Thin Film Deposition and PVD PDF
Document Details
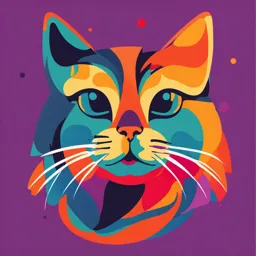
Uploaded by VisionaryChromium
Tags
Summary
This document provides an overview of thin film deposition techniques, including PVD, CVD, evaporation, sputtering, and electron beam evaporation. It discusses various deposition methods and their applications in areas like IC fabrication and other technological fields. The document highlights the significance of controlling film properties and cost-effectiveness in material science applications.
Full Transcript
Thin Film Deposition Any technologies available to deposit thin layers of material onto a substrate of different material. Such technologies are used to achieve the desired properties of the thin film without affecting the bulk properties of the substrate. Thin film de...
Thin Film Deposition Any technologies available to deposit thin layers of material onto a substrate of different material. Such technologies are used to achieve the desired properties of the thin film without affecting the bulk properties of the substrate. Thin film deposition belongs to the larger area of surface coating technologies & phenomena as it alters & improves the properties of the substrate material by treating the surface only for the deposited film properties & highly cost effectiveness. For example, a steel cutter but can be hardened by diamond coating or a steel drill bit hardened by titanium coating. The applications can only be limited by material science or our imagination. Thin Film Deposition With the help of photolithography & etching, many layers can be deposited & patterned on top of each other in IC fabrication. Thin Film Deposition Techniques Categorized into Physical Vapour Deposition (PVD) & Chemical Vapour Deposition (CVD). PVD Techniques: Evaporation Sputtering CVD Techniques: Atmospheric Pressure CVD (APCVD) Low Pressure CVD (LPCVD) Plasma Enhanced CVD (PECVD) Electron Beam Evaporation Evaporation Vacuum process. Involves heating of materials to the point of vaporization. The evaporated material vaporizes, transported by line of sight to & solidifies on the substrate. It follows the 2R (2x Radius) & 1R circumference for uniformity & perpendicular deposition respectively (to be covered in Advanced Wafer Fabrication Technology). Electron-Beam Evaporation Tungsten heater or high-intensity electron beam (EB Gun) is used to heat up the material. EB is preferred method for IC as there is no contamination from the tungsten filament. Tungsten heating evaporation only good for metal & non-metals of low melting point & use in car lights & decorative coatings Only EB can be used to evaporate metal or dielectrics with high melting point. Sputtering Vacuum process. Plasma (ionised gas) of argon by Magnetron (Combine Electric & Magnetic Field). Argon ions bombard the Target (material to deposit) to knock out & dislodge the atoms at the surface. Ejected atoms deposit on the substrate. Conductive materials use DC or RF power source. Non conductive materials can only use RF power source Ion Beam Sputtering to be covered in Advanced Wafer Fabrication Technology Sputtering Depending on the configuration for differing advantages & disadvantages based on placement of the Target & Substrate: Down Sputtering Up Sputtering Side Sputtering EB Evaporation versus Sputtering EB Evaporation Uniformity only with planetary design (to be covered in Advanced Wafer Fabrication Technology). Moderate film density, stress & adhesion. High deposition rate for metal & dielectrics Good directionality (so can do lift off technique) High material utilization Uses: laser optics, solar panels, optical coatings & lift off technique for MEMS (to be covered in Advanced Wafer Fabrication Technology) Sputtering Excellent uniformity without need for planetary design Good film density, stress & adhesion High deposition rate for metals only Low directionality (so cannot do lift off technique) High system cost & complexity Uses: media & DLC in HDD, specific optical & electrical properties