Art of Reading Buildings PDF
Document Details
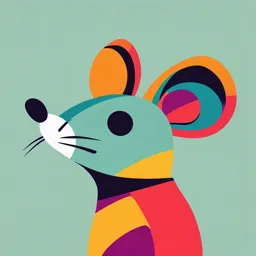
Uploaded by BalancedImpressionism
Montgomery College
Tags
Summary
This document provides an overview of building concepts, including loads, types of loads, and primary forces. It details the properties and uses of different building materials, such as wood, steel, and concrete.
Full Transcript
Art of Reading buildings Ch 2 Building Concepts - Loads - static or dynamic - gravity is responsible for most of the load and is trying to atten the building regardless of re - Dead load - building + anything permanently attached to it - Live Loads - transient, mo...
Art of Reading buildings Ch 2 Building Concepts - Loads - static or dynamic - gravity is responsible for most of the load and is trying to atten the building regardless of re - Dead load - building + anything permanently attached to it - Live Loads - transient, moving, impacting or static (furniture) - Types of Loads - Concentrated - at one point - Distributed - carried over multiple points of building - Impact - moving or sudden ( weather, crowds, streams) - Repeated - intermittent (people on escalator) - Static - rarely move - Suspended - hanging from something - Wind/Snow - atmospheric loads - Fire load - used to estimate BTU - re service only - Note: Roof cut can be live, impact or distributed load 3 Way Loads are Imposed 1. Axial - through center of material 2. Eccentric - o center causing material to want to bend 3. Torsion - cause material to twist 3 Primary forces from loading material 1. Compression - attens or crushes 2. Tension - pull apart or stretch 3. Shear - tear or slide apart - Note: Materials must be able to transfer load to the earth in the form of compression (guide wires are the exception and force is applied in tension or shear) - Surface-to-mass ratio - amount of heat that can be absorbed before breaking down - - More mass to relative exposed surface area the more re resistive it is ff fl fi fi fi fl - High Surface-to-mass ratio means less burn time - - modern engineering - example sheathing - Note: as material degrade they change shape and distribute load di erently and may fail rapidly Engineers - New buildings are high strength low mass - Brittle - fracture or fail when stressed or deformed - breaks before bends - Ductile - bend, de ect or stretch as a load is applied - bends before breaks - Building industry is the second leading user of plastics to shipping Building materials Wood - Pine can be cut 25 years after it is planted - Old growth is denser - 1986 Wood grading system changed 3,2,1(best) - Nominal vs full dimensional lumber - Mass is lost when wood burns - Wood showed signs of collapse in the past compared to today - Glulam - small cut lumber joined to make beams because large trees don’t exist - Sheathing - plywood (replaced by OSB), particle board (weak used for ash over), decorative - Engineered wood Products (EWP) - made from new/rapid growth forests shredded into pulp or vegetable bers - replaced cut lumber - greater strength sti ness than steel - OSB - used for roof, oors - degrades with sun, moisture and heat - Laminated Veneer Lumber LVL - loaded axial perpendicular to grain - beams, joists - Laminated Strained Lumber LSL or PSL - aked wood strands - glues derived from crude oil - Cross Laminated Timber CLT - 3-7 layers - columns, long spans - similar to glulam - 1 ton of wood = 5X concrete, 24x Steel, 126x aluminum of energy to create 1 ton - char at slow predictable rate - Glue laminated timber GTL - multiple layers of dimensional lumber - can be curved ff fl fl ff fl fi fl - Finger Jointed lumber - create long lengths - join wood at 90* - Steel - staple for 2 centuries - true bones of a structure - excellent resistance compression, shear and tension forces - excellent surface-to-mass - collects heat - casting - hot (50% strength loss @1,100*F AKA extruded) or - cold rolling (stronger steel, c-channel, nuts and bolts, losses 55% strength @ 800*F AKA cut or rolled) - Note: structural steel elongates or expands @1,000*F 10”/100’ - Cast Iron/ pig metal - brittle - heat resistant but crumbles from hose streams and loading changes = eccentric loading - cooling may cause implosion - Aluminum - most abundant metal - soft with high strength to weight ratio - Titanium - abundant and light weight/high strength - too expensive for construction - Concrete - Portland cement+sand+aggregate (gravel)+ water - solid mass - low slump stronger then high slump (wetter) - great compression - poor tensile and shear strength and brittle - slowly absorbs and retains heat causing moisture to spall - overhaul stress to re ghters - Reinforced Concrete - rebar added - Pre Post (factory)/ tensioned concrete (job site) - steel cables tensioned to strengthen concrete - Precast concrete - factory reinforced - walls (tilt up slabs) - oor/roofs (t-slabs) fl fi fi - Monolithic Buildings (single stone-latin) - poured on site with rebar skeleton in forms - 1 oor at at time - Masonry - brittle material - brick, tile, concrete block (cinder block most common wall) or stone - Mortar holds together (may spall or wash out) - compressive force strengthens (strength from axial loads) - Note: roof lost the masonry walls are susceptible to eccentric loads (wind/ hose streams) additional loss of mortar creates instability fl CH 3 Structural Elements Foundations - buildings anchor to earth - Foundations - weight distribution pads - Slabs - horizontal elements that rest on ground - Pilings - driven down in the earth Columns - compressive loads carried axially (squares, rectangles, cylinders) - Hollow Columns - hot rolled steel H shape (I shape prone to bucking) - Pillar - free standing vertical post - Buttress - exterior wall bracing to support lateral loads from beams and truss appears perpendicular to the wall - may also be called Pilaster but are normally decorative appears as vertical stack - Struts - are horizontal columns - Rakers - diagonal columns in the earth to hold shoring for trenches Beams - perpendicular loads delivered to there posed load creating opposing forces - De ection - caused by load on beam - Neutral Plane - place in beam where a hole can be placed for piping… - 2x width = 2x strength - 2x Depth = 4x strength - Simple Beam - supported on 2 ends - Continuous Beam supported in 3 or more columns - Cantilever Beam - supported only at 1 end - Lintel - spans opening in load bearing wall - Girder - beam that carries other beams - Ledger - shelf for other beams attached to a column - Joist - creates oor or roof assembly - Rafter - joist supporting the roof - Ridge Beam - upper most beam of a pitched roof fl fl - Purlin - support roof sheathing and ceilings - Suspended (hung) Beams - supported by a cable or rod from above - examples of vertical beams are retraining walls, antennas and highway billboards - Parts of I beams - top and bottom cord/ ange - middle web/ stem made from engineered wood or steel - 2 most popular: 1. Truss - uses ridged triangles with open web - strength is provided by depth and triangles (similar solid design signi cantly increase weight size and cost) 2. Planar Truss - 2 top cords, bottom cord and open web - web members are vertical or diagonal added to increase the load - example king post truss - Triangular Truss - most commonly used for roofs - Parallel Cord Truss - top and b bottom cords run same plane (wood, metal or combination) - Arched Truss (common tin 1950’s) - top cord arched and bottom straight - 2 types: 1. Ridged (Rib) arch truss made with heavy timber not attached to bottom cord 2. Bowstring - horizontal tension bottom cord with buttresses/ pilasters to help accept lateral live loads - Whipple - father of modern bridge used arched truss designs based o Pratt Truss to design Iron bridges Connection - small low mass points that must transfers a great deal of force with low resistance to re and are considered the weak links of construction - types of connections: - Pinned - (restrained) screw, nailed, nut and bolt - spot welds or rivet to pass through force to a single point - Ridged - (restrained) welded, glued, poured concrete with steel, spread the transfer of loads - Gravity - (unrestrained) pockets in masonry for beams/rafters/joists that’s are loaded with gravitational weight from above ff fi fi fl - Fire cuts - diagonal cuts on top of beams/rafters/joist to allow oor to fail without damaging walls - gravity connections used in the late 1800-early 1900’s any evidence of oor sag exterior ops - Gusset plates/ Joist hangers are technically pinned connections they should be considered unrestrained connection Structural Assembly - engineered collection of interconnecting building components - Assembly built/ Performance designed construction - individual pieces of construction are codependent on others to from a sound unit - Sheathing - all material used to cover (encase) walls/roofs/ceilings of framed structures (platform or sub oor) - Walls - load bearing and non-load bearing - Wall types - Panel - single story exterior - Curtain - exterior enclose multiple stories - Partition - separate rooms - Party - shared by 2 buildings maybe structural - shear - adds sti ness help resist impact load of wind Structural Hierarchy - progressive order in which building loads are delivered to the earth - Structural types: - Framed/ stick built - Monolithic - concrete and steel form single story - Post and Beams/ Skeletal - no load bearing walls - Tilt up - prefab reinforce concrete pinned together - Wall Bearing - roofs and oors rest on load bearing walls ff fl fl fl fl Ch 4 Classifying Buildings (NFPA 220) - re ghters must consider the construction type so they can make judgments regarding strengths and weaknesses of the building that can help or hinder suppression e orts - 5 building classes is a trap that can lead to error - 3 step process for familiarization/ rapid size up: 1. Pre-incident study 2. Pre- re familiarization of the actual structure 3. On-scene pre-and post incident experience - Classify buildings by size/type/era/use - NFPA 220 5 types of Building Construction - The combustibility and the re resistance rating of buildings structural elements - Limited combustible - Materials have half the potential of wood 3500 BTUs or less - Noncombustible - material will not ignite, burn, support, combustion, or release, ammable vapors when heated - Fire resistance rating (FFR) - length of time required to burn through a material (lab controlled test, re is going to have greater or less heat) - Flame spread rating (FSR) - length of time it takes to burn across the surface of a given material - Protected - res resistance rating of at least one hour - Unprotected - heat and Fire will cause degradation of structural integrity - Numerical designations: - 1st # - Roman Numeral - type of construction - 3 #’s in ( ) 1. Fire resistance in hrs - exterior bearing walls 2. Fire resistance in hrs - structural Frame 3. Fire resistance in hrs - oor construction - Type 3 - 5 easily identi ed from street type 1-2 identi ed from interior buildings - Type 1 Fire Resistive - Constructed of approved, non-combustibles or limited combustible materials fi fi fi fl fi fi fl fi ff fi fi - Most resistive to re and collapse, due to their masonry and protected steel structural members - Primary hazard is contents within the building - 4 methods to protect concrete: 1. Encasement with concrete 2. Encasement with gypsum 3. Spray on applied coding - (vermiculite) very common method 4. Special paint cover - expands 15-30x when exposed to heat - Open areas are the enemy of compartmentalization - Concrete - spalls and exposes rebar and retains heat - HVAC - helps with re extension and should be shut down - Interstitial areas - false oors (computer rooms) and suspended ceilings, voids for extension - Curtain wall construction - 3-4” gap between hangers and structural steel allows for extension - 2 goals of curtain wall construction 1. exterior walls nished quickly 2. Protected workers on interior - 3 categories of oor plans 1. Center hallway - stair shift at either end 2. Center core - stairs and elevator in core 3. Combination - larger buildings using both oor plans - Shafts - allow for extension/ smoke travel - Forcible entry - More di cult, metal door jams and frames… unless you have , master key - Ventilation - di cult due to windows, not opening and masonry construction Type II - noncombustible construction - Approved noncombustible or limited combustible materials - Structural steel unprotected, su er signi cant detriment (damage) during a re leads to collapse - Similar features as type 1 but less stringent requirements - 3 characterizations of type II: 1. Concrete tip-up (slabs or block) ffi ffi fi fl fi fi fi fl ff fi fl 2. Unprotected steel frame enclosed by concrete tip up (slabs or block) 3. Unprotected steel frame enclosed by steel walls - Principal hazard is the roo ng material and contents in the building - Steel - twist, sag, or collapse when exposed to heat - 3 types of wall that collapse: 1. Unreinforced masonry (URM) - susceptible to collapse from expanding and spoiling steel structure members I can easily collapse outwards 2x height 2. Reinforced masonry - not as willing of a candidate for collapse concrete ll block or brick with reinforced rebar steel in Portland cement for motor 3. Tilt up or precast - stands up to re well but doesn't allow steel to expand forcing collapse outward from pressure of steel - dangerous due to its reliability on intact building component for stability - Collapse, potential from onset of re - Contents - primary hazard to unprotected steel - Name on exterior of building is a great indicator of contents - Residential or commercial residential activities will have a reduced re load and more compartmentalization compared to commercial businesses with open spaces and higher re load - Extension - primary consideration in multi story buildings, particularly residential and commercial residential - Smoke predominantly responsible for deaths Type III - Ordinary Construction - Load bearing Exterior walls made of approved non-combustible or limited combustible and interior assemblies made of wood - “ Main Street USA” - brick and joist construction (tax payers, hotels, strip malls/ mini mall) - Post 1940’s cinder block walls - Geometry and glue has replaced size and nails/bolts/steel plates, and conventional lumber - Vertical extension is major contributor to loss of life in multistory buildings remote from the point of origin - Shafts/ Open stairways contribute to this factor fi fi fi fi fi fi - Cocklofts/ Attics with dimensional lumber will resist the e ects of re for longer periods of time as compared to lightweight truss - Truss loft - allow Fire to easily extend in numerous directions - Rapid collapse, expected due to gang-nail plates and glue from lightweight construction - Attics - large enough for storage, HVAC… rapid re spread - Alterations and concealed space/ voids - Alterations can signi cantly weaken original design and create new void spaces - Exterior changed assume the Interior has been changed - Remodels done with lightweight construction - Stacked kitchens and baths are examples of pipe chases - Parapet wall - Wall extends 1-8’ above roof line - Parapet walls used with type of construction: - Tilt-up slabs - Modern Masonry - Unreinforced, masonry construction - (greatest collapse hazar) - Capped by coping stones that are subject to falling in older construction due to loss of adhesion and our held by gravity - Cornices - old and new construction considered an unstable component and should not be used do you support weight of re ghter or aerial device - New Cornices made of glue and foam are ammable and do not support weight - Old style cornices used to cover bottom of roof made of stone or wood inserted into “lets” in block wall (age and weather enemy of both) - Previous Fires - Repairs completed with less integrity than original structure - Style roof, not appropriate for age of building - Visible modi cations to roof - Façades - Conceal voids and allow for extension Type IV - heavy timber/ mill construction - Exterior, interior, load bearing walls made of approved non- combustible or limited combustible with interior structural elements made of solid or laminated wood without concealed spaces fi fi fi fi fi fl fi ff - Masonry exterior that encloses is an interior lumberyard - Late 1800’s - 1900’s - Standards for construction: - Columns not less than 8 inches thick - oors loads - Columns 6”w x 8"d - support roof and ceiling loads - oor beams/ girders not less than 6” w x10” d - Roof decks not less than 2 “d - 2 hour re rating for load bearing interior/ exterior walls - Floors and decks will not be concealed only in equipment rooms - Mill building may not be the standard built before standard - Renovations - Maybe vacant due to location (downtown) - Modi cations create void spaces - Converted into multi family housing - May have retro tted re sprinkler systems - Opening, shafts, doors - Minimal compartmentalization, built for manufacturing - Fire doors used to separate building with fusible links no longer work - Size of re and collapse areas - Fire spread, increased by petroleum laden oor planks - Large fuel load/ surface mass for heat ignite, takes a noteworthy amount of time - Large bore streams, defensive for well advanced res destroying buildings, position well away from collapse zone - Potential for large con agration buildings can be a whole city blocks and connected with walkways - These buildings are not impervious, and should not be ignored Type V - wood frame construction - Structural elements entirely or partially wood and other approved material - Responsible for the majority of deaths to re ghters and civilians - More single-family dwellings, and any other type - Longer they burn the weaker they become because all structural components will burn - Types of type 5 construction: - Stack log fl fi fi fi fi fi fl fl fi fl fi fi - Interlock logs, ll space with chinking that create a drafty and sti building - Strongest form of wood construction - Roof decking, weak link - Roof timber, SAG before collapse giving small warning - Rafters tails only expanding past exterior walls and corners and gable ends suggest lightweight construction roof. (should I have multiple rafter tails) - Fire spread - dictated by interior, geometry, and contents - Collapse - localized collapse and burn through of roof decking - Interior your threat of collapse from lofts - Post and beam (braced frame) - 2 primary structural components 1. Columns 2. Girts/ ribbon boards - horizontal beams used to support oors - Unobstructed oor space (pole barn) - Mortise Tenon joints (date back to 2,600 BC) - Eventually replaced by bolts and plates - Rafters with ridge beams for roof - Fire spread - rapid due to open construction and re loading - Collapse - Heavy timber/ bolts collapse di erently due to loss of exterior walls and roof sheathing, causing loss in rigidity - Mortise/ tenon joints multiple oors collapse due to loss of joints - Balloon frame (Chicago construction) - Popular when long length of lumber were available - Replaced by platform framing 2 x 4 x 16” - Joist attached by ribbon board (larger) - Long open void spaces between stud and oor joists - uninterrupted, vertical and horizontal pathways for a re - Roof rafter spaced on 3’ - Veneer exterior walls - Visual cues from the street: - Up to 3 stories - Shiplap or asbestos shingles - Visible 2 x 4 rough cut rafters on 2’ spacing - Windows are narrow and line up of vertical fl ff fl fi fl ff fl fi fi - Fire spread - rapid travel up continuous voids into attic - Remember interconnected void spaces - Collapse concerns - aging alterations, un nished, basement leads to oor collapse, sagging oor and roof given notice before collapse - Burn for sometime before integrity is lost - Lightweight construction is a concern - Western platform (conventional, legacy and engineered (lightweight)) - Most common type of wood construction - Multi story buildings use double plates and re-blocking in the exterior walls to act as re stops - 2 types of Fire stop 1. Fire blocking - Wood blocks between studs 2. Double plates - WWII - de ning of construction industry - Building block approach each oor separate from each other - Basic cap and stack method with 8’ studs - 3 subdivisions of western platform - Conventional, Legacy and Engineered (light weight) 1. Conventional (classic wood frame) - use true rough cut dimensional lumber 1800 -1940 - Rough cut - quickly chars and slows burn rate of wood - Used - Lath and plaster, tongue in groove wood oors, nails and screws - Compartmentalization and re stopping, make conventional platform resistive to collapse - Signs of sagging, or bowing before collapse 2. Legacy - uses milled lumber, solid wood frame building and nails used for connection points that hit center of wood - Can have trussed roof using solid wood and nails or Staples to secure wood - Craftsman built - only solid wood is used - Rapid collapse, potential of trusses - New techniques and pro t enhancing our concerns for re ghters (1.5" x 3.5" studs, smooth plane nished lumber, steel hangers, plywood sheathing) - Larger rooms and geometry, also have a roll. fi fi fl fi fi fi fi fl fl fi fi fi fl - Primary hazard - Use of so ts, larger spaces, split foyer allow for re spread - Increased use of smaller dimensional lumber, metal hangers, and plywood/OSB sheeting, increasing re spread and reduce collapse time from conventional platform - Poke through’s/ penetrations - utility chases add to re spread - Fire ghters should be concerned of rapid collapse, potential of trusses 3. Engineered wood platform (lightweight construction) - uses engineered wood products in combination with adhesive to bond structural connections together. - Radically di erent from dimensional lumber - Uses geometry in place of mass for structural members and assembly building techniques to achieve strength - Primary hazard - Momentous negative impact on re ground operations from the perspective of fast failure rates, and re ghter injury, and death - Conventional/legacy - 15 - 20 min. failure rate - Engineer (lightweight) - 5 to 7 min. failure rate - Aggravating the problem is gusset plates that are surface attached or glue that lique es at low heat - Lightweight wood buildings Exacerbate re spread concerns - Truss spaces are like balloon frame, only worse - Truss spaces are like a wood crib lots of exposed spaces and air space that can spread re - Truss space is wide open causes three-dimensional re spread instead of separate stud and joist channels - Poke through construction also applies to the webbing of trusses - Synthetic materials, burn hotter at an extraordinary heat release rate - Heat release rate of plastics accelerates the calcination of Drywall, allowing faster, access to combustibles fi ffi ff fi fi fi fi fi fi fi fi fi fi - Lightweight trusses have the greatest negative impact on structural integrity - Lost Interior re ghting time, buildings collapse quickly - Green technology is additional reason for concern, buildings built with less number - Tan or brown smoke is a sign of degradation of mass in lightweight wood buildings fi fi Classifying buildings – hybrid, era, use, type and size considerations - CH 5 - Hybrid building - Building that combines various NFPA 220 types into a structure or built in a way that re ghters cannot t the building into NFPA 220 types - Anything of mixed origins - Combined NFPA 220 building types - NFPA 5000 and IBC address how buildings can be combined - Occupancy separation - build single structure for multiple uses by using an approved re barrier to meet time requirements to mix various construction types or use of re sprinklers, without re barriers - Alternative construction methods (non-NFPA 220 types) - Example: Straw house with wood truss roof is label type 5 - Little information on re spread/collapse - 4 factors of risk and tactical decisions during suppression operations (era, use, type, size): 1. Era - time period structure was built - Age can be used here, but this text equate age to deterioration - Era directly impacts operations - Pre-WWI - (historical) - 1700s – up to WWI - High mass materials for walls and solid mass beams to support roofs and oors (cut stones, bricks, steel) - High mass nature, absorbed heat an allowed for re ghting time - Aggressive Interior, re ghting evolved from these buildings - Smoke with a non-issue - Con agration res of wood structures of this era are tied to code development - Fire spread through open doorways, hallways, combustible voids, poke through’s, balloon frame due to the lack of re fi fl fl fi fi fi fi fi fi fi fi fi fi fi fi stops and easily spread to other closely spaced wood buildings - con agration - Brick and stone help minimize building to building spread - Tactically - prevent re spread - Aggressively search void spaces for re - Transoms above doors fail 1st and allow re spread - Address exposure issues to prevent con agration - Collapse warning, signs of sagging roofs and oors or cracks in mortar, noises typically self announcing - Common construction features leading to collapse: - Gravity connections -Wood beam in masonry wall pockets - Without re cuts in beam, bricks will push out of load bearing walls - Cast iron columns - become brittle when heated - Mortar - water soluble and can wash out between bricks - Portland cement - more water resistive - Added exterior elements, alterations and aging - Use of spreaders to disperse loan, metal rods attached to spreaders, fail under heat conditions - Anchors hold wood rafters in place on the exterior - Pre-WWII - (industrial) - 1918 - 1939 - Sears o ered mail homes (1.5 story bungalows) - Wood is the material of choice for homebuilding - High-rises built in greater numbers at higher heights - 2 factors of industrial development era: 1. Engineering - designed buildings larger with attention to strength and durability - High-mass material is still the standard 2. Standardized building code - Make building systems more reliable - Fire safety was considered by both engineering and code - Fire spread - Industrial area buildings, sheer size “ re grew with building size” ff fi fi fl fi fi fl fi fl - Open stairways/central hallways ( re and smoke and unchecked) - Utility chases - Engineering right into the original construction - Flammable insulating materials - Void spaces - increased incidences of backdrafts and cold smoke explosions - Collapse - Longer span steel trusses - Converted open truss space to storage areas which adds dead and live loads, roof system is not designed for this - Post WWII - (Legacy) “greatest generation” - Minimum materials, quicker/easier construction methods - Stronger “can-do” attitude and lust for freedom, postwar - Baby boomers/ suburban America was born - Type 1 legacy - Stadiums, Arenas, public assembly, most restrictive codes with steel reinforced concrete - High-rises concrete core with steel web and glass curtain - Type 2 legacy - Manufacturing, warehousing and institutions (Schools and hospitals) - Brick, block and concrete for a load bearing walls/ columns - Heavy timber or steel beams - Entirely steel buildings built in post and beam fashion - Type 3 legacy - Suburban strip mall - CMU’s for load bearing walls - Floors and roofs solid wood joist - Type 4 legacy - Churches and resorts “those that could a ord it” - Heavy timber roof and oors diminished - Fire spread - Code helps re ghters in Legacy era - Aggressive interior re attack - Fire protection systems fi fi fi fl fi ff - Legacy era, re protection systems can be overwhelmed by today's Fire loads (synthetics vs conventional materials) - Use of glass creates faster oor- oor re spread (auto exposure) - Windows, harder to break, increases potential for ashover - Updates to legacy buildings may attach cable trays to nish ceilings and walls - Collapse - Most re ghter friendly buildings, durability demands came together - Gravity - buildings will fall/ fail when exposed to uncontrolled re - Open spans - Open wide beam spans - Occupancy shift - used in a manner never intended - Overloading - hoarding, collecting, overstocking -Post great depression - Cumulative dead load is suddenly stressed - Aging of building materials - Engineered (light weight) - 1960-70’s slowly added to Legacy construction - Engineered lightweight buildings (ELB) - language in codes slowed the evolution of this type of construction. 1980’s building Industry made the case to allow more innovation - Most anything built after 1990 is ELB - Lightweight - low mass or high surface-to- mass materials, glue, staples, assembly built systems - Assembly built systems - each and every component interacts with each other to make structurally sound - Stronger buildings using less material - Fire spread - Assembly built ELB comes up short on duration and structural integrity when attacked by re - Hotter res in lower mass buildings - Interior re ghting time lost in ELB fl fi fi fi fi fi fi fi fl fl fi fi fi 2. Use - what building is being used for - Occupancy - what someone wants to use the building for - Code in uence by the killing power of re - Occupancy requirements - designed to give occupants a reasonable chance to escape building on re - Occupancy changes require permitting by jurisdictions - Codes di erentiate occupancies established by NFPA 5000 and IBC - Types of occupancy - Assembly, business, daycare, educational, factory, hazardous, institutional, Mercantile, residential, storage, utility and miscellaneous - Use these terms with on scene report to help describe occupancy/use and queue other units into potential Fire loads - Fire spread - Closely related to the contents of a given building 3. Type - NFPA or hybrid - Past an present contraction has been a detriment to re service - Primary element of size up is building construction type - Type of construction helps identify strengths/ weakness and how building will resist heat and re - 3 primary building attributes 1. Relevant Strength of Building 2. Amount if available time for interior operations 3. Length of Time building will resist e ects of heat prior to collapse - 5 construction classi cation does not address some aspects of a building under demolition by heat, re and gravity - NFPA 220 - provides basic underpinnings of a building 4. Size - relative footprint and height of building - Simplicity - common re service (small, medium, large big-box, high-rise - Frustration - understanding, interpretation of terms - Use these 4 factors to classify a building - Classifying a building is a key step in initial and on-going to size up - Classifying “like using radar to see the looming threats” fl ff fi fi fi ff fi fi fi fi - 6 Considerations of communication 1. Perception 2. Foot Print of a Building (L x W) 3. Interior arrangement (walls/ contents) 4. # of oors above/ below grade 5. Amount of Available Resources (apparatus/ sta ng) 6. Size of Fire - 2, 4, 6 method (rapid size up for initial building size) - 2 = small - 2 stories or less (single with basement) - 2,000 sq ‘ or less - 200’ or less hand line - 2 hand lines or less for o ensive attack - 4 = medium - 4 stories or less (single with basement) - 4,000 sq ‘ or less - 400’ or less hand line - 4 hand lines or less for o ensive attack - 6 = large - 6 stories or less (taller is high-rise) - 6,000 sq ‘ or less - 600’ or greater hand line - 6 hand lines or less for o ensive attack - Conservative o cer will plan for the worst case - Better to judge bigger than be wrong, bump up to greater size if close to max - Big Box - Home Depot, Walmart, aircraft, hangers, theaters, assembly line manufacturing, standalone anchor stores - Fire load has the ability to overrun sprinkler system - Mega-Box - MGM Grand, Caesars palace, Boeing assembly plant, airport terminals, mega-malls with multiple anchor stores - Most departments require signi cant amounts of mutual aid - High-rise - building exceeds 75’ and/or 7-8 stories - Big box and MegaBox can be considered horizontal high-rises - Residential - most common building type - Responsible for the most civilian and re ghter deaths - External size (1st view) L x W x H + above and below grade - 360° size up fl ffi ff ff ff fi fi fi ffi - Commercial - - 3 Factors 1. Exterior/interior - size can be quickly veri ed 2. Fire load - continents 3. Search considerations - Business hours/non-business hours - Factors of a major impact on time and resource commitment - Physical size included initial size up - Basements/below grade can be multiple levels, parking garage and interconnect structures (FDA) fi Foundations, oors, ceilings, and walls – CH 7 - Contribute to either a partial or total collapse of the structure or not providing signi cant time and structural integrity to allow extinguishment in a timely manner - Base of operations - platform will safely support you for the duration of operations - Foundation - anchor to earth, base for all elements above - Most obscure portion of structural size up - Provide clues to the era of construction - Industrial era utilize steel reinforced concrete - Low slump, high aggregate (Portland cement) - Rough cut block - residential post and beam - Fieldstones, granite, limestone, and brick - old buildings 1800 -1930 - Three types of foundations: 1. Slab on grade 2. Perimeter - 2 con gurations - Crawl space - Will have vents - Slab on grade 3. Basement/cellar - most dangerous - Frost lines mandate, deep footings due to freeze and thaw cycles - Look out basement - above grade windows - Sub levels - multiple levels below grade - Floors over basements maybe unprotected, exposed truss system - Floor - - Support interior live and dead loads acting as a diaphragm to transfer lateral loads to the walls of the structure - Lightweight construction found anywhere in structure, assume everything is lightweight - Dissimilar oor level designations with sloped ground around building fi fl fl fi - 4 parts of a oor: 1. Support 2. Joists - Dimensional lumber o ers resistance to Fire, unlike lightweight I- beams - 4 ways to support for Joist - Joist pockets, ledger/ribbon, top plate, metal hangers 3. Sub- ooring 4. Floor covering - Joist hangers are the most inferior way to connect oors the walls - Light weight concrete used with metal pan sub oors is considered structural - Tiles, Terrazo, and hardwood oors increase the dead load and accelerate collapse, especially in lightweight construction - Carpet/ laminate, create toxic smoke - Ceiling - - Ceilings are directly connected to overhead oors - Directly fastened to ceilings - lath and plaster, metal wire mesh, decorative tin/ wood, Drywall, concrete, suspended - Lath and plaster, more re resistive than Drywall - Lath and plaster absorb more heat than drywall and collapse in smaller sections - Tin conducts heat, not prone to rapid collapse - Decorative wood can suddenly collapse due to signi cant weight - Drywall least re resistance, but does not retain or radiate heat - Drywall collapses in large sections wet or pulled - Concrete ceiling oors absorb and radiate heat, severe limiting factor in suppression and overall - Interstitial space - Space above suspended ceiling - Plenum space - interstitial space used for HVAC air return - Entanglement hazard, when suspended ceilings fall - Spaces above ceilings (suspended) can accumulate smoke and/ or spread re - Turn o the HVAC systems if possible fl ff fi fl fi fl ff fi fl fl fl fl fi - Wall - - 2 types of division walls 1. Occupancy - 2. Fire wall - grade to at least 18” above roof - Cut holes in roof on uninvolved side, inspect attic for holes in re wall/ horizontal extension - 2 type of re wall construction 1. Brick Noggin - Brick used to ll space between woods, dead load concerns -old style 2. Drywall - Partition wall - Floor to ceiling - Party wall - sure by two buildings or occupancies - Adjoining walls - minimize extension unless balloon frame - O set walls - 7” gap between walls used for sound, deadening or insulation - allow for horizontal and vertical re spread, check for extension - Exterior Walls - principal Support for roof and oors “wall column” - Exception - Post and beam - Balloon frame - Full length studs, 3 stories - horizontal and vertical le extension, and void spaces - Windows, lineup vertically - Rafter tails, 2’ or greater seen at roo ine - Platform framing - 2” x 6” - Fire blocking/ Double plate - All oors match each other - Advanced Framing (in line or stack framing) - 24” on center - 2 stud corners (3-4 normal) - Roof trusses/ I joist oors - Single plateVinyl siding = PVC - 10-30% less lumber - Exterior siding - 2 purposes: 1. Lateral bracing and strength 2. Backing for exterior material - Old - 1”x 6” replaced by plywood and now OSB 0.5” ff fl fi fl fi fi fl fi fl fi - Use SCBA when asbestos shingles are found - Wood singles contribute to combustible load - Fiber cement siding - re resistive/ noncombustible, Long life, low maintenance - Plywood T-11 - easily burn/ rapidly disintegrate - Vinyl Siding - melts, gives o noxious fumes - asphalt felt siding - Post WWII, petroleum based, looks like felt or bricks, absolutely no re retardant properties, highly ammable, major autoexposure concerns - Masonry veneer - collapse with exterior walls weakening - Connected with metal tabs - Inset windows - Plaster/stucco - non- ammable no hazard on structure re - Corrugated - metal/aluminum or berglass ( berglass quickly fails under re conditions) - Masonry walls - Used for reduce maintenance, heat resistance, look good and tensile strength - Unreinforced masonry - without Portland cement, steel rebar, or strapping - Concrete in ll - gaps between parallel course is lled with concrete and brick and vertical or horizontal runs - Reinforced masonry - Open cells lled with concrete and steel rebar, steel rebar mortar joints - Rebar - increased stability/strength of concrete, rough surface helps bond to concrete - Wythe - one unit thickness, continuous vertical section - Interconnected for strength with multiple Wythe’s exterior walls (exterior nice brick/ interior Eco Brick) - Common in older brick masonry - 4 categories of masonry wall: - (Unreinforced Brick, Reinforced Brick, Weight-Bearing, Veneer) 1. Unreinforced Brick - Prior to 1930, water soluble mortar - Earthquake/ re hazard to re ghters - King row - Block laid on end add strength, visual cue for multiple Wythe - Deeply recessed windows fl fi fi fi fl fi fi fi f fi fi fi fi fi fi - Collapse hazard with types of roofs - bowstring, tied truss, Lamela - Earthquakes modi cations of unreinforced Brick - Pre 1933 - No Portland cement or rebar, 13” thick exterior walls, Let roof joists re cut to cause interior collapse of oor, 3 - 5’ parapet - Post 1933 - Portland cement with rebar, 9” thick walls, anchored joist and rafters to exterior wall - Post 1959 - 4-6” bond beam for parapet walls along public walkways or exits, 16” or lower parapet, rafter tie plates every 4’ - Post 1971 - walls anchored to oor and roof system, strengthen roof construction - Safe areas - Corners during collapse - 2x times building height 2. Reinforced brick - Post 1933 not willing candidates for collapse - Simulator appearance of king row - Portland concrete and rebar 3. Weight-bearing - Multiple Wythe wall (prone to collapse when roof collapse) - replaced by concrete lled with rebar cinderblocks (CMU) - Big-box construction - Veneer walls cover CMU weight-bearing walls (good bond not prone to collapse) - Venere can conduct heat to backing (concern for wood frame, veneer collapse) - Concrete walls - 2 categories 1. Formed walls fi fl fi fi fl - 6 - 8” inch thick walls, 1- 6+ stories, dimensional lumber/heavy timber interiors, construction style, not used anymore - Buttresses - Used to resist lateral force, must oppose each other, sign of arched roof - Pilasters - architectural members, structural piers, 2. Tilt-up panels - Cost-e ective - Wall to wall/roof to wall - steel plates welded to tilt-up panels 4. Veneer ff Reading Roof - Ch 8 - Strength and weaknesses of a building is enhanced by reading one of the most important/ visible aspects, the roof - 1/5th of primary components of a building - Identify era of the building - East Coast roofs have more layers of material - Diagonal sheathing - 1 x 6” on 45° angle - Jack rafter - span between ridge boards and wall plates - Live load - people, snow, wind, furniture - Dead load - permanently attached to the structure - Roof slope/pitch - (4:12) 4” rise/ 1’ - Sheathing - encase walls, ceilings and roofs (plywood, OSB, dimensional lumber) - Skip sheathing - 4 - 6” gap between 1 x 4” or 1 x 6” - Straight sheathing - 1 x 6 @ 90° angle to roof rafters - Sheathing increases roof stability - Timber truss - older roofs, dimensional lumber - Truss loft - Open Web nature of trusses - 8 Most common roof styles: 1. Gable - Most popular in United States, Single family - Stick frame/A-frame construction - dimensional lumber - Ridge board and rafters (2 x 6) 16 - 24” on center - bungalow is a variation - 2 x 4 or 2 x 36” on center rafters no ridge - Light weight - 2 x 4, 2 x 3, 2 x 6 rafter truss, nger jointed with glue, gusset plates, 2 x 6 or 2 x 4 2’ on center - Glue softens out 350 - 400° (independent re department studies) fi fi - Metal trusses is variant due to cost of wood - Strength - Conventional construction last 4 hrs longer than light weight/ engineered - Ridge and valleys, strongest area of roof - Hazard - Light weight/ engineered construction - 1/4 time of conventional construction (glue, connector plates fail) - OSB/plywood fail faster than space sheathing - Rafter tails may help you identify dimensional vs lightweight construction (if not covered by so t) 2. Hip - Irregular pyramid, replaced at sides of a gable roof with slopes, similar to gable roof - Ridgepole with hip/ Valley rafters , 2 x 6 on 16 - 24” centers (rough sawn 36” on center) - Strengths - Conventional construction - Hazard - Trusses for rafters, mimic lightweight construction 3. Gambrel - Gamba - latin means horses hock/ leg - Two sided, broken obtuse triangle, so lower slope is steeper than upper slope - Advantageous, snow/ water runo and maximum headroom/ space below roof - Most popular use - Barns - conventional lumber, mostly - Hazard - re load - Roof ventilation di cult without aerial 4. Monitor (Lantern Roof) - 2 shed roofs support a gable roof (Barns, storage) - Unusual to nd to nd lower portion/ oor underneath shed roof - Conventional or lightweight construction fi fi ffi fi fl ffi ff fl - Vertical Ventilate shed roof easier than Gable use aerial - Strength - Vertical ventilation to upper window - Hazard - Large open space vertical/horizontal extension - Dead load on lower section from upper section - Sidings fail quickly 5. Sawtooth - 19th century, manufacturing/industrial - Design primary light source before electricity - Glass faces away from equator - Constructed with triangles and parallel roof surfaces - 2 x 6 rafters with 1 x 6 sheathing - Windows can be used as ventilation - Not a common form of construction today - Strength - Perimeters/Windows strongest areas - Dimensional lumber - old construction - Support post increase strength of roof (very stout roof supports work) - Hazard - Underside of roof exposed - Lightweight construction 6. Flat - Cost e ective design, more than lightweight construction - May have shed roof/ half gable 10° or 10 - 20° low pitch - Shed roofs normally 20° or greater - Conventional at roof - 0 to 10°, minimum 6° for drainage - Rafters or Joists, wood or metal with bridging/ scissor bracing to increase stability (2 x 6 with 1 x 6 construction) - Focus on re ground - Identify the type of at roof - Old style you let pockets - Strengths - perimeter of roof strongest - dimensional lumber - Hazard ff fi fl fl - Degree of hazard dependent on rafters, dimension, spacing and size - Plywood/OSB o er minimal integrity under re conditions - Multiple layers of roo ng contribute to dead load Flat Roof with wooden I Joist ( lightweight construction) - Diaphragm nailing - staggered 4 x 8 sheets of plywood or OSB - Strength - Perimeter - Hazard - Micro lam/ LVL - cheap grade lumber laminated used for structural members - Threefold : 1. I Joists (closed web) 3/8” stem and 2 x 3 or 2 x 4 chords take a little time to burn causing rapid collapse 1. Painted dark to minimize presence 2. Convection degrades glue 1. Moisture steamed out of glue turns to dust 3. HVAC ducts remove web and allow for horizontal extension Flat Roof with Open Web (OWC) - Open Web steel (OWS) - 2” cold rolled steel - Parallel wood chords, cross, connected by steel tube web members - Top chord supported (bridge e ect) bottom chord not supported in tension - Hazard - Rapid collapse - Extinguish from safe areas not directly involved in re - Extension - Strength - Perimeter is it strength Flat roof with metal gusset plates or glue - Most common lightweight truss, favorite method of roof construction for residential and commercial - Spans up to 80’ ff fi ff fi fi - Metal gusset plate (MPG) - 3/8” nails - Strength - Perimeter - Hazard - Early roof failure - rapid collapse, due to bottom chord or webbing failure Flat roof penalized - Only found west of the Mississippi, rarely east of Mississippi - 2 types - all wood or hybrid - wood and steel - MGP trusses can be substituted for purlins - MGPs are not gang nails - Identi ed simply by pulling ceiling or Rafter tails - Glue trusses fail faster - Safe areas - Are the areas not involved in re - Laminated wood beams last longer than steel - Strength - Perimeter/ steel - Hazard - Hollow 4” steel - expect collapse - Joists burn through quickly - Kraft paper, delaminates, and tar gives o toxic gases causing possible ashover/ horizontal extension Flat roof open webbed bar joist - Central and eastern states - Bar Joist, corrugated steel, insulation board and asphalt roof - Strength - Perimeter - Hazard - 800 - 1000° steel expands, twists, and fails - Roo ng material causes re travel (metal Deck re) - Presence of noncombustible roof material, unknown to IC Flat roof nonstructural, lightweight concrete - Wood or steel sub structure covered by corrugated metal - (Q or Robertson decking) and lightweight concrete - Identi ed after Fire or during ventilation attempt fi fi fi fl fi f fi fi - add additional insulation properties for buildings, near airports, freeways, expressways, turnpikes, and other high noise areas - Used for oors in multi story construction - Strengths - Perimeter - Strength Dependent on span - Hazard - Masonry blades, ine ective, rotary saw with carbide tip (wood or multi purpose) required for ventilation - Carbide tip chainsaw will work, but detrimental to saw 7. Bridge truss (Pratt/ Howe Truss) - Direct descendent of Bridges - Side sloped from exterior wall, to at roof - Trapezoid shaped truss - Bottom chord longer than top chord - Commercial building construction - Diagonal sheathing post mid 1930s added stability - Earthquake prone areas have OSB or plywood on top of sheathing - Appears Mansard, at roof no center peak - Strength - Identi ed by sloping sides and ends and at top - Collapse not an initial concern, indicated by sagging, predictably fail - Hazard - Strength dependent on span and dimension of lumber - Multiple layers of roof 8. Arched - All arched roofs, categorized, bowstring truss, do too well documented catastrophic collapse - Rigid arch/ bowstring are true truss, Lamella/ tired arch are not - 4 arched roof types (Lamella, Tied Arch, Arched Truss, Bowstring ) 1. Lamella (Summerbell roof) - German, brown derby restaurant, Diamond/ honeycomb pattern structural members fi fl fl ff fl fl - Largest hump shape - Vertical ventilation from aerial device - 3 methods Support - Arches terminate on ground foundation - Exterior walls supported by buttresses - Internal tie rods with turnbuckles - Strength - Solid built - Hazard - 20% or greater roof involvement leads to collapse - Multiple roo ng layers di cult to ventilate 2. Tide arched roof - Lacks diagonal webbing, to be bow string - Metal tie rods (5/8”) to counter lateral forces, Wall plates tied to exterior walls - Primarily steel - Pilasters or buttress reinforcement - Strength - Dimensional lumber/ sheathing - Hazard - Early failure of Tie rods and turnbuckles - Exterior walls are pushed out - Failure of any part of the roof equals total collapse - 3. Arched truss (ribbed/ ridged arched truss) - Direct descendent of bridge truss - Arched rather than trapezoid - 2 clues not bow string 1. Substantial bottom cord 2. bottom cord sits on the wall top cord does not touch - Strength - Dimensional lumber early structural collapse not a concern - Fails in sections - Parameter - Hazard - More integrity and stability than other arched roofs, still susceptible to collapse - Push exterior walls out fi ffi - Splits and cracks in bottom cord collapse, warning sign - Tension rods Added to correct issue make it become bowstring truss 4. Bowstring roof - Tied arch with diagonal tension rods to form a web - Design for arch bridges made its way to construction - Wood, iron (hammond, all iron, strongest), or a combination - Commercial buildings/ warehouses - Strength - Dimensional lumber early structural collapse not a concern - Fails in sections - Parameter - Hazard - Jack rafters forcibly push end walls outward trust system fails - Unique roof construction considerations - Parallel chord truss ( at roofs)/ gable truss (A-Frame) - Rough cut dimensional lumber - 1800s - 1900s moderate size commercial buildings, lumber was plentiful - Strength - Predictively fail in sections - Perimeter - Hazard - Long burn time, interior personal overcommit - Gable truss exposed ceiling - Parallel chord protected ceiling conceals re - Multiple layers of roo ng - Size of truss directly a ects the amount of time available before collapse - Dimensional lumber with bolts and plates vs lightweight glue, and gusset plates - Timber truss roofs can last 30 minutes in re condition - Visual identi ers - older style easily identi able by there arched shapes - Early failure potential - roof failure cannot be reliably predicted fi fi fl ff fi fi fi - Timber truss roofs can last 30 minutes in re condition - alterations, exceed original capacity of structure add to live in dead load - 3 conditions of ceilings added to bottom cords (mass) 1. Added weight of ceiling 2. Di cult access 3. Additional weight of store materials - Location - East coast buildings are signi cantly older - Size - Length and dimension of lumber - O ensive operations/ aggressive interior attack - Collapse potential of trusses is minimal if Fire is not involving trusses - Short Interior attack duration to bring re under control - Defensive operations - unknown, re extent - Extension found above ceiling after inspection holes - Corrugated roofs - Inexpensive, easy to erect, larger or small - Steel (18-20 ga) aluminum or berglass over wooden or steel substructure - Flat, gable or hip roofs - Fiberglass panels embedded in roof for light - Work o Ariel or roof ladder - Strength - Ridge and perimeter - Hazard - Rapid failure of materials, especially light panels - Extremely hazardous - Rain roof - Added on to change appearance of existing building - Used were 2 arched roofs meet - HVAC and other equipment is now placed on original roof - Popular on mobile home/ like structures - Strength - Depending on original structure - Perimeter ff ffi ff fi fi fi fi fi - Hazard - 3 Basic factors: 1. believe 1 roof instead of 2 2. Dead load increased 3. May not observe, smoke and re while attempting to ventilate, abnormally, large attic - Inverted roof (raised roof) - Bottom structural elements carry load opposite of standard roof construction - Perimeter provide strength - Smaller top members weaken under re conditions, dangerous to roof personnel (smallest dimension lumber against roof sheathing) - Roof coverings - Hot mop (tar and gravel) - Felt paper, melted, asphalt, and stones (prevents damage to asphalt) - Cost-e ective - Extremely ammable, di cult vertical ventilation - Composite shingle - Most popular, commercial and residential pitched roofs - Typically last 15 to 20 years (come in 30 and 50 year) - New shingles without tear o increases dead load - Wood shake shingles - Varying dimensions, last 15 years’ - High ammability not allowed in some areas of the country - Extension caused by ying brands (multiple blocks away) - Clay tile/ Slate/ concrete tile - Spanish style, long lifespan - Reduce interior temperature 5 to 10° - Noncombustible - Signi cant dead load - Fall on re ghters working blow - Concrete tile is the lightest fi fl ff fi fi fl fl ffi ff fi fi - Metal roo ng (standing seam - most popular) - Made to look like other style roofs - Longevity - 20% savings on energy bills - Light weight 22 - 26 ga - Void spaces between roof decking - Remove metal @ ridge ow water - Razor sharp - single ply roofs (membrane roofs) - Insulation covered by waterproof membrane - Covered in rocks - White membrane - adhered system - Flammable/ toxic gases - Roof appendages - Appendage - something connected, or joined to a large or more important thing - “Added to a speci c roof style for an explicit purpose” - Chimney - venting u gas or smoke - Fire Place - designed for heating or cooking - Zero clearance replace - pre-fabricated, installed almost directly against combustibles such as walls and oors, Wood frame exterior and exterior coverings - Lack of re stopping in vertical channel from top to bottom of replace - Vertical channel “ modern version of balloon frame construction” - Check for vertical extension all the way to attic - Masonry Fire Place - Exterior Fire place - no issues unless unsubstantial construction, cracked allowing for extension into structure - Interior replaces - 2 substantial size up considerations 1. Roof ventilation may be challenging 2. Middle of the roof chimney unreinforced denotes, older construction, dimensional lumber (central replace maximum heat transfer to home, no longer needed) fi fi fi fi fi fi fl fl fl fi - Attic Vents - Reasons for attic Vents: - Remove or minimize moisture - Reduce buildup of heat in attic (reduce building temp.) - Increase longevity of exposed material - Attic ventilation - Air in from so ts/ exterior walls creates ow path to vents in the top 1/3 roof - Cricket - excellent Avenue for re extension - Space where horizontal and vertical wall meet on roof creates a pocket - Airshafts/ Light wells - Smoke issuing, indicate location of Fire (adjoining structure) - Extension in shafts - Covered shafts on roof may not support re ghters (rectangle areas do not match other areas) - Sky Lights - See oor below area clear - Good indicator of building oor plans - Boxed in, so ventilation ventilates interior not attic - Penthouse/ Bulkhead - Indicates stairwell condition - Elevator Shaft - Indicates conditions in building - Floor vent does not support re ghter weight - Roof Scuttle - Indicates re activity - If left open may draw re back into building - Vent Pipes - Vertical re/ smoke extension - Plastic melts becomes pathway for extension “Flammable Wick” - Discoloration around pipe indicates extension in chase fl fi fi fi fl fi fi fi ffi fi fi fl - Sagging roof vent pipe is “growing upwards” - Ventilators - louvered or metal caps suspended above pipe - Fan Shafts - Kitchen hood re due to grease build up - Check entire length of shaft - Advertising signs/ Cellular Towers - Building not built for additional dead load causing rapid failure of roof members under re conditions - Division walls - Prevent horizontal extension if kept intact, not breached fi fi Building features and concerns - Ch 9 - Most buildings have windows doors and utility systems 1. Windows - Overlooked during size up due to their commonality - 3 components of a window: frame, glazing sash - 4 Types of Windows: - stationary - sliding (most common vertical or Horizontal sliding) - pivoting - swinging (types of swinging: casement, awning, hopper, projector and jalousie - Glass - brittle material, derived from silica, soda ash, and lime. - Glass Types: - Plate/ Annealed - Most common type, residential window - Easily crack with ame contact smoke/heat 600° - Heat-Strengthened - Heat strengthened 1150°, not as strong as temper glass - Modern residential and commercial - Tempered - 5x stronger than plate/ annealed - High-rise buildings - “Tempered” etched in glass - Hard to brake (use pointed end of pick axe or halogen), crumbles when broken - heat resistant - Laminated/ Safety - Polyester or Polyvinyl layer sandwiched between 2 pieces of tempered glass - adds strength - Keeps broken glass in sash fl - Film torn with tools from sash - Wired - Increases strength (security) and re resistance - Most di cult to break and remove - Thermoplastic - 250x stronger than safety glass - Power tools for removal - Plexglass/ Texan - imitate glass - Air Blast Resistant - Stop glass shards from explosion - Conventional forcible entry tools, remove glass and mesh - Hurricane/ impact Resistant - Impact resistant glass - Very di cult to remove - 1992 became more popular after Hurricane Andrew, existed since 1974 - PVB membrane layer or Polycarbonate ( exible Plastic Lexan like) both are di cult to force entry on - Impact glass makes “thunk” sound when tapped - Impact Resistant Doors - Bank vault locking mechanism - Hinge pins do not pull - Hinge screws 3/4 x 1/4 beefed up door to jamb and jamb to frame 3”x3/8 1000 lb shear strength every 8 - 10 inches - Impact resistant window testing: - Large (6’ Douglas fur)/ small (stones) missile - may shatter but no rips or tears in impact membrane - Rain/ water in ltration - 8”/ hr. Water and 110-120 mph wind - Pressure test - interior/ exterior. Pressures placed on. Window for 5 hrs. - Must pass all 3 test to be sold as Impact resistant - Features of impact resistant construction (strength/ collapse resistance): - non-Uplift roof system - Increase strapping or anchoring for walls and oors - Wall and roof sheathing penetration resistant - Garage door strengthening - Protection for horizontal wind driven rain - Blast resistance (explosive devices) ffi ffi fi ffi fi fl fl - Building is tighter and has greater risk for ashover/ smoke explosion - Public buildings, jails, government buildings, military buildings - Forcible Entry - K-saw (rotary saw) - best choice - Chain saw - shatter glass 1st - Hand tools - technique matters - Make doggy door ( ap), make cuts around edges, shatter 1st - 1 less cut and ow path control - Ballistic Resistant - Mistakenly called bullet proof - Polycarbonate layers clad with glass - Thickness = bullet type resistance - Timely escape not e ective - Long time to open - If windows are high security so are doors - Energy E cient/ E-glass - Re ect UV rays and minimize heat conductivity - Double/ triple pane with inert gas - Commercial metal/ wood frames - Higher temperatures lead to possibility of ashover - 4.0 mm lm added a glass for e ciency (similar to laminated glass) - Security bars - Remove them especially with interior attack - Barricaded windows - Bolt heads indicate interior 2 x 4 framing for strength - Normally plywood or OSB - Additional window considerations - Windows ush with the exterior wall = Frame construction - Windows inset = concrete/ masonry construction - Windows indicate room type: - Small frosted - bathrooms, poor entry point - Kitchen - windows higher on wall than others (counter top) - Picture - family room… large room, entry/egress/ ventilation - Small between oors - stairwell - Rectangular side/ back - bedrooms, entry/egress/ventilation fl fi ffi fl fl fl fl ff ffi fl fl - Near Grade - basement/ cellar - Attic - blinds, shades, AC unit indicate living area - Commercial (large) - plate or tempered glass use care when braking - Older Residential - wooden double hung (sash chords w/ weights), vinyl = replacement - Concrete Tilt-ups - windows noteworthy above grade, light source (not usable for entry/ egress/ ventilation) 2. Doors - Large openings, enhances deploying through them - Enter at oor level below heat/ smoke - Parts: Door, jamb, strike (receives lock, stops door swing), lock - 4 basic door type: 1. Swinging 2. Sliding 3. Overhead 4. Rotating - 3 Basic Construction types 1. Wood - Hollow core -cheap/lightweight - Wood panel - panels are easiest to break out - Solid - strongest 2. Metal - Kalamine - wood covered with metal - Power tools to cut metal doors 3. Glass - 2 types 1. Frameless - Substantial 2. Aluminum fra