DRM2432 Occupational Safety and Health - Mechanical Hazard PDF
Document Details
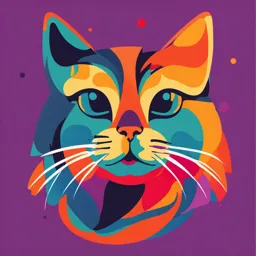
Uploaded by DaringAgate5278
Universiti Malaysia Pahang
Tags
Related
- Topic Assessment 3 Hazards and Risks in Electrical Installation PDF
- Fitter-1st-semesters mcqs PDF
- Clearwater Fire And Rescue Department Confined Space Procedures PDF
- Fire, Electrical, and Mechanical Safety Practices (PDF)
- FITTER THEORY ITI 1st YEAR QUESTION BANK PART-01 PDF
- HSEV1005 Module 6 Manual and Mechanical Handling Hazards PDF
Summary
This document presents various topics related to mechanical hazards, including hand-held power tools, general hazards, and forklift safety within the context of occupational safety.
Full Transcript
DRM2432 OCCUPATIONAL SAFETY AND HEALTH TOPIC 4 MECHANICAL HAZARD LESSON OUTCOMES 1. Describe the characteristics of mechanical hazard 2. Examples of mechanical hazard 3. Precautions to control mechanical hazard. SEGAMAT: Seorang pekerja kilang maut apabila tersepi...
DRM2432 OCCUPATIONAL SAFETY AND HEALTH TOPIC 4 MECHANICAL HAZARD LESSON OUTCOMES 1. Describe the characteristics of mechanical hazard 2. Examples of mechanical hazard 3. Precautions to control mechanical hazard. SEGAMAT: Seorang pekerja kilang maut apabila tersepit pada rantai mesin di sebuah kilang memproses buah kelapa sawit di Jalan Genuang, di sini hari ini. Anggota bomba dan penyelamat yang dipanggil mengambil masa kira-kira 30 minit untuk mengeluarkan mayat Gan Kian Beng, 57. Jurucakap Pusat Gerakan Operasi (PGO) Jabatan Bomba dan Penyelamat Malaysia (JBPM) Bandar Baru berkata, pihaknya menerima panggilan kecemasan tentang kejadian pada pukul 3.18 petang. 3 5 HAND-HELD POWER TOOLS HAZARD AND RISK MANAGEMENT OF HAND-HELD POWER TOOLS Hand-held power tools 6 Hand-held power tools 7 Hand-held power tools 8 9 Hand-held power tools General hazards ▪ mechanical entanglement in ▪ manual handling problem with a risk of rotating spindles or sanding discs; injury if the tool is heavy or very powerful; ▪ waste material flying out of the ▪ hand–arm vibration, especially with cutting area; pneumatic drill and chainsaws, disc cutters ▪ coming into contact with the and petrol-driven units; cutting blades or drill bits; ▪ tripping hazard from trailing cables, hoses ▪ risk of hitting electrical, gas or or power supplies water services when drilling into ▪ equipment and cables or cutting the building surfaces; electrical cable; ▪ electrocution/electric shock from poorly maintained ▪ eye hazard from flying particles; Hand-held power tools Typical safety controls and instructions ▪ Guarding ✓ Must be provided to protect operator from: Point of operation In-running nip points Rotating parts Flying chips and sparks ▪ Operating controls and switches ✓ Equipped with a constant-pressure switch or control that shuts off the power when pressure is Point of operation is the area on a machine where work is actually performed upon released the material being processed. Point of operation shall mean that part of the machine ✓ Handles should where the becutting, work of designed to protect shearing, operators squeezing, from drawing, orexcessive vibration manipulating and the stock keep their in any hands away from danger areas other way is done. Point of operation is the area on a machine where work is actually performed upon the Hand-held power tools material being processed. Point of operation shall mean that part of the machine where the work of cutting, shearing, squeezing, drawing, or Typical safety controls and instructions manipulating the stock in any other way is done. ▪ Guarding ✓ Must be provided to protect operator from: Point of operation In-running nip points Rotating parts Flying chips and sparks ▪ Operating controls and switches ✓ Equipped with a constant-pressure switch or control that shuts off the power when pressure is released ✓ Handles should be designed to protect operators from excessive vibration and keep their hands away from danger areas Hand-held power tools Typical safety controls and instructions ▪ Safe operations/ instructions ✓ Shall protected against electrical shock, personal injury, ill health and risk of fire ✓ Should read the instruction before using equipment and ensure there are followed: ▪ Maintain a clean and tidy working area ▪ Never expose power tools to rain ▪ Do not use power tools in the vicinity of combustible fluids, dust or gases unless tested ▪ Handle by authorized person ▪ Stored in safe place ▪ Use right tools ▪ Wear suitable work clothes, safety glasses, respirator mask ▪ Do not abuse the power cable 14 MACHINERY HAZARD HAZARD AND RISK MANAGEMENT OF MACHINE Causes of Machine Accidents 1. Negligence 2. Not using Lockout/Tagout 3. Unauthorized persons doing maintenance or using the machines 4. Missing parts or loose machine guards Where Mechanical Hazards Occur? Point of operation All parts of the machine which move, such as: ▪ flywheels, pulleys, belts, couplings, chains, cranks, gears, etc. ▪ feed mechanisms and auxiliary parts of the machine In-running nip points Point of Operation That point where work is performed on the material, such as cutting, shaping, boring, or forming of stock must be guarded. Rotating Parts 20 / 73 In-Running Nip Points 21 / 73 Rotating cylinders Belt and pulley Chain and sprocket Rack and pinion Classification of mechanical hazards 1. Crushing hazard through being trapped between a moving part of a machine and a fixed structure, such as a wall or any material in a machine; 2. Shearing hazard which traps part of the body, typically a hand or fingers, between moving and fixed parts of the machine; 3. Cutting or severing hazard through contact with a cutting edge, such as a band saw or rotating cutting disc 4. Entanglement hazard with the machinery which grips loose clothing, hair or working material, such as emery paper, around revolving exposed parts of the machinery. The smaller the diameter of the revolving part the easier it is to get a wrap or entanglement; SLIDE | 22 2 2 Classification of mechanical hazards 5. Drawing-in or trapping hazard such as between in-running gear wheels or rollers or between belts and pulley drives; 6.Impact hazard when a moving part directly strikes a person, such as with the accidental movement of a robot’s working arm when maintenance is taking place; 7. Stabbing or puncture hazard through ejection of particles from a machine or a sharp operating component like a needle on a sewing machine; 8. Contact with a friction or abrasion hazard , for example on grinding wheels or sanding machines; 9. high-pressure fluid injection (ejection hazard) for example, from a hydraulic system leak. SLIDE | 23 2 3 MACHINE SAFEGUARD Can be found at the point of operation, the power 24 transmission apparatus or at the area of transverse motion. TYPES OF GUARDS i. Fixed Guards A permanent part of the machine Usually made of sheet metal, screen, bars or other material which will withstand the anticipated impact Preferred type of guard. Fixed Guards 25 Advantages Limitations ▪ Can be constructed to suit Can be limited to specific many specific applications operations ▪ In-plant construction is often Machine adjustment and repair possible often require its removal, thereby necessitating other means of ▪ Can provide maximum protection for maintenance protection personnel ▪ Usually requires minimum maintenance ▪ Can be suitable to high production, repetitive operations ii. Interlocked Guard 26 Usually connected to a mechanism that will cut off the power automatically Could use electrical, mechanical or hydraulic systems Operation relies on a manual reset system Interlocked Guard 27 Advantages Limitations Can provide maximum Requires careful adjustment protection and maintenance Allows access to the machine May be easy to disengage for removing jams without time consuming removal of the fixed guards iii) Adjustable Guard 28 Very flexible to accommodate various types of stock. Manually adjusted Adjustable Guard 29 Advantages Limitations Can be constructed to suit Hands may enter danger area - many specific applications protection may not be complete at all times Can be adjusted to admit varying sizes of stock May require frequent maintenance and/or adjustment The guard may be made ineffective by the operator May interfere with visibility iv) Self-Adjusting 30 The opening is determined by the movement of the stock through the guard. Does not always provide maximum protection. Self-Adjusting 31 Advantages Limitations Off-the-shelf guards are often Does not always provide commercially available maximum protection May interfere with visibility May require frequent maintenance and adjustment FATALITIES Many fatalities have resulted from 32 employees getting caught in rotating shafts such as well boring drills, lathes & saw blades. UNSAFE CONDITIONS Transmission system Unguarded saw blade should be guarded POWER-DRIVEN MACHINES’ GUARDING Using a wire guard to stop the Using a gate system to keep hands out machine when a worker gets of the point of operation area. too close. The operator must push both This cable will stop the buttons at the top of the machine when it is pulled. machine to insure that his hands are not in the point of operation area The tripod type bar on top This safety bar will stop the of this machine can be machine if the worker gets too grabbed by a worker to stop close to the operation area. the machine. A shield of safety glass prevents sparks and particles from striking the worker. The operator must press This operator has wrist cuffs both of the control attached to her arms to keep her from putting them in harms way. buttons at the same time to operate this press. 38 Forklift Safety HAZARD AND RISK MANAGEMENT OF FORKLIFT FORKLIFT SAFETY Forklifts are useful for moving raw materials, tools and equipment in many industries. These accidents result from: Lack of operator training Poor maintenance of the forklift No safe systems of work OPERATORS Selection of operators Physical and mental fitness Training Basic, job specific & familiarisation Authorisation to operate Written permission Driver competency – Certificate & continuous assessment Lockable ignition & key holder MAINTENANCE Must do daily checking on system & main components System : Components : Hydraulics Tyre pressure Brakes Brakes / hand break Battery Horn Lights Steering Lights / beacon Fuel SYSTEM OF WORKS DO NOT! : Pick up a load if someone is standing close Allow people to walk underneath the load Try to pick up an unsuitable load Leave a lift truck unattended with the engine running Drive forward if visibility is impaired by a load. How to operate a Forklift Safely 41 / 60 Keep arms and legs inside the truck MOSH - MATERIAL HANDLING Handle only stable loads Keep speed low - you may have to stop Be careful when making sharp turns with a raised load If a load blocks your view, travel in reverse No riders, unless there’s an approved seat Don’t drive with forks raised Wear safety belts or other restraint devices How to drive the forklift on an 42 / 60 incline/ramp? When driving an empty truck, travel in reverse up an incline, and forward down an incline. Always make sure the forks pointing downhill/downwards If you are driving a loaded truck, travel forward up an incline, and backward down an incline. Always make sure the forks pointing uphill/upwards Forklift hazards 43 Overturning Overloading Collisions Silent operation of the electrically powered forklift truck – can make pedestrians unaware of its presence Uneven road surface Overhead obstruction Loss of load DO’S: Only issue keys to authorised drivers On completion of work, park the forklift in designated area Be careful with pedestrians / obey site rules / speed limits Sound horn at potential danger spots Stop before entering a building, sound horn then proceed Avoid violent breaking Always travel with the forks roughly 150 mm above ground level Before raising a load check overhead for obstructions. 45 THANK YOU