Composite Materials and Structure-Property Relationship PDF
Document Details
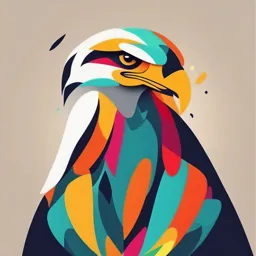
Uploaded by SolidRiver6831
TUM School of Engineering and Design
2024
Prof. Dr.-Ing. K. Drechsler
Tags
Summary
This document from TUM School of Engineering and Design covers composite materials and structure-property relationships. The text is oriented for students in 2024/2025. It delves into polymer matrix systems, mechanical properties, thermosets, and thermoplastics. The text includes diagrams and figures to help explain these concepts, including discussions on the structure and use of these materials.
Full Transcript
Composite Materials and Structure-Property Relationship 6 Polymer Matrix Systems Prof. Dr.-Ing. K. Drechsler Leo Körber, M. Sc. Nils Siemen, M. Sc. Chair of Carbon Composites TUM School of Engineering and Design Technical University of Munich 6.1. Content 6. Polymer Matrix Systems 6.1. Co...
Composite Materials and Structure-Property Relationship 6 Polymer Matrix Systems Prof. Dr.-Ing. K. Drechsler Leo Körber, M. Sc. Nils Siemen, M. Sc. Chair of Carbon Composites TUM School of Engineering and Design Technical University of Munich 6.1. Content 6. Polymer Matrix Systems 6.1. Content 6.2. Motivation 6.3. Basic Chemistry of Polymers 6.4. Mechanical Properties of Polymers 6.5. Thermoset Matrix Systems 6.6. Thermoplastic Matrix Systems 6.7. References WS 2024/25 | Composite Materials and Structure-Property-Relationship 2 Chair of Carbon Composites TUM School of Engineering and Design Technical University of Munich 6.2. Motivation 6.2.1. Classification of Composites 6.2.2. Functions of the Matrix 6.2.3. Constituent vs. Composite Stress-Strain Response WS 2024/25 | Composite Materials and Structure-Property-Relationship 3 Chair of Carbon Composites TUM School of Engineering and Design Technical University of Munich 6.2.1. Classification of Composites Composite Material Reinforcement Matrix Structure Fiber Type Polymer Metal Ceramic Continuous Discontinuous Natural Thermoplastic Short Unidirectional Organic Thermoset (0,1 – 1 mm) Long Woven / Textile Inorganic Elastomer (1 - 50 mm) Non-Woven Metal WS 2024/25 | Composite Materials and Structure-Property-Relationship 4 Chair of Carbon Composites TUM School of Engineering and Design Technical University of Munich 6.2.2. Functions of the Matrix The matrix component has the following important functions: Fixation of the fibers in the designated geometrical position Load transfer to and between the fibers (load transmission) Carrier of shear stresses and mechanical load in transverse direction to the fibers Fig. 2: Cross section through 0°/90° CFRP laminate. Joining of individual plies (ply-interface) and load transfer between plies Fiber Support of fibers for compressive loads (stability, prevention of kinking) Matrix Arrest of cracks (tough matrices) Protection of the fibers against external hazards Fig. 1: Cross section through (e.g. environmental medium, abrasion etc.) UD CFRP laminate. WS 2024/25 | Composite Materials and Structure-Property-Relationship 5 Chair of Carbon Composites TUM School of Engineering and Design Technical University of Munich 6.2.3. Constituent vs. Composite Stress-Strain Response Ef > Em Elastic modulus of fiber should be higher than modulus of matrix Rf > Rm Strength of fiber higher than matrix; otherwise no reinforcement ef < em No damage of matrix before fiber allowed; higher failure strain of matrix Carbon Fiber Stress Stress Composite Fiber Matrix Matrix , 𝜀𝑐 Strain Strain Fig. 1: Comparison of the stress-strain behavior of fiber, matrix and the composite material. WS 2024/25 | Composite Materials and Structure-Property-Relationship 6 Chair of Carbon Composites TUM School of Engineering and Design Technical University of Munich 6.2.3. Constituent vs. Composite Stress-Strain Response fiber fiber Decrease in strain Stress Stress Decrease in strain at break at break Increase of the modulus matrix matrix Strain Strain WS 2024/25 | Composite Materials and Structure-Property-Relationship 7 Chair of Carbon Composites TUM School of Engineering and Design Technical University of Munich 6.3. Basic Chemistry of Polymers 6.3.1. Definitions 6.3.2. Classification of Polyreactions 6.3.3. Molecular Weight Distribution 6.3.4. Main Polymer Types 6.3.5. Glass Transition Temperature 6.3.6. Service Temperatures of Polymers WS 2024/25 | Composite Materials and Structure-Property-Relationship 8 Chair of Carbon Composites TUM School of Engineering and Design Technical University of Munich 6.3.1. Definitions H H H H Plastic n x C C C C Polymer Processing Co-Polymer H H H H n Polymer Blend Monomer Polyreaction Repeat Unit (Ethene) (Ethylene) Polymer Compound Polymer Polymer: (πολύ poly ‚much‘ und μέρος méros ‚part‘) Monomer Molecule consisting of several repeat units. Plastics = Polymer compound or blend + additive(s) WS 2024/25 | Composite Materials and Structure-Property-Relationship 9 Chair of Carbon Composites TUM School of Engineering and Design Technical University of Munich 6.3.2. Classification of Polyreactions Polyreaction Step-growth reaction Chain-growth reaction (all components in the system (growing chain reacts only react simultaneously) with monomer) Polycondensation Polyelimination Polymerization Polyaddition anionic radical cationic insertion group transfer WS 2024/25 | Composite Materials and Structure-Property-Relationship 10 Chair of Carbon Composites TUM School of Engineering and Design Technical University of Munich 6.3.2. Classification of Polyreactions Polymerisation Monomer Polymer WS 2024/25 | Composite Materials and Structure-Property-Relationship 11 Chair of Carbon Composites TUM School of Engineering and Design Technical University of Munich 6.3.2. Classification of Polyreactions Polyaddition + Monomer A Monomer B Polymer WS 2024/25 | Composite Materials and Structure-Property-Relationship 12 Chair of Carbon Composites TUM School of Engineering and Design Technical University of Munich 6.3.2. Classification of Polyreactions Polycondensation + Monomer A Monomer B Polymer By-products WS 2024/25 | Composite Materials and Structure-Property-Relationship 13 Chair of Carbon Composites TUM School of Engineering and Design Technical University of Munich 6.3.2 Classification of Polyreaction nA + nB A-B n nM Mn Step-Growth Reaction Chain-Growth Reaction ▪ One reaction is responsible for polymer formation. ▪ Initiation, propagation and termination reactions Reaction have different rates and mechanisms. ▪ Any two molecular species present can react; ▪ The growth reaction takes place by the addition of Polymer Growth slow, random growth takes place. one unit at a time to the active end of the polymer chain. ▪ Molecular weight rises steadily throughout the ▪ High molecular weight polymer is formed rapidly. Polymer Molecular reaction. High conversion is required for high Weight molecular weight polymer. Monomer ▪ Monomer disappears in the early stages of the ▪ Monomer concentration decreases steadily Concentration During reaction. throughout the reaction. Reaction ▪ A relatively broad, calculable distribution of ▪ Mixture contains only monomer, high molecular Composition of the molecular species are present throughout the weight polymer and only about 10-8 part of growing Reaction course of the reaction. chains. WS 2024/25 | Composite Materials and Structure-Property-Relationship 14 Chair of Carbon Composites TUM School of Engineering and Design Technical University of Munich 6.3.3. Molecular Weight Distribution Not all chains have exactly the same length Polymers are polydisperse → Distribution of the molar mass within the polymer (typical molar masses in the range of: 2 ∙ 104 − 5 ∙ 106 g/mol) Long polymer chains → increase of mechanical properties Short polymer chains → improvement of processing the polymer (reduced viscosity) Molecular Weight dm/dM Fig. 1: Molecular weight distributions of Weight Percent per different polystyrene polymers with a broad distribution (solid line) and a narrow distribution (dashed line). Mn number average of molecular weight Mη viscosity average of molecular weight MW mass average of molecular weight. Molecular Weight [g/mol] WS 2024/25 | Composite Materials and Structure-Property-Relationship 15 Chair of Carbon Composites TUM School of Engineering and Design Technical University of Munich 6.3.4. Main Polymer Types – Overview (1/4) The 3 main types of polymers used as matrix system in composites Decisive is the degree of cross-linking between the polymer chains Thermosets Elastomers Thermoplastics amorphous semi-crystalline Epoxy (EP) Silicone Polyethylene terephthalate (PET) Unsaturated Polyurethane (PU) Polybutylene terephthalate (PBT) polyester resins (UP) Polyamide (PA) Vinylester resins (VE) Polyphenylene sulfide (PPS) Phenolic resins Polyether ether ketone (PEEK) WS 2024/25 | Composite Materials and Structure-Property-Relationship 16 Chair of Carbon Composites TUM School of Engineering and Design Technical University of Munich 6.3.4. Main Polymer Types – Thermosets (2/4) Quantitatively most important group of matrix systems Solid polymer via chemical reaction of two components: resin and hardener Strongly cross-linked chain molecule, 3D-network Degree of curing (cross-linking) determines mechanical properties high modulus due to dense melting not possible cross-linkage → welding not possible low creep relatively brittle, without further modifications critical as engineering high thermal and material (additives, fibers) chemical stability recycling difficult (grinding only) easy processing due to low viscosity WS 2024/25 | Composite Materials and Structure-Property-Relationship 17 Chair of Carbon Composites TUM School of Engineering and Design Technical University of Munich 6.3.4. Main Polymer Types – Elastomers (3/4) Polymer chains are weakly cross-linked Service temperature above glass transition temperature (Tg) Made from rubber materials via vulcanization very high strains ( > 100 % ) melting not possible → welding not possible reversible deformations due to low stiffness generally not usable for structural composites → no support for compressive loads recycling difficult (grinding only) WS 2024/25 | Composite Materials and Structure-Property-Relationship 18 Chair of Carbon Composites TUM School of Engineering and Design Technical University of Munich 6.3.4. Main Polymer Types – Thermoplastics (4/4) Only secondary bonds between molecules (no cross-linkage) Amorphous and semi-crystalline thermoplastics With increasing crystallinity: modulus , strength , durability , fracture toughness , shrinkage amorphous semi-crystalline Degree of crystallinity depends on cooling rate during manufacturing process meltable (reversible, several times) tendency towards creep recyclable infiltration difficult due to high viscosity weldable partly high moisture absorption (PA) → reduction of mechanical properties ideal for forming processes WS 2024/25 | Composite Materials and Structure-Property-Relationship 19 Chair of Carbon Composites TUM School of Engineering and Design Technical University of Munich 6.3.5. Glass Transition Temperature (1/2) Transition from the energy-elastic state into the entropy- Energy-Elastic Entropy-Elastic elastic state is defined as the glass transition state of the State State polymer. Storage Modulus (N/mm2) The glass transition temperature (Tg) is defined as the temperature at which the biggest change of the material properties (elastic and shear modulus etc.) occur. Glass Transition State Tg Temperature (°C) Fig. 1: The glass transition state can be observed as a change of the storage modulus with increasing temperature. WS 2024/25 | Composite Materials and Structure-Property-Relationship 20 Chair of Carbon Composites TUM School of Engineering and Design Technical University of Munich 6.3.5. Glass Transition Temperature (2/2) Change of material properties from low to high temperature Energy-Elastic Entropy-Elastic State State in the glass transition state : Increase of Storage Modulus (N/mm2) Thermal expansion coefficient Specific heat capacity Failure strain Glass Transition State Decrease of Elastic modulus and shear modulus Strength Tg Temperature (°C) Fig. 1: The glass transition state can be observed as a change of the storage modulus with increasing temperature. WS 2024/25 | Composite Materials and Structure-Property-Relationship 21 Chair of Carbon Composites TUM School of Engineering and Design Technical University of Munich 6.3.6. Service Temperatures of Polymers Service Temperature of polymers vary with the polymer type: Shear Modulus G (N/mm2) Amorphous Thermoplastics Tservice < Tg Tservice :Service Temperature (blue marker) Tg : Glass Transition Temperature (main dispersion) Tsec Tg Tsec : Secondary dispersion Temperature Tm : Melting Temperature of crystalline phase Temperature T Tdec : Decomposition Temperature Fig. 1: Service temperature regimes (blue) for amorphous thermoplastics WS 2024/25 | Composite Materials and Structure-Property-Relationship 22 Chair of Carbon Composites TUM School of Engineering and Design Technical University of Munich 6.3.6. Service Temperatures of Polymers Service Temperature of polymers vary with the polymer type: Shear Modulus G (N/mm2) Semi-crystalline Thermoplastics Tservice < Tm Tservice :Service Temperature (blue marker) Tsec Tg Tm Tg : Glass Transition Temperature (main dispersion) Tsec : Secondary dispersion Temperature Temperature T Tm : Melting Temperature of crystalline phase Fig. 1: Service temperature regimes (blue) for semi- Tdec : Decomposition Temperature crystalline. WS 2024/25 | Composite Materials and Structure-Property-Relationship 23 Chair of Carbon Composites TUM School of Engineering and Design Technical University of Munich 6.3.6. Service Temperatures of Polymers Service Temperature of polymers vary with the polymer type: Shear Modulus G (N/mm2) Elastomers Tg < Tservice < Tdec Tservice :Service Temperature (blue marker) Tg : Glass Transition Temperature (main dispersion) Tg Tdec Tsec : Secondary dispersion Temperature Temperature T Tm : Melting Temperature of crystalline phase Tdec : Decomposition Temperature Fig. 1: Service temperature regimes (blue) for elastomers. WS 2024/25 | Composite Materials and Structure-Property-Relationship 24 Chair of Carbon Composites TUM School of Engineering and Design Technical University of Munich 6.3.6. Service Temperatures of Polymers Service Temperature of polymers vary with the polymer type: Shear Modulus G (N/mm2) Thermosets Tservice < Tg Tservice :Service Temperature (blue marker) Tg Tdec Tg : Glass Transition Temperature (main dispersion) Tsec : Secondary dispersion Temperature Temperature T Tm : Melting Temperature of crystalline phase Fig. 1: Service temperature regimes (blue) for thermosets Tdec : Decomposition Temperature. WS 2024/25 | Composite Materials and Structure-Property-Relationship 25 Chair of Carbon Composites TUM School of Engineering and Design Technical University of Munich 6.3.6. Service Temperatures of Polymers Thermosets Thermoplastics 300 PEEK Service temperature [°C] 250 PF EP 200 PES 150 VE PP 100 UP 50 0 1 2 4 6 8 10 20 40 60 80100 800 Elongation at fracture[%] WS 2024/25 | Composite Materials and Structure-Property-Relationship 26 Chair of Carbon Composites TUM School of Engineering and Design Technical University of Munich 6.3.7. Additives Act as „poor solvents“ for the polymer Plasticizers Decrease the operating temperature for shaping Flame Retardant Internal extinguishers Thermal Absorb heat by decomposing into Heat Lead-organyls less reactive products Light UV-Absorbers Stabilizers Additives Mechanic Fibers Oxygen Anti-oxidants Atmosphere Moisture Hydro-phobics Color pigments, anti-shrinking, Active self-healing etc. Fillers Extenders: Fill volume lower Inactive the price Antistatic Agents Blowing Agents [madisonpolymers.com] WS 2024/25 | Composite Materials and Structure-Property-Relationship 27 Chair of Carbon Composites TUM School of Engineering and Design Technical University of Munich 6.4. Mechanical Properties of Polymers 6.4.1. Stress-Strain Behavior 6.4.2. Creep and Stress Relaxation 6.4.3. Rheology 6.4.4. Temperature and Time Dependency 6.4.5. Rheology - Measurement WS 2024/25 | Composite Materials and Structure-Property-Relationship 28 Chair of Carbon Composites TUM School of Engineering and Design Technical University of Munich 6.4.1. Stress-Strain Behavior (1/2) Monotonic Loading A: Brittle polymers, (Thermosets) B: Elastic-plastic polymers (Thermoplastics) C: Elastic polymers (Elastomers) WS 2024/25 | Composite Materials and Structure-Property-Relationship 29 Chair of Carbon Composites TUM School of Engineering and Design Technical University of Munich 6.4.1. Stress-Strain Behavior (2/2) Thermoplastic - Monotonic Loading T < Tg (1) Linear elastic Highly oriented deformation polymer structure (2) Nonlinear elastic deformation (3) (3) Necking (2) (4) Plastic deformation (4) 𝜎𝑦 : Yield Strength (1) 𝜎𝑚 : Tensile Strength WS 2024/25 | Composite Materials and Structure-Property-Relationship 30 Chair of Carbon Composites TUM School of Engineering and Design Technical University of Munich 6.4.2. Creep and Stress Relaxation Polymers do not respond according to Hook’s law. Hook’s law is only valid as an approximation for small strains at temperatures under glass transition temperature (Tg) Creep Stress Relaxation Time dependent deformation at constant load. Time dependent stress at constant initial elongation. F(t) = const. F(t) ∆l (t) ∆l (t) = const. F = const. ∆l fixed WS 2024/25 | Composite Materials and Structure-Property-Relationship 31 Chair of Carbon Composites TUM School of Engineering and Design Technical University of Munich 6.4.3. Rheology - Definition Generalized study of the deformation of materials Analogous to elasticity, includes also the viscous behavior The main fields of study of rheology are: Response of materials to mechanical loads and deformations Relations between stress, strain and strain rate Dependency with temperature and time Rheology is usually interpreted as the measurement of viscosity -> Non cured thermosets or fused thermoplastics WS 2024/25 | Composite Materials and Structure-Property-Relationship 32 Chair of Carbon Composites TUM School of Engineering and Design Technical University of Munich 6.4.3. Rheology – Viscosity (1/3) Ratio between shear stress and shear strain rate. Caused by internal friction in the fluid, inducing shear stress. 𝜏 Fig. 1: Water, η=1 mPas Fig. 2: Olive oil, η=100 mPas Fig. 3: Honey, η=10000 mPas y 𝜂= 𝛾ሶ v F 𝑣 = Velocity in x-direction [m/s] 𝑑𝑣 𝑦 = Distance in y-direction [m] 𝜏 ∝ (1) 𝑑𝑦 𝜂 = Dynamic viscosity [Pas] 𝜏 = Shear stress [Pa] y 𝑑𝑣 𝛾ሶ = Shear rate [1/s] 𝛾ሶ = (2) NEWTONIAN FLUID 𝑑𝑦 x 𝑑𝑣 𝜏=𝜂 = 𝜂𝛾ሶ (3) 𝑑𝑦 Fig. 2: Behavior of a Newtonian Fluid WS 2024/25 | Composite Materials and Structure-Property-Relationship 33 Chair of Carbon Composites TUM School of Engineering and Design Technical University of Munich 6.4.3. Rheology – Viscosity (2/3) Dynamic Viscosity Complex Viscosity Kinematic Viscosity 𝜏 ∗ 𝜏(𝑡) 𝜂 𝑚2 𝜂= 𝜂 = 𝜐= 𝛾ሶ 𝛾(𝑡) ሶ 𝜌 𝑠 v v (t) x (t) Fig. 1: Constant movement Fig. 2: Back and forth movement Heat input 𝛾ሶ = Shear rate [1/s] g 𝜌 = Density [kg/m³] 𝜂∗ = Complex viscosity [Pas] 𝜐 = Kinematic Viscosity [m²/s] 𝜂 = Dynamic viscosity [Pas] (𝑡) = Time-dependent Fig. 3: Capillary viscometer 𝜏 = Shear stress [Pa] [Mezger 2010] WS 2024/25 | Composite Materials and Structure-Property-Relationship 34 Chair of Carbon Composites TUM School of Engineering and Design Technical University of Munich 6.4.3. Rheology – Viscosity (3/3) In reality many fluids show non-newtonian behavior 𝜏 [𝑃𝑎] The viscosity of these fluids changes with the applied shear rate 𝛾ሶ [1/𝑠] For the characterization of these fluids in the lab a suitable shear rate must be chosen, which represents the shear rates occurring during processing Fig. 1: Shear stress to shear rate 𝛾[1/𝑠] ሶ Examples for Shear-thickening: corn starch in water 𝜂[𝑃𝑎 𝑠] Shear-thinning: polymer melts, blood Newtonian: water Fig. 2: Viscosity to shear rate 𝛾[1/𝑠] ሶ Newtonian Shear- thickening Shear- thinning WS 2024/25 | Composite Materials and Structure-Property-Relationship 35 Chair of Carbon Composites TUM School of Engineering and Design Technical University of Munich 6.4.3 Rheology - Measurement A Rheometer is a device able to apply torques and measure angles very precisely Different measuring systems can be used that consist of a rotating and a fixed or counter rotating geometry The substance/material to be analyzed is placed between both geometries For each measuring system, depending on the geometry, there is a relation between: The applied torque (M) and the resulting shear stress (𝜏): 𝜏 = 𝐶𝑠𝑠 𝑀 The measured angle (𝜑)/ rotational speed (n) and 60 the resulting shear strain / shear rate: γ= 𝐶 𝜑 2𝜋 𝑠𝑟 γሶ = 𝐶𝑠𝑟 𝑛 a Fig. 1: Plate-Plate Geometry, Fig. 2: Cone-Plate Geometry, Fig. 3: Double-Slit Geometry, 𝛾ሶ 𝑅 ≠ 𝑐𝑜𝑛𝑠𝑡 𝛾ሶ 𝑅 = 𝑐𝑜𝑛𝑠𝑡. 𝑅=𝑐𝑜𝑛𝑠𝑡. [Mezger 2010] WS 2024/25 | Composite Materials and Structure-Property-Relationship 36 Chair of Carbon Composites TUM School of Engineering and Design Technical University of Munich 6.4.3 Rheology - Oscillatory Measurement (1/2) Strain (Set): Stress (Measured): Complex Modulus: 𝜏 = Shear stress [Pa] 𝜏 𝑡 𝜏𝐴 𝛾ሶ = Shear rate [1/s] 𝐺∗ = = 𝑒 𝑖(𝛿) 𝑡 = Time [s] 𝜸 𝒕 = 𝜸𝑨 𝒆𝒊𝝎𝒕 𝝉 𝒕 = 𝝉𝑨 𝒆𝒊(𝝎𝒕+𝜹) 𝛾 𝑡 𝛾𝐴 = Deflection [-] γ 𝜔 = Velocity [1/s] 𝛾ሶ 𝑡 = 𝑖 𝜔 𝛾𝐴 𝑒 𝑖𝜔𝑡 Complex Viscosity: 𝛿 = Phase Shift [rad] 𝝅 𝛾ሶ 𝑡 = 𝜔 𝛾𝐴 𝑒 𝑖(𝜔𝑡+ 𝟐 ) ∗ 𝜏 𝑡 𝜏𝐴 𝑖(𝛿−𝜋) 𝝅 𝜂 = = 𝑒 2 𝒊(𝝎𝒕+ ) 𝛾ሶ 𝑡 𝛾𝐴ሶ 𝜸ሶ 𝒕 = 𝜸ሶ 𝑨 𝒆 𝟐 𝜏(𝑡) 𝛾(𝑡) 𝛾(𝑡) ሶ 𝜏(𝑡) 𝛾(𝑡) 𝛾(𝑡) ሶ 𝜋 [Mezger 2010] Fig. 1: Ideal viscous behaviour 𝛿 = = 90° Fig. 2: Ideal elastic behaviour δ = 0 2 WS 2024/25 | Composite Materials and Structure-Property-Relationship 37 Chair of Carbon Composites TUM School of Engineering and Design Technical University of Munich 6.4.3 Rheology - Oscillatory Measurement (2/2) Complex Viscosity h* Complex shear modulus G* 𝜏(𝑡) 𝜏(𝑡) Definition 𝜂∗ = 𝐺∗ = 𝛾(𝑡) ሶ 𝛾 (𝑡) Characteristic for elastic behaviour h‘‘ G‘ (Storage Modulus) Characteristic for viscous behaviour h‘ G‘‘ (Loss Modulus) 𝜏𝐴 sin 𝛿 𝐺 ′′ 𝜏𝐴 cos 𝛿 𝐺′ Conversion 𝜂′ = = 𝜂 ′′ = = 𝛾𝐴 𝜔 𝜔 𝛾𝐴 𝜔 𝜔 Absolute value 𝜂∗ = 𝜂 ′ 2 + 𝜂 ′′ 2 𝐺∗ = 𝐺 ′ 2 + 𝐺 ′′ 2 Fig. 1: Relations between the complex shear modulus and the complex viscosity Im h‘ Re Im h‘‘ d h* G* 𝐺′ = Storage Modulus [Pa] G‘‘ 𝐺 ′′ = Loss Modulus [Pa] tan 𝛿 = Loss Factor d G‘ Re [Mezger 2010] Fig. 2: Imaginary and real part of the Fig. 3: Imaginary and real part of the complex viscosity complex shear modulus WS 2024/25 | Composite Materials and Structure-Property-Relationship 38 Chair of Carbon Composites TUM School of Engineering and Design Technical University of Munich 6.4.3 Rheology - Summary Viscoelasticity Viscous Visco-elastic Elastic Ideal viscous Viscous-elastic Transition Viscous-elastic Ideal elastic (Gel-Point) or solid 𝛿 = 90° 90° > 𝛿 > 45° 𝛿 = 45° 45° > 𝛿 > 0° 𝛿 = 0° tan 𝛿 → ∞ tan 𝛿 > 1 tan 𝛿 = 1 tan 𝛿 < 1 tan 𝛿 → 0 𝐺′ → 0 𝐺 ′′ > 𝐺 ′ 𝐺 ′ = 𝐺 ′′ 𝐺 ′ > 𝐺 ′′ 𝐺 ′′ → 0 Fig. 1: Different states of fluids and solids [Mezger 2010] WS 2024/25 | Composite Materials and Structure-Property-Relationship 39 Chair of Carbon Composites TUM School of Engineering and Design Technical University of Munich 6.4.3. Rheology - Models (1/4) 𝐸 𝜎 Hook Model 𝜎 𝜎, 𝜀 𝜀 𝜎 Spring 𝜎 = const Elastic behavior Does not describe creep (constant load of the spring results on a constant and immediate deformation) Fig. 1: Elastic behavior of a spring 𝑡 𝜂 𝜎 𝜎 𝜎 𝜀 Newton Model 𝜎, 𝜀 Damper 𝜎 = const Viscous behavior Does not describe elasticity Fig. 2: Creep behavior of damper 𝑡 WS 2024/25 | Composite Materials and Structure-Property-Relationship 40 Chair of Carbon Composites TUM School of Engineering and Design Technical University of Munich 6.4.3. Rheology - Models (2/4) Maxwell Model 𝜎 𝜎, 𝜀 𝜀 Spring and damper in serial connection Elastic plastic behavior 𝜎 = const Usable to describe stress relaxation Does not describe creep recovery (after releasing the load, only elastic part of the deformation is recovered) 𝑡 Fig. 1: Creep and creep recovery behavior of the Maxwell Approximation for polymer melts element. 𝜎, 𝜀 𝜎 𝜎0 𝜀 𝜂 𝐸 𝜎 𝜎 𝑡 Fig. 2: Stress relaxation of the Maxwell element. WS 2024/25 | Composite Materials and Structure-Property-Relationship 41 Chair of Carbon Composites TUM School of Engineering and Design Technical University of Munich 6.4.3. Rheology - Models (3/4) Voigt-Kelvin Model Spring and damper are parallel Usable to describe creep Does not describe stress relaxation (constant deformation would reduce the model to Hook’s law) Approximation for ideal elastomers 𝜎 𝜂 𝜎 = const 𝜀 𝜎, 𝜀 𝜎 𝜎 𝜎 𝜀= 𝐸 𝑡 𝐸 Fig. 1: Creep and creep recovery behavior of the Voigt-Kelvin element. WS 2024/25 | Composite Materials and Structure-Property-Relationship 42 Chair of Carbon Composites TUM School of Engineering and Design Technical University of Munich 6.4.3. Rheology - Models (4/4) 4-Parameter (Burger) Model Serial configuration of Maxwell Model and Voigt-Kelvin Model Good approximation for real polymers → More complex combinations of these models are used to simulate a more realistic mechanical response of a polymeric material. 𝜎, 𝜀 𝜂1 𝜂2 𝐸2 𝜎 𝜎 𝑡 𝐸1 Fig. 1: Creep and creep recovery behavior of the Burger element. WS 2024/25 | Composite Materials and Structure-Property-Relationship 43 Chair of Carbon Composites TUM School of Engineering and Design Technical University of Munich 6.4.4. Temperature and Time Equivalence Increasing the deformation rate has a similar effect as reducing the temperature Failure strength increases with increasing strain rate Failure strength increases with decreasing temperature → This effect is known as the Time-Temperature equivalence Fig. 1: Temperature and strain rate sensitivity of polymethyl methacrylate (PMMA). WS 2024/25 | Composite Materials and Structure-Property-Relationship 44 Chair of Carbon Composites TUM School of Engineering and Design Technical University of Munich 6.5. Thermoset Matrix Systems 6.5.1. Curing of a Thermoset 6.5.2. Rheology of Thermosets 6.5.3. Commonly used Thermoset Resin Systems 6.5.4. Epoxy Resins 6.5.5. Curing Agent 6.5.6. Post Curing WS 2024/25 | Composite Materials and Structure-Property-Relationship 45 Chair of Carbon Composites TUM School of Engineering and Design Technical University of Munich 6.5.1. Curing of a Thermoset (a) Start of curing with monomer stage (b) Linear growth and branching of molecules (~50% degree of curing) (c) Formation of gelled but incompletely cross-linked network (d) Fully cured thermoset polymer Fig. 1: Curing of a thermoset polymer. WS 2024/25 | Composite Materials and Structure-Property-Relationship 46 Chair of Carbon Composites TUM School of Engineering and Design Technical University of Munich 6.5.1. Curing of a Thermoset [Ellis 1993] Fig. 1: Overview of mechanisms during the processing of resin systems WS 2024/25 | Composite Materials and Structure-Property-Relationship 47 Chair of Carbon Composites TUM School of Engineering and Design Technical University of Munich 6.5.2. Rheology of Thermosets Pot life: Time where no apparent curing occurs and the resin can be used for infiltration Gel Point: The branched structures extend throughout the whole sample. Some molecules are still dissolved in the network structure. Point in time where the storage and loss modulus are equal. Rheological behavior is relevant for processing: viscosity determines infiltration/impregnation time Darcy’s law 𝑢ത = Velocity field 𝐾ധ = Permeability tensor ന 𝐾 = Viscosity 𝜇 𝑢ത = − 𝛻𝑃 = Pressure gradient 𝜇 𝛻𝑃 WS 2024/25 | Composite Materials and Structure-Property-Relationship 48 Chair of Carbon Composites TUM School of Engineering and Design Technical University of Munich 6.5.2. Rheology of Thermosets Resulting viscosity curve of the matrix system Viscosity Physical viscosity reduction due to temperature increase chemical cross- in the resin linking time WS 2024/25 | Composite Materials and Structure-Property-Relationship 49 Chair of Carbon Composites TUM School of Engineering and Design Technical University of Munich 6.5.3. Commonly used Thermoset Resin Systems Unsaturated polyester resins (UP) Unsaturated polyester are built by polycondensation of saturated and unsaturated organic- acids like di-carbon-acid and di-alcohol (di-ole) High E-Modulus, shore-hardness and heat- and chemical-resistance A wide meshed network leads to high flexibility and good impact resistance. Vinyl ester resins (VE) Instead of unsaturated poly-esters, vinyl-ester can be used Resin with advanced impact resistance Polyimides (PI) Polycondensation reaction and polyaddition reaction High mechanical strength in a high temperature range (up to 240°C, short-time at 360°C) Good abrasion resistance Epoxy resins (EP) Polyaddition/copolymerisation reaction with a multifunctional curing agent WS 2024/25 | Composite Materials and Structure-Property-Relationship 50 Chair of Carbon Composites TUM School of Engineering and Design Technical University of Munich 6.5.4. Epoxy Resins Epoxy resins are mostly used in highly stressed composite parts in aerospace and automotive applications. Low shrinkage during curing → manufacturing of O dimensionally accurate parts Excellent fiber matrix adhesion CH CH2 Good fatigue strength Fig. 1: Epoxy group. Excellent electrical isolating properties More expensive than UP-resins Curing times can be longer than for UP-resins (optimization with activators) Toxic → employment protection is necessary [directindustry.com] WS 2024/25 | Composite Materials and Structure-Property-Relationship 51 Chair of Carbon Composites TUM School of Engineering and Design Technical University of Munich 6.5.4. Epoxy Resins Curing Reaction of Epoxies WS 2024/25 | Composite Materials and Structure-Property-Relationship 52 Chair of Carbon Composites TUM School of Engineering and Design Technical University of Munich 6.5.5. Curing Agent (1/2) The curing agent (hardener) is no catalyst but a reaction partner for the epoxy resin. The curing agent builds a network with the thermoset polymer, thus the amount of the resin and curing agent must have a stoichiometric ratio (mixing ratio). One-component resins systems already have a dosed amount of curing agent in the resin which is activated by heating up the resin system. Resin Curing agent Fig. 1: Mixing of resin and curing agent with stoichiometric ratio. WS 2024/25 | Composite Materials and Structure-Property-Relationship 53 Chair of Carbon Composites TUM School of Engineering and Design Technical University of Munich 6.5.5. Curing Agent (2/2) Influence of Mixing Ratio on Material Properties The mixing ratio of epoxy resin and hardener (here Amine) influences significantly the mechanical and thermal properties of the cured thermoset. 1 pph = 1 part amine per 100 part epoxy Fig. 1: Glass transition temperature as a function of amine Fig. 2: Flexural storage modulus (DMA) at 110°C as a function of content for the epoxy resin EPON 828-PACM 20. amine content for the epoxy resin EPON 828-PACM 20. WS 2024/25 | Composite Materials and Structure-Property-Relationship 54 Chair of Carbon Composites TUM School of Engineering and Design Technical University of Munich 6.5.6. Post Curing The degree of cure strongly influences the mechanical properties of the resin system. Post-curing Temperature Post-curing Temperature woven fabric woven fabric Tensile strength [MPa] Young´s modulus [MPa] fleece fleece neat resin neat resin Degree of cure [%] Degree of cure [%] Fig. 1: Tensile strength of UP-Resin Palatal® A 420-01 Fig. 2: Young’s modulus of UP-Resin Palatal® A 420-01 at different post-cure temperatures. at different post-cure temperatures WS 2024/25 | Composite Materials and Structure-Property-Relationship 55 Chair of Carbon Composites TUM School of Engineering and Design Technical University of Munich 6.6. Thermoplastic Polymers 6.6.1. Thermoplastics vs. Thermosets 6.6.2. Challenges for Thermoplastic Composite Materials 6.6.3. Classification of Thermoplastic Polymers 6.6.4. Polymer Structures and Crystallinity 6.6.5. Influence of Temperature 6.6.6. Rheology of Thermoplastics 6.6.7. Moisture Absorption 6.6.8. Applications of Fiber Reinforced Thermoplastics WS 2024/25 | Composite Materials and Structure-Property-Relationship 56 Chair of Carbon Composites TUM School of Engineering and Design Technical University of Munich 6.6.1. Thermoplastics vs. Thermosets Thermosets are predominantly used in Shelf Life carbon reinforced plastics but the dominance is permanently declining due to several advantages of Fast Recycling thermoplastic matrices: Processing Thermoplastic Composites Fracture Thermo- Thoughness forming Weldable WS 2024/25 | Composite Materials and Structure-Property-Relationship 57 Chair of Carbon Composites TUM School of Engineering and Design Technical University of Munich 6.6.2. Challenges for Thermoplastic Composite Materials Difficulty of fiber impregnation PP: η≈138 Pas Epoxy-Resin: η≈0.7 Pas High temperature stability of thermoplastics tools and moldings PEEK Tm: 334 °C PA Tm: 180-260°C Creep Moisture absorption Compatibility of fiber sizing and matrix material WS 2024/25 | Composite Materials and Structure-Property-Relationship 58 Chair of Carbon Composites TUM School of Engineering and Design Technical University of Munich 6.6.3. Classification of Thermoplastic Polymers Increase in Volume (t/year) PI Price and Performance PEI PEEK Specialty PES PTFE Polymers PVDC PA11 PA12 PVDF PPS PC PPO/PS POM Engineering ASA PET Plastics SMA ABS PMMA PA6 PA6,6 SAN PP Commodity PVC, PS PE-LD PE-HD Plastics Amorphous Semi-Crystalline WS 2024/25 | Composite Materials and Structure-Property-Relationship 59 Chair of Carbon Composites TUM School of Engineering and Design Technical University of Munich 6.6.4. Polymer Structure and Crystallinity (1/4) Amorphous Example: PMMA, PS, PC, PVC Usage below Tg Transparent (glassy) Fig. 1: Amorphous thermoplastic. Semi-crystalline Example: PE, PP, PBT, PET Usage below Tmelt Opaque Fig. 2: Semi-crystalline thermoplastic. WS 2024/25 | Composite Materials and Structure-Property-Relationship 60 Chair of Carbon Composites TUM School of Engineering and Design Technical University of Munich 6.6.4. Polymer Structure and Crystallinity (2/4) Spherulites Fig. 1: Transmission electron micrograph showing Fig. 2: Schematic drawing of a spherulite structure in the spherulite structure in a natural rubber semi-crystaline polymers. specimen. Chain-folded lamellar crystallites (white lines) approximately 10 nm thick extend in radial direction from the center (15,000x). WS 2024/25 | Composite Materials and Structure-Property-Relationship 61 Chair of Carbon Composites TUM School of Engineering and Design Technical University of Munich 6.6.4. Polymer Structure and Crystallinity (3/4) Impact of the degree of crystallinity on the mechanical properties : Increase of Decrease of ▪ Melting temperature ▪ Impact resistance ▪ Tensile strength ▪ Failure strain ▪ Elastic modulus ▪ Mechanical dampening ▪ Hardness ▪ Thermal expansion ▪ Resistance against solvents ▪ Moisture absorption WS 2024/25 | Composite Materials and Structure-Property-Relationship 62 Chair of Carbon Composites TUM School of Engineering and Design Technical University of Munich 6.6.4. Polymer Structure and Crystallinity (4/4) Relation of the Molecular Structure and the Material Properties Primary Bond gives Bonding to other Type of molecule Molecular shape Molecular size Molecular order molecules (chemical) influences influences influences influences influences gives Secondary Bond influences results in Crystallinity influences Mechanical and Solubility and Chemical and Density thermal properties moisture uptake electrical properties WS 2024/25 | Composite Materials and Structure-Property-Relationship 63 Chair of Carbon Composites TUM School of Engineering and Design Technical University of Munich 6.6.5. Influence of Temperature a) Amorphous thermoplastics are used under Tg where the material is brittle. Above Tg the polymer melts and can be thermoformed. At even higher temperatures the polymer degrades. Semi-crystalline thermoplastic polymers are used below Tm. b) Above Tg the amorphous regions in the polymer structure are moveable without solving the entanglements. The material is in this temperature region very tough. Fig. 1: Strength and elongation of amorphous (a) and semi-crystalline (b) thermoplastics as a function of temperature. WS 2024/25 | Composite Materials and Structure-Property-Relationship 64 Chair of Carbon Composites TUM School of Engineering and Design Technical University of Munich 6.6.6. Rheology of Thermoplastics (1/3) Shear viscosity of thermoplastics very high due to high molecular weight Influencing factors: molecular weight, temperature, pressure, fillers and additives 1,0E+03 Molecular Pressure weight Filler Complex viscosity [Pa s] Additives 1,0E+02 Oscillatory measurement of Temperature polyamide 6 at 260°C 1,0E+01 1,0E-02 1,0E-01 1,0E+00 1,0E+01 Shear rate [s-1] WS 2024/25 | Composite Materials and Structure-Property-Relationship 65 Chair of Carbon Composites TUM School of Engineering and Design Technical University of Munich 6.6.6. Rheology of Thermoplastics (2/3) Thermoplastic melts show non-Newtonian behavior: viscosity decreases with increasing shear rates Viscosity of thermoplastics lowers with increasing temperature: 1,0E+03 η0 = 278 Pas Oscillatory measurement of Complex viscosity [Pa s] polyamide 6 at 260°C - 47% Oscillatory measurement of 1,0E+02 η0 = 147 Pas polyamide 6 at 270°C Oscillatory measurement of polyamide 6 at 280°C 1,0E+01 3,0E-02 3,0E-01 3,0E+00 Shear rate [s-1] WS 2024/25 | Composite Materials and Structure-Property-Relationship 66 Chair of Carbon Composites TUM School of Engineering and Design Technical University of Munich 6.6.6. Rheology of Thermoplastics (3/3) Thermoplastic melts should be characterized at shear rates occurring during processing due to non-Newtonian behavior Typical thermoplastic processing conditions e.g. injection molding/extrusion involve high shear rates Other processes such as double-belt pressing or thermoforming involve low shear rates Various rheometers applicable for different shear rates [TU Dresden] WS 2024/25 | Composite Materials and Structure-Property-Relationship 67 Chair of Carbon Composites TUM School of Engineering and Design Technical University of Munich 6.6.7. Moisture Absorption Water Absorption Tensile strength pure 35% GF pure 35% GF pure 35% GF ] humid dried Relative Moisture WS 2024/25 | Composite Materials and Structure-Property-Relationship 68 Chair of Carbon Composites TUM School of Engineering and Design Technical University of Munich 6.7. Typical Thermoplastic Matrices for Composites 6.7.1 Classification of Thermoplastic Polymers 6.7.2 Polypropylene (PP) 6.7.3 Polyamide (PA) 6.7.4 Polyphenylene Sulfide (PPS) 6.7.5 Polyether Ether Ketone (PEEK) 6.7.6 Polyetherimide (PEI) 6.7.7 Polyether Sulfone (PES) WS 2024/25 | Composite Materials and Structure-Property-Relationship 69 Chair of Carbon Composites TUM School of Engineering and Design Technical University of Munich 6.7.2 Polypropylene (PP) CH3 CH3 H3C n Semi-crystalline Tg of -10 °C – 0°C Fig. 1: GM and Fiat group pedal carrier made of 30% short glass fiber reinforced Melting temperature 165°C PP [BOREALIS]. Minor moisture absorption Commonly used with glass fibers or glass mat Automotive applications: Bumpers, front ends, seat shells, underbody panels, instrument panels Fig. 2: VW Golf Foamed Instrument Panel Carrier made of 20% glass fiber reinforced PP [BOREALIS]. WS 2024/25 | Composite Materials and Structure-Property-Relationship 70 Chair of Carbon Composites TUM School of Engineering and Design Technical University of Munich 6.7.3 Polyamide (PA) O CH3 H3C NH n Semi-crystalline Fig. 1: Trail bike wheel (Tag Wheels FRX5) made of injection molded DuPont™ Zytel® 8018 PA66 with 15% glass fibers Tg ~ 60°C [TAG Wheels]. Melting Temperature: 180-260°C Characteristic: amide-group Most common PA 6.6, PA 6, PA 12 Reversible moisture uptake in amorphous parts Fig. 2: Back injection-molded airbag housing made of a nylon 6 sheet with 47% continuous glass overmolded with a nylon 6 containing 40% short glass fibers. [KraussMaffei, LanXess, Bond Laminates, Takata] WS 2024/25 | Composite Materials and Structure-Property-Relationship 71 Chair of Carbon Composites TUM School of Engineering and Design Technical University of Munich 6.7.4 Polyphenylene Sulfide (PPS) S CH3 H3C n Semi-crystalline Tg of 95°C Melting point at 275°C Good resistance to aggressive fluids such as fuels and Skydrol hydraulic fluid Fig. 1: G650 rudder made of Fig. 2: Booster demonstrator for carbon/PPS [FOKKER]. Ariane 6 [LCC]. WS 2024/25 | Composite Materials and Structure-Property-Relationship 72 Chair of Carbon Composites TUM School of Engineering and Design Technical University of Munich 6.7.5 Polyether Ether Ketone (PEEK) O CH3 H3C O O n Fig. 1: Bracket of A350 cabin doors made of a fiber reinforced PEEK composite Semi-crystalline material [AIRBUS Helicopters]. Degree of crystallinity: 25-40 % Tg of 143°C High melting point of 334°C Excellent mechanical properties Outstanding chemical resistance properties that are retained to high temperatures Low water absorption Drawback: High costs > 30 €/kg Fig. 2: Fuselage panel demonstrator made with carbon fiber/PEEK prepreg [FOKKER]. WS 2024/25 | Composite Materials and Structure-Property-Relationship 73 Chair of Carbon Composites TUM School of Engineering and Design Technical University of Munich 6.7.6 Polyetherimide (PEI) O O O H3C N O CH3 HN CH3 O O n Amorphous Fig. 1: Wheel made of carbon/PEI [SABIC, Kringlan Composites]. Usage up to 170°C Low smoke emission Retains 47 % strength retention at 190°C Tough resin like PES Easier to process than PES or PEEK Good chemical resistance Soluble in partially halogenated solvents Fig. 2: Rudder trailing edge made of carbon/PEI. The laminate is folded in the middle by hot wire heating. WS 2024/25 | Composite Materials and Structure-Property-Relationship 74 Chair of Carbon Composites TUM School of Engineering and Design Technical University of Munich 6.7.7 Polyether Sulfone (PES) O O H3C O S O S O OH O n Usage up to 200°C for > 1000 h without loss of strength and negligible changes in dimensions. Low flammability Softening temperature 220°C Water absorption of 0.15 % at RH Tough resin Good chemical resistance Fig. 1: PES thermoplastic foam for heat-resistant structures in aircraft Incorporation in epoxy resin systems as toughener interior applications. [DIAB] WS 2024/25 | Composite Materials and Structure-Property-Relationship 75 Chair of Carbon Composites TUM School of Engineering and Design Technical University of Munich 6.8. Comparison to Other Materials (1/2) [MPa] [g/cm³] [MPa] [g/cm³] 8 6000 3000 7 5000 2500 6 4000 5 2000 4 3000 1500 3 2000 1000 2 1000 500 1 0 0 0 Density Tensile Strength Specific Tensile Strength WS 2024/25 | Composite Materials and Structure-Property-Relationship 76 Chair of Carbon Composites TUM School of Engineering and Design Technical University of Munich 6.8. Comparison to Other Materials (2/2) [GPa] [g/cm³] [GPa] [g/cm³] 8 500 250 7 400 6 200 5 300 150 4 3 200 100 2 100 50 1 0 0 0 Density Tensile Modulus Specific Tensile Modulus WS 2024/25 | Composite Materials and Structure-Property-Relationship 77 Chair of Carbon Composites TUM School of Engineering and Design Technical University of Munich 6.9. References P. Eyerer, T. Hirth, P. Elsner - Polymer Engineering (2008), ISBN: 978-3-540-72402-5 H. Schürmann - Konstruieren mit Faser-Kunststoff-Verbunden (2007), ISBN: 978-3-540-72189-5 W.D. Callister, D.G. Rethwisch - Materials Science and Engineering (2006), ISBN: 0-471-73696-1 J. Richeton, S. Ahzi, K.S. Vecchio, F.C. Jiang, R.R. Adharapurapu, Int. J. Solids Struct. 43 (2006) 2318-2335 M. Flemming, G. Ziegmann, S. Roth – Faserverbundbauweisen (1995), ISBN: 3-540-58645-8 M.R. Vanlandingham, R.F. Eduljee, J.W. Gillespie Jr., J. Appl. Polym. Sci. 71 (1999) 699–712 R.B. Prime, Thermal characterization of polymer materials, Academic Press, New York (1982) 435–569 G.W. Ehrenstein, E. Bittmann – Duroplaste Aushärtung Prüfung Eigenschaften (1997), ISBN: 3-446-18917-3 W. Weißbach, Werkstoffkunde, Friedr. Vieweg & Sohn Verlag GWV Fachverlage GmbH, Wiesbaden, 2007 G. Menges, E. Haberstroh, W. Michaeli, E. Schmachtenberg, Menges Werkstoffkunde Kunststoffe (2011), ISBN: 3446427627 Baur, Brinkmann, Osswald, Schmachtenberg, Saechtling Kunststoff Taschenbuch (2007) ISBN: 978-3-446-40352-9 H. Domininhaus, Die Kunststoffe und ihre Eigenschaften (2005), ISBN: 3-540-21410-0 WS 2024/25 | Composite Materials and Structure-Property-Relationship 78 Chair of Carbon Composites TUM School of Engineering and Design Technical University of Munich 6.9. References https://www.researchgate.net/figure/Crosslinking-reaction-between-the-epoxide-ring-and-the-primary-amine_fig2_230641818 [accessed 24 Nov, 2019] WS 2024/25 | Composite Materials and Structure-Property-Relationship 79