Asphalt Mixes and Designs PDF
Document Details
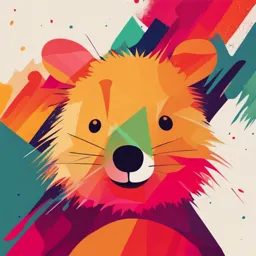
Uploaded by ProsperousSnake3347
University of Dar es Salaam
Tags
Summary
This document details different types of asphalt mixtures, including hot mix asphalt and cold mix asphalt. It also explores various methods of preparing these mixtures, such as the penetration method and inverted penetration method. The properties of these mixtures, such as stability and durability, are also discussed.
Full Transcript
3.4 LIQUEFIED ASPHALTS Normal (Pen-grade) asphalts exist as semi- solids (highly viscous) at room temp. May be liquefied so they can be used without necessity of (or with min.) heating Two products are common - Asphalt emulsions (bituminous emulsions or emulsified asphalt/bitu...
3.4 LIQUEFIED ASPHALTS Normal (Pen-grade) asphalts exist as semi- solids (highly viscous) at room temp. May be liquefied so they can be used without necessity of (or with min.) heating Two products are common - Asphalt emulsions (bituminous emulsions or emulsified asphalt/bitumen) - Cutback asphalts (cutback bitumen or cutbacks) 3.4.1 Asphalt Emulsions Liquefied asphalt obtained by dispersion of asphalt globules in water (containing emulsifying agent). Manufacturing involves passing hot asphalt and water containing emulsifying agent under pressure through a colloid mill to produce extremely small (< 5-10 μm) globules or droplets of asphalt suspended in water Asphalt Emulsion cont… Emulsifiers are additives used to promote dispersion and stability of asphalt-water mixture (w/out segregation) NB: Asphalt is an organic material → does not mix with H2O Emulsifying agent imparts an electric charge to surface of asphalt globules → globules repel one another (→disperse) On the basis of the type of electric charge, asphalt emulsions may be categorized as: - Cationic emulsion (electro-positively charged), or - Anionic emulsion (electro-negatively charged) Acidic (siliceous) aggreg. (sandstone, quartz & siliceous gravel) are negatively charged → compatible with cationic emulsions Basic aggregates (limestones, dolomite, etc.) are positively charged and are therefore compatible with anionic emulsions Classification of Asphalt Emulsions Based on setting/breaking of emulsions: Evaporation of emulsion water leads to formation of a continuous film of asphalt on the surface of aggregates (coalescing). Depending on the rate of setting or breaking, emulsion may be classified as: - Rapid setting (RS) - Medium setting (MS), or - Slow setting (SS) Depends on composition of emulsion; porosity of aggr; rate of evaporation of water (wind, RH, temp); surface chemistry of aggregates. 3.4.2 Cutback Asphalts Obtained when an asphalt is liquefied by dissolution in an organic solvent (called cutter) Curing of cutback-aggregate mixtures occurs by evaporation of the cutter from the cutback. Highly-volatile cutter (e.g. naphtha or gasoline) gives a “Rapid Curing (RC)” cutback Medium-volatile cutter (e.g. kerosene) gives “Medium Curing (MC)” cutback Low-volatile cutter (e.g. diesel or gasoil) gives “Slow Curing (SC)” cutback Common cutback grades are MC-30 and (RC, MC, RC) – 70, 250, 800 and 3000 The number gives the min. viscosity at 60°C (cSt) 3.5 Distillation of Asphalts For separation into components:- fugitive petrolenes and residual asphaltic bitumens Can be done on cutbacks as well as emulsions - Cutbacks (ASTM D-402) - Emulsions (ASTM D-244) Distillation of Emulsions Distillation of Cutbacks 4.0 ASPHALT MIX TYPES AND DESIGN Methods of preparing asphalt mixtures for pavements include - Hot Mix Asphalt (HMA) – heated asphalt + heated aggreg. - Cold Mix Asphalt – cutback or emulsion mixed with aggreg. and laid at ambient temperature. - Penetration Method – heated asphalt sprayed over and allowed to penetrate compacted crushed aggregates - Inverted Penetration Method – spreading asphalt binder over the roadway surface and laying selected aggregates to penetrate the asphalt. Asphalt mixes so produced include (i) Asphalt concrete (AC); (ii) Rolled asphalt; (iii) Mastic asphalt; (iv) Surface treatment (slurry seals, dressing); (v) Bituminous macadam; (vi) Penetration macadam Principal Bituminous Mix Types 1. Asphalt Concrete: A high quality, thoroughly controlled mixture of hot asphalt binder and hot mineral aggregates 2. Rolled Asphalt: A high quality mortar type produced using fine aggregate and penetration grade asphalt. These mixes are more flexible and durable than asphalt concrete 3. Mastic Asphalt: A mortar type of bituminous mix usually cast into blocks, with 14-17% hard asphalt binder (10-25 pen). For crack sealing, to prevent attrition of aggregates, etc. 4. Bitumen Macadams: They contain coarsely graded mineral aggregates coated with asphalt in premix plants. They have higher air voids than AC 5. Penetration Macadams: Produced by spraying heated, dissolved or emulsified asphalt over compacted crushed aggregate in-situ. 6. Surface Treatments: Inc. surface dressing, Otta seals,etc. 5.1 Types of Bituminous Surfacing OTTA SEAL CONSTR. Spreading of aggregate over cutback asphalt spray Rolling with pneumatic Rollers in Otta seal construction 4.1 ASPHALT CONCRETE Produced by the HMA method Primarily used for construction of flexible pavements Very strong paving material, can sustain very heavy traffic loads (roads & airfields) - structural strength to pvmt May be designed as “open-graded” or “dense-graded” or Gap- graded Important (required) properties of AC: (i) Stability; (ii) Durability; (iii) Flexibility; (iv) Fatigue resistance; (v) Skid resistance; (vi) Impermeability; (vii) Workability Required Properties of AC 1) Stability: - Resistance to deformation due to applied load - Depends on cohesion of binder and internal friction of mineral aggregate - Associated with low asphalt contents, dense aggreg gradation & well compacted impervious mixtures - Insufficient stability leads to rutting and corrugations 2) Durability: - Resistance of AC to disintegration by weathering and traffic. Weather → oxidation (age-hardening) - Controlled by thickness of asphalt film around aggr - Enhanced by high AC contents, dense aggregate gradations and well-compacted impervious mixtures 3) Flexibility - Ability of AC to conform to base deformations (e.g. localized/differential settlements) without cracking - Enhanced by high asphalt contents and relatively open-graded aggregates 4) Fatigue resistance - Resistance to pavement failure due to repeated traffic loading (failure in form of alligator cracking) - Dense-graded mixtures offer higher fatigue resist. 5) Skid resistance - Controlled by aggregate physical characteristics (texture, shape & resistance to polish) - Also, low asphalt content & open-graded aggregate 6) Impermeability - Resistance to penetration of water and air - Improves pavement durability and stability - Facilitated by high asphalt content, dense gradation and sufficient compaction (→ imperviousness) 7) Workability - Ease of AC placement and compaction (with reasonable effort) - Factors that promote high stability cause workability problems (→ a compromise required) 8) Others include “Resistance to temperature cracking” and “Resistance to stripping” MIX Bitumen Aggregate Air Voids (in PROPERTY content gradation compacted mix) High Low Dense Open High Low Stability X X X Durability X X X Flexibility X X X Fatigue resist X X X Skid resist. X X X Impermeab. X X X Workability X X X 4.2 ASPHALT MIX DESIGN Two primary properties desirable in design of asphalt concrete mixtures are stability and durability (i.e. getting a stable AC mix that is durable) Factors to also consider are economy and workability Aim is therefore “to find an economical gradation and blend of aggregate and asphalt that will yield a mix having:- 1. Sufficient asphalt binder to ensure a durable pavmnt 2. Sufficient mix stability to serve without distortion or displacement at the anticipated traffic load 3. Sufficient voids in the compacted mix to avoid bleeding 4. Sufficient workability to facilitate proper compaction” Addit. requirements: Flexibility, fatigue- & skid resistance 4.2.1 MARSHALL MIX DESIGN Developed by Bruce Marshall in the US Aims at obtaining a dense mix of high stability but with adequate void content to allow sufficient binder content for good durability and flexibility Standardized in ASTM D1559 and AASHTO T245 Standard procedure involves: (i)Prep. of test specimens, h ≈ 63.5 mm, Ф ≈ 101.5 mm - heating, drying, mixing and compacting in mould - both faces of sample receives same number of compaction blows, determined by the traffic levels Traffic level Number of blows/face Light (ESAL < 104) 35 Medium (ESAL = 104-106) 50 Heavy (ESAL > 106) 75 Marshal Mix Design cont… (ii) Bulk density test Determined on compacted cooled specimens by the water displacement method, with a thin coat of paraffin wax on it (iii) Stability and flow test Specimens are conditioned for 30-40 min in water bath at 60ºC. They are compressed in the Marshall test machine (rate 50.8mm/min) for determination of Stability and Flow NB: Stability is the max load resistance (kN) that the test specimen will develop at 60ºC in the Marshall test. :Flow is the total deformation (in 0.25 mm units) of the specimen at failure when subjected to compression in the Marshall stability test Marshall Mix Design Test Set-up Marshal Mix Design cont… (iv) Density-voids analysis - This involves determination of voids using known and computed density (specific gravity) values - Three types of voids are considered, namely: VMA = Voids in Mineral Aggregates VTM = (Air) Voids in Total Mix VFB = Voids Filled with Binder (also VFA - asphalt) (v) Interpretation of test results The obtained data are used to prepare plots which are used to determine the optimum binder content (vi) Determination of the optimum binder content The content that fulfills the requirements Density-Voids Analysis Mineral aggregates are porous; can absorb water and asphalt to a var. degree. For Marshall mix design, we consider Bulk SG and Effective SG IMPORTANT DEFINITIONS 1. Voids in Total compacted Mix (VTM) Total volume of the small pockets of air existing between the coated aggregate particles in a compacted asphalt paving mixture, expressed as a percentage of the bulk volume of the compacted mixture VTM = (Va/Vm)* 100% 2. Asphalt binder content (Pb) Pb = (Mb/Mm)* 100% 3. Effective asphalt binder (volume) (Vbe) The volume of total asphalt (content) minus the portion of asphalt ‘lost’ by absorption into the aggregate particles Vbe = Vb – Vba NB: Absorbed binder: Pba = (Mba/Mg)*100% IMPORTANT DEFINITIONS cont… 4. Voids in Mineral Aggregate (VMA) The volume of inter-granular void space between the aggregate particles of compacted paving mixture that includes the air voids (VTM) and effective asphalt binder content (Pbe), expressed as a percent of total volume of the mixture specimen VMA = [(Va + Vbe) / Vm] *100% 5. Volume Filled with Binder (VFB) The percentage of the voids in the mineral aggregates (VMA) that is ‘occupied’ by the effective asphalt binder (i.e. voids in mineral aggregate minus voids in the compacted total mix, expressed as a percent of the voids in mineral aggregates) VFB = (Vbe/VMA)*100% = [(VMA-VTM)/VMA] * 100% SUMMARY OF RELATIONSHIPS 1) Mm = Mb + Mg = Mbe + Mba + Mg 2) Vm = Vg + Vbe + Va = Vg + (Vb - Vba) + Va 3) ρmb = Mm/Vm ; (Gm = ρmb/ ρw) 4) Vgb = Mg/ ρgb = Mg/(Ggb*ρw) 5) Mb = Pb * Mm ; Vb = Mb/ρb = Mb/(Gb* ρw) 6) Mba = Pba * Mg ; Vba = Mba/ ρba = Mba/(Gb* ρw) 7) Vbe = Vb - Vba 8) Va = Vm - (Vg + Vbe) = 1 - (Vg + Vbe), cons. unit volume SUMMARY OF RELATIONSHIPS cont… 9) VTM = (Va/Vm)*100% = (Va/1)*100% if Vm = 1 m3 10) VMA = [(Vbe + Va)/Vm] *100% = (Vbe+Va)*100% 11) VFB = [Vbe/(Vbe+Va)] *100% = [(VMA-VTM)/VMA] *100% NB: Theoretical maximum density (max. s/gravity, Gmm): Imaginary density that would result if the specimen had been compacted so that there were no voids in the aggregate- binder mixture (i.e. Va = 0; VTM = 0%) Gmm = Mm/(Vbe+Vg) = Mm/(Vb+Vge) = Mm/[(Mb/Gb) + (Mg/Gge)] = 100/[(Pb/Gb) + (Pg/Gge)] Marshall Mix Design - EXAMPLE An asphalt concrete mix has a bulk density of 2440kg/m3, a binder content, Pb of 5.8% and aggregate binder absorption of 0.8%. If the specific gravities of aggregates and asphalt binder are 2.67 and 1.03 respectively, find the AV (VTM), VMA and VFB SOLUTION: Considering 1 m3 of AC mixture: Mm = ρm *1 = 2440 kg Mb = Pb * Mm = 0.058 * 2440 = 142 kg Mg = Mm - Mb = 2440 - 142 = 2298 kg Mba = Pba * Mg = 0.008 * 2298 = 18 kg Mbe = Mb - Mba = 142 – 18 = 124 kg SOLUTION cont… Vg = Mg/(Ggb * ρw) = 2298/(2.67 * 1000) = 0.861 m3 Vbe = Mbe/(Gb * ρw) = 124/(1.03 * 1000) = 0.120 m3 Va = Vm – (Vgb + Vbe) = 1 – (0.861 + 0.120) = 0.019 m3 Therefore: VTM = (Va/Vm) * 100% = (0.019/1)*100% = 1.9% VMA = [(Va+Vbe)/Vm]*100% = [(0.019 + 0.120)/1]*100% = 13.9% VFB = [Vbe/(Va+Vbe)]*100% = [0.120/(0.019+0.120)]*100% = 89.5%