Weaving Mechanisms PDF
Document Details
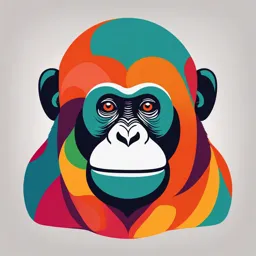
Uploaded by LovelyDaisy
Shakeel Ahmad Paracha
Tags
Summary
This document provides information on the picking motion in weaving mechanisms. It describes the process of passing weft yarns through the warp shed, different types of picking motions, and loom timing. It also discusses the advantages of shuttle picking and disadvantages of over picking.
Full Transcript
Textile Institute of Pakistan, Karachi. TEXT312 (Weaving Mechanisms) The Picking Motion The process of passing weft yarns through the warp shed is called as picking. Picking is done to complete the interlacement process so that a woven fabric can be formed....
Textile Institute of Pakistan, Karachi. TEXT312 (Weaving Mechanisms) The Picking Motion The process of passing weft yarns through the warp shed is called as picking. Picking is done to complete the interlacement process so that a woven fabric can be formed. Number of picks/min. inserted is known as speed of machine and it depends upon picking media and shedding system. If width of loom increases, then picks/min. will decrease. o Shuttle loom : 300 picks/min o Projectile loom : 1050 picks/min o Air-jet loom : 1500 picks/min o Rapier loom : 700 picks/min o Water jet loom : 1000 picks/min Types of Picking Motions Prepared By: Shakeel Ahmad Paracha Page 1 of 29 Textile Institute of Pakistan, Karachi. TEXT312 (Weaving Mechanisms) Loom Timing Loom timing is defined as relative chronological sequences of various primary and secondary motions expressed in terms of angular position of crank. The loom timing is shown in the figure. Loom timing diagram for shuttle loom o Sley Motion 0°: Beat-up takes place and sley occupies its forward most position. 180°: Sley occupies its backward most position. 0° - 180°: Sley moves backward. 180° - 360°: Sley moves forward. o Picking and Checking 80° - 110°: Picking mechanism starts. 105° - 110°: Shuttle enters in the shed. 240° - 250°: Shuttle leaves the shed. 270°: Shuttle strikes the swell in the shuttle box. 300°: Shuttle comes to rest. o Shedding (for early shedding) 30°: Shed is fully open. 30° - 150°: Heald dwell (shed remains fully open). 150° - 270°: Shed closes. 270°: Shed closed or shed level. 270° - 30°: Shed opens again (in opposite direction). o Shedding (for late shedding) 120°: Shed is fully open. 120° - 240°: Heald dwell (shed remains fully open). 240° - 360°: Shed closes. 360°: Shed closed or shed level. 360° - 120°: Shed opens again (in opposite direction). The operations have been delayed by 90° in case of late shedding. Prepared By: Shakeel Ahmad Paracha Page 2 of 29 Textile Institute of Pakistan, Karachi. TEXT312 (Weaving Mechanisms) The Shuttle Picking When insertion of weft yarn through the warp shed is carried out by shuttle then this type of picking is called as shuttle picking. Shuttle looms have a picking unit provided on both sides of the loom. Each picking unit works after every two picks, so its drive is obtained from the bottom shaft. The Shuttle Shuttle is a rectangular piece of wood. Both sides of shuttle are tapered for easy and accurate entry through the shed. Length of shuttle is about 12 - 14 inches and weighs about 14 - 17 ounces. The main body of the shuttle is hollow from inside to accommodate a package known as pirn. A clip is provided on one side of the shuttle to hold the pirn securely. On the other side of the shuttle there is a shuttle eye, through which the weft yarn is removed. Sometimes the inner walls of the shuttle are lined with fur or bristles in order to minimize friction and tension while the weft yarn is withdrawn. The shuttle is thrown from one side of the loom to the other by means of a picking stick provided on both sides of the loom. Prepared By: Shakeel Ahmad Paracha Page 3 of 29 Textile Institute of Pakistan, Karachi. TEXT312 (Weaving Mechanisms) The shuttle flies over a wooden race board and is then collected in the shuttle box, which is also placed at both sides of the race board. For the correct flight of the shuttle, it is necessary that both the shuttle boxes, picking sticks and the race board should be aligned. Different types and sizes of shuttles Different types and sizes of pirns or quills Classification of Shuttle Picking The shuttle Picking mechanism can be classified into two categories: o Over picking o Under picking Prepared By: Shakeel Ahmad Paracha Page 4 of 29 Textile Institute of Pakistan, Karachi. TEXT312 (Weaving Mechanisms) Over Picking o In over picking mechanism, the picking unit is provided above or over the loom. Under Picking o The under-picking unit is placed under or below the loom. Over Picking Over picking is controlled by picking cam which is fixed on the bottom shaft. At first the motion comes from motor to machine pulley. Then the motion comes into the bottom shaft and thus picking cam. When picking cam rotates and its nose portion meets cone. This causes rotation of the picking shaft. As a result, the picking stick, which is attached to the uppermost end of picking shaft, swing in a horizontal plane over the loom and transmits the motion to shuttle through picking strap and picker guided by a spindle. Picking strap is a leather or polymeric belt which is flexible. Here picker is constrained by the spindle to move in a straight line which otherwise would have followed a path of arc. Obviously, this restriction of path is achieved at the expense of some energy. Moreover, pairs of picking cam and follower installed at either end of the loom have seldom ensured picking of equal strength (force). The cams responsible for impulsive rotation of the picking stick receive motion through bottom shaft. Over Picking mechanism Over Picking mechanism on a Loom How to increase PPM By increasing motor speed. By setting the cone stud nearer to the picking tappet. By decreasing the picking strap. Prepared By: Shakeel Ahmad Paracha Page 5 of 29 Textile Institute of Pakistan, Karachi. TEXT312 (Weaving Mechanisms) By altering the position of picking arm towards the center of the loom. By decreasing the length of the stroke of picking tappet. Disadvantages of Over Picking This is an old type of picking method and has become obsolete now because of the following disadvantages: o This type of picking mechanism is only suitable for slow speed and does not work properly at higher speeds. o It occupies lot of space no room is left for mounting the weft replenishing motion necessary for automatic shuttle looms. o Over picking mechanism requires the use of spindle. The spindle is regularly oiled which often causes oil marks in the fabric. Under Picking Under picking is also controlled by picking cam which is fixed on the bottom shaft which displaces the cone turning the picking shaft (side shaft) located horizontally. The other end of the picking shaft is connected with upright picking stick through the picking strap (lug strap). This causes the picking stick to move in a vertical plane and transmits the motion to shuttle by the picker attached at the upper end of it. In this system the picking stick and other appendages are located below the shuttle trajectory while picking cams and follower, as usual, below the loom and driven from bottom shaft. Under Picking mechanism Under Picking mechanism on a Loom Advantages of Under Picking This type of picking mechanism is suitable for high speed automatic looms. It occupies less space on the loom and weft replenishing motion can easily be mounted above the picking mechanism. Prepared By: Shakeel Ahmad Paracha Page 6 of 29 Textile Institute of Pakistan, Karachi. TEXT312 (Weaving Mechanisms) No spindle is used hence the oil spots on the fabric are avoided. How to increase PPM By increasing motor speed. By increasing the nose shape of picking tappet. By decreasing the length of picking arm. Differences between Over Picking & Under Picking Over Picking Under Picking o Picking arm position is above the shuttle box. o Picking arm position is under the shuttle box. o Lower loom speed. o Higher loom speed. o Used for narrow looms. o Used in medium and wider loom. o Light and medium wt. of fabric. o Heavy wt. fabric. o Less power required. o More power required. o Works more smoothly. o Works less smoothly. o Less direct action. o More direct action. o More wear and tear. o Less wear and tear. o No weft replenishing motion. o Weft replenishing motion. o Requires more frequent oiling. o No spindle so no oiling is required. o Comparatively gentle in picking action. o Comparatively harsh in picking action. Shuttle Checking Mechanism The average speed of the shuttle is 50 feet/sec and is achieved through an acceleration of 2500 inches/sec2. As the shuttle is thrown from one side of the loom to the other, it reaches the opposite shuttle box with this great velocity. To avoid damage to loom parts, the shuttle should be completely stopped as it is collected in the opposite shuttle box before it is thrown back by the picker stick. To stop the shuttle, a shuttle checking mechanism is used in either of the shuttle boxes as shown below: Prepared By: Shakeel Ahmad Paracha Page 7 of 29 Textile Institute of Pakistan, Karachi. TEXT312 (Weaving Mechanisms) Advantages of Shuttle Picking Shuttle picking produces automatic selvedges without the aid of an external selvedge device. The shuttle is a versatile picking object because it can carry variety of weft yarns e.g. plain, fancy, thick, and thin etc. Since the weft yarn is carried by the pirn placed in the shuttle, so in this case, the weft yarns become protected from the dust, dirt and lint particles. The cost of producing fabric is low especially when variety of fabric is to be produced on the same loom. Limitations/disadvantages of Shuttle Picking The shuttle method of carrying the weft has a disadvantage that only a limited capacity/length of weft yarn can be carried. For shuttle picking, because of the shuttle size, a bigger shed is required for satisfactory picking. This puts lot of strain and forces on the warp yarns. In shuttle picking an extra process of winding i.e., pirn winding is involved that increases the cost and time required for weft preparation. Also, pirns exhaust more quickly because of their limited size so this also increases the cost of winding operation. The weft replenishing cost in terms of labour will also be increased. As the yarn from the pirn is withdrawn, it also causes changes in the twist of the yarn. Shuttle has a weight of 14 - 17 ounces. In order to displace this weight from one side of the loom to the other, large amount of energy is required. Usually, shuttle picking consumes about half of the loom power only for picking. The shuttle because of its weight and the need of retarding the shuttle on the opposite side, more wear and tear of the loom parts take place. Whenever shuttle picking is used, the need of additional motion called as warp protector motion must be used. The speed of the loom cannot be increased beyond a certain limit. Shuttle picking mechanism and its retardation causes lot of noise. It has been observed through research that a typical weaving shed has a noise level of 105 decibels. Another safety hazard of shuttle weaving is the shuttle flying off the loom. The average speed of the shuttle is about 50 feet per second, at this high speed it can cause serious injuries to the workers and in rare cases, deaths are also reported. Prepared By: Shakeel Ahmad Paracha Page 8 of 29 Textile Institute of Pakistan, Karachi. TEXT312 (Weaving Mechanisms) The Shuttle-less Picking In shuttle-less picking, the picking medium (carrier) is other than shuttle. Shuttle-less picking systems can be categorized with respect to the nature of carrier and its flight through warp shed. A carrier may either be solid or fluid and its flight partially guided or fully guided. Types of Shuttle-less Picking Shuttle-less picking can be categorized as: o Projectile picking o Air-jet picking o Water-jet picking o Rapier picking The Projectile Picking Features of Projectile Picking The projectile method of picking was successfully introduced by Sulzer in 1952. It uses a projectile with a gripper to insert the weft yarn. Wide variety of fabrics ranging from light to medium weight dress fabrics to heavy weight industrial fabrics. This picking technique is suitable for any type of yarn i.e., cotton, wool, synthetic & blended. Low power consumption at high speeds as compared to shuttle picking. Up to six multi-colour pick can be inserted. Wider widths allow more savings in energy and space. Weft cone is directly used for picking. Picking & receiving units are separated from the sley. Picking takes place from one side & several projectiles are used at a time. Number of projectiles depends upon the working width of machine. Maximum width of projectile machine is 540 cm. Projectile moves through guide teeth from picking to receiving unit. Projectile moves through conveyor chain from receiving to picking unit. Every pick is cut off at the picking side after picking leaving length of 15 mm. Prepared By: Shakeel Ahmad Paracha Page 9 of 29 Textile Institute of Pakistan, Karachi. TEXT312 (Weaving Mechanisms) The reed & guide teeth are stationary during picking. The receiving unit is adjustable according to width of fabric. Smaller shed opening due to smaller projectile size. Two picks can be inserted in the same shed. In case of weft breakage, the take-up roller and healed frames can be driven in reverse by a pick finding mechanism. Picking parts are made of high steel material; no wooden or leather parts are used as in shuttle loom. Higher speed due to less mass of projectile as compared to shuttle. W.I.R is 900 - 2000 m/min. Because of less mass of projectile, it is easier to stop the projectile in receiving unit. The Projectile Wt. of projectile = 34 - 40 gms. (Wt. of shuttle = (0.4 - 0.5 kgs.) Projectiles are either made up of steel or carbon composite material. D1, D12 & D2 are different types of steel projectiles. Carbon composite projectiles are classified as K3 type. These types of projectiles are used for weaving different types of fabrics. K 3 type is preferred for weaving delicate fabrics. Prepared By: Shakeel Ahmad Paracha Page 10 of 29 Textile Institute of Pakistan, Karachi. TEXT312 (Weaving Mechanisms) Projectile Picking Parts Supply Package o It is also known as weft package. o It may be in cone or cheese form. o The weight may be from 2.5, 4.167, 6.25 lbs. depending upon the count of yarn. Pre-winder o It is also known as weft feeder or accumulator. o It draws the weft yarn from the package & winds it on the drum. o The length of stored yarn should be 2 - 3 picks. o Its speed is synchronized with the loom speed. o Number of feeders depends upon the number of weft colours. Weft Brake o It reduces the speed of weft yarn. o It acts like brake. o It consists of brake band & moving lever. o Number of weft brakes is equal to the number of feeders. Weft Tensioner o It provides required tension to the weft yarn. o It is made of synthetic lever. o It has ceramic eye. Projectile Feeder Gripper o It transfers the weft yarn to the jaws of projectile gripper. o It also depends upon the number of feeders. o Stroke of feeder gripper is 60 - 65 mm. Projectile o It consists of body & gripper. o Number of projectiles depends upon width of cloth. o It travels through guide tooth. Scissor o It is also known as weft cutter. o It cuts the weft yarn on picking side after picking. Selvedge Gripper o It grips both the ends of weft before beat-up of weft. Prepared By: Shakeel Ahmad Paracha Page 11 of 29 Textile Institute of Pakistan, Karachi. TEXT312 (Weaving Mechanisms) o Two grippers are required per width of cloth. Tuck-in Needle o It bends the cut end of weft yarn on both sides into fell of cloth. o Two tuck-in needles are required per width. Projectile Brake o It stops the moving projectile on receiving side. o It consists of three portions: Front brake Rear brake Lower brake Returner o When the projectile is stopped, it returns the projectile in opening position in receiving side. Receiving Side Opener o It opens the jaws of projectile gripper on receiving side. Expeller o It pushes the empty projectile on conveyor chain. Phases of Projectile Picking 1st Phase (A): o Projectile is moving in picking position. o Projectile feeder gripper is holding weft yarn. o Weft brake is holding weft yarn. o Weft tensioner is applying tension to weft. 2nd Phase (B): o Projectile feeder gripper “2” is opened. o Projectile gripper “1” grips weft end. Prepared By: Shakeel Ahmad Paracha Page 12 of 29 Textile Institute of Pakistan, Karachi. TEXT312 (Weaving Mechanisms) 3rd Phase (C): o Projectile has picked across the shed. o Weft tensioner “3” is releasing the force. o Weft brake “4” is releasing the force. 4th Phase (D): o Projectile is stopped by brake. o Projectile is pushed back by returner in opening position. o Weft tensioner “3” is applying force to carry the slack weft. o Projectile feeder “2” moves near the edge of cloth to grip the weft and brings it back for transfer to next projectile. 5th Phase (E): o Projectile feeder “2” has gripped the weft yarn. o Selvedge gripper “5” is holding the weft yarn on both sides. 6th Phase (F): o Projectile “1” is separated from the weft by projectile opener. o Projectile is expelled on the conveyor chain by expeller. o Weft is cut on picking side by the scissor “6”. 7th Phase (G): o The weft is now beaten up by the reed. o Projectile feeder “2” & weft tensioner “3” return to its original position gripping the weft end for repeating the operation. o In the meanwhile, the two tuck in needles “7” tuck the weft ends in selvedge portion. Prepared By: Shakeel Ahmad Paracha Page 13 of 29 Textile Institute of Pakistan, Karachi. TEXT312 (Weaving Mechanisms) Prepared By: Shakeel Ahmad Paracha Page 14 of 29 Textile Institute of Pakistan, Karachi. TEXT312 (Weaving Mechanisms) The Air-jet Picking Definition o The process of drawing filling yarn from the supply package & inserting this filling yarn through warp shed with the help of air stream/air-jet is called air-jet Picking. The timing diagram of main & sub-nozzles Prepared By: Shakeel Ahmad Paracha Page 15 of 29 Textile Institute of Pakistan, Karachi. TEXT312 (Weaving Mechanisms) Air-jet Picking Major Parts Supply Package o The package may cone or cheese and fitted on cone stand. o The yarn is unwounded by over end withdrawal. o The weight of supply package may be 2.5 - 6.25 lbs. depending upon count of yarn. o The weight of filament yarn package may be 8 - 10 lbs. Cone Stand o It is used to keep the cones to feed the yarn to the pre-winder. o The cones are mounted on rubber pegs on cone stand. o There is a disc tensioner through which yarn is passed through before feeding to the pre- winder. o The function of disc tensioner is to provide the necessary tension to yarn during unwinding from the cone. o The disc tensioner is also used as a guide for the passage of yarn. Supply Package Cone Stand Rubber Peg Disc Tensioner Pre-winder/Weft Accumulator/Weft Feeder o It is used to feed the yarn to the main nozzle/fixed nozzle. o There is a magnetic pin which detects the number of windings on the pre-winder dial and starts the pre-winder to wind the yarn on pre-winder dial when the number of windings on dial are reduced to a fixed number of windings. o Usually 2 - 3 picks yarn is stored on dial. o The number of windings depend upon the pick length (fabric width). o Number of windings on pre-winder dial can be increased or decreased by adjusting the fingers. o There is a nut mounted on the finger which is loosen or tighten to adjust the dial diameter. Prepared By: Shakeel Ahmad Paracha Page 16 of 29 Textile Institute of Pakistan, Karachi. TEXT312 (Weaving Mechanisms) o There is a red colour light on magnetic pin assembly which starts to blink when winding process is carried out on the pre-winder dial. o There are two buttons which are used to unwind the windings from the dial. Pre-winder Side View Pre-winder Front View Pre-winder Dial Finger Magnetic Pin Electromagnetic Pin Assembly ABS (Automatic Brake System) o This system is used to ensure the continuous weft yarn supply to the main nozzle/fixed nozzle. o It vibrates continuously to detect the yarn supply. o It stops the loom when the yarn breaks. It also smoothens the yarn supply by providing the specific tension to the yarn. Main Nozzle/Fixed Nozzle o It is used to feed the yarn to tandom/movable nozzle. o Number of main nozzles depend upon the Number of pre-winders used. o Proper alignment at specific angle, of main nozzle is very necessary. Prepared By: Shakeel Ahmad Paracha Page 17 of 29 Textile Institute of Pakistan, Karachi. TEXT312 (Weaving Mechanisms) o If main nozzle is not properly aligned at any specific angle it will cause weft breakage. Tandom Nozzle/Movable Nozzle o Tandom nozzle is used for blowing of weft yarn during pick insertion. o It passes the weft yarn to the sub-nozzles. o Number of tandom nozzles depend upon the number of pre-winders used. o This nozzle is fixed on sley and move along reed during beat-up. o The distance between the tandom nozzle and weft cutter (LHS cutter) should be so much that during beat-up the tandom nozzle should not strike with the weft cutter. o Number of main nozzles and number of tandom nozzles are always equal. Relay Nozzles o These are also known as sub-nozzles. o Sub-nozzles are fitted on the sley. o Sub-nozzles are arranged over the entire length of the reed & assist the main nozzle in blowing the pick through guide channel. o The sub-nozzles are divided into groups. o Each group of sub-nozzles consists of 5 sub-nozzles and works after certain interval of time in such a way that second group (valve) starts working during the operation of first group (valve). o Air is supplied to the sub-nozzles via solenoid valves. o Each solenoid valve supplies air pressure to 2 - 5 sub-nozzles. o These solenoid valves receive the air pressure from main air supply pipe. o The amount of air pressure increases from left to right in sub-nozzles. o The distance between sub-nozzles is kept 10 - 15 mm depending on the count of weft yarn. o The jets of any sub-nozzle should not be choke otherwise it will cause weft breakage and cause weft loose. Prepared By: Shakeel Ahmad Paracha Page 18 of 29 Textile Institute of Pakistan, Karachi. TEXT312 (Weaving Mechanisms) o The sub-nozzles have varying pitch i.e., the distance b/w two consecutive nozzles and this distance decreases from picking to receiving side to compensate the drop in air pressure. Solenoid Valve o One end of solenoid valve is connected to relay nozzle while other end is connected to air tank. o It regulates the amount of air by electromagnetic function. o Sub-nozzles have the solenoid valves in such a way that one valve operates a group of 2 - 5 sub-nozzles. o The main nozzle has its own solenoid valve. Cutters o There are two cutters, one on picking side & other on receiving side. o The picking side cuter is called as weft cutter & receiving side is known as leno cutter or waste cutter. o The weft cutter cuts the weft yarn after insertion of pick near the selvedge leaving 5 - 10 mm yarn on selvedge. o While the leno cutter separates the leno waste on receiving side. o Following parameters are important for the cutters: Cutting position Cutting degree (250˚ - 300˚) Condition of cutter o There are two types of cutters. o Electrical cutter which is operated with the help of electric motor and other is mechanical cutter, which is operated with the help of lever, which gets drive from loom shaft. Prepared By: Shakeel Ahmad Paracha Page 19 of 29 Textile Institute of Pakistan, Karachi. TEXT312 (Weaving Mechanisms) Catch Cords o These are mostly the synthetic yarns, which grip the weft waste on receiving side of machine. o Number of catch cords ranges from 8 - 12. o These have independent shedding and are used directly without size. Weft Sensors (FD1, FD2) o There are two sensors on receiving side of machine having a distance of 120 - 130 mm b/w them. o These sensors sense the arrival of weft yarn. o The 1st sensor (FD1) ensures the presence of weft yarn if weft yarn is present, the machine will continue to run if yarn is absent then machine will stop. o The 2nd sensor (FD2) has reverse function and ensures the absence of yarn, if weft yarn reaches up to 2nd sensor the machine stops otherwise it will continue to run. Prepared By: Shakeel Ahmad Paracha Page 20 of 29 Textile Institute of Pakistan, Karachi. TEXT312 (Weaving Mechanisms) Stretch Nozzles o The stretch nozzles ensure that the filling yarn remains stretched during closing of shed at beat-up position. o It is mounted at receiving side. Profile Reed o The reed having grooves in it called as profile. o The profile creates a path for traveling of filling yarn from picking to receiving side. o The profile should be in such position that warp yarn should not be in the way during traveling from picking to receiving side. o The reed should be properly cleaned to avoid breakage of warp & weft yarns. Temples o Temples are used to hold the fabric during fabric formation. o Temples also stretch the fabric. o Different types of temples can be used depending upon the fabric quality. o For light weight fabrics ring type temples are used and for heavy weight fabrics pin types temples are used. o Temples are used on both sides of fabric. Prepared By: Shakeel Ahmad Paracha Page 21 of 29 Textile Institute of Pakistan, Karachi. TEXT312 (Weaving Mechanisms) The Water-jet Picking Definition The process of drawing filling yarn from the supply package & inserting this filling yarn through warp shed with the help of water stream/water-jet is called water-jet picking. History of Water-jet Loom o Water-jet weaving machines were first developed in Czechoslovakia in the 1950s and subsequently refined by the Japanese in the 1960s. o The water-jet loom was first shown at the Brussels Textile Machinery Exhibition in 1995. o These Machines have made significant appearance in Japan and some European countries, where more than 60,000 Machines are installed. o However, they cannot be called versatile and flexible. Introduction of Water-jet Loom o A water-jet is the machine for weaving cloth (loom) which uses a jet of water to insert the weft (crosswise yarns) into the warp (lengthwise yarns). o The force of water carriers the yarn from one side to the other. o These machines are produced only by few companies and are used for the manufacture of light and medium weight fabrics with standard characteristics and in water repellent fibre materials. o Water-jet machines are extensively used in East Asia but have limited importance in other countries. o They are characterized by high insertion performance and low energy consumption. o In this technique, a water-jet is shot under force and with it a weft yarn. o The force of the water as it is propelled across the shed carries the yarn to the opposite side. o This machine is economical in its operation. o A water-jet of only 0.1 cm is enough to carry a yarn across a 48-inch shed. o The amount of water required for each weft yarn is less than 2.0 cm3. o Water-jet machines can reach speeds of 2,000 metres of picks per minute. Prepared By: Shakeel Ahmad Paracha Page 22 of 29 Textile Institute of Pakistan, Karachi. TEXT312 (Weaving Mechanisms) Water-jet Loom Major Parts o Main nozzle (1): The water pressure is released from it. o Accumulator (2): It is the device on which reserve length of pick is wound. o Tension Regulator (3): To maintain the tension on weft (filling) yarn. o Weft (filling) Clamper (4): It is to hold the tip of the weft (filling) yarn. o Leno mechanism (5): It is to form the selvedge. o Front roller (6): The woven fabric is passes from the front roller. o Cone (7): It is a kind of weft (filling) package. o Pump (8): It is used to pressurize the water from the source to the water tank of the loom. o Container (9): Container is used as water reservoir. o Cam (10): It is required for the functioning of the pump. o Selvedge cones (11): Selvedge cones the packages of the selvedge ends. o Leno heald eye (12): It is the device through which the leno yarns pass to form leno selvedge. o Clamping device (13): The selvedge ends are passes through it. o Thermal device (14): Use to cut the weft yarn. o Heald frames (15): The warp yarns pass through the heald eyes mounted on the heald shaft for lifting during shedding. o Cloth roll (16): It is the woven fabric roll. Water-jet Loom Working o The weft yarn, which is fed from cone 7, is drawn-off by a feeding and measuring device (accumulator) 2 and then passes through a tension regulator 3 and a weft clamp 4. o When the picking has to take place, the weft clamp loosens its hold and the weft yarn is inserted inside a nozzle 1 and is struck by a jet of pressurized water and launched through the shed at high speed. o After the picking has taken place, while the weft is hold flat by the yarns which are moved by the leno mechanisms 5, the thermal knives 14 enter into action on the launch side to cut the weft, and on the opposite side to trim the fabric. Prepared By: Shakeel Ahmad Paracha Page 23 of 29 Textile Institute of Pakistan, Karachi. TEXT312 (Weaving Mechanisms) o A yarn clamping device 13 holds the weft waste, which is cut off by the right-handed thermal knife, while rotating gears arrange for its removal (centre selvedge). o The water is conveyed by a pump 8, provided with a filter, the piston of which is controlled by a cam 10 producing the phases of water suction from the container 9 and of water supply to nozzle 1. o The sequence of the launch phases is such that the pump 8 enters into action and the initial water-jet serves only to straighten the residual small piece of weft, from nozzle 1 to thermal knife 14. o This action, which has a duration time varying from 5 - 30 rotation degrees of the main shaft, depends on the yarn count and is named guide angle. o The yarn flight forms a so-called flight angle, leaving clamp 4 open to permit to the pressurized water-jet to insert the weft thread into the shed. o The clamp opening time varies according to reed width and to loom running speed. o On yarn exit from the shed, there is an electrical feeler or an infrared sensor which checks the presence of the weft yarn and makes the machine to stop in case of absence of the weft. o A drying device removes the humidity absorbed by the fabric, sucking it through grooves produced in the front beam 6 of the machine. o A maximum of two weft colours can be inserted (weft mixer). Prepared By: Shakeel Ahmad Paracha Page 24 of 29 Textile Institute of Pakistan, Karachi. TEXT312 (Weaving Mechanisms) The Rapier Picking Definition o That type of picking in which single or double rapiers are used as picking media is called rapier insertion and these rapiers are attached at the end of rigid wall and flexible tape. o The rapiers are made of coated steel or reinforced high-performance man-made fibers like carbon. Classification of Rapier Weaving Machines o The rapier weaving machines can be classified on the following basis as: Type of Rapier Rigid, Flexible Number of Rapiers Single, Double or Twin Method of Picking. Gabler, Dewas Single Rapier o Only one rapier takes the weft yarn from picking to receiving side. o Rapier is attached at the end of a rigid rod and rapier has to move across the full width of the shed for pick insertion. o No weft transfer, so no chance of missing the weft yarn. o Mass of reciprocating parts is high. o More dwell period is required as rapier has to travel more distance, so speed is less. o W.I.R = 400 m/min. o Large area or space is required for the rigid rapier system because rod has to move more. Prepared By: Shakeel Ahmad Paracha Page 25 of 29 Textile Institute of Pakistan, Karachi. TEXT312 (Weaving Mechanisms) Double Rapier o They may be rigid or flexible. o Two rapiers are used for Picking. One is called as donor & the other is called as acceptor. Donor It takes the yarn from picking to the center. Acceptor It takes the weft from center to receiving side. Rapier insertion Entrance of both rapiers through the shed from opposite sides is called as rapier insertion. Rapier withdrawal When the weft is transferred to the acceptor both rapiers move backward & it is called as rapier withdrawal. o Double rapier picking is further sub divided into following categories: Rigid Rapier Gabler Dewas Flexible Rapier Rigid Rapier o Thin wall tubes, 10 to 15 mm, or hollow bars of rectangular cross section. Prepared By: Shakeel Ahmad Paracha Page 26 of 29 Textile Institute of Pakistan, Karachi. TEXT312 (Weaving Mechanisms) o Advantages They do not require guiding across the warp sheet; the rapier head slides on the race board. High mass and rigid construction ensure straight movement of rapier heads. A great diversity of both warp and weft yarns in yarn count and character. Dewas Tip to tip picking. The tip of the weft yarn is firmly gripped by the rapier heads during the entire period of picking. Gabler Picking in the form of hairpin. The weft yarn is not firmly gripped, merely yarned around the rapier head. After its transfer at the center, it is straightened as the taker retracts the shed. Prepared By: Shakeel Ahmad Paracha Page 27 of 29 Textile Institute of Pakistan, Karachi. TEXT312 (Weaving Mechanisms) Flexible Rapier o Tapes of rectangular cross section, 25 x 10 mm, made of steel or plastic. o They require guiding across the shed especially for larger working widths. o The ribbed guide is similar to that used in projectile weaving machines. o The guides pass under the cloth fell when the sley approaches its most forward position. Prepared By: Shakeel Ahmad Paracha Page 28 of 29 Textile Institute of Pakistan, Karachi. TEXT312 (Weaving Mechanisms) Advantages & Disadvantages of Flexible Rapier Advantages Disadvantages o Less floor space requirement, productivity o The warp yarns should not be damaged by is higher. the ribbed guides. o Flexible rapier bands are wound on wheels o Guiding system may lead to the end or placed in semicircular channels when breakages. they are withdrawn outside the shed, and o Using fancy yarns in warp direction is the result is wide working widths up to 5 m. almost impossible. o By eliminating guides, there is an advantage of reducing warp breakage and weaving of fancy yarns becomes much easier because the obstructions are removed from the warp shed. Advantages & Disadvantages of Shuttle-less Looms Advantages of Shuttle-less Looms Disadvantages of Shuttle-less Looms o Production is high due to high rate of the o The price of loom having Shuttle-less picking. picking mechanism is higher. o Less labour cost due to high productivity. o Weak yarns cannot be used because speed of o Defect-free cloth for longer length. Shuttle-less picking is very high. o Shuttle-less loom creates less noise. o Looms having Water jet picking mechanism are equipped with efficient drying unit since o Pirn winding process is eliminated. wet fabric cannot be stored in a roll. Due to o Its weaver beams have larger flanges that this reason, cost of production increases. can accommodate 3 times more warp sheet. o Accident percentage is low. o Easy maintenance and less workload for workers. o Used for high scale production. o The efficiency of shuttle-less loom is higher than shuttle loom. Prepared By: Shakeel Ahmad Paracha Page 29 of 29