Steel Beam Design Calculations PDF
Document Details
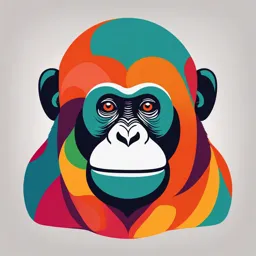
Uploaded by ReadyChicago
Tags
Summary
This document shows calculations related to steel beam design for various conditions, covering topics such as bending stress, section modulus, moment of inertia, and radius of gyration. It includes examples of calculations for different beam configurations and provides formulas for different load cases, allowing engineers to determine appropriate beam dimension and properties for structural applications.
Full Transcript
BENDING STRESS The stresses caused by the bending moment are known as bending or flexure stresses, and the relation between these stresses and bending moment is expressed by the flexure. A ) LATERALLY SUPPORTED BEAMS fb= M/S fb=bending stress S=section modulus M= bending moment 1....
BENDING STRESS The stresses caused by the bending moment are known as bending or flexure stresses, and the relation between these stresses and bending moment is expressed by the flexure. A ) LATERALLY SUPPORTED BEAMS fb= M/S fb=bending stress S=section modulus M= bending moment 1. Compact sections Fb = 0.66Fy Fb= allowable bending stress Fy= yield stress, unit tensile stress Flange width-thickness ratio: 𝒃𝒇 𝟏𝟕𝟎 ≤ 𝟐𝒕𝒇 √𝑭𝒚 bf= flange width, mm tf = flange thickness, mm Web depth- thickness ratio: 𝒅 𝟏𝟔𝟖𝟎 ≤ 𝒕𝒘 √𝑭𝒀 d= depth, mm tw= web thickness, mm 2.Non – compact section: Fb= 0.60 Fy Flange width –thickness ratio: 𝒃𝒇 𝟏𝟕𝟎 ≥ 𝟐𝒕𝒇 √𝑭𝒚 3. Partially Compact Section: 𝒃𝒇 Fb=Fy[0.79-0.000762 𝟐𝒕𝒇 𝑭𝒚 Flange width-thickness ratio: 𝒃𝒇 𝟏𝟕𝟎 𝒃𝒇 𝟐𝟓𝟎 𝟐𝒕𝒇 > √𝑭𝒚 < 𝟐𝒕𝒇 √𝑭𝒚 When Lb Lu 𝟏𝟑𝟖𝟎𝟎 Lu= 𝒅 use Fb=0.60 Fy 𝑭𝒚 𝒃𝒇𝒕𝒇 3. When Lb >Lc and Lb< Lu 𝒃𝒇 Use Fb =Fy [0.79 – 0.00076 √𝑭𝒚 𝟐𝒕𝒇 B) LATERALLY UNSUPPORTED BEAMS 1. When L > Lc L> Lu 𝟕𝟎𝟑𝟎𝟎𝑪𝒃 𝑳𝒓 𝟑𝟓𝟐𝟎𝟎𝟎𝟎𝑪𝒃 𝑭𝒚 < 𝒓𝑻< 𝑭𝒚 𝑳 𝟐 𝑭𝒚 𝟐 𝒓𝑻 Fb=[ - 𝟑 𝟏𝟎.𝟓𝟓 𝒙𝟏𝟎⁶𝑪𝒃 ] Fy 𝟖𝟑𝟎𝟎𝟎𝑪𝒃 Fb = 𝑳𝒅 𝒃𝒇 𝒕𝒇 Use biggest value of Fb but should be < 0.60 Fy 2. L > Lc L> Lu 𝟕𝟎𝟑𝟎𝟎𝟎 𝑪𝒃 𝑳 𝟑𝟓𝟐𝟎𝟎𝟎𝟎 𝑪𝒃 < < 𝑭𝒚 𝒓𝒕 𝑭𝒚 𝟏𝟏𝟕𝟎 𝒙 𝟏𝟎³ Fb= 𝑳 ( )² 𝒓𝑻 𝟖𝟑𝟎𝟎𝟎 𝑪𝒃 Fb = 𝑳𝒅 𝒃𝒇 𝒕𝒇 Use biggest value of Fb but should be < 0.60Fy 𝑰𝒚 rt = 𝑨 𝟏 𝟏 A = Af + 𝟔 Aw A= bf tf + 𝟔 h tw 𝒉 𝒕𝒇 𝒃𝒇³ ( 𝒕𝒘)³ 𝑰 𝟑 I = 𝟏𝟐 + 𝟏𝟐 rt = 𝑨 I =Iy ( approximately ) 𝟏.𝟎𝟓 𝑴𝟏 𝑴𝟏 Cb= 1.75 + 𝑴𝟐 + 0.30 ( 𝑴𝟐 )² Cb = 2.3 max. value Cb= bending coefficient dependent on moment gradient A W 775 x 287 steel beam has the following dimensions: H= 775mm total beam depth tw= 19mm web thickness b= 360mm flange width tf= 32mm flange thickness a)Determine the moment of inertia with respect to the X-axis. b)Determine the section modulus with respect to x-axis. c)Determine the radius of gyration with respect to x-axis. d)Determine the moment of inertia with respect to the y-axis. e)Determine the section modulus with respect to y-axis. f)Determine the radius of gyration with respect to y-axis. a) Moment of Inertia to the X-axis 2 𝒃𝒅³ Ix= ∑( 𝑰𝒈 + 𝑨𝒅 ) I= 𝟏𝟐 𝟑𝟔𝟎 ( 𝟕𝟓𝟓 )³ 𝟑𝟒𝟏 ( 𝟔𝟗𝟏)³ Ix = 𝟏𝟐 – 𝟏𝟐 Ix = 3,535,289, 124 mm⁴ b) Section Modulus to the X –axis 𝑰𝒙 Sx= 𝑪𝒙 𝟑,𝟓𝟑𝟓,𝟐𝟖𝟗𝟏𝟐𝟒 Sx = = 9,365,004 mm³ 𝟑𝟕𝟕.𝟓 c) Radius of Gyration to the X-axis 𝑰𝒙 𝟑,𝟓𝟑𝟓,𝟐𝟖𝟗,𝟏𝟐𝟒 rt = = = 97,743 mm 𝑨𝒕 𝟑𝟔𝟏𝟔𝟗 a) Moment of inertia to the Y-axis 𝒅𝒃³ Iy = ∑( 𝑰𝒈 + 𝑨𝒅2 ) Iy = 𝟏𝟐 𝟕𝟓𝟓 (𝟑𝟔𝟎)³ (𝟔𝟗𝟏)(𝟑𝟒𝟏)³ Iy = - 𝟏𝟐 𝟏𝟐 Iy = 652,155,974 mm⁴ b) Section modulus to the Y-axis 𝑰𝒚 𝟔𝟓𝟐,𝟏𝟓𝟓,𝟗𝟕𝟒 Sy = = = 3, 623,088 mm³ 𝑪𝒚 𝟏𝟖𝟎 c) Radius of gyration to the Y-axis 𝑰𝒚 𝟔𝟓𝟐,𝟏𝟓𝟓,𝟗𝟕𝟒 ry= 𝑨𝒕 = 𝟑𝟔,𝟏𝟔𝟗 = 18,031 mm A section of steel wide flange as shown, it laterally supported. The yield strength is Fy= 250 Mpa. Determine the allowablbe bending stress and if it is a compact or non-compact section. Solution: 𝒅 𝟏𝟔𝟖𝟎 If < Compact Section Use: Fb= 0.66FY 𝒕𝒘 𝑭𝒚 d= 755mm tw=19 mm 𝟕𝟓𝟓 𝟏𝟔𝟖𝟎 < 𝟏𝟗 𝟐𝟓𝟎 39.74 < 106.25 Use Fb= 0.66(250) Fb= 165 Mpa A 10 m. beam simply supported at the end carries auniformly distributed load of 16 Kn/m over its entire length. 16 Kn/m 10 m Which of the following give the lightest W shape beam that will not exceed a flexural stress of 120 Mpa ? a. W 610 x 82 Sx = 1870 x 10 mm³ A = 10400 mm² ω = 81.9 kg/m b. W530 x 85 Sx = 1810 x 10 mm³ A = 10800 mm² ω = 84.4 kg/m c. W 460 x 82 Sx = 1610 x 10 mm³ A = 10400 mm² ω = 81.9 kg/m d. W = 360 x 79 Sx = 1280 x 10 mm³ A = 10100 mm² ω = 79.3 kg/m 16.828 10 ² M= = 210.35kn.m 8 M= 200 kn.m 210.35 𝑥 10⁶ S= 𝑀 120 S= S = 1,752,916 mm³ 𝑓 200 𝑥 10⁶ S= 1,753 x 10³< 1810 x 10³ mm³ S= Safe 120 S = 1667 x 10³ Actual max. stress in beam: Try W 530 x 85 𝑀 f= Sx = 1810 x 10³ 𝑆 ω = 84.4 kg/m 210.35 𝑥 10⁶ f= wt of beam =84.4 ( 9.81) 1810 𝑥 10³ f = 116.22 Mpa Wt of beam = 827.96 say 828 N/m