Body Repair PDF
Document Details
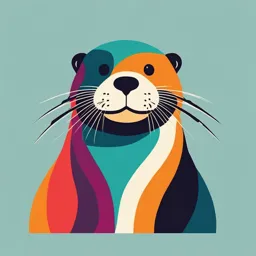
Uploaded by RenewedElder
Ghabbour
ENG/ AMR DAOUD
Tags
Summary
This document provides an overview of automotive body repair methods, covering different techniques like Paintless Dent Removal (PDR), body filler, hammering and dolly, and patching. It also explains the importance of body repair in restoring vehicle appearance, ensuring safety, preventing further damage, and restoring component function.
Full Transcript
Body Handout Unit 9: (Body Repair Methods) Definition of Body repair: -Car body repair is a process that involves repairing, restoring, and maintaining the exterior of a vehicle that may have suffered damage, scratches, dents, or other struc...
Body Handout Unit 9: (Body Repair Methods) Definition of Body repair: -Car body repair is a process that involves repairing, restoring, and maintaining the exterior of a vehicle that may have suffered damage, scratches, dents, or other structural damage. Body repair includes painting and maintenance work that aims to restore the visual appearance of the vehicle to as close to its original condition as Possible. Importance of Body repair: 1) Restoring Vehicle Appearance 2) Ensuring Safety 3) Preventing More Serious Damage 4) Restore Body Component Function ENG/ AMR DAOUD 1 1 Techniques of Body repair: If you’ve been in a car accident or even just obtained a single dent, there are several methods of auto repair used today depending on the type of damage that has occurred, and choosing the suitable method of repairing depends on the location of damage (ex: difficulty of using a certain method due to the inaccessibility to the affected area), the methods are: 1) Paintless Dent Removal (PDR) 2) Body Filler 3) Hammering and Dolly 4) Patching ENG/ AMR DAOUD 2 2 5) Bumper Repair/Replacement 6) Frame alignment. Paintless Dent removal (PDR): Paintless dent removal is a method of auto repair that can fix dents the size of a football. The type of car PDR can be used on is varied— generally 1990 models and later. Paintless dent removal is most effective when the paint has not been broken or cracked, the dent is not near the edge of the panel and the panel has not had previous body repair. The main appeal of PDR is that there is no worry of incorrect color matching, and the car actually maintains its original paint color. This technique requires patience, as the dent must be slowly massaged into its original position. However, the process can usually be completed in one day, as there is no need for multiple coats of paint to dry. ENG/ AMR DAOUD 3 3 Conditions of using Paintless Dent removal: (1) No old damage such as putty or tinning (2) The diameter of the dent is no larger than a tennis ball. (3) The dent is a maximum of 0.5 mm deep. (4) Dent has no sharp edge or point. (5) The paint surface is not damaged. Methods of Paintless Dents Removal: a) Leverage method: levers of different lengths and shapes are used for bulging, The dent is pressed from behind with these levers, therefore the dent must be accessible from behind. Tools of leverage method: i) Fluorescent tube: it makes height deviations in the body panel clearly visible. ii) Hot air gun: to heat the surface of the sheet to avoid cracks in the paint. Steps of Levering Dents: i) Mark the dent with a grease pencil ii) Align the fluorescent tube with the dent. iii) Heat the surface to approx. 25°C with the hot air gun. iv) Press the sheet metal back with the lever until it is plastically deformed. (Begin at the edge of the dent & the sheet metal have to be "over pressed" a little, because the plastic deformation) ENG/ AMR DAOUD 4 4 b) Pull method: With the pull method, the dent is pulled out again. It is applied when the dent is only accessible from the outside. Steps of Pull Method: i) adhere Hot glue on the paint surface ii) pull out The dent with a pulling hammer or pulling device iii) Remove glue with a hair dryer or a solvent Body Filler Method: Body filler is a product made of plastic resin, which makes it sandable on metal. If a car has a dent, it is not unusual for car owners to use a bit of body filler to seal the damage. The disadvantage to this method is that filler can scab off easily, making the repair not so permanent. Because of this, many auto mechanics today use more proper methods like hammering to repair a damaged car. ENG/ AMR DAOUD 5 5 Hammer and Dolly Method: The hammer and dolly method is the most effective method, and requires lots of practice and auto mechanic training in order to successfully pull off. A dolly is a flat and usually rectangular piece of metal which acts as an anvil for the hammer. With this dent repair method, the dent is sandwiched between the hammer and dolly to guide the metal back into shape. Techniques of Hammer and Dolly Method: Hammer off Dolly method: Used to raise low spots and lower high spots simultaneously, Often used to rough out or shape large areas of damage during initial straightening Hold dolly under lowest area on back of panel, then hit any area next to dolly Start at outer perimeter and work toward center Control straightening by altering how hard to hit hammer, how hard to push dolly, how far away dolly is from hammer blows Hammer on Dolly method: Hold dolly against back of damage and hammer right over top of dolly Repeatedly move point of hammer impact and dolly slightly, each blow overlapping Start at outside and work toward center Shapes of dolly and hammer must match desired shape of panel Start with light hammer blows, and work up to stronger blows ENG/ AMR DAOUD 6 6 Patching: Cars are not immune to the effects of the environment, so rot can become an issue for older vehicles where holes caused by rot will lead to a failed auto inspection, Some incorrect methods that mechanics have found car owners doing is applying body filler to, or sticking a cloth tape over the hole. Method of Patching: The proper method of repair is to weld new metal in place of the older rotting piece. Cutting out the old metal will stop the spread of rust, and welding will strengthen the metal. Neither of these methods are as effective as welding because they will not stop the spread of the rust to the rest of the car’s body Steps of Patching Body repair: X Dimension i) Determining the size of the affected area (identify the start & end point of the affected area) Y Dimension ENG/ AMR DAOUD 7 7 ii) Designing a template for the more complicated affected areas using Drawing Papers iii) Cutting the new metal to match the dimensions of the affected area and install it correctly iv) Removing the defected metal using the grinder tool or laser cutting machine v) Welding the new metal part and finishing the surface ENG/ AMR DAOUD 8 8 Bumper Repair/Replacement: Many drivers ignore minor bumper damage to save money or simply forget to get the bumper repaired. But in the long run, getting a bumper repair is the best option. Bumpers with cracks, scratches or dents can look very unsightly and can result in a safety risk, Types of Bumper Damage: - Minor Bumper Damage: and in this case, bumper can be repaired without replacement. - Major Bumper Damage: in this case, the bumper is completely damaged and needs to be replaced ENG/ AMR DAOUD 9 9 Frame alignment: There are different methods that are used for frame alignment which depends on measuring the frame in different ways as shown in the below pictures: ENG/ AMR DAOUD 10 10 ENG/ AMR DAOUD 11 11 8|Page 12 Body Handout Unit 10: (Body Analysis) Body Analysis of a vehicle ater Accidents: Accurate Body analysis of a vehicle after accidents and determining the actual size & impact of damage is a skill that comes after many trainings & experience, and in order to have the accurate analysis, fixed steps should be taken before the first visual inspection which are: - Asking the driver about: a) Speed of the vehicle at the time of the accident b) Size, shape, position and speed of the vehicles involved c) Angle and direction of movement of the vehicle at the moment of impact - Walk around the whole vehicle to recognize the extent of damage. - After this rough examination, the damage can be narrowed down and more precisely to be examined. - An assessment is made as to whether it still makes sense to repair vehicle ENG/ AMR DAOUD 1 13 Classification of Damage: Classification of damage can be according to: a) Type of Damage b) Damaged Components c) Size of Damage Types of Damage: - Old Damage: is unrepaired damage to vehicles. It is quite possible that a renewed damage affects the old damage or covers the old damage - Secondary Damage: is damage that occurs as a result of an accident. So it has to be checked which other components were damaged such as the radiator, engine, gearbox, axles, steering, Control devices, electrical lines. - Hidden Damage: is damage that cannot be seen at first glance. Therefore become during the visual inspection, e.g. in the passenger compartment and trunk, protective, insulating and Trim panels removed or lifted to avoid damage to the underbody and chassis recognizable longitudinal beams. ENG/ AMR DAOUD 2 14 Damaged Components: In any accident , the car components need to be carefully examined to identify the extent of the damage and to determine the defective beams for an accurate analysis & diagnosis, The main Components of any vehicle is classified into: a) Primary Beams: the main supporting parts of a body such as main, longitudinal and cross beams, A-, B-, C-pillars, rocker panels, strut mounts, engine, axle and gearbox mounts b) Secondary Beams: are the supporting parts. These include wheel housing, side panel, welded Mudguards, roof, bulkhead, welded end panels, small parallel longitudinal and cross members, bonded windshields. c) Paneling Parts: are the non-structural parts such as bonnet, tailgate, doors,screwed fenders and end plates, bumper ENG/ AMR DAOUD 3 15 Size of Damage: Depending on the extent of damage, The size of Damage is classified into: - Minor Damage - Small Damage - Medium Damage - Huge Damage ENG/ AMR DAOUD 4 16 - Total Loss Determining the extent of Damage: In order to determine the actual extent of damage, first , a rough examinations should be made by walking around the whole vehicle , then , there are some tests that should be held as follows: a) Visual Inspection: In this test, Both the damage and the entire vehicle are checked , making sure that the following observations are covered which are : i. the size and direction of the impact ii. the location the damage coming from iii. whether the vehicle was twisted, warped, or bent overall iv. whether damage due to just one hit, or were there multiple hits to the Body also , the following parts needs to be checked: i. Body sheet metal ii. Vehicle underside iii. Other assemblies iv. Vehicle interior ENG/ AMR DAOUD 5 17 b) Touch Test: The touch test is a supplement to the visual test. Here are areas of Body outer skin scanned; this is how the body and vehicle construction mechanic can dent or feel bumps. c) Noise Test: During the noise test, "non-typical noises" are detected that indicate a malfunction, e.g. strange noises when closing and opening a door or the pedals, also, Loose or missing attachments of body parts are also detected - they "rattle". d) Smell Test: The smell test can be used to detect leaking components, for example: 1) if exhaust gases penetrate the vehicle interior 2) if the brake fluid drips on the hot engine. 3) burned insulation of cables can also be recognized by the smell of burning e) Functional Test: Functional testing includes checking all moving body parts for their position and Mobility This applies above all to the vehicle doors, flaps, sliding roof, windows, hinges and locks ENG/ AMR DAOUD 6 18 19 Body Handout Unit 13: (Chassis Measurement) After Accidents, and after determining the extent of the damage, if the damage defects the chassis, the main step of accurate alignment is to Measure the chassis or the body frame. Importance of Chassis Measurement: The main goal of chassis alignment is to determine damage occurred as the result of the accident and to know the accurate alignment required, where the technician measure the chassis and refer it to the standard measures mentioned in the manufacturer catalogue of the vehicle and then to set up the strategy of chassis alignment. ENG/ AMR DAOUD 1 20 Types of Chassis Measurement: - Two-Dimensional Measuring method: The two-dimensional measurement is carried out with a telescopic measuring gauge. Telescopic measuring gauges are sometimes also called compasses. Note: Its more preferred to use the telescopic measuring gauge than the measuring tape due to its higher accuracy ENG/ AMR DAOUD 2 21 Concept of Measurement of the telescopic measuring gauge: - Its main concept of measuring is measuring the diagonals of the frame and comparing if there is a deviation or not. - If the deviation is more than 0.5 mm, then the frame is wrapped and must be addressed. - Distances also can be compared for symmetry; the right side of the vehicle should match the left side which is called "Left-Right Comparison". - if you compare the points of the axle attachment at the front left of the vehicle with the rear right and set there, if there are deviations, this can indicate structural damage (frame damage). Which can determine whether a repair still makes sense. ENG/ AMR DAOUD 3 22 - Three-Dimensional Measuring method: The three-dimensional measurements based on adding the measurement of the height in addition to the two-dimensional measurements, For an exact body measurement, the individual body points (length, width & height) should be measured Concept of Measurement of the three-dimensional method: - The three-dimensional is performed by placing the vehicle on a flat surface (straightening Bench) where the vehicle is firmly fixed on universal clamps Methods of three-dimensional measurement: - Mechanical measuring system - Electronic measuring system ENG/ AMR DAOUD 4 23 Main components of the Mechanical measuring system: a) Alloy Frame b) Longitudinal Slide c) Cross Slide d) Measuring cylinder e) Angle inverter. f) Centering sleeves for measuring bodies. How to measure the frame by using Mechanical measuring system? a) Prepare the reference measurement for the vehicle you need to measure from the manufacturer to identify the reference points or attachment points b) Place the vehicle on the straightening bench and make sure its firmly fixed by the universal clamps c) Use the moving measuring components in the system with its suitable function to get the accurate (length , width & height ) dimensions d) Compare the measured dimensions with the reference ones to detect any deviations. ENG/ AMR DAOUD 5 24 Main Components of Electronic measuring system: - Alloy Frame - Longitudinal Slide - Measuring Slide (Fig.A) - Computer with installed Software. (Fig.A) ENG/ AMR DAOUD 6 25 How to measure the frame by using Electronic measuring system? a) Select the type of the vehicle you need to measure from the Software to identify the reference points or attachment points. b) Place the vehicle on the straightening bench and make sure its firmly fixed by the universal clamps c) Follow the reference points and attachment points that are shown in the software with the measuring slide (Fig.A) to get the accurate (length , width & height ) dimensions d) The software will analyze the input data and will detect the deviation and point on the suitable pull locations for correct alignment. ENG/ AMR DAOUD 7 26 27 Body repair Body repair plastic unit Student Personal Information Table of Content: Student Name: Student Class: 28 Introduction Lesson 1 : Safety for body repair work shop. Safety first always select personal protective equipment( Eyewear, gloves , hearing and respiratory protection for your job & workplace. The appropriate PPE should be worn without wearing any jewelry. Keep the floor clean and free from oils or grease. Do not rest the soldering iron on anything flammable while it heats up. Do not use the grinder or welding gun without a protective mask because of the gas resulting from welding is very poisonous. 2 | Page 29 Plastic Bonding. adhesive Bonding is the process of joining two surfaces together, usually with the creation of a smooth bond. Plastic bonding uses adhesives instead of fasteners to join plastic substrates together. These substrates can be made of the same type of plastic, or they can be made of different types of plastic. Bonding can also involve joining a plastic substrate to a non-plastic material. In body and vehicle construction, adhesives are used for bonding: One-component adhesive Two-component adhesive 3 | Page 30 One component epoxy adhesive is a type of adhesive that consists of a resin and a hardener combined into a single package. Unlike two- component epoxies that require mixing before use, OCEA simplifies the bonding process by eliminating manual blending. Once applied, it cures through a chemical reaction triggered by heat, moisture, or a combination of both. This curing process transforms the adhesive into a strong and durable bond, providing excellent adhesion to various substrates. Plastic Bonding with One-component Adhesive: Which material or materials do you want to join with plastic bonding adhesives!! There are many different types of plastics, and each one has different material properties. type of plastic or, in the case of dissimilar materials, two different plastics or the plastic and the non-plastic material. Example: Apply one-component adhesive Adhere sandwich panels to the flatbed understructure Press with weights for curing 4 | Page 31 Two-component Adhesive. Which is the best Adhesive? You can back to the service Manuel to know the recommended product. clean the surfaces with a non-aggressive Before applying the adhesive make sure to clean the surfaces with a non-aggressive product or remove any dirt or release agent left from the mould. 5 | Page 32 Two-component Adhesive. Mix the mixture & Apply the adhesive. First we have to make the mixture. Usually this adhesive comes with a single-use mixer nozzle, but it can also be made by hand, with a flat stick. Apply pressure Once the piece is in the right position, we have to apply pressure (preferably with a clamp. Repair Plastic cracks with Two-component Adhesive: Step 1: Choose an Adhesive & clean the component Step 2: Grind a "V" Step 3: Mix the Adhesive Step 4: Spread the Plastic Filler Step 5: Sand and Contour Step 6: Paint 6 | Page 33 Plastic Welding Plastic welding is a welding process carried out using a technique aimed at welding two pieces of plastic. The choice of technology depends on the type of plastic to be welded, the geometry of the shape at the welding site, as well as the duration of the welding process and its financial cost. These techniques generally rely on heating. Identifying Plastic: 1- Plastic welding is done through heat and pressure. The plastic parts in the welding area and the welding rod are heated until they reach a doughy state and then pressed together. 7 | Page 34 2- Plastic welding can only be performed on thermoplastic components. The welding rod as the joining material must be made of the same thermoplastic as the component being repaired. Welding a Crack in Plastic: A crack in a plastic component can be welded using the following steps: Preparatory work Plastic welding Creating a paintable surface 8 | Page 35 1 Preparatory work Pre-clean with a high-pressure cleaner. Clean the damaged area on both sides with a plastic cleaner. Remove the edges part Drill the end of the crack with a 5mm drill bit; this prevents the crack from continuing due to tension. Tape off the front side of the component to avoid damaging the paint. Sand both surfaces (grit P 120), Chamfer the edges of the crack with a router or scraper to match the shape of the weld seam to the welding rod. 9 | Page 36 2- Plastic Welding: Use a welding iron or hot air gun as a heat source. Heat the weld seam and welding rod together until they reach a Dough condition. Press the welding rod vertically into the weld seam with uniform force. Depending on the size and location of the damaged area, reinforcement such as aluminum mesh is welded from the back. The aluminum mesh should overlap the crack by 5mm to 7mm. It is fixed with adhesive and starting from the center. 10 | P a g e 37 3- Creating a Paintable Surface: Grind the front side with a flap disc at a slow speed, grit P 120; Caution: adhesive can smear. Finish with grit P 320, then clean with a plastic cleaner. 11 | P a g e 38 Thermoplastic & thermoset. advantages Thermoplastics generally have high strength. They are lightweight materials, and they can replace metals, thus, also exhibiting a weight-saving advantage. They have relatively low processing cost. Disadvantages They have poor resistance to hydrocarbons, organic and highly polar solvents. They are not creep-resistant which leads to weakened plastic parts when exposed to long-term stress loads. Advantages Thermoset plastic parts have excellent strength attributes. Thermosets do not lose strength when they are exposed to higher temperatures. Disadvantages They also often have low tensile strength and ductility in plastic parts that require designs with thick walls. 12 | P a g e 39 Automotive glass Automotive glass is one of the structural elements designed to provide the required level of visibility and perform a protective function. Glasses protect the driver and passengers from headwinds, dust, dirt, rain and stones flying from under the wheels of other moving vehicles. Automotive glass can also be treated to include other beneficial properties such as protection from harmful infrared rays, preventing excessive heating in the car, and reducing noise. All of these properties can be incorporated into the glass to maximize comfort while driving your car Manufacturing Process 40 Manufacturing Process The production of glass is a complex process that involves a variety of steps and techniques. While the specifics of the process can vary depending on the type of glass being produced, most glass is manufactured using a similar set of basic steps as explained below: 1: Batch Mixing 2: Melting: 3: Forming 4: Cooling: 5: Inspection and cutting 6: Staking and storage Step 1: Batch mixing: The first step in the production of glass is to mix together the raw materials that will be used to create the glass. This typically involves combining silica sand, soda ash, limestone, and other materials in a large batch mixer. Step 2: Melting: Once the raw materials have been mixed together, they are then melted in a furnace at temperatures of up to 1700°C. This high temperature causes the mixture to become molten and allows it to be shaped into the desired form. Step 3: Forming: Once the glass has been melted, it can be shaped into the desired form using a variety of techniques. For example, it can be blown into a mold, rolled into sheets, or spun into fibers. Step 4: Annealing: After the glass has been shaped, it is then slowly cooled to room temperature in a process known as annealing. This helps to prevent the glass from cracking or breaking due to internal stresses. 41 Step 5: Finishing: Finally, the glass is finished to give it the desired properties and characteristics. This may involve cutting, grinding, polishing, or coating the glass, depending on its intended use Types of Glass There are many different types of glass, each with its own unique properties and characteristics. Some of the most common types of glass include: 1. Tempered glass: is a type of glass that has been treated with heat or chemicals to make it stronger and more resistant to breakage. It is often used in car windows, shower doors, and other applications where safety is a concern. Tempered automotive glass is highly effective in lowering impact- related breakage. In case the glass is hit by an external force, your safety will not be compromised as it shatters into small pieces. Tempered automotive glass is also durable and dramatically efficient in reducing noise and vibrations inside your vehicle. It also offers a clear vision for a comfortable riding experience. 42 2.Laminated glass: Laminated glass is made by sandwiching a layer of plastic between two layers of glass. It is often used in windshields, skylights, and other applications where safety and security are important Two or more sheets of either annealed or heat-treated glass are separated by a special PVB interlayer to ensure perfect adhesion between constituent elements. The interlayer is normally made of PVB (Poly Vinyl Butyral), which is a type of resin that provides strong binding, optical clarity, and toughness. Laminated automotive glass offers enhanced safety on breakage. When it breaks, the glass pieces remain stuck to the PVB interlayer and do not fall apart. When a normal glass breaks, it forms large shards which can cause serious injury. The interlayer acts as an extra layer of protection against such breakage risks. Laminated automotive glass also has a greater impact, stress, and intrusion resistance; making it significantly better than normal glass. For better security, endurance, and optical clarity, go for laminated automotive glass. 43 3.Float glass: This is the most common type of glass and is made from a mixture of soda ash, lime, and silica. It is used in everything from windows and bottles to light bulbs and phone screens. 3.Tinted Glass: Tinted glass can be made by adding metal oxides to the raw materials during the manufacturing process. This can impact the transparency and clarity of the glass, and may also increase the amount of energy needed to produce it. 44 Types of glass, properties and Applications Glass Type Properties Applications 1.Float Glass Smooth surface, uniform Windows, mirrors, table thickness tops 2.Tempered Glass High impact resistance, Shower doors, car breaks into small pieces windows, safety glass 3.Laminated Glass Safety holds together Car windshields, skylights, when shattered hurricane-resistant windows 4.Tinted Glass Reduces light and heat, Buildings located in sunny available in a variety of areas colors 5. Wired Glass Safety and fire-rated, Fire-rated doors and holds together when windows, skylights, shattered greenhouses 6. Insulated Glass Energy efficient, Windows, doors reduces heat transfer 7. Mirrored Glass Reflective surface, creates Bathrooms, dressing mirror-like effect rooms 8 Low-E Glass Energy efficient, reflects Windows, doors, heat and light insulated glass 45 When To Replace a Windshield ? We consider several factors when we decide whether to repair or replace your windshield, including the size of the crack and its location. Repairs are always preferred over a replacement because of the convenience and price. Noticing a crack on your windshield doesn't necessarily mean you'll need a replacement. As we've mentioned earlier, most windshield damage can be repaired if you take fast action. However, the following signs indicate that you may need to replace your windshield as soon as possible. Cracks are deep set and larger than 3 inches in length You have multiple cracks on your windshield that obscure your vision Your windshield is more than 5 years old, and simple repair solutions aren't as effective The adhesive bond of the vehicle windshield can be broken using: Heating wire Wire Cutting knife Heating wire method: Heating wire is inserted. The heating wire is connected to the car battery; by heating, the adhesive bond is loosened. Wire pull method: The adhesive layer is pierced, a wire is inserted, and by moving back and forth, the adhesive bond is cut Cutting knife method : cold or heated, is driven electrically or pneumatically. The oscillating movement of the cutting knife cuts through the adhesive bond 46 Types of Windshield Damage 1.Chips : Chips are the smallest and least severe category of cracks that might impact your windshield. These occur when a small object collides with your window, such as a pebble or a tiny piece of debris. Chips won't significantly impact your windshield's integrity, but they can obscure your vision depending on their location. In most cases, mechanics can repair a chip without much difficulty. 2. Bull's-eye : A wide and circular crater is the telltale sign of a Bull's-eye crack. These can often resemble larger and deeper Chip cracks. Bull's- eyes may not pose an immediate risk to your windshield, but they can gradually become deeper and wider if untreated. A Bull's-eye can become harder to repair over time, as dust and debris can seep into the impact point and weaken your windshield. 3. Starburs : Starburst cracks appear as impact points surrounded by radiating, spiderweb-like cracks. Starburst cracks can pose a great risk to your windshield's integrity and may worsen under added pressure from the wind or subsequent impacts. If this type of crack is no greater than 3 inches, it's possible to repair it. Any length above that threshold may require windshield replacement 47 4 Edge Cracks : Edge Cracks are easily identifiable due to their location; they spread from the ends of the windshield and stretch toward the center. Edge Cracks pose a severe risk to a windshield's integrity as pressure and debris can drastically hasten their spread. In most cases, only small Edge cracks are repairable. To ensure a vehicle's safety, windshield replacement is often the best option for medium to large Edge Cracks. 5.Angel Wings Angel Wings are moderately sized cracks with distinct on either side of the impact point. Angel Wings may not pose an immediate threat to your windshield's integrity, but they can worsen over time. It's normally possible to fix Angel Wing cracks with repair kits instead of replacing the entire windshield What material is used to fix car glass? It is a special adhesive known as silicone or polyurethane. Polyurethane: It is the most commonly used material to fix car glass. It has high adhesive strength and flexibility that makes it able to withstand vibrations and temperature changes. It ensures the stability of the glass and maintains its insulation from water and air. 48 Repairing vehicle windshields: If only the outer glass pane is damaged by stone chips, and the film and inner pane are undamaged, then the windshield does not always need to be replaced. In many cases, the vehicle windshield can also be repaired. Conditions necessary for the glass repair process: Attach a mirror to better observe the damage. Remove loose glass shards and dirt. Clean the surface. Place the injector over the stone chip. Use a pump to extract air from the damaged area. Resin is sucked into the cavity of the damaged area due to the vacuum. Repeat the process until the damaged area is completely filled with resin. Remove the injector and cover the repair area with protective film. Cure the resin with a UV lamp. After curing, remove the protective film. Finish the surface and clean the windshield." 49 Question bank unit 19 Put (√) or (×): 1) Active safety is an aggressive type of safety (×) 2) Brakes is an example of active safety (√) 3) Passive safety prevents any material or individuals' life losses (×) 4) Breaking point is the concept for active safety (×) 5) Side impact protection is by increasing side door strength (√) Mention 3 electronic system for active safety. 1- Reverse sensor 2- Reverse camera 3- Light sensor 4- Infrared sensor 5- Tire pressure sensor 6- Blind spot sensor mention 3 mechanical system for Active safety. 1- ABS (Anti-lock brake system) 2- EBS (Electronic brake distributer) 3- AEB (Automatic emergency brake) 4- ACC (Adaptive cruise control) 5- TCS (Traction control system) 6- ESP (Electronic stability program) Mention examples for passive safety. 1- Seatbelt 2- Airbags 3- Active head restraint Choose the correct answer: 1 - ……………………. Is an example of passive safety (seatbelt – reverse camera – light sensor) 2- …………………………………………. using crumple or crash zones to absorb crash energy (ABS – ESP – Front & rear impact protection) 50