Vacuum Systems Chem 497 2020 PDF
Document Details
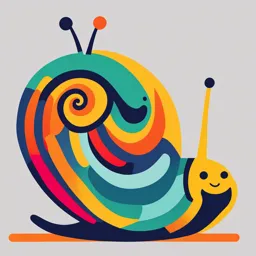
Uploaded by HumourousMetonymy
İzmir Institute of Technology
2020
Tags
Summary
This document discusses various aspects of vacuum systems, particularly those used in GC/MS (Gas Chromatography-Mass Spectrometry) instruments. It covers topics such as vacuum types, components, and related concepts. This document may be part of a larger body of notes or an assignment.
Full Transcript
Vacuum Systems A large amount of the hardware visible on GC/MS instruments concerns the pumping and vacuum systems. A very high vacuum is essential in the mass spectrometer for the following reasons: 1. High voltage breakdown may occur in the multiplier, source, or analyzer if th...
Vacuum Systems A large amount of the hardware visible on GC/MS instruments concerns the pumping and vacuum systems. A very high vacuum is essential in the mass spectrometer for the following reasons: 1. High voltage breakdown may occur in the multiplier, source, or analyzer if the pressure becomes too great. 2. Oxygen from residual air and leaks will cause filament burnout in the ion source and ion gauges. 3. The mean free path of molecules in the system must be long enough , or ion-molecule collisions will occur. 4. As the pressure rises, regulation of the electron current through the ion source becomes more difficult. Vacuum Systems 5. Ion-molecule reactions start to occur as the pressure rises, producing changes in fragmentation patterns. This effect is used to advantage in chemical ionization (CI), but the pumping requirements for the analyzer relative to the ion source are even more difficult in the CI mode. Also, for good chemical ionization, the reagent gas pressure must be stable and controllable. 6. High background pressures may occur due to the presence of compounds in the mass spectrometer. These give interfering mass spectra, making interpretation difficult. 7. Contamination of ion-source components, slits or rods, and multipliers increases with higher pressures. This necessitates downtime for cleaning and affects running costs. Vacuum Systems In addition to the very high vacuum system, some form of medium-to- high auxiliary vacuum arrangement is required for the following tasks: 1. Rough pumping of the mass spectrometer is necessary before the very high vacuum pumping system is applied, whenever the instrument has been vented to the atmosphere (for example, during source cleaning). 2. Rough pumping is needed to clear the reagent and carrier gas lines, to prevent cross contamination when new gases are selected. 3. The GC/MS interface usually contains a sample-enrichment device for electron impact work. This usually requires a pump to remove excess carrier gas. 4. Diverters are frequently used in the GC/MS interfaces to prevent the entry of solvent fronts and unwanted compounds of the GC eluent into the mass spectrometer. The unwanted carrier gas with solvent or sample may be pumped away by a bypass arrangement. 5. Auxiliary inlets, such as the probe and batch inlets, have interlocks that must be rough-pumped before they are connected to the main vacuum system. Vacuum Systems In practice the auxiliary high vacuum system and the very high vacuum system are not entirely separate. Same pumps are used for several tasks, either together or at different times. In addition, there is an increase in the use of pneumatic or differential pressure controls for variable geometry/conductance sources and isolation valves. The pumping requirements for these tasks are modest, and the spare capacity of one of the system pumps is often used for this purpose. Vacuum Terms Atmospheric Pressure. Varies with the weather, but for scientific purposes considered to be constant at 1.013 X 10 5 Pa (760 torr). Conductance. In a pumping system, the inverse of pumping resistance. Conductance figures relate to the ease with which a vacuum system is pumped; the higher the conductance, the faster the pumping. Each element of a vacuum system has a conductance. The conductances add in an analogous way to conductivity (inverse of resistance) in electrical circuits. Generally speaking, the larger the diameter and straighter the path of the pumping system to the pumps, the greater is the system's conductance. Differential Pumping. The independent pumping of two regions of a vacuum system that are separated by a restriction. Vacuum Terms Fore-Vacuum. Same as rough vacuum; the vacuum usually provided by forepumps or roughing pumps. High Vacuum (HV). The pressure region at or below 10-3 torr. Leaks and Virtual Leaks. All vacuum systems leak, it is just a matter of degree. In practice we consider a leak to be any extra leakage that tends to increase the normal "leak-free" pressure. These leaks should be detectable by the mass spectrometer if a gas or solvent is applied to the leaking area. But in practice this is not always as simple a test as it seems. If gas or liquid is trapped inside the vacuum envelope, it may leak out into the system. For example, air trapped under a gasket seal within the mass spectrometer will give a "leak spectrum" but is not detectable from the outside. These are virtual leaks; they will eventually pump away, but this may take days or even weeks. Vacuum Terms Mean Free Path. Distance traveled by a molecule in its normal kinetic motion before it strikes another molecule. Partial Pressure. The pressure contribution due to each component of a mixture of gases. Pascal. The standard unit of pressure corresponding to a force of 1 newton per square meter (1 N/m2); named after the French scientist Blaise Pascal. Pumping Speed. The amount of gas at a specified pressure pumped away by a pumping system, expressed as volume per unit of time. Rough Vacuum. The vacuum usually provided by a rotary pump, typically in the range 1.3 X 102 to 1.3 X 10-1 Pa (1 to 10-3 torr). Sometimes referred to as backing pressure from the use of a rotary pump (or a forepump) to back a diffusion pump. Vacuum Terms Torr. A unit for measurement of pressure. Defined as the pressure required to support a column of mercury 1 mm high. Named after 17th-century vacuum researcher Evangelista Torricelli. 1 torr = 1 mm Hg = 133.332 Pa. ≈ 133 Pa 1 atm = 101 325 Pa = 1.01325 bar Vacuum. Any pressure below atmospheric pressure. Very High Vacuum (VHV). Pressure at or below 10-6 torr. UltraHigh Vacuum (UHV). The pressure region at or below 10-8 torr. Viscous or Turbulent Flow. The flow of a gas in which the motion of each gas molecule is dependent on its neighbors and there are frequent collisions and mixing. Laminar or Molecular Flow. The flow of a gas in which the motion of each gas molecule is considered to be independent of its neighbors and there are rare collisions. Vacuum Pressure Units And Typical System Parameters The international standard of measure for pressure in the SI system of units is the pascal (Pa). Traditionally in high vacuum work the torr has been the base unit for measurement and it is still widely used. One torr is equivalent to 133.332 Pa, or 1 Pa is equivalent to 7.5 X 10-3 torr. Typically, rotary pumps achieve pressures around 1 Pa, and diffusion pumps work in the millipascal range and lower. The pascal, defined as a force per unit area, is more meaningful at these low pressures than the torr, which is defined as the pressure needed to support a column of mercury 1 mm high. At 1.3 X 10-6 Pa (10-8 torr), the approximate limit for most GC/MS systems, the pressure is insufficient to support a column of mercury even one atom high. Nevertheless, even at this low pressure there will be about 3.8 X 1010 molecular impacts on each square millimeter of the vacuum chamber surface per second. Vacuum Pressure Units And Typical System Parameters Amazingly, the mean free path at this pressure (10-8 torr), is about 5 km, and the number of molecules per cubic centimeter is about 2.7 X 108. At atmospheric pressure there are 2 X 1019 molecules per cubic centimeter. Each second, 3 X 1023 molecules "hit" each square centimeter of a container's surface, exerting a force on the container. The mean free path of each molecule is 6.5 X l0-8 m.* For a typical mass spectrometer with a path length of 500 mm, the pressure must be reduced to 1.3 X 10-2 Pa (10-4 torr) or less throughout the mass spectrometer to prevent collisions. In practice, this means that the pressure must be 5 to 10 times lower in the main pumping region to allow for pumping speed restrictions caused by slits and lenses and for the statistical spread in actual free paths of all the molecules present. Further reductions in pressure are necessary to accommodate the high field strengths and very long path lengths encountered in some instruments. *These figures are approximate only and are based on nitrogen gas at room temperature. Vacuum Components The GC/MS vacuum system consists of a number of units and assemblies, as shown in Figure 1. The requirements will vary from one instrument to another, but the essential components are high-vacuum and low-vacuum pumps, pipe-work, baffles, valves, gauges, sensors, and gas supply controllers. In addition there are unseen elements, such as pump oils and vacuum seals. Various aspects of these components and their relevance to GC/MS instruments are discussed in the following pages Figure 1. The basic GC/MS vacuum system arrangement. Rotary Pumps There are a number of different types of rotary pumps. All use the same principle of taking a large volume of low-pressure gas and compressing it to a smaller volume by the action of a rotating device. The most common type used on GC/MS systems consists of a cylindrical rotor mounted eccentrically in a cvlindrical chamber (Figure 2). Spring-loaded rotor blades are mounted diametrically through the rotor sealing against the inner surfaces of the chamber. The rotor is turned by an electric motor either directly or via a belt drive. The rotor blades are free to move in and out of the rotor and will sweep out a varying volume as the pump is turned. The gas inlet port is connected to the point of largest enclosed volume, and the outlet port is arranged to coincide with the smallest compressed volume. Gas is ejected through a spring-loaded flap valve, which prevents gas from reentering the pump. The sealing is further improved by immersing the pumping assembly in an oil bath and allowing some of the oil into the pump chamber. This seals the small end gaps between the rotor blades and pumping chamber. The oil also serves as a lubricant. Small-bore oilways allow some oil along the drive shafts into the rotor chamber. This lubrication reduces pump wear by lowering friction between rotor blades and the cylinder walls. Even so, the pump will run quite hot. Rotary Pumps As a consequence, the oil must be suitable for high-temperature operation, producing a low vapor pressure even in the presence of air and other gases and vapors. Highly refined hydrocarbon oils are usually used, sometimes with additives to prevent oxidation. The limiting pressure for a rotary pump depends principally on its compression ratio and the oil vapor pressure. To improve the compression ratio, pumps are often made with two chambers or stages connected in series. With good oils 1.3 X 10 -2 Pa (10 -4 torr) can be achieved, but this can be significantly degraded when pumping condensable vapors such as water vapor, as found in air, and solvents that are usually derived from divertors dumping the gas chromatograph solvent front. As the pumped gas is compressed, the partial pressure of an included vapor may reach its saturation vapor pressure. If this occurs before all the gas reaches atmospheric pressure, when the flap valve would normally open, the vapor will condense and will then be trapped as a liquid in the pump oil. When this oil reenters the pumping chamber via the oilways, the solvent or water may evaporate, thus setting a limit on the ultimate pressure obtainable. Figure 2. Cross section or a rotary vacuum pump. Rotary Pumps Gas Ballasting. To overcome the problem of condensation, a system of gas ballasting is used. Once the rotor passes the inlet port, the gas is trapped at a reduced pressure in a decreasing volume. If some air from outside is allowed to enter this space, the pressure quickly builds up, forcing open the flap valve before the vapor partial pressure reaches saturation. Condensation is therefore prevented. In addition, the large amount of gas pumped through the oil gives a large surface area for further vapor evaporation. The frequency with which a pump must be gas ballasted will depend on each application and the location in the pumping system. Some pumps may require ballasting once a week, while others may never need this attention. Pumping efficiency is reduced during ballasting, because air leakage past the rotor blade edges causes backstreaming into the vacuum system. Even with ballasting, pump oils eventually become contaminated, and they should be changed at regular intervals if pumping speed is to be maintained. Pumping speed is a function of size and speed of rotation. A direct-drive pump usually has a greater pumping speed than a belt-driven unit of about the same physical size, but wear on the rotor blades and oil seals is greater. Diffusion Pumps The diffusion pump moves gas from one area to another by establishing conditions in which the mean free path for molecules in one direction is greater than in the opposite direction. The diffusion pump consists of an enclosed chamber in which a stack of concentric jets are mounted (Fig. 3). A small charge of oil covers the bottom of the chamber, which is heated strongly. The oil boils vigorously, producing a heavy vapor stream, which passes up the inside of the stack and out through the jets. These are angled downwards so that the escaping vapor produces a cloud of molecules moving rapidly toward the bottom of the pump. The outside of the pump is cooled, usually by a water jacket or cooling rings but sometimes by an air blower. The oil vapor is condensed and runs down to the bottom of the pump into the boiler to repeat the cycle. Any gas molecules that happen to diffuse into the pump will suddenly encounter a strong stream of particles moving predominantly downwards. Consequently, the gas molecules will be driven down to the lower part of the pump. A pressure difference of up to five orders of magnitude can be developed across the pump. Diffusion Pumps Diffusion Pumps Unfortunately, the diffusion pump cannot operate with its outlet to the atmospheric pressure. Under such conditions there would be a number of problems: - The vapor jets would encounter such a large number of molecules that the flow would become turbulent and not necessarily downwards. The oil would have to be heated much more strongly to achieve a sufficiently high boiling rate. -There would be significant oxidation of the oil and pump elements. -Even five orders of magnitude reduction in pressure would give only about 1.3 Pa (10-2 torr) inlet pressure if the pump operated with its outlet at atmospheric pressure. - Hence, it is necessary for the diffusion pump to be backed by another pump, which must be capable of operating with its inlet in the 1.3 to 0.13 Pa (1O -2 to 10-3 torr) region and its outlet at atmospheric pressure. This is usually accomplished with a rotary vacuum pump. Diffusion Pumps The diffusion pump can create an ultimate vacuum of about 1.3 X 10 -6 Pa (10-8 torr) with an outlet pressure of 0.13 Pa (10 -3 torr). This may take some time to achieve depending on the pumping speed and the rate of outgassing of the system. One problem that can occur is that gas molecules entering the pump are condensed with the oil and are then boiled off, cycling around the pump and reducing its efficiency. To overcome this problem the pump is designed so that a significant portion of the boiling oil, with impurities, is allowed to pump along the backing arm. A series of baffles cool the vapor slowly so that most of the oil condenses and runs back but the impurity is held in a warm gaseous state and is pumped away. There is always a steady but small loss of diffusion pump oil to the backing pump. Also, while the flow of oil vapor from the jets is predominantly downwards, some does escape upwards. The oil loss is usually so slow that the pumps need only be checked every 12 to 18 months. Diffusion Pump Fluids The ultimate pressure obtainable with a diffusion pump depends on the vapor pressure of the pumping fluid. Cold baffles reduce the ultimate pressure, but it is still the characteristics of the fluid that set the limit. Fluids of very low vapor pressure have to be used. The choice of fluid will depend on the pumping requirements in each application. The principal types available are discussed below. Diffusion Pump Fluids Polyphenyl Ether Oils. These organic oils are used extensively in GC/MS systems. There are a number of types, and they should not be mixed. They are very susceptible to oxidation if operated with a large air throughput. Silicone Oils. Oils based on silicon polymers. They will tolerate more air than polyphenyl ether oils and so are often used in inlet vacuum interlocks. Unfortunately, they crack and eventually oxidize to form silica (silicon dioxide), a very hard insulating material. They are not suitable for areas where the critical instrument components cannot be physically cleaned. That is, they may be acceptable in source and slit areas that can be abrasively cleaned but are disastrous if deposited on electron multipliers. Hence, they are not generally used in diffusion pumps in the main system. Mercury. An efficient pump fluid, but it has a high vapor pressure, 0.13 Pa (10-3 torr), at room temperature. Some form of cold baffle is therefore essential, and there is a real danger of the mercury migrating from the pump to the baffle surface. Mercury vapor is also very corrosive and extremely toxic, and hence it is not often used in GC/MS systems. Turbomolecular Pumps The pumping action of a turbomolecular pump is similar in some respects to that of a diffusion pump, in that the mean free path of gas molecules is greater in one preferred direction. With diffusion pumps, this is due to collisions with molecules of the pump oil vapor. In turbomolecular pumps, the gas molecules collide with moving rotor blades. The mean free path in an open enclosure would be equal in all directions, but the collisions with the rotor impart energy to the gas in a preferred direction. Consequently the gas is moved, that is pumped, through the rotor/stator assembly. As the gas is pushed through the pump, its pressure is increased. If the pressure is increased to a point where the mean free path becomes small and a collision with another gas molecule rather than the rotor is more likely, then the pumping action will cease. To prevent this, the turbomolecular pump must be backed by another type of pump, usually a rotary mechanical pump. Turbomolecular Pumps A cross section of a typical turbomolecular pump is shown in Figure 4. A normal rotor/stator arrangement has a number of disk pairs, which act as pumps in series. As the pressure is increased along the rotor, the pumping characteristics of the rotor blades must vary. The blades near the high-vacuum end of the pump must have a high pumping speed, and compression ratio is sacrificed. At the low- vacuum, high-pressure end the compression ratio must be high, and pumping speed is compromised. The two types of blades can be seen in the photograph of a typical turbomolecular pump rotor in Figure 5. Rotor speeds vary with type, but a typical unit will operate at 40,000 rpm and some go as fast as 80,000 rpm. Consequently, the assembly must be very carefully balanced to prevent vibration. At these high speeds the rotor bearings must be lubricated The bearing oil could get quite hot and vaporize, streaming into the vacuum system if water or blown air cooling were not used. Even so, bearing life is limited and bearings and their oil have to be replaced at regular intervals. Changing bearings on single-rotor vertically mounted pumps is a job for a specialist, as the rotor has to be removed and balanced when it is replaced. On the horizontally mounted double-rotor versions, bearing replacement is usually more straightforward and can be done on site. Figure 4, Sectional view of a Pfeiffer turbomolecular pump. 1. Motor; 2. oil-cooled bearing; 3. rotor assembly; 4. ultrahigh vacuum flange; 5. rotor disk; 6. stator disk; 7. roughing vacuum line; 8. heater; 9. water cooler. (Arthur Pfeiffer GmbH) Figure 5. Rotor assembly of a pfeiffer TPU 510 turbomolecular pump. (Arthur Pfeiffer GmbH) Turbomolecular Pumps There is always the possibility of small particles, ionizer screws, or solids probe cups entering the GC/MS vacuum system. Even quite a small object hitting a rotor traveling at 50,000 rpm can cause it to disintegrate. To protect it, a fine mesh is usually fitted across the throat of the pump. Turbomolecular pumps are usually vented directly to atmospheric pressure. Electronic trips are fitted to protect the drive motor and its controller from the overload. The pump is usually fitted with a venting flange. Air entering at this point will rush through the pump toward the backing pump lines. This prevents bearing oil from the rotary and turbomolecular pumps from being blown into the vacuum chamber. It is normal to fit a filter on the vent inlet to prevent particles from entering the pump, and often GC/MS manufacturers fit an air-drying unit. This not only acts as a particle filter but also prevents moisture from entering the vacuum chamber, improving its subsequent pumpdown characteristics. Venting takes only about a minute; the pump stops quite quickly due to the friction of the air loading. Pumpdown takes longer, 10 min being typical. Oil and Vapor Traps Cold Baffles. To prevent backstreaming of oil out of the top of diffusion pumps, some form of high conductance cold baffle is often used. Baffles can take the form of chevrons, disks, rings, or concentric cylinders and are usually cooled. With concentric cylinders, the inner cylinder has a tube to the outside so that it can be filled with refrigerated alcohol or liquid nitrogen. The other types can be cooled with liquids at either normal or reduced temperatures or by means of thermoelectric devices known as Peltier effect coolers. Apart from preventing oil loss from the diffusion pump, the cold baffles can act as pumps. If molecules coming into contact with the surface are cooled sufficiently they will condense and no longer contribute to the partial pressure of the gas in the vacuum system. Other molecules hitting the baffle may cause them to be knocked off with sufficient energy to reenter the gas phase. Hence the cold baffles are efficient pumps only when a very high vacuum has already been established. Oil and Vapor Traps Foreline Traps. There is always a small amount of oil vapor backstreaming from a rotary pump. This backstreaming will increase when the pumps have a significant gas throughput or when there is a leak in the pumping lines. The oil mist entering the pumped enclosure is undesirable. It gives rise to a high back- ground spectrum in the mass spectrometer and reduces the efficiency of diffusion pumps. Source and transfer line contamination is also a problem when backstreaming occurs in interface backing pumps. To prevent this contamination, a trap can be fitted in the pumping line immediately above the rotary pump inlet port. These foreline traps consist of a relatively large chamber containing pellets of a molecular sieve material. The chamber is made large enough to give a satisfactory conductance. Oil mist and some vapors are absorbed by the molecular sieve and hence do not stream further back down the line. In time the molecular sieve becomes saturated and loses its efficiency. In addition to oil vapor, it may well absorb significant amounts of water and solvent vapors. It is then necessary to recharge the filter trap. The old sieve pellets can be restored by baking. This is sometimes done in situ, by an enclosed foreline trap heater. It is then necessary to isolate the pumping line immediately above the trap to prevent massive backstreaming. To improve the pumping of the out-gassed water and solvent, it is normal to open the gas Vacuum Gauges Pirani Gauges. Operating in the region from 1333 Pa (10 torr) down to 0.13 Pa (10-3 torr), Pirani gauges are used to measure the pressure in backing pump lines and other areas normally evacuated by rotary pumps. The gauge contains resistance elements that form part of a resistance bridge or Wheatstone net circuit. The bridge out-of-balance voltage is a function of the vacuum pressure. A typical arrangement is shown in Figure 6. The bridge circuit consists of two stable resistors Rl and R2 and the Pirani gauge resistors R3 and R4. A voltage is applied across the resistor arrangement. The Pirani gauge resistors are very temperature dependent. They are heated by the current flowing through them, and their resistance changes. Resistor R3 is cooled by the surrounding gas, and so its resistance is a function of the local pressure. Resistor R4 is not cooled by the surrounding gas in the vacuum system but by thermal contact with the gauge enclosure. As a result, it compensates for ambient temperature changes. The bridge out-of-balance voltage, VB , is therefore a function of the pressure and independent of operating temperature changes. The greater the vacuum pressure, the greater the number of cooling gas molecules and hence the greater the out-of-balance voltage. This voltage could be displayed directly on a galvanometer calibrated in pressure units, but it is more usual to feed the signal via buffer amplifiers to linearizing and display circuits. Vacuum Gauges Figure 6. Vacuum measurement using a Pirani gauge. Vacuum Gauges Thermocouple Gauge. As with Pirani gauges, thermocouple gauges are used in backing lines; and they operate from about 1.3 X 104 Pa (100 torr) down to 1.3 X 10-1 Pa (10-3 torr). They are extremely simple in construction and require simple driving circuits, but their response characteristic is very nonlinear. The gauge consists of two dissimilar wires mounted in the vacuum enclosure to form a cross. They are spot welded together at the center. Figure 7.Vacuum measurement using a thermocouple gauge Vacuum Gauges Thermocouple Gauge. One of the wires is heated by an applied ac voltage, as shown in Figure 7. The mains line voltage is converted to a symmetrical square wave by a limiting circuit and applied to a driving transformer. The output of the transformer is used to heat the gauge wire AC. Wire BD forms a thermocouple junction with wire AC. A metering circuit connected between the center-tapped transformer output and the thermocouple will sense the temperature-dependent voltage but not the heating ac voltage. A temperature-dependent resistor (thermistor) Rl is usually fitted inside the gauge connector to compensate for ambient temperature changes. Vacuum Gauges Thermocouple Gauge The temperature of the wire is dependent on the applied voltage and on the rate of cooling by the surrounding gas. The heating voltage is made independent of mains variations by the limiting circuit, and so the output voltage of the thermocouple is a function of the gauge pressure. Although normally provided, the output connection D is not needed in this circuit arrangement. Figure 7.Vacuum measurement using a thermocouple gauge Vacuum Gauges Ion Gauge. Below about 1.3 X 10-1 Pa (10 -3 torr) there are insufficient gas molecules for cooling effects to be used as a gauge system, and ionization techniques must be used. The Bayard- Alpert ion gauge can measure pressures of 1.3 X 10 -6 Pa (10 -8 torr) or less, with an upper limit of about 1.3 X 10 -1 Pa (10 -3 torr). Electrons emitted from a heated filament (Fig. 8) are accelerated toward an open grid. They collide with gas molecules to produce positive ions by an electron-impact mechanism. The positive ions are collected, and the resultant current, which is a function of the ion gauge pressure, is measured. Figure 8. Typical ion gauge control circuits Vacuum Gauges Ion Gauge. A control circuit regulates the emission of electrons from the filament by controlling the filament- heating current and hence the temperature. Typically the filament is held at —30 V with respect to ground. It is mounted outside a grid, normally an open coil, which is held at about +150 V. Electrons are therefore accelerated toward the grid and may make several traverses before reaching it. If an electron comes close to a gas molecule, a positive ion may be formed as a result of an inelastic collision. The number of ions formed is a function of the gas pressure. Ions formed inside the coiled grid are trapped electrically and will be driven to the coaxial collector wire, giving a pressure-dependent current into the electrometer measurement circuit. Vacuum Gauges Ion Gauge. The electrons hit the grid with a significant amount of energy and may cause the generation of soft x-rays. These can impinge on the collector, causing photoelectric emission. This will cause a small amount of current to be sensed even if there are no gas molecules in the gauge. The resultant pressure apparently measured is known as the x-ray pressure limit. The small area of the collector wire limits this effect, so pressures down to 1.3 X 10~6 Pa (10~8 torr) can be measured accurately. Ions collected on the wire give up their charge and re-form as neutral molecules. They may return to the gas phase or stay adsorbed on the collector surface. The ion gauge therefore acts as an ion pump and it is necessary to degas the gauge from time to time. This is usually achieved by using the grid coil as a heater. A large current is passed through the grid coil, which raises the gauge temperature. Heating for 10 to 15 min every week is usually enough to outgas it sufficiently. Some ions are formed outside the coiled grid; they are repelled and will stick to the gauge enclosure. These external ion/electron pairs usually recombine to form neutral molecules, which may well stick to the gauge's inner surface. As the surface becomes "dirty," significant tracking may occur between the collector grid and filament feedthrough, causing the gauge to give erratic or erroneous readings. This, too, can be overcome by outgassing the gauge by periodically heating the coil for 10 to 15 min. Vacuum Seals Mass spectrometer vacuum chambers are not usually made from a single enclosure but rather from a number of parts connected together. To ensure the vacuum integrity of each joint, a vacuum seal is required. As with the vacuum chamber, the seals must be impervious to gas flow, and the material of the seal must be soft enough to match exactly to the mating surfaces. It should also show a low vapor pressure and a low rate of outgassing, so that there is no significant contribution to the residual gas in the system. Seals can be divided into two basic categories, demountable and moving. The material used for each type will depend on the exact function and operating conditions of the seal. Demountable Seals. Some parts of the vacuum system are joined semipermanently, but it is necessary to open up or take apart sections from time to time for routine servicing and repairs. If this were not the case, then the joined parts could be welded together. "Rubber" O-rings are commonly used, especially for medium- to high-vacuum applications. A number of different elastomers have been tried, and the major problem with them is the outgassing of hydrocarbons. For GC/MS work a compromise between the partial pressure and the nature of the outgassed material is necessary. To minimize the effect on system performance it is necessary for the outgassed material to be of low molecular weight. This becomes even more critical if the seal is to be operated above room temperature. Vacuum Seals The most common rubberlike material used for O-rings is Viton. At room temperature, Viton tends to outgas water, carbon monoxide, and carbondioxide with very little hydrocarbon. As the temperature rises, the hydrocarbon levels also rise, but even so the seal is satisfactory for most applications up to almost 100°C and can be used in systems that have to be baked (outgassed by heating) up to about 300°C. These properties have led to an increasing use of Viton seals in GC/MS vacuum systems in recent years. For lower backgrounds at elevated temperatures and for the operation at very high or ultrahigh vacuum, it is necessary to use metal seals. These have the disadvantage of having to be replaced each time the seal is opened, although with care some knife-edge flange gaskets can be reused several times. In this type of seal, the surfaces to be joined are machined so as to form sharp projections or knife edges. These cut into either side of the metal gasket which is formed into a flat ring. Oxygen-free, high conductivity (OFHC) copper, a soft, high quality copper, is usually used. When opening up the chamber or replacing an old copper gasket, it is often necessary to pry the pieces apart. Care must be taken not to damage the small knife edges of the flanges. Vacuum Seals O-rings and knife-edge flanges do not allow the joined parts to mate precisely, and the actual alignment will depend on the tightness of the flange bolt and the size of the seal. In areas where alignment is critical, spigot flanges are often used. The two joining pieces are carefully machined to give a precise fit. A very thin ring of soft metal is used to effect a seal, gold and indium being the most common. These rings, only a fraction of a millimeter in diameter, are compressed almost to nothing as the flanges are bolted together and the precise alignment is maintained. Indium and gold rings are not reusable, although the material is usually saved as valuable scrap. Vacuum Seals Figure 9. Three types of demountable vacuum seals, a) O-ring in retaining groove. Note how trapped gas pockets are minimized by correct ratio of O- ring to groove size, b) Knife-edge seal, c) Spigot flange. Gold or indium ring (seen in cross section here) compresses to a very thin seal. Vacuum Seals Moving Seals. Vacuum interlock valves and solids probe inlet seals must show properties similar to those of demountable seals, as well as being resilient enough to form a seal while moving (or to a moving part, such as a probe wand). Viton and Teflon are the most commonly used materials. For connections to a very high vacuum, a single seal is not usually sufficient, the leak rate during motion being too great. In order to overcome this problem, two or three seals are used in series, as shown in Figure 10. Often the space between the seals is pumped independently as this greatly reduces the leak rate to the high-vacuum enclosure. Wear is usually high, and these seals tend to have a short life. Teflon , in particular, tends to flow, and seals made from it have to be replaced regularly. In some cases, Viton seals can be lubricated. The lubricating fluid must show the same high qualities as the rest of the vacuum chamber. Apiezon greases and even diffusion pump oil can be used. Only the smallest quantities should be applied, or there will be a serious risk of system contamination. Excess grease or oil can also trap gas, giving rise to virtual leaks. Figure 10. Differentially pumped sliding seal Valve Requirements in GC/MS Valves may be used to separate different parts of the system. Isolation valves above diffusion pumps, for instance, allow the operator to vent the manifold region to atmosphere without switching off and cooling the pump heaters. This is a great time-saver, as the pumps may take up to an hour to cool and a similar time to warm up. The differential pressure across the isolation valve is often used to good advantage to hold the valve firmly closed; this allows the use of relatively hard and therefore long-lasting seal materials. Before the diffusion pump isolation valves are opened, the manifold must be evacuated. A valve between the manifold and a rotary pump is opened to reduce the pressure sufficiently. This valve must be closed before the isolation valves are opened, or significant rotary pump oil backstreaming will occur. It is also necessary to allow objects or gases into the vacuum chamber. Vacuum interlocks usually have two valves, one connected to a rough pumping line and another allowing entry to the chamber. In the case of a probe inlet, the probe wand is positioned and an outer seal is tightened. The trapped air is then pumped away by opening the valve to a rotary pump. When the pressure is low enough, the valve to the main vacuum chamber can be opened and the probe inserted. There is usually a significant leak as the probe wand slides through the seal. A second seal at the high-vacuum side of the assembly helps minimize the effect of such a leak. Valve Requirements in GC/MS Gases may also be admitted to the vacuum system from batch inlets or calibration sample vials, or from chemical ionization (CI) reagent gas inlets. The valves used for this purpose must provide both the on/off and flow-regulation functions. Valves that are satisfactory for carrying gases or liquids under pressure may not work well when the pressure differential is reversed. It is important that the valve be chosen specifically for vacuum applications with due consideration to the contribution made to the background spectrum by the valve materials. It is also important to choose a valve that can handle the gases used. Some CI reagent gases are very corrosive, and the correct type of valve metal body and synthetic seals must be specified. Other Pumping Arrangements The pumping arrangements discussed so far are by no means the only approaches manufacturers have used on their GC/MS systems. Hewlett- Packard, with their bench-top GC/MS, actually placed their mass spectrometer assembly inside a diffusion pump (Fig. 11). This gives a very compact arrangement, truly a bench-top instrument. A criticism of this design has been that the transfer line from the gas chro- matograph must pass through the hot diffusion pump oil at the pump base. This problem is overcome by retaining the basic tight enclosure around the mass spectrometer but using an external diffusion pump (Fig. 12). The package is still quite small and is easily accommodated in a bench-top unit. The transfer line and ion source can be independently heated, an important consideration for use in the chemical ionization mode. An interesting feature of two instruments described above is the mass analyzer flange seal. An elastomer O-ring sealing against a flared mouth is used. The vertical mounting arrangement makes use of the analyzer's weight as well as the vacuum to hold it in place. As a consequence, bolts are not required to secure the assembly. Figure 11. A novel solution to GC/MS vacuum system design. The HP 5992 mass analyzer is shown being placed inside its own diffusion pump. (Hewlett-Packard Corporation) Figure 12. The compact HP 5995 B vacuum system