Spuring 2024.pptx
Document Details
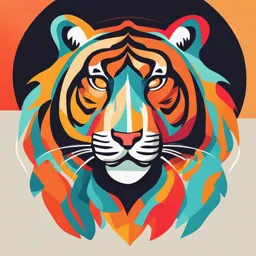
Uploaded by AdaptableSweetPea
Tags
Full Transcript
Spruing By Akhlas Elsarah Sprue Sprue Is a channel or a series of channels in the set investment through which the molten alloy flows to reach the pattern areas. Requirements: Sprue must allow molten wax to escape from mold. Sprue must enable molte...
Spruing By Akhlas Elsarah Sprue Sprue Is a channel or a series of channels in the set investment through which the molten alloy flows to reach the pattern areas. Requirements: Sprue must allow molten wax to escape from mold. Sprue must enable molten metal to flow into the mold with little turbulence as possible. Metal within the space must remain molten slightly longer than that has filled the mold, thus acting as reservoir to compensate for casting solidification shrinkage. Types of sprue formers Wax sprue former Melts at the same rate as the pattern. Allow easy escape of molten wax leaving no carbon residues. Available in different shapes and gauges. ) Plastic sprue former Advantages : used when casting FPD because they add rigidity to the pattern → decrease distortion. Disadvantages: Plastic softens at higher temperature than wax pattern – Carbon residues may be left after burning. – Plastic has higher expansion before softening than wax pattern → investment cracking. – If plastic didn’t melt at same time as wax → it will block the escape pathway of wax → wax will boil → erosion of mold inner surface → rough casting. To overcome this problem Apply a thin layer of wax over the entire surface of plastic sprue former. Hollow plastic sprues may be used. C) Metal sprue former Either solid or hollow. Removed from investment before wax elimination. Examination of the orifice after removal of sprue to make sure no investment particles has broken off → incomplete casting. Made of non rusting metal to avoid wax contamination. Hollow sprues increase contact surface area and strengthen the attachment between the sprue and pattern. Spruing methods A – Direct spruing The flow of molten metal is directly from the casting crucible to the pattern area in the ring. Requires less time and effort than indirect method. Used for single units and small multiunit patterns. Disadvantages: Back pressure porosity at the junction of the restoration and spure may occur. B – Indirect spruing The molten alloy takes an indirect route or path before it reaches the pattern area. In the indirect method, the sprue former is not attached to the wax pattern directly, but first to a large diameter horizontal wax rod called "Runner Bar". Runner bar will act as reservoir to prevent solidification shrinkage and hence the name "Reservoir Bar". Disadvantages: Only used for low density alloy like gold alloy Sprue former diameter Sprue former gauge number is 6, 8 and 10. The larger the number, the smaller the size of the sprue former diameter. The size of the sprue former usually varies according to the size of the wax pattern used as well as the casting technique used. The larger the sprue size; – The better the flow of metal. – Act as reservoir → less solidification shrinkage. In indirect spruing → the reservoir should be equal or larger than the thickest area of the largest pattern. Example; metal pontics and large molar retainer. Length: The length of the sprue former generally should not exceed 6 mm or be less than 2 mm, since both excessively long or excessively short sprue formers present problems in obtaining high quality castings. With a very long sprue former, it is more likely that the first portion to solidify will be the sprue, with resulting porosity in the casting It should be long enough to leave minimum 6mm between the wax pattern and the end of investment because if ; – Less than 6mm → the investment may fracture during casting. – More than 6mm → the air will not be able to escape during casting causing back pressure porosity. A distance of about 6-8 mm should be left between the end of the casting ring and the wax pattern in case of gypsum-bonded investment, and 3-4 mm in case of phosphate-bonded investment Sprue former attachment Sprue former is attached to the thickest part (Example; largest non functional cusp) of the wax pattern away from margins and occlusal contacts. Point of attachment should allow metal to be directed from the thickest part to all other parts of the mold without flowing opposite direction of the casting force i.e. not 90 degrees with the thickest portion). Must allow for proper positioning of the pattern in the ring. Point of attachment of sprue to pattern should be smoothed to decrease turbulence. The attachment area should not be restricted because necking increases casting porosity and reduces mold filling. Crucible former Cone shape base made of rubber or metal. It constitutes the base of the casting ring during investing. The crucible former is tall enough to allow the use of short sprue while positioning the pattern near the end of the ring. It provides a funnel to the investing ring, to facilitate entrance of molten alloy. Casting ring and liner Casting ring holds investment in place during setting and restricts its expansion. Ring liner is placed inside the ring to allow for more expansion (wetting the liner → increase hygroscopic expansion) Ring liner is made of cellulose and fiber glass. Asbestos is no longer used because it is carcinogenic. Ringless investment technique → a paper or plastic casting ring designed to allow unrestricted expansion is used with higher strength phosphate bonded investments to support the investment during setting and removed before burnout process. The aim of using a resilient liner is to: 1. Allow different types of investment expansion (act as a cushion). 2. Facilitate venting during casting procedure. 3. Facilitate the removal of the investment block after casting. Spurning technique 2.5mm diameter (10 gauge) sprue → molar crowns and metal ceramic restorations, while 2mm diameter (12 gauge) sprue → for premolar crowns and partial coverage restorations. The sprue is attached to nonfunctional cusp (thickest portion) at an obtuse angle with adjacent axial walls or occlusal surface to facilitate mold filling. Remove the pattern and insert sprue into the hole of crucible former and lute it in place with wax. Spray a surfactant (wetting agent) on the pattern → increase wetting of wax by investment. The sprue former should be attached to the thickest portion of the pattern, away from margins and occlusal contacts. Line the ring by ring liner leaving 2mm from the end of ring (to prevent the slippage of the whole mass during casting procedure) and moistens the liner. Place the ring over the pattern and check the position of pattern in the ring regarding its central position and distance between it and the end of the ring.