Etching Techniques PDF
Document Details
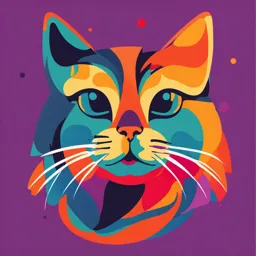
Uploaded by VisionaryChromium
Tags
Summary
This document describes different etching techniques, focusing on wet and dry etching processes in material science and microelectronics. It also highlights the critical step of photoresist removal. The document touches upon the limitations of current optical lithography techniques.
Full Transcript
Etching Etching is to remove any material layer not protected by hardened photoresist after photolithography. It uses the reaction between the chemical (wet etching) or ionized gas (dry or plasma etching) with the material. High degree of selectivity is required so th...
Etching Etching is to remove any material layer not protected by hardened photoresist after photolithography. It uses the reaction between the chemical (wet etching) or ionized gas (dry or plasma etching) with the material. High degree of selectivity is required so that etchant will remove material layer more rapidly than photoresist. There are 2 techniques of etching: Wet etching (also known as chemical etching) Dry etching (also known as plasma etching) Wet Etching Use chemicals for example diluted HF acid also known as Buffered oxide etch (BOE) to etch silicon dioxide. More hazardous. Simple & less costly system. Isotropic process, etching equally in all direction causing undercut. Wet Isotropic Etch Dry Etching Use RF excitation to ionize the gas (plasma) in a vacuum system for example CF4 gas to etch silicon dioxide. Less hazardous. Complex & more costly system. Anisotropic process, without causing undercut. Wet Isotropic Etch Reactive Ion Etching (RIE) Reactive-ion etching (RIE) combines the plasma etching and sputtering action (covered in thin film deposition) of the ionized gas (plasma). It is used for cutting deep trenches especially for MEMS application & fabrication. Highly anisotropic Isotropic & highly Anisotropic etching in MEMS fabrication Photoresist Removal Although strictly speaking, this is not part of etching but it is always done after etching. After etching, photoresist is removed leaving behind the un-etched material layer (pattern of the mask used in photolithography) Typically uses resist stripper or acetone after wet etching. Oxygen plasma is used after dry etching, also known as photoresist ashing Summary Wet Etching Dry Etching Requires disposal of relative Requires only small amount of large amounts of liquid reactant gas & exhausted safely chemical waste (Hazardous) (less Hazardous) Simple & less costly system Complex & more costly system Isotropic Generally anisotropic Summary Material layer formation followed by Photolithography followed by Etching, also known as Lithography Today we are reaching the limits of optical lithography. The wavelength of light is too long to produce smaller features.