SOPs Purchase (Manual & Guide).docx
Document Details
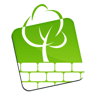
Uploaded by OldStationSupply
Full Transcript
PURCHASE MANUAL Responsible Office: Main Office Effective Date:10/05/2023 TABLE OF CONTENTS PP-000 - INTRODUCTION 3 PP-001 – PURCHASE ORDER 6 PP-001.1 - PO Creation 6 PP-001.1 A – PO Creation from a ‘Sales Order’ 7 PP-001.1 B – PO Creation from ‘Minimum Inventory’ 8 PP-001.1 C – PO Creation for ‘BUL...
PURCHASE MANUAL Responsible Office: Main Office Effective Date:10/05/2023 TABLE OF CONTENTS PP-000 - INTRODUCTION 3 PP-001 – PURCHASE ORDER 6 PP-001.1 - PO Creation 6 PP-001.1 A – PO Creation from a ‘Sales Order’ 7 PP-001.1 B – PO Creation from ‘Minimum Inventory’ 8 PP-001.1 C – PO Creation for ‘BULK Products’ 9 PP-001.2 - Order Confirmation and Updating ETA 10 PP-001.3 - Canceling POs 11 PP-001.4 - Receiving Product from POs 12 PP-001.4 A - Receiving ‘Products we Picked up at the Vendor’ 12 PP-001.4 B - Receiving ‘Full Order Deliveries from the Vendor’ 13 PP-001.4 C - Receiving ‘Partial Order Deliveries from the Vendor’ 14 PP-001.4 D - Receiving ‘Minimum Inventory’ 14 PP-001.5 – Printing Labels 15 PP-001.5 A - Printing ‘External Labels’ 15 PP-001.5 B - Printing ‘Internal Labels without Price’ 15 PP-001.5 C - Printing ‘Internal Labels with Price’ 16 PP-001.6 - Returning Material 16 PP-001.6 A - Returning Damaged Material 16 PP-002 – NEGATIVE INVENTORY 17 PP-003 – OPEN ORDERS AVAILABILITY & PICKUP LISTS 18 PP-003.1 - Creating a Pickup List 19 PP-003.2 - Creating Combined Pickup list 19 PP-003.3 – Requesting a Delivery Load 20 PP-004 – SHIPPING REPORT 21 PP-005 – COUNTING INVENTORY 23 PP-005.1 – Counting Annual Inventory 23 PP-006 – CHECKING AVAILABILITY 24 PP-007 – REQUESTING SAMPLES 25 PP-008 – PURCHASING OFFICE SUPPLIES 25 Revision History Date of Change Responsible Summary of Change October 2023 Sigrid Pessanha Document creation – v1 February 2024 Karen Mejias Document additions PP-000 - INTRODUCTION The Purchase Standard Operating Procedure (SOP) stands as a comprehensive guide that delineates the meticulous steps and standardized protocols governing the procurement processes. This SOP serves as an indispensable resource for all individuals engaged in procurement activities, ensuring a structured and efficient approach to acquiring outdoor and landscape supplies. At the heart of this document is our commitment to establishing a Purchasing framework finely attuned to the unique demands of the OSS. The primary objective is to cultivate a procurement process marked by consistency, transparency, and alignment with the distinctive needs of our business. Standard Operating Procedures functions as a compass for our procurement professionals, offering clarity on their responsibilities and serving as a reference for navigating the intricacies of the procurement lifecycle. Roles / Responsibilities Manager roles are: Oversee and manage the overall purchasing process. Develop and implement purchasing policies and procedures in alignment with company goals. Ensure compliance with budgetary constraints while maintaining product quality standards. Establish and maintain relationships with vendors to negotiate favorable terms and pricing. Provide guidance and support to the Purchaser and Receiving personnel. Review and approve purchase orders before submission to vendors. Define procurement strategies and sourcing methods. Evaluate and select vendors based on performance, quality, and reliability. Negotiate and finalize contracts, terms, and conditions with suppliers. Monitor market trends and industry changes to identify cost-saving opportunities. Resolve purchasing-related issues and disputes. Conduct regular performance reviews of vendors. Collaborate with other departments to understand their procurement needs. Purchaser roles are: Execute the purchasing process as directed by the Purchasing Manager. Prepare and process purchase orders based on approved requisitions. Source suppliers, obtain quotes, and negotiate terms within established guidelines. Ensure timely delivery while maintaining inventory levels. Collaborate with the Receiving personnel for efficient order fulfillment. Review purchase requisitions for accuracy and completeness. Identify potential suppliers and request quotations. Evaluate supplier proposals and negotiate terms. Coordinate with the Receiving personnel to confirm product specifications and quantities. Communicate with vendors to track order status and resolve delivery issues. Report any variances or discrepancies to the Purchasing Manager. Warehouse Receiving & Shipping roles are: Receive and inspect incoming shipments. Ensure the accuracy and quality of received materials. Collaborate with the Purchaser to reconcile any discrepancies. Report damaged or defective products to the Purchasing Manager. Verify received materials against purchase orders and shipping documents. Inspect products for quality and compliance with specifications. Record and report any discrepancies or damages promptly. Communicate with the Purchaser to resolve issues related to deliveries. Organize and manage the storage of received materials. Assist in periodic inventory counts and audits. Definitions Some common words used in this document are: Purchase Order - A Purchase Order (PO for short) is a document issued by Old Station to one of our vendors, indicating the types, quantities, and agreed prices for products we wish to purchase. It serves as a legally binding contract between us, outlining the terms and conditions of the transaction, including delivery dates, payment terms, and other relevant details. The PO initiates the purchasing process and provides a formal record of the agreement, facilitating smooth communication and efficient transaction processing between the facilities involved. Minimum Inventory - Minimum inventory refers to the smallest quantity of products that Old Station maintains in its inventory to ensure continuity of operations and meet customer demand during unforeseen circumstances, such as delays in supply or unexpected increases in demand. Minimal inventory acts as a buffer to prevent stockouts and disruptions in production or sales, providing a safety net to mitigate risks associated with inventory management. It represents the minimum level of inventory that Old Station considers necessary to sustain its operations while effectively managing costs and maximizing efficiency. Order Confirmation – An order confirmation is a formal acknowledgment sent by a vendor to us, confirming the details of a purchase transaction. It typically includes information such as the items ordered, quantities, prices, payment terms, shipping details, and expected delivery dates. The purpose of an order confirmation is to provide both parties with a written record of the agreed-upon terms and to ensure accuracy in the fulfillment of the order. Additionally, it serves as a contractual document that helps prevent misunderstandings and disputes by confirming the terms of the purchase. ETA – (Estimated Time of Arrival) - ETA refers to the anticipated time when the order is expected to arrive at OSS. It is an estimate provided by the vendor. Providing an accurate ETA helps manage expectations, improves customer satisfaction, and allows for better planning and coordination of customer deliveries/ pickup. RMA - (Return Merchandise Authorization) - RMA is a formal authorization provided by a vendor to us allowing the return of purchased merchandise for repair, replacement, or refund. It serves as a control mechanism for managing returns efficiently and ensures that returns are handled according to established procedures. The RMA typically includes details such as the reason for the return, the condition of the merchandise, any applicable restocking fees or return shipping instructions, and a unique authorization number. Additionally, RMAs help prevent unauthorized returns and facilitate smoother transactions between buyers and sellers. Return of Approval Form – the Return Approval Form serves as an internal and crucial document that navigates through a collaborative effort involving various departments within Old Station. Each department plays a unique role in assessing the return request, from the customer service team gathering details to the warehouse team verifying inventory status and more. Effective communication and coordination among these departments are key to streamlining the return approval workflow within each section below. PP-001 – PURCHASE ORDER The purpose of the Purchase Order procedure is to establish a systematic and efficient process for creating, managing, and tracking purchase orders for OSS. This ensures timely and accurate procurement while maintaining optimal inventory levels and providing clear guidelines for handling various order scenarios. The expected outcome of this procedure is a streamlined and standardized purchase order process that enables the company to: Fulfill customer orders promptly and accurately. Maintain an optimal inventory level to meet demand. Efficiently manage bulk and minimal inventory orders. Respond to order cancellations, pickups, and deliveries with precision. Effectively handle damaged or returned materials. Generate external and internal labels as needed. In the PP-001 module and its extensions we will cover: Creating different types of POs From a Sales Order For Minimum Inventory For Bulk Orders Sending POs to specific companies PO Confirmations and Updating ETAs Canceling POs Receiving Products from POs Printing internal and external labels Damaged material & Returning material PP-001.1 - PO Creation In PP-001.1, we will explore creating various types of Purchase Orders (POs) tailored to meet specific needs and scenarios. From generating POs derived from Sales Orders to ensuring minimum inventory levels are maintained and handling bulk orders efficiently. Whether it's converting customer requests into tangible orders, optimizing inventory management, or capitalizing on cost-effective bulk purchasing, this overview will equip you with the knowledge and tools to navigate the nuances of creating different types of POs effectively. For step-by-step guides, please refer to the supporting documents attached to this manual. PP-001.1 A – PO Creation from a ‘Sales Order’ Receive the pick sheet from sales team and verify all the information (use this checklist) Open the SO and check each item availability of each item Right clicking the Product and look up… In the Count tab - you can see in the Net Ordered field how many need to be ordered considering the already ordered and sold. In the General tab you will find information about the material, such as the minimum to request or lead time. Write on the pick sheet the number of items to be ordered or IN in case of stocked Change the item status to ORDERED or TO BE PULLED as availability and the Purchase Method to Associated or Stocked. Do not forget the pallet. Go to Process > Create Order > Click in Create and Fill out the following fields: Internal Notes tab: Customer - SO - Salesperson- Ship Date Ordered date: today Ship Via: Pickup or Delivery Description: C (Customer) or MI (Minimal Inventory) Ordered - adjust the quantity to be ordered. Memo tab: the vendor's address available in vendor id field (right clicking > look up) if pickup order. Write the PO number and quantity missing in the pick sheet Print the PO and send to approbation, first the Purchase Manager followed by CEO. **FABRICATION: The quote also needs to be signed by CEO to be send to the vendor. After approved, send by the order by email to the vendor (except to Techo-Bloc and Rafferty – procedure below) Sending by email - File> send PURCHASE ORDER (PLAIN PAPER) and select to send by outlook Select the vendor's contact and in Outlook select the template PO's and send it. **Fabrication: Scan the quote signed and send together with the PO. Write SENT – DATE in printed PO Take the sales orders and pick sheet on sales office. Put the PO in “Waiting Confirmation/ETA” folder until receive the order confirmation and the ETA. PP-001.1 A-1 - Sending Techo-Bloc POs After the internal PO approbation, access the Techo-Bloc ecommerce portal (https://orders.techo-bloc.com/) Fill out the information requested (PO Number; mode of delivery; Site; requested date) and Next. Look by the item code and Click in ADD. Fill out the quantity, unit, type and save. Click in Next to submit the order. Write “Sent – Date” and the online order number in PO and wait to order confirmation by email. Take the sales orders and pick sheet on sales office. Put the PO in “Waiting Confirmation/ETA” folder until receive the order confirmation and the ETA by email. PP-001.1 A-2 - Sending Rafferty POs After the internal PO approbation, access the Rafferty portal (https://ajax.raffertyaluminum.com/login.php) Search for the product – Usually the Rafferty code is on the end of EBMS description. Put the quantity ordered. After adding all the items, go to VIEW PALLET to confirm the order. Confirm the item, quantity ordered, price and submit the order. Change the Delivery Location, add the PO number and choose to send the order confirmation by email. Review the order and submit. Write “Sent – Date” in the PO - and wait to order confirmation by email. Take the sales orders and pick sheet on sales office. Put the PO in “Waiting Confirmation/ETA” folder until receive the order confirmation and the ETA by email. PP-001.1 B – PO Creation from ‘Minimum Inventory’ Minimum inventory refers to the lowest amount of stock that Old Station should maintain for specific products. This level ensures that Old Station can still meet customer demand without running out of the product. Steps Frequency of POs: April - June: once a week. July - November: once a week but CEO might exclude items. Winter: CEO decides how often purchasing will check the minimum inventory. Also, he might exclude items. PP-001.1 C – PO Creation for ‘BULK Products’ Creating POs for bulk items involves ordering large quantities of materials (such as Loom, Mulch, Crushed Stone, etc.) at once, ensuring we meet demand while optimizing cost-effectiveness. Steps Yard responsible will give you a bulk request. You should create a new PO, clicking in + Select the vendor of the item requested. Fill out the order date; Ship via = Delivery; Description = Bulk and the ordered date. Select the material and check the minimum quantity. Print the order, Bulk does not need any approbation. Send the PO to the vendor by email and write “sent - date” in the PO printed. Keep the PO in bulk folder until receive the material. Important: When receiving the Bulk load, make sure you receive exactly the weight you see on the vendor's paperwork and change the "ordered" quantity to be the same as you are receiving. Also, check the product's description. BE CAREFUL of changing when you ordered more than 1 load (receive all together). PP-001.2 - Order Confirmation and Updating ETA After the Purchase Order (PO) is created and sent to the vendor, we will receive the order confirmation indicating the ETA (estimated time of arrival) or if the items are available for pickup. The Purchase Admin must update all ETAs so that salespeople can relay this information to customers. This not only helps customers plan effectively but also enables salespeople to proactively address any potential delays or challenges, demonstrating their dedication to resolving issues and delivering exceptional service. Overall, regular updates on ETAs contribute to a positive customer experience and strengthen the relationship between the salesperson and the customer. Steps Print the order confirmation and staple it to PO. Confirm the following information in the order confirmation: Product ID Description (color, size, finish) Quantity (pallet quantity and main ordered) Price If something is different of PO: Check with the vendor if the product we ordered is the same that was entered. Check on speck book what is the quantity/PL to see if EBMS has the wrong quantity. If the problem is not between the speck book and EBMS, ask the vendor what is going on. Look up the product on EBMS and check the cost: If the cost on the product and order confirmation matches, highlight the wrong cost and write the correct one on the PO. DO NOT edit the cost on EBMS. If the cost on the product doesn't match with the order confirmation, check on the vendor's price list, if it as same as the price list write on order confirmation the right price and bring to purchase manager to update the material price in EBMS, if the price is different from the price list, ask the vendor to check it. IN EBMS, find the PO go to ETA tab and fill out. Send an e-mail to the salesperson if the ETA is later than the SO ship date. File the PO and Order confirmation, stapled, on the vendor’s folder. PP-001.3 - Canceling POs This process is designed to streamline the procedures involved in canceling or handling purchase orders when unexpected situations arise. In this process, we will navigate through two distinct scenarios: first, when a customer initiates a return while the associated purchase order is still pending, and second, when a vendor deletes an inventory order before fulfillment. By following these steps, you'll ensure a smooth and organized approach to canceling purchase orders, maintaining transparency, and preserving the integrity of our procurement system. Steps If a customer returns materials, and the associated purchase order is still awaiting those materials, follow these steps: Do not bring the items. Send an email to the vendor requesting order cancellation. Collect all relevant paperwork. Provide the paperwork to the purchase manager to delete the EBMS order. If you create an inventory order but do not receive the materials within a reasonable time, and the vendor deletes the order: Gather all necessary documents. Print the remaining purchase order. Hand over the paperwork to the purchase manager for removal of the items deleted by the vendor. PP-001.4 - Receiving Product from POs Receiving products from Purchase Orders (POs) involves the physical receipt and verification of goods specified in the PO by the purchasing and warehouse receiving department in Old Station’s yard. This process typically begins with the arrival of the ordered items at our yard, where they are inspected by the Warehouse Coordinator for accuracy, quality, and quantity. Upon satisfactory inspection, the purchase department must acknowledge the receipt in the Old Station's system, updating inventory records and triggering further actions, such as invoicing and payment processing. For step-by-step guides, please refer to the supporting documents attached to this manual. PP-001.4 A - Receiving ‘Products we Picked up at the Vendor’ This process refers to the process of physically obtaining and verifying the products from the PO and collected from the vendor's location. Steps The yard guy will give you the pickup list and the vendor’s shipping signed. Open the purchase order in EBMS and receive the items. Save. Open the sale order by clicking on the linked document. Update the field Item Status in sales order to “To be Pulled”. Save. Write in Pickup list the customer’s name, SO number, if it is customer pickup or delivery, received, date and initials. Find the Pick sheet at the sales office and put it on board to be pulled. Join the pickup list with the purchase order and all the other paperwork about this PO in folder orders received to be processed. Important: If the PO has remaining materials to receive, make a copy of it and keep the original one in the vendor’s folder. Confirm that all the labels were printed and gave to yard responsible, write “L” (label printed) on the side of each item received. Important: Internal materials (shelf materials) should be scanned to receive and need to write “scanned” on the side of each item scanned. PP-001.4 B - Receiving ‘Full Order Deliveries from the Vendor’ This process entails of physically acquiring and validating the products specified in the PO, which are delivered to Old Station directly from and by the vendor. Steps The yard guy will give you the vendor’s shipping list signed by him on the side of each received item. Print the receiving checklist. File> Print > Receiving checklist to receive full order Open the purchase order in EBMS and receive the items. Save. Open the sale order clicking in linked document Update the field Item Status in sales order to “To be Pulled”. Save. Write in Receiving Checklist the quantity received, the customer’s name, SO number, if it is customer pickup or delivery and received, date and initials. Find the Pick sheet at the sales office and put it on board to be pulled. Join the pickup list with the purchase order and all the other paperwork about this PO in folder orders received to be processed. Important: If the PO has remaining materials to receive, make a copy of it and keep the original one in the vendor’s folder. Confirm that all the labels were printed and gave to yard responsible, write “L” (label printed) on the side of each item received. Important: Internal materials (shelf materials) should be scanned to receive and need to write “scanned” on the side of each item scanned. PP-001.4 C - Receiving ‘Partial Order Deliveries from the Vendor’ This process entails physically acquiring and validating partial of the products specified in the PO, which are delivered to Old Station directly from and by the vendor. Steps The yard guy will give you the vendor’s shipping list signed by him on the side of each received item. Open the purchase order in EBMS If it is not delivered the full order, you are still waiting for some items, you should fill the items received in pickup list collum – do not forget to receive the pallets too. Print the Pickup List - File> Print > Pickup List to receive partial order Receive the items and Save. Open the sale order clicking in linked document Update the field Item Status in sales order to “To be Pulled”. Save. Write in Pickup List the quantity received, the customer’s name, SO number, if it is customer pickup or delivery and received, date and initials. Important: Internal materials (shelf materials) should be scanned to receive and need to write “scanned” on the side of each item scanned. Make a copy of the Purchase Order. Find the Pick sheet at the sales office and put it on board to be pulled. Join the pickup list and the vendor’s shipping confirmation with the purchase order copy in folder orders received to be processed. Confirm that all the labels were printed and gave to yard responsible, write “L” (label printed) on the side of each item received. PP-001.4 D - Receiving ‘Minimum Inventory’ The process of acquiring and confirming the receipt of a minimal quantity of products from the PO, ensuring that inventory levels are maintained at the minimum required threshold, it’s up to the vendor’s discretion to deliver or if we need to pick up. If you receive the material of a Minimal Inventory order, you should send an email to the sales team with the list of the received materials and receive them in EBMS as the customer order. In receiving checklist paperwork write “SI” (Sales Informed) instead of the customer information. PP-001.5 – Printing Labels Labels play a crucial role in accurately identifying and tracking inventory items, facilitating smooth operations and efficient inventory management. Throughout PP-001.5, we will explore the step-by-step processes of generating and printing labels, ensuring clarity, and accuracy. Once a pickup list, either individual or combined, is sent or upon receipt of a delivery confirmation, it is mandatory to print the labels. For step-by-step guides, please refer to the supporting documents attached to this manual. PP-001.5 A - Printing ‘External Labels’ These labels are essential for accurately identifying and tracking items in our outdoor yard, these labels are strong enough to endure weather conditions and longevity in various working conditions. Steps Before you print, you need to check if it was already printed before. All the printed labels are in vendors label folder. If it is not printed yet, open the PO “labels” Add the material ID of the labels that you need to print, fill the received field. You must print multiples of 4. File> Print > 3 C – Inventory Yard Hort Label from Invoice Click in Print Preview Confirm if the preview is OK, so print. After finishing the print, delete all the items of LABELS PO and save. If this step is missed, the inventory will show wrong information. Important information: All the labels need to have the color printed. If the product code is just letters, do not print and wait until we receive the material to check the code in vendor’s label. Request to yard responsible to send you a label photo as soon as we receive the material. Send the photo to CEO and request him to update the product code. After that, you can print the label. Do not forget to check if the label is not already printed. PP-001.5 B - Printing ‘Internal Labels without Price’ Internal labels without prices, also known as product labels, are utilized to identify each individual item. These labels do not display prices and are primarily used for organizational purposes, allowing staff to locate and manage inventory efficiently. Steps Before you print, you need to check if it was already printed before. All the printed labels are in vendors label folder. The internal label is printed from the sales computer, so you need to go there, open the EBMS on that computer to follow. Open the PO “labels” Add the material ID of the labels that you need to print, fill the received field. This label is individual. File> Print > 6 – Inventory Labels from Invoice (3 x 1) Change the printer to Datamax and print it. PP-001.5 C - Printing ‘Internal Labels with Price’ On the other hand, internal labels with prices, also known as shelf labels, serve the specific purpose of indicating the price of products directly on the shelves themselves, aiding customers in identifying product costs while browsing the store. Steps The internal label is printed from the sales computer, so you need to go there, open the EBMS on that computer to follow. Open the product catalog Look for the material (CTRL+F) Open the product and print from it. Change the printer to Datamax and print it. Close the EBMS. PP-001.6 - Returning Material If any material should be returned to the vendor, you will receive a Return Approval Form from a Sales Admin. Confirm if the vendor will accept the material back, so you must create a negative PO to update the inventory. Send the PO to the vendor and wait for the RMA. After receiving the RMA, schedule the return for the next pickup or vendor’s delivery. Keep yard updated about the return. PP-001.6 A - Returning Damaged Material If any material is damaged, you must create a negative PO for the vendor to update the inventory. Send the PO to the vendor to check the return of the material. The vendor will evaluate and inform the next step (if it should be returned, swapped, or just a credit obtained). Keep yard updated about the return. When the vendor receives the material, they will process the return and give the credit. PP-002 – NEGATIVE INVENTORY The purpose of this procedure is to ensure the accuracy and completeness of Sales Orders (SO) by conducting a thorough review of the Inventory Needed for Sales Orders in the EBMS system. The procedure aims to identify any instances of negative inventory that may indicate missing materials required for fulfilling sales orders. By performing this check, we aim to prevent oversight and confirm that the sales team has communicated all necessary information to the purchasing department, avoiding potential delays and customer dissatisfaction. The expected outcome of this procedure is a comprehensive review of the Inventory Needed for Sales Orders, with a focus on identifying any negative quantities. By investigating and verifying each case of negative inventory, we aim to distinguish between genuine sales orders and mere copy orders. In the event of true orders, the expected outcome is to prompt timely communication with the salesperson and subsequent initiation of the standard procurement process to ensure the required materials are ordered promptly. For step-by-step guides, please refer to the supporting documents attached to this manual. Steps In EBMS, click in Post All Transactions and after in Reporting Click in Inventory > Counts/Values > Inventory Needed For Sales Orders > Print Print Preview Check if something is showing in the last collum (Qty. Needed) that it is not copy order. If something is showing, ask the salesperson about the order, to check if it is only a copy or a true order. True orders need to be ordered the missing material as the usual sales process. Tips Negative inventory must be pulled once a week, before the minimum inventory report. PP-003 – OPEN ORDERS AVAILABILITY & PICKUP LISTS This SOP is designed to streamline the daily process of managing open orders from Techo-Bloc, Nicolock, and Unilock. The primary objectives are to ensure the timely receipt and printing of reports containing open orders, confirm the availability of items and estimated time of arrival (ETA), and initiate necessary actions such as requesting loads for materials that are ready for shipment. By implementing this procedure, we aim to enhance communication with suppliers, optimize inventory management, and facilitate the efficient planning of material transportation. The expected outcome of this procedure is a systematic and proactive approach to managing open orders. By receiving and reviewing daily reports, confirming item availability and ETA, and initiating appropriate actions based on vendor availability and ship dates, we anticipate: Improved visibility into the status of open orders. Timely response to vendor availability and ship date confirmations. Enhanced coordination with suppliers for efficient material pickup and transportation. Minimization of delays and optimization of inventory flow. Steps Every day, you should receive and print reports containing open orders from Techo-Bloc, Nicolock, and Unilock. If a report is not received, you should promptly request it from the respective supplier. In this report you can confirm the available item and the ETA of the orders. Confirm the ship date and vendor availability you should request a load to bring the materials. Reports Techo-Bloc – Create a pickup list of when materials are available. Unilock – highlight the available items and print. Create a pickup list of when materials are available. Nicolock – Request a load when a full load becomes available. PP-003.1 - Creating a Pickup List Open the order to pickup Fill out the quantity to pickup Go to File> Print > 4 D - Pickup list (Custom)… Click in Print Preview Check if all the information is right (weight, vendor address, pallets) In PDF document opened, click to send by email and send it to dispatch ([email protected]) Email Subject: VENDOR PICKUP - MM/DD - CUSTOMER (if it is for a customer) **Add REVISED if it was updated. After you send the pickup list, you should print the labels. PP-003.2 - Creating Combined Pickup list Write in Memo field the PO's number that will be combined Fill the pickup quantity in item in each PO and save – combine all the pallets in only one PO. Go to File> Print > 5 D1 - Combined Pickup list (Custom)… Write the PO's numbers to be combined and click in Print Preview In PDF document opened, click to send by email and send it to dispatch Email Subject: VENDOR PICKUP - MM/DD - CUSTOMER (if it is to a customer) **Add REVISED if it was updated. After you send the pickup list or combined pickup list, you should print the labels. PP-003.3 – Requesting a Delivery Load In this process, we ensure streamlined logistics by initiating delivery requests exclusively for Nicolock, CT, while allowing other delivery vendors to proceed with direct shipping as ordered. Below, you'll find step-by-step instructions to ensure efficient handling of the delivery process. VENDOR ETA - (IF IN STOCK) Pickup BELGARD 1-2 DAYS NICOLOCK, MA 1-3 DAYS TECHO-BLOC, MA 1-3 DAYS MSI 1-3 DAYS R R STONE 1-2 DAYS STILES & HART 1-3 DAYS STONEYARD 1-3 DAYS UNILOCK 1-2 DAYS Delivery INSTONE MON/THURS DELIVERY NICOLOCK, CT 2 WEEKS OUTDOOR LIVING WED/FRI SHIPMENT TECHO-BLOC, PA 3-4 DAYS PORTLAND STONE 3-5 DAYS RAFFERTY 2-4 DAYS ROCK OF AGES 4 WEEKS S. McCLAIN CHECK WITH EMERSON WESTWOOD MILLS 10 DAYS Steps Initiate a delivery request exclusively for Nicolock, CT. Other delivery vendors should proceed with direct shipping as ordered. As table VENDOR ETA - (IF IN STOCK). Ensure that you have a full load ready, weighing 47,500 lbs, before requesting delivery for Nicolock, CT. Send an email to the following recipients: Kelly Cox [email protected] Connecticut Orders [email protected] Dowell Silva [email protected] Requesting the Nicolock delivery. Upon receiving confirmation from Nicolock, verify that the load details are correct. Print the necessary labels for the shipment. PP-004 – SHIPPING REPORT This procedure was established to ensure proactive customer follow-up and maintain control over all orders. By generating and reviewing a weekly report, the aim is to identify and highlight pending sales orders in the EBMS system that require attention due to outdated internal notes. This procedure enhances customer satisfaction and operational efficiency by promptly addressing any unresolved issues or updates related to sales orders. The expected outcome of this procedure is a comprehensive report that highlights any pending sales orders in the EBMS system, based on the criteria of outdated internal notes. By implementing this process, we anticipate: Improved customer communication and satisfaction through timely follow-up. Enhanced control over the status of all orders within the specified date range. Identification of pending orders for resolution and internal collaboration. Streamlined operations and proactive order management. Steps Create this report every Tuesday and give it to the sales manager and receive it back on Friday. In EBMS, click in Post All Transactions and after in Reporting Click in Sales > Shipping Schedule> Print Change the date to begin 6 months before and the end date 1 month after the actual date. Click in pint preview. In the generated report you need to check if the SO is updated. If there is more than 2 weeks (passed the ship date) and there are no notes on the order explaining why order haven't been picked up, highlight with appropriate color (see picture), and add a small note on the shipping schedule about what's going on. Pickup orders: Delivery orders: Pulled: Check on internal notes if the salesperson is in touch and customer is aware the order is ready to pick-up. Backorder (BO): highlight with the BO color and write "BO" and the updated ETA. Partially pulled/BO: highlight with the BO color and write "Partially pulled" and the updated ETA. (check on BO with vendors while doing the Shipping Schedule). No item status: Check print log to see if it is a SO copy. If it is a real SO, highlight with the Office Manager color and write "no item status". Pulled: Highlight with Dispatch color the SO line. Partially pulled/BO: highlight with BO and Dispatch color. Also, add notes for Dispatch to see if customer will get the partial delivery. Once all SO were checked, give the Shipping Schedule to the Office Manager. The Shipping Schedule must be returned to purchasing by Friday. If any SO has been seated for more than 2 months, the Sales Manager must take immediate action to resolve the issue. If unresolved, the Office Manager should escalate the matter to CEO for resolution. DISPATCH Dispatch will check all SO highlighted with their color. Dispatch will analyze each SO to check: If they have the SO copy or original paperwork for the delivery. If all highlighted SO are on the delivery schedule. If SO, has BO, follow up with Purchasing what is the product situation to confirm when the product will get here. (If 2 days before the delivery date Purchasing and salesperson don't have a solution for the BO items, CEO must be notified. Important: when talking about SO, purchasing, salesperson and dispatch must communicate by email. TIPS Do not close print preview before finishing the shipping schedule. Check the print log to see if it's a confirmed order or only a SO copy. PP-005 – COUNTING INVENTORY One key aspect of inventory management is accurately counting and tracking inventory requests from time to time. If you need to confirm if some inventory is right, you should fill out the Inventory Count Forms, usually when there is just one layer or unit of one product for a long time. To check if it is in perfect condition to sell or needs to be ordered. You will fill out the fields: Code, Brand, Item Description, Date and TIME. The yard responsible for it will count the items and write the quantity, condition of the material and sign. If some EBMS inventory adjust is necessary, you will fill out the Available/ SO not pulled in Office collum, sign, give and explain to the CEO for the inventory adjust. Checking EBMS: Look up all sales orders we have for this product to check if it is pulled. Take a screenshot of the sales orders list, so you can see how everything was when you counted the items. Print the screenshot, so you can register all notes. Put the date. Have the yard manager check what is pulled to make sure the quantity is right. Check the pending received Purchase Order. Check if there is any piece on the display. Check if there is any return that has not been processed yet. After adjusting, archive the form in the inventory folder. For examples, please refer to the supporting documents attached to this manual. PP-005.1 – Counting Annual Inventory Counting annual inventory, also known as year-end inventory count, is a comprehensive process where Old Station physically counts and verifies all the items in its inventory at the end of the year. This process is essential for ensuring the accuracy of inventory records, identifying discrepancies, and evaluating the financial health of the business. Export items for each product from the system (e.g. Blue Mist, Stanstead Unilock, etc.). Paste and copy the exported list to a "Counting" sheet (picture). Make sure the code and description fields are filled in. Whoever is counting the physical inventory fills in the date, and the column "Physical Count 1st". When the yard brings the sheet back to the office, the "System" column will be filled in. If there is a discrepancy, the office will have someone do the 2nd count. If still wrong, have a 3rd person. Once the count is verified, highlight in orange the row that needs to be adjusted and give the sheet to CEO. * A list of discontinued and second priority products should be generated twice a year, so purchasing can return discontinued products we didn't sale during the year. We cannot return products that have been discontinued for more than one year from their discontinuation date. Important: Set a reminder on the Purchasing calendar to ensure timely generation of this list for the following vendors: UNILOCK, NICOLOCK, BELGARD, TECHO, AND UMACO PP-006 – CHECKING AVAILABILITY In this procedure, we outline the steps for efficiently checking material availability in response to sales inquiries. Ensuring timely responses and accurate information is essential for maintaining customer satisfaction and facilitating smooth transactions. Steps When some salesperson sends an email asking for material availability, you should send an email to the vendor asking. Do not ask about the price before checking the price list. Check the vendor’s email in EBMS – looking by vendor Ctrl+F and look for the vendor In contact tab, find the email address Send an email asking about the availability of the materials, after having an answer return to sales. PP-007 – REQUESTING SAMPLES In this procedure, we outline the steps for requesting samples, which are crucial for customers to confirm the material or color of a product before ordering. Salesperson will send you the template requesting samples Check the vendor’s email in EBMS – looking by vendor details In contact tab, find the sales rep email address. Send the request to the vendor and answer the salesperson. Important: For requesting a Techo-Bloc samples you must send the Techo Sample Request Form to [email protected]. PP-008 – PURCHASING OFFICE SUPPLIES