Investing and Casting Techniques in Dentistry PDF
Document Details
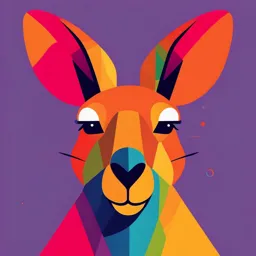
Uploaded by CureAllColosseum6953
Sana'a University
Tags
Summary
This document explores dental casting methods, focusing on the lost-wax process and various investment materials used in dental restorations. It details the selection of casting alloys, crucial investment material properties, and the sprue technique. The document also includes casting procedures and considerations, highlighting important aspects of mold construction and expansion compensation.
Full Transcript
 **Lost-wax technique** is used to convert a wax pattern into a casting. It involves three steps: **Selecting a Casting Alloy** ============================= **Classification of dental casting alloys** A. **Noble metal content: (based on chemical behavior)** B. **Cost:**...
 **Lost-wax technique** is used to convert a wax pattern into a casting. It involves three steps: **Selecting a Casting Alloy** ============================= **Classification of dental casting alloys** A. **Noble metal content: (based on chemical behavior)** B. **Cost:** C. **Physical properties and intended use:** - **Type I (soft)** used for simple inlays (class I and class V Inlays). - **Type II (medium)** used for complex inlays; class II Inlays and Onlays - **Type III (hard)**used for crowns and fixed dental prosthesis (Bridges) - **Type IV (extra hard)** used for removable partial dentures. Porcelain-type alloys with a high noble metal content have hardness similar to that of type III alloys, while base metal alloys are harder than type IV alloys. D. **ADA Dental Alloys Classification System** - **High-noble alloys** have a noble metal content of 60% or greater. At least 40% of the alloy must be gold. - **Titanium and titanium alloys** must be at least 85% titanium. - **Noble alloys** must be at least 25 % noble metal. - **Predominantly base alloys** have noble metal content less than 25%. **Requirements of investment material** - Controllable expansion to compensate for the solidification shrinkage of the alloy. - The ability to produce smooth castings with accurate surface reproduction (no nodules). - Chemical stability at high casting temperature; investment must not decompose to give off gases that could damage the surface of the alloy. - Sufficient strength to resist casting forces. - Sufficient porosity to allow for gas escape; pores in the investment allow adequate venting and prevent back-pressure porosity. - Easily manipulated. - Ease of divesting: easy recovery of the casting. - Inexpensive. **Classification of investment materials by binder (provides strength)** They are selected according to the type of casting alloy. 1. **Gypsum-bonded investment:** - It is restricted to casting of conventional type II, III and IV gold alloys. - They are not suitable for casting metal-ceramic alloys because; - The gypsum is unstable at the high temperatures, exceeding 650 °C (1200 °F). °F). - Sulfide contamination of the alloy can occur. 2. **Phosphate-bonded investment:** - They are used for casting high-gold or palladium content alloys and used for high melting point alloys. They are stable - They are the material of choice for casting metal-ceramic alloys because; - They are more stable at high temperatures, above 650 °C (1200 °F) - They expand rapidly and precisely at the temperatures used for casting alloys. 3. **Silica-bonded investment:** - It is used for casting high-melting point alloys as cobalt chromium alloys. **Spruing** - The process of attaching a sprue former or sprue pin to the wax pattern. It provides a channel through which molten alloy can reach the mold in an invested ring after the wax elimination. - Sprue former is a small-diameter pin or tube made of wax, plastic, or metal, while sprue is a channel within the hardened investment, left by the sprue former following burnout, through which molten metal flows into a mold cavity. - Sprue design depends on many factors, type of restoration, the used alloy, and the casting machine. ***Basic sprue requirements:*** - It must allow molten wax to escape from the mold. - It must enable the molten alloy to flow into the mold with as little turbulence as possible. - The metal within it must remain molten slightly longer than the alloy that has filled the mold. This provides a reservoir to compensate for the shrinkage that occurs during solidification of the casting alloy. - It must allow for centering of the pattern in the ring (a single crown should be centered in the ring, equidistant from its walls, while for fixed prosthesis that is cast as one piece, the pattern is placed near the center of a large or special oval ring, rather than if a portion of a multiunit wax pattern is only partially centered and partially near the edge of a smaller ring. ***Sprue dimensions:*** - A sprue with a relatively large diameter is recommended because this improves the flow of molten alloy into the mold and ensures a reservoir during solidification. - A 2.5-mm (10-gauge) sprue is recommended for molar crowns or metal-ceramic castings, and a 2-mm (12-gauge) sprue for premolar and partial-coverage restorations. ***Sprue attachment:*** - One end of the sprue former is attached to the wax pattern and the other end to the crucible former. - It should be attached to the bulkiest noncritical part of the pattern, away from margins and occlusal contacts. Normally, the largest nonfunctional cusp is used. - Better placement is at a 45° to the pattern to permit the stream of the molten metal to be directed to all parts of the mold without having to flow opposite the direction of the casting force. - The best castability and least porosity is produced by a sprue former--wax pattern junction that is either straight or slightly flared. - The sprue's point of attachment to the pattern should be carefully smoothed to minimize turbulence. ***Length:*** - The sprue former should be just long enough so that the highest point on the wax pattern will be 6.0 mm from the end of the ring. (Why?) to provide pathways for sufficient gas escape during casting. - If the pattern is too close to the end of the ring, the molten alloy may blast through the investment during casting; if it is too far, gases may not escape rapidly enough to permit complete filling of the mold with alloy. - Wax sprues are preferred for most castings because they melt at the same rate as the pattern and thus allow easy escape of the molten wax. - The sprue itself should be no longer than 6.0 mm to provide adequate bulk of molten alloy during solidification. -.If the sprue is too thin or too long, the gold may solidify in the sprue before it does in the larger cavity formed by the wax pattern. - If this happens, molten gold cannot be drawn from the reservoir ("button") as the casting solidifies, and shrink-spot porosity will occur in the bulkiest part of the casting. - If the sprue is directed at a right angle to a flat wall of the mold, a "hot spot" may be created at that point, or mold erosion may occur. This will keep the alloy adjacent to it molten after the rest of the casting has solidified, causing suck-back porosity. - Cellulose liners burn out before the casting is made, allowing unrestricted thermal expansion and easy escape of gases from the mold during casting. However, this deprives the investment of support by the ring and may result in cracking of the investment and fins on the casting. - The manufacturers recommend that approximately 3.0 mm of ring at each end be left unlined so that the investment will be partially supported by direct contact with the ring after the liner has burned out. - The liner should be 3.0 mm short of both ends of the ring. This will allow supporting contact of the investment with the ring after the cellulose liner has burned out. It is also theorized that this restriction near the open end willprovide for more uniform expansion ***Venting:*** - **Small auxiliary sprues or vents have been recommended to improve casting of thin patterns. These may help gases escape during casting or may ensure that solidification begins in critical areas by acting as a heat sink.** - ***Note*: internal porosity can result from using long or thin sprue. This could be overcome by using a reservoir or a larger sprue. These will maintain the alloy molten longer than the rest of the casting and supply this alloy to those areas that solidify and shrink first.** **Crucible Former** - It is the conical base to which the sprue former is attached during the investment procedure. - It can be made of rubber, plastic, or metal. This convex base makes a concave depression in the refractory material. - With most modern machines, the crucible former is tall, to allow use of a short sprue and to enable the pattern to be positioned near the end of the casting ring. **Casting Ring and Liner** - The casting ring serves as a container for the investment while it sets and restricts the setting expansion of the mold. It can be made of metal, plastic, or paper. - A liner is placed inside the ring to allow for more expansion because the liner is somewhat compressible. Use of two liners allows for additional compression and enables increased setting expansion of the investment material. - The liner must be 3mm short from the edge of the ring on both sides to provide support for the investment material, **lock the investment within the ring, equalize radial and axial expansion and** prevent longitudinal expansion. - Cellulose paper liners or refractory ceramic fiber liners are now used instead of asbestos that was used before due to its health hazards. - Help in venting. - Act as a cushion directing the thermal expansion outward. - Facilitate separation of the investment from the ring after casting. - Act as a source of water for hygroscopic expansion. ***Ringless Investment Technique*** - With the use of higher strength, phosphate-bonded investments, the ringless technique has become quite popular. - A paper or plastic casting ring is used and is designed to allow unrestricted expansion. This can be useful with higher melting alloys that shrink more because of a longer cooling trajectory.  **Sprue technique Armamentarium** A. Sprue B. Sticky wax C. Rubber crucible former D. Casting ring E. Ring liner F. Bunsen burner G. Pattern cleaner H. Scalpel blade I. Forceps **Step-by-step procedure for a single casting** - Attach a wax sprue to the bulkiest non-functional cusp of the wax pattern and position it to form an obtuse angle (135°) with the adjacent axial walls and occlusal surface to facilitate filling of the mold. - Add wax to the point of attachment and smooth it to prevent turbulence during casting. - Remove the pattern from the die, using extreme caution not to distort it. - Holding the sprue with forceps, insert it into the hole in the crucible former. It should now be luted into place with wax, and the junction between sprue and crucible should be smoothed. - Use of a surfactant (**surface tension reducer) to** minimize surface tension and enhance wetting of the pattern during investing. - Line the casting ring, keeping it flush with the open end, and moisten the liner. - Place the ring over the pattern to ensure that it is long enough to cover the pattern with about 6 mm of investment. If necessary, the sprue may be shortened, or a longer ring may be chosen.  ***Procedure for Multiple Castings*** - Two units may be cast with a runner bar, or each unit may be fed from a separate sprue. - When more than two units are being cast together, each is joined to a runner bar. A single sprue is used to feed the runner bar. **Investing** Vacuum mixing with brush application of investment is the best way for optimum results. The wax pattern should be invested immediately because any delay will lead to distortion of the pattern due to stress relief of the wax. ***Shrinkage compensation:*** While investing wax patterns, the molten alloys used for dental restorations shrink upon solidification. There are four mechanisms that can play a role in producing an expanded mold: 1. Setting expansion. 2. Hygroscopic expansion. 3. Wax pattern expansion. 4. Thermal expansion. 1. ***Setting expansion*** Setting expansion of the investment occurs because of normal crystal growth in the investment material. This type of expansion, in air, normally is about 0.4%, but expansion is partially restricted by the metal investment ring. 2. ***Hygroscopic expansion*** The investment is allowed to set in the presence of water, producing additional expansion. Maximum expansion could be achieved by immersing an investment-filled ring in a 100 F (38 C) water bath, and it ranges from 1.2% to 2.2%. **Hygroscopic expansion** Amount of setting expansion occurs when a gypsum-bonded casting investment is immersed in 38 °C water during setting. 3. ***Wax pattern expansion*** Expansion of wax pattern while the investment is still fluid occurs when the wax is warmed above the temperature at which it was formed. 4. ***Thermal expansion*** Thermal expansion of the investment occurs when the investment is heated in the burnout oven. ***Note:*** Titanium may be an ideal alternative to precious alloys for patients who are allergic to other metals and require a fixed prosthesis. **Investment for all ceramic restorations** Two types have been developed recently for producing all ceramic restorations - The first type is composed of phosphate-bonded refractories and is used for the cast glass technique. - The second type is the refractory die type of material which is used for all ceramic veneers, inlays, and crowns. - Refractory dies are made by pouring the investment into impressions, when the investment is set, the die is removed and is heated to remove gases. - Next, porcelain or other ceramic powders are added to the die surface and fired. **Investing technique Armamentarium** A. Vacuum mixer and bowl B. Vibrator C. Investment powder (gypsum or phosphate bonded) D. Water or colloidal silica E. Spatula F. Brush G. Surfactant graduated cylinder. H. Crucible former I. Casting ring and liner ***Step-by-Step Investing Procedure* (always** follow the manufacturer's instructions) - A casting ring with an outside diameter of 32 mm is used and lined with a resilient liner. - The wax pattern is coated with a surfactant. - Vacuum mixing of investment materials is highly recommended to obtain consistent results in casting with minimal surface defects, especially when phosphate-bonded investments are being used. Good results are possible with the brush application of vacuum-mixed investment or when the investment is poured into the ring under vacuum. - The correct program on the mixing unit is selected. - Investment is added to precisely measured-out liquid. - The chuck of the mixing bowl is inserted into the slot of the vacuum mixer. - The bowl is stabilized by the vacuum created between its lid and the base of the unit as mixing progresses. - A No. 6 or No. 8 brush is used to coat the pattern. - Once the pattern is completely coated, the casting ring can now be attached. - Casting ring with liner affixed to the crucible former. - The bowl is vibrated, and the ring is filled. When the investment reaches the level of the wax pattern, the ring must be tilted to reduce the risk of trapping air inside the pattern. - The ring is filled completely. **Burnout (Wax elimination)** It consists of heating the investment in the controlled furnace. ***Purposes:*** - To eliminate all moisture from the invested ring. - To eliminate the wax that is used to form the pattern from the mold cavity. - To produce the necessary expansion in investment to compensate for the alloy shrinkage. - To raise the temperature of the mold to the proper point to receive the molten metal when the cast is made. ***Step by step procedure:*** - Allow the investment to set for the recommended time (usually 1 hour), and then remove the rubber crucible former, leaving a funnel-shaped entrance to the mold (crater) - If a metal sprue is used, remove it as well. The ring should be placed in a humidor if stored overnight. - The smooth "skin" that forms on the ring with phosphate-bonded investments should be removed with a plaster knife, and any loose particles of investment should be blown off with compressed air. - Reexamine the ring for any residual particles, and then place it with the sprue and crater facing down in the furnace on a ribbed tray. The tray allows the molten wax to flow out freely. - Heat the furnace to 200°C (392°F) and hold this temperature for 30 minutes. Most of the wax is then eliminated. - Increase the heat to the final burnout temperature (generally 650°C \[1202°F\] or 480°C \[896°F\] if a hygroscopic technique is used; follow the manufacturer's instructions) and hold that temperature for 45 minutes. - The investment should not be overheated or kept at the chosen temperature too long. - Gypsum-bonded investments are not stable above 650°C. Also, some carbon in carbon-containing investments burns off, which causes increased surface roughness of the casting. *Because the heating rate affects expansion, it also should be standardized as part of the investing and casting protocol to routinely obtain accurately fitting castings.* - When the casting ring is transferred to the casting machine, a quick visual check of the sprue in shaded light is helpful to see whether it is properly heated. It should be a cherry-red color. - Burnout prepares the mold for the molten alloy and allows thermal expansion to occur. If thermal expansion alone will provide compensation expansion, a high-temperature technique (1,200°F, 650°C) is employed. If a 100°F water bath (hygroscopic technique) was used to expand the wax pattern, a lower temperature (900°F, 480°C) can be utilized. - Heating must be gradual to allow steam to escape without cracking the mold. The crucible former is carefully separated from the ring. The crater and bottom of the ring are checked for any small chips of investment, and any that are found are removed because they could contaminate the casting later. - The casting ring, with the crater down, is placed into a 600°F (315°C) oven and left for 30 minutes. By burning out in an inverted position, much of the wax will run out of the mold as it is melted, carrying any loose chips of investment with it. - Casting tongs are used to transfer the ring to a hotter furnace (either 900°F \[482°C\] or 1,200°F \[650°C\], depending on the technique used) for 1 hour. - As an alternative, the ring can be placed in a cold oven and heated slowly to the casting temperature. - The ring should be set crater up about 10 minutes before the casting is made. This allows oxygen to contact the internal area of the mold to ensure complete wax residue elimination. - A black appearance of the investment surrounding the sprue hole is an indication that there are still carbon particles from the wax permeating the investment. These can impede the escape of gases through the investment as the casting alloy enters the mold and prevent the margins from being completely cast. - A bright, clean appearance of the casting is the result of the reducing action of residual carbon and may indicate that it was cast too soon. - No more than 30 seconds should be allowed to elapse between the time the ring is removed from the oven and the molten alloy is centrifuged into the mold. - Any undue delay will cause heat loss and resultant mold contraction. Therefore, it is imperative that all materials and equipment used in casting be ready ahead of time. It is also helpful to enlist an assistant to transfer the hot ring from oven to cradle until more experience is gained. **Casting** - The casting machine requires a heat source (reducing flame of a torch or electricity) to melt the alloy and a casting force to overcome the high surface tension of the molten alloy, as well as the resistance of the gas within the mold. - The mold is not removed from the burnout furnace until the alloy has melted and is ready to cast. - The crucible should be preheated, to avoid freezing of the alloy within the crucible leading to an incomplete casting. - Cleaning a previously cast alloy is necessary to remove investment debris and oxides before its reuse - Conventional alloys can be melted with a gas-air torch, but for the metal-ceramic alloys in a higher melting range, a gas-oxygen torch is needed. - For base metal alloys, a multi-orifice gas-oxygen torch or an oxyacetylene torch is needed. **Casting technique:** **Dental flux** The Latin word for flux means "flow". Flux is a compound applied to molten alloy that dissolves or prevents the formation of oxides and other undesirable substances that may reduce the quality or strength of a solder therefore assisting in the flow of the alloy. A small amount of flux should be sprinkled onto the warmed metal ***Procedure*** - The casting machine is given three clockwise turns (four if metal-ceramic alloys are used) and locked in position with the pin. - The cradle and counterbalance weights are checked for the appropriate size of the casting ring. - A crucible for the alloy being cast is placed in the machine. - The torch (gas-air for regular alloys, gas-oxygen for metal-ceramic) is lit and adjusted. - For metal-ceramic alloys, the clinician should wear a pair of colored gogglesto protect the eyes and also to enable direct viewing of the melt. - The crucible is preheated, particularly over the trajectory that will be in contact with the alloy, and the alloy is added. Preheating avoids excessive slag formation during casting. - Also, when metal-ceramic alloys are cast, a crucible that is too cool can "freeze" the alloy, which results in an incomplete casting. - The mass of the alloy must be sufficient to sustain adequate casting pressure. With a high-density noble metal alloy, 6 g(4 dwt\*) is typically adequate for premolar and anterior castings, 9 g (6 dwt) is adequate for molar castings, and 12 g (8 dwt) is adequate for pontics. - The alloy is heated in the reducing part of the flame until it is ready to cast. - A little flux can be added to conventional gold alloys (not to metal-ceramic alloys). - Gold alloys ball up and have a mirror-like shiny surface that appears to be spinning. - Nickel-chromium and cobalt alloys are ready to cast when the sharp edges of the ingot round over. - The mold is placed in the cradle of the casting machine and kept on the alloy with the reducing flame until the crucible is moved into position. - The casting machine arm is then released to make the casting. The machine is allowed to spin until it has slowed enough so that it can be stopped by hand, and the ring is removed with casting tongs. - After the red glow has disappeared from the button, the casting ring is plunged under running cold water into a large rubber mixing bowl. - Gypsum-bonded investments disintegrate quickly, and residue is eliminated easily with a toothbrush. Final traces can be removed ultrasonically. Oxides are removed by pickling in 50% hydrochloric acid (or, preferably, a nonfuming substitute. - Phosphate-bonded investments do not disintegrate equally well, and some must be removed forcibly from the casting ring. They can be under running water. - A knife is used to trim the investment at the button end of the ring (Fig. 22-28, *A*). The other end is not trimmed because of the risk of damaging the margin. - When the ring liner is exposed, the investment can be pushed out of the ring (see Fig. 22-28, *B*). It is then broken apart under running water (because it is still hot. - The remaining investment is carefully removed with a small blunt instrument and any traces are dissolved in hydrofluoric acid or a less caustic substitute. - Care must be taken to prevents cratching of the internal surface of the casting or damage to the margins. **Accelerated casting method** - Conventional casting techniques require considerable time, typically 1 hour for bench set (generally judged as the time taken for the investment to reach its maximum exothermic setting reaction temperature) for the investment and 1 to 2 hours for the wax elimination. An accelerated casting procedure that reduces this time to 30 to40 minutes has been proposed. - Initially suggested as a way to make cast post and core restorations in a one visit procedure (also for castings made for dental licensure examinations), the procedure has been found to produce castings with accuracy and surface roughness similar to those produced by traditional methods.37,38 The technique entails the use of a phosphate-bonded investment in which approximately 15 minutes is needed for bench set and 15 minutes for wax elimination by placement of the ring in a furnace preheated to 815°C (1500°F). **Finishing metal restorations** ***Evaluation*** - The casting is never fitted on the die until the inner surface has been carefully evaluated under magnification. The internal portion of the casting is inspected for the presence of small nodules or metal bubbles. Even tiny imperfections can cause damage to the stone die. A die may be rendered useless in a matter of seconds if a casting is fitted prematurely. Ideally, the casting should touch the die only in the marginal region and there should be a slight gap ever where else for the future cement film. This space allows cement to escape as the crown is seated and provides some thermal insulation under metal crowns. The external surface is finished by first cutting the sprues from the casting using a separate disc. The coarse rubber disc is used to smooth away the roughness left by the separating disc. The casting should be seated completely before checking the occlusion. The groove on the occlusal surface is smoothed with a fissure bur, and the cusp ridges are finished with small rubber sulci disc. The inner surface should be air-abraded or sandblasted in preparation for try-in +-----------------------------------+-----------------------------------+ | **Problem/ cause** | | +===================================+===================================+ | **Rough casting** | | | | | | - Excess surfactant | | | | | | - Improper water-to-powder | | | ratio | | | | | | - Excessive burnout temperature | | +-----------------------------------+-----------------------------------+ | **Large nodule** | | | | | | Air trapped during investing | | | procedure | | +-----------------------------------+-----------------------------------+ | **Multiple nodules** | | | | | | - Inadequate vacuum during | | | investing | | | | | | - Improper brush technique | | | | | | Lack of surfactant | | +-----------------------------------+-----------------------------------+ | **Nodules on occlusal** |  | | | | | **Surface** | | | | | | Excessive vibration | | +-----------------------------------+-----------------------------------+ | **Fins/wings** | - | | | | | - Increased water-to-powder | | | ratio | | | | | | - Pattern too near edge of | | | investment | | | | | | - Premature heating (mold still | | | wet) | | | | | | - Too-rapid heating | | | | | | - Dropped mold | | +-----------------------------------+-----------------------------------+ | **Incomplete casting** | | | | | | - Wax pattern too thin | | | | | | - Cool mold or melted alloy | | | | | | Inadequate metal | | +-----------------------------------+-----------------------------------+ | **Incomplete casting with shiny, | | | rounded defect** | | | | | | - Incomplete wax elimination | | +-----------------------------------+-----------------------------------+ | **Solidification | | | shrinkage("suck-back") porosity** | | | | | | - Improper pattern position | | | | | | Narrow, long sprue | | +-----------------------------------+-----------------------------------+ | **Inclusion porosity** | | | | | | Particle of investment dislodged | | | during casting | | +-----------------------------------+-----------------------------------+ | **Marginal discrepancy** | - | | | | | - Wax pattern distortion | | | | | | Uneven expansion | | +-----------------------------------+-----------------------------------+ | **Inadequate or | | | excessiveexpansion** | | | | | | - Improper water-to-powder | | | ratio | | | | | | Improper mixing time Improper | | | burnout temperature | | +-----------------------------------+-----------------------------------+ **References** **CASTING DEFECTS** **CASTING POROSITIES** **Types of Porosity in Casting \| Casting Defects \| ASPIRE MDS \| Dr Bhaumik Joshi** Factors that increase expansion27of gypsum-bonded investments include the following: Use of a full-width ring liner Prolonged spatulation Storage at 100% humidity Lower water-to-powder ratio Use of a dry liner Use of two ring liners Hygroscopic technique with the pattern in theupper part of the ring. A. Warreth, Y. Elkareimi All-ceramic restorations: a review of the literatureThe Saudi Dental Journal, 32 (8) (2020), pp. 365-372 **INVESTING AND CASTING FULL METAL CROWN** https://youtu.be/L\_s5IDKBJmc?si=2-9vaM4qQzvh8wmx 