Composite Materials PDF
Document Details
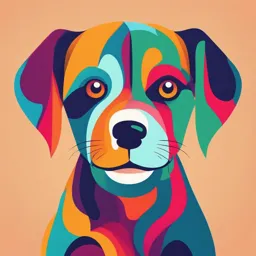
Uploaded by AffectionateConstellation1690
Dr. ir. Sina N. Dezfuli
Tags
Summary
This document provides an overview of composite materials, discussing their types, components, properties, manufacturing, and applications in various industries. It covers topics such as fiber-reinforced composites, polymer matrix composites, and metal matrix composites.
Full Transcript
COMPOSITE MATERIALS PM1T2 Dr. ir. Sina N. Dezfuli What is a composite? A composite material is formed by combining two or more materials, which may or may not have significantly different physical or chemical properties. In this combination, the resulting material manifests characterist...
COMPOSITE MATERIALS PM1T2 Dr. ir. Sina N. Dezfuli What is a composite? A composite material is formed by combining two or more materials, which may or may not have significantly different physical or chemical properties. In this combination, the resulting material manifests characteristics that are distinct from those of its individual components. Notably, in a composite, the constituent materials are not fully blended into a single homogeneous entity. Instead, each component remains individually recognizable and maintains its own identity within the final structure. This aspect of composites, where the constituents are both separate and identifiable, contributes to the unique properties of these materials. Key Components of composites 1. Matrix: This is the 'binder' or 'container' part of the composite. It holds the reinforcement material in place and helps to distribute load among the fibers. Common matrix materials include polymers, metals, and ceramics. 2. Reinforcement: This gives the composite its strength and rigidity. It's usually stronger and stiffer than the matrix, and it's typically in the form of fibers. Examples include glass, carbon, or Kevlar fibers. Figure 1. General illustration of the microstructure of a two-phase composite Types of Composites 1. Fiber-Reinforced Composites: These are made of a matrix reinforced with fibers. They can be further classified into:  Glass Fiber-Reinforced Polymer (GFRP): Used in boat hulls, sports equipment.  Carbon Fiber-Reinforced Polymer (CFRP): Used in aerospace, high-performance vehicles. 2. Particle-Reinforced Composites: These have a matrix filled with particulate matter. Examples include concrete (cement matrix with aggregate particles) and some types of dental fillings. 3. Laminar Composites: Made by stacking layers of different materials. Plywood is a common example. Figure 2. Types of composites 1. Polymer Matrix Composites (PMC) Polymer Matrix Composites consist of a polymer-based (e.g.,epoxy resin) as the matrix that is reinforced with fibers or particles (like glass, carbon, or aramid). The polymer matrix binds the reinforcement together, providing shape and protecting it from environmental exposure and damage. PMCs are known for their light weight, high strength, and resistance to corrosion. Figure 3. Illustration of polymer matrix composites Polymer matrix composites (PMCs) are widely used in various industries due to their unique properties, such as high strength-to-weight ratio, corrosion resistance, and flexibility. Here are some real-life examples of PMCs along with their applications: Carbon Fiber Reinforced Polymer (CFRP): 1. Composition: Carbon fiber composites consist of carbon fibers, which are long, thin strands of material composed mostly of carbon atoms. These fibers are embedded in a polymer matrix, typically epoxy resin. 2. Properties:  High Strength and Low Weight: Carbon fibers are extremely strong and stiff yet lightweight. This makes the composite ideal for applications where strength-to-weight ratio is crucial.  Thermal and Electrical Conductivity: Carbon fibers also have good thermal and electrical conductivity.  Corrosion Resistance: They are resistant to corrosion, which is a significant advantage over metals. 3. Manufacturing Processes:  Lay-Up Method: Layers of carbon fiber cloth are laid into a mold and then coated with resin.  Pultrusion: Continuous fibers are pulled through a resin bath and then through a heated die to form a continuous profile. 4. Advantages:  Superior strength-to-weight ratio.  Good fatigue resistance. 5. Disadvantages:  High cost of production.  Limited impact resistance. 6. Applications:  Aerospace Industry: Used in the manufacturing of aircraft components such as wings, fuselage sections, and tail units due to its high strength and low weight. Examples include the Boeing 787 Dreamliner and Airbus A350, which use CFRP extensively to reduce weight and increase fuel efficiency.  Automotive Industry: High-performance and luxury cars like those from Ferrari and Lamborghini use CFRP for body panels and structural components to enhance performance and fuel efficiency.  Sports Equipment: Used in making lightweight and strong sporting goods like tennis rackets, golf clubs, and bicycles. Brands like Trek and Specialized produce carbon fiber bicycles. Glass Fiber Reinforced Polymer (GFRP): 1. Composition: Glass fiber composites consist of glass fibers embedded in a polymer matrix. The glass fibers are made from fine strands of glass and are available in various forms like E- glass, S-glass, etc. 2. Properties: a. High Strength: Good tensile strength, though not as high as carbon fibers. b. Flexibility: More flexible than carbon fibers. c. Electrical Insulation: Excellent electrical insulating properties. 3. Manufacturing Processes: a. Filament Winding: Continuous glass fibers are wound around a form after being coated with resin. b. Hand Lay-Up: Similar to carbon fiber but using glass fiber mats or cloths. 4. Advantages: a. Lower cost than carbon fiber composites. b. Good impact resistance. 5. Disadvantages: a. Heavier than carbon fiber. b. Lower strength-to-weight ratio. 6. Applications a. Building and Construction: Used in the construction of bridges, roofing, and panels due to its strength and durability. For example, GFRP rebars are used as a corrosion- resistant alternative to steel in reinforced concrete. b. Marine Applications: GFRP is used in boat hulls, masts, and sails due to its resistance to water and corrosion. Many modern yachts and small boats are made from GFRP. c. Automotive Industry: Used for making body panels and components in cars to reduce weight while maintaining strength. Figure 4. Illustration of Glass and Carbon fiber reinforced polymer matrix composite Aramid Fiber Composites: d. Ballistic Protection: Used in bulletproof vests and helmets for military and law enforcement. Kevlar, a well-known aramid fiber, is used for its high strength and impact resistance. e. Sports Equipment: High-performance helmets for motorsports and cycling often use aramid fiber composites for their strength and light weight. Basalt Fiber Composites: f. Infrastructure: Used in the construction of roads and bridges for reinforcement due to its high mechanical strength and durability. g. Fire Protection: Due to its high thermal resistance, basalt fiber composites are used in fireproof textiles and building materials. Polyethylene Fiber Composites: h. Personal Armor: Ultra-high-molecular-weight polyethylene (UHMWPE) composites are used in personal body armor due to their high impact resistance and lightweight. i. Ropes and Cables: Used in maritime applications for mooring lines and nets because of their strength, lightweight, and resistance to water. These examples illustrate the versatility of polymer matrix composites across various sectors. Their unique properties make them suitable for specialized applications where traditional materials like metal or wood may not be as effective. Anisotropy in Fiber Composites 1. Definition: Anisotropy in fiber composites refers to the directional dependence of material properties. Unlike isotropic materials, which have uniform properties in all directions, anisotropic materials like fiber composites exhibit different mechanical and physical properties depending on the orientation of the fibers within the matrix. 2. Causes: The anisotropic nature is primarily due to the alignment of fibers. Fibers are much stronger and stiffer along their length compared to across their diameter. Therefore, the composite's strength, stiffness, and other properties are highest in the direction parallel to the fibers and lower in perpendicular directions. 3. Implications: This directional dependence of properties can be both beneficial and limiting. It allows for tailoring the material properties to specific application requirements, but it also means that the material may be weaker in certain orientations. Figure 5. Anisotropy in fiber composites 2. Metal Matrix Composites (MMC) Metal Matrix Composites are composed of a metal or alloy matrix reinforced with fibers or particles. Common metals used include aluminum, titanium, and magnesium. MMCs combine the ductility and toughness of metals with the high strength and stiffness of the reinforcement, resulting in materials that are strong, stiff, and capable of operating under wider temperature ranges compared to traditional metals. Figure 6. Metal matrix composites 1. Aluminum Matrix Composites:  Aerospace Industry: Used in components like propellers, rotor blades, and landing gear due to their high strength-to-weight ratio and improved wear resistance. For instance, some aircraft brake systems use aluminum matrix composites for better heat dissipation.  Automotive Industry: Used in engine components such as pistons, connecting rods, and drive shafts. The high thermal conductivity and low expansion of aluminum MMCs are beneficial for these applications. Porsche and Ferrari have used MMCs in some of their high-performance engines.  Sporting Goods: High-end bicycles and baseball bats sometimes use aluminum MMCs for enhanced strength and reduced weight. 2. Titanium Matrix Composites:  Aerospace and Aviation: Used in high-temperature components of jet engines, like compressor blades and vanes, due to their excellent strength and temperature resistance.  Biomedical Applications: Used in implants and prosthetics because of titanium's biocompatibility and the improved wear resistance provided by the composite material. 3. Nickel Matrix Composites:  Turbine Blades: Used in gas turbine engines for aircraft and power generation. The addition of ceramic fibers to a nickel matrix increases high-temperature strength and corrosion resistance.  Thermal Barrier Coatings: Applied in high-temperature environments like in rocket engine components for improved thermal resistance. 4. Magnesium Matrix Composites:  Automotive Industry: Used in components like gearboxes and clutch housings for reducing the overall weight of the vehicle. Magnesium MMCs provide a good balance of lightness and strength.  Electronics: Used in portable electronics like laptops and cameras for sturdy, yet lightweight casings.  Degradable Orthopedic Implants: Magnesium MMCs are also being explored for use in orthopedic implants such as screws, pins, and plates used in bone surgery. The advantage of using magnesium in these applications is its biocompatibility and the fact that it is naturally found in the human body, reducing the risk of adverse reactions. As the implant degrades, it releases magnesium ions, which can promote bone growth and healing. The controlled degradation of these implants means that they provide support during the healing process and then gradually dissolve, negating the need for a second surgery to remove the implant.The mechanical properties of these implants can be tailored through the use of different composite materials to match the properties of bone, reducing stress shielding effects. Figure 7. Biodegradable magnesium matrix composites for orthopedics 3. Ceramic Matrix Composites (CMC) Figure 8. Ceramic matrix composites Ceramic Matrix Composites consist of reinforcement materials embedded in a ceramic matrix. These composites are designed to overcome the major drawback of conventional ceramics – their brittleness. CMCs maintain the high-temperature stability and wear resistance of ceramics while offering improved toughness. They are ideal for applications that require resistance to high temperatures and harsh environments. Metal-reinforced ceramic matrix composite (CMC) would have more toughness than its monolithic ceramic counterpart. It’s underlying mechanism involves understanding the inherent properties of ceramics and metals and how their combination in a composite material can enhance overall performance. Properties of Monolithic Ceramics  High Hardness and Strength: Ceramics are known for their hardness and compressive strength.  Brittleness: Ceramics lack plastic deformation and are brittle, meaning they tend to fracture under tensile stress or impact without significant prior deformation.  Low Toughness: Due to their brittleness, ceramics have low fracture toughness. They are unable to absorb much energy before fracturing. Properties of Metals  Ductility: Metals can undergo significant plastic deformation before failure. This property allows metals to absorb and dissipate energy.  Toughness: Metals generally have high toughness, which means they can absorb more energy before failing.  Thermal and Electrical Conductivity: Metals typically have good thermal and electrical conductivity. Metal-Reinforced Ceramic Matrix Composites When metals are incorporated into a ceramic matrix to form a composite, the resulting material combines the best attributes of both ceramics and metals: 1. Increased Toughness: The ductility of the metal reinforcement in CMCs enhances the toughness of the material. The metal can undergo plastic deformation, which helps to absorb and dissipate energy that would otherwise cause a brittle ceramic to crack or fracture. 2. Crack Bridging: Metal reinforcements can bridge the cracks that form in the ceramic matrix. When a crack begins to propagate in a ceramic, it can be "bridged" or "pinned" by the metal reinforcement. This bridging effect slows down or stops the growth of cracks, enhancing the toughness. 3. Crack Deflection: The presence of metal fibers or particles can cause a crack to change direction or become deflected when it encounters a metal inclusion. This crack deflection process absorbs energy and increases the path a crack must travel, effectively increasing the material's resistance to fracture. 4. Thermal Stress Relief: Differential thermal expansion between the metal and ceramic components can lead to the development of internal stresses. However, the ductility of the metal can help accommodate these stresses, reducing the likelihood of crack formation due to thermal stress. 5. Improved Fracture Behavior: The composite material does not fail catastrophically like a monolithic ceramic. Instead, the failure is more gradual due to the metal's ability to deform, providing some warning before total failure. In summary, the incorporation of metal into a ceramic matrix in CMCs results in a material that retains the high-temperature resistance and hardness of ceramics but with significantly improved toughness due to the ductility, energy absorption, and crack-arresting properties of the metal reinforcement. This makes metal-reinforced CMCs suitable for applications where both high strength and toughness are required, which is not possible with monolithic ceramics. Figure 9. Crack propagation in monolithic ceramic and CMCs Applications of CMCs: 1. Aerospace Industry:  Jet Engine Components: CMCs are used in turbine blades, combustor liners, and nozzle vanes in jet engines. They can withstand high temperatures without requiring cooling, which improves engine efficiency. For example, General Electric and Rolls- Royce have been incorporating CMCs in their latest jet engines.  Spacecraft Components: Used in the nose caps and wing leading edges of space shuttles and re-entry spacecraft due to their excellent thermal shock resistance. 2. Automotive Industry:  Brake Systems: High-performance and luxury vehicles use CMC brake discs because they offer better high-temperature performance and wear resistance than traditional materials, leading to longer lifespan and improved safety.  Heat Shields: Used in exhaust systems and heat shields for high-performance vehicles, providing better heat resistance and reducing overall vehicle weight. 3. Energy Sector:  Nuclear Fusion Reactors: CMCs are used in components that are exposed to extremely high temperatures and corrosive environments in nuclear fusion reactors.  Gas Turbines: Used in stationary gas turbines for power generation, particularly in high-temperature components, to increase efficiency and reduce emissions. 4. Tools and machinery:  Cutting Tools: CMCs are used to make cutting tools for high-speed machining of metals. They remain stable at high temperatures, maintaining sharpness and precision.  Protective Coatings: Applied as coatings on industrial machinery parts exposed to high temperatures and corrosive environments. 5. Medical Applications:  Prosthetic Devices: Biocompatible ceramic matrix composites are used in certain prosthetic implants, such as hip and knee replacements, due to their high wear resistance and compatibility with human tissues. 6. Electronics:  Semiconductor Manufacturing: CMCs are used in semiconductor manufacturing equipment due to their ability to withstand high temperatures and corrosive chemicals. 7. Defense and Armor:  Ballistic Armor: Used in body armor and vehicle armor, offering high hardness and shock resistance to provide protection against high-velocity projectiles. CMCs stand out in environments where high temperatures, corrosion, wear, and strength are critical factors. Their unique properties make them suitable for specialized applications in industries where traditional materials are inadequate. The development and use of CMCs represent a significant advancement in materials technology, offering solutions to some of the most demanding engineering challenges. Figure 10. Common ceramic materials used to fabricate CMCs 4. Hybrid Composites Hybrid Composites are materials made by combining two or more different types of reinforcements into a single matrix. The idea is to blend the qualities of each type of reinforcement to achieve a balance of properties that are not possible with a single type of reinforcement. For example, a combination of carbon and glass fibers in a polymer matrix can provide a balance of strength, stiffness, and cost-effectiveness. Hybrid composites allow for tailored properties specific to the requirements of the application. Rule of mixture: Rule of Mixtures for composite materials is used to estimate the strength and stiffness of a composite. 1. σc is the predicted tensile (or compressive) strength of the composite material. 2. Ec is the predicted Young's modulus (a measure of stiffness) of the composite material. 3. σf is the tensile (or compressive) strength of the fiber material. 4. Ef is the Young's modulus of the fiber material. 5. σm is the tensile (or compressive) strength of the matrix material. 6. Em is the Young's modulus of the matrix material. 7. x is the volume fraction of fibers in the composite. The first equation predicts the composite's strength (σc) as a weighted average of the strengths of the fiber and matrix, according to their volume fractions in the composite. The second equation predicts the composite's Young's modulus (Ec) in a similar manner, as a weighted average of the moduli of the fiber and matrix. These formulas are based on the assumption that the fibers are aligned in the loading direction, and the load is transferred efficiently between the matrix and the fiber. It's a linear approximation, and real- world results may vary due to factors like fiber-matrix bonding, fiber distribution, and anisotropy in the composite material.