Unitatea 4: Sisteme moderne de management a producţiei PDF
Document Details
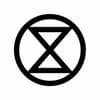
Uploaded by k0rn3a
Tags
Summary
This document provides an overview of modern production management systems, focusing on MRP (Material Requirements Planning) and MRP II (Manufacturing Requirements Planning). It details the components, inputs, outputs, and considerations for implementing these systems, including examples and practical applications.
Full Transcript
Unitatea 4. Sisteme moderne de management a producţiei 4.1. Sistemele de management a producţiei de tip MRP (Material Requirements Planning) şi MRP II (Manufacturing Requirements Planning) 4.1.1. MRP MRP este un sistem computerizat de management al stocurilor utilizat în scopul planificării şi contr...
Unitatea 4. Sisteme moderne de management a producţiei 4.1. Sistemele de management a producţiei de tip MRP (Material Requirements Planning) şi MRP II (Manufacturing Requirements Planning) 4.1.1. MRP MRP este un sistem computerizat de management al stocurilor utilizat în scopul planificării şi controlului stocurilor de materii prime şi materiale, componente şi subansamble necesare realizării produselor finite care fac obiectul activităţii de bază a firmei. Este utilizat frecvent pentru a stabili, realiza şi controla programele de producţie (fabricaţie) aferente diferitelor perioade de timp – zi, săptămână, lună, trimestru sau, eventual an. Se pretează în special producţiei de serie - mare şi mijlocie, organizată pe bază de loturi în cadrul căreia produsele finite se obţin dintr-un număr mare de componente în urma parcurgerii mai multor faze de producţie. De la apariţia sa, sistemul a fost preluat în primul rând de acele firme care îşi desfăşurau activitatea de producţie utilizând ca unitate de evidenţă şi management a producţiei lotul optim de fabricaţie, cu varianta practică de lot economic. Identificând tipul, cantitatea şi momentul în care componentele sunt necesare, sistemele MRP permit/ favorizează reducerea costurilor cu stocurile, îmbunătăţirea eficienţei programării producţiei şi răspunsul rapid la schimbările pieţei. Scopul utilizării unui sistem MRP este acela de a avea la dispoziţie componentele necesare exact la momentul când sunt necesare, nici mai repede, nici mai târziu. MRP tratează diferit materiile prime, componentele, subansamblele şi produsele finite putând fi utilizat ca instrument de programare şi control al producţiei. De asemenea un astfel de sistem permite evidenţa comenzilor (interne sau externe) efectuate şi reprogramarea acestora dacă apar întârzieri. Aspectele principale ale existenţei şi funcţionării unui sistem MRP sunt relativ simple implicând următoarele întrebări: 1. Ce cantitate de produse trebuie realizată? 2. Când trebuie produsă această cantitate? 3. Care este componenţa produsului ( materii prime, componente) ? 4. Ce tipuri de componente şi în ce cantităţi există în stoc? 5. Ce cantitate trebuie comandată de la furnizori? 6. Care este timpul de onorare a comenzii (lead time) de către furnizori şi care este, în consecinţă, momentul plasării comenzii către aceştia? Un sistem MRP are trei elemente componente, respectiv: . Procesarea (prelucrarea) datelor; . Ieşirile. A. Intrările sunt constituite din mai multe tipuri de date care se pot grupa în următoarele trei module: Programul de producţie (Master Production Schedule - MPS ) poate fi stabilit zilnic, săptămânal sau lunar (în funcţie de gradul de detaliere a MRP-ului) şi cuprinde cantităţile din fiecare tip de produs care urmează să se realizeze şi momentul la care acestea sunt necesar să fie produse. Cantităţile care apar în programul de producţie pot proveni din mai multe surse: cererea clienţilor, previziuni ale cererii şi/sau cantităţi necesare pentru formarea stocurilor sezoniere. Acesta trebuie corelat în prealabil cu disponibilităţile de capacitate, referitoare atât la maşini şi utilaje (prezentarea balanţelor de corelare capacitate - încărcare) cât şi la forţa de muncă necesară/disponibilă. Din icaţie reprezintă veriga de legătură între obiectivele strategice de ansamblu ale unităţii şi modul concret în care acestea se realizează - prin sarcinile simple de muncă ce se desfăşoară la nivel de loc de muncă, formaţie de lucru, secţie sau atelier. Structurile constructive ale produselor (Bill of Material - BOM) - cuprind informaţii legate de modul de obţinere al unei unităţi de produs finit: (1) componentele (tipul şi cantitatea) care trebuie să se regăsească în produsul finit - ansamble, subansamble, elementele componente ale acestora - reperele, şi (2) modul în care acestea ajung să se încorporeze în componentele superioare lor ca şi complexitate. Structura constructivă a produsului trebuie să prezinte componenţa produsului în ordine ierarhică, evidenţiind cantitatea din fiecare element component necesară obţinerii unei unităţi din elementul constructiv de pe nivelul imediat superior. Poate avea forma unui arbore, în vârful ierarhiei situându-se produsul finit, iar la baza acesteia cele mai simple elemente constructive, formă tabelară pe mai multe nivele sau formă tabelară pe un singur nivel. Structura constructivă trebuie să fie exactă/ precisă pentru a se putea determina cantităţile exacte din fiecare element component. Evidenţa stocurilor trebuie să fie detaliată din punct de vedere al fazelor procesului de producţie în care se află cantităţile respective - materie primă, producţie neterminată sau produse finite şi pe intervale de timp şi de asemenea să fie cât mai precisă. Cu cât controlul stocurilor este mai detaliat, cu atât programele de producţie pot fi mai precis stabilite. Evidenţa stocurilor va include: - cantităţile brute necesare; - intrările programate; - stocurile existente; - elemente proprii fiecărui element component: furnizorul, timpul de livrare, mărimea lotului aprovizionat; - schimbări datorate intrărilor, ieşirilor, comenzilor anulate etc.. Ca şi structura constructivă a produsului evidenţa stocurilor trebuie să fie exactă, lipsa preciziei putând afecta respectarea termenelor de livrare a produselor finite. 2. Procesarea datelor se referă în mod concret la aplicarea sistemului de management a producţiei de tip MRP, respectiv transformarea Intrărilor în Ieşiri. Evidenţele de bază ale oricărui sistem MRP cuprind situaţii referitoare la fiecare tip de produs care face parte dintr-un program de fabricaţie: tipul produsului, eşalonarea cantitativă a livrărilor prevăzute în program pe perioade scurte de timp (săptămânal), intrări planificate, stocuri iniţiale şi finale săptămânale, comenzi noi lansate şi materializarea lor în stoc. Astfel, plecând de la cantitatea de produse finite necesară la un moment dat, pe baza structurii constructive şi a informaţiilor privind stocurile vor fi stabilite momentul şi cantităţile necesare din fiecare element constructiv. Sarcina unui sistem MRP este să furnizeze cantităţile nete necesare. Cantitatea netă în momentul t = Cantitatea brută în momentul t ( programul de fabricaţie) – Nivelul stocurilor în momentul t + Stocul de siguranţă . Pe lângă aceste informaţii un sistem MRP II (Manufacturing Requirements Planning) are nevoie şi de date care să-i ofere posibilitatea analizei asupra acoperirii programelor de producţie din punct de vedere cantitativ şi calitativ cu capacitatea de producţie necesară precum şi cu forţa de muncă necesară ca număr de angajaţi şi pregătire profesională. 3. Ieşirile se concretizează în principal sub forma unor informaţii, situaţii sau rapoarte care sunt clasificate în două categorii: rapoarte primare şi rapoarte secundare. Rapoartele primare – informaţiile privind planificarea şi controlul producţiei şi al stocurilor reprezintă obiectul rapoartelor primare. Aceste rapoarte includ: 1. Comenzile planificate – o programare care precizează cantitatea şi momentul comenzilor viitoare. 2. Lansarea comenzilor - autorizarea execuţiei comenzilor planificate. 3. Schimbări ale comenzilor planificate, inclusiv revizuiri al datelor limită sau ale cantităţilor comenzilor şi anulări ale unor comenzi. Rapoarte secundare – controlul performanţei, planificare şi situaţii de excepţie 1. Rapoartele privind controlul performanţei evaluează modul de operare al sistemului. Ajută managerii să stabilească devierile de la plan, incluzând nerespectarea termenelor de livrare, epuizarea stocurilor şi oferă informaţii pentru evaluarea eficienţei din punctul de vedere al costurilor. 2. Rapoarte de planificare sunt utile pentru previziunea cantităţii de stocuri necesare. Ele includ angajamentele de aprovizionare şi alte informaţii ce pot fi utilizate pentru stabilirea necesarului viitor de materiale. 3. Rapoarte ale situaţiilor excepţionale atrag atenţia asupra discrepanţelor majore ca de exemplu comenzi întârziate, rată mare a defectelor, erori de raportare, cereri de componente inexistente. 4.1.2. MRP II . MRP II este o colecţie de soft-uri ce permite circulaţia informaţiei, nu doar în interiorul compartimentului Producţie, dar şi între diferitele compartimente ale unei firme, legate într-un fel sau altul cu activitatea de producţie propriu-zisă (Marketing, Financiar) precum şi extinderea scopului planificării componentelor necesare cu planificarea capacităţii de producţie ncesare. Figura nr 3.6. furnizează o imagine de ansamblu legată de MRP II, cu prezentarea celor trei compartimente care au beneficii directe de pe urma utilizării unui astfel de sistem. Oportunitatea oferită de sistemele MRP II de a furniza informaţii "pe loc" asupra diverselor probleme sau cerinţe venite din partea clienţilor, poate crea premisele necesare respectivei întreprinderi de a realiza un avantaj competitiv pe piaţă, faţă de o alta care dispune sau nu de un sistem informatizat, dar în nici un caz de unul mai bine integrat între diferitele compartimente. 4.1.3. Avantajele şi dezavantajele sistemelor MRP şi MRP II Avantajele implementării unui sistem de tip MRP sau MRP II au ca şi punct central de plecare această tendinţă de reducere a stocurilor şi, implicit, a cheltuielilor suplimentare (imobilizărilor) ce ar rezulta în condiţiile menţinerii stocurilor la un nivel ridicat. Considerăm că aceste avantaje se referă la: nivele reduse ale stocurilor care determină economii concretizate în necesarul de fonduri financiare, necesarul de spaţii pentru activităţi ca depozitare, manipulare, recepţie, etc.; viteza mai mare de rotaţie a stocurilor, cu implicaţii directe asupra reducerii nivelului de mijloace băneşti imobilizate; satisfacerea la un nivel superior a cerinţelor pieţei (din punct de vedere al cantităţilor şi a termenelor de onorare a diferitelor cereri; posibilitatea de a reduce termenul de onorare a comenzii, prin includerea acestora în programele de fabricaţie detaliate; creşterea gradului de utilizare a capacităţilor de producţie în cadrul sistemelor MRP II, datorită includerii în cadrul acestuia a problemelor legate de capacitate; capacitatea sistemului de a realiza legătura între cererea pieţei concretizată în comenzi certe sau previziuni statistice şi programele de fabricaţie/aprovizionare, pe perioade scurte de timp; îmbunătăţirea activităţii de planificare prin implicarea directă a tuturor verigilor de producţie în stabilirea cantităţilor şi a termenelor de livrare. Dezavantajele decurg, în mod paradoxal, tot din nivelul redus al stocurilor. Considerăm că acestea se referă la: gradul redus de flexibilitate, care poate avea consecinţe nefavorabile grave asupra rezultatelor producţiei, în condiţiile contemporane ale industriei, caracterizate ca un mediu de concurenţă intensă, din ce în ce mai dură. Altfel ocurilor pot crea la un moment dat dereglări în derularea programelor de fabricaţie, care se pot remedia doar în anumite limite. Căile de remediere a unor astfel de situaţii pot fi: modificarea programelor iniţiale; îmbunătăţiri aduse procesului de producţie care să aducă o creştere a productivităţii muncii sau o creştere a gradului de utilizare a capacităţii de producţie sau reducerea unor durate de execuţie; găsirea unor modalităţi care să atragă alţi clienţi pentru produsele finite în cazul în care perturbările au determinat pierderea clienţilor deja existenţi, ca de exemplu: servicii suplimentare sau noi pentru produs, reducerea unor cheltuieli ale clienţilor (transport, service, instalare). posibilitatea de a rezolva unele probleme legate de procesul de producţie care se pot ivi datorită nivelului redus al stocurilor, dar care nu ar apărea dacă aceste stocuri ar fi fost la un nivel mai mare. De exemplu, un furnizor care nu îşi respectă contractele încheiate poate fi acoperit dacă întreprinderea dispune de stocuri; costurile acesteia cresc datorită stocurilor mari dar şi datorită unor cheltuieli care ar putea să apară datorită furnizorului - creşterea cheltuielilor de transport datorită neonorării contractelor, determinate de utilizarea redusă a capacităţii mijloacelor de transport. cantitatea mare de date necesară pentru obţinerea programelor de fabricaţie şi a altor informaţii necesare procesului de fabricaţie; în plus, achiziţionarea soft-urilor MRP este destul de costisitoare, pe lângă necesitatea de a avea reţeaua de calculatoare care să realizeze în mod efectiv derularea programelor MRP. Utilizarea în mod practic a unui sistem MRP presupune îndeplinirea prealabilă a mai multor condiţii: programele de fabricaţie trebuie cunoscute în avans; perioadele de îndeplinire a acestora să fie scurte: săptămânale, cel mult lunare. planurile să fie relativ stabile, fără abateri semnificative; sistemul informaţional legat de stocuri/furnizori să fie bine pus la punct ; cunoaşterea termenelor de livrare, dar şi a contractelor cu furnizorii. 4.2. Sistemele ERP Sistemele ERP (Enterprise Resource Planning) reprezintă pasul următor în evoluţia sistemelor computerizate integrate de management a producţiei care a început cu MRP şi MRPII. Ca şi MRP II, sistemele ERP au un nucleu MRP. ERP reprezintă un efort extins de a integra înregistrări standardizate care să permită utilizarea comună a informaţiilor de către diferite departamente ale unei organizaţii, ceea ce va conduce la un management mai eficient al sistemului. ERP urmăreşte integrarea tuturor funcţiunilor firmei într-un singur sistem informaţional computerizat care permite satisfacerea cerinţelor specifice ale acestora. Sistemele ERP permit organizaţiei să aibă o viziune completă asupra operaţiunilor nemaifiind necesar efortul de a pune cap la cap informaţiile produse în cadrul diferitelor funcţiuni sau divizii organizatorice. ERP are rolul de a integra punctele-cheie ale unei afaceri oferind: - o perspectivă globală a ceea ce se întâmplă în cadrul structurii organizaţionale; -o cooperare, cu efort minim, între diversele departamente; - un flux al informaţiei sigur şi fără redundanţe în cadrul firmei. Sistemul ERP presupune existenţa unei baze de date care este accesibilă întregii organizaţii. Angajaţii pot accesa anumite informaţii din această bază de date pe bază de parolă. Existenţa unei singure baze de date cu toate informaţiile referitoare la firmă favorizează monitorizarea de către manageri a tuturor produselor firmei, în toate locaţiile acesteia, în orice moment. Baza de date colectează informaţiile şi le face disponibile diferitelor aplicaţii ale sistemului software. O informaţie introdusă într-o aplicaţie presupune actualizarea informaţiilor în celelalte aplicaţii cum ar fi baza de date cu informaţii financiare şi contabile, baza de date cu informaţiile referitoare la resursele umane şi la salarii, cea cu informaţii referitoare şi clienţi şi vânzări etc. astfel, sistemele ERP oferă angajaţilor acces la informaţii în timp real. Acest proces elimină numeroase probleme de coordonare între funcţiuni pe care celelalte sisteme care nu erau integrate le aveau. Implementarea unui sistem ERP este un proces de lungă durată, un sistem complet necesitând o durată de implementare de unu până la trei ani. Adoptarea unui astfel de sistem necesită de multe ori schimbarea modului de acţiune a companiei precum şi a modului de execuţie a sarcinilor de serviciu de către fiecare angajat. Există trei motive majore pentru care firmele optează pentru un astfel de sistem: 1) Integrarea informaţiilor financiare – fiecare departament are versiunea proprie (propriul set de indicatori, informaţii financiare) atunci când ne referim de aportul lor la performanţa companiei. Sistemele ERP creează o singură versiune a informaţiilor financiare întrucât toată lumea foloseşte acelaşi sistem. 2) Standardizarea proceselor de fabricaţie şi utilizarea unui singur sistem informatic integrat poate duce la economie de timp, creşterea productivităţii şi la reducerea numărului de angajaţi. 3) Standardizarea informaţiilor legate de resursa umană – companiile mari care au în structura lor mai multe unităţi de afaceri s-ar putea să nu deţină o singură metodă pentru înregistrarea timpului lucrat şi pentru comunicarea cu angajaţii. Un sistem ERP poate rezolva această problemă. Avantajele sistemelor ERP sunt următoarele: diminuează stocarea datelor redundante; elimină necesitatea re-codificării si reformatării datelor dintr-un sistem pentru utilizarea acestora în alte sisteme; îmbunătăţeşte canalele de comunicare între sisteme facilitând astfel automatizarea transferului de date; optimizează fluxurile de date din cadrul companiei. Principalele dezavantaje ale sistemelor ERP sunt: aplicaţiile sunt foarte scumpe si dificil de implementat ( implementarea este mult mai costisitoare decât software-ul respectiv). inflexibile (generice, nespecifice unei industrii anume – cu toate că modificări de cod sunt posibile, dar foarte costisitoare). capacităţi analitice scăzute (destinate tranzacţiilor, sunt în principal operaţionale ) 4.3. Sistemele de management al producţiei de tip Just In Time ( JIT ) Termenul JIT provine din traducerea în limba engleză „Just in Time”, care tradus în limba română înseamnă „Exact la Timp”. Aceasta presupune că cele trei elemente indispensabile oricărei activităţi productive - capital, echipament şi muncă sunt disponibile “exact la timp”, astfel încât să se respecte obiectivele care revin funcţiunii de producţie, conform celor derivate din obiectivele generale ale întreprinderii. La fiecare loc de muncă din cadrul procesului de producţie se produce cantitatea necesară şi acest lucru se realizează la momentul în care aceasta este cerută de locul de muncă următor, în conformitate cu fluxul tehnologic. Principiile care stau la baza funcţionării oricărui sistem de tip JIT sunt următoarele: A. Eliminarea pierderilor înseamnă ca întreprinderea să acorde atenţie oricărui factor care poate provoca la un moment dat un prejudiciu activităţii de producţie, în sens larg, care va determina implicit rezultate economico-financiare nesatisfăcătoare la nivelul întreprinderii. Între aceşti factori se pot aminti: 1. necorelarea între capacitatea de producţie existentă şi necesităţile corespunzătoare unei anumite perioade de timp; 2. supradimensionarea necesarului de personal, care determină cheltuieli suplimentare cu salariile; 3. erori în derularea procesului de producţie care pot avea efecte negative propagabile în cât mai multe faze ale procesului de fabricaţie; 4. neconcordanţa între producţie şi cererea pieţei. B. Îmbunătăţirea continuă: la nivelul procesului de producţie se urmăreşte perfecţionarea continuă a procesului de fabricaţie, care să ducă la creşterea productivităţii muncii, implicit la creşterea eficienţei economice a întregii activităţi. C. Calitatea perfectă a produsului şi a producţiei. Calitatea trebuie asigurată la locul de muncă iar muncitorul care execută o operaţie este direct răspunzător de fiecare piesă prelucrată care iese de pe maşina lui. D. Zero Stocuri - în vederea îndeplinirii acestui principiu se impun respectarea unor premise, astfel: . eliminarea aleatorului şi a incertitudinilor; . necesitatea de a avea furnizori stabili şi de încredere care să respecte în întregime contractele stabilite; . proiectarea corespunzătoare a produselor, pieselor şi subansamblelor, cu scopul prioritar de a se realiza în conformitate cu condiţiile impuse de piaţă, din toate punctele de vedere; . reducerea la zero a probabilităţii de căderi accidentale a utilajelor şi echipamentelor; . . respectarea în orice moment şi la fiecare loc de muncă a standardelor de calitate, astfel încât să se asigure necesităţile pentru orice loc de muncă în momentul oportun; . utilizarea în cadrul programării producţiei a loturilor minim posibile, care să tindă spre loturi unitare (n=1); . respectarea cerinţelor pieţei şi preocuparea pentru satisfacerea acestora în orice moment. . E. Respect faţă de factorul uman. Este o parte importantă a filosofiei JIT, care necesită poate cea mai îndelungată perioadă de timp pentru a fi implementată. . F. Orientarea activităţii pe termen lung. Deoarece rezultatele JIT cer, în majoritatea cazurilor, perioade mari de timp pentru a fi percepute, managementul este acela care trebuie să caute şi să găsească soluţii prin care să motiveze muncitorii precum şi restul angajaţilor să gândească în spiritul JIT. . Orice sistem de management a producţiei de tip JIT are anumite trăsături comune, indiferent de specificul întreprinderii care îl implementează şi care, în ultimă instanţă, contribuie la îmbunătăţirea performanţelor economice ale proceselor de producţie respective. Considerăm că aceste caracteristici se referă la: . 1. Simplitate - sistemele JIT nu presupun un volum mare nici de date de intrare, nici referitor la prelucrarea acestora. În mod concret, un JIT presupune derularea simplă a procesului de producţie, astfel încât fiecare sarcină de muncă să se realizeze exact în cantitatea în care este necesară locului de muncă următor pe fluxul tehnologic, precum şi la momentul oportun. O condiţie necesară pentru ca acest obiectiv să poată fi îndeplinit, este şi respectarea în permanenţă, la nivelul oricărui loc de muncă, a standardelor de calitate cerute de procesul de producţie. . 2. Flexibilitatea este a doua trăsătură indispensabilă funcţionării eficiente a unui sistem JIT. Ea trebuie să se manifeste sub diferite forme, care considerăm că sunt următoarele: . flexibilitate în procesul de aprovizionare; . flexibilitate în procesul de producţie; . flexibilitatea forţei de muncă; . flexibilitate în satisfacerea cererii pieţei. 3. Continuitatea şi gradul maxim de utilizare a capacităţilor de producţie se referă la utilizarea resurselor de producţie astfel încât să se realizeze un flux uniform de producţie, care să asigure în acelaşi timp şi un grad maxim posibil de utilizare al capacităţii de producţie. 4. Producţia de tip “PULL” este ultima, dar nu şi cea mai puţin importantă dintre caracteristicile unui sistem JIT. Abordarea de tip “PULL” presupune ca şi punct de plecare piaţa şi cererea manifestată în cadrul acesteia, în orice moment în care se găseşte ca şi stadiu procesul de fabricaţie. În cazul sistemelor de producţie de tip “PULL” caracteristica de bază este că, în orice moment al desfăşurării procesului de producţie, sarcina de muncă de la un loc de muncă (i) este determinată de cererea din piesa / produsul respectiv la locul de muncă (i+1). Cu alte cuvinte se produce numai dacă este nevoie de acele cantităţi la locurile de muncă următoare. Producţia de tip PULL are anumite avantaje: piaţa este factorul hotărâtor care “împinge” resursele de producţie (materiale, financiare, umane, informaţionale) în interiorul acestuia, spre deosebire de celelalte sisteme în care produsele finite sunt împinse spre piaţă; se operează cu loturi mici, ce determină cheltuieli de imobilizare mici, faţă de loturile calculate în mod tradiţional; sistemele PULL operează cu timpi de reglare frecvenţi, dar reduşi, în timp ce managementul tradiţional al producţiei aduce în discuţie doar raportul direct proporţional care există între mărimea lotului de fabricaţie şi timpul de reglare - timpul de pregătire-încheiere. Astfel, cu cât lotul utilizat este mai mare, cu atât numărul de lansări este mai mic, ceea ce determină timpi/cheltuieli de pregătireîncheiere mici; nu se ţine cont de posibilitatea că durata de realizare a acestor reglări s-ar putea reduce la o simplă apăsare de buton/tastă - obiectiv JIT, ceea ce ar face să devină mai puţin semnificativă frecvenţa mare a reglărilor; sistemele de tip PULL operează cu nivele reduse ale stocurilor, determinate de containerele Kanban, pe când celelalte sisteme au în vedere minimizarea stocurilor, la nivele mai puţin semnificative; orice sistem PULL promovează, prin construcţia sa, rezolvarea problemelor care pot să apară în cadrul fluxului tehnologic, datorită nivelului redus de stocuri care nu îi permite neglijarea sau amânarea acestor probleme, în contradicţie cu sistemele de tip PUSH care pot acoperi la un moment dat anumite deficienţe în cadrul procesului; sistemele PULL produc permanent în scopul satisfacerii cererii pieţei la momentul în cauză, în timp ce sistemele de tip PUSH sunt, prin tradiţie, caracteristice producţiei pe bază de stoc. Pentru a putea aduce în discuţie plusurile, respectiv minusurile unui JIT, vom prezenta pe baza aspectelor tratate până acum, elementele cheie ale unui JIT, astfel: mediu economic stabil; producţie de tip continuu; corelarea eficientă a capacităţilor de producţie; mijloace de muncă adecvate utilizării JIT; stocuri minime; loturi de fabricaţie şi interoperaţionale minim posibile; timp minim de realizare a unui produs; timpi minimi de pregătire-încheiere; activitate interoperaţională eficientă - transport, manipulări, etc. calitate ridicată pe tot parcursul procesului de fabricaţie; forţă de muncă cu calificare flexibilă (policalificată); capacitate de a rezolva problemele la nivelul fiecărui loc de muncă; tehnica Kanban, ca fiind cea mai potrivită pentru evidenţa şi controlul stocurilor. Dacă aceste elemente sunt respectate, sistemul JIT va funcţiona cu succes. Gradul de reuşită este direct proporţional cu respectarea acestor elemente esenţiale. De aici poate apărea un dezavantaj major, respectiv ineficienţa sistemului, datorită nerespectării unuia sau mai multor elemente din cele enumerate anterior. De asemenea, respectarea elementelor de mai sus poate releva mai multe avantaje directe ale unui JIT, respectiv: posibilitatea de a onora într-un timp record o comandă de pe piaţă - din elementele g, k, l, m. productivitate superioară a muncii datorită elementelor b, c, j. creşterea calităţii producţiei şi a produselor - e, j, l. planificarea şi programarea mult simplificată a producţiei -e, f, l, m.