Palm Beach County Fire Rescue Driver Operator Manual PDF
Document Details
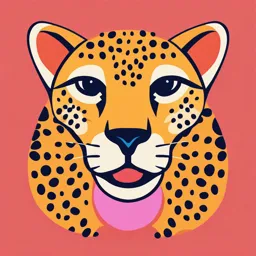
Uploaded by AstonishedOnomatopoeia
Palm Beach State College
2021
Melissa V. Watson & Douglas B. Watson
Tags
Related
- Chesapeake Fire Department Apparatus/Vehicle Backing Policy PDF
- Manual de Autoescala Giratoria DLK 23-12 Vario CC (PDF)
- Hoffman Estates Fire Department Fire Scene Operations - 015 PDF
- Phoenix Regional Fireground Safety Procedures PDF
- Buffalo Fire Department Operations Manual - PDF
- Palm Beach County Fire Rescue Driver Operator Manual PDF
Summary
This is a driver operator manual for Palm Beach County Fire Rescue. It covers emergency driving, water sources, fireground hydraulics, drafting, foam operation, tools and equipment, vehicle maintenance, and pump testing. It is based on the 8th edition, published in 2021.
Full Transcript
This Page Intentionally Left Blank 2 Palm Beach County Fire Rescue Driver Operator Manual Table of Contents Introduction Chapter 1 Emergency Driving (...
This Page Intentionally Left Blank 2 Palm Beach County Fire Rescue Driver Operator Manual Table of Contents Introduction Chapter 1 Emergency Driving (EVOC) & Apparatus Positioning Chapter 2 Water Sources Chapter 3 Fireground Hydraulics Chapter 4 Drafting Chapter 5 Foam Operation Chapter 6 Tools and Equipment Chapter 7 Vehicle Maintenance Chapter 8 Pump Testing Compiled and written by: Melissa V. Watson, Captain, Training and Safety Division, Palm Beach County Fire Rescue, & Douglas B. Watson, Retired Captain, Training & Safety Division, Palm Beach County Fire Rescue 8th Edition, Copyright © 2021 3 This Page Intentionally Left Blank 4 Palm Beach County Fire Rescue Driver Operator Manual Introduction The intent of this manual is to provide a foundation from which all Driver Operators should work and reference. This condensed and comprehensive guide addresses many subjects associated with fire service hydraulics and pumping apparatus. Additional resources can be found in the following publications: IFSTA Pumping Apparatus, Driver/Operator Handbook NFPA 1002, Standard for Fire Apparatus Driver/Operator Professional Qualifications NFPA 1901, Standard for Automotive Fire Apparatus NFPA 1906, Standard for Wildland Fire Apparatus NFPA 1911, Standard for Service Tests of Fire Pumps on Fire Apparatus NFPA 24, Private Fire Service Mains and their Appurtenances (Hydrants) NFPA 1142, Dry Hydrants PBCFR Hose Manual PBCFR Pump Testing Guide One of the best qualities a Driver Operator (DO) can possess is common sense and the ability to troubleshoot problems. Being able to think fast and calculate accurately, knowing the abilities and limitations of your apparatus, knowing how to troubleshoot your equipment, and being able to improvise in a moment’s time, are all desirable traits of a DO. Remember when something won’t start, flow, pump, or isn’t there, your crew will be coming to you for help. It is essential that you, as the DO, know what is carried on the apparatus, how it works, and how to troubleshoot and overcome any problems. Making the right decisions will keep you from having to justify your actions. 5 This Page Intentionally Left Blank 6 Palm Beach County Fire Rescue Driver Operator Manual Chapter 1 Emergency Driving (EVOC) & Apparatus Positioning Firefighters are more likely to die traveling to or from a fire, than fighting one, and motor vehicles pose a greater hazard than flames”. ~National Fire Protection Association 7 Introduction Palm Beach County Fire Rescue units respond to nearly 150,000 calls per year. That coupled with travel to and from training, public education events, area familiarization, and so on, puts our personnel on the road and at risk on a daily basis. This chapter covers some basic skills and techniques to help reduce that risk, as well as important information on apparatus positioning. Each year, approximately 20-25% of all firefighter injuries and deaths are caused by vehicle collisions while responding to or returning from emergency calls. This is the second leading cause of death in firefighters. Some of the reasons for these incidents include: excessive speed, improper navigation through intersections, unfamiliarity with the apparatus, lack of seatbelt use, and lack of driver training. The first goal of any Driver Operator (DO) is to get the apparatus and crew to the scene in an expedient, safe and efficient manner. Simply put, we are no good to the citizens we serve if we do not safely make it to the call. Every PBCFR DO must comply with all Florida state motor vehicle laws, ordinances and regulations as well as all County driver rules, and relevant Department of Transportation (DOT) regulations. DOs must also abide by all departmental polices/procedures and Standard Operating Guidelines (SOG) governing the operation of emergency vehicles. Additionally, the DO must be familiar with the concepts of defensive driving, including: safe following distances, evasive maneuvers, and anticipating other driver’s actions. As a DO, it’s also important to understand reaction and braking times, and weight transfer of apparatus. Do not get complacent. Most accidents involving fire apparatus occur when you would least expect it - during daylight hours with dry road conditions. In the state of Florida, drivers of authorized emergency vehicles are not required to have a CDL (Commercial Driver’s License), but must possess a Class E license. DOs shall operate all fire apparatus and other departmental vehicles in a safe and defensive manner in accordance with PBCFR policies/procedures and SOGs and Florida State Statutes and laws. Recent legal decisions have held that a DO who violates these state statutes and/or laws can be held accountable and subjected to criminal and/or civil prosecution. It is your responsibility as the driver to exercise “due regard” for the safety of all persons and property. 8 Due regard – A reasonable careful person performing similar duties under similar circumstances would act in the same manner. Along with “due regard”, emergency vehicle operations shall at all times, be consistent with “reasonable safety” and Florida State Statutes. Reasonable safety – factors that must be taken into account when deciding whether the need to engage in emergency vehicle operation is “outweighed” by the potential risk(s) to the public if emergency vehicle operation is initiated. Reasonable safety shall be based upon all available information, including but not limited to: 1. Type of call; 2. Type of roadway, traffic and weather conditions; and 3. Any other factor(s), which could impact on emergency vehicle operation. The bottom line is that you can, and may, be held accountable for your actions. To improve your driving skills, the PBCFR EVOC Driving Course is available to any employee or company that wishes to use it. Contact the Driver Training Coordinator in the Training & Safety Division to schedule and reserve the course. A map of the course is provided below, and the elements of the PBCFR EVOC Driving Course are as follows: #1 – Lane Change #2 – Turn Around #3 – Serpentine (forward and reverse) #4 – Diminishing Lane #5 – Straight Lane (forward and reverse) #6 – Alley Dock #7 – Straight Lane #8 – Lane Change 9 10 Gross Vehicle Weights The average vehicle weights for apparatus in Palm Beach County Fire-Rescue are as follows: Freightliner Engine 33,000 E-One Typhoon Engine 38,000 Sutphen Engine 40,000 Aerial Apparatus 50,000 Tender 57,000 Brush Truck 28,500 Note: The weight of each unit is fully loaded with equipment, water, and crew. Keep in mind when driving these vehicles that they are extremely heavy and do not handle or stop as fast as the privately owned vehicle you drive. As a DO, it is important to be familiar with weight transfer, reaction time, braking time, and angle of approach/departure. Each of these things affects your handling of the vehicle. Another factor that you must consider is that fire apparatus is not only heavy, it is “top-heavy”, with a greater propensity for rollover. Responding to Emergencies Driving any fire apparatus is a privilege and a craft that you should continue to hone throughout your career. Sadly, driving is the second leading cause of firefighter fatalities. Here are some general driving guidelines to help keep you and your crew safe while driving any PBCFR apparatus. These guidelines are in accordance with general safe driving practices and PBCFR policy #FR-O-303 Vehicle Apparatus Safety and SOGs 110-01 Emergency and Non- Emergency Response and 310-01 Traffic Operations. Preparation One of the most important steps you can take toward being a good Driver Operator is to properly prepare for the job. At the start of each shift it is essential that you perform a thorough truck check and document any problems that you may find. From making sure all of the equipment is where it belongs and in proper working order to ensuring that your water tank is full - each step matters. In addition to performing a systematic truck check, be sure to adjust your seat and mirrors at the start of each shift, and make yourself familiar with the inside of the cab, before you drive. 11 Safe Driving Practices All Drivers of Fire Rescue vehicles shall comply with all Florida State Motor Vehicle Laws, ordinances and regulations as well as all County driver rules and relevant Department of Transportation (DOT) regulations. Drivers of emergency vehicles are exempt from certain traffic laws by Florida State Statutes. The exemptions, however, do not relieve the driver of an emergency vehicle from exercising “due regard” for the safety of all persons and property. Emergency vehicle operation shall at all times, be consistent with “reasonable safety” and Florida State Statutes. Reasonable safety – factors that must be taken into account when deciding whether the need to engage in emergency vehicle operation is “outweighed” by the potential risk(s) to the public if emergency vehicle operation is initiated. Reasonable safety shall be based upon all available information, including but not limited to: 1. Type of call; 2. Type of roadway, traffic and conditions; and 3. Any other factor(s), which could have an impact on emergency vehicle operation Each driver shall observe safe-operating procedures at all times so as not to endanger employees, the public, property or equipment. Each driver shall conduct a thorough walk- around inspection (Safety Circle Check) of the vehicle before the initial operation. ALL personnel shall wear a seat belt when riding in a Fire Rescue vehicle. Exceptions are authorized when the use of a seat belt interferes with patient care and when loading hose on a moving apparatus. 12 Drivers shall not move Fire Rescue vehicles until all persons on the vehicle are seated and secured with seat belts in approved, riding positions. In addition, while the vehicle is in motion, the donning and doffing of equipment, and personal protection clothing that requires removal of any restraining belt or other device, shall be prohibited. Riding on the tailboard/running board or any other location other than a designated seat of any Fire Rescue vehicle is expressly prohibited. Loose equipment shall not be permitted in the cab of the vehicle. Stations with an emergency traffic control device (traffic signal) must activate the signal for every emergency response made from that station. Non-emergency use of emergency traffic signals is prohibited. When responding to an emergency, the vehicle’s visual and audible warning devices shall be used to alert other vehicular and pedestrian traffic. For increased safety, ensure headlights are on when vehicle is in operation. When responding at night, turn off “wig wag” lights to keep from blinding oncoming traffic. Headlights should be illuminated in normal position (low beam). Units responding to emergency incidents should monitor the radio TAC channel to gather as much information as possible prior to arrival. Speeds in excess of the posted speed limit are authorized during emergency responses so long as responders and the public are not endangered. Driving into oncoming lanes is a last resort for extreme situations and should be done at slow rates of speed, using extreme caution. Under no circumstances shall a driver be permitted to use a communication device while responding to an emergency, even if the device is equipped with a hands- free device. Siren Use Believe it or not, there is an actual method to optimizing your siren use. Often, it’s not that people can’t hear us, it’s that they cannot tell where the sound is coming from. On top of that, drivers are distracted by cell phones, loud music, and are driving cars that are designed to have increased noise insulation. Understanding proper siren use may help you combat some of these challenges. Scientific studies have led to the following useful information in regards to siren use: Always use your siren when responding to an emergency. 13 Be aware that at 40 mph a siren can project 300 feet, at 50 mph you “outrun” your siren. Utilize “wail” mode, or the Federal Q. When approaching intersections, switch from “wail” to “yelp” between 200-300 feet before the intersection. Use air horns as you approach and travel through intersections. Intersection Safety When approaching an intersection being controlled by a stop sign, red traffic signal, or other traffic control device that requires the flow of traffic to stop, you must come to a complete stop and proceed only when the traffic flow and safety permits, clearing one lane of traffic at a time. When approaching an intersection being controlled by a green traffic signal, you should reduce the speed of the vehicle and cover the brake to a point where it could avoid a collision should the need to do so become necessary. When approaching large, heavily blocked intersections, consideration should be made about shutting off vehicle emergency lights and sirens so as not to force civilian vehicles out into the intersection at a red light. Limited Access Highways Emergency vehicles may make use of a “U” turn to gain entry to traffic traveling in the opposite direction when responding to emergencies on limited access highways (i.e., I-95, Florida’s Turnpike). USE EXTREME CAUTION! 14 For the safety of personnel in the vehicle, at no other times are “U” turns on limited access highways permitted. Emergency vehicles shall proceed to the next interchange or exit and turn around in a safe location. Exceptions would include excessive travel distances to next exit (i.e. next County.) Types of Emergency Response Code 1 – Response to be normal driving which does not require the use of emergency lights and siren. Code 2 - Activity as normal driving with the use of emergency warning lights only, for non-emergency response such as participation in parades, dignitary escorts, or other similar events. Code 3 – Response as the use of lights and/or siren when responding to an emergency call. Responding with Multiple Units When two or more units are traveling Code 3 together in the same direction, maintain a separation distance of at least 300 to 500 feet apart. Do NOT pass another emergency vehicle that is responding Code 3 with you. Use extreme caution at intersections. Anticipate other units approaching the intersection from another direction. When traffic warrants it, drive in the center lane, allowing traffic to pull off to both the right and left. 15 Keep the cab and compartment doors closed when not in use. Practice “good housekeeping” when operating on scene. Night Driving Techniques Dim dash and panel lights. Reduce speed. Keep headlights and windshield clean. Keep your eyes moving – scan the roadway. Skid Control Remove foot from the accelerator. Steer the vehicle in the same direction that you are skidding (“steer into the skid”). Do NOT brake! Slow and regain control. Tire Blowout Accelerate initially. Slow down. Signal intentions. Safely pull off the roadway. Apparatus Positioning on or Near Roadways The following recommendations regarding positioning of apparatus on or near roadways should be followed. Placement can be affected by weather, time of day, scene lighting, traffic speed and volume, hills, curves and other obstructions. If police have not yet arrived, first control oncoming vehicular traffic before addressing the emergency. Remember that smoke generated by fires can dramatically decrease visibility. Along with these general roadway safety guidelines, all Palm Beach County Fire Rescue personnel must complete the “Blocking Procedures at Roadway Incidents” training module on Target Solutions. 16 General Roadway Safety Personnel working in and around traffic shall wear department approved traffic safety vests at all times. For added visibility and safety, don traffic vest over your bunker coat. Wear your bunker gear and helmet when working at traffic accident scenes. Never turn your back on traffic! Never trust traffic! Always be aware of your surroundings! Limit your time on scene to what is required to complete the assignment. Mark with paint and move vehicles from the roadway whenever possible. Use the apparatus, emergency and scene lights, safety cones, flares and law enforcement personnel to gain control of traffic, redirect traffic, and protect the work zone. Avoid using firefighters to direct traffic if at all possible. Call for PBSO early to help with traffic control. Working at incidents that occur within intersections, use extreme caution. STAY ALERT and aware of your surroundings at all times. Assign someone as a “lookout” to act as a safety officer and keep an eye on traffic. Position apparatus at a 45-degree angle to the roadway between traffic and the work zone. Position apparatus to protect the loading area of transport vehicles and create a Safe Work Area. Take a minimum of one and a half (1.5) lanes of traffic to protect the Safe Work Area. Take more lanes if necessary to keep personnel and citizens safe. Turn the apparatus wheels away from the incident. 17 Chock wheels of the blocking apparatus. Traffic cones shall be deployed at 15 foot intervals upstream of the blocking apparatus with the furthest traffic cone approximately 75 feet upstream to allow adequate advance warning. On limited access highways, cones should be placed 150 feet upstream of the blocking apparatus to divert and direct traffic away from the scene. To accommodate this, it may be necessary to use additional cones off the Rescue, Law Enforcement, or other apparatus. Per PBCFR Dispatch Protocols, for any call located on a highway, regardless of the call type, an additional suppression unit will be dispatched for the purpose of blocking the incident and creating a Safe Work Area. If necessary, have PBSO close the roadway. Direct any ambulatory occupants off the roadway, keeping them out of harm’s way. While working on scene at night, turn the headlights off if the apparatus is facing oncoming traffic. Use flares to illuminate cones at night or in fog/smoke conditions. (Confirm that there are no fuel leaks first.) Use scene lights on the apparatus, or deploy scene lights to illuminate the work area. Be sure to place scene lights so they do not blind other drivers or oncoming traffic. When working near railroad tracks, always treat the tracks as active. Never stop or park on railroad tracks. Park on the same side of the tracks as the incident. 18 Fireground Positioning First due units set the stage for the remainder of the incident. Good initial placement will contribute to the successful outcome of any incident. This section addresses the positioning of pumping apparatus for fire attack and water supply. Because the topic of positioning specialty apparatus (Aerials, Tenders) can be complex, it will not be covered in this section, but is addressed in a separate class. Positioning of engines for relay and water shuttle operations is covered in Chapter 2 of this manual (“Water Sources”). There is no one set rule that applies to positioning of apparatus on the fireground. Rescue situations, water availability, apparatus exposure, method of attack, weather, terrain, positioning requirements of other apparatus, department SOG’s and tactical judgment are all deciding factors. General Fireground Positioning Guidelines Rescue is always the first priority on a fire scene. First arriving units must evaluate conditions and leave room for the aerial apparatus if necessary. Position apparatus so tools, equipment or ladders can be quickly deployed to complete a rescue. Water supply may dictate positioning. The engine should be able to connect to a hydrant and pump attack lines while operating in a safe and effective manner. Method of fire attack can govern placement: Operating in an offensive mode will warrant keeping the engine closer to the building to ensure the nozzle reaches the fire and tools and equipment are readily available to firefighters. A defensive operation may require the engine to be placed a greater distance from the structure. Take the collapse zone into consideration. The collapse zone is at least 1½ times the height of the building. Weather and wind direction should be taken into account. When possible, position the engine upwind of the incident. 19 Terrain can have a significant effect on apparatus placement. Given the choice, always choose a paved surface over an unpaved surface. Always try to keep a minimum of two wheels on the pavement at all times. Relocation potential must be considered. Conditions may change for the worse and you may need to re-position the apparatus. Apparatus that are not being used should be parked out of the way, or remain in the staging area so as to not interfere with fireground operations. Position the apparatus so that you maximize its use. Generally, the front of the building should be left available for the aerial apparatus, unless directed otherwise by the Incident Commander. Do not block the entire roadway. Maintain access for hose lines and later arriving apparatus. When laying supply lines be sure to move them off the roadway prior to charging them. Leave plenty of room for incoming units. Use cones to protect hose lines and control vehicular traffic near the incident. Stay clear of power lines that may fall and contact apparatus. Be aware of your surroundings. Power lines should be given adequate clearance. Park at least 25’ from the rear of any apparatus to allow enough room to remove the ground ladders and equipment from the rear compartments. Backing of Apparatus A large percentage of accidents involving fire apparatus occur while backing. These incidents have the potential to be quite serious, yet they are often easily avoidable. Whenever possible, drivers should plan their travel routes in advance to avoid backing. However, when backing is essential, we must ensure that it is safe to do so, and that the area is clear prior to backing any apparatus. The following guidelines shall be used in addition to those specified in PBCFR policy #FR-O-303 Vehicle Apparatus Safety regarding the backing of apparatus. 20 Backing shall be done only after the driver of the vehicle has performed a Safety Circle Check (walk around the vehicle) to ensure the line of travel is safe for backing. When backing a vehicle, the driver shall not back the same unless such movement can be made safely without interfering with traffic and/or any stationary object. When backing, the driver shall have the assistance of at least one Fire Rescue employee. The default place for this person to position themselves shall be to the rear of the vehicle being backed up, on the most appropriate side, and in such a position that the backup person is not in the path of the vehicle. If another Fire Rescue person is not available, the driver of the vehicle shall get out and visually inspect the area behind the vehicle before backing. Strict caution must be observed. Both the driver and the backup person shall have eye-to-eye contact with each other via the outside mirror of the vehicle. The driver’s window shall be down, and a portable radio shall be used by the backup person to ensure verbal communication with the driver. In EVERY backup situation, visual contact between the driver and the backup person shall be maintained. IF AT ANY TIME THE DRIVER LOSES VISUAL CONTACT WITH THE BACKUP PERSON THE DRIVER SHALL STOP IMMEDIATELY. The vehicle shall remain stopped until such time that visual contact is restored. When backing up a vehicle at night, the backup person should use a flashlight in a manner that allows the driver to see the spotter. Avoid shining the flashlight in the driver’s eyes or mirror. When backing any apparatus equipped with a back-up camera, do not use the camera if you have a backup person. It is imperative that you maintain eye contact with your back-up person at all times, and follow their directions. When a backup person is not available, the camera should only be used in conjunction with the vehicle’s mirrors. In addition to performing a Safety Circle Check, when backing any apparatus without a backup person, activate the emergency warning lights, and sound a short horn blast prior to backing as an added precaution. 21 PBCFR Backing Hand Signals To avoid confusion and maintain consistency throughout the department, the following hand signals shall be used by all Palm Beach County Fire Rescue personnel when performing the role of backup person, and backing any apparatus. Straight Back: One hand above the shoulders with palm toward face, waving back. Other hand at your side. (Left or right hand optional) Turn: Both arms pointing in the same direction. Driver will verbally advise the backup person which way the turn will be made. The backup person will then assist the driver in backing the apparatus. 22 Stop: Single arm fully extended above head with hand in a fist. Be sure to yell or radio the “stop” order loud enough for the driver to hear the warning. (Left or right hand optional) ***Refer to PBCFR policy #FR-O-303 Vehicle Apparatus Safety, SOG 110-01 Emergency and Non-Emergency Response and SOG 310-01 Traffic Operations for more information.*** 23 This Page Intentionally Left Blank 24 Palm Beach County Fire Rescue Driver Operator Manual Chapter 2 Water Sources 25 Introduction A DO must be able to obtain water from a variety of sources that may be available on or around the fireground. Adequate water supply is one of the most vital steps in ensuring success during fireground operations. To deliver water for fireground operations, the DO has several options: Tank Supply Hydrant Static Water Source (Drafting) Dry Hydrant Water Tanks or Cisterns Relay Pumping Water Shuttle Operations Nurse Tender Direct Pumping Modified Direct Pumping Folding/Dump Tank Operations Each of these options along with other important information will be discussed in detail throughout this chapter. Radio Designation As a Driver Operator working on E51 for example, your radio designation would be “Driver Engine 5-1”, the Officer’s designation would be “Engine 5-1”, and the firefighter would be “Firefighter Engine 5-1”. Tank Supply The amount of water available on each apparatus must be considered when making tactical decisions. Tank water on the fireground can quickly be depleted depending on the gallons per minute (GPM) being discharged. Apparatus in Palm Beach County Fire Rescue have the following water tank capacities: Engines 750 or 1,000 gallons Aerials 500 gallons Brush Trucks 500 or 750 gallons Tenders 3,000 gallons 600 series Brush Trucks 300 gallons Rescue Pumper 300 gallons When operating solely from tank water, the DO needs to accurately calculate how much time is available to firefighting crews and must notify them when the tank level drops to 50% full and again at 25% full. 26 When flowing 150 GPM from the onboard water tank, it will take approximately 5 minutes before running out of water (from a standard PBCFR Engine with 750 gallon water tank). It is strongly suggested that you do not supply more than 200 GPM unless you are connected to a secure water source. Master streams should not be supplied unless connected to a secure water source. The FDC should not be supplied until connected to a secure water source. When flowing from the water tank, notify command and crews when your tank water level is at 50%. When flowing from the water tank, you must notify command and crews when your tank water level drops to 25%, and perform an emergency evacuation. Emergency Evacuation Per PBCFR SOG 210-01 Communications and the PBCFR Incident Management System Operations Manual, the term “Emergency Evacuation” should be used to advise personnel of imminent danger requiring the evacuation of the scene or area to an established safe place (Rally Point). Once an Emergency Evacuation has been announced: The Communication Center shall sound the radio alert tones and advise all companies on the incident to evacuate the building immediately. This message shall be repeated twice. Emergency Traffic shall be in effect and all routine radio traffic shall cease. The units on scene shall blast their air horns intermittently (one to ten seconds blowing, followed by one to ten seconds of silence) for 50 seconds. All personnel shall immediately evacuate the building or area. All personnel shall report to their supervisor or a pre-designated area. It is the responsibility of the Incident Commander to follow SOG 220-01 Personnel Accountability and perform a PAR. Along the same lines, if at any time, the DO experiences any mechanical problem while pumping that requires the apparatus to be shut down, the DO shall immediately advise 27 the IC of the situation, and perform an Emergency Evacuation if deemed necessary. Hydrants Fire hydrants have been a reliable source of water supply for the fire service since the early 1800’s. While they’ve evolved since then, the purpose remains steadfast; to provide a pressurized water source for use in firefighting operations. In Palm Beach County alone, there are tens of thousands of fire hydrants accessible for fire department use. Each hydrant is equipped with two 2.5” side port openings, and one 4.5” front steamer opening. These openings are fitted with National Standard Thread (NST aka NHT), designed for use with standard fire hose. ***As a safety reminder, always stand behind the hydrant any time you are operating it. PBCFR provides hydrant data through the Water Source Locator software, which is located on the PBCFR Intranet and can be accessed from any PBCFR fire station computer. This system shows the location of the hydrant, and offers general information such as the static pressure and the expected flow in GPM. Within the system hydrants are color coded, and a legend is provided. Operational fire hydrants are represented with a green hydrant symbol -. Non-operational hydrants are designated with a red hydrant symbol -. Drafting sites and dry hydrants are also marked in the Water Source Locator System, and will be discussed later in this chapter. The capacity of fire hydrants is generally measured in GPM. The location, operation and flow of fire hydrants may influence fire department operations during a fire incident. When choosing a hydrant, the closest hydrant may not always be the “best” hydrant. It is possible that the closest hydrant may be too close to the fire and may put the safety of personnel and apparatus in jeopardy. Keep this in mind when positioning at a fire scene. Given the choice, a hydrant located on a large main is preferred over a hydrant located on a “dead-end” main. We generally do not know the size of the water main we are working from unless it is pre-determined on a Quick Access Survey (QAS). In an emergency, the Incident Commander (IC) can obtain water supply and fire flow information from the Communications Center, the Fire Operations Officer (FOO), by contacting the Water Officer, or by contacting the water department directly. Per policy #FR-B-103 Use of Fire Hydrants, in the event a fire emergency requires large fire flow, multiple hydrants, or a boost of hydrant pressure, the Incident Commander shall direct the Communications Center to notify the appropriate Water Utility Company. It is 28 important that the water utility company be notified of the exact location and needs at the time of the incident. This policy further states that each Battalion shall submit all hydrant water usage to the Water Officer on a monthly basis. The water use shall be documented using policy #FR-B-103 Attachment B, the “Monthly Hydrant Water Usage Log”. This shall include water used for tank refills, weekly truck checks, training exercises, and any emergency fire operations. If you find a fire hydrant that is in disrepair or out of service, your officer must notify the FOO, and the Water Officer using policy #FR-B-103 Attachment A, the “Fire Hydrant Non-Functional/Out of Service Notice”. When laying 5” supply lines from or to a hydrant, you should drive between 10 – 15 mph to prevent the couplings from dropping on the tailboard. **Do not exceed 15 mph. Once supply lines are on the ground you must take into account access for incoming apparatus. Remember each section of 5” hose weighs over 100 pounds dry weight. It’s imperative that supply lines are moved off to the side of the roadway before charging the hydrant. It’s important to know that throughout Palm Beach County, you may come across fire hydrants that are equipped with Captivater locking fire hydrant caps. These caps are identified by the stainless steel “Lock Barrel” that is located in the center of the cap. You must use a Captivater hydrant wrench to remove the caps from these hydrants. For this reason, every Palm Beach County Fire Rescue operational unit is outfitted with a Captivater hydrant wrench. If you are unfamiliar with the use of this hydrant wrench, please refer to the Quick Skill located in the Driver Operator folder in the File Center on Target Solutions. Note: When painted over, the lock barrels may be difficult to operate. You may need to chip some of the paint off to get the end of the Captivater wrench over the lock barrel or to pull the lock barrel out. 29 The city of Boynton Beach and other isolated areas of Palm Beach County have installed Sigelock fire hydrants as their primary pressurized water source. It is possible that you may encounter one of these hydrants if assigned to a station that neighbors the area. For this reason, Sigelock hydrant wrenches have also been distributed to PBCFR fire suppression apparatus. If you are not familiar with the operation and use of a Sigelock fire hydrant, please refer to the Quick Skill located in the Driver Operator folder in the File Center on Target Solutions. Reclaimed Water Flushing Hydrants These hydrants are identified by their unique shape and purple/pink color. The highly chlorinated reclaimed water is used for irrigation purposes. The hydrants are provided so the local utility company can periodically flush the system. Reclaimed water hydrants installed by Palm Beach County Water Utilities are equipped with a single 2½” discharge port with fire department threads (NST aka NHT) and are capable of discharging up to 500 GPM. These hydrants are not considered a secure water source. They should only be used as a last resort, until a secure water source can be established. Static Water Sources Another option for obtaining water is to draft from a static water source. Drafting is the process of raising water from a static source up and into a fire pump. Examples of static sources include the ocean, canals, lakes, ponds, swimming pools and portable folding/dump tanks. Drafting may be used to: supply water to attack lines, support water shuttle operations, or supply an engine in a relay operation. Before attempting to draft, it should be determined that the site is accessible, and there is a sufficient supply of water is available. Again, the Water Source Locator software is a useful tool in identifying reliable water sources for drafting. Reliable drafting sites are marked on the Water Source Locator with a blue hydrant symbol -. Drafting is discussed in detail in Chapter 4 of this manual (“Drafting”). Note: Periods of drought may affect known static sources; Water levels may be too low for use. 30 Dry Hydrants Dry hydrants are non-pressurized hydrants designed for use in a drafting application. They are permanently installed fixtures that are strategically placed alongside static water sources such as lakes, ponds, canals, etc. In areas where pressurized water systems are either unavailable, or lines are too small to support fire flows, dry hydrants may be used as the water supply. Each dry hydrant is tested and tagged annually, as is required by Palm Beach County Fire Code. Green tags represent dry hydrants that are fully operational and have passed the annual test. Red tags indicate a hydrant that has failed the annual test and therefore should not be used. Some dry hydrants are outfitted with an inline check valve between the steamer port and the water source. If there is a check valve present, it should be clearly marked as such “CV- No Back- Flush”. Dry hydrants that do not have a check valve must be back flushed prior to use, to dislodge and clear any debris from the strainer. If the dry hydrant has a check valve present, then you should not back flush it. Back flushing a dry hydrant that has a check valve will result in damage to the dry hydrant. To draft from a dry hydrant, you will use 6” hard suction, just as you would with a traditional draft. The fitting on a dry hydrant will either be 6” NST, or 4.5” NST. If it is the latter, you will need a 6” to 4.5” adaptor to make the connection to the hard suction. Once you’ve made your connections, and back flushed the pipe if necessary, the drafting operation is the same as obtaining a draft from any other static water source. Dry Hydrants are marked in the Water Source Locator system with an orange hydrant symbol -. 31 Water Tanks and Cisterns As development continues to expand across Palm Beach County it brings with it new challenges for the fire service. Many construction sites may be well into the building process, but the accompanying fire hydrants have yet to be installed. County fire inspectors are diligently working to confirm that these sites not only have some sort of water supply on location, but that they also have access roads capable of supporting fire department apparatus. In said situations, the county code requires contractors to provide a water tank capable of holding a minimum of 20,000 gallons of water. These tanks or cisterns must have visible signage clearly marking the tank as a fire department water supply. Furthermore, it must be located within 400 feet of the structure. Water tanks may come in a variety of shapes or sizes, but they should always be marked for ease of identification. As you can see, it’s important to know your zone and identify any unique water sources before you need them. Because these tanks are gravity fed, the incoming pressure will not be enough to support firefighting operations. To remedy this, you will need to pull a draft from these sources. If applicable, always ensure that any vent openings on the container are open prior to pulling your prime. This will aid in getting the draft. Although you may encounter anomalies, the connection to these water tanks is commonly outfitted with 4½” NST male threads like you would find on a fire hydrant steamer or a dry hydrant. If this is the case, you will need to use a 6” to 4.5” adaptor to make the connection to the hard suction as you would when using a dry hydrant. Rural Water Supply Operations In many of the rural western communities of Palm Beach County, pressurized water sources are scarce. For this reason, it is important for every driver to be familiar with 32 alternate means of rural water supply operations. When considering such operations, there is no one single solution for every fire scene. Each incident is unique, and each incident will dictate which tactics are optimal. The initial OIC will determine the most appropriate means for establishing an adequate water supply in rural areas, but as the DO it is your job to have an in depth understanding of each method. The four means of providing a continuous water supply for firefighting in Palm Beach County are: Relay Pumping, Modified Direct Pumping, Nurse Tender, and Folding/Dump Tank operations. Given the option, relay pumping is the preferred method of water supply as it provides a continuous uninterrupted water source. It is common for units to begin the initial fire attack with one method, and then transition to a relay during the incident. Locating Water Sources In many cases it may be difficult to locate the nearest water source, especially at night. Responding units can request assistance from the Communications Center to help with this. Both the Water Source Locator software and satellite mapping imagery are useful tools in identifying nearby water sources. The Water Source Locator provides the location and flow of fire hydrants, and the location of dry hydrants and static water sources. Relay Pumping In some situations, the water source may be remote from the fire scene, and in order to supply water to the fire a relay pumping operation must be established. Whether using a hydrant or a static water source, relay pumping involves pumping water through fire hose from the source to at least one other apparatus at the scene. The number of apparatus involved in a relay will depend on the length of the lay, and the fire flow needed to combat the fire. Any apparatus equipped with a fire pump can participate in the relay. The engine located at the water source is referred to as the “source” engine or pumper, and the engine located on the scene is referred to as the “attack” engine or pumper. Any apparatus placed between the source and attack engines are referred to as “relay” pumpers. It is always best to place the largest capacity pump at the water source. When relaying water, laying 5” supply lines is preferred, as it has less friction loss, and delivers the maximum GPM available. When laying lines for a relay pumping operation, it is essential that hose lines are placed off to the side of the roadway before being charged to maintain access and egress on the roadway for other units. While every situation is unique, when laying a 5” supply line from a hydrant, if the attack engine will be more than 500’ from the hydrant, a relay should be established by placing an engine at the source. This distance decreases to 300’ from the hydrant for 3” supply line. 33 When two pumpers are involved in a relay it’s a fairly simple operation, but when more apparatus are required it may be beneficial to appoint a Water Supply Officer (WSO). Although it is preferred, you are not required to be an “officer” to be appointed as a Water Supply Officer on a fire scene. What is essential is that the WSO be well versed in rural water supply operations and tactics. Relay pumping operations require good communication and often require excessive radio traffic, especially when setting up the relay. It may be beneficial to assign a separate TAC channel dedicated to water supply operations, so as to not interfere with other on scene communications. If a WSO is appointed, they should be the only one that communicates with the IC. Prior to establishing a relay, consideration must be given to the volume of water needed on the scene and the distance from the water source to the scene. When operating in a relay, each engine must maintain at least 20 psi residual pressure on their intake gauge. The pump discharge pressure (PDP) for each apparatus within the relay is calculated by adding the friction loss in the 5” (or 3”) supply line to the 20 psi residual pressure for the engine you are supplying. Simply put: PDP = Friction Loss + 20 psi Each driver in the relay must set their PDP based on this formula. Therefore, there are a few key things each driver must know prior to calculating their PDP. In order to figure out the friction loss, we must know the total GPM that is flowing, and the distance that you are pumping it to the next engine in the relay. Calculating friction loss will be discussed at length in Chapter 3 of this manual (“Fire Hydraulics”). Note: A starting pressure of 50 psi may be used when initially setting up the relay pumping operation. Calculate the actual PDP and adjust your pressure as soon as possible. Once all the apparatus are in place and hose connections are made the relay can begin. Each Driver Operator should have their intake bleeder valve open. Remember, relay pumping operations always begin at the source. The source engine begins by obtaining a water supply, and then relays it to the next engine in line. Depending on the situation, this may be to another engine in the relay (relay pumper), or directly to the attack engine. If the source engine is using a static source and is equipped with a governor, they should remain in “RPM” mode throughout the operation. All other units within the relay that are 34 equipped with a governor should be in “PSI” mode. All DOs should monitor the ground conditions under and around their apparatus during the operation. When shutting down a relay pumping operation, always start by shutting down the attack engine first, and then work backward toward the water source. Spacing of relay engines is important in that the goal is to have all engines in the relay operating at approximately the same RPM. This prevents any one apparatus from working too hard throughout the incident. The spacing of engines in a relay will be discussed further in Chapter 3 of this manual (“Fire Hydraulics”). A form of relay pumping known as “Pumping in Series” will be discussed further in Chapter 3 of this manual (“Fire Hydraulics”). Water Shuttle Operations A water shuttle operation is another means used to supply water to the fire scene when a reliable water source is not readily available. Water shuttles involve a process in which tenders, engines, or brush trucks deliver their load of water to the scene, travel to a fill site to reload with water, and then return to the scene to unload again. Shuttles are generally used when the water source is so remote from the emergency scene, that relay pumping is not practical. However, when given the choice between relay pumping or a water shuttle operation, relay pumping proves to be a more dependable choice. Much like relay pumping, a water shuttle operation requires ongoing radio communications and coordination between all units within the shuttle and the attack engine. It may be beneficial to appoint a Water Supply Officer (WSO). Again, you do not have to be an “officer” to be appointed as a WSO on a fire scene. Depending on the extent of the incident, the WSO may want to assign a dump site supervisor and a fill site supervisor. It is also recommended to request a separate TAC channel dedicated to water supply operations. Recall, only the Water Supply Officer shall communicate with the IC. In any water shuttle operation, making good decisions during set up is critical to a successful operation. Pre-incident planning may be helpful with this. Know your zone! The following are the three primary types water shuttle operations used by PBCFR in rural areas of Palm Beach County: Nurse Tender Operations Modified Direct Pumping Operations Portable Folding/Dump Tank Operations Nurse Tender Operations This method involves a tender that parks immediately adjacent to the attack pumper. The attack pumper begins fire attack from its onboard water tank. The first arriving tender then relays water to the attack engine using 5” supply line. A second tender, and 35 additional apparatus are used to shuttle water from the source and refill the nurse tender throughout the incident. Positioning of the nurse tender is crucial, as it must be easily accessible for incoming apparatus to refill the onboard water tank. The primary advantage of this method is that in many cases the nurse tender is so large that the fire is controlled before there is a need to refill the tank. However, it is important to know that this method is only recommended on short duration fires such as room and contents, garage fires, or shed fires. If it is anticipated that the incident will last for an extended period of time, crews should transition to a relay pumping operation. Also, if there is any potential for the incident to expand, a nurse tender should not be used. Note: The attack engine should keep its onboard water tank full at all times, so if the nurse tender runs out of water, the attack engine’s water tank may be used to withdraw crews until a water supply can be re-established. Direct Pumping This type of operation is a combination of Nurse Tender and Relay Pumping operations. It entails two apparatus supplying a single attack engine via a single 3” supply line using a siamese as shown in the illustration. Upon arrival, the attack engine lays a supply line going in to the scene. The next arriving engine and/or tender connects a siamese to the end of the supply line and begins to relay water to the attack engine from its onboard water tank. When the second supply unit arrives it connects to the open port on the siamese and pumps at half the pressure of the first engine/tender. In doing so, the water from the second supply apparatus remains static because the pressure on the clapper valve of the siamese will be greater from the first due apparatus. As the first due supply engine/tender runs out of water, the pressure will drop and the second supply unit will take over, increasing to the desired pump pressure. The empty apparatus disconnects and leaves to refill with water while another apparatus arrives in its place. The process is repeated throughout the incident. This method limits the water supply to the attack engine to 500 GPM due to the critical velocity of 3” hose, as discussed in Chapter 3 (Fireground Hydraulics). For this reason, PBCFR has adopted 36 Modified Direct Pumping as the preferred method of water supply in rural areas until a relay can be established. Modified Direct Pumping In a modified direct pumping operation, rather than being supplied by one apparatus at a time, the attack engine may be supplied by more than one unit at a time through multiple supply lines. This tactic takes into consideration the extent of the fire and the fire flow that will be required. For short duration structure fires such as room and contents, garage fires, and small shed fires modified direct pumping is an acceptable tactic. It uses all units on scene as supply pumpers, and is recommended for the first due response on confirmed structure fires in rural areas with limited water supply. The benefits of this tactic is that it may yield a water supply of 6000 gallons for initial fire attack from the water carried on two engines, two brush trucks, and a tender. There are a few important things that must be taken into consideration when using this method for water supply: For long narrow driveways or limited access areas, the attack engine should lay an initial supply line from the street toward the fire. Brush trucks should be positioned close to the attack engine but out of the way of other apparatus, since they may not be in use after their initial water tank supply is empty. Position tenders in an area that is free and clear of other apparatus for easier access and egress. Transition to a relay pumping operation as soon as possible if you anticipate that the incident will last for an extended period of time. Folding/Dump Tank Operations Folding/Dump Tank operations should not be the first choice of water supply in rural areas due to several limitations. However, it may be useful when a reliable water source is so far from the fire scene that setting up a relay pumping operation would be impractical. This method involves the process in which tenders, engines, or brush trucks deliver their load of water to a portable folding/dump tank placed at the scene, known as the “dump site”. These units then travel to a “fill site”, reload with water, and then return to the fire scene to dump again. This process is repeated throughout the incident, and the fill site 37 can either be a pressurized fire hydrant, or a static source. Detailed information on the “dump site” and “fill site” is discussed later in this chapter. Portable folding/dump tanks are carried on all PBCFR tenders and can hold up to 3000-3500 gallons The success of a Folding/Dump Tank operation depends on three key components: 1. Location of the dump site; 2. Location of the fill site; 3. Route travelled between the dump site and fill site. To assist with these decisions, pre-incident planning is imperative in all non-hydranted areas. The Communications Center may be helpful in gaining useful information on hydrant location and flow, draft site locations, and dry hydrant locations. Dump Site Considerations The dump site consists of one or more portable folding/dump tanks located at or near the emergency scene. The best dump sites are those located so that tender drivers can drive in a straight line, with minimal maneuvering. The first arriving tender shall connect directly to the attack engine and supply water as needed to allow time for the folding/dump tank operation to be established. Once the dump tank is set up, the tender can dump the rest of its water into it before heading to the fill site. As additional units arrive at the dump site they should be directed into position by a spotter to dump their load into the portable tank. To expedite the operation, tender drivers should remain inside the apparatus, and the spotter should operate the dump valve. Tenders are capable of dumping their entire water tank within 3-4 minutes. In fact, NFPA 1901 requires that all tenders be able to dump their tank at a minimum average flow rate of 1000 GPM for the first 90 % of the tank. 38 In some situations, the attack engine may draft directly from the dump tank and pump to its own attack lines. However, per PBCFR SOGs it is recommended that a supply engine should be placed at the folding/dump tank to establish a draft and relay water to the attack engine using 5” supply line. When drafting from a folding/dump tank apparatus should use 6” hard suction and a low level strainer whenever possible. Low level strainers are carried on all PBCFR tenders and are capable of drafting water from a dump tank down to a level of about two inches. Placement of the dump tank is critical, keeping in mind the ease of access and egress for units within the water shuttle. Often, this may not be close to the fire. If a narrow driveway or dead end street limits access, it may be necessary to place the dump tank on the street or at the nearest intersection. Consider having PBSO close the roadway to the public along the water shuttle route. Limitations to be considered when performing a folding/dump tank operation: Setting up these operations can be time consuming and manpower intensive. The folding/dump tank requires a large, level, unobstructed area. If placed improperly, the folding/dump tank may block access for incoming apparatus. Requires a minimum of 2 tenders, in addition to engines and brush trucks shuttling water from the source to the folding/dump tank. Folding/dump tank operations cannot be used to supply master streams or aerial apparatus. At a flow rate of 300 GPM the dump tank will need to be refilled at least every 10 minutes to keep up with the discharge. Incidents that require flow rates in excess of 300 GPM are best served by multiple folding/dump tanks. A second low level strainer can be used as a jet syphon to move water from one dump tank to the next. In some cases, it may also be necessary to establish two or more independent water shuttle operations, for example “east shuttle” and “west shuttle”. Communication is key. During such incidents, a Water Supply Officer should be appointed to coordinate water supply operations and if at all possible every effort should be made to transition to a relay pumping operation. 39 Dump Site Tips: Place the dump tank on level ground whenever possible. This will optimize the amount of water the tank will hold. If time permits, place a salvage cover on the ground below the dump tank. This limits wear on the liner and may prevent punctures. The supply engine should flow a booster line or other small discharge back into the dump tank to ensure that they do not lose the prime as attack lines shut down. The supply and attack engines should keep their water tanks full at all times, to be used as a backup supply if needed. When drafting from a folding/dump tank, if possible, use a pump intake with a gated valve (MIV) to allow an uninterrupted transition from drafting to supplying the attack engine from your onboard tank water. It is recommended to use 2 sections of hard suction with the low level strainer when drafting from a dump tank. This gives the hose less tension and allows easy placement in the lowest part of the tank. The “spotter” should monitor the condition of the ground around the dump tank throughout the operation. Large open areas such as parking lots make good dump sites. Know your zone! Fill Site Considerations The purpose of the fill site is to reload the apparatus as quickly as possible, so they can return to the scene with a full tank of water. Although fill sites can either be located at a fire hydrant or a static water source, hydrants are the preferred method when available. The fill site should be selected with travel distance, capacity of supply, pressure of supply, and ease of access in mind. 40 When the fill site is located at a hydrant, the source apparatus should use 5” LDH as a supply line to maximize their water supply. If a static source is used the minimum pump capacity of the fill site apparatus should be 1250 GPM. It is optimal to choose a draft site that offers minimal lift to maximize the available water supply. Depending on the ease of access and egress, a cone may be placed at the fill site to be used as a marker, giving drivers a visual aid as to where they should position at the fill site. The cone should be placed so that when the driver stops the unit, the cone sits alongside the driver’s door. To expedite the operation, tender drivers should remain in the apparatus at all times. A “make and break” person should be assigned to the fill site, and is responsible for making and breaking all connections to and from the apparatus within the water shuttle. While 5” hose can move more water than 3”, due to the weight of the hose when it is full of water it’s more difficult to handle, and therefore more time consuming. With this in mind, it is recommended that two 3” hose lines be used to fill the apparatus as fast and efficiently as possible. A gate valve should be placed on each fill line, and the hose should remain charged at all times. Only one tender should be filled at a time, and ideally each tender should be filled at a minimum rate of 1000 gallons per minute. If there is limited access to the fill site, the “make and break” person may also need to double as a “spotter”, guiding the apparatus into position at the fill site before transitioning into the “make and break” role and filling the apparatus. Again, the driver should remain inside the apparatus, to expedite the operation and egress. Once each unit is full, they proceed to the dump site to dump their tank, and return to the fill site again. This process is repeated throughout the firefighting operation. A circular route of travel is considered the optimum arrangement when setting up a water shuttle operation. Paved roads are optimal, but not always an option in rural areas. The “make and break” person should periodically monitor the ground conditions around the fill site throughout the operation. Whether operating from a draft, or a hydrant, a booster line or other small discharge should be used to keep water circulating between fills. This will maintain the prime, and keep the pump cool. 41 If the fill site is a static source, when the operation is complete all pumps and equipment should be back flushed to clear any debris. This should be done before returning to service. Tender Apparatus Considerations Each tender carries 3000 gallons of water. Tender apparatus carry extra foam and SCBA bottles for on-scene replenishment. Due to its large size it may be advantageous for the tender to back down a roadway. Some PBCFR tenders have the ability to dump their water tank from either side of the apparatus and/or from the back of the unit. Other Rural Water Supply Considerations For all working structure fires in rural areas, a second tender should be requested during the initial response. Until a secure water source can be established and a relay put into place, it is not recommended to use master stream devices or aerial apparatus. When estimating hose lays in rural areas, a standard 1 ¼ acre lot is approximately 200’ feet in width. Whenever possible, assure that any supply line laid out is kept to one side of the roadway to allow access for later arriving apparatus. Due to the limited road size in rural areas, whenever possible all apparatus should be positioned so as not to block future access of incoming apparatus, especially during water shuttle operations. A typical single family dwelling requires an average fire flow between 250 to 500 GPM. A typical single family dwelling requires an average of 2,000 to 10,000 gallons of water to extinguish. 42 Flow Calculation For all water shuttle operations, the Incident Commander or Water Supply Officer may determine how many gallons per minute each tender can provide by using the following formula: V/ (A + B + C) = GPM V = Tender gallons A = Time to connect to supply and empty (minutes) B = Time to connect and fill tank (minutes) C = Driving time (minutes) *** For optimal ISO ratings, the first tender must begin dumping water within 5 minutes of the first pumper’s arrival at the fire scene. The pumper must continue to be supplied with a minimum of 250 GPM for two hours. *** Float-a-pumps In areas where a draft site is inaccessible, the use of float-a-pumps may be necessary as a last resort for water supply. Float-a- pump operations have the following limitations: Carried on PBCFR Brush Trucks. Capacities vary from unit to unit. It is recommended that a minimum of two high volume float-a-pumps be used to relay water. Place the source pumper as close as possible to the float-a-pumps. Float-a-pumps must be monitored at all times, to maintain fuel levels, and ensure that the strainer remains free of clogs. Never leave a Float-a-pump unattended on a fire scene. The following illustration is an example of Float-a-pump operations. 43 Float-a-Pump Operations ***Refer to PBCFR SOG 420-10 Rural Water Supply for Structural Firefighting for more information.*** 44 Palm Beach County Fire Rescue Driver Operator Manual Chapter 3 Fireground Hydraulics 45 Introduction In addition to driving the fire apparatus to and from the emergency scene, the DO is also responsible for operating the fire pump and possessing a thorough knowledge of all the tools and equipment carried onboard. Much of the material contained in this chapter is the result of actual test data that was developed by PBCFR personnel using PBCFR equipment. Testing our own equipment, fire hose, nozzles, and appliances is beneficial to us in several ways. Primarily, we can be certain that the flow, force, and/or pressure is safe and practical to what we use here at Palm Beach County Fire Rescue and that our crews are achieving the proper GPM at the nozzle. To produce effective fire streams, an extensive knowledge of hydraulics is essential. This chapter will help provide you with a system for developing effective fire streams and an understanding of fire stream management. An adequate supply of water delivered properly is essential for successful extinguishment. Any delay, or inadequate supply of water, will greatly jeopardize fireground operations and the safety of crews working at the fire scene. Abbreviations The following are common abbreviations that are used in fireground hydraulics and throughout this manual: AL Appliance Loss d Diameter EL Elevation Loss/Gain FDC Fire Department Connection FL Friction Loss TPL Total Pressure Loss GPM Gallons per Minute NP Nozzle Pressure NR Nozzle Reaction psi Pounds per Square Inch PDP Pump Discharge Pressure Q GPM/100 LDH Large Diameter Hose L Length/100 Definitions of Terms Driver Operators must understand the following definitions as they relate to fire service hydraulics: Appliance: Term applied to any wye, siamese, ground monitor, reducer, adaptor, fitting or other piece of hardware used in conjunction with fire hose for the purpose of delivering water. Back Pressure (also known as “Head Pressure): Pressure generated by the weight of a column of water above the pump (.434 psi per foot of elevation). 46 Discharge: The quantity of water issuing from an opening expressed in gallons per minute (GPM). Drafting: The process of raising water from a static source to supply fire apparatus. Elevation Pressure: Pressure that is gained or lost due to elevation (.434 psi rounded up to.5 psi per foot). Engine: Also known as a “Pumper”. The most basic type of fire apparatus consisting of a fire pump, water tank, and fire hose. Fire Department Connection: A device to which a pumper connects to boost or supplement the water flow in a sprinkler or standpipe system. Flow Pressure: Pressure created by the rate of flow or velocity of water coming from a discharge opening (measured using a pitot gauge). Force: A measurement of weight that is expressed in pounds. Friction Loss: Loss of pressure created by the turbulence of water moving against the interior walls of fire hose, piping, or appliances. Master Stream: A large caliber hose stream capable of flowing 350 GPM or more. Normal Operating Pressure: Pressure on a water system during regular domestic consumption. Nozzle Pressure: Pressure at which water is discharged from a nozzle. Nozzle Reaction: Force directed back at a person or device holding a nozzle by the velocity of water being discharged, measured in pounds. Pitot Gauge: Instrument that is inserted into a stream of water to measure the velocity flow pressure of a stream. Pressure: Force per unit area, measured in pounds per square inch (psi). Residual Pressure: That part of the total available pressure not used to overcome friction loss or gravity while forcing water through fire hose, piping, and appliances. It is the pressure remaining when water is flowing. Siamese: Hose appliance that combines two or more lines into one, fitted with two or more female inlets, and one male discharge. 47 Static Pressure: Stored potential energy available to force water through fire hose, piping, and appliances. Static means at rest or without motion. Velocity: Speed at which water travels through fire hose, piping, and appliances, measured in feet per second (FPS). Water Hammer: Force created by the rapid deceleration of water, generally resulting from closing a nozzle or valve too quickly. Wye: Hose appliance with one female inlet and two or more male outlets that are usually gated (known as a gated wye). General Principles and Measurements Because water is the most common extinguishing agent, a basic understanding of its physical properties is essential. The following principles and measurements are commonly associated with fireground hydraulics: 1 cubic foot contains 1728 cubic inches 1 cubic foot contains 7.48 gallons 1 gallon contains 231 cubic inches 1 gallon of water weighs 8.34 pounds 1 cubic foot of water weighs 62.4 pounds 1 psi will raise a 1 square inch column of water 2.304 feet A column of water 1 foot high exerts a downward pressure of.434 psi A column of mercury 1 inch high exerts the same downward pressure as 13.55” of water A 50 foot section of 1¾” hose contains 6.3 gallons & weighs 72.5 pounds (including the weight of the hose - Hi-Combat & Ponn Conquest) A 50 foot section of 2½” Hi-Combat hose contains 16.9 gallons & weighs 173.7 pounds (including the weight of the hose) A 50 foot section of 2½” TruID 2.5 hose contains 12.8 gallons & weighs 136.8 pounds (including the weight of the hose) A 50 foot section of 3” hose contains 18.4 gallons & weighs 195.3 pounds (including the weight of the hose) A 100 foot section of 5” hose contains 102 gallons & weighs 955 pounds (including the weight of the hose) Principles of Pressure There are six basic principles of pressure relevant to the study of fire service hydraulics. 48 1st Principle: Fluid pressure is perpendicular to any surface on which it acts 2nd Principle: When a fluid is at rest, fluid pressure is the same in all directions 3rd Principle: Pressure that is applied to a confined fluid from without is transmitted equally in all directions 49 4th Principle: The pressure of a liquid in an open container is proportional to its depth Mercury 5th Principle: The pressure of a liquid in an open container is proportional to the density of the liquid 50 6th Principle: The pressure of a liquid on the bottom of a container is independent of the shape of the vessel 5 Types of Pressure Static Pressure: Water at rest or not moving. Flow Pressure: The velocity of water coming from a discharge opening. Residual Pressure: Pressure remaining when water is flowing. Elevation Pressure: Pressure gain or loss due to elevation. Atmospheric Pressure: Pressure exerted by the air surrounding us (14.7 psi at sea level). Finding the Area “Area” is expressed in “square” units. Generally, in the fire service square miles, acres, feet or inches are used. It may be necessary to determine the “area” of a container, building or geographical area. This is done by measuring two dimensions, the length and the width and then multiplying the two. Be sure to convert all measurements to the same units prior to multiplying them, i.e.; inches, feet, etc. Q: What is the area of a building that measures 120’ wide and is 225’ long? A: Area = 120 x 225 = 27,000 square feet. Finding the area of a circle is done by using the formula: Area = 0.7854 x d2 In this formula, “d” represents the diameter of the circle. As in all conversion problems, start by converting all measurements to the same units prior to doing any multiplication, i.e.; inches, feet, etc. 51 Diameter is measured across the middle of a circle from edge to edge Q: What is the area of a smooth bore tip that has a 2” diameter? A: Area = 0.7854 x 22 = 0.7854 x 4 = 3.14 square inches While this may seem irrelevant at the moment, you will see that using these formulas to build from we are able to find the amount of water flowing and necessary fire flows at any given incident. Finding the Volume Sometimes it may be necessary to find the “volume” of a container such as a pool, drafting tank or even a structure. “Volume” is expressed in “cubic” units. To calculate volume, multiply the three dimensions: length, width, and height of an object (L x W x H). Again, be sure to convert all measurements to the same units prior to doing any multiplication, i.e.; inches, feet, etc. Q: What is the volume of a box measuring 10” by 14” by 4”? A: Volume = 10 x 14 x 4 = 560 cubic inches. To determine how many gallons of water this container will hold, remember there are 231 cubic inches in one gallon. Therefore, we divide 560 by 231 and the answer is 2.42 gallons. To take it a step further, we can also calculate the weight of water within this container. Each gallon of water weighs 8.34 pounds. Therefore, the weight = 2.42 x 8.34 = 20.18 lbs. Q: What is the volume of a container 42” by 10’ by 24”? A: First, convert all measurements to inches or feet. Volume = 42” x 120” x 24” = 120,960 cubic inches 52 To determine how many gallons of water this container will hold, remember there are 231 cubic inches in one gallon. Therefore, we divide 120,960 by 231 and the answer is 523.64 gallons. To take it a step further, we can also calculate the weight of water within this container. Each gallon of water weighs 8.34 pounds. Therefore, the weight = 523.64 x 8.34 = 4367.16 lbs. Finding the Volume of a Cylinder The volume of a cylinder can be found by first determining the area of the circle, and then multiplying the answer by the length. Volume = 0.7854 x d2 x length Be sure to convert all measurements to the same units prior to doing any multiplication, i.e.; inches, feet, etc. Q: What is the volume of a cylindrical tank that has a 10’ diameter and is 5’ long? A: Volume = 0.7854 x 102 x 5 0.7854 x 100 x 5 0.7854 X 500 = 392.7 cubic feet To convert this to gallons, remember that one cubic foot contains 7.48 gallons. Therefore, we multiply 392.7 by 7.48 and the answer is 2937.4 gallons. **Food for thought, a 1⅛" tip (250 GPM) literally flows one ton of water every minute.** Friction Loss Friction loss is pressure used to overcome resistance while forcing water through fire hose, pipes, and appliances. Each friction loss calculation is based on 100 feet of hose, but before you can figure out the friction loss, you must know the following factors: the volume or quantity of water flowing (expressed in GPM) the size of the hose the length of the lay Friction loss is independent of pressure when the GPM remains constant in the same size hose. In other words, if 200 GPM is flowing through a 2½” hose line at 50 psi, the friction loss will remain the same if the pressure is increased to 100 psi. Smaller hose creates more friction than larger hose when flowing the same amount of water. This is because in smaller hose, more of the water comes in contact with the sides of the hose, thus creating more friction. 53 When the GPM remains constant, if the length of the hose lay is doubled, then the friction loss will double. For example, 100’ of 1¾” flowing 100 GPM has 15 psi friction loss, therefore 200’ of 1¾” flowing the same GPM will have 30 psi friction loss. Other factors that affect friction loss in hose lines are: Rough linings inside fire hose Sharp bends or kinks Improper or protruding gaskets Appliances Partially closed valves Friction Loss Calculations While working in the field, it is necessary for Driver Operators to perform quick calculations when figuring out the friction loss in varied hose lines. Each calculation is based on 100 feet of hose. There are many ways to estimate the friction loss in fire hose. Methods like the old hand, new hand, drop 10, and the condensed Q are just a few that you may be familiar with. Conceivably, the most accurate method to determine friction loss is to conduct your own tests. By doing so you will know, with almost exact certainty, the volume of water flowing at specific pressures. Additionally, this enables us to have consistency in friction loss calculations department wide. The 1¾” pre-connected hand lines used by PBCFR are 200’ in length, and the hose is manufactured by Ponn Conquest. This hose is color coded to match the nozzle, so each pre-connected attack line is easily identifiable from the pump panel. Several tests were conducted on this hose to determine the average friction loss per 100’ of hose. Here are the findings of those tests: Friction Loss in 1¾” Ponn Conquest Hose GPM Friction Loss in 100’ 100 15 psi 150 20 psi 185 25 psi 200 35 psi Friction Loss in 1¾” Hi-Combat Hose GPM Friction Loss in 100’ 100 12 psi 150 24 psi 185 36 psi 200 40 psi 54 Calculating Friction Loss in 3” Hose – Q² x L (“Condensed Q” Method) An easy way to calculate friction loss in 3” hose is to use the Q² x L Method, also known as the Condensed Q Method. This is the preferred field method for calculating friction loss in 3” hose at PBCFR. To use Q² x L, you must first understand what “Q” represents. Q = the GPM flow divided by 100. While this may sound complicated, once explained, you will see that it’s quite simple and easy to use. You simply drop any zeros and place a decimal point after the first digit. For example, for 400 GPM, Q = 4.0 For 250 GPM, Q = 2.5 Once you have determined what Q is, square Q (multiply it by itself) to find the friction loss per 100 feet of 3” hose. Squaring numbers is easy when Q is a full number such as 2,3,4,5, etc. For example, when the hose line is flowing 300 GPM, Q = 3. Q² = 3 x 3 = 9 Therefore, the FL in 3” hose flowing 300 GPM is 9 psi per 100 feet of hose. When Q is not a full number, for instance 2.5, 3.5, 4.5, 5.5, squaring numbers may seem like a daunting task in the field. However, there is an easy and reliable way to square a number that ends with “.5”. To do so, take the 1st digit of the GPM and multiply it by the next higher whole number. For example, for 250 GPM Q = 2.5. To square 2.5 without a calculator, rather than multiplying 2.5 x 2.5, you will take the 1st digit which is 2, and then multiply it by the next higher whole number which is 3. Using this method, the FL for 250 GPM = 2 x 3 = 6 psi per 100’. Another way to think of it is that you are rounding down and rounding up, and then multiplying the 1st digit from each. So if the flow is 350 GPM, Q = 3.5. You would simply round down to 300 GPM and round up to 400 GPM. Next, take the 1st digit of each, and multiply them to get your friction loss. In this example, 3 x 4 = 12 psi of FL per 100’. Friction Loss in 3” Hose (Average coefficient was determined to be:.72) GPM Friction Loss in 100’ 100 1 psi 150 2 psi 200 4 psi 250 6 psi 300 9 psi 350 12 psi 400 16 psi 450 20 psi 500 25 psi 55 Once you have the friction loss per 100 feet of hose, you now need to multiply that by L. L represents the length of the lay divided by 100. For example, if you have a 500 foot hose lay, L = 500/100 = 5. You now multiply the friction loss that you calculated times L. This will give you the total friction loss over the full length of the hose lay. For example, what is the friction loss in 300 feet of 3” flowing 400 GPM? FL = Q² x L Q² = 4 x 4 = 16 L = 300/100 = 3 Answer: FL = 16 x 3 = 48 psi ***3” hose is used for supplying apparatus with water, or as supply line for a ground monitor, or FDC. It should not be used as a hand line. The only exception would be if the 3" line was used as a stationary exposure line with a “Kelly Loop” in place.*** Calculating Friction Loss in 2½” Hose – 2 x Q² x L There are two types of 2.5” hose currently carried on PBCFR apparatus. The pre- connected hose used as a blitz line is manufactured by Angus and called Hi-Combat ®. This hose line is 200 feet long and pre-connected to the right rear discharge of our engines. The hose is green and white for easy identification on the fire ground. The second type of 2.5” hose carried on our apparatus is Tru-ID 2.5 ® which is manufactured by the Key Hose Company. A total of 200’ of Tru-ID 2.5 is carried on our apparatus in four 50’ bundles. Each bundle will be packed as a Denver Load for easy deployment. Although it is not limited to this, the primary purpose of this hose is to be used during standpipe operations. To calculate the friction loss in 2½” hose, begin by figuring out the friction loss as you would for 3” hose. The next step is to double the result. You now have the friction loss for 2.5” hose. For example, if you are flowing 200 GPM through 200’ of 2.5” hose, you will first calculate the friction loss for 3” hose, which is 4 psi per 100’. Next, simply double 4 psi to obtain the friction loss for 2.5” hose. In this case the friction loss is 8 psi per 100 feet of hose. Friction Loss in 2½” Hose (Average coefficient was determined to be: 1.68) GPM Friction Loss in 100’ 100 2 psi 150 4 psi 200 8 psi 250 12 psi 300 18 psi Once you have the friction loss per 100 feet of hose, you now need to multiply that by the length (L). Remember L represents the length of the lay divided by 100. For example, if you have a 200 foot hose lay, L = 200/100 = 2. You now multiply the friction loss that you calculated times L. This will give you the total friction loss over the full distance of the hose line. In the example above, the total friction loss in the hose would be 16 psi. 56 Q: What is the friction loss in 200 feet of 2.5” hose flowing 300 GPM? A: FL = 2 x Q² x L FL = 2 x (3 x 3) x L FL = 2 x 9 x L FL = 18 x L L = 200/100 = 2 Answer: FL = 18 x 2 = 36 psi Coefficient Method of Calculating Friction Loss – CQ²L When calculating friction loss in a classroom setting, the coefficient method of determining friction loss yields a more precise answer versus the Q2 or 2 x Q2 methods. When using the coefficient method, “C” represents a predetermined coefficient for the hose. “Q” represents the quantity of water/100 (GPM), and “L” represents the length of the hose/100. The table below lists the coefficients for the various hose sizes used at PBCFR. To achieve the most accurate answer, never round numbers when using this equation. Hose Size Coefficient 1¾” 10.8 2½” 1.68 3” 0.72 5” 0.08 Q. Using the coefficient method, calculate the friction loss in 350’ of 2½” hose flowing 150 GPM. A. Substituting the coefficient for 2½” hose into the CQ2L equation we have: FL = 1.68 x (1.5) 2 x 3.5 1.68 x 2.25 x 3.5 1.68 x 7.875 FL = 13.23 psi Q. Using the coefficient method, calculate the friction loss in 400’ of 3” hose flowing 300 GPM. A. Substituting the coefficient for 3” hose into the CQ2L equation we have: FL = 0.72 x (3) 2 x 4 0.72 x 9 x 4 0.72 x 36 FL = 25.92 psi Flows of less than 95 GPM Friction loss for flows less than 95 GPM is negligible in 1¾”, 2½”, 3”, and 5” hose. Therefore, when using the field method, if you are flowing less than 95 GPM, it is not necessary to calculate the friction loss. Flows at 95 GPM or more can be rounded up to 100 GPM and calculated accordingly. This includes flows through the foam educator, which will be discussed in detail in Chapter 5 of this manual (“Foam Operations”). 57 Friction Loss in 5” Hose – 5” Hand Method When calculating friction loss in the classroom setting, the preferred method for 5” hose is the coefficient method, as described above. However, when you are out in the field the coefficient method is impractical. For this reason, at PBCFR we use the 5” Hand Method to calculate friction loss in 5” hose in the field. To use the 5” hand method, simply look at the palm of your left hand. Beginnin