Test Content Part 4.pptx
Document Details
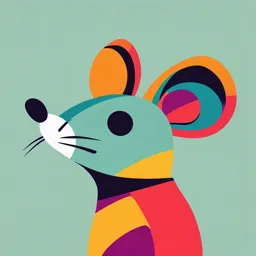
Uploaded by StimulatingScholarship
Full Transcript
Analyze 1 The 5 Why Technique o To push for root causes, start with your focused problem and then ask “Why?” several times o Example • Focused problem: Customers complain about waiting too long to get connected to staff during lunch hours Why does this problem happen? Backup operators take lon...
Analyze 1 The 5 Why Technique o To push for root causes, start with your focused problem and then ask “Why?” several times o Example • Focused problem: Customers complain about waiting too long to get connected to staff during lunch hours Why does this problem happen? Backup operators take longer to connect callers. Why does it take backup operators longer? Backup operators don’t know the job as well as the regular operator/receptionists do. Why don’t operators know the job as well? There is no special training; no job aids make up for the gap in experience and on-the-job learning for the backups. Why don’t they have special training or job aids? In the past, the organization has not recognized this need. Why hasn’t the organization recognized the need? The organization has no system to identify training needs. Verify each assumption on the spot—where the activity in question is taking place 2 Why-Why and Mile-Deep Thinking Problem Problem Problem Problem Problem Problem Problem Problem Problem Problem Problem Problem Problem A B C D E F G H I J K L M Ask the question “Why?” five times 1. “Why did X happen?” Because of W 2. “Why did W happen?” Because of V 3. “Why did V happen?” Because of U 4. “Why did U happen?” Because of T 5. “Why did T happen?” Because of S Etc. Local focus on causes Why? Wider focus on causes Why? Wider focus on causes Why? Wider focus on causes Why? Wider focus on causes Why? Wider focus on causes 3 Looking for Relationships • Graphic displays can help you structure possible causes to find relationships that will shed new light on your problem Ishikawa Diagram Tree Diagram Means Means/Objective Means Means/Objective Means Means/Objective Problem Statement Means Objective Means Means/Objective Means Means/Objective Means Means/Objective Means 4 Ishikawa Diagram Definition High number of grammar errors High number of misspelled words Reporters and editors do not review grammar Reporters and editors do not use spellchecker t no er ck ly he d lc en ’s el fri sk Sp serde u py rs co rro is e it h do k atc in o c rs ito Th t b ed jo nd ut s a bo er a rt w er po no ck Re t k che no ell sp Copy editors busy tracking down facts ’s sk de py rs co rro is e it h k atc in o c Th b t jo Reporters unaware of correct grammar Reporters have poor typing skills High number of “major errors” Results of accuracy checks unclear L no ack ta of tio s n tan da rd Hard to detect errors R m epo an rt y er so s u ur se ce s So in ur c c in or es fo re p rm ct ro vi at de i Re on do po cu rte In m rs en n do lin tin ot in e e g d g ch ito sp ec ec rs ifi ks n ot cs Re ch po ec rt ki e r ng s n fa ot ct s o Ishikawa diagrams graphically display potential causes of a problem o The layout shows causeand-effect relationships between the potential causes Accuracy checks not done High number of wrong names, numbers, and facts 5 Ishikawa Diagram Features High number of grammar errors High number of misspelled words Reporters and editors do not review grammar Reporters unaware of correct grammar t no er ck ly he d ’s lc en el ri sk f Sp serde py rs u co rro is e it h k atc do in c rs o Th b t ito jo ed nd u t s a bo er a rt w er po no ck Re ot k lche n el sp Copy editors busy tracking down facts ’s sk de py rs co r r o is e it h k atc in o c Th b t jo Arrows indicate the direction of potential causeand-effect Reporters and editors do not use spellchecker Narrowly defined problem forms the “head” of the “fish” Causes listed on the diagram should potentially contribute to this problem Reporters have poor typing skills High number of “major errors” Results of accuracy checks unclear da rd L no ack t a of tio s n tan R m epo an rt y er so s u ur se ce S s in our in cor ces fo re p rm ct ro vi at de i Re on do po cu rte m rs In en n do lin tin ot in e e g g di sp ch to ec ec rs ifi ks n cs ot Re ch po ec r t ki ers ng n fa ot ct s Hard to detect errors Accuracy checks not done Causes grouped by relationship to each other High number of wrong names, numbers, and facts Potential causes at lower level would contribute to cause at next level up The “spine” leads into the head (problem statement) Contributing causes are arranged on smaller and smaller “bones” 6 Ishikawa Diagram Uses • Stimulate thinking during a brainstorm of potential causes • Understand relationships between and among potential causes • Track which potential causes have been investigated and which have proved to contribute significantly to the problem 7 Effective Use of Ishikawa Diagrams • Start with a narrowly defined problem • Capture cause-and-effect relationships between units and subunits Incorrect request forms Math errors Wrong budget codes Late reimbursements • Causes on the diagram must be verified with 8 Common Mistakes to Avoid • Do not use this tool as an alternative form of outlining Telephones Number of lines VRUs Service problem • Do not use the tool to list potential solutions Telephone problems Get new VRU menu Purchase new system Service problem 9 Causal Thinking vs. Outline Thinking Unskilled backups Causal Thinking No method to identify training needs Company does not recognize need No job aids No training No one’s responsibility Too long to connect callers Supervisors Full-time Receptionists Backups Outline Thinking People Temporary 10 Eight-Step Process for Creating an Ishikawa Diagram 1. 2. 3. 4. 5. 6. 7. 8. Review the focused problem Identify possible causes Sort possible causes into reasonable clusters Use in conjunction Choose a cluster and label a main bone with process Develop and arrange bones for that cluster mapping, which should Develop other main bones serve as an input to Add title, date, and contact person the causeSelect possible causes to verify with data and-effect diagram 11 Step 1: Review the Focused Problem High number of “major errors” caught in the last editing stage o The newspaper team wanted to reduce the number of errors caught in the very last editing stage o The team members wrote their focused problem statement in a box with an arrow going into it 12 Step 2: Identify Possible Causes Possible Causes Reporters do not review grammar Copyeditors too busy Reporters unaware of correct grammar Standards unclear Hard to detect errors Sources provide incorrect information Spelling Reporters not checking facts Accuracy checks not done Reporters need to use spellchecker Reporters do not think it is their job to catch errors Editors do not think it is their job Editors do not review grammar Reporters think it is copydesk’s job to catch errors 13 Step 3: Sort Possible Causes into Reasonable Clusters Reporters do not review grammar Editors do not review grammar Reporters unaware of correct grammar Reporters do not think it is their job to catch errors Reporters and editors do not review grammar Spelling Copyeditors too busy Reporters need to use spellchecker Copyeditors busy tracking down facts Reporters and editors do not use spellchecker Hard to detect errors Reporters think it is copydesk’s Standards unclear job to catch errors Reporters not checking facts Editors do not think it is their job Accuracy checks not done Sources provide incorrect information o Sort the possible causes into clusters of items that seem to go together o In this example: • • • Two items have been combined in the first cluster Items that were not worded as possible causes were deleted or reworded in the second cluster One item was clarified 14 Step 4: Choose a Cluster and Label a Main Bone Cluster Copyeditors busy tracking down facts Reporters and editors do not use spellchecker Reporters think it is copydesk’s job to catch errors Editors do not think it is their job High number of misspelled words High number of “major errors” caught in the last editing stage o The other clusters were labeled “High number of grammar errors” and “High number of wrong names, numbers, and facts” 15 Step 5: Develop and Arrange Bones for That Cluster Cluster Copyeditors busy tracking down facts Reporters and editors do not use spellchecker Reporters think it is copydesk’s job to catch errors Editors do not think it is their job Additional Items Reporters have poor typing skills Reporters and editors do not know about spellchecker Spellchecker not user-friendly High number of misspelled words Reporters have poor typing skills ot rn ke ec ly d ch ell ien ’s sk Sp er-fr de y us o p rs ot s c rro it i h e on sd ink atc tor er Th to c di eck job d e l ch an spel rs rte ut po abo Re ow kn Copyeditors busy tracking down facts Reporters and editors do not use spellchecker High number of “major errors” caught in the last editing stage o The team worked through the “might cause” process and came up with three additional items for the diagram 16 Steps 6–8: Complete Diagram and Select Causes to Verify High number of grammar errors High number of misspelled words Reporters and editors do not use spellchecker Copyeditors busy tracking down facts Reporters and editors do not review grammar ’s esk yd s op s c error it i ink tch Th to ca job Reporters unaware of correct grammar not ker hec dly n ellc Sp -frie ’s r esk use yd s op s c ror t it i h er no do ink tc Th to ca ors er dit eck job h de an pellc rs s rte ut po bo Re ow a kn Reporters have poor typing skills Results of accuracy checks unclear High number of “major errors” dar d • It is important to keep in mind that a cause-andeffect diagram helps identify and organize possible causes, but these must still be verified before you take action Re p ma orte ny rs u so u s e rce s Sou r inc ces orr pr ect ovi inf de orm ati Re on p do orte cu r me s n o nt i t ng spe I nl cifi ine cs no t d edit oin ors gc he cks Re po che rte cki rs n La c ng o no k o f fac t tat ts ion stan Hard to detect errors Accuracy checks not done High number of wrong names, numbers, and facts 17 Group Activity: Creating an Ishikawa Diagram Objective: Practice creating a cause-and-effect diagram as a team Instructions: • Work in groups of five to seven people • Follow the eight steps to create an Ishikawa diagram on a flipchart or other large sheet of paper • Try to complete at least two main bones of the diagram • Be prepared to share your work with the whole class o There is no “right” answer since each group will have looked at the problem differently Time: 30 minutes 18 Short Loop 19 Analyze Phase Outcome • Using the analysis tools, you should now have identified the root causes and key inputs for the major wastes and problem areas. 20 Improve 5S+1 & Workplace Organization 21 Evolution of 5S Wording Japanese 5S Translation 5S+1 Seiri Organization S1 – Sort Seiton Orderliness S2 – Store or Set in Order Seiso Cleaning up S3 – Shine Seiketsu Cleanliness S4 – Standardize Shitsuke Discipline S5 – Sustain +1 – Safety “Workplace Organization” is another phrase that describes what 5S is all about. Remember that the scope is not merely cleaning up and arranging, but creating a culture of discipline and order to eliminate waste and improve process flow! 22 Benefits of an Organized Workplace · · · · · · Scrap Reduction Productivity increases Reduced set-up and change-over times Lower maintenance costs, higher up-time Less work-in-process and fewer supplies Improved employee safety 23 5S+1 OBJECTIVES • All unnecessary items will be removed and the areas will be organized so that only what is needed is there. • Everything will be arranged so that waste is eliminated or reduced. • It will be obvious if anything is not in its proper place. • The work and storage areas, machines, etc., will be clean and arranged to help prevent problems. • Standard procedures will be written and available where they are needed. 24 5S+1 OBJECTIVES “A PLACE FOR EVERYTHING. . . AND EVERYTHING IN ITS PLACE” DETERMINE LOCATION PREPARE LOCATION INDICATE LOCATION INDICATE ITEM INDICATE AMOUNT MAKE ORDERLINESS A HABIT 25 5S+1 S1- Sort S2 - Store, or Set in Order S3 - Shine S4 - Standardize S5 - Sustain + Safety 26 27 S1 SORT SORT OUT ALL UNNECESSARY ITEMS o “If in doubt...take it out” o “Weeding” EASIER TO FIND THINGS INCLUDES WIP, PAPERWORK, TOOLS, SUPPLIES, & EQUIPMENT IMPROVES SAFETY, COSTS, QUALITY, AND WORKING CONDITIONS 28 S2 - Store or Set in Order “A PLACE FOR EVERYTHING & EVERYTHING IN ITS PLACE.” THINGS ARE PLACED SO THEY ARE EASY TO USE, AND ALIGNED WITH THE PROCESS FLOW, “ERGONOMIC” THINGS AND THEIR SPACES ARE MARKED SO IT IS OBVIOUS WHERE EVERYTHING BELONGS (“Visual Factory”) INCLUDES EVERYTHING IN THE WORKPLACE (including personal storage) IMPROVES SAFETY, COSTS, QUALITY & WORKING CONDITIONS 29 S3 - SHINE or CLEAN-UP CLEAN-UP o (NOT MAKE PRETTY) MACHINES & EQUIPMENT AS WELL AS FLOORS & WALLS IMPROVES MAINTENANCE, SAFETY, QUALITY, & WORKING CONDITIONS UNCOVER AND FIX PROBLEMS THAT BECOME EVIDENT. 30 S4 - STANDARDIZE ESTABLISH STANDARDS & PROCEDURES - POST WORK INSTRUCTIONS - BEST PRACTICES / TECHNIQUES MAINTENANCE OF S-1, S-2 & S-3 EVERYONE FEELS RESPONSIBLE FOR CONDITION OF WORKPLACE INTEGRATED INTO EVERYONE’S JOB CONTINUOUS EFFORT TO IMPROVE WORKPLACE 31 S5 SUSTAIN (DISCIPLINE) FOLLOW STANDARDS & PROCEDURES WHEN STANDARD IS CHANGED, EVERYONE FOLLOWS NEW STANDARD MOST DIFFICULT OF THE STEPS REQUIRES EMPLOYEE INVOLVEMENT 32 33 S + 1 SAFETY ADDED TO THE TRADITIONAL “5S” MODEL AS A LOGICAL AND STRATEGIC SUPPLEMENT. Effective machine guarding Proper lock-out / tag-out Eliminate or minimize physical strain from manual handling (ergonomics) Eliminate electrical and chemical hazards Proper use of personal protective equipment Eliminate unsafe working conditions 34 WPO / 5S Exercise Conduct a Workplace Organization (S-1 only) on your wallet or purse. Plan to report your findings or results. 35 WORKPLACE ORGANIZATION S-1 SORT S-2 STORE, SET IN ORDER S +1 SAFETY S-5 SUSTAIN S-4 STANDARDIZE S-3 SHINE 36 5S Measurement Levels LEVEL 5 Continuous Improvement LEVEL 4 Focus On Reliability LEVEL 3 Make It Visual LEVEL 2 Focus On Basics LEVEL 1 Just Beginning Cleanliness problem areas are identified and mess prevention actions are in place. Needed items can be retrieved in 30 seconds with minimum movement. Potential problems are identified and countermeasures documented. Proven methods for area arrangement and practices are shared and used. Root causes are eliminated and improvement actions include prevention. Cleaning schedules and responsibilities are documented and followed. Minimal needed items arranged in manner based on retrieval frequency. Work area cleaning, inspection, and supply restocking done daily. Proven methods for area arrangement and practices are used in the area. Sources, frequency of problems are noted w/ root cause & corrective action. Initial cleaning is done and mess sources are known and corrected. Needed items are outlined, dedicated locations are labeled in planned quantities. Visual controls and indicators are set and marked for work area. Agreements on labeling, quantities, and controls are documented. Work group is routinely checking area to maintain 5-S agreements. Necessary and unnecessary items are identified; those not needed are gone. Needed items are safely stored and organized according to usage frequency. Key area items are marked to check and required level of performance noted. Work group has documented area arrangement and controls. Initial 5-S level is established and and is posted in the area. Items are randomly placed throughout the workplace. Key area items checked are not identified and are unmarked. Work area methods are not always followed and are not documented. Work area checks are randomly done and there is no 5-S measurement. Shine Standardize Needed and not needed items are mixed throughout the area. Sort Store Sustain 37 Safety Measurement Levels LEVEL 5 Continuous Improvement LEVEL 4 Focus On Reliability LEVEL 3 Make It Visual LEVEL 2 Focus On Basics LEVEL 1 Just Beginning Accident rate of 0 > 2 yrs. Ideal ergonomics with lean process flow. No protective equipment needed. Accident rate < industry average > 1 year. Accident prevention plan being implemented. Need for protective equipment reduced. Heavy lifting and movement minimized. Guarding in place and protective equipment used. Accident rate > industry average. Unsafe conditions obvious. Safety 38 WPO / 5S+1 Radar Chart IN A T US 1 SH INE 2 You can use an Excel file to do an assessment and create this radar chart: 5S+1 Assessment Levels.xls Y 3 4 5 SORT STANDARDIZE S SA FE T O ST RE 39 SEVEN WASTES Over-Production Waiting Transportation 5S+1 is another Lean tool to look for and eliminate waste. Processing Inventories Motion Defective Products 40 WORKPLACE ORGANIZATION 5S + 1 IMPLEMENTATION SUMMARY SEPARATE NEEDED ITEMS FROM UNNEEDED ITEMS, MOVE OUT UNNEEDED ITEMS, THROW OUT WHATEVER IS REALLY NOT NEEDED SET UP IDEAL ARRANGEMENT BASED ON LEAN PROCESS FLOW, INDICATE WHERE, WHAT TYPE AND HOW MANY CLEAN UP AND MAINTAIN STANDARDIZE AND DOCUMENT 41 BIB Standard Areas of application --Security Security --Machine Machine --Quality Quality --Productivity, Productivity,flow, flow,.... --Obj. Obj.::implementation implementation of of aa Michelin Michelin standard standard on on aa work work zone. zone. --Work Work direction direction :: -- Diagnose Diagnose -- Sort Sort -- Arange Arange -- Clean Cleanto toinspect inspect -- Interlock Interlock -- Sustain Sustain 42 EL-CO-MO-RE • ELCOMORE are the four steps you will use in order to tackle wastes within the process: 1. 2. 3. 4. EL – Eliminate activity CO – Combine activities MO – Modify or rearrange activities RE – Reduce or simplify the activities 43 Bib Standard Standard Bib Identity Card Card Identity Objective: Introduction of a standard for a work zone which improves safety, cleanliness and organisation without any investment by getting everybody involved. Duration: 2 deployment models Team: 1 Facilitator 1 Crew manager 4 Production workers 1– 2 Outsiders 1 Team Leader Support teams : - Safety - Maintenance - Quality - Planning Procedure: Stage 1 Diagnose Stage 2 Sort Stage 3 Stage 4 Arrange Clean to inspect Stage 5 Process locks Stage 6 Sustain 44 Quick Changeover / SMED (Bib Flex) 45 Quick Changeover What Is a Production Machine Changeover? “The internal stopped machine time between the completion of the last good part, from a Factory Order running on a machine, to the first good part on the next Factory Order!” This is often called Part-To-Part Changeover 46 Quick Changeover Production Machine Changeover Set-up Adjust Set-up: The total time from the last good part on the previous factory order to the time the first part is produced (good or bad). Adjust: Time from the end of setup to the tooling running good product in production. The time it takes to “tweak” the process to produce the first good part. 47 Quick Changeover Benefits • Reduced cycle time from Order Entry to shipment to the Customer. • Changeover time reduced. • Inventory reductions. • Improved customer service. • Improved product quality. • Reduced costs. • Free up to total capacity and resources. • Increased Sales $. 48 Quick Changeover QCO will Impact Plant Measures by: • • • • • More frequent changeovers. Smaller batches. Improved inventory turns. Reduced scrap. Improved responsiveness and flexibility of customer. 49 Quick Changeover Four Principles Pre Work: Document the Current Process and Time 1. Define Internal & External Elements 2. Convert Internal to External 3. Streamline Internal 4. Streamline External DEFINITIONS INTERNAL Those elements which are done with the machine stopped. EXTERNAL Those elements which are done while the machine is running. STREAMLINE INTERNAL Reducing the machine time (method change / improve the method). STREAMLINE EXTERNAL Reducing the labor time and cost. 50 Quick Changeover Reduction Methodology CHANGEOVER TIME 1 1RUN A INTERNAL RUN B Define Internal and External elements. 2 RUN A 50% REDUCTION RUN B Remove External elements. 3 RUN A RUN B - 75% Convert Internal to External. ADDED CAPACITY 4 RUN A -90% RUN B Streamline Internal elements. 51 BIB Flex Areas of application -Dimension -Dimensionchange change --Obj. Obj.::<<50% 50% --Low Lowinvestments investments --Before Before== Week Week-6 -6 --During During== 55days days --After= 30 After= 30day daylist list 90 90days daysDPI/MP DPI/MPand andPIT PIT --Work Workdirection direction:: -- benchmark benchmark -- Internal Internal//External External -- Ergonomic Ergonomic -- Waste Wasteelimination elimination 52 BIBflex Identity Card Objective: To simulate an optimised dimension change without major investment To estimate an optimised dimension change with investment Gains : 50% + Duration : 4-5 days Support teams: Team: 1 Facilitator 1 or 2 Production workers 1 or 2 Maintenance workers 1 or 2 set up /dimension change people 1 Quality Technician 1 Industrial Engineer 1 MP person - safety - maintenance *** - quality - central Animation: Day 1 Training Observation Summary /obj. Breakdown of zones Day 2 Training opti.zone/Creativity Implementation Day 3 Implementation Gantt training Evaluations of results Day 4 Challenge++ Size change Simulation sustainability Day 5 Construction and execution of the summary presentation 53 What If…..? When machines are scheduled, they run 100% of the time. Tooling set-up time is under 10 minutes (average). Tooling/machines are in “perfect” condition, no adjustment necessary. Standard order completion time. 54 8 RULES FOR IMPROVING CHANGEOVER RULE 1 Changeover begins and ends with work-place organization. RULE 2 Change internal changeover into external changeover, improve the remaining internal changeover, then improve external changeover RULE 3 Bolts are our enemies. RULE 4 If you have to use your hands, make sure your feet stay put. RULE 5 Don’t rely on special tooling/machine readjustment skills. RULE 6 Standardize all changeover operations. RULE 7 Standards are not changed, unless an improved method is proven. RULE 8 Successful Demonstrated Practices (S.D.P.) the best, retrofit the rest and share. 55