TQM Reviewer Midterm PDF
Document Details
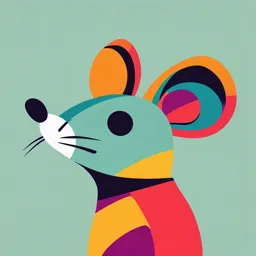
Uploaded by PrudentArchetype
Tags
Related
Summary
This document reviews key concepts in operations management, including factors of production, goods vs. services, and quality function deployment. It also discusses continuous improvement methods like Six Sigma and Taguchi concepts.
Full Transcript
CHAPTER 1: OPERATIONS AND PRODUCTIVITY Provider, not product is often transportable Site of facility important for customer interaction Production is the creation of goods and services....
CHAPTER 1: OPERATIONS AND PRODUCTIVITY Provider, not product is often transportable Site of facility important for customer interaction Production is the creation of goods and services. Revenue generated primarily from the intangible Operations management (OM) is the set of activities that service creates value in the form of goods and services by transforming inputs into outputs Production management deals with decision-making related to production processes to ensure goods or services are Inputs (Factors of Production) produced according to specifications, in the required amount, 1.Natural Resources on schedule, and at minimum cost. (E.S. Buffa) 2.Human Resources 3.Raw Materials Production management is the process of planning and 4.Capital regulating the operations responsible for transforming materials into finished products. (A.W. Field) Outputs 1.Product Production management is concerned with the process of 2.Service converting inputs (such as men, materials, money, and methods) into outputs like goods or services. (H.A. Harding). Goods are physical products that can be seen, touched, or possibly consumed. Operations management involves three main types of decisions: Services are primary or complementary activities that do not directly produce physical products. Production planning – Decisions on where, when, and how production will occur, including site locations and obtaining Characteristics of Goods necessary resources. Tangible product Production control – Focuses on controlling quality and Consistent product definition costs, scheduling, and managing Production usually separates from consumption day-to-day operations. Can be inventoried Low customer interaction Improving production and operations – Developing more efficient methods for producing goods or services. Characteristics of Service Intangible product Why Study OM? Produced and consumed at same time Often unique OM is one of three major functions (marketing, High customer interaction finance, and operations) of any organization Inconsistent product definition We want (and need) to know how goods and services Often knowledge-based are produced Frequently dispersed We want to understand what operations managers do OM is such a costly part of an organization Goods Versus Services Organizing to Produce Goods and Services Attributes of Goods (Tangible Product) Essential functions: Can be resold Some aspects of quality measurable ❖ Marketing - generates demand Selling is distinct from production ❖ Production/operations - creates the product Product is transportable ❖ Finance/accounting - tracks how well the Site of facility important for cost organization is doing, pays bills, collects the more. Site of facility important for customer contact Often easy to automate Revenue generated primarily from tangible product Attributes of Services (Intangible Products) Reselling Unusual Difficulty to inventory Quality difficult to measure Selling is part of service Frederick W. Taylor ❖ Born 1856; died 1915 ❖ Known as 'father of scientific management' ❖ In 1881, as chief engineer for Midvale Steel, studied how tasks were done ❖ Began first motion and time studies ❖ Created efficiency principles Taylor's Principles ❖ Management Should Take More Responsibility for: ❖ Matching employees to right job ❖ Providing the proper training ❖ Providing proper work methods and tools ❖ Establishing legitimate incentives for work to be accomplished Frank & Lillian Gilbreth ❖ Frank (1868-1924); Lillian (1878-1972) ❖ Husband-and-wife engineering team ❖ Further developed work measurement methods ❖ Applied efficiency methods to their home and 12 children! ❖ Book & Movie: "Cheaper by the Dozen," book: "Bells on Their Toes” Henry Ford ❖ Born 1863; died 1947 The Heritage of OM ❖ In 1903, created Ford Motor Company ❖ In 1913, first used moving assembly line to make Division of labor (Adam Smith 1776; Charles Model T Babbage 1852) ❖ Unfinished product moved by conveyor past work Standardized parts (Whitney 1800) station Scientific Management (Taylor 1881) ❖ Paid workers very well for 1911 ($5/day!) Coordinated assembly line (Ford/ Sorenson 1913) Gantt charts (Gantt 1916) W. Edwards Deming Motion study (Frank and Lillian Gilbreth 1922) ❖ Born 1900; died 1993 Quality control (Shewhart 1924; Deming 1950) ❖ Engineer and physicist The Heritage of OM ❖ Credited with teaching Japan quality control methods Computer (Atanasoff 1938) in post- WW2 CPM/PERT (DuPont 1957) ❖ Used statistics to analyze process Material requirements planning (Orlicky 1960) ❖ His methods involve workers in decisions Computer aided design (CAD 1970) Flexible manufacturing system (FMS 1975) Productivity Productivity = Units produced / Input used Baldrige Quality Awards (1980) Computer integrated manufacturing (1990) Measure of process improvement Globalization (1992) Represents output relative to input Internet (1995) Only through productivity increases can our standard of living improve Eli Whitney ❖ Born 1765; died 1825 Productivity Challenge ❖ In 1798, received government contract to make Productivity is the ratio of outputs (goods and services) 10,000 muskets divided by the inputs (resources such as labor and capital) ❖ Showed that machine tools could make standardized parts to exact specifications The objective is to improve productivity! ❖ Musket parts could be used in any musket Important Note! country, a global firm has the means to relocate unneeded Production is a measure of output only and not a measure of personnel to more prosperous country. efficiency Missions and Strategies Labor Productivity An effective operations management effort must have a mission Productivity = Units produced / Labor-hours used so it knows where it is going and a strategy so it knows how to succeed. Multi-Factor Productivity Productivity= Output / Labor + Capital + Material + Energy + Mission states the purpose or rationale for organization's Miscellaneous existence. This provides boundaries and focus for organizations and the concept around which the industry can rally. Also known as total factor productivity Strategy is an organization's action plan to achieve the mission. Outputs and inputs are often expressed in dollars Each department has a strategy for achieving its own mission and at the same time helping the firm attain the overall mission. LESSON 2: Operations Strategy In A Global Environment For many firms/organizations, the operations function provides a competitive advantage. Globalization means the speedup of movements and exchanges (of human beings, goods, and services, capital, technologies or Competitive advantage implies the creation of a system that cultural practices) all over the planet. has a unique advantage over competitors. According to WHO, globalization can be defined as the increased interconnectedness and interdependence of peoples 1. - is concerned with providing uniqueness. This can be and countries. attained, for example, through innovative design, by providing a broad product line, by offering excellent Globalization is the process by which ideas, knowledge, after-sale service, or through adding a sensory information, goods and services spread around the world. In experience to the product or service offering. The idea business, the term is used in an economic context to describe of experience differentiation is to engage the customer integrated economies marked by free trade, the free flow of to use people's five senses so they become immersed, capital among countries and easy access to foreign resources, or even an active participant in the product. Example including labor markets, to maximize returns and benefit for the on this are Disney with its Magic Kingdom and Hard common good. Rock Cafe with its classic rock music, big screen rock Reasons to Globalize videos, memorabilia, etc 1. Reduce Costs - Foreign locations with lower wage rates and tariffs can lower direct and indirect costs. 2. Improve the Supply Chain - The supply chain can be 2. Low-Cost leadership - Entails achieving maximum improved by locating facilities closer to countries with unique value, as perceived by the customer. This can be resources attained, for example, via low overhead, effective 3. Provide Better Goods and Services - In order to provide capacity use, or efficient inventory management. A better goods and services, we need a better understanding of low cost strategy does not imply low quality. differences in culture and of the way business is done in different countries. 4. Understand Markets - Interacting with foreign customers 3. Response - also referred to as flexible response, is a and suppliers can lead to new opportunities. Knowledge of the set of values related to rapid, flexible, and reliable markets not only helps industries understand where the market performance. This can be attained, for example, by is going but also helps them diversify their customer base, add offering a flexible product line, reliable scheduling, or production flexibility, and smooth the business cycle. speedy delivery. In practice, differentiation, low cost, and response can increase productivity and generate a 5. Learn to improve operations - Learning cannot be done sustainable competitive advantage. Proper alone. Industries are able to serve their customers well when implementation of the following decisions by OM will they are open to free flow of ideas. allow these advantages to be achieved. 6. Attract and Retain Global Talent - Global organizations can attract and retain better employees by offering more employment opportunities. During economic downturns in one Ten Strategic OM Decisions Decisions must be made regarding desired levels of reliability and stability, and system must be established to maintain that Differentiation, low cost, and response can be achieved when reliability and stability. managers make effective decisions in 10 areas of OM. These are collectively known as operations decisions. The 10 Issues in Operations Strategy decisions of OM that support missions and implement strategies Perspective utilized before establishing and attempting to are: implement a strategy: 1. Goods and service design: 1. Resources view Designing goods and services defines much of the This is a method used to evaluate the resources at their disposal transformation process. Costs, quality, and human resource and manage or alter them to decisions are often determined by design decisions. Designs achieve competitive challenge. usually determine the lower limits of cost and the upper limits of quality. 2. Value-chain analysis. 2. Quality: The customer's quality expectations must be This is a method that is used to identify activities that represent determined and policies and procedures established to identify strengths, or potential strengths and may be opportunities for and achieve that quality. developing competitive advantage. 3. Process and capacity design: 3. Five forces method. Process options are available for products and services. Process This is a method of analyzing the five forces- immediate rivals, decisions commit management to specific technology, quality, potential entrants, customers, suppliers, and substitute products, human resource use, and maintenance. These expenses and in the competitive environment. capital commitments determ much of the firm's basic cost structure. Strategy Development and Implementation Once OM understands the firm itself and the environment, a 4. Location selection: SWOT analysis should follow., then the key success factors Facility location decisions for both manufacturing and service should be identified as well as the core competencies. organizations may determine the firm's ultimate success. Errors made at this juncture may overwhelm other efficiencies. SWOT Analysis is a formal review of the internal strengths and weaknesses and 5. Layout design: the external opportunity and threats. This provides an excellent Material flows, capacity needs, personnel levels, technology model for evaluating a strategy. decisions, and inventory requirements influence layout. Core competencies. are the set of unique skills, talents, and capabilities that a firm 6.Human resources and job design: does at a world-class standard. They allow a firm to set itself People are an integral and expensive part of the total system apart and develop a competitive advantage. design. Therefore, the quality of work life provided, the talent and skills required, and their costs must be determined. Organizations that prosper identify their core competencies and 7. Supply-chain management: nurture them. While McDonald's KSFs may include layout, its These decisions determine what is to be made and what is to be core competency may be consistency and quality. purchased. Consideration is also given to quality, delivery, and innovation, all at a satisfactory price. Mutual trust between Analyze the Environment. buyer and supplier is necessary for effective purchasing Identify the strengths, weaknesses, opportunities, and threats. Understand the environment, customers, industry, and 8. Inventory: competitors. Inventory decisions can be optimized only when customer satisfaction, suppliers, production schedules, and human Determine the Corporate Mission resource planning are considered. State the reason for the firm's existence and identify the value it wishes to create 9. Scheduling: Feasible and efficient schedules of production must be Form a Strategy developed; the demands on human resources and facilities must Build a competitive advantage, such as low price, design or be determined and controlled. volume flexibility, quality, quick delivery, dependability, after- anie services, or broad product lines. 10. Maintenance: Global Operations and Strategy Options 3. Organization lags in its knowledge of new technology due to weakened functional divisions. International business 4. Team members have no functional area home, their Team is any firm that engages in international trade or investment members worry about life-after-project because they have Multinational corporation (MNC) 2. Functional Project - At the other end of the project A firm that has extensive involvement in international business, organization spectrum is the functional project, owning or controlling facilities in more than one country housing the project within a functional division. The organizational structure might look like the one shown Operations managers of international and multinational firms below: approach global opportunities with one of four operations strategies: Advantages 1. Team members can work on several projects. 2. Technical expertise is maintained within the functional area INTERNATIONAL STRATEGY even if individuals leave the project or organization. A strategy in which global markets are penetrated using exports 3. There is a functional area where team members go back to and licenses. after completing the project. Functional specialists can advance vertically. MULTIDOMESTIC STRATEGY 4. A critical mass of specialized functional area experts A strategy in which operating decisions are decentralized to each country to enhance local responsiveness. Disadvantages 1.Aspects of the project that are not directly related to the GLOBAL STRATEGY functional area get shortchanged A strategy in which operating decisions are centralized and 2.Motivation of team members is often weak. headquarters coordinates the standardization and learning 3.Needs of the client are secondary and are responded to slowly. between facilities. 3. Matrix Project This attempts to blend the properties of functional and TRANSNATIONAL STRATEGY pure project structures. A strategy that combines the benefits of global- scale Each project utilizes people from different functional efficiencies with the benefits of local responsiveness. areas. The project manager decides what tasks and when they LESSON 3: PROJECT MANAGEMENT need to be performed but functional managers control which people and technologies are to be A project refers to a series of related tasks directed toward some major output that requires to be completed in a specified time Senior management decides whether a weak, balanced or strong considering costs and quality constraints. form of a matrix. This refers to whether project managers have little, equal or more authority Structuring Projects than the functional managers who control the resources. 1. Pure Project -is a self-contained team works full time Disadvantages on the project. It is a small project oriented team that 1. There are two bosses. Who is listened to first, the functional is autonomous, an entrepreneurial center of manager or the project manager? opportunity and characterized by speed and flexibility 2. Requires strong negotiating skills from the project manager. (Tom Peters). 3. Sub-optimization is a danger as project managers might hoard resources for their own project and consequently harming Advantages other projects. 1. Only the project manager has full authority over the project. 2. Team members report to only one boss. Project management involves planning, directing and 3. Lines of communication are shorter so that decisions are controlling resources (people, equipment and material) to meet quick the technical, cost and time constraints of the project. The primary challenge of project management is to achieve all of Disadvantages the project goals within the given constraint. 1. Resources are duplicated because equipment and people are not shared across projects. IMPORTANCE OF PROJECT MANAGEMENT 2. Team members are often both physically and psychologically removed from headquarters so that organizational goals and policies are ignored. 1. Strategic Alignment -Ensures what is being delivered is Identifying precedence relationships right and will deliver real value against the business Sequencing activities opportunities Determining activity times & costs 2. Clear Focus and Objective - Ensure there's a proper plan for Estimating material & worker requirements executing on strategic goals. Determining critical activities 3. Quality Control - Ensures the quality of whatever is being delivered, consistently hits the mark. Purposes of Project Scheduling 4. Leadership - Brings leadership and direction to projects. 1. Shows the relationship of each activity to others and to the 5. Risk Management - Ensures risks are properly managed and whole project mitigated against to avoid becoming issues. 2. Identifies the precedence relationships among activities 6. Orderly Process - Ensures proper project process is followed 3. Encourages the setting of realistic time and cost estimates for throughout the project life cycle. each activity 7. Subject Matter Expertise - Someone needs to be able to 4. Helps make better use of people, money, and material understand if everyone's doing what they should. resources by identifying critical bottlenecks in the project 8. Continuous Oversight - Ensures a project's progress is tracked and reported properly. Scheduling Techniques 9. Managing and Learning from Failure and Success - It 1. Ensure that all activities are planned for learn from the successes and failures of the past. 2. Their order of performance is accounted for 3. The activity time estimates are recorded Phases of Project Management: 4. The overall project time is developed 1. Planning- This includes goal setting, defining the project and team organization Project Life Cycle 2. Scheduling - This phase relates people, money, and supplies to specific activities and relates these to activities 1.Definition Stage - This stage has two parts. The first part 3. Controlling - Monitors resources, costs, and budgets. It also involves conceptualizing the project. The organization, here, revises or changes the plan. may recognize the need for the project or respond to a request for a proposal from a potential customer or client. Project Planning In this phase a project organization is usually formed to make The second part involves conducting the feasibility studies.This sure existing programs continue to run smoothly on a day to day examines the expected costs, benefits and risks of undertaking basis while new projects are successfully completed. the project. The Role of the Project Manager Goals, specifications, tasks, responsibilities and teams for the Highly visible Responsible for making sure that: project are set; the project manager is appointed. All necessary activities are finished in order and Sometimes referred to as the initiation stage. A business on time problem (or an opportunity) is usually identified and might The project comes in within budget solicit several solutions. The feasibility then is conducted to The project meets quality goals explore the ability of different solutions in solving the problem The people assigned to the project receive or taking advantage of the opportunity at hand. motivation, direction, and information 2.Planning Stage This stage spells out details of the work and the risks involved. This entails preparing specifics for the followin: Project managers should be: Good coaches Project Plan: Outlines the activities, tasks, Good communicators dependencies and time frames. Able to organize activities from a variety of disciplines Resource Plan: Lists the labor, equipment and materials required. Project Scheduling Financial Plan: Identifying the labor, equipment and This phase involves sequencing and allotting time to all project materials costs. activities. The manager decides how long each activity will take Quality Plan: Provide quality targets, assurance and and compute how many people and materials will be needed at control measures each stage of production. Managers also chart separate Risk Plan: Highlight potential risks and actions taken schedules for personnel needs by type of skill. Gantt charts are to mitigate them. also used in scheduling. Acceptance Plan: List the criteria to be met to gain customer acceptance. Project Scheduling Communications Plan: List the information needed to inform stakeholders. Questions PERT & CPM Can Answer Procurement Plan: Identify products to be sourced from suppliers. 1. When will the entire project be completed? 2. What are the critical activities or tasks in the project? The project is now ready for execution after all these plans are 3. Which are the noncritical activities? put in place. 4. What is the probability the project will be completed by a specific date? 3. Execution Stage Involves implementing each of the activities and tasks in project 5. Is the project on schedule, behind schedule, or ahead of plan.Monitoring and controlling activities are executed to schedule? ensure that the deliverables of the project are met. Changes, 6. Is the money spent equal to, less than, or greater than the risks and issues are identified and reviewed against the budget? acceptance criteria.This phase often accounts for the majority 7. Are there enough resources available to finish the project on of time and resources consumed by a project. time? 8. If the project must be finished in a shorter time, what is the 4. Delivery Stage way to accomplish this at least cost? Involves delivering the final deliverables to the customer, handing over project documentation, terminating supplier Approaches for drawing a project contracts, releasing project resources (reassigning personnel and dealing with any leftover materials and equipment) and 1.Activity on node (AON) - a network diagram in which nodes communicating the closure of the project to all stakeholders. designate activities. A post implementation review is undertaken to quantify the overall success of the project and list any lessons learned for 2.Activity in arrows - in which arrows designate activities. The future projects. nodes here represent the starting and finishing times of an Closure is achieved. activity and are also called events. So the nodes here do not consume time and resources. Project Management Techniques 1. Gantt Chart PERT and CPM 2. Critical Path Method 3. Program Evaluation and Review Technique Network techniques Developed in 1950's CPM by DuPont for chemical plants (1957) PERT by Booz, Allen & Hamilton with the U.S. Navy, Gantt charts for Polaris missile (1958) are low-cost planning charts used in scheduling resources and Consider precedence relationships and allotted time interdependencies Each uses a different estimate of activity times Critical Path Method (CPM) This was developed for scheduling maintenance shutdowns at CPM assumes we know a fixed time estimate for each activity chemical processing plants owned by Du Pont. maintenance and there is no variability in activity times projects are performed often in this industry. reasonably PERT uses a probability distribution for activity times to allow accurate time estimates for activities are available. for variability CPM is based on the assumptions that project activity times can be estimated accurately and that they do not vary. Three time estimates are required Six Steps PERT & CPM Optimistic time (a) - if everything goes according to plan 1. Define the project and prepare the work breakdown structure Pessimistic time (b) - assuming very unfavorable conditions 2. Develop relationships among the activities decide which activities must precede and which must follow others Most likely time (m) - most realistic 3. Draw the network connecting all of the activities Estimate 4. Assign time and/or cost estimates to each activity 5. Compute the longest time path through the network- this is called the critical path 6. Use the network to help plan, schedule, monitor, and control the project If an activity has only a single immediate predecessor, its ES equals the EF of the predecessor If an activity has multiple immediate predecessors, its ES is the maximum of all the EF values of its predecessors ES Max (EF of all immediate predecessors) The earliest finish time (EF) of an activity is the sum of its earliest start time (ES) and its activity time EF = ES + Activity time Computing Slack Time After computing the ES, EF, LS, and LF times for all activities, compute the slack or free time for each activity Slack is the length of time an activity can be delayed without delaying the entire project Perform a Critical Path Analysis Earliest start (ES) = earliest time at which an activity can start, assuming all predecessors have been completed Earliest finish (EF) = earliest time at which an activity can be finished Latest start (LS) = latest time at which an activity can start so as to not delay the completion time of the entire project Latest finish (LF) = latest time by which an activity has to be finished so as to not delay the completion time of the entire project LESSON 4: FORECASTING Forward Pass Forecasting Predicting future event Begin at starting event and work forward Underlying basis of all business decisions Production Earliest Start Time Rule: Personal Inventory Facilities Jury of Executive Opinion Involves small group of high-level experts and Short-range forecast managers Up to 1 year, generally less than 3 months Group estimates demand by working together Purchasing, job scheduling, workforce levels, job assignments, production levels Combines managerial experience with statistical Medium-range forecast models 3 months to 3 years Relatively quick 'Group-think' disadvantage Sales and production planning, budgeting Sales Force Composite Long-range forecast salesperson projects his or her sales 3 years Combined at district and national levels New product planning, facility location, research and Sales reps know customers' wants development Tends to be overly optimistic Types of Forecasts Delphi Method Iterative group process, continues until consensus is Economic forecasts reached Address business cycle - inflation rate, money supply, 3 types of participants housing starts, etc. Technological forecasts Predict rate of technological progress 1. Decision makers Impacts development of new products 2. Staff 3. Respondents Demand forecasts Predict sales of existing products and services Consumer Market Survey Ask customers about purchasing plans Strategic Importance of Forecasting What consumers say, and what they actually do are often different 1. Human Resources - Hiring, training, laying off workers Sometimes difficult to answer 2.Capacity - Capacity shortages can result in undependable delivery, loss of customers, loss of market share 3.Supply Chain Management - Good supplier relations and Quantitative Methods price advantages Used when situation is 'stable' and historical data exist Existing products Seven Steps in Forecasting Current technology 1. Determine the use of the forecast Involves mathematical techniques 2. Select the items to be forecasted e.g., forecasting sales of color televisions 3. Determine the time horizon of the forecast 4. Select the forecasting model(s) 5. Gather the data Quantitative Method Approaches: 6. Make the forecast 7. Validate and implement results 1. Naive Approach 2. Moving Average Forecasting Approaches 3. Exponential Smoothing 4. Trend Projection Qualitative Methods 5. Linear Analysis Used when situation is vague and little data exist New products New technology Naive Approach Assumes demand in next period is the same as demand Involves intuition, experience e.g., forecasting sales on in most recent period - e.g., If January sales were 68, then February sales will be 68 Internet Sometimes cost effective and efficient Qualitative Method Approaches: Can be good starting point Aggressive new product development requires that CHAPTER 5: DESIGNS OF GOODS AND SERVICE organizations build structures internally that have open communication with customers, innovative product Product Strategy - An effective product strategy connects development cultures, aggressive R & D, strong leadership, product decisions with investment, market phase and product formal incentives, and training. life cycle, and defines the breadth of the product line. Brainstorming is a technique to generate new ideas where a Product Decision - Product decision refers to the selection, diverse group of people share, without criticism, ideas on a definition, and design of products. particular topic. Its objective is to develop and implement a product strategy that New Product Opportunities meets the demands of the marketplace with a competitive 1. Understanding the customer advantage. 2. Economic change 3. Sociological and demographic change Criteria of an Effective Product Strategy: 4. Technological change 5. Political/legal change 1. Selection of Goods and Services 6. Market practice, professional standards, suppliers, Product selection is choosing the good or service to provide distributors. customers or clients by developing a competitive advantage through differentiation, low cost, rapid response or a 1.Understanding the customer combination of the is the premier issue in new-product development. Many products are initially thought of and even prototyped by users Product Life Cycle: rather than producers. Hence operations managers must be "tuned in" to the market and particularly these innovative lead users. 2.Economic change brings increasing levels of affluence in the the long run but economic cycles and price changes in the short run. In the long run, for instance, more and more people can afford automobiles, but in the short run, a recession may weaken the demand for automobiles. 3.Sociological and demographic Introduction change may appear in such factors as decreasing family Fine tuning may warrant unusual expenses for size. This trend alters the size preference for homes, Research apartments, and automobiles. Product development Process modification and enhancement 4. Technological change makes possible everything from cell phones to iPods to artificial Supplier development hearts. Growth Product design begins to stabilize 5. Political/legal change Effective forecasting of capacity becomes necessary brings about new trade agreements, tariffs, and government Adding or enhancing capacity may be necessary requirements. Maturity Competitors now established 6. Other changes may be brought about through market High volume, innovative production may be needed practice, professional standards, suppliers, and distributors. Improved cost control, reduction in options, paring down of product line Stages of Product Development System Decline Unless product makes a special contribution to the organization, must plan to terminate offering Product-by-Value Analysis Lists products in descending order of their individual dollar contribution to the firm Lists the total annual dollar contribution of the product Helps management evaluate alternative strategies 2. Generating Goods and Services QUALITY FUNCTION DEVELOPMENT (QFD) Quality function deployment is a process for determining customer requirements(customer “wants”) and translating them into the attributes (the “hows”) that each functional area can understand and act on. One of the tools of QFD is the house of quality. The house of quality is a graphic technique for defining the relationship between customer desires and product (or service). To build the house of quality, we perform seven basic steps: 1. Identify customer wants 2. Identify how the good/service will satisfy customer wants 3. Relate customer wants to product how 4. Identify relationships between the firm's hows 5. Develop importance ratings 6. Evaluate competing product 7. Compare performance to desirable technical attributes \ Four Approaches for Product Development Historically - distinct departments Duties and responsibilities are defined Difficult to foster forward thinking A Champion Product manager drives the product through the product development system and related organizations Team approach Cross functional - representatives from all disciplines or functions Product development teams, design for manufacturability teams, value engineering teams Japanese "whole organization" approach No organizational divisions Product development teams Teams charged with moving from market requirements for a product to achieving product success. Concurrent engineering Use of participating teams in design and engineering activities. Manufacturability and value engineering Activities that help improve a product's design, production, maintainability, and use. ISSUES FOR PRODUCT DESIGN The Ethical Approach 1.Robust Design - a design that can be produced to View product design from a systems perspective requirements even with unfavorable conditions in the Inputs, processes, outputs production process. Costs to the firm/costs to society Consider the entire life cycle of the product Product is designed so that small variations in Goals for Ethical and Environmentally Friendly Designs production or assembly do not adversely affect the product 1. Develop safe and more environmentally sound products Typically results in lower cost and higher quality 2. Minimize waste of raw materials and energy 3. Reduce environmental liabilities 2. Modular Design - a design in which parts or components of 4. Increase cost-effectiveness of complying with environmental a product are subdivided into modules that are easily regulations interchanged or replaced. 5. Be recognized as a good corporate citizen Products designed in easily segmented components Adds flexibility to both production and marketing Guidelines for Environmentally Friendly Designs Improved ability to satisfy customer requirements 1. Make products recyclable 3.Computer-aided design (CAD) - interactive use of a 2. Use recycled materials computer to develop and document a product. 3. Use less harmful ingredients Using computers to design products and prepare 4. Use lighter components engineering documentation 5. Use less energy Shorter development cycles, improved accuracy, 6. Use less material lower cost Information and designs can be deployed worldwide Time-Based Competition Product life cycles are becoming shorter and the rate 4.Computer-aided manufacturing (CAM) - the use of of technological change is increasing information technology to control machinery. Developing new products faster can result in a competitive advantage Utilizing specialized computers and program to control manufacturing equipment Acquiring Technology Often driven by the CAD system (CAD/CAM) By Purchasing a Firm 5.Virtual Reality Technology – is a visual form of Speeds development communication in which images substitute for the real thing but Issues concern the fit between the acquired still allow the user to respond interactively. organization and product and the host Computer technology used to develop an interactive, Through Joint Ventures 3-D model of a product from the basic CAD Both organizations learn Risks are shared Allows people to 'see' the finished design before a Through Alliances physical model is built Cooperative agreements between independent Very effective in large-scale designs such as plant organizations layout Defining The Product 6.Value Analysis – is a review of successful products that takes First definition is in terms of functions place during the production process. Rigorous specifications are developed during the design phase Focuses on design improvement during production Manufactured products will have an engineering drawing Seeks improvements leading either to a better product Bill of material (BOM) lists the components of a product or a product which can be produced more economically Engineering drawing Shows dimensions, tolerances, and materials Ethics and Environmentally Friendly Designs Shows codes for Group Technology It is possible to enhance productivity, drive down Bill of Material costs, and preserve resources Lists components, quantities and where used Shows product structure Effective at any stage of the product life cycle Design Documents for Production Production Assembly drawing Destruction Assembly chart Modularization Route sheet Reduce customer interaction, often through automation Work order Engineering change notices (ECNS) LESSON 6: MANAGING QUALITY 1. Assembly Drawing Shows exploded view of product Details relative locations to show how to assemble the product 2. Assembly Chart Identifies the point of production where components flow into subassemblies and ultimately into the final product 3. Route Sheet Lists the operations and times required to produce a component 4. Work Order Instructions to produce a given quantity of a particular item, usually to a schedule 5. Engineering change notices (ECN) correction or modification to a product's definition or documentation Engineering drawing Definition of Quality Bill of material Quality, according to W. Edwards Deming is "meeting of Quite common with long product life cycles, long customers' needs", manufacturing lead times, or rapidly changing Quality, according to J.M. Duran is "fitness for use", technologies Quality, according to Philip B. Crosby is "conformance for requirements" Configuration Management Quality, according to the American Society for Quality, is the The need to manage ECNs has led to the development totality of features and characteristics of a product or service of configuration management systems that bears on its ability to satisfy stated or implied needs. A product's planned and changing components are Others, however, believe that the definition of quality fall into accurately identified and control and accountability for several categories: change are identified and maintained For user based: quality lies in the eyes of the Product Life-Cycle Management (PLM) beholder, and higher quality means better performance, nicer features, and other improvements. Integrated software that brings together most, if not all, For manufacturing based: Quality means elements of product design and manufacture conforming to standards and "making it right the first Product design time." CAD/CAM, DFMA For Product based: Quality is a precise and Product routing measurable variable. Materials Assembly Implications of Quality Environmental The following are the reasons why quality is important: Service Design 1. Company reputation: An organization can expect its reputation for quality- Service typically includes direct interaction with the be it good or bad-to follow it. Quality will show up in customer perceptions about the firm's new products, employment practices, and supplier relations. Increased opportunity for customization 2. Product liability: Reduced productivity The courts increasingly hold organizations that design, produce, or distribute faulty products or services liable Cost and quality are still determined at the design stage for damages or injuries resulting from their use 3. Global implications: Delay customization For both company and a country to compete effectively in the global economy, products must meet Joseph M. Juran global quality, design, and price expectations. Inferior Born: December 20, 1904 products harm a firm's profitability and the country's Died: February 28, 2008 balance of payments. Joseph Juran is an internationally acclaimed quality guru, similar to Edwards Deming, Strongly Malcom Baldrige National Quality Award influencing Japanese Manufacturing Process Joseph Juran belief’s that “quality does not happen by Established in 1988 by the U.S. government accident” gave rise to the trilogy of history Designed to promote TQM practices Recent winners Philip B. Crosby Premier Inc., MESA Products, Sunny Fresh Foods, Known as the Fun Uncle of the Quality Revolution Park Place Lexus, North He popularized the idea of of the “cost of the quality” Mississippi Medical Center, The Bama that is figuring out how much it really costs to do Companies, Richland College, Texas Nameplate things badly Company, Inc. Cost of Quality (COQ) Ethics and Quality Management Refers to the cost of doing things wrong--that is, the Operations managers must deliver healthy, safe, price of nonconformance. quality products and services Poor quality risks injuries, lawsuits, recalls, and Four major categories associated with cost of quality: regulation Organizations are judged by how they respond to Prevention costs - costs associated with reducing the potential problems for defective parts or services (e.g., training, quality All stakeholders much be considered improvement programs). International Quality Standards Appraisal costs - costs related to evaluating products, processes, parts or services (e.g., testing, labs, inspectors) ISO 9000- is a set of quality standards developed by the International Organization for Standardization (ISO). The focus Internal failure - costs that occur before delivery of defective is to establish quality management procedures, through parts or services (e.g., rework, returned goods, liabilities, lost leadership, detailed documentation, work instructions, and goodwill, costs to society). recordkeeping. External costs - costs that occur after delivery of defective To become ISO 9000 certified, organizations go through a 9- to parts or services (e.g., rework, returned goods, liabilities, lost 18-month process that involve documenting quality procedures, goodwill, costs to society). an on-site assessment, and an ongoing series of audits of their products or services. Leaders in Quality ISO 14000- is a series of environmental management standards W. Edwards Deming that contain five core elements: 14 Points for Management 1.Environmental management Joseph M. Juran 2.Auditing Top management commitment, fitness for use 3.Performance Evaluation 4.Labeling Armand Feigenbaum 5. Life cycle assessments Total Quality Control Total Quality Management (TQM) Philip B. Crosby Quality is Free, zero defects ➤ refers to a quality emphasis that encompasses the entire organization, from supplier to customer. W. Edwards Deming (1900-1993) ➤ stresses a commitment by management to have a continuing company wide drive toward excellence in all aspects of Father of Quality products and services that are important to the customer. Understanding of the system ➤ management of an entire organization so that it excels in all Understanding human behavior aspects of products and services that are important to the Understanding variation success ceded to his customer. approach Taught Japan after WWII and transformed quality Deming's Fourteen Points In 1980 Transformed American quality revolution 1. Create consistency of purpose The Foundations of Six Sigma 2. Lead to promote change 3. Build quality into the product; stop depending on inspection Six Sigma 4. Build long-term relationships based on performance, not price 1. Define critical outputs and identify gaps for improvement 5. Continuously improve product, quality, and service 2. Measure the work and collect process data 6. Start training 3. Analyze the data 7. Emphasize leadership 4. Improve the process 8. Drive out fear 5. Control the new process to make sure new performance is 9. Break down barriers between departments maintained 10. Stop haranguing workers 11. Support, help, improve Six Sigma Implementation 12. Remove barriers to pride in work 13. Institute a vigorous program of education and self- Emphasize defects per million improvement opportunities as a standard metric 14. Put everybody in the company to work on the Provide extensive training transformation Focus on corporate sponsor support (Champions) Create qualified process improvement experts (Black SEVEN CONCEPTS FOR AN EFFECTIVE TQM Belts, Green Belts, etc.) PROGRAM Set stretch objectives 1. Continuous Improvement 3. Employee Empowerment TQM requires a never-ending process of continuous improvement that covers people, equipment, suppliers, This means involving employees in every step of the materials, and procedures. The basis of the philosophy production process. Enlarging employee jobs so that is that every aspect of an operation can be improved. the added responsibility and authority is moved to the The end goal is perfection, which is never achieved but lowest level possible in the organization. always sought. Techniques for building employee empowerment include: Plan-Do-Check-Act (PDCA Model) developed by Walter Shewhart as his version of continuous 1.Building communication networks that include employees improvement. 2. Developing open, supportive supervisors 3.Moving responsibility from both managers and staff to 1. Continuous Improvement production employees 4. Building high-morale organizations The Japanese use the word Kaizen to describe this 5.Creating such formal organization structures as teams ongoing process of unending improvement Quality circle is a group of employees who meet regularly with In the U.S., TQM and zero defects are also used to a facilitator to solve work-related problems in their work areas. describe continuous improvement efforts. They are trained in planning, problem solving, and statistical methods. 2. Six Sigma 4. Benchmarking The term SIX SIGMA, popularized by Motorola, Honeywell, and General Electric, has two meanings in involves selecting a demonstrated standard of TQM. products, services, costs, or practices that represent the very best performance for a process or activity. A. In Statistical sense, it describes a process, product, or service with an extremely high capability (99.9997% accuracy), and 3.4 The steps for developing benchmarks are: defects per million opportunities (DPMO) Selecting best practices to use as a standard for B. It is a program designed to reduce defects to help lower costs, performance save time, and improve customer satisfaction. Determine what to benchmark Form a benchmark team Six Sigma is a comprehensive system -- a strategy, a discipline, Identify benchmarking partners and a set of tools - for achieving and sustaining business success. Collect and analyze benchmarking information Take action to match or exceed the benchmark It is a strategy because it focuses on total customer satisfaction. 5. Just-in-Time (JIT) It is a discipline because it follows the formal Six Sigma Improvement Model known as DMAIC. The five- step The philosophy behind just-in-time (JIT) is one of Flowcharts continuing improvement and enforced prob- lem solving. JIT systems are designed to produce or deliver Tools for Identifying Problems goods just as they are needed. JIT is related to quality in three ways: Histogram JIT cuts the cost of quality: This occurs because Statistical process control chart scrap, rework, inventory investment, and damage costs are directly related to inventory on hand. Because there is less inventory on hand with JIT, costs are lower. In addition, inventory hides bad quality, whereas JIT 1. A check sheet is any kind of a form that is designed immediately exposes bad quality. for recording data. In many cases, the re- cording is done so the patterns are easily seen while the data are JIT improves quality: As JIT shrinks lead time it being taken keeps evidence of errors fresh and limits the number of potential sources of error. JIT creates, in effect, an 2. Scatter Diagram: A graph of the value of one variable early warning system for quality problems, both within vs. another variable- scatter diagrams show the the firm and with vendors. relationship between two measurements. Better quality means less inventory and a better, easier-to-employ JIT system: Often the purpose of keeping inventory is to protect against poor production 3. Cause-and-Effect Diagram: A tool that identifies performance resulting from unreliable quality. If process elements (causes) that might effect an outcome consistent quality exists, JIT allows firms to reduce all also known as an Ishikawa diagram or a fish-bone the costs associated with inventory. chart 6. Taguchi Concepts 4. Pareto charts are a method of organizing errors, problems, or defects to help focus on problem- solving These are engineering and experimental design efforts. They are based on the work of Vilfredo Pareto, methods to improve product and process design. a 19th-century economist. Joseph The goal is to identify the key component and process 5. Flowchart (Process Diagram): A chart that describes variables affecting product variation. the steps in a process Genichi Taguchi provided us with three concepts 6. Histogram: A distribution showing the frequency cy aimed at improving both product and process quality. of occurrences of a variable These are Quality robust are products that can be produced uniformly 7. Statistical Process Control Chart: A chart with time and consistently in adverse manufacturing and environmental on the horizontal axis to plot values of a statistic conditions. Taguchi's idea is to remove the effects of adverse conditions instead of removing the causes. Statistical Process Control (SPC) Quality loss function (QLF) is a mathematical function that Uses statistics and control charts to tell when to take identifies all costs connected with poor quality and shows how corrective action these costs increase as product quality moves from what the Drives process improvement customer wants. Four key steps Target-Oriented Quality is a philosophy of continuous improvement to bring a product exactly on target 1. Measure the process 2. When a change is indicated, find the assignable cause 7. Knowledge of Tools of Tqm 3. Eliminate or incorporate the cause 4. Restart the revised process Tools of TQM Inspection Tools for Generating Ideas Check sheets Involves examining items to see if an item is good or Scatter diagrams defective Cause-and-effect diagrams Detect a defective product 1. Does not correct deficiencies in process or product Tools to Organize the Data 2. It is expensive Pareto charts Issues Determinants of Service Quality 1. When to inspect 2. Where in process to inspect Reliability involves consistency of performance and dependability. It means that the firm performs the service right When and Where to Inspect the first time and that the firm honors its promises. 1. At the supplier's plant while the supplier is producing Responsiveness concerns the willingness or readiness of 2. At your facility upon receipt of goods from the supplier employees to provide service. It involves timeliness of service. 3. Before costly or irreversible processes 4. During the step-by-step production process Competence means possession of the required skills and 5. When production or service is complete knowledge to perform the service. 6. Before delivery to your customer 7. At the point of customer contact Access involves approachability and ease of contact. The best inspection can be thought of as no inspection at all; Courtesy involves politeness, respect, consideration, and this "inspection" is always done at the source-it is just doing the friendliness of contact personnel (including receptionists, job properly with the operator ensuring that this is so. This may telephone operators, etc.). be called source inspection (or source control) and is consistent with the concept of employee empowerment, where individual Communication means keeping customers informed in employees self-check their own work language they can understand and listening to them. It may mean that the company has to adjust its language for different A poka-yoke is a foolproof device or technique that ensures consumers increasing the level of sophistication with a well- production of good units every time. These special devices educated customer and speaking simply and plainly with a avoid errors and provide quick feedback of problems novice. Attributes Versus Variables Credibility involves trustworthiness, believability, and honesty. It involves having the customer's best interests at heart. Attributes Security is the freedom from danger, risk, or doubt. Items are either good or bad, acceptable or unacceptable Understanding/knowing the customer involves making the Does not address degree of failure effort to understand the customers needs. Variables Tangibles include the physical evidence of the service. Measures dimensions such as weight, speed, height, or strength Service Recovery Strategy Falls within an acceptable range Managers should have a plan for when services fail ☑ Use different statistical techniques Marriott's LEARN routine 1. Listen TQM In Services 2. Empathize 3. Apologize 4. React 5. Notify Service quality is more difficult to measure than the quality of goods Service quality perceptions depend on 1. Intangible differences between products 2. Intangible expectations customers have of those products Service Quality The Operations Manager must recognize: 1. The tangible component of services is important 2. The service process is important 3. The service is judged against the customer's expectations 4. Exceptions will occur