Chapter 19: Managerial Accounting PDF
Document Details
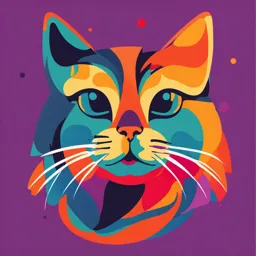
Uploaded by PraisingLandArt
Southeast Business School
Dr Arafat Hossain
Tags
Summary
This document is a chapter on managerial accounting, covering topics such as managerial accounting, cost accounting, manufacturing costs, product costs versus period costs, and providing illustrations of cost concepts.
Full Transcript
Chapter 19: Managerial 1 Accounting Dr Arafat Hossain Assistant Professor Southeast Business School 2 Chapter 19: Managerial Accounting Managerial/Management accounting and Cost accounting Manage...
Chapter 19: Managerial 1 Accounting Dr Arafat Hossain Assistant Professor Southeast Business School 2 Chapter 19: Managerial Accounting Managerial/Management accounting and Cost accounting Managerial Accounting Managerial accounting provides economic and financial information for managers and other internal users. Managerial accounting provides tools to assist management in making decisions and to evaluate the effectiveness of those decisions. Cost Accounting To succeed, the company needs to determine and control the costs of material, labor, and overhead, and understand the relationship between costs and profits. 3 Chapter 19: Managerial Accounting Describe the classes of manufacturing costs and the differences between product and period costs. Managerial Cost Concepts and Classification Manufacturing costs Product vs. period costs Illustration of cost concepts Manufacturing costs Manufacturing consists of activities and processes that convert raw materials into finished goods. Manufacturing costs are classified as direct materials, direct labor, and manufacturing overhead. 4 Chapter 19: Managerial Accounting Describe the classes of manufacturing costs (Contd.) Direct materials Vs Indirect materials: Direct materials: To obtain the materials that will be converted into the finished product. Raw materials are the basic materials and parts used in the manufacturing process. For example, Flour in the baking of bread. Indirect materials: Raw materials cannot be easily associated with the finished product. These are called indirect materials. For example, polishing compounds used by garment company for the finishing garments' products. Direct labor Vs Indirect labor: Direct labor: The work of factory employees that can be physically and directly associated with converting raw materials into finished goods is direct labor. Indirect labor: Indirect labor refers to the work of employees that has no physical association with the finished product or for which it is impractical to trace costs to the goods produced. Examples include wages of factory maintenance people. Like indirect materials, companies classify indirect labor as manufacturing overhead Chapter 19: Managerial Accounting 5 Describe the classes of manufacturing costs (Contd.) Manufacturing Overhead: Manufacturing overhead consists of costs that are indirectly associated with the manufacture of the finished product. Overhead costs also include manufacturing costs that cannot be classified as direct materials or direct labor. Manufacturing overhead includes indirect materials, indirect labor, depreciation on factory buildings and machines, and insurance, taxes, and maintenance on factory facilities. The differences between product and period costs (Contd.) Product costs vs. period costs Product costs: Each of the manufacturing cost components—direct materials, direct labor, and manufacturing overhead—are product costs. product costs are costs that are a necessary and integral part of producing the finished product. Period costs: Period costs are costs that are matched with the revenue of a specific time period rather than included as part of the cost of a salable product. Period costs include selling and administrative expenses. 6 Chapter 19: Managerial Accounting Describe the classes of manufacturing costs and the differences between product and period costs Illustration of Cost Concepts Here are some of the costs that your Snowboard Factory would incur: 1. The materials cost of each snowboard (wood cores, fiberglass, resins, metal screw holes, metal edges, and ink) is $30. 2. The labor costs (for example, to trim and shape each board using jig saws and band saws) are $40. 3. Depreciation on the factory building and equipment (for example, presses, grinding machines, and lacquer machines) used to make the snowboards is $25,000 per year. 4. Property taxes on the factory building (where the snowboards are made) are $6,000 per year. Chapter 19: Managerial Accounting 7 Describe the classes of manufacturing costs and the differences between product and period costs (Contd.) 5. Advertising costs (mostly online and catalogue) are $60,000 per year. 6. Sales commissions related to snowboard sales are $20 per snowboard. 7. Salaries for factory maintenance employees are $45,000 per year. 8. The salary of the plant manager is $70,000. 9. The cost of shipping is $8 per snowboard. Chapter 19: Managerial Accounting 8 Demonstrate how to compute cost of goods manufactured and prepare financial statements for a manufacturer: 1. Income statement 2. Cost of goods manufactured/Cost of goods manufactured schedule 3. Balance sheet Income Statement (for Manufacturing Firm) Under a periodic inventory system, the income statements of manufacturing company compute cost of goods sold by the following equation: Illustration 19-6 shows the methods. (Page: 845) Cost of Goods Sold = (Beginning Finished Goods Inventory + Cost of Goods Manufactured) – Ending Finished Goods Inventory. The cost of goods sold (COGS) is the sum of all costs (e.g., direct raw material and direct labor) associated with making a product. It appears on an income statement. 9 Chapter 19: Managerial Accounting Cost of Goods Manufactured How companies determine the cost of goods manufactured (for manufacturing firm)? The cost of goods manufactured = Total cost of work in process inventory - The ending work in process inventory. Total cost of work in process inventory (for the year) = The cost of the beginning work in process inventory + the total manufacturing costs for the current period. The cost of the beginning work in process inventory: Current Designs has a number of kayaks in various stages of production. These partially completed units are called beginning work in process inventory. It involves the cost. Total manufacturing costs = Direct materials costs + direct labor costs + manufacturing overhead (in the current year). Work in process (WIP) inventory refers to materials that are waiting to be assembled and sold. 10 Chapter 19: Managerial Accounting Cost of Goods Manufactured (Contd.) The ending work in process inventory. At the end of the year, Current Designs may have some kayaks that are only partially completed. The costs of these partially completed units become the cost of the ending work in process inventory. 11 Chapter 19: Managerial Accounting How prepare a balance sheet statement (for a manufacturing company)? Here, we will determine the total current assets of a manufacturing company. Current assets are cash, accounts receivable, inventory, and prepaid insurance. Inventory The balance sheet for a manufacturer may have 3 inventory accounts a) finished goods, work in process, and raw materials, as shown in Illustration 19-10 for Current Designs’ kayak inventory. a) Finished goods inventory (the year ending balance) b) Work in process inventory (the year ending balance) c) Raw materials inventory (the year ending balance). 12 Chapter 19: Managerial Accounting Home Exercises Please do the problem again, which we have solved in the class. Do it 3 Problem. (page: 847). Practice exercises: 2 Tommi Corporation (page 858). Practice problem: Superior Company (page: 858) Do-It 19-3 (page 862). Math Instructions for Final Examination 1. How to compute cost of goods manufactured? 2. How to prepare an income statement (cost of goods sold) 3. How to prepare balance sheet statement (current assets)