Valves-Food PDF July 2021
Document Details
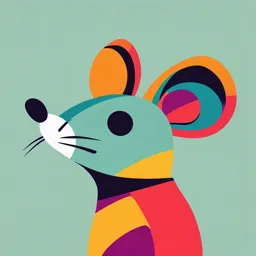
Uploaded by BoomingMotif
TU Dublin
2021
Tags
Summary
This document presented by TU Dublin describes various types of valves used in food processing plants. It examines rotating valves, reciprocating valves, safety valves, including specific types such as ball valves and butterfly valves, outlining advantages and disadvantages as well as safety considerations.
Full Transcript
Valves © TU Dublin Valves – Areas to Consider 1) The different types of valves used in the food and drinks industry 2) The advantages and disadvantages of the various valves 3) The reasons why one valve might be used in preference to another 4) The safety features assoc...
Valves © TU Dublin Valves – Areas to Consider 1) The different types of valves used in the food and drinks industry 2) The advantages and disadvantages of the various valves 3) The reasons why one valve might be used in preference to another 4) The safety features associated with the different valves 5) The common operational problems that might arise with the use of certain valves 6) Types of Valves a) Rotating Stem Valves a) Ball, Butterfly b) Reciprocating Stem Valves a) Diaphragm c) Non-Return Valve d) Pressure Relief Valve © TU Dublin Valves ▪ Two major groups: 1. Those in direct contact with food materials 2. Those handling utility services ▪ Valves play an important role in product transfer. ▪ They are used to control the direction of material along a pipeline. ▪ Valves in the open position allow the materials (solvents, plant utilities, intermediates and the product) to flow forward. ▪ Valves in the closed position will stop the materials from flowing forward. © TU Dublin Valves ▪ The consequences of a valve being left open or closed can be hazardous to the operator and can also cause product contamination. ▪ A closed valve can lead to pressure build-ups in process equipment. ▪ If a valve is left open by mistake it could result in the wrong fluid going into the vessel. ▪ It is important that the operator knows which valves should be opened and which valves should be closed for a particular process © TU Dublin Valves ▪ There are numerous types of valves that are used throughout a food processing plant. ▪ Some valves are manually controlled using wheels or leavers. ▪ Other valves are computer controlled and operate from a central system automatically. ▪ Examples of common valve types are 1. Control valves or shutoff valves These can be reciprocating stem or rotating stem types 2. Non-return valves - check valves © TU Dublin Control Valves ▪ Control valves are widely used in the industry to regulate flow through pipelines. ▪ Two categories of control valves: ▪ Rotating Stem ▪ Reciprocating Stem © TU Dublin Rotating Stem Valves - Ball Valve ▪ A ball valve is a rotating stem control valve and is mainly used for on/off duties. It controls the flow of the fluid through the pipeline. ▪ It is NOT used to accurately control the flow rate of fluids. ▪ The basic construction of a ball valve is a spherical ball in a pipeline with a similar diameter to the pipeline. ▪ There is also a hole through the center of the sphere to allow fluids to flow through the pipeline © TU Dublin Rotating Stem Valves - Ball Valve ▪ When the ball is rotated through 90o it closes the valve by presenting the sides of the sphere to the on coming fluids. ▪ Similarly to open the valve, it is rotated back through 90o presenting the hole in the center of the sphere so the fluids can flow down the pipeline http://www.spiraxsarco.com/images/resources/steam-engineering-tutorials/12/2/fig_12_2_1.gif © TU Dublin Rotating Stem Valves - Ball Valve © TU Dublin Rotating Stem Valves - Ball Valve ▪ This valve is very simple to operate and is suitable for controlling the movement of corrosive materials. ▪ The ball can be constructed from corrosive resistant materials such as PTFE. ▪ The ball valve can also operate at high Example of the temperatures and pressures, for internals of an example 200oC and 300 atmospheres of open manual ball valve. pressure © TU Dublin Rotating Stem Valves - Ball Valve ▪ Advantages ▪ Low pressure loss when opened. ▪ Easy to operate. ▪ No lubrication required therefore minimizing the chances of contamination to the product. ▪ Provides an excellent seal and therefore very little leakage occurs. ▪ Can be used for corrosive materials. ▪ This type of valve can be used with suspensions but frequent cleaning may be required. ▪ Disadvantages ▪ The valve is not suitable for accurate control of flow. ▪ Product can be trapped behind the ball resulting in bacterial growth and contamination © TU Dublin Rotating Stem Valves - Butterfly Valve ▪ Usually found in large diameter pipelines and is often used for controlling gas and steam flow. ▪ A circular disc in a pipeline that can be rotated through 90o. When disc is fully opened the disc is parallel with the flow and allows full flow of material. When disc is closed it is at right angles to the flow and stops the flow of liquid. ▪ Butterfly valves are also fitted with sealing rings to ensure complete shut off. © TU Dublin Rotating Stem Valves - Butterfly Valve Butterfly Valve in Open and Closed Positions © TU Dublin Rotating Stem Valves - Butterfly Valve ▪ Advantages ▪ Cheap and reliable ▪ Fast and easy to operate as valve has only to be rotated through 90o. ▪ The valve takes up very little space. ▪ When the valve is fully open it presents very little resistance to the flow. ▪ Disadvantages ▪ The valve may be prone to leaks if it is not locked into position. Fast flowing or dense liquids can push the valve open. ▪ Product can become trapped behind the disc resulting in bacterial growth. Reciprocating Stem Valves ▪ Reciprocating stem valves use a closing gate that travels perpendicularly to the receiving seat that seals the valve shut. ▪ Common types include; the single and the double seated sliding stem globe valve. ▪ The single and double seated sliding stem globe valves have a similar construction. They consist of two main parts; the actuator and the valve body. ▪ The actuator provides the plug, which sits into the valve body to seal or open the valve. The actuator can be operated manually by turning a wheel or automatically by an automated system. © ITT Dublin Reciprocating Stem Valves Advantages ▪ These valves are effective for flow control. The size of the valve opening can be increased or decreased easily with control over the orifice size. ▪ One seated valves provide a tight seal. Disadvantages ▪ Double seated valves can be prone to leaks and should be used in conjunction with another valve or a one seated valve where a tight seal is required. ▪ The seals may need to be replaced regularly if corrosive liquids or liquids at high pressure are being transferred. ▪ Product can get caught in the seats of these valves. © TU Dublin Reciprocating Stem Valves: Diaphragm ▪ Diaphragm valves are used in applications where cleanliness, bubble-tight shutoff and chemical compatibility are paramount. ▪ Due to the diaphragm valves streamlined flow path, absence of cavities and minimal contact surfaces, it is considered the valve least likely to cause contamination. © ITT Dublin Reciprocating Stem Valves: Diaphragm ▪ They are available in two designs 1. the weir style and 2. straightway diaphragm valve. ▪ The straightway valve having no flow obstruction is suited for high flow, slurry applications © TU Dublin Reciprocating Stem Valves: Diaphragm Typical “Weir Style” diaphragm valves Diaphragm Weir © TU Dublin Reciprocating Stem Valves: Diaphragm © TU Dublin Reciprocating Stem Valves: Diaphragm ▪ Advantages ▪ Stream lined path, absence of cavities, and minimal contact surfaces make it the valve least likely to cause contamination. ▪ Wide range of diaphragm materials available make it useful for many applications and fluid types. ▪ Can be used effectively as control valves, although not as effective as a globe type control valves. ▪ Easy to maintain. ▪ Reliable closure, the resilient diaphragm seats tightly against the weir. ▪ Prevention of leakage, the diaphragm protects components that may be prone to corrosion. ▪ Disadvantages ▪ Diaphragm valves are not suitable for high temperature or pressure applications. © TU Dublin Globe-type Control Valves © TU Dublin Reciprocating Stem Valves: Shuttle Reciprocating valves can come in many configurations often complex, which can be used in specialised piping systems. The valve opposite is Flow after called a shuttle valve. Actuation It is used to alter the Inlet direction of flow to Normal either the top valve Flow port or the bottom. © TU Dublin Shuttle Valve Non-Return Valves – Check Valves Two main types of non-return valves are 1. hinged and 2. a ball non-return valve. Non return valves can also be spring loaded, such that a certain pressure is required to open the valve. Non-return valves only allow flow in one direction. They automatically close if the flow stops or flows in the opposite direction. This prevents the fluids flowing back to the vessel they came from. – Preventing back flow is a very important part of contamination prevention. © TU Dublin Non-Return Valves There are a number of problems with these types of valves, the following are three of the more common problems: 1) There tends to be a lot of wear and tear to these valves due to the moving parts of the valve. 2) The seats are also prone to wear and tear and tend to crack and cause leakage problems. 3) The valves may not shut tightly enough for slurries because the small particles can get between the seat and the flap. The main use for these valves is to ensure that the fluid only flows in one direction and to prevent the fluids flowing back into the vessel they were pumped from © TU Dublin Non-Return Valves (Check Valves) Example of the operation of non-return valves. © TU Dublin Non-Return Valves (Ball Valves) © TU Dublin Pressure Relief Valves - (Safety Valves) ▪ Pressure relief valves are fitted as a safety feature to most reactors. ▪ The valve stays closed as long as the pressure is at normal level. The valve is kept closed by a spring, which is set at a certain tension. ▪ As long as the pressure within the vessel is below this value the system remains closed. ▪ If the pressure exceeds this level the spring will be compressed and open the valve, thus relieving the pressure within the vessel © TU Dublin Pressure Relief Valves - (Safety Valves) These valves are important for vessels that generate gases or steam. – The release of these gases lowers the pressure to a safe level. Pressure relief valves are also used in conjunction with bursting disks. – Bursting disks are an extra safety precaution if the pressure rises too quickly. – Bursting disks are resistant to higher pressures but when they burst they do not reseal automatically and must be replaced © TU Dublin Pressure Relief Valves - (Safety Valves) Safety Valve & combination bursting disc Safety Valve Bursting Disc © TU Dublin Bursting Discs ▪ Example of a bursting disc before and after rupture © TU Dublin Summary ▪ Rotating valves versus reciprocating type valves ▪ Reciprocating valves as control valves ▪ Operation of safety valves, non return valves, and bursting discs © TU Dublin