Industrial Garment Machinery PDF
Document Details
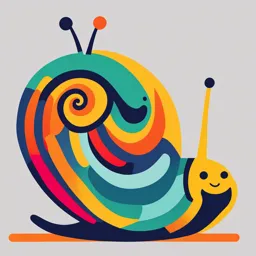
Uploaded by LovelyHydra7018
Government Polytechnic Osmanabad
Tags
Summary
These notes cover the different types of sewing defects, the need for both corrective and preventive maintenance, and the effects of Industry 4.0 on the garment industry. It's a good resource for learning about industrial garment machinery and the associated topics.
Full Transcript
INDUSTRIAL GARMENT MACHINERY Fashion Technology III Semester DIFFERENT TYPES OF SEWING DEFECTS Uneven Stitching: This occurs when the stitching lines are not consistent in length or spacing. Skipped Stitches: When the sewing machine misses stitches, creating gaps in...
INDUSTRIAL GARMENT MACHINERY Fashion Technology III Semester DIFFERENT TYPES OF SEWING DEFECTS Uneven Stitching: This occurs when the stitching lines are not consistent in length or spacing. Skipped Stitches: When the sewing machine misses stitches, creating gaps in the fabric. Puckering: Fabric gathers or forms wrinkles around the stitches, usually a sign of tension issues. Thread Breakage: The thread snaps during the sewing process, leading to incomplete seams. Seam Slippage: The fabric layers in a seam shift or pull apart, compromising the integrity of the seam. Incorrect Tension: Uneven tightness of stitches on the fabric, causing loops or puckering. Bobbin Issues: Problems with the bobbin thread, such as tangling or uneven winding, can result in defects. Fabric Damage: Fabric can get snagged, torn, or stretched during the sewing process. Misaligned Patterns: When patterns or designs on the fabric don't match up correctly. Overlapping Seams: Sewing lines that cross or overlap unintentionally. Inconsistent Seam Allowance: Variations in the width of the seam allowance throughout the project. Notches and Clipping Mistakes: Errors in cutting notches or clips can affect the fit and appearance of the final product. Mismatched Thread Color: Using the wrong thread color can be a noticeable and distracting defect. Zigzagging Seams: When straight seams unintentionally zigzag, creating an irregular appearance. NEED FOR CORRECTIVE MAINTENANCE Corrective maintenance for sewing machines is essential to ensure their optimal performance and longevity. Here's why it's necessary: Quality Control: Corrective maintenance helps maintain the quality of stitched products by addressing defects promptly. This ensures that each item meets the desired standards. Reduced Downtime: Regularly correcting issues as they arise prevents prolonged machine downtime. This is crucial for production efficiency, especially in industrial settings where time is money. Cost Savings: Addressing small issues early on can prevent them from escalating into major problems. This proactive approach can save significant repair costs and potential replacement expenses. Extended Machine Life: Proper corrective maintenance contributes to the overall longevity of the sewing machine. Timely repairs and adjustments help prevent wear and tear, ensuring a longer operational life. Consistent Performance: Sewing machines need to operate consistently to produce uniform stitches. Corrective maintenance helps maintain the machine's performance at a consistent and reliable level. Minimized Product Defects: Regular maintenance reduces the likelihood of defects in stitched products. This is crucial for industries where product quality is a top priority. Safety Compliance: A well-maintained sewing machine is less likely to pose safety hazards. This is particularly important in industrial settings where adherence to safety standards is a priority. Customer Satisfaction: Consistently producing high-quality products through well- maintained sewing machines contributes to customer satisfaction. Satisfied customers are more likely to be repeat customers. Efficient Workflow: By minimizing disruptions due to machine malfunctions, corrective maintenance helps maintain a smooth and efficient workflow. This is crucial for meeting production deadlines and targets. Operator Morale: Well-maintained machines are easier and more enjoyable for operators to work with. This can positively impact operator morale and productivity. In summary, corrective maintenance is vital for maintaining the health and performance of sewing machines, ensuring they operate efficiently, produce high-quality products, and contribute to a smooth and cost-effective production process. NEED FOR PREVENTIVE MAINTENANCE Equipment Longevity: Regular preventive maintenance helps extend the lifespan of sewing machines. It involves routine inspections, cleaning, and lubrication, which can prevent wear and tear over time. Reduced Downtime: By addressing potential issues before they escalate, preventive maintenance minimizes unexpected breakdowns. This leads to less downtime and ensures a more consistent production flow. Cost Savings: Investing in preventive maintenance is a cost-effective strategy. It is often less expensive to address small issues early on than to deal with major repairs or replacements resulting from neglect. Consistent Product Quality: Regular maintenance ensures that the sewing machine operates at its optimal level, producing consistent and high-quality stitches. This is crucial for maintaining product standards. Improved Efficiency: Well-maintained machines operate more efficiently. Preventive maintenance includes calibration and adjustments, contributing to smoother and more precise stitching. Safety Assurance: Regular inspections during preventive maintenance help identify and address safety concerns. This is important for creating a safe working environment for machine operators. Adherence to Standards: In industrial settings, adherence to quality and safety standards is paramount. Preventive maintenance helps ensure that sewing machines meet or exceed these standards. Operator Training and Skill Development: During preventive maintenance, operators can receive training on best practices for machine care. This contributes to their skill development and helps them become more efficient in their roles. Energy Efficiency: Well-maintained machines often operate more energy- efficiently. Regular checks and adjustments can optimize energy consumption, leading to potential cost savings. Preservation of Resale Value: If you ever decide to upgrade or replace your sewing machine, a history of preventive maintenance can enhance its resale value. Potential buyers are more likely to invest in a machine with a well-documented maintenance record. EFFECTS OF INDUSTRY 4.0 IN GARMENT INDUSTRY Industry 4.0, characterized by the integration of digital technologies into manufacturing processes, has significant effects on the garment industry. Here are some key impacts: Automation and Robotics: Implementation of robotics and automated systems streamlines production processes, increasing efficiency and reducing the need for manual labor. This can lead to faster and more cost-effective garment production. Smart Factories: Garment factories are becoming smarter with the use of Internet of Things (IoT) devices and sensors. These technologies enable real-time monitoring of production processes, machinery, and inventory, optimizing overall operations. Data Analytics and Predictive Maintenance: The garment industry benefits from data analytics for demand forecasting, inventory management, and production planning. Predictive maintenance helps prevent machine breakdowns, reducing downtime and maintenance costs. Customization and Personalization: Industry 4.0 allows for greater customization and personalization in garment manufacturing. Advanced technologies enable the production of smaller batches or even individualized clothing items, meeting the growing demand for personalized fashion. Supply Chain Visibility: The integration of digital technologies provides enhanced visibility across the entire supply chain. This includes tracking raw materials, monitoring production stages, and managing distribution. Improved transparency leads to better coordination and responsiveness. 3D Printing and Digital Prototyping: 3D printing technology enables rapid prototyping and the creation of customized components. This not only speeds up the design and development process but also reduces waste in the prototyping stage. E-Commerce Integration: Industry 4.0 facilitates seamless integration with e-commerce platforms. This allows for better alignment between production and consumer demand, reducing excess inventory and enabling a more demand-driven production model. Augmented Reality (AR) and Virtual Reality (VR): AR and VR technologies are used for virtual fitting rooms, enabling customers to visualize how garments will look on them before making a purchase. This enhances the online shopping experience and reduces the likelihood of returns. Sustainability and Traceability: Industry 4.0 supports sustainability initiatives in the garment industry. Through the use of technology, manufacturers can track and trace the origins of materials, monitor energy consumption, and implement eco-friendly practices. Skill Requirements and Workforce Changes: The adoption of Industry 4.0 technologies requires a workforce with digital literacy and skills in areas such as data analysis, programming, and maintenance of advanced machinery. Training and upskilling become essential in this evolving landscape. The integration of Industry 4.0 in the garment industry brings about a transformation in processes, from design to production and supply chain management. While it enhances efficiency and flexibility, it also necessitates adaptation to new technologies and changes in workforce skills.