cost object. For example, a chair is made of wood. Source documents, such as a requisition or an invoice, assist in tracing the exact quantity of wood used in producing the chair. Wood is an example of direct (raw) materials. Employees directly involved in producing the chair, e.g. carpenters (people who physically produce the chair during the production process), are classified as “direct labour”. This is illustrated in Figure 2.1. #### 2.4.2 Cost allocation The term cost allocation is used to describe the assignment of indirect costs to a particular cost object, for example indirect material, rent of the factory and depreciation of plant and equipment that are necessary to secure orders and get the finished product directly to the customer. This is illustrated in Figure 2.1. A Diagram showing "Cost Assignment to a cost Object" | Type of cost | Cost assignment | Cost Object | | :-------------------------------------------------------- | :-------------------------------------------------------------------------- | :----------------------------------------------------------------------- | | Direct cost (related to a particular cost object) | Encompasses both cost tracing and cost allocation | It is anything for which a separate measurement of cost is desired (e.g. chair) | | :-------------------------------------------------------- | :-------------------------------------------------------------------------- | :----------------------------------------------------------------------- | | Direct cost (related to a particular cost object)Indirect cost (Related to a particular cost object but cannot be traded to it in an economically feasible way ) | Encompasses both cost tracing and cost allocation | It is anything for which a separate measurement of cost is desired (e.g. chair) | ## 2.5 Manufacturing and Non-Manufacturing Costs It was mentioned in the introduction (paragraph 2.1) to this chapter that costs can be classified according to the purpose of the classification. If the purpose is to determine the manufacturing costs of a cost object, the classification of costs will be categorised into manufacturing or non-manufacturing costs. Determining the value of inventory of a manufacturing company typically warrants classification of costs as either manufacturing or non-manufacturing. ### 2.5.1 Manufacturing costs Manufacturing cost – also called product cost or factory cost – is usually defined as the sum of three cost elements: direct materials, direct labour and manufacturing or factory overheads. Direct labour plus direct material is called prime (primary) cost. Conversion cost refers to the cost of converting purchased raw (direct) materials into finished goods. Therefore, direct labour plus manufacturing overheads are conversion costs. Refer to Figure 2.2. A distinction between manufacturing and non-manufacturing costs are made for the purpose of inventory measurement. The International Financial Reporting Standards Figure 2.2 Manufacturing costs A flow chart describing the manufacturing of chairs. The steps are as follows: Manufacturing costs of production a chair divided into. Trace allocated. First is Direct material that is traced to the prime cost, then direct labour which are carpenters produce chair. Product Cost. Manufacturing overhead includes indirect material and indirect labour. ### 2.5.1.1 Direct materials These are materials that are directly related to the cost of a unit. They form an integral part of the finished product and are included explicitly in calculating the cost of the product. Examples of direct materials are wood to manufacture furniture and crude oil to manufacture petrol. Certain costs, related to the purchasing of direct materials, are usually included in direct material cost, for example import duties paid and delivery cost of direct materials. ### 2.5.1.2 Direct labour Direct labour is the cost of the labourers who convert direct materials into finished products. It forms part of the total manufacturing cost that can be traced to, or otherwise identified with, the units of output produced. Typically, direct labour comprises those employees who are directly involved in the manufacturing or assembling process. Direct labour must be measured in terms of time spent and rate of remuneration (cost). It is obvious that the cost of labour is necessary to determine the cost of a product (and eventually the selling price). It is important to record the time spent because it is an indication of ### 2.5.1.3 Manufacturing/factory overheads This broad category includes all indirect manufacturing costs other than direct materials and direct labour. These costs are classified as indirect costs because they are not directly traceable to a product (or cost object). An indirect cost is not directly traceable to a product when the indirect cost is not devisable to each individual product or when it is not economically feasible to trace the indirect cost to a product. Examples are indirect labour of those employees indirectly associated with production, supplies, factory water and electricity, supervisors in the production process, machine maintenance and depreciation of factory buildings. These costs are apportioned (or allocated) to individual products by one of a variety of methods that are discussed in Chapter 5. ### 2.5.2 Non-manufacturing costs Figure 2.3 Non-manufacturing costs shows that: Administrative costs (e.g. Finance or Interest) and Marketing costs e.g. sales commission are both types of non-manufacturing costs Non-manufacturing costs fall into two broad classifications: marketing costs (selling and distribution) and administrative costs. Marketing costs begin at the point at which the manufacturing costs end. That is when manufacturing has been completed and the product is in a saleable condition. It includes the costs of promotion, selling and delivery (distribution). Administrative costs include costs incurred in directing and controlling the organisation. The salary of a manager in charge of manufacturing can be treated as manufacturing overheads, whereas the salary of a manager in charge of administration will be treated as administrative overheads. Finance costs (e.g. interest paid) could also be included in administrative costs. ## 2.6 DIRECT AND INDIRECT COSTS All costs can be classified as either a direct or an indirect cost. Direct costs are specific costs that can be conveniently identified with a product or service, cost object, cost 2.6.1 Direct costs Direct costs are those costs that can easily be traced to a cost object. A source document, such as a requisition form for material or a cost of production report indicating the labour hours of the employees directly involved in the production process, is usually available to ensure accurate tracing of the costs. Examples include direct materials and direct labour, discussed in paragraphs 2.5.1.1 and 2.5.1.2. 2.6.2 Indirect costs Indirect costs are costs that are necessary, for example, in the process to produce a product, but are difficult or not economically feasible to trace directly to the product. Indirect material, depreciation of plant and indirect labour are examples of indirect costs. Note the similarity thereof to manufacturing (or non-manufacturing) overheads. Therefore, indirect costs are the same as overheads. An explanation of how to determine whether a cost is a direct or indirect cost is illustrated in the next two paragraphs. Indirect materials are materials that are needed for the completion of a product but that are not classified as direct materials, because it is not worth the effort to trace the costs of relatively insignificant materials consumed (generally because of their low value) to the final product. Examples include nails, screws and glue. Indirect materials form part of manufacturing overheads. Indirect labour is labour that is not directly traced to the construction, composition or production of the finished product. Indirect labour includes the wages of supervisors, general helpers, maintenance workers and usually material handlers. Indirect labour forms part of manufacturing overheads. ## 2.7 COSTS VERSUS EXPENSES Cost is used in Management Accounting. Product cost (cost of inventory of raw materials, work-in-process (WIP) and finished goods) and expense are used in Financial Accounting. A cost is a sacrifice of resources, while an expense measures the outflow of assets. All expenses are costs, but not all costs are expenses in the period in which they are incurred, even though they become expenses in a later period, for example finished goods inventory in one period is classified as a cost, but when it is sold in a future period, it is then expensed in the statement of comprehensive income. | Cost category | Statement of financial position | Statement of comprehensive income | | :----------------------------------------- | :------------------------------------ | :-------------------------------- | | Product cost | Direct material inventory | | | • Direct material | Direct materials used in production | Cost of sales | | • purchases | Work-in-process inventory | | | • Direct labour | Products completed | | | • Manufacturing overheads | Finished goods inventory | | | Selling and distribution administrative cost | | Selling and administrative expenses | ## 2.8 PRODUCT AND PERIOD COSTS Product costs are costs that are identified with goods produced with the purpose of selling them. In a manufacturing organisation these are the costs that are attached to the product, such as direct materials, direct labour and manufacturing overheads which are included when valuing inventory for finished goods or work-in-process, until they are sold Period costs are costs that are not included in the inventory valuation. They are therefore treated as expenses in the period in which they are incurred. An example of ## 2.9 COST BEHAVIOUR In Cost and Management Accounting many factors affect the level of costs incurred. These factors include the price of material, the number of products produced and so forth. Cost behaviour is a major factor in the planning, control, performance measurement and decision-making functions. When we talk about cost behaviour we are referring to the way in which costs are affected by fluctuations in the level of activity (volume such as products produced, labour time used, etc.). Variable costs and fixed costs are the two most frequently recognised cost behaviour patterns. Fixed costs may be thought of as the costs of being in business, while variable costs are the costs of doing business. Semi-variable (mixed) costs have a fixed element regardless of the level of volume output (within the relevant range) in addition to a variable cost element. 2. 9.1 Fixed costs A fixed cost in total (e.g. rent) remains unchanged irrespective of the level of output (volume) (see Figure 2.6(1)) within a relevant range (see Figure 2.6(2) and Example 2.1). A company rents a factory building in which it could manufacture up to 600 000 products per month. Assume that the rent is R40 000 per month. If the company only produces 400 000 products during a specific month, the total rent paid will remain R40 000. Rent is thus a fixed cost in this scenario because within the relevant range of 0-600 000 products the total cost remained at R40 000. Fixed costs per unit decrease as activity increases and fixed costs per unit will increase as activity decreases (see Figure 2.6(4)). Table 2.2 illustrates a company's total fixed costs as well as the fixed cost per unit within a range of 0–600 000 units of production. Table 2.2 Analysis of a company’s fixed cost | Units produced | Total cost | Cost per unit | | :------------- | :--------- | :------------ | | 1 | R40 000 | R40 000.00 | | 40 000 | R40 000 | R1.00 | | 200 000 | R40 000 | R0.20 | | 600 000 | R40 000 | R0.07 | Table 2.3 Fixed cost behaviour | | Volume increases | Volume decreases | | ------------------------------ | ---------------- | ---------------- | | Total fixed costs | Remain constant | Remain constant | | Fixed costs per unit | Decrease | Increase | | Examples of fixed, costs, are: | | | ## 2.9.2 Step fixed costs Step fixed, costs, are fixed, over a certain range of output increase 2.9.3 Variable costs A total cost that varies in direct proportion to changes in activity volume is a variable Table 2.4 Analysis of a company’s variable costs | Units produced | Material cost per unit | Total material cost | | :------------- | :--------------------- | :------------------ | | 300 | R200 | R60 000 | | 600 | R200 | R120 000 | | 1 200 | R200 | R240 000 | | 2 400 | R200 | R480 000 | Table 2.5 Variable cost behaviour | | Activity increases | Activity decreases | | :------ | :--------------- | :--------------- | | (a) Total variable cost | Increases proportionately | decreases proportionately | | (b) Variable cost per unit | Remains constant | remains constant | Table 2.6 Analysis of a company's fixed cost Chart: Total Cost y axis and Volume over x axis ## 2.9.4 Semi variable (mixed) costs A semi variable, or mixed cost, is one that contains both fixed and variable 0 to 10 of volume There are three bullet points of variable cost. These are: Remain constant per unit at all level of output Increase in total with increase reduction level 2.9.5 Non linear variable costs These charts are cost shown by a activity level increase 2.10 COST SEPARATION, AND ESTIMATION | |:---| As previously discussed, different types of cost are likely to behave differently when volume/activity changes. When studying cost, the cost accountant 2. 1 01 High tow method In this method there is a study on cost Here are the following bullet point. 1Select the highest and lowest level of volume and that corresponding cost. 1. January, is 600. April is1, 000. The cause is 3.7..2 is cause 71.5 2 Subtract the lowest value from the highest value for both volume . 3.7..5 3.4..5 1. To calculate the variable cost, it is called is 2.5 per unit. 2. Replace 25 000 3. If apple was is ,000 * .8 4. Therefore if total cost for the 28:40 it would. Calculating 2 -.5 is ,.8.0 total mixture cost | Month | Total cost | Volume (units) | | :------- | :--------- | :------------- | | January | 2 - 4.5 | .6 | | February | -2.5 | 800. | | March | 3000 | 700 | | April | 2 -4.5 | . | One can that drive that within the relevant range The total mixture cost Cost functions Y =a + bx ## EXAMPLE (2.10 2) Scatter graph 2 - 4.15 Classification of cost related to product Direct material * Direct relate the product * Prime cost * Indirect material is nail sandpaper Factory Overhead Manufacturer cost Other * Marketing and distribution * Accounting Note: There is another way to ask me to return the details on Figure 2.15, if this is unreadable for any reason.