Chapter 6 Fuel Systems PDF
Document Details
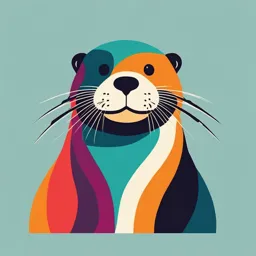
Uploaded by WiseCreativity
Singapore Polytechnic
Tags
Summary
This document details the fuel systems of aircraft, covering concepts like basic fuel system requirements, storage, and distribution, with diagrams, and safety measures for fueling.
Full Transcript
ME3531 Aircraft Systems Chapter 6: Fuel Systems For Training Purpose Only Official (Closed), Non-Sensitive Fuel Basic Fuel Systems Requirements All powered aircraft require fuel on board to operate the engine(s). A fuel sys...
ME3531 Aircraft Systems Chapter 6: Fuel Systems For Training Purpose Only Official (Closed), Non-Sensitive Fuel Basic Fuel Systems Requirements All powered aircraft require fuel on board to operate the engine(s). A fuel system consisting of storage tanks, pumps, filters, valves, fuel lines, metering devices, and monitoring devices is designed. The fuel system must meet the following; To provide an uninterrupted flow of contaminant-free fuel regardless of the aircraft’s attitude. Since fuel load can be a significant portion of the aircraft’s weight, a sufficiently strong airframe must be designed. Varying fuel loads and shifts in weight during maneuvers must not negatively affect control of the aircraft in flight. To construct and arrange to ensure fuel flow at a rate and pressure established for proper engine and auxiliary power unit (APU) functioning under each likely operating condition. To ensure no fuel pump can draw fuel from more than one tank at a time. There must also be a means to prevent the introduction of air into the system. A turbine engine powered airplane must meet applicable fuel venting requirements. To provide independence between multiple fuel storage and supply systems so that failure of any one component in one system will not result in loss of fuel storage or supply of another system. Page ▪ 2 For Training Purpose Only Official (Closed), Non-Sensitive Fuel Fuel Storage System Turbine Engine Fuel Each fuel system must meet the following; Able to withstand, without failure, the loads under likely operating conditions. Able to isolated from personnel compartments and protected from hazards due to unintended temperature influences. Fuel being jettisoned free of the airframe on Able to provide fuel for at least one- half hour of a transport category aircraft. operation at maximum continuous power or thrust and be capable of jettisoning fuel safely if required for landing. Fuel jettisoning systems are also referred to as fuel dump systems. Page ▪ 3 For Training Purpose Only Official (Closed), Non-Sensitive Fuel Aircraft Fuel Aircraft with turbine engines use a type of fuel known as jet fuel (Jet A, Jet B), turbine engine fuel is designed for use in turbine engines and should never be mixed with aviation gasoline. Various inhibitors are added into jet fuel to control corrosion, oxidation, ice, and microbial and bacterial growth. The choice of turbine engine fuel depends on a number of conflicting factors. While it is desirable to use a fuel that is low in volatility to resist vapor lock and evaporation while in the aircraft’s fuel tanks, turbine engine aircraft operate in cold environments. Turbine engines must start readily and be able to restart while in flight. Fuel with high volatility makes this easier. Page ▪ 4 For Training Purpose Only Official (Closed), Non-Sensitive Fuel Jet Transport Aircraft Fuel Systems Jet transport fuel systems can be regarded as a handful of fuel subsystems as follows: 1. Storage 2. Vent 3. Distribution 4. Feed 5. Indicating Boeing 777 fuel tank locations and capacities Storage Integral fuel tanks are the norm with much of each wing’s structure sealed to enable its use as a fuel tank. Center wing section or fuselage tanks are also common. These may be sealed structure or bladder type. The main and auxiliary fuel tanks, surge tanks may also be found on jet transports. These normally empty tanks located in the wing structure outboard of the main wing tanks are used for fuel overflow. A check valve allows the one-way drainage of fuel back into the main tanks. Surge tanks are also use for fuel system venting. Page ▪ 5 For Training Purpose Only Official (Closed), Non-Sensitive Fuel Jet Transport Aircraft Fuel Systems Vent Transport category fuel systems require venting with a series of vent tubing and channels exists that connects all tanks to vent space in the surge tanks (if present) or vent overboard. Venting must be configured to ensure the fuel is vented regardless of the attitude of the aircraft or the quantity of fuel on board. A fuel vent system with associated float and check Distribution valves that stop fuel and keep the tanks vented regardless of the aircraft attitude. A transport category aircraft fuel distribution subsystem consists of the following: Pressure fueling components Defueling components Transfer system Fuel jettison or dump system A central pressure refueling station on a transport category aircraft allows all Single-point pressure fueling at a fueling station accessible fuel tanks to be filled from one by ramp refueling trucks allows all aircraft fuel tanks to be position. filled with one connection of the fuel hose. Leading and trailing edge wing locations are common for these stations. Page ▪ 6 For Training Purpose Only Official (Closed), Non-Sensitive Fuel Jet Transport Aircraft Fuel Systems Feed The boost pumps move fuel into a transfer manifold. Opening the fuel valve on one of the tanks transfers the fuel into that tank. The transfer/crossfeed manifold and boost pumps are also used to jettison fuel overboard by opening the proper dump valves with a boost pump(s) operating. Additionally, the transfer/crossfeed system can function to supply the engines if the normal engine fuel feed malfunctions. The in-tank fuel boost pumps pump fuel under pressure through a shutoff valve for each engine. A manifold or connecting tubing typically allows any tank to supply any engine through the use of crossfeed valves. Boost pump bypasses allow fuel flow should a pump fail. Note that the engines are designed to be able to run without any fuel boost pumps operating. But, each engine’s Fuel system for the Boeing 727 Jet transport shutoff valve must be open to allow flow to the engines from the tanks. The engine fuel systems, have some means for heating the fuel usually through an exchange with hot air or hot oil taken from the engine. The fuel cooled oil cooler (FCOC) which not only heats the fuel but also cools the engine oil. Page ▪ 7 For Training Purpose Only Official (Closed), Non-Sensitive Fuel Jet Transport Aircraft Fuel Systems Indicating Fuel indicating systems on jet transport aircraft monitor a variety of parameters and it is shows on the instrumental panel or is displayed on the multifunction display (MFD). True fuel flow indicators for each engine are used as the primary means for monitoring fuel delivery to the engines. The temperature sensor is usually located in a main fuel tank and the fuel temperature indicates a warning light. The fuel filters have bypasses that permit fuel flow around the filters if clogged. A fuel filter bypass warning lights will be illuminated Low fuel pressure warning lights are also common on jet transport aircraft. The sensors for these are located in the boost pump outlet line. They give an indication of possible boost pump failure Fuel quantity gauges are important features on all aircraft. Indications exist for all tanks on a transport category aircraft. Often, these use a capacitance type fuel quantity indication system and a fuel totalizer (total fuel remaining in all the fuel tank). Page ▪ 8 For Training Purpose Only Official (Closed), Non-Sensitive Fuel Fuel System Components Fuel Tanks There are three basic types of aircraft fuel tanks: rigid removable tanks, bladder tanks, and integral fuel tanks. Aircraft fuel tanks have a low area called a sump that is Sumping a fuel tank with a fuel strainer designed as a place for contaminants and water to that is designed to collect the sump settle. The sump is equipped with a drain valve used to drain material in the clear cylinder to be remove the impurities during preflight walk-around examined for the presence of inspection. contaminants. Most aircraft fuel tanks contain some sort of baffling to subdue the fuel from shifting rapidly during flight maneuvers. Baffling in fuel tank Page ▪ 9 For Training Purpose Only Official (Closed), Non-Sensitive Fuel Fuel System Components Rigid Removable Fuel Tanks A rigid tank is made from various materials, and it is strapped into the airframe structure. The tanks are often riveted or welded together and can include baffles. Being able to remove and repair, or replace, a fuel tank can be a great convenience if a leak or malfunction with A typical rigid removable aircraft fuel tank and its parts. the tank exists. Bladder Fuel Tanks A fuel tank made out of a reinforced flexible material called a bladder tank can be used instead of a rigid tank. A bladder tank contains most of the features and components of a rigid tank. Bladder tanks must be attached to the structure with clips A bladder fuel tank or other fastening devices. for a light aircraft. Page ▪ 10 For Training Purpose Only Official (Closed), Non-Sensitive Fuel Fuel System Components Integral Fuel Tanks Transport category and high performance aircraft, part of the structure of the wings or fuselage is sealed with a fuel resistant two-part sealant to form a fuel tank. The sealed skin and structural members provide the highest volume of space available with the lowest weight. This type of tank is called an integral fuel tank since it forms a tank as a unit within the airframe structure. When an aircraft maneuvers, the long horizontal nature of an integral wing tank Baffle check valves.Fuel is prevented from requires baffling to keep the fuel from sloshing. The wing ribs and box beam flowing outboard during maneuvers. structural members serve as baffles and others may be added specifically for that purpose. Baffle check valves are commonly used. These valves allow fuel to move to the low, inboard sections of the tank but prevent it from moving outboard. They ensure that the fuel boost pumps located in the bottom of the tanks at the lowest points above the sumps always have fuel to pump regardless of aircraft attitude. Integral fuel tanks must have access panels for inspection and repairs of the tanks and other fuel system components. On large aircraft, technicians physically enter the tank for maintenance. When entering and performing maintenance on an integral fuel tank, all fuel must be emptied from the tank and Fuel tank access panel locations, and strict safety procedures must be followed. Fuel vapors must be purged from the typical fuel tank access panel seals tank and respiratory equipment must be used by the technician. Page ▪ 11 For Training Purpose Only Official (Closed), Non-Sensitive Fuel Fuel System Components Fuel Valves There are many fuel valve uses in aircraft fuel systems. They are used to shut off fuel flow or to route the fuel to a desired location. Manually-Operated Gate Valves A hand-operated gate valve used in transport category aircraft fuel systems. Fuel flow is controlled with a series of ON/OFF, or shutoff, type valves that are plumbed between system components. Hand- operated gate valves can be used, especially as fire control valves, requiring no electrical power to shutoff fuel flow when the emergency fire handle is pulled. The valves are typically positioned in the fuel feed line to each engine. Motor-Operated Valves The use of electric motors to operate fuel system valves to either allow fuel to flow or shut off flow to various tanks and aircraft An electric motor-driven gate valve engines. commonly used in large aircraft fuel systems. Page ▪ 12 For Training Purpose Only Official (Closed), Non-Sensitive Fuel Fuel System Components Fuel Pumps Aircraft are equipped with boost pumps to provide fuel under positive pressure to the engine-driven pump and during starting when the engine-driven pump is not yet up to speed for sufficient fuel delivery. In the event, boost pumps fail, the aircraft engine receive fuel by gravity-feed. A centrifugal fuel boost pump can be submersed in the fuel tank (A) or can be attached to the outside of the tank with inlet and outlet plumbing extending into the tank (B) Page ▪ 13 For Training Purpose Only Official (Closed), Non-Sensitive Fuel Fuel System Components Centrifugal Boost Pumps A centrifugal boost pump takes in fuel at the center of an impeller and expels it to the outside as the impeller turns. An outlet check valve prevents fuel from flowing back through the pump. A fuel feed line is connected to the pump outlet. A bypass valve may be installed in the fuel feed system to allow the engine-driven pump to pull fuel from the tank if the boost pump is not operating. The centrifugal boost pump is used to supply the engine- driven fuel pump, back up the engine driven fuel pump, and transfer fuel from tank to tank if the aircraft is so designed. The internal workings of a centrifugal fuel boost pump. Fuel is drawn into the center of the impeller Centrifugal fuel pumps located in fuel tanks ensure positive through a screen. It is moved to the outside of the pressure throughout the fuel system regardless of case by the impeller and out the fuel outlet tube. temperature, altitude, or flight attitude thus preventing vapor lock. The inlet of both types of centrifugal pump is covered with a screen to prevent the ingestion of foreign matter. Page ▪ 14 For Training Purpose Only Official (Closed), Non-Sensitive Fuel Fuel System Components Ejector Pumps Fuel tanks with in-tank fuel pumps, such as centrifugal pumps, are constructed to maintain a fuel supply to the engine driven pump inlet at all times. This ensures that the pump does not cavitate and that the pump is cooled by the fuel. The section of the fuel tank dedicated for the pump installation may be partitioned off with baffles that contain check valves, also known as flapper valves. These allow fuel to flow inboard to the pump during maneuvers but does not allow it to flow outboard. Some aircraft use ejector pumps to help ensure that liquid fuel is always at the inlet of the pump. A relatively small diameter line An ejector pump uses a venturi to draw fuel circulates pump outflow back into the section of the tank where the into the boost pump sump area of the fuel tank. pump is located. The fuel is directed through a venturi that is part of the ejector. As the fuel rushes through the venturi, low pressure is formed. An inlet, or line that originates outside of the tank pump area, allows fuel to be drawn into the ejector assembly where it is pumped into the fuel pump tank section. Together, with baffle check valves, ejector pumps keep a positive head of fuel at the inlet of the pump. Page ▪ 15 For Training Purpose Only Official (Closed), Non-Sensitive Fuel Fuel System Components Fuel Filters All aircraft fuel systems have filters and strainers to ensure that the fuel delivered to the engine(s) is free from contaminants. Two main types of fuel cleaning device are utilized on aircraft. Fuel strainers are usually constructed of relatively coarse wire mesh. They are designed to trap large pieces of debris and prevent their passage through the fuel system. Fuel Fuel tank outlet finger strainers strainers do not inhibit the flow of water. Fuel filters generally are usually fine mesh. Finger screens allow a large amount of debris to be trapped while still permitting fuel to flow. Turbine engine fuel control units are extremely close tolerance devices. It is imperative that fuel delivered to them is clean and contaminant free. The used of micronic filters makes this possible. The changeable cellulose filter mesh type can block particles 10–200 microns in size and absorbs water if it is present. The small size of the mesh raises the possibility of the filter being blocked by debris or water. Therefore, a relief valve is included in the filter assembly that bypasses fuel through the unit should pressure build up from blockage. A pop A typical micronic fuel filter with changeable cellulose filter element. indicator extends to indicate that the bypass valve is open. Page ▪ 16 For Training Purpose Only Official (Closed), Non-Sensitive Fuel Fuel System Components Fuel Heaters and Ice Prevention Turbine powered aircraft operate at high altitude where the temperature is very low. As the fuel in the fuel tanks cools, water in the fuel condenses and freezes. It may form ice crystals in the tank or as the fuel/water solution slows and contacts the cool filter element on its way through fuel filter to the engine(s). The formation of ice on the filter element blocks the flow of fuel through the filter. A valve in the filter unit bypasses unfiltered fuel when this occurs. An air-fuel heat exchanger uses engine compressor bleed air to warm the fuel on many turbine engine powered aircraft Fuel heaters are used to warm the fuel so that ice does not form. These heat exchanger units also heat the fuel sufficiently to melt any ice that has already formed. The most common types of fuel heaters are air/fuel heaters and oil/fuel heaters. An air/fuel heater uses warm compressor bleed air to heat the fuel. An oil/fuel exchanger heats the fuel with hot engine oil. Page ▪ 17 For Training Purpose Only Official (Closed), Non-Sensitive Fuel Fuel System Indicators Aircraft fuel systems utilize various indicators. All systems are required to have some sort of fuel quantity indicator. Fuel flow, pressure, and temperature are monitored on many aircraft. Various warning lights and annunciations are also used. Fuel Quantity Indicating Display Digital indicators are available that work with the same variable resistance signal from the tank unit. They convert the variable resistance into a digital display in the cockpit instrument head. Fully digital instrumentation systems, such as those found in a glass cockpit aircraft, convert the variable resistance into a digital signal to be processed in a computer and displayed on a flat screen panel. Digital fuel quantity gauges that work off of variable resistance from the tank unit Page ▪ 18 For Training Purpose Only Official (Closed), Non-Sensitive Fuel Fuel System Indicators Fuel Quantity Indicating Probes and Compensators Variable capacitance transmitters are installed in the fuel tanks extending from the top to the bottom of each tank in the usable fuel. Several of these tank units, or fuel probes as they are A fuel tank transmitter for a capacitance-type fuel quantity indicating system sometimes called, may be installed in a large tank. They are wired in parallel. As the level of the fuel changes, the capacitance of each unit changes. The capacitance transmitted by all of the probes in a tank is totalled and computed and display on quantity indicator in the cockpit. As the aircraft maneuvers, some probes are in more fuel than others due to the attitude of the aircraft. The indication remains steady, because the total capacitance transmitted by all of the probes remains the same. A compensator unit (mounted low in the tank so it is always covered with fuel) modifies current flow to reflect temperature A fuel quantity tank unit and compensator unit variations of the fuel, which affect fuel density and thus installed inside a wing tank. capacitance of the tank units. Page ▪ 19 For Training Purpose Only Official (Closed), Non-Sensitive Fuel Fuel System Indicators Fuel Quantity Using Drip Sticks The drip sticks, are mounted throughout each tank. When pushed and rotated, the drip stick can be lowered until fuel begins to exit the hole on the bottom of each stick. This is the point at which the top of the stick is equal to the height of the fuel. The sticks have a calibrated scale on them. By adding the indications of all of the drip sticks and converting to pounds or gallons via a chart supplied by the manufacturer, the quantity of the fuel in the tank can be ascertained A fuel drip stick Page ▪ 20 For Training Purpose Only Official (Closed), Non-Sensitive Fuel Fuel System Indicators Fuel Flowmeters A mass flow fuel flow indicating system used on turbine-engine aircraft uses the direct relationship between viscosity and mass to display fuel flow in pounds per hour. Fuel Temperature Gauges The pilot will be informed when fuel temperature approaches the possibility of ice formation in the fuel system, especially at the fuel filter. A low fuel temperature can be corrected with the use of a fuel heater if the aircraft is so equipped. A mass flow fuel flow indicating system Page ▪ 21 For Training Purpose Only Official (Closed), Non-Sensitive Fuel Fueling There are two types of fueling processes: over-the-wing refueling and pressure refueling. Over-the-wing refueling is accomplished by opening the fuel tank cap on the upper surface of the wing or fuselage, if equipped with fuselage tanks. The fueling nozzle is Over-the-wing refueling carefully inserted into the fill opening and fuel is pumped into the tank. Pressure refueling occurs at the bottom, front, or rear of the fuel tank. A pressure refueling nozzle locks onto the fueling port at the aircraft fueling station. Gauges are monitored to ascertain when the tanks are properly loaded. An automatic shutoff system may be part of the aircraft system. It closes the fueling valve when the tanks are full. This panel at the pressure refueling station has valve position switches and quantity gauges to be used during refueling Float Valve Page ▪ 22 For Training Purpose Only Official (Closed), Non-Sensitive Fuel Fueling Safety measures Always fuel and defuel outside, not in a hangar that serves as an enclosed area for vapors to build up to a combustible level. Clothing worn by refueling personnel should not promote static electricity buildup. Fire extinguishers should be on hand. Bonding cables should be attached to guard against static electricity buildup. Any open flame, such as a lit cigarette, must be extinguished. Operation of any electrical devices must be avoided. Radio and radar use is prohibited. Spilled fuel poses an additional fire hazard Page ▪ 23 For Training Purpose Only