Fabric Structure and Design PDF
Document Details
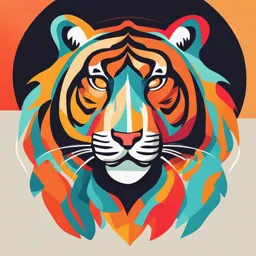
Uploaded by CongratulatoryThermodynamics
Kumaraguru College of Technology, Coimbatore
2004
N. Gokarneshan
Tags
Summary
This textbook covers the fundamental aspects of fabric structure and design, providing detailed information about looms, weaving mechanisms, and different types of fabrics used by textile technology students.
Full Transcript
THIS PAGE IS BLANK Copyright © 2004, New Age International (P) Ltd., Publishers Published by New Age International (P) Ltd., Publishers All rights reserved. No part of this ebook may be reproduced in any form, by photostat, microfilm, xerography, or any other means, or incorporated into any inf...
THIS PAGE IS BLANK Copyright © 2004, New Age International (P) Ltd., Publishers Published by New Age International (P) Ltd., Publishers All rights reserved. No part of this ebook may be reproduced in any form, by photostat, microfilm, xerography, or any other means, or incorporated into any information retrieval system, electronic or mechanical, without the written permission of the publisher. All inquiries should be emailed to [email protected] ISBN (10) : 81-224-2307-8 ISBN (13) : 978-81-224-2307-5 PUBLISHING FOR ONE WORLD NEW AGE INTERNATIONAL (P) LIMITED, PUBLISHERS 4835/24, Ansari Road, Daryaganj, New Delhi - 110002 Visit us at www.newagepublishers.com DEDICATED TO MY BELOVED PARENTS, WIFE, SON AND MY REVERRED GURU THIS PAGE IS BLANK FOREWORD I am pleased that Mr. Gokarneshan has brought out this book. I have gone through the contents of the book and strongly recommend it for the students of textile technology at diploma and undergraduate levels. As the subject “fabric structure and design” forms the core in the syllabi of many universities and polytechnics, this book will be invaluable to all students. The book has been well structured and can be easily assimilated even by an average student. The review questions and exercises in each chapter will be very useful to the students. Though a number of books are available on the subject, yet I strongly feel that this book is ideal for the students. Also the teachers will find it easy to teach the students with the help of this book. Undoubtedly the books of Watson’s textile design which have been used by students world wide from time immemorial, have covered the subject in a detailed manner. Though this book does not deal the subject so exhaustively as the other recommended books, it presents the matter in the simplest way. The reader will therefore not experience any difficulty in understanding the fundamentals of the subject. There is always scope for improvement in the quality of the book. I am sure that the book will be appreciated by the readers. I appreciate the initiative and efforts taken by the author in the preparation of the book. In fact he had consulted me about his plans in writing this book. I wish that he continues to make more such valuable contributions in the near future. I also wish him all the success in his endeavours. Dr. V. Subramaniam Retd. Professor Department of Textile Technology Anna University CHENNAI - 600 025 THIS PAGE IS BLANK PREFACE It gives me a great pleasure to bring out this book. Fabric structure is a core subject for undergraduate and diploma courses. It is an interesting subject provided the basic concept underlying the subject is well understood. The aim of the author is therefore to bring fundamentals of the subject right down to the level of the average student. The special feature of the book is its simplicity. The book has been structured well with simple explanations and illustrations. The chapter end review questions and exercises add more value to the book. In other words the book is designed to be a student edition. I am grateful to those who have helped and supported me during the preparation of this book. I would first of all wish to express my gratitude to M/s New Age International Private Ltd., Publishers, for their valuable suggestions in enhancing the value of the book. The main source of motivation in bringing out this book is my beloved correspondent Prof. K. Arumugam. He has been constantly encouraging and motivating teaching faculty of our college to write books. His encouraging words inspired me to write this book. I thank Dr.V. Subramaniam who went through the contents of the book and appreciated it. I also thank my beloved principal Dr. K. K. Padmanabhan who was also another source of inspiration for me. I am also grateful to my HOD Dr. V. Natarajan for his encouragement. Last but not the least I wish to express my special gratitude to Mr. K. Aravindan and Miss. A. Karuna for their able assistance in preparing the illustrations. I am also thankful to those who directly or indirectly helped me in the preparation of this book. I sincerely hope the contents of the book will be properly assimilated by the readers. It is to be noted that this book deals with only the fundamental aspects of fabric design and that the reader is suggested to refer to the books on Watson’s Textile Design and Colour and Watson’s Advanced Design for enhancing his/her knowledge on the subject. I heartily welcome suggestions regarding corrections, additions or modifications needed to improve the value of the book. Error if any is regretted. Coimbatore N. GOKARNESHAN THIS PAGE IS BLANK CONTENTS 1. LOOMS AND LOOM MECHANISMS 1 2. WOVEN DESIGN FUNDAMENTALS 7 3. PLAIN WEAVES 16 4. TWILL WEAVES 22 5. HONEY COMB WEAVES 37 6. HUCK A BACK WEAVES 42 7. CREPE WEAVE 45 8. BEDFORD CORDS 50 9. WELTS AND PIQUES 56 10. MOCK LENO WEAVES 62 11. BACKED FABRICS 67 12. PILE FABRICS 73 13. EXTRA WARP AND EXTRA WEFT FIGURED FABRICS 92 14. DOUBLE CLOTHS 100 15. BASIC ASPECTS OF COLOURS AND ITS EFFECTS 116 APPENDICES 129 GLOSSARY OF IMPORTANT FABRIC TERMS 131 BIBLIOGRAPHY 139 THIS PAGE IS BLANK CHAPTER Looms and Loom Mechanisms 1.1 INTRODUCTION A loom is a device that causes interlacement two sets of threads, namely, warp and weft threads, to form a fabric. The very first loom in history is the pit loom. Subsequently the handloom was developed and then the power loom. After the advent of power looms, a number of developments have taken place. The very first power looms that had been developed were of the non automatic type. These looms had neither a positive let off device nor warp stop mechanism or a weft changing mechanism. This demanded a great deal of attention from the weaver. The semi automatic loom was then developed which incorporated two out of the above three mentioned mechanisms. Then the automatic loom was developed which had all the three essential mechanisms, namely, positive let off device, warp stop mechanism and weft replenishment mechanism. The last century saw the development of shuttle less weaving mechanisms. 1.2 CLASSIFICATION OF LOOMS The chart below shows the broad classification of the various types of looms. Hand loom Power loom Dobby Jacquard Shuttle Shuttle less Non automatic Semi automatic Automatic Projectile Rapier Air jet Water jet Warp pattern Weft pattern Tappet Dobby Jacquard Multiple boxes 1.3 BRIEF DESCRIPTION OF VARIOUS LOOMS The hand loom was operated by the weaver using his hands to propel the shuttle from one end to another. The weaver used his foot to operate the healds. The production in this type of loom was obviously very less and thus varied from weaver to weaver. 2 Fabric Structure and Design The power loom was operated by power. This reduced the strain of the weaver. Considerable automation has taken place which resulted in lesser strain of the operatives and increasing the production and efficiency of the loom. The shuttle less looms are good examples. The tappet, dobby and jacquard are warp patterning mechanisms. Among the shuttle looms, the tappet loom is the simplest. It is suitable for weaving up to 8 heald shafts. The dobby loom is suitable for figuring upto 40 heald shafts and the jacquard is suitable for elaborate designs running to several picks. The advantage of the jacquard mechanism is that it can control individual warp ends and hence has a large figuring capacity. ∑ The multiple box mechanism is suitable for weft patterning, particularly in creating checked ef- fects in the fabric. The colouring capacity of the multiple boxes ranges from 2 to 24. ∑ The shuttle less looms have the advantage of higher speed and efficiency than the conventional shuttle looms. Also larger weft packages minimize the frequency of weft changes thus improving the loom efficiency. 1.4 BASIC LOOM MECHANISMS The basic mechanisms in any type of loom can be classified as follows: (a) Primary motions (b) Secondary motions, and (c) Auxiliary motions. The primary motions can further be divided as shedding, picking and beat up motions. The shedding opens the warp sheet into layers to facilitate passage of shuttle. The picking motion causes the shuttle carrying weft to be propelled from one end of loom to another. The beat up motion lays the previously laid weft to the fell of the cloth. The secondary motions comprise of take up and let off motions. The take up motion helps to wind the cloth on to the cloth roller and also influences the pick density in the cloth. The let off motion helps to let the warp from the weaver’s beam at an uniform rate thus maintaining the warp tension constant throughout the weaving process. The auxiliary motions consist of the warp stop motion, weft stop motion and warp protector motion. The warp stop motion is used to stop the loom in the event of warp breakages. This is necessary to prevent fabric defects such as missing ends and floats. The weft stop motion is used to stop the loom in the event of weft exhaustion or weft breakages. This is necessary to prevent missing weft threads called cracks, in the fabric. The warp protector is used to prevent multiple warp thread breakages in the event of shuttle getting trapped in the middle of the warp sheet. 1.5 GENERAL PASSAGE OF MATERIAL THROUGH A LOOM The passage of warp through a loom is shown in Fig. 1.1. The warp after leaving the weaver’s beam 1 passes over two bars 2 and 3 connected by a bracket at each end. One half of the warp end now passes under the back lease rod 4, and the other half passes over this rod. Those warp ends which pass under the back lease rod pass over the front lease rod 5, and ends from over the back lease rod pass under the front lease rod. Therefore, the warp is completely divided as it passes through the lease rods, and facilitates the straightening of any warp ends which may break and become entangled before they reach the healds 6 and 7. The lease rods also assist in forming an even shed. Leaving the lease rods, the warp ends next Looms and Loom Mechanisms 3 pass through the healds. Odd numbered pass through the front heald 7, and the even numbered ends pass through the back heald 6. The healds consists of heald wires with eyes at the centre through which the warp ends are passed, the warp ends being thus controlled in their upward and downward movement. The warp ends next pass through the reed 8, this being comprised of a flat wire comb with the teeth secured at both ends. Usually two ends pass between one tooth and the next—this space being termed “dent”. In the figure, two warp ends are represented as being in the same dent. PATH OF WARP YARN AND CLOTH THROUGH A LOOM 5 4 11 10 9 8 6 3 2 7 12 1 13 1 – Weavers Beam 9 – Feel of the Cloth 2,3 – Two bars of Back Rest 10 – Temple 14 4 – Back Lease Rod 11– Breast Beam 5 – Front Lease Rod 12 – Emery Roller 6 – Back Heald 13 – Tension Rod 7 – Front Heald 14 – Cloth Roller 8 – Reed Fig. 1.1 Passage of warp in a loom At the point 9 is what is known as the ‘Cloth fell’. It may be considered as the point where the warp and weft become cloth, because it is at this point where the last pick of weft, which was left by the shuttle, becomes beaten up. Passing forward, the cloth is held at each side by a temple 10 which holds the cloth fell out to the width of the warp yarn, in the reed. From the temples the cloth passes over the breast beam/front rest 11, partly round the sand or emery roller K, over the steel roller, or tension rod L, and then on to the cloth roller M. 1.6 DESCRIPTION OF IMPORTANT PARTS OF A LOOM 1.6.1 Heald shaft This part is related to the shedding mechanism. The heald shaft is made of wood or metal such as aluminium. It carries a number of heald wires through which the ends of the warp sheet pass. The heald shafts are also known as ‘heald frames’ or ‘heald staves’. The number of heald shafts depends on the warp repeat of the weave. It is decided by the drafting plan of a weave. The main function of the heald shaft is as follows: (i)It helps in shed formation (ii)It is useful in identifying broken warp threads (iii)It maintains the order or sequence of the warp threads (iv) It determines the order of lifting or lowering the required number of healds for a pick. In other words it helps in forming the design or pattern in a fabric. (v) It determines the warp thread density in a fabric, i.e. the numbers of heald wires per inch deter- mine the warp thread density per inch. 4 Fabric Structure and Design 1.6.2 Sley or lay It is made of wood and consists of the sley race or race board, reed cap and metal swords carried at either ends. The sley mechanism swings to and fro. It is responsible for pushing the last pick of weft to the fell of the cloth by means of the beat up motion. The sley moves faster when moving towards the fell of the cloth and moves slower when moving backwards. This unequal movement is known as ‘eccentricity of the sley’. It is needed in order to perform the beat up and also to give sufficient time for passage of shuttle to pass through the warp shed. The beat up of the lastly laid pick of weft is accomplished through a metal reed attached to the sley. 1.6.3 Shuttle It is basically a weft carrier and helps in interlacement of the weft with the warp threads to form cloth. The shuttle which is made of wood passes from one end of the loom to the other. It travels along the wooden sley race and passes between the top and bottom layers of the warp sheet. The shuttle enters a shuttle box fitted at either ends of the loom, after passing through the warp shed. A shuttle normally weighs about 0.45 kgs. 1.6.4 Shuttle box It is the housing for the shuttle and is made of wood. It has a spindle and a picker. It may also accommodate the picker without spindle. The top and side of the box towards the sley race are open. The shuttle dwells inside the box for the intermediate period between two successive picks. 1.6.5 Picker The picker is a piece made either of leather or synthetic material. It may be placed on a spindle or grooves in the shuttle box. It is used to drive the shuttle from one box to another. It also sustains the force of the shuttle while entering the box. 1.6.6 Reed It is a metallic comb that is fixed to the sley with a reed cap. The reed is made of a number of wires and the gap between wires is known as dents. Each dent can accommodate one, two or more warp ends. The count of the reed is decided by the number of dents in two inches. The reed performs a number of functions which are enumerated as follows: (i) It pushes the lastly laid pick of weft to the cloth fell (ii) It helps to maintain the position of the warp threads (iii) It acts as a guide to the shuttle which passes from one end of the loom to the other. (iv) It determines the fineness of the cloth in conjunction with the healds. (v) It determines the openness or closeness of the fabric. There are various types of reed such as ordinary reed, gauze reed, expanding reed, V reed etc. 1.6.7 Warp beam This is also known as the weaver’s beam. It is fixed at the back of the loom. The warp sheet is wound on to this beam. The length of warp in the beam may be more than a thousand metres. Looms and Loom Mechanisms 5 1.6.8 Back beam This is also known as the back rest. It is placed above the weaver’s beam. It may be of the fixed or floating type. In the first case the back rest merely acts as a guide to the warp sheet coming from the weaver’s beam. In the second case it acts both as a guide and as a sensor for sensing the warp tension. 1.6.9 Breast beam It is also known as the front rest. It is placed above the cloth roller at the front of the loom and acts as a guide for the cloth being wound on to the cloth roller. The front rest together with the back rest helps to keep the warp yarn and cloth in horizontal position and also maintain proper tension to facilitate weaving. 1.6.10 Cloth beam It is also known as the cloth roller. The woven cloth is wound on to this roller. This roller is placed below the front rest. REVIEW QUESTIONS 1. What are primary motions in a loom? 2. What are secondary motions in a loom? 3. What are the objects of the Take-up motion in a loom? 4. What are the objects of the Let-off motion in a loom? 5. What is the function of the Reed? 6. Why are Temples necessary in a loom? 7. Mention the function of the picker in a loom. 8. What is the need for the Back-Rest in a loom? 9. What do you understand by the term ‘fell of the cloth’? 10. Give the other name for the Front-rest. 11. What do you understand by the term ‘Dent’? 12. Mention the function of the Breast beam. 13. Define count of the ‘Reed’. 14. Define ‘Heald count’. 15. What is the function of the Sley in a loom? 16. Define the ‘Eccentricity of the Sley’. EXERCISE 1. With the aid of a neat sketch explain the passage of warp through a loom. 2. Explain the functions of the various important parts of the loom. 3. Give the classification of looms and loom mechanisms. 6 Fabric Structure and Design PRACTICE 1. Observe the passage of warp in a loom and note the position of the various parts. 2. During the working of a loom note the sequence of actions of the primary, secondary and auxiliary mo- tions. 3. Measure the width of the loom by measuring the width of the reed. 4. Measure the height of the warp shed by measuring the distance between the warp threads of the extreme heald shafts. 5. Find out the count of the reed and healds. The reed count is found by counting the number of dents in 2 inches of the reed. The count of the healds is found by counting the number of heald wires in one inch, from the front to back heald shafts. CHAPTER 2 Woven Design Fundamentals 2.1 INTRODUCTION A woven cloth is formed by the interlacement of two sets of threads, namely, warp and weft threads. These threads are interlaced with one another according to the type of weave or design. The warp threads are those that run longitudinally along the length of the fabric and the weft threads are those that run transversely across the fabric. For the sake of convenience the warp threads are termed as ends and the weft as picks or fillings. 2.2 CLASSIFICATION OF WOVEN STRUCTURES Woven structures are classified into the following categories: (i) Simple structures (ii) Compound structures In case of simple structures, there is only one series of warp and weft threads. These threads interlace with one another perpendicularly. All the neighbouring warp and weft threads are parallel to one another and play an equally important role in determining the properties of the fabric. In case of compound structures, there may be more than one series threads, of which one set forms the body or ground and the other forms the figuring or ornamentation. Unlike the simple structures, the neighbouring threads need not be parallel to one another. 2.3 METHODS OF WEAVE REPRESENTATION A weave is the interlacing pattern of the warp and weft. Two kinds of interlacing are possible : (i) Warp overlap in which warp is above weft (ii) Weft overlap in which weft is above warp When the warp is lifted above the inserted weft, a warp overlap is obtained. When the warp thread is lowered, the weft thread is inserted above the warp thread and the weft overlap is obtained. 8 Fabric Structure and Design There are two practical methods of weave representation : (i) Linear (ii) Canvas In the linear method each warp thread is represented by a vertical line and each weft thread by a horizontal line. The point of intersection of lines corresponding to a warp overlap is marked by the dot, and the point of intersection corresponding to weft overlap remains unmarked.. Though this is a simple method, it is seldom used because the designer has to draw plenty of horizontal and vertical lines, which is time consuming. In the canvas method, a squared paper is employed, on which each vertical space represents a warp thread and each horizontal space represents a weft thread. Each square therefore indicates an intersection of warp and weft thread. To show the warp overlap, a square is filled in or shaded. The blank square indicates that the weft thread is placed over the warp i.e. weft overlap. Several types of marks may be used to indicate the warp overlap. The ‘x’ mark is most commonly used. A weave diagram is shown below (Fig. 2.1). X X X X X X X X Fig. 2.1. Weave representation (Canvas method) 2.4 WEAVE REPEAT (REPEAT SIZE) The repeat of a weave is a quantitative expression of any given weave. It indicates the minimum number of warp and weft threads for a given weave. It comprises of warp and weft repeat. The size of the repeat may be even or uneven depending upon the nature of the weave. In elementary weaves such as plain, twill, satin etc. the repeat size is normally even. However in weaves such as honey comb, huck a back the repeat size may be even or uneven. For any weave the repeat size is the sum of the warp and weft floats. Thus in case of a 2/1 twill the repeat size is 3 ¥ 3. It is common practice to denote one repeat of a weave on design paper. 2.5 BASIC ELEMENTS OF A WOVEN DESIGN The three basic elements in a woven design are : (i) Design (ii) Draft or drawing plan (iii) Peg or lifting plan The design indicates the interlacement of warp and weft threads in the repeat of the design. It is made up of a number of squares, which constitute the repeat size of a design. The vertical direction of the squares indicate the picks and the horizontal direction indicates the ends. A blank in a square indicates Woven Design Fundamentals 9 that a warp goes below the corresponding weft and ‘X’ mark in the square indicates that the warp floats above the weft. The draft or drawing plan indicates the manner of drawing the ends through the heald eyes and it also denotes the number of heald shaft required for a given weave repeat. The choice of the type of drafting plan depends upon the type of fabric woven. The peg or lifting plan provides useful information to the weaver. It denotes the order of lifting of heald shafts. In a peg plan the vertical spaces indicate the heald shafts and the horizontal spaces indicate the picks. The peg plan depends upon the drafting plan. In the case of a straight draft, the peg plan will be the same as the design. Hence no peg plan is necessary in the case of a straight draft. The design, draft and peg plan are illustrated with the aid of an example shown below (Fig. 2.2) Drafting Plan 4 X 3 X 2 X 1 X 4 X X 4 X X 3 X X 3 X X 2 X X 2 X X 1 X 1 X X 1 2 3 4 1 2 3 4 Design Peg Plan Fig. 2.2. Basic elements of a Woven Design (2/2 twill weave) 2.6 TYPES OF DRAFT PLANS The various drafts are classified as follows : (i) Straight (ii) Pointed (iii) Skip and sateen (iv) Broken (v) Divided (vi) Grouped (vii) Curved (viii) Combination 2.6.1 Straight draft This is the most commonly used draft. It is the simplest of all the types of draft plans. In this kind of draft the drafting order progresses successively from first to the last heald frame. Thus the first warp end of a weave is drawn through the first heald shaft, the second warp through the second heald frame and so on. 10 Fabric Structure and Design One important feature of the straight draft that distinguishes it from other types of draft plans is that the peg or lifting plan is same as the design. Hence it is sufficient to indicate only the design. Fig. 2.3 shows the straight draft. 4 X X X 3 X X X 2 X X X 1 X X X 1 2 3 4 Repeat Fig. 2.3. Straight Draft 2.6.2 Skip draft The skip draft is suitable for weaving fabrics having heavy warp thread density. In this kind of draft plan the number of heald frames may be twice or more than the minimum required for a weave. The purpose of using more heald frames than the minimum recommended is only to distribute the warp threads more uniformly so as to prevent abrasion of the threads due to overcrowding. (Fig. 2.4) Draft Repeat 6 X II 5 X 4 X 3 X I 2 X 1 X 1 2 3 4 5 6 Warp Repeat Fig. 2.4. Skip Draft Woven Design Fundamentals 11 The heald frames are divided into two groups. All even numbered warp threads are drawn through the first group of heald frames and all odd numbered warp ends are drawn through the second group of heald frames. The sateen draft serves the same purpose as the skip draft. A skip draft is normally employed for weaves such as plain and twill upto a repeat of 4. Whereas the sateen draft is used for weaves having repeat size of more than 5. 2.6.3 Pointed draft This is similar to a straight draft. It is suitable for weaves such as pointed twill, diamond weaves and ordinary types of honeycombs. The straight draft is reversed after half the repeat warp way. The number of heald shafts is about half the repeat size of the weave. Fig. 2.5 shows a pointed draft. 6 X 5 X X 4 X X 3 X X 2 X X 1 X 6 5 4 3 2 1 Fig. 2.5. Waved Twill and Pointed Draft 2.6.4 Broken draft A broken draft almost resembles the pointed draft. However the pointed effect is broken. This type of draft is suitable for weaves such as herringbone twills (Fig. 2.6). 12 Fabric Structure and Design 4 X X X X 3 X X X X 2 X X X X X X X X 1 8 7 6 5 4 3 2 1 1 2 3 4 5 6 7 8 9 10 11 12 13 14 15 16 Fig. 2.6. Waved Twill and Broken Draft 2.6.5 Divided draft This draft is used for weaves having two series of warp threads such as terry, double cloth, warp backed cloth etc. As can be seen in Fig. 2.7, the two sets of warp threads, say, face and back warps are divided into two groups. The first group is for 8 heald shafts and second for 9-12 heald shafts. 12 X X 11 X X 10 X X 9 X X 1 2 3 4 5 6 7 8 9 10 11 12 13 14 15 16 8 X 7 X 6 X 5 X 4 X 3 X 2 X 1 X 1 2 3 4 5 6 7 8 9 10 11 12 13 14 15 16 Fig. 2.7. Divided Draft 2.6.6 Grouped drafts These drafts are employed for the production of stripe and check designs, in which the stripes have different weaves or their combinations. This draft (Fig. 2.8) is used for producing the fabric with two different stripes. The repeat of the draft is determined by the number of stripes and the number of threads in each stripe. The number of shafts in the draft depends upon the number of stripes and the warp repeat of weave of each stripe. Woven Design Fundamentals 13 7 X X X 6 X X X 5 X X X 4 X X X 3 X X X X X 2 X X X X X 1 X X X X X 1 2 3 4 5 6 7 8 9 10 11 12 13 14 15 1 2 3 4 5 6 7 8 9 10 11 12 Fig. 2.8 Grouped draft repeat size 12 +15=27 Grouped draft 2.6.7 Combined draft Various methods of drawing in can be combined in one draft for producing a certain type of fabric. Two or more drafts described above can be applied simultaneously, for example, straight and skip or sateen, grouped and curved, and so on. Combined draft is the most complicated and can be chosen only if there are some technological or economical reasons. The designer having a great experience can do it properly. 2.7 RELATION BETWEEN DESIGN, DRAFT AND LIFTING PLAN The construction of any woven fabric depends upon the design, draft and the lifting plan and these are very closely dependent upon one another. A thorough knowledge of this interdependence is very valuable to the designer upon whose skill several mechanical limitations of the loom may be imposed. In many cases it is only his innate acquaintance with the drafting systems and the possibilities of manipulating the lifting orders which enables him to introduce variety into apparently rigid mechanical systems of operation. In normal practice the designer has to produce a range of designs for looms with a known pattern scope. This usually involves the draft and the lifting plan construction. A similar procedure is adopted when the designer is asked to reproduce a specific design from a sample. The weave in the sample is analysed and a suitable draft and lifting plan is derived. 2.8 DENTING PLAN Warp ends during weaving are spaced out across the width of the warp sheet according to the desired density by the wires of the reed. The most frequent order of density is one, two, three, four ends per dent. There are some types of fabrics, however, which require an irregular order of denting to emphasize certain design feature, and in such cases the order of arrangement of the ends in the reed becomes an essential part of the design and must be indicated carefully and in the correct relationship in respect of the weave and the draft. The various methods of indicating the denting are shown in Fig. 2.9. X X X X A X X X X X X X X 14 Fabric Structure and Design X X X B X X X C D Fig. 2.9. Various Methods of representing the Denting Plans At A, is shown a matt weave design. The different denting plans for this design are shown at B, C, and D. However the type of denting plans shown at B is most commonly used. REVIEW QUESTIONS 1. How are woven fabrics classified? 2. What are the basic elements of woven design? 3. Define the term ‘weave’. 4. Mention the practical methods of weave representation? Which one is preferred? 5. What is repeat of weave? 6. Mention the importance of design, draft and pegplan? 7. Mention the various types of drafts. 8. How does straight draft differ from other types of drafts? 9. When are skip and ‘sateen’ drafts used? 10. Mention the weaves which use pointed draft. 11. Mention the weaves which employ broken draft. 12. Give examples of weaves which use divided draft. 13. Where are grouped drafts used? 14. Under what circumstances are curved drafts used? 15. What is denting plan? EXERCISE 1. Explain the various elements of woven design with an example. 2. Explain the importance of the various types of draft plans and indicate their practical utility. Woven Design Fundamentals 15 PRACTICE 1. Check the draft and peg plans on the loom for the following weaves : (a) Plain (b) Twill (c) Pointed twill (d) Herringbone twill (e) Satin/Sateen (f) Terry Hint : The draft plan for the above weaves is to be checked on the loom weaving the particular type of fabrics. The draft plan is checked by observing the manner of drawing the warp threads through the heald wires of the heald frames and also noting the number of heald frames used for the above weaves. This should be done for one repeat. The peg plan can be checked by turning the hand wheel/index wheel of the loom by hand. The order of rising of the heald shafts is to be noted and this is the peg plan for the given design. 2. Find out the denting order on the loom for the following weaves : (a) Plain (b) Twill (c) Pointed twill (d) Herringbone twill (e) Satin/Sateen (f) Terry (g) Huck a back (h) Honey comb Hint : The order of denting in a loom is found by counting the number of warp threads drawn through a dent wire of the reed. It normally depends on the repeat size of the weave. 3 CHAPTER Plain Weaves 3.1 INTRODUCTION The plain weave is variously known as “calico” or “tabby” weave. It is the simplest of all weaves having a repeat size of 2. The range of application of this weave is wide. The plain weave has the following characteristics : (i) It has the maximum number of binding points (ii) The threads interlace on alternate order of 1 up and 1 down. (iii) The thread density is limited (iv) Cloth thickness and mass per unit area are limited. (v) It produces a relatively stronger fabric that is obtained by any other simple combination of threads, excepting that of “gauze”or “cross weaving”. The principle involved in the construction of plain cloth is the interlacement of any two continuous threads either warp or weft in an exactly contrary manner to each other, with every thread in each series passing alternately under and over consecutive threads of other series interlaces uniformly throughout the fabric. By this plan of interlacement, every thread in each series interlaces with every thread in the other series to the maximum extent, thereby producing a comparatively firm and strong texture of cloth. A complete unit of the plain weave occupies only two warp threads and two picks of weft (Fig. 3.1), which is the design for that weave. 2 X X X X 1 X X X X 2 X X X X 1 X X X X 2 X X X X 1 X X X X 2 X X X X 1 X X X X 1 2 1 2 1 2 1 2 Fig. 3.1. Plain or Tabby Weave Plain Weaves 17 3.2 TEXTURAL STABILITY OF PLAIN WEAVE IN RELATION TO OTHER WEAVES The firmness of any woven structure depends on the frequency of interlacing between the warp and weft threads. The greater the number of intersections the better will be the firmness of the cloth. Let us consider the case of two fabrics woven with identical warp and weft counts and thread settings. Consider that one is woven as plain weave and the other with any other weave such as twill, sateen etc. It will be seen that the latter will be less firm, and therefore of weaker texture than the former, because the threads composing it would be bent in a lesser degree than those of the plain weave, thereby causing them to be less firmly compacted. Thus it is important that the counts of warp and weft, the number of warp threads and picks per inch, and the weave, should be properly proportioned, in order to obtain the best results. 3.3 RANGE OF TEXTURES PRODUCED IN PLAIN WEAVES The plain weave is produced in a variety of forms and textures, possessing totally different characteristics, which adapt it for specific purposes. A variety of forms in textures are produced : (i) By causing a differential tension between the warp threads during weaving. (ii) By using various counts of yarn for weaving different types of fabrics, (iii) By using warp and weft yarns of different counts in the same fabric, The term ‘texture’ is related to type of material, counts of yarn, relative density of threads, weight, bulk, feel during handle, and other properties. The range of textures produced in plain cloth is wide. An ideal plain cloth is one which has identical or similar warp and weft constructional parameters. 3.4 END USES Plain weave finds extensive uses. It is used in cambric, muslin, blanket, canvas, dhothi, saree, shirting, suiting, etc. 3.5 MODIFICATION OF PLAIN WEAVE The plain weave may be modified by extending it warp or weft way or both. The extension of the plain weave thus produces a rib effect. A warp rib results from extending the plain weave in the warp direction and a weft rib structure results from extending the plain weave in the weft direction. A matt rib results from extending the plain weave in both directions. The chart below shows the derivatives/modifications of plain weave : Plain weave Warp rib Weft rib Matt rib Regular Irregular Regular Irregular Regular Irregular 3.6 WARP RIB WEAVES These are produced by extending the plain weave in warp wary direction. Fig 3.2 shows the warp rib weaves constructed on regular and irregular basis. 18 Fabric Structure and Design Warp rib Weave-regular Warp rib Weaves-irregular F E X X X X X X X X X X X X X X X X A X X X X B X X X X X X X X X X X X X X X X X X X X X X X X X X D X X C Fig. 3.2. Warp rib Weaves At A, B and C are seen regular warp rib weaves and at D, is shown the irregular warp rib weave. E and F show the interlacing of D and A respectively. 3.7 WEFT RIB WEAVES These are constructed by extending the plain weave in weft direction as shown in Fig. 3.3. Weft rib Weaves-regular Weft rib Weaves-irregular Plain Weaves 19 X X X X X X X X A X X X X X X X X X X X X X X X X X X B X X X X X X X X X X X X X X X X X X X X C X X X X X X X X X X X X X X X X X X X X D X X X X X X X X X X X X Fig. 3.3. Weft rib Weaves In both the warp and weft rib weaves, the appearance of the cloth depends on the respective thread settings, and to achieve good effects, it is necessary to weave a weft rib with a high number of picks per inch and a comparatively low number of ends per inch. Similarly the warp rib effect can be enhanced with a high number of ends per inch and a comparatively low number of picks per inch. The prominence of the rib can be increased by suitable use of coarse and fine yarns. The dependence of all rib constructions upon the correct thread settings is marked. The typical constructional particulars for a weft rib structure is given below: Warp - 2/14s & 36s Ends/inch - 56 Weft - 18s Picks/inch - 100 The typical constructional particulars for a warp rib structure is given below: Warp - 30s cotton Ends/inch - 126 Weft - 15s cotton Picks/inch - 38 3.8 USES Rib weaves are used in gross grain cloths, matelasse fabrics, repp cloth which is extensively employed for window blinds in railway carriages and other vehicles, upholstering furniture, and cambric picket handkerchief. 20 Fabric Structure and Design 3.9 MATT RIB WEAVES These weaves are also variously known as hopsack or basket weaves. The matt rib structures result from extending the plain weave in both directions. The regular and irregular types are shown in Fig. 3.4 matt weaves -regular matt rib weaves -irregular X X X X X X X X X X X X X X X X X X X X X X X X X X (A) (B) Fig. 3.4. Mat weaves In case of regular matt weave, the plain weaves are extended equally in the warp and weft directions, where as in case of irregular matt weaves, the plain weave is extended unevenly or irregularly in the warp and weft directions. 3.10 USES Matt weave finds extensive uses for a great variety of fabrics such as dress materials, shirtings, sail cloth, duck cloth etc. REVIEW QUESTIONS 1. Give the other names of plain weave. 2. Mention the basic characteristics of a plain weave. 3. Define the term ‘texture’. 4. Mention the end uses of plain weave. 5. Classify the plain weave. Plain Weaves 21 6. Define warp rib, weft rib, and matt rib. 7. Give the standard quality particulars for a weft rib cloth. 8. Give the other names of matt weave. 9. Give the typical constructional particulars for a warp rib structure. 10. Mention the end uses of rib weaves. 11. Give the end uses of matt weaves. EXERCISE 1. Give the design, draft and peg plan for the following : (a) 2/3 warp rib (b) 5/5 warp rib (c) 4/2 weft rib (d) 6/3 weft rib (e) 4/4 matt rib (f) 2/4 matt rib (g) 4/3 matt rib Also indicate the denting order for the above weaves. PRACTICE 1. Analyse a plain woven shirting, suiting, casement, and canvas fabric for the following constructional particulars. (a) Cloth width in cms/inches (b) Warp count and weft count (c) Ends/inch or ends/cm (d) Picks/inch or picks/cm (e) Areal density (GSM i.e. gms/metre2 ) (f) Warp and weft crimp (%) (g) Warp and weft cover factors (h) Cloth cover factor (i) Reed count 2. Analyse the following fabrics for all the constructional parameters: (a) Twill shirting (b) Pointed twill (c) Herring bone twill (d) Gaberdene (e) Denim (f) Satin/Sateen 4 CHAPTER Twill Weaves 4.1 INTRODUCTION Twill weaves are the weaves that find a wide range of application. They can be constructed in a variety of ways. The main feature of these weaves that distinguishes from other types is the presence of pronounced diagonal lines that run along the width of the fabric. The basic characteristics of twill weaves are : (i) They form diagonal lines from one selvedge to another. (ii) More ends per unit area and picks per unit area than plain cloth. (iii) Less binding points than plain cloth (iv) Better cover than plain weave (v) More cloth thickness and mass per unit area. 4.2 CLASSIFICATION OF TWILL WEAVES The twill weaves are produced in a wide variety of forms. They are however classified broadly into important categories, namely : (i) Ordinary or continuous twills (ii) Zig zag , pointed or wavy twills (iii) Rearranged twills such as satin/sateen weaves and corkscrew weaves (iv) Combination twills (v) Broken twills (vi) Figured and other related twill weaves The above types of twills are further subclassified as: (a) Warp face twills (b) Weft face twills (c) Warp and weft face twills 4.3 CONTINUOUS TWILLS 4.3.1 Warp faced twills In these types of twills the warp thread floats over all the picks in a repeat except one pick. The minimum repeat size required is 3. Examples of warp faced twills are 2/1, 3/1, 4/1, 5/1 etc. Twill Weaves 23 Some examples of warp faced twills are shown in Fig. 4.1. Fig. 4.1A, C and D show a right handed or Z twill and Fig. 4.1B shows a left handed or ‘S’ twill. 4.3.2 Weft faced twills These twills are the reverse of the previous ones. In these weaves the weft thread floats over the warp on all picks in a repeat except one. Examples of weft faced twills are 1/2, 1/3, 1/4, 1/5 etc. Some types of weft faced twills are shown in Fig. 4.2. X X X X X X X X X X X X X X X A B C D Fig. 4.2. Weft Faced Twill Fig. 4.2 B, C and D show a right handed or ‘Z’ twill and Fig. A shows left handed or ‘S’ twill. 4.3.3 Balanced and unbalanced twills In these types of twills the warp and weft floats may be equal or unequal. In other words the twills may be of the reversible or irreversible types. Accordingly they may be known as balanced and unbalanced twills. Examples of balanced twills are 2/2, 3/3, 4/4, 5/5 etc. Examples of unbalanced twills are 2/3, 4/2, 5/3 etc. The 2/2 twill is popularly known as “Gaberdene” weave. Fig. 4.3 A and B show designs for balanced and unbalanced twills and C and D show the interlacement diagrams of a 4/1 twill and 1/4 twill (warp faced) (weft faced). warp faced twill weft faced twill C D X X X X X X X X A B X X X X X X X X X X Balanced Unbalanced Fig. 4.3. Balanced and unbalanced Twill 24 Fabric Structure and Design 4.4 WARP AND WEFT FACED TWILLS In these twills the warp and weft floats may be equal or unequal with either the warp floats predominating the weft floats and vice versa. Some examples of these twills are shown in Fig. 4.4 A, B and C respectively. X X X X X X X X X X X X X X X X X X X X X X X X X X X X X X X X X X X A B C Fig. 4.4. Warp and Weft faced Twill 4.5 THE ANGLE OF TWILL The angle of twill is the angle between the diagonal twill line and an imaginary horizontal line or axis parallel to the weft. This angle is dependent on the ratio between the ends/inch and picks/inch in the cloth. When the warp ends/inch is equal to the weft picks/inch, the twill angle will be 45°. When the warp ends/inch exceeds the weft picks/inch the twill angle will be an obtuse angle i.e., >45° (high angle or steep twill). When the weft picks/inch exceeds the warp ends/inch, the twill angle will be an acute angle i.e.,